THE MECHANISM of GRAIN GROWTH in CERAMICS by C. M
Total Page:16
File Type:pdf, Size:1020Kb
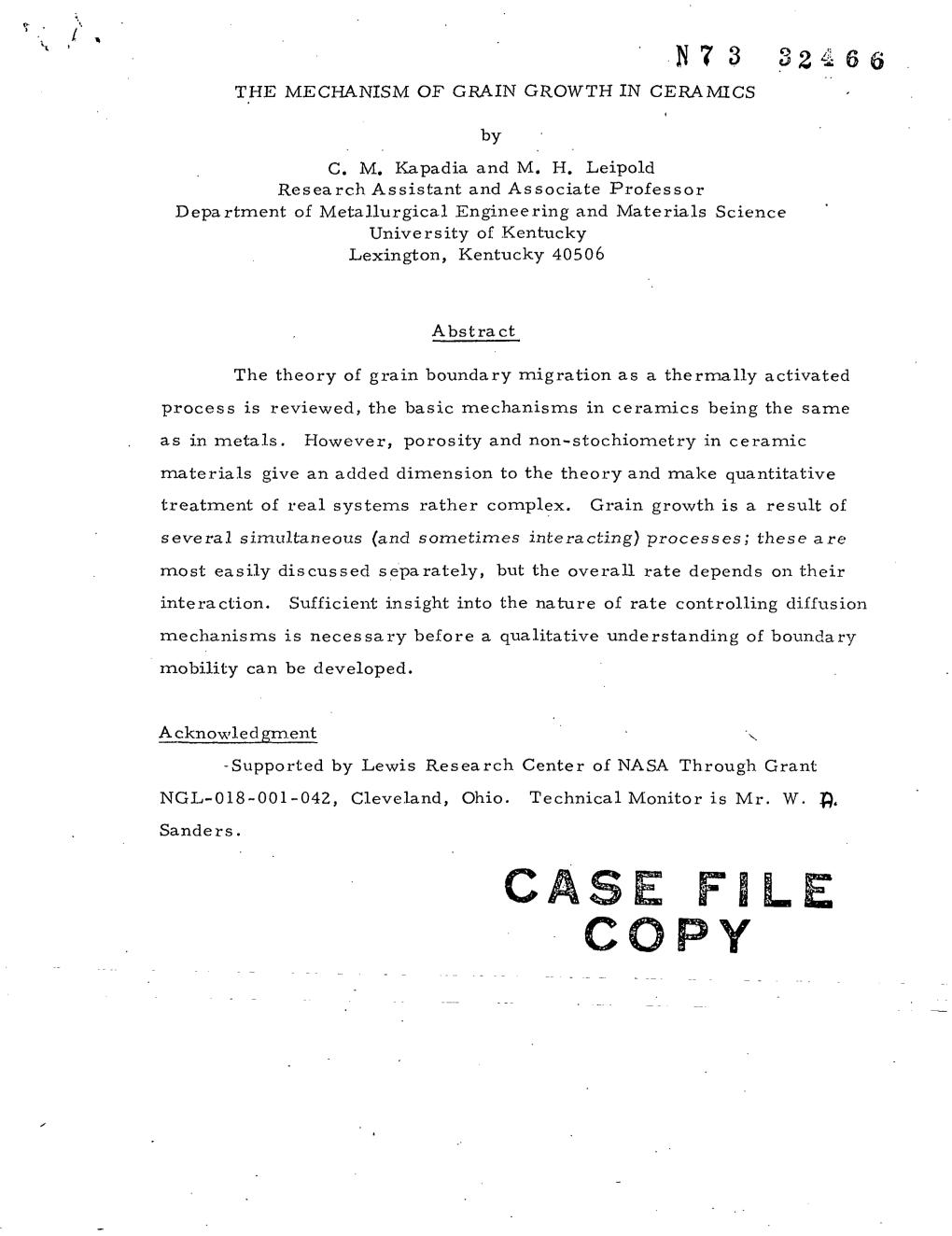
Load more
Recommended publications
-
Quartz Grainsize Evolution During Dynamic Recrystallization Across a Natural Shear Zone Boundary
Journal of Structural Geology 109 (2018) 120–126 Contents lists available at ScienceDirect Journal of Structural Geology journal homepage: www.elsevier.com/locate/jsg Quartz grainsize evolution during dynamic recrystallization across a natural T shear zone boundary ∗ Haoran Xia , John P. Platt Department of Earth Sciences, University of Southern California, Los Angeles, CA 90089-0740, USA ARTICLE INFO ABSTRACT Keywords: Although it is widely accepted that grainsize reduction by dynamic recrystallization can lead to strain locali- Dynamic recrystallization zation, the details of the grainsize evolution during dynamic recrystallization remain unclear. We investigated Bulge the bulge size and grainsizes of quartz at approximately the initiation and the completion stages of bulging Subgrain recrystallization across the upper boundary of a 500 m thick mylonite zone above the Vincent fault in the San Grainsize evolution Gabriel Mountains, southern California. Within uncertainty, the average bulge size of quartz, 4.7 ± 1.5 μm, is Vincent fault the same as the recrystallized grainsize, 4.5 ± 1.5 μm, at the incipient stage of dynamic recrystallization, and also the same within uncertainties as the recrystallized grainsize when dynamic recrystallization is largely complete, 4.7 ± 1.3 μm. These observations indicate that the recrystallized grainsize is controlled by the nu- cleation process and does not change afterwards. It is also consistent with the experimental finding that the quartz recrystallized grainsize paleopiezometer is independent of -
Using Grain Boundary Irregularity to Quantify Dynamic Recrystallization in Ice
Acta Materialia 209 (2021) 116810 Contents lists available at ScienceDirect Acta Materialia journal homepage: www.elsevier.com/locate/actamat Using grain boundary irregularity to quantify dynamic recrystallization in ice ∗ Sheng Fan a, , David J. Prior a, Andrew J. Cross b,c, David L. Goldsby b, Travis F. Hager b, Marianne Negrini a, Chao Qi d a Department of Geology, University of Otago, Dunedin, New Zealand b Department of Earth and Environmental Science, University of Pennsylvania, Philadelphia, PA, United States c Department of Geology and Geophysics, Woods Hole Oceanographic Institution, Woods Hole, MA, United States d Institute of Geology and Geophysics, Chinese Academy of Sciences, Beijing, China a r t i c l e i n f o a b s t r a c t Article history: Dynamic recrystallization is an important mechanical weakening mechanism during the deformation of Received 24 December 2020 ice, yet we currently lack robust quantitative tools for identifying recrystallized grains in the “migration” Revised 7 March 2021 recrystallization regime that dominates ice deformation at temperatures close to the ice melting point. Accepted 10 March 2021 Here, we propose grain boundary irregularity as a quantitative means for discriminating between recrys- Available online 15 March 2021 tallized (high sphericity, low irregularity) and remnant (low sphericity, high irregularity) grains. To this Keywords: end, we analysed cryogenic electron backscatter diffraction (cryo-EBSD) data of deformed polycrystalline High-temperature deformation ice, to quantify dynamic recrystallization using grain boundary irregularity statistics. Grain boundary ir- Grain boundary irregularity regularity has an inverse relationship with a sphericity parameter, , defined as the ratio of grain area Dynamic recrystallization and grain perimeter, divided by grain radius in 2-D so that the measurement is grain size independent. -
Grain Boundary Loops in Graphene
Grain Boundary Loops in Graphene Eric Cockayne,1§ Gregory M. Rutter,2,3 Nathan P. Guisinger,3* Jason N. Crain,3 Phillip N. First,2 and Joseph A. Stroscio3§ 1Ceramics Division, NIST, Gaithersburg, MD 20899 2School of Physics, Georgia Institute of Technology, Atlanta, GA 30332 3Center for Nanoscale Science and Technology, NIST, Gaithersburg, MD 20899 Topological defects can affect the physical properties of graphene in unexpected ways. Harnessing their influence may lead to enhanced control of both material strength and electrical properties. Here we present a new class of topological defects in graphene composed of a rotating sequence of dislocations that close on themselves, forming grain boundary loops that either conserve the number of atoms in the hexagonal lattice or accommodate vacancy/interstitial reconstruction, while leaving no unsatisfied bonds. One grain boundary loop is observed as a “flower” pattern in scanning tunneling microscopy (STM) studies of epitaxial graphene grown on SiC(0001). We show that the flower defect has the lowest energy per dislocation core of any known topological defect in graphene, providing a natural explanation for its growth via the coalescence of mobile dislocations. §Authors to whom correspondence should be addressed:[email protected], [email protected] * Present address: Argonne National Laboratory, Argonne, IL 1 I. Introduction The symmetry of the graphene honeycomb lattice is a key element for determining many of graphene's unique electronic properties. The sub-lattice symmetry of graphene gives rise to its low energy electronic structure, which is characterized by linear energy-momentum dispersion.1 The spinor-like eigenstates of graphene lead to one of its celebrated properties, reduced backscattering (i.e., high carrier mobility), which results from pseudo-spin conservation in scattering within a smooth disorder potential.2,3 Topological lattice defects break the sublattice symmetry, allowing insight into the fundamental quantum properties of graphene. -
Grain Boundary Phases in Bcc Metals
Nanoscale Grain boundary phases in bcc metals Journal: Nanoscale Manuscript ID NR-ART-01-2018-000271.R1 Article Type: Paper Date Submitted by the Author: 06-Mar-2018 Complete List of Authors: Frolov, Timofey; Lawrence Livermore National Laboratory, Setyawan, Wahyu; Pacific Northwest National Laboratory, Kurtz, Richard; Pacific Northwest National Laboratory Marian, Jaime ; University of California Los Angeles Oganov, Artem; Stony Brook University Rudd, Robert; Lawrence Livermore National Laboratory Zhu, Qiang; University of Nevada Las Vegas Page 1 of 34 Nanoscale Grain boundary phases in bcc metals T. Frolov,1 W. Setyawan,2 R. J. Kurtz,2 J. Marian,3 A. R. Oganov,4, ∗ R. E. Rudd,1 and Q. Zhu5 1Lawrence Livermore National Laboratory, Livermore, California 94550, USA 2Pacific Northwest National Laboratory, P. O. Box 999, Richland, Washington 99352, USA 3Department of Materials Science and Engineering, University of California Los Angeles, Los Angeles, California 90095, USA 4Stony Brook University, Stony Brook, New York 11794, USA 5Department of Physics and Astronomy, High Pressure Science and Engineering Center, University of Nevada, Las Vegas, Nevada 89154, USA Abstract We report a computational discovery of novel grain boundary structures and multiple grain boundary phases in elemental body-centered cubic (bcc) metals represented by tungsten, tantalum and molybde- num. While grain boundary structures created by the γ-surface method as a union of two perfect half crystals have been studied extensively, it is known that the method has limitations and does not always predict the correct ground states. Here, we use a newly developed computational tool, based on evolu- tionary algorithms, to perform a grand-canonical search of a high-angle symmetric tilt and twist bound- aries in tungsten, and we find new ground states and multiple phases that cannot be described using the conventional structural unit model. -
Grain Boundary Properties of Elemental Metals
Acta Materialia 186 (2020) 40–49 Contents lists available at ScienceDirect Acta Materialia journal homepage: www.elsevier.com/locate/actamat Full length article Grain boundary properties of elemental metals Hui Zheng a,1, Xiang-Guo Li a,1, Richard Tran a, Chi Chen a, Matthew Horton b, ∗ Donald Winston b, Kristin Aslaug Persson b,c, Shyue Ping Ong a, a Department of NanoEngineering, University of California San Diego, 9500 Gilman Dr, Mail Code 0448, La Jolla, CA 92093-0448, United States b Energy Technologies Area, Lawrence Berkeley National Laboratory, Berkeley, CA 94720, United States c Department of Materials Science & Engineering, University of California Berkeley, Berkeley, CA 94720-1760, United States a r t i c l e i n f o a b s t r a c t Article history: The structure and energy of grain boundaries (GBs) are essential for predicting the properties of polycrys- Received 26 July 2019 talline materials. In this work, we use high-throughput density functional theory calculations workflow Revised 13 December 2019 to construct the Grain Boundary Database (GBDB), the largest database of DFT-computed grain boundary Accepted 14 December 2019 properties to date. The database currently encompasses 327 GBs of 58 elemental metals, including 10 Available online 19 December 2019 common twist or symmetric tilt GBs for body-centered cubic (bcc) and face-centered cubic (fcc) systems Keywords: and the 7 [0 0 01] twist GB for hexagonal close-packed (hcp) systems. In particular, we demonstrate a Grain boundary novel scaled-structural template approach for HT GB calculations, which reduces the computational cost DFT of converging GB structures by a factor of ~ 3–6. -
Grain Growth During Spark Plasma and Flash Sintering of Ceramic Nanoparticles: a Review Rachman Chaim, Geoffroy Chevallier, Alicia Weibel, Claude Estournes
Grain growth during spark plasma and flash sintering of ceramic nanoparticles: a review Rachman Chaim, Geoffroy Chevallier, Alicia Weibel, Claude Estournes To cite this version: Rachman Chaim, Geoffroy Chevallier, Alicia Weibel, Claude Estournes. Grain growth during spark plasma and flash sintering of ceramic nanoparticles: a review. Journal of Materials Science, Springer Verlag, 2018, vol. 53 (n° 5), pp. 3087-3105. 10.1007/s10853-017-1761-7. hal-01682331 HAL Id: hal-01682331 https://hal.archives-ouvertes.fr/hal-01682331 Submitted on 12 Jan 2018 HAL is a multi-disciplinary open access L’archive ouverte pluridisciplinaire HAL, est archive for the deposit and dissemination of sci- destinée au dépôt et à la diffusion de documents entific research documents, whether they are pub- scientifiques de niveau recherche, publiés ou non, lished or not. The documents may come from émanant des établissements d’enseignement et de teaching and research institutions in France or recherche français ou étrangers, des laboratoires abroad, or from public or private research centers. publics ou privés. Open Archive TOULOUSE Archive Ouverte (OATAO) OATAO is an open access repository that collects the work of Toulouse researchers and makes it freely available over the web where possible. This is an author-deposited version published in : http://oatao.univ-toulouse.fr/ Eprints ID : 19431 To link to this article : DOI:10.1007/s10853-017-1761-7 URL : http://dx.doi.org/10.1007/s10853-017-1761-7 To cite this version : Chaim, Rachman and Chevallier, Geoffroy and Weibel, Alicia and Estournes, Claude Grain growth during spark plasma and flash sintering of ceramic nanoparticles: a review. -
Electronic Properties of Grains and Grain Boundaries in Graphene Grown by Chemical Vapor Deposition
Electronic properties of grains and grain boundaries in graphene grown by chemical vapor deposition Luis A. Jaureguia,b, Helin Caoa,c, Wei Wud,e, Qingkai Yud,e,f, Yong P. Chenc,a,b,* a Birck Nanotechnology Center, Purdue University, West Lafayette, IN 47907, USA b School of Electrical and Computer Engineering, Purdue University, West Lafayette, IN 47907, USA c Department of Physics, Purdue University, West Lafayette, IN 47907, USA d Center for Advanced Materials, University of Houston, Houston, TX 77204, USA e Department of Electrical and Computer Engineering, University of Houston, Houston, TX 77204, USA f Ingram School of Engineering and Materials Science, Engineering and Commercialization Program, Texas State University, San Marcos, TX 78666, USA ABSTRACT We synthesize hexagonal shaped single-crystal graphene, with edges parallel to the zig-zag orientations, by ambient pressure CVD on polycrystalline Cu foils. We measure the electronic properties of such grains as well as of individual graphene grain boundaries, formed when two grains merged during the growth. The grain boundaries are visualized using Raman mapping of the D band intensity, and we show that individual boundaries between coalesced grains impede electrical transport in graphene and induce prominent weak localization, indicative of intervalley scattering in graphene. * Corresponding author. Tel.: +1 765 494 0947; Fax: +1 765 494 0706 E-mail address: [email protected] (Y. P. Chen) 1. Introduction Since its discovery, graphene has attracted a lot of attention in many fields. Graphene’s potential applications have motivated the development of large-scale synthesis of graphene grown by several methods, including graphitization of SiC surfaces [1, 2] and chemical vapor deposition (CVD) on transition metals such as Ni [3-5] and Cu [6]. -
Phase Field Modelling of Abnormal Grain Growth
materials Article Phase Field Modelling of Abnormal Grain Growth Ying Liu 1, Matthias Militzer 1,* and Michel Perez 2 1 The Centre for Metallurgical Process Engineering, The University of British Columbia, Vancouver, BC V6T1Z4, Canada; [email protected] 2 MATEIS, UMR CNRS 5510, INSA Lyon, Univ. Lyon, F69621 Villeurbanne, France; [email protected] * Correspondence: [email protected]; Tel.: +1-604-822-3676 Received: 20 October 2019; Accepted: 27 November 2019; Published: 5 December 2019 Abstract: Heterogeneous grain structures may develop due to abnormal grain growth during processing of polycrystalline materials ranging from metals and alloys to ceramics. The phenomenon must be controlled in practical applications where typically homogeneous grain structures are desired. Recent advances in experimental and computational techniques have, thus, stimulated the need to revisit the underlying growth mechanisms. Here, phase field modelling is used to systematically evaluate conditions for initiation of abnormal grain growth. Grain boundaries are classified into two classes, i.e., high- and low-mobility boundaries. Three different approaches are considered for having high- and low-mobility boundaries: (i) critical threshold angle of grain boundary disorientation above which boundaries are highly mobile, (ii) two grain types A and B with the A–B boundaries being highly mobile, and (iii) three grain types, A, B and C with the A–B boundaries being fast. For these different scenarios, 2D simulations have been performed to quantify the effect of variations in the mobility ratio, threshold angle and fractions of grain types, respectively, on the potential onset of abnormal grain growth and the degree of heterogeneity in the resulting grain structures. -
Emission of Dislocations from Grain Boundaries and Its Role in Nanomaterials
crystals Review Emission of Dislocations from Grain Boundaries and Its Role in Nanomaterials James C. M. Li 1,*, C. R. Feng 2 and Bhakta B. Rath 2 1 Department of Mechanical Engineering, University of Rochester, Rochester, NY 14627, USA 2 U.S. Naval Research Laboratory, 4555 Overlook Ave SW, Washington, DC 20375, USA; [email protected] (C.R.F.); [email protected] (B.B.R.) * Correspondence: [email protected] Abstract: The Frank-Read model, as a way of generating dislocations in metals and alloys, is widely accepted. In the early 1960s, Li proposed an alternate mechanism. Namely, grain boundary sources for dislocations, with the aim of providing a different model for the Hall-Petch relation without the need of dislocation pile-ups at grain boundaries, or Frank-Read sources inside the grain. This article provides a review of his model, and supporting evidence for grain boundaries or interfacial sources of dislocations, including direct observations using transmission electron microscopy. The Li model has acquired new interest with the recent development of nanomaterial and multilayers. It is now known that nanocrystalline metals/alloys show a behavior different from conventional polycrystalline materials. The role of grain boundary sources in nanomaterials is reviewed briefly. Keywords: dislocation emission; grain boundaries; nanomaterials; Hall-Petch relation; metals and alloys 1. Introduction To explain the properties of crystalline aggregates, such as crystal plasticity, Taylor [1,2] provided a theoretical construct of line defects in the atomic scale of the crystal lattice. Citation: Li, J.C.M.; Feng, C.R.; With the use of the electron microscope, the sample presence of dislocations validated Rath, B.B. -
Development of the Microstructure of the Silicon Nitride Based Ceramics
Materials Research, Vol. 2, No. 3, 165-172, 1999. © 1999 Development of the Microstructure of the Silicon Nitride Based Ceramics J.C. Bressiani, V. Izhevskyi*, Ana H. A. Bressiani Instituto de Pesquisas Energéticas e Nucleares, IPEN, C.P. 11049 Pinheiros 05422-970 São Paulo - SP, Brazil Received: August 15, 1998; Revised: March 30, 1999 Basic regularities of silicon nitride based materials microstructure formation and development in interrelation with processing conditions, type of sintering additives, and starting powders properties are discussed. Models of abnormal or exaggerated grain growth are critically reassessed. Results of several model experiments conducted in order to determine the most important factors directing the microstructure formation processes in RE-fluxed Si3N4 ceramics are reviewed. Existing data on the mechanisms governing the microstructure development of Si3N4-based ceramics are analyzed and several principles of microstructure tailoring are formulated. Keywords: silicon nitride, microstructure, phase transformation, liquid phase sintering 1. Introduction the Weibull modulus of the fracture strength of silicon nitride. A small transverse grain size was shown to give Mechanical properties of the Si3N4-based ceramics higher Weibull modulus than the coarse microstructures. such as strength and fracture toughness as well as Weibull The observed increase in fracture resistance was mainly modulus are strongly dependent on the microstructure. attributed to crack deflection, and crack bridging mecha- Formation of the resulting microstructure is dictated by the nism3-6. In some cases crack branching was also observed. densification mechanism, i.e., reactive liquid phase sinter- An important role in fracture resistance improvement is ing. The α-Si3N4 in the starting powder compact is trans- played also by the secondary phase. -
TEM and STEM Investigation of Grain Boundaries and Second Phases In
Philosophical Magazine, Vol. 87, No. 34, 1 December 2007, 5447–5459 TEM and STEM investigation of grain boundaries and second phases in barium titanate S. J. ZHENGyz, K. DU*y, X. H. SANGyz and X. L. MAy yShenyang National Laboratory for Materials Science, Institute of Metal Research, Chinese Academy of Sciences, 72 Wenhua Road, 110016 Shenyang, China zGraduate School of Chinese Academy of Sciences, 100049 Beijing, China (Received 5 June 2007; in final form 26 August 2007) An intergranular layer was found in 0.4 mol% Y-doped BaTiO3, which was sintered below the eutectic temperature in air. The layer possessed a crystal structure similar to Ba6Ti17O40 with a thickness of 0.7 nm. Plate-like second phases of Ba6Ti17O40 were also observed at triple-grain junctions and an orientation relationship of ð111Þt==ð001Þm, ð112Þt==ð602Þm and ½110t==½010m was determined between the tetragonal BaTiO3 and the monoclinic Ba6Ti17O40. The detailed structure of the interface between BaTiO3 and Ba6Ti17O40 was resolved Downloaded By: [Du, K.] At: 00:06 31 October 2007 by scanning transmission electron microscopy and high-resolution transmission electron microscopy investigations. 1. Introduction BaTiO3-based compounds are one of the most important electronic ceramics, which have numerous applications in sensors, multilayer ceramic capacitors and tuneable microwave devices [1–3]. For example, Y-doped BaTiO3 ceramics, with their excellent positive temperature coefficient of resistivity (PTC), are widely used as commercial thermistors. It is generally accepted that the electrical properties of the BaTiO3 ceramics, particularly the PTC effect, are closely related to their grain boundaries (GBs) [4–7]. Intensive studies have been performed on the GB structures in BaTiO3 ceramics in the development of materials and to understand the electrical behaviour of barium titanate compounds [8–16]. -
THE EFFECTS of DOPANTS and COMPLEXIONS on GRAIN BOUNDARY DIFFUSION and FRACTURE TOUGHNESS in Α-Al2o3
THE EFFECTS OF DOPANTS AND COMPLEXIONS ON GRAIN BOUNDARY DIFFUSION AND FRACTURE TOUGHNESS IN α-Al2O3 BY LIN FENG DISSERTATION Submitted in partial fulfillment of the requirements for the degree of Doctor of Philosophy in Materials Science and Engineering in the Graduate College of the University of Illinois at Urbana-Champaign, 2017 Urbana, Illinois Doctoral Committee: Associate Professor Shen Dillon, Chair Professor John Lambros Assistant Professor Jessica Krogstad Assistant Professor Daniel Shoemaker ABSTRACT Grain boundaries often play a dominant role in determining material properties and processing, which originates from their distinct local structures, chemistry, and properties. Understanding and controlling grain boundary structure-property relationships has been an ongoing challenge that is critical for engineering materials, and motivates this dissertation study. Here, α-Al2O3 is chosen as a model system due its importance as a structural, optical, and high temperature refractory ceramic whose grain boundary properties remain poorly understood despite several decades of intensive investigation. Significant controversy still surrounds two important properties of alumina that depend on its grain boundaries; diffusional transport and mechanical fracture. Previously enigmatic grain boundary behavior in alumina, such as abnormal grain growth, were found to derive from chemically or thermally induced grain boundary phase transitions or complexion transitions. This work investigates the hypothesis that such complexion transitions could also impact grain boundary diffusivity and grain boundary mechanical strength. Scanning transmission electron microscopy based energy- dispersive spectroscopy and secondary ion mass spectrometry are utilized to characterize chemical diffusion profiles and quantify lattice and grain boundary diffusivity in Mg2+ and Si4+ doped alumina. It has found that Cr3+ cation chemical tracer diffusion in both the alumina lattice and grain boundaries is insensitive to dopants and complexion type.