Outline of Design of Deflection Potentiometers, with Notes on the Design of Moving- Coil Galvanometers
Total Page:16
File Type:pdf, Size:1020Kb
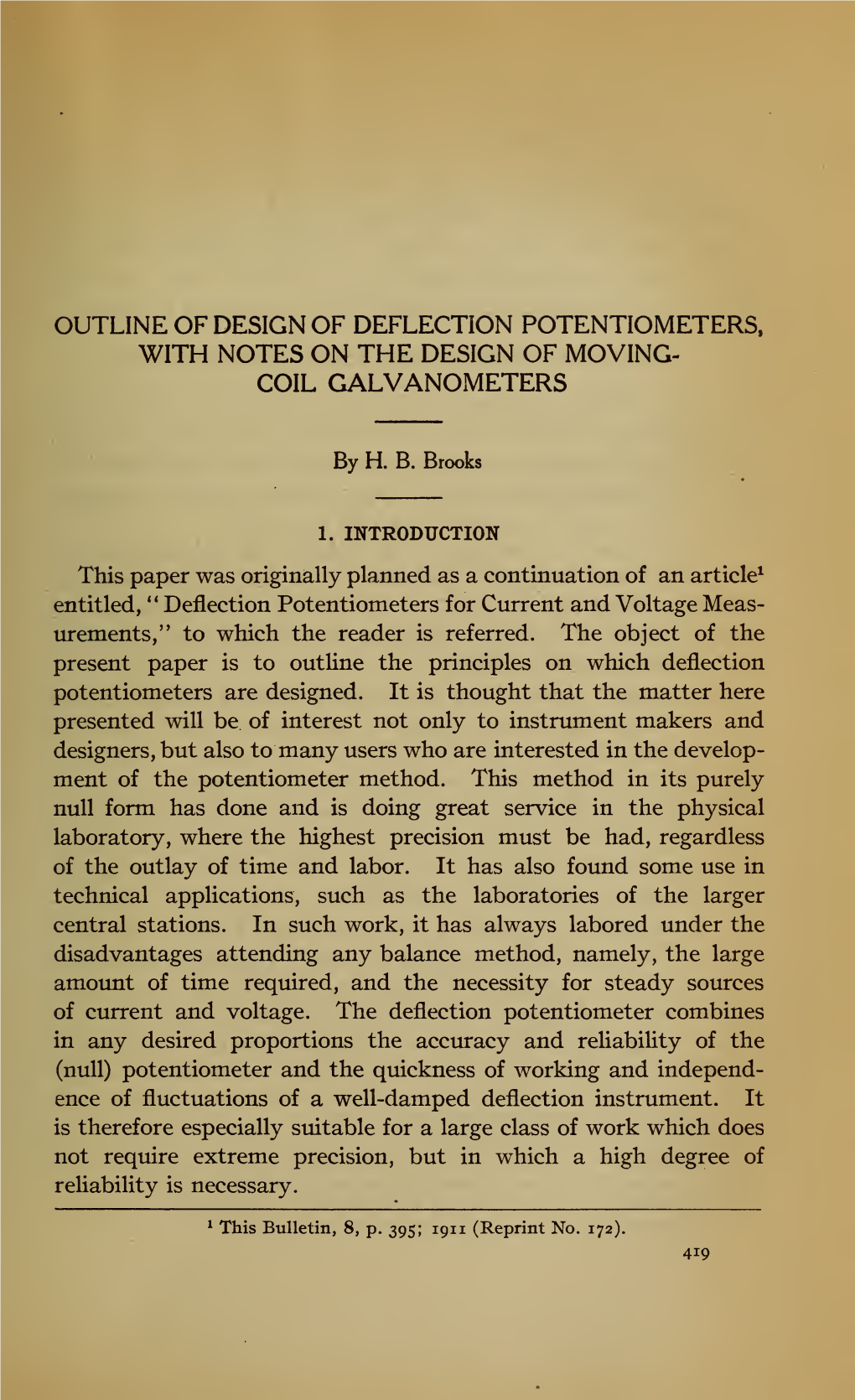
Load more
Recommended publications
-
To Design and Construct the Project Neon Design-Build Project Through a Design-Build Contract
REQUEST FOR PROPOSALS (RFP) RFP Number: 001-15-015 To Design and Construct The Project Neon Design-Build Project through a Design-Build Contract Volume II Contract Appendices 1263 South Stewart Street, Room 101 Carson City, NV 89712 Attention: Mark Stewart Phone: (775) 888-7101 ext. 2124 Fax: (775) 888-7101 Dated as of November 9, 2015 APPENDIX 1 ABBREVIATIONS AND DEFINITIONS [Provided Separately] Nevada Department of Transportation Appendix 1 RFP Number: 001-15-015 Project Neon Design-Build Project Page 1 of 1 Design-Build Contract Appendices Execution Version Abbreviations and Definitions APPENDIX 2 DEPARTMENT-PROVIDED APPROVALS 1. Final Environmental Impact Statement and Section 4(f) Evaluation; I-15 Corridor Improvements and Local Arterial Improvements; Project NEON; Clark County, Las Vegas, Nevada; NDOT Project I.D. 73457E1P; FHWA-NV-EIS-09-01-F (May 28, 2010) 2. Record of Decision; For Environmental Impact Statement and Section 4(f) Evaluation Study; I-15 Corridor Improvements and Local Arterial Improvements; Project NEON; Clark County, Las Vegas, Nevada; NDOT Project I.D. 73457E1P; FHWA-NV-EIS-09- 01-F (October 21, 2010) 3. Environmental Impact Statement Reevaluation (Number 1); Project Name: Project NEON; Project Location: Las Vegas, Clark County (I-15 from Sahara to Spaghetti Bowl) Project Identification Numbers: Nevada Department of Transportation (NDOT) Project ID Number: 73457E1P; FHWA Project ID Number: FHWA-NV-EIS-09-01-F; Document Type and Approval Date: Final Environmental Impact Statement and Section 4(f) Evaluation: May 28, 2010; Record of Decision (ROD): October 21, 2010; Reevaluation: The first reevaluation was approved on August 29, 2012. -
Architectural Thesis
Architectural Thesis A. Master of Architecture Program Architectural Design Thesis Architectural Design Thesis is an independent design research project on a topic selected and developed by the student. Design Thesis is an opportunity for each student in the Master of Architecture or Master of Science in Architecture (Architectural Design Track) to define an individual position with regard to the discipline of architecture. Normally, Design Thesis occurs during the final two semesters of a student’s curriculum at UMSoA, and includes Directed Research (ARC 699) and Final Degree Project (ARC 610). Graduate M.Arch. students are expected to pursue an independent thesis project in their last semester. In exceptional cases and only with the approval of the Program Director, student can pursue an alternative track after completing the thesis preparation course under the direction of selected instructors, including visiting critics if applicable. During the Spring semester preceding their final year, the Program Director will ask students to prepare and submit a well‐defined proposal of their research topic, along with their current portfolio. Research topics are individual, but may be constrained within a proposed ‘meta‐theme’, or by selected topics. Students must prepare a concise 300‐word proposal describing a topic and how it will be investigated. The proposal should introduce the topic and describe its relevance to the field of architecture; it should identify specific questions that will be addressed; and specify the methodology to be used, and explain the appropriateness of the methodology. During the Spring semester preceding the thesis year, students will select a Fall Upper Level Design Studio that best corresponds with their research topic (to be taken in parallel with ARC 699 Directed Research). -
Automated Improvement of Software Architecture Models for Performance and Other Quality Attributes
Automated Improvement of Software Architecture Models for Performance and Other Quality Attributes Zur Erlangung des akademischen Grades eines Doktors der Ingenieurwissenschaften von der Fakultät für Informatik des Karlsruher Instituts für Technologie (KIT) genehmigte Dissertation von Anne Koziolek geb. Martens aus Oldenburg Tag der mündlichen Prüfung: 14.07.2011 Erster Gutachter: Prof. Dr. Ralf Reussner Zweiter Gutachter: Prof. Dr. Andreas Oberweis KIT – Universität des Landes Baden-Württemberg und nationales Forschungszentrum der Helmholtz-Gemeinschaft www.kit.edu Automated Improvement of Software Architecture Models for Performance and Other Quality Attributes PhD thesis to gain the degree “Doktor der Ingenieurwissenschaften” at the Department of Informatics of the Karlsruhe Institute of Technology (KIT) Dissertation by Anne Koziolek neé Martens Oldenburg Day of defence: 14.07.2011 Referees: Prof. Dr. Ralf Reussner Prof. Dr. Andreas Oberweis KIT – University of the State of Baden-Wuerttemberg and National Laboratory of the Helmholtz Association www.kit.edu Contents Abstract xi Zusammenfassung xiii Danksagungen xvii 1. Introduction 1 1.1. Motivation . 1 1.2. Problem . 4 1.3. Existing Solutions . 5 1.4. Contributions . 6 1.5. Outline . 9 I. Foundations and Related Work 11 2. Component-based Software Architectures and Quality 13 2.1. Component-based Software Architecture . 13 2.1.1. Definitions . 13 2.1.2. Component-based Software Development Process . 17 2.2. Quality of Software Architectures . 18 2.2.1. Quality Attributes of Software Architecture . 18 2.2.2. Quantitative Quality Properties . 21 2.3. Modelling Concepts . 24 2.3.1. Models and Metamodels . 24 2.3.2. Essential Meta Object Facility . 26 2.4. Model-based Quality Prediction . -
2014 Comprehensive Plan
2014 Comprehensive Plan 2014 COMPREHENSIVE PLAN City of Cedar Park, Texas Adopted November 20, 2014 Freese and Nichols, Inc. 2711 North Haskell Avenue Suite 3300 Dallas, Texas 75204 [This page intentionally left blank for double-sided printing.] 2014 Comprehensive Plan Acknowledgements Committee members and staff members provided knowledge, assistance, and insight throughout the process of developing this plan. The contributions of the following people are appreciated and helped to make this planning process and document possible: The Citizens of Cedar Park Current City Council (sworn in May 22, 2014) Matt Powell Stephen Thomas, Place 1 Mayor Corbin Van Arsdale, Place 2 Lyle Grimes, Place 3 Jon Lux, Place 5 Lowell Moore, Place 4 Mayor Pro-Tem Don Tracy, Place 6 Previous City Council Matt Powell Stephen Thomas, Place 1 Mayor Mitch Fuller, Place 2 Lyle Grimes, Place 3 Don Tracy, Place 6 Lowell Moore, Place 4 Mayor Pro-Tem Jon Lux, Place 5 Planning & Zoning Commission Scott Rogers, Place 1 Nicholas Kauffman, Place 5 Gregory Merrell, Place 2 Holly Hogue, Place 6 Kevin Harris, Place 3, Vice Chair Kelly Brent, Place 7, Secretary Audrey Wernecke, Place 4, Chair Comprehensive Plan Advisory Committee (CPAC) Danny Bell, Business Owner James Maness, HOA Representative Kelly Brent, P&Z Commissioner Tony Moline, Chamber of Commerce Linda Haywood, ACC Lowell Moore, City Council Trey Hensley, HOA Representative Matt Powell, Mayor Mo Jahadi, Business Owner Will Streit, LISD Bob Ingraham, 4A Board Don Tracy, City Council Doug James, Non-Profit Ed Trevis, -
Design Guidelines
City of Seattle WSBLE Design Guidelines Seattle Design Commission 1.07.2021 The last time we met… 1. Using Design Tools in “interim” to inform design decisions during EIS process 2. Sub-committee on Evaluation Tools 3. Continue to develop design goals, with a focus on sustainability, art, and equity PRESENTATION OUTLINE 1) Design Guideline Development 2) Recap: Evaluation Tools Sub-Committee Meeting 3) Draft Design Goals 4) Draft Outline of Design Guideline Sections 5) Next Steps 1Guideline Development PROCESS & MILESTONES • Ongoing Co-Planning • Meeting series focused on sharing information and development of Design Tools • Internal Coordination • Developing Guidelines in coordination with development • Upcoming DG Milestones ONLINE WORKSHOPS • Series of online workshops and surveys for City’s Board & Commissions • Equity • Sustainability • Art • Special Structures • Taking place Q1 2021 • Will inform Goals, Fundamentals, and all Design Guidelines 2Evaluation Tools PROMPTS – Sample EVALUATION TOOL - Sample SDC Sub-Committee Meeting • Consider prioritizing different guidelines at different phases • Community prioritization of guidelines • Integrate community input, values, and priorities • Tool to be used mainly by COS Staff, resulting in Staff Report 3Design Goals DESIGN GUIDELINES IN CONTEXT The Design Guidelines help implement the City’s ST3 vision, guiding principles, and objectives. DOCUMENT ORGANIZATION INTRODUCTION GUIDELINES DESIGN RESPONSE & EVALUATION Background A. Context Analysis Prompts & Response Purpose B. Design Fundamentals -
Outline of Design Prosecution in Japan
OUTLINE OF DESIGN PROSECUTION IN JAPAN 1. Protectable Designs ············································································· 1 2. Application ························································································· 3 3. Registration Requirements ···································································· 5 4. Related design system (Article 10) ·························································· 6 5. Substantive Examination······································································· 6 6. International Registration of Industrial Designs under Hague Agreement ········ 7 7. Invalidation Trial ·················································································· 8 For further information, please contact: SHIN-TOKYO BUILDING 3-1, MARUNOUCHI 3-CHOME CHIYODA-KU, TOKYO 100-8355 JAPAN TELEPHONE: 81-3-3211-8741 FACSIMILE: 81-3-3214-6358 81-3-3214-6359 E-MAIL: [email protected] www.nakapat.gr.jp PATENT, TRADEMARK, COPYRIGHT, UNFAIR COMPETITION LAW, LICENSING, CORPORATE AND INTERNATIONAL TRADE MATTERS AND LITIGATION ○C NAKAMURA & PARTNERS, 2021 1. Protectable Designs Under the Japanese Design Act, (1) Article Design, (2) Graphic Image Design, and (3) Building Design can be registered for protection. Additionally, by combining these designs, (4) Design for A Set of Articles, and (5) Interior Design can be also registered for protection. Each design can be registered as a partial design or an entire design. (1) Article Design (Article 2) Articles subject to the Design Act are tangible -
Request for Qualifications for Design-Build Services Rfq #2021-002
REQUEST FOR QUALIFICATIONS FOR DESIGN-BUILD SERVICES RFQ #2021-002 Design-Builder for Medina County Park District H2Ohio Kennard Road Restoration Project Medina County Park District 6364 Deerview Lane Medina, Ohio 44256 Issue Date: June 29, 2021 Due Date: July 27, 2021 1 Medina County Park District History, Mission, and Core Values Medina County Park District (MCPD) was formed on April 19, 1965 under Ohio Revised Code Chapter 1545. The district's boundaries include all of Medina County except Hinckley Township. After the park district was established, a statement of purpose was formulated: "Medina County Park District seeks to enhance the quality of all life through education, conservation, and the protection of natural resources." Since its formation, the park district has acquired and developed land in areas throughout the county. Emphasis has been placed on acquiring land for open space preservation and preservation of unique natural resources. Medina County Park District currently manages more than 7,200 acres. The park district is governed by a three-person board of commissioners that is appointed by the Medina County Probate Judge. Commissioners serve without compensation. The board appoints the director, who oversees day-to-day operations. Residents of the county support the park district through a one-mill property tax. These monies are used to purchase land for the preservation of wildlife and natural resources, to fund the development of park facilities, and to facilitate day-to-day operations of the district. Medina County Park District offers services and facilities without discrimination. Core Values Medina County Park District employees and volunteers are expected to share these values: INTEGRITY: We uphold the highest standards and ethical principles, demonstrating honesty in all of our actions. -
Adopted May 19, 2005
Planning, Preservation & Urban Design Division City Planning & Development Department Kansas City, MO Adopted May 19, 2005 Old Film Row Urban Design Concept Plan Prepared for: City Planning and Development Department Prepared by: Gould Evans Goodman Associates Thanks to Old Film Row, Inc. and Crossroads Community Association who provided their time and input throughout the acknowledgements planning process. The Concept Plan represents the first step to a long-range vision and commitment to future implementation. Success will ultimately be achieved through dedication, communi- cation, and cooperation among the area's stakeholders, various City departments of Kansas City, Missouri, and elected officials. Old Film Row Advisory Committee Chris Accardo Suzie Aron Jeff Becker Ernie Block Mike Burke Shaul Jolles Dan Mieners Brad Nicholson Butch Rigby Jake Schopp Joe Serviss John Shipp Mayor Kay Barnes City Council of Kansas City, Missouri First District Second District Deb Hermann (at-large) Bonnie Sue Cooper (at-large) Bill Skaggs John Fairfield Above: Historical photos of film-indus- Third District Fourth District try employees. Troy Nash (at-large) Jim Glover (at-large) Saundra McFadden-Weaver Jim Rowland Fifth District Sixth District Becky Nace (at-large) Alvin Brooks (at-large) Terry Riley Charles A. Eddy Special thanks to Butch Rigby, Ernie and City Planning and Development Department Marilyn Block, and Jeff Becker who provided their time and spaces for public workshops, Advisory Committee meetings, and the char- Director rette. Robert Langenkamp, AICP Additional thanks to Morgan C. Shaw for permission to use the Old Film Row logo. Division Manager Debra L. Smith, AIA, AICP Historical photos provided by John Shipp and Butch Rigby. -
Design & Access Statement
DESIGN & ACCESS STATEMENT July 2017 For Attleborough Land Ltd and the principal landowners Attleborough Land Ltd CLIENT and the principal landowners Attleborough Land Ltd and the Attleborough Land Ltd and the principal landowners principal landowners (referred to as Attleborough Land Ltd from now on) are 2 Frederic Mews, Kinnerton Street, one of the UK’s leading land promotion companies. They London, SW1X 8EQ currently have over 20,000 houses in planning and recently T. +44 (0)0844 412 8005 obtained planning for 750 houses in Chelmsford, Essex and 1,200 houses in Hethersett, Norwich. Attleborough Land Ltd works with landowners to add value to their land through the planning system and seeks to maximise the value of their land for the benefit of everyone involved. Attleborough Land Ltd has been involved with Attleborough Strategic Urban Extension (SUE) since 2009 and has taken considerable time in preparing a comprehensive outline planning application. Attleborough Land Ltd prides itself on working closely with key local stakeholders such as Breckland Council, Norfolk County Council, Attleborough Town Council and the Attleborough Development Partnership (ADP). Several design workshops and charrettes have been held over the past few years to prepare and propose a development that will complement and enhance the existing town of Attleborough. PAGE II ATTLEBOROUGH - DESIGN & ACCESS STATEMENT CONTACTS / THE TEAM CONSULTANT TEAM JTP - Masterplanners Bidwells - Planners Neil Tully Associates - Landscape CgMs Consulting - Archaeology 23-25 Great Sutton Street, 16 Upper King Street, Norwich, 23-25 Great Sutton Street, 140 London Wall, London EC1V 0DN Norfolk, NR3 1HA London, EC1V 0DN London, EC2Y 5DN T. -
Designing Information Systems: a Pragmatic Account
Designing Information Systems Jonas Sjöström Designing Information Systems A Pragmatic Account Dissertation presented at Uppsala University to be publicly examined in Auditorium Minus, Gustavianum, Uppsala, Monday, October 25, 2010 at 13:15 for the degree of Doctor of Phi- losophy. The examination will be conducted in English. Abstract Sjöström, J. 2010. Designing Information Systems. A pragmatic account. 268 pp. Uppsala. ISBN 978-91-506-2149-5. Information technology (IT) plays an increasingly important role for individuals, organiza- tions, markets, and society as a whole. IT systems are artefacts (human made objects) de- signed for various purposes. Given the multiple-purpose characteristics of computers, such artefacts may, for example, support workflows, perform advanced calculations, support hu- man communication and socialization, enable delivery of services and digital products, facili- tate learning, or simply entertain. The diverging application areas for IT present a challenge to designers who, as a consequence, have to address increasingly divergent design situations. There have been numerous arguments suggesting that the IT artefact has been 'taken for granted', and needs to be understood and conceptualized better within information systems (IS) research. This thesis is based on the pragmatist notion that one important value of IT resides in its potential to support human collaboration. Such a belief has implications for the development of (1) knowledge aimed for action, change and improvement; (2) knowledge about actions, activities and practices; and (3) knowledge through action, experimentation and exploration. A view of the IT artefact is outlined, showing it as part of a social and techno- logical context. IT artefact design is explained in relation to the induction of social change. -
Health Care Design: Current and Potential Research and Development June H
Health Care Design: Current and Potential Research and Development June H. Park Translated by Kate Hunter Introduction Health, no longer an individual’s private matter, but also a precious Downloaded from http://direct.mit.edu/desi/article-pdf/31/1/63/1715390/desi_a_00310.pdf by guest on 30 September 2021 resource in society, can be “designed.” This article investigates the contribution design can make to health care, concentrating primar- ily on the various research and development perspectives that health care design offers in connection with chronic illness. Design and Health Care Reflecting on design in the context of medicine and health care is relatively new. The research project carried out by Bruce Archer in the early 1960s, which eventually led to the “King’s Fund Bed”—a prototype of all modern hospital beds—counts among the first instances of design in medicine. In the meantime, in a wide array of more or less established situations in medical practice, design has made an important difference; this area of specialization is now known as medical design.1 In industrial design, many medi- cal aids and devices have been developed for patients, doctors, and nursing staff, or even as capital goods for hospitals and doctors’ practices. The design of clinics and rehabilitation centers—both their architectural and interior design—makes various contribu- tions to improvements in therapy and care processes. E-Health is an umbrella term for concepts ranging from telediagnostics, tele- monitoring, and e-counseling to efforts to form a network -
BUILD-IT: a Brick-Based Tool for Direct Interaction
M. Fjeld, M. Bichsel & M. Rauterberg (in press): BUILD-IT: a brick-based tool for direct interaction. In D. Harris (ed.) Engineering, Psychology and Cognitive Ergonomics. Vol. 4, Hampshire: Ashgate, pp. 205-212. BUILD-IT: a brick-based tool for direct interaction Morten Fjeld(1), Martin Bichsel(2) (1)Institute for Hygiene and Applied Physiology (IHA) (2)Institute for Design and Construction Methods (IKB) Swiss Federal Institute of Technology (ETH Zurich) Matthias Rauterberg Center for Research on User-System Interaction (IPO) Technical University Eindhoven (TUE) Abstract BUILD-IT is a planning tool based on intuitive computer vision technology, supporting complex planning and configuration tasks. Based on real, tangible bricks as an interaction medium, it represents a new approach to Human Computer Interaction (HCI). It allows a group of people, seated around a table, to move virtual objects using a real brick as a interaction handler. Object manipulation and image display take place within the very same interaction space. Together with the image displayed on the table, a perspective view of the situation is projected on a vertical screen. The system offers all kinds of users access to state-of-the-art computing and visualisation, requiring little computer literacy. It offers a new way of interaction, facilitating team-based evaluation of alternative layouts. Keywords Direct interaction, graspable interface, computer vision, augmented reality 205 M. Fjeld, M. Bichsel & M. Rauterberg (in press): BUILD-IT: a brick-based tool for direct interaction. In D. Harris (ed.) Engineering, Psychology and Cognitive Ergonomics. Vol. 4, Hampshire: Ashgate, pp. 205-212. Introduction Supporting natural behaviour in Human-Computer-Interaction (HCI) is getting increasingly important.