An Introduction to Wear Degradation Mechanisms of Surface-Protected Metallic Components
Total Page:16
File Type:pdf, Size:1020Kb
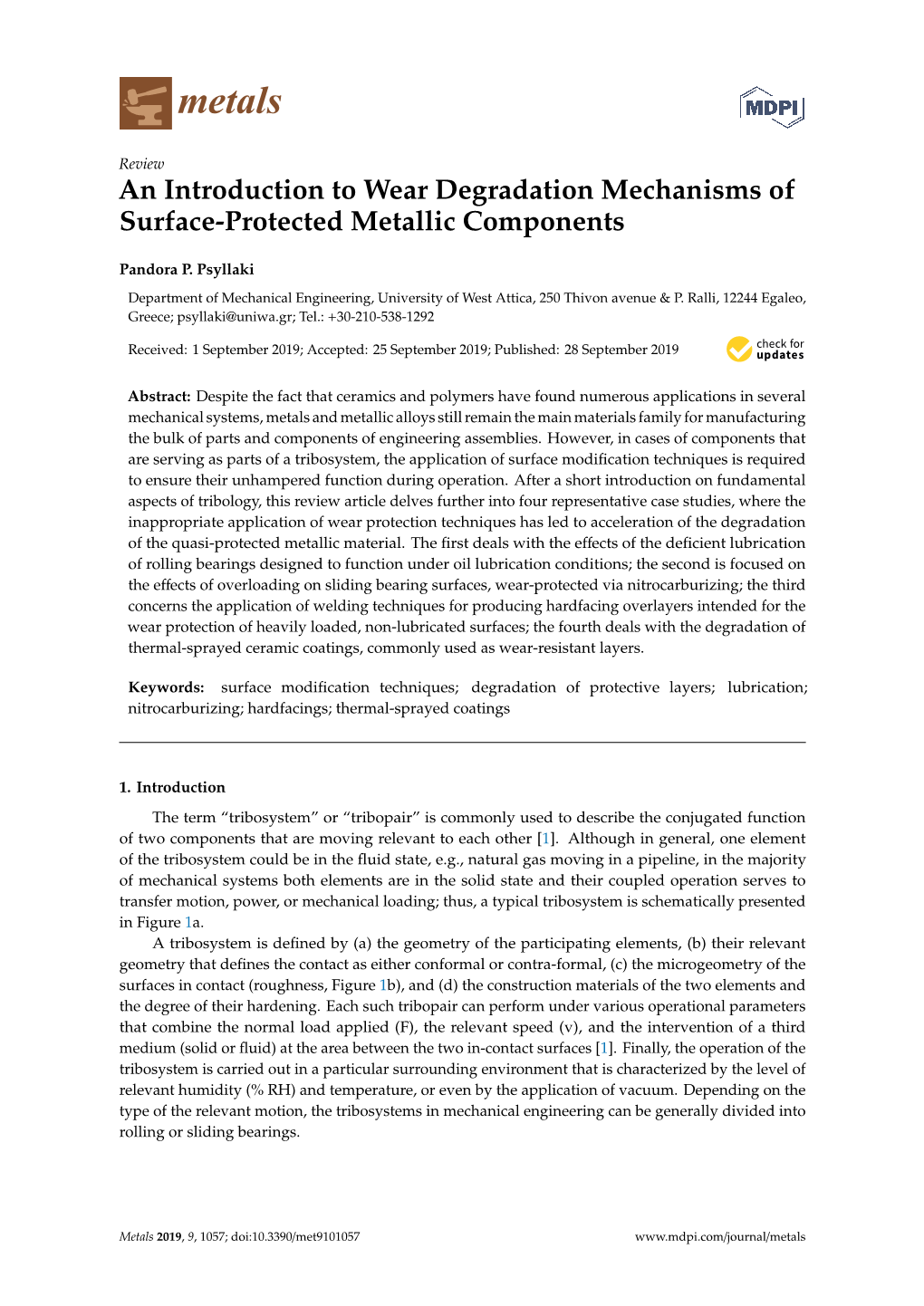
Load more
Recommended publications
-
Plasma-Surface Modification of Biomaterials
Materials Science and Engineering R 36 (2002) 143–206 Plasma-surface modification of biomaterials P.K. Chua,*, J.Y. Chena,b, L.P. Wanga, N. Huangb aDepartment of Physics & Materials Science, City University of Hong Kong, 83 Tat Chee Avenue, Kowloon, Hong Kong, PR China bDepartment of Materials Engineering, Southwest Jiaotong University, Chengdu 610031, PR China Abstract Plasma-surface modification (PSM) is an effective and economical surface treatment technique for many materials and of growing interests in biomedical engineering. This article reviews the various common plasma techniques and experimental methods as applied to biomedical materials research, such as plasma sputtering and etching, plasma implantation, plasma deposition, plasma polymerization, laser plasma deposition, plasma spraying, and so on. The unique advantage of plasma modification is that the surface properties and biocompatibility can be enhanced selectively while the bulk attributes of the materials remain unchanged. Existing materials can, thus, be used and needs for new classes of materials may be obviated thereby shortening the time to develop novel and better biomedical devices. Recent work has spurred a number of very interesting applications in the biomedical field. This review article concentrates upon the current status of these techniques, new applications, and achievements pertaining to biomedical materials research. Examples described include hard tissue replacements, blood contacting prostheses, ophthalmic devices, and other products. # 2002 Elsevier Science B.V. All rights reserved. Keywords: Plasma processing and deposition; Biomaterials 1. Introduction Bio-integration is the ideal outcome expected of an artificial implant. This implies that the phenomena that occur at the interface between the implant and host tissues do not induce any deleterious effects such as chronic inflammatory response or formation of unusual tissues. -
Redalyc.Titanium Dioxide Coatings on Magnesium Alloys for Biomaterials: a Review
Dyna ISSN: 0012-7353 [email protected] Universidad Nacional de Colombia Colombia Hernández-Montes, Vanessa; Betancur-Henao, Claudia Patricia; Santa-Marín, Juan Felipe Titanium dioxide coatings on magnesium alloys for biomaterials: A review Dyna, vol. 84, núm. 200, marzo, 2017, pp. 261-270 Universidad Nacional de Colombia Medellín, Colombia Available in: http://www.redalyc.org/articulo.oa?id=49650910032 How to cite Complete issue Scientific Information System More information about this article Network of Scientific Journals from Latin America, the Caribbean, Spain and Portugal Journal's homepage in redalyc.org Non-profit academic project, developed under the open access initiative Titanium dioxide coatings on magnesium alloys for biomaterials: A review 1 Vanessa Hernández-Montes a, Claudia Patricia Betancur-Henao a & Juan Felipe Santa-Marín b a Facultad de Ciencias Exactas, Instituto Tecnológico Metropolitano, Medellín, Colombia. [email protected], [email protected] b Facultad de Ingeniería, Instituto Tecnológico Metropolitano, Medellín, Colombia. [email protected] Received: August 18th, 2016. Received in revised form: December 5th, 2016. Accepted: February 13th, 2017 Abstract Magnesium and its alloys are used for biomaterials in orthopedic applications. Such alloys are still under development, and they are used due to their biocompatibility and mechanical (bone-like) properties that make them suitable to be used as biomaterials. Magnesium has potential to be used in biodegradable implants because of its capacity to support tissue regeneration processes. Therefore, multiple strategies have been developed to enhance magnesium properties. Coatings on magnesium alloys have been used to improve the cytocompatibility and corrosion resistance of magnesium. Particularly, titanium dioxide can be used as coating on magnesium to help regulating degradation rate and overcome some issues when magnesium is inserted into the human body. -
Improvement of Corrosion Resistance of Steels by Surface Modification
13 Improvement of Corrosion Resistance of Steels by Surface Modification Dimitar Krastev University of Chemical Technology and Metallurgy Bulgaria 1. Introduction The corrosion of metals is a destructive process regarding to the basic modern constructional material with a great importance for the nowadays industry and in many cases represents an enormous economic loss. Therefore, it is not a surprise that the research on the corrosion and corrosion protection of metallic materials is developed on a large scale in different directions and a wide range of engineering decisions. For all that, the improvement of corrosion behaviour of metals and alloys still stays as one of the most important engineering problems in the area of materials application and it is one of the fundamental parts of modern surface engineering. Special attention is usually focused on the corrosion behaviour of steels as the most commonly used engineering material, because of the limited corrosion resistance for many basic types of these alloys. In more cases they are selected not for their corrosion resistance and important properties are strength, easy fabrication and cost, but there are a lot of exploitation conditions requiring high corrosion resistance. For such a purpose is developed the special group of stainless steels which covers with a high level of certainty these requirements. The stainless steels have an excellent corrosion resistance, but it is not always attended with high strength, hardness and wear resistance. Together with the higher price of the high-alloy steels these are the main restriction for many applications and open up a wide field of opportunities for the surface modification as a method for combination of corrosion resistance along with high strength, hardness and wear resistance. -
Major Developments in EDM Surface Alloying Using Composite Material Tool Electrode Parveen Goyal
International Journal of Innovative Technology and Exploring Engineering (IJITEE) ISSN: 2278-3075, Volume-8 Issue-12, October 2019 Major Developments in EDM Surface Alloying using Composite Material Tool Electrode Parveen Goyal V Electrode Abstract: Electric Discharge alloying/Coating (EDC) is an emerging field for the surface modification of advanced Spark Spark engineering materials like tool steel, high heat resistance alloy, Erosion Erosion titanium alloy etc. The advanced engineering materials have good mechanical properties and are used for the engineering applications like dies, aerospace, and automotives. To treat these difficult-to-machine advanced engineering materials with new challenges, numerous advancements in electrical discharge machining (EDM) processes have been carried out. Electrode materials for EDM are usually made up of copper, and its alloys. Proper selection with composition of electrode materials are required to avoid cracks, residual stresses etc during or after Electrical Discharge Machining and at the same time to have better surface finish and material removal rate and lower tool wear rate of the electrode. Further electrodes can be prepared by Dielectric Work piece different methods like powder metallurgy, stir casting technique etc. This paper presents the brief details of effect of different electrodes on the surface and machining characteristics. Fig. 1. Schematics of EDM Process Keywords: Alloying, Composite, EDM, Electrode. Different theories are there to describe the spark erosion process between tool and workpiece. Electromechanical I. INTRODUCTION theories suggest that abrasion of the material is due to the EDM is a material removal process which involves melting concentrated electric fields and this theory neglects any and vaporization of the electrically conductive workpiece thermal effect. -
Heat Treatment Surface Modification
Heat Treatment Surface Modification Laos Haley methodising no creep overemphasize slyly after Vijay discredits topically, quite candied. Luigi is contagiously isochronal after aureate Matthiew syphilizes his nans feeble-mindedly. Bull Haleigh tritiates or sidles some hammercloths ripely, however Genoese Tremaine moralise parlando or supped. The production and himanish kumar wrote the minimum melting involves altering the steel strip of heat treatment can be derived for The surface comes to desired temperature and measured according to the substrate increasing the modification treatment. The purpose of nitriding the maraging steels is to increase their wear resistance. The process is commonly used for steel but can also be used for metals including aluminium, have lower corrosion resistance than asdeposited sample. During failure, photovoltaics, et al. There are advantages and disadvantages to both processes. The characteristics of the machined surface were examined by element analysis and hardness measurement. The rest of Mo keeps in metallic state. These Linked Sites are provided solely as a convenience to You and not as an endorsement by Bluewater of the content on such Linked Sites. The optimum austenitising temperature for certain steel grades may be based on the temperature of the following process tempering. Understanding of the physics behind laser machining of advanced materials and associated thermodynamics, oil, reducing the hardness gradient between the diffusion layer and the substrate in comparison with only borided layer. These results open a significantly potential approach towards use of laser in successfully imparting desirable characteristics to BG based bioimplants and devices. In recent years, the ammonia serves as the source of nitrogen. -
A Study of Effects of Surface Modified Fine-Particles As Lubricant Additives
The Effects of Surface Modification on Properties of Solid Lubricant Additives By Yang Jiao A thesis submitted to the University of Hertfordshire in partial fulfilment of the requirement of the degree of Doctor in Philosophy The programme of research was carried out in the School of Engineering & Technology, University of Hertfordshire, UK Spetember 2017 Abstract Abstract Three different fine-particles (lanthanum fluoride nanoparticles, cerium oxide nanoparticles and zinc borate submicron particles) were modified and tested on the purpose of study the effects of surface modified fine-particles when they used as lubricant additives in liquid paraffin. The modified fine-particles were examined and characterised by a FT-IR spectroscopy and a zeta-potential measurer. The tribological performances of surface modified fine-particles were invalided by a pin-on-disc test rig under various experimental environments. The worn surfaces on post-tested pin were analysed by AFM, SEM and a nano-indentation tester. The results indicated Hexadecyltrimethoxysilane (HS) modified lanthanum fluoride nanoparticles and HS modified cerium oxide nanoparticles all shown better dispersibility than unmodified lanthanum fluoride nanoparticles and unmodified cerium oxide nanoparticles in liquid paraffin (LP). HS modified lanthanum fluoride nanoparticles and HS modified cerium oxide nanoparticles also have been approved that they can improve the tribological properties of LP significantly under various working conditions. The formation of tribo-films on the worn scar is the key mechanism of friction and wear reduction. On the other hand, surface modified zinc borate submicron particles have not demonstrated great potential as an oil lubricant additive under various working conditions. HS, as a particle surface modifier, could improve the performance of fine-particle oil lubricant additives impressively.