Conceptual Design of an Unloading System for Continuous Tracks
Total Page:16
File Type:pdf, Size:1020Kb
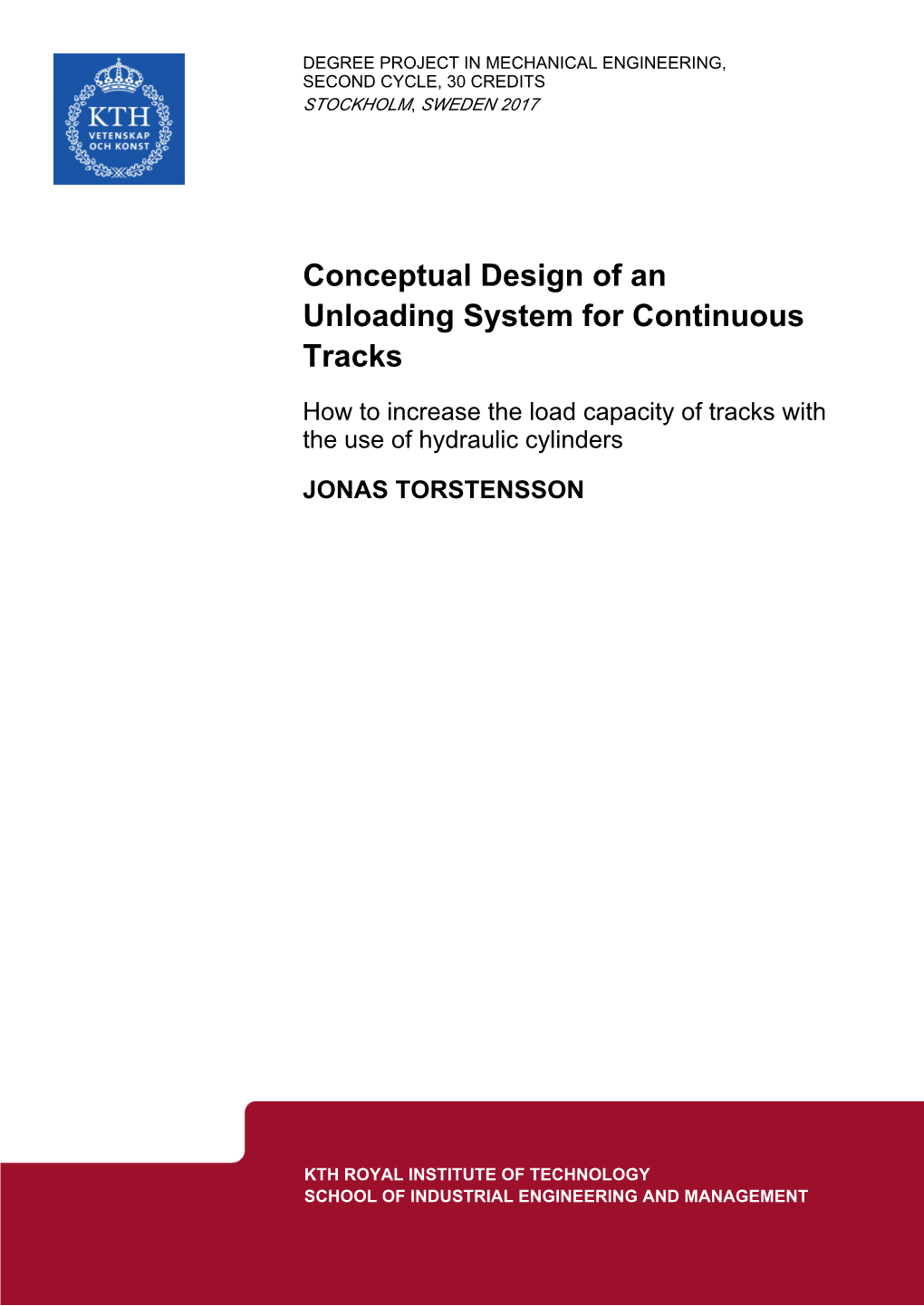
Load more
Recommended publications
-
A Piezoelectric Tracked Vehicle with Potential Application to Planetary Exploration
View metadata, citation and similar papers at core.ac.uk brought to you by CORE provided by Springer - Publisher Connector Article Mechanical Engineering April 2012 Vol.57 No.11: 13391342 doi: 10.1007/s11434-012-5004-7 A piezoelectric tracked vehicle with potential application to planetary exploration JIN JiaMei*, QIAN Fu, YANG Ying, ZHANG JianHui & ZHU KongJun State Key Laboratory of Mechanics and Control of Mechanical Structures, Nanjing University of Aeronautics and Astronautics, Nanjing 210016, China Received October 9, 2011; accepted November 17, 2011 A piezoelectric driving method for rover vehicles is proposed in this paper. Employing this method, a tracked vehicle driven by friction forces from a frame mounted with piezoelectric elements was developed. The vehicle is designed with no driver sprocket, no idler-wheel and no supporting bogie wheels, and the vehicle thus requires no lubrication and has potential application in plan- etary exploration. The frame consists of a pair of piezoelectric transducers. Each transducer comprises four annular parts jointed by beams adhered with piezoelectric ceramics. The tracks are set to the outer surface of the annular parts by means of track ten- sion. Traveling rotating waves are generated by piezoelectric transducers in the annular parts, which generate microscopic ellipti- cal motions at the interface of the tracks. The microscopic elliptical motions from the piezoelectric transducers drive the track vehicle to move. Finite elements analysis was carried out to verify the operation principle using commercial software ANSYS. Piezoelectric transducers were fabricated, assembled and tested to validate the concepts of the proposed rover vehicle and confirm the simulation results. -
An Evaluation of Wheel-Track Systems: Abridged Version for Introduction to Robotics Course Hannah Lyness MSR Thesis Presentation
An Evaluation of Wheel-Track Systems: Abridged Version for Introduction to Robotics Course Hannah Lyness MSR Thesis Presentation Committee: Dimitrios Apostolopoulos (Head), David Wettergreen, Venkat Rajagopalan 1 Presentation Outline . Introduction . Motivation . Research Question . Technology History . A Novel Wheel-Track Design . Prototype Testing . Terramechanics Background . Comparative Evaluation . Conclusion 2 Wheels and Tracks Each Offer Different Advantages Wheels Tracks “HMMWV (Humvee) High-Mobility Multipurpose Wheeled Vehicle, United States of America.” The Global Armoured and Counter-IED Vehicles Market 2011-2021. http://www.army-technology.com/projects/hmmvv/, Jason Fudge. M1A1 Abrams Tank 4th Tank Battalion. Nov. 22, 2008. URL: http://military-photo.blogspot.com/2008/11/m1a1-abrams-tank-4th-tank-battalion.html (visited on 08/13/2016). Introduction 3 Wheels and Tracks Each Offer Different Advantages Wheels Tracks Lower system losses “HMMWV (Humvee) High-Mobility Multipurpose Wheeled Vehicle, United States of America.” The Global Armoured and Counter-IED Vehicles Market 2011-2021. http://www.army-technology.com/projects/hmmvv/, Jason Fudge. M1A1 Abrams Tank 4th Tank Battalion. Nov. 22, 2008. URL: http://military-photo.blogspot.com/2008/11/m1a1-abrams-tank-4th-tank-battalion.html (visited on 08/13/2016). Introduction 3 Wheels and Tracks Each Offer Different Advantages Wheels Tracks Lower system losses Lower acoustic signature Reduced fuel consumption “HMMWV (Humvee) High-Mobility Multipurpose Wheeled Vehicle, United States of America.” The Global Armoured and Counter-IED Vehicles Market 2011-2021. http://www.army-technology.com/projects/hmmvv/, Jason Fudge. M1A1 Abrams Tank 4th Tank Battalion. Nov. 22, 2008. URL: http://military-photo.blogspot.com/2008/11/m1a1-abrams-tank-4th-tank-battalion.html (visited on 08/13/2016). -
Design of a Fully Autonomous Mobile Pipeline Exploration Robot
Louisiana State University LSU Digital Commons LSU Master's Theses Graduate School 2008 Design of a Fully Autonomous Mobile Pipeline Exploration Robot (FAMPER) Jong-Hoon Kim Louisiana State University and Agricultural and Mechanical College, [email protected] Follow this and additional works at: https://digitalcommons.lsu.edu/gradschool_theses Part of the Computer Sciences Commons Recommended Citation Kim, Jong-Hoon, "Design of a Fully Autonomous Mobile Pipeline Exploration Robot (FAMPER)" (2008). LSU Master's Theses. 1284. https://digitalcommons.lsu.edu/gradschool_theses/1284 This Thesis is brought to you for free and open access by the Graduate School at LSU Digital Commons. It has been accepted for inclusion in LSU Master's Theses by an authorized graduate school editor of LSU Digital Commons. For more information, please contact [email protected]. DESIGN OF A FULLY AUTONOMOUS MOBILE PIPELINE EXPLORATION ROBOT (FAMPER) A Thesis Submitted to the Graduate Faculty of the Louisiana State University and Basic Science College in partial fulfillment of the requirements for the degree of Master of Science in System Science in The Department of Computer Science by Jong-Hoon Kim B.E., Seoul National University of Technology in Seoul, South Korea, 2005 December 2008 ACKNOWLEDGEMENTS I am pleased to thank the many people who made this thesis possible. I cannot imagine this thesis without their generous help. I will remember, and appreciate their contributions forever. I would like to deeply thank Dr.Iyengar. He has enhanced my confidence, motivation, and always inspired me. With his support I could complete this thesis. I wish to express sincere thanks to Dr.Ullmer, both for his advice, and also for letting me use the equipments in the Tangviz Lab generously. -
Design and Modelling of a Minimally Actuated Serial Robot Yotam Ayalon, Lior Damti and David Zarrouk
IEEE Robotics and Automation Letters (RAL) paper presented at the 2020 IEEE/RSJ International Conference on Intelligent Robots and Systems (IROS) October 25-29, 2020, Las Vegas, NV, USA (Virtual) Design and Modelling of a Minimally Actuated Serial Robot Yotam Ayalon, Lior Damti and David Zarrouk Abstract—In this paper we present a minimally actuated addressed the planning problem using different optimization overly redundant serial robot (MASR). The robot is composed strategies that have led to substantial advances [24]-[28]. of a planar arm comprised of ten passive rotational joints and a single mobile actuator that travels over the links to reach To simplify the kinematics and actuation, and minimize designated joints and rotate them. The joints remain locked, the dynamic modeling, we suggested in previous works a using a worm gear setup, after the mobile actuator moves to minimally actuated reconfigurable track robot [29], and a another link. A gripper is attached to the mobile actuator thus preliminary design concept serial robot with a mobile allowing it to transport objects along the links to decrease the actuator MASR which travels along the links to rotate the actuation of the joints and the working time. A linear stepper joints [30]. The MASR incorporates multiple characteristics motor is used to control the vertical motion of the robot in 3D and advantages from both minimally actuated robots and space. Along the paper, we present the mechanical design of the hyper redundant robots. The smaller number of motors and robot with 10 passive joints and the automatic actuation of the the simplicity of the design allow for increased reliability, mobile actuator. -
Research in the Intelligence Community in the Age of Artificial
Research Forum Using artificial intelligence in the IDF Computer Service Directorate. Photo: Bamahane website Research in the Intelligence Community in the Age of Artificial Intelligence Shmuel Even and David Siman-Tov By their very nature, intelligence communities are ideal customers for new information technologies. This article addresses two questions: How do new information technologies, primarily artificial intelligence, contribute to the intelligence community’s research activities? What challenges are posed by the assimilation of artificial intelligence in this field? The integration of artificial intelligence in strategic research may provide intelligence agencies with enhanced capabilities in helping leaders understand an emerging reality, detect changes of course early, and manage risks and opportunities. However, the path to achievement of these capabilities is replete with challenges. Keywords: intelligence research, intelligence assessment, war alert, situation assessment, decision making, strategy, artificial intelligence, machine learning Shmuel Even and David Siman-Tov | Research in the Intelligence Community in the Age of Artificial Intellligenc 37 Introduction 2. An artificial system developed in computer Artificial intelligence (AI) is a major evolutionary software, physical hardware, or other context step in the broad field of information that solves tasks requiring human-like technologies. The elements enabling AI perception, cognition, planning, learning, technology applications are the augmentation communication, or physical action. of computerization capabilities, growth in the 3. An artificial system designed to think or volume of information, better algorithms, and act like a human, including cognitive growth in investments (Grimland, 2018). AI-based architectures and neural networks. applications are increasingly integrated in daily 4. A set of techniques, including “machine life, and their impact can be expected to expand learning,” that is designed to approximate and intensify in many spheres (“How to Ensure a cognitive task. -
Continuous Track Design
Proceedings of the 2nd European Conference on Industrial Engineering and Operations Management (IEOM) Paris, France, July 26-27, 2018 Video Game: Continuous Track Design Jason Li San Mateo High School, San Mateo, CA, USA [email protected] Mason Chen Stanford OHS, Palo Alto, CA, USA [email protected] Abstract Have you ever wondered why tanks use the continuous track design instead of just regular wheels? What are the advantages and disadvantages behind this design? This STEM project is to study continuous track design by playing the hill climb racing video game, and applying Minitab statistics to determine the positive and negative aspects of it. The benefit of this project is to research and explore an interesting topic and have fun playing video games at the same time. While doing the project, we will use the Mountain stage in the game, the stage with the most extreme terrain and assess five various cars; Hotrod, Moon lander, Super off-road, tank and hovercraft. Each vehicle has a different wheel design or continuous track design. We will compare their performances based on the distance they can climb on the mountains. Our hypotheses is we want to determine whether there is any measurement repeatability, so that players could duplicate the similar result to prove the playing patterns are less-human dependent. The other objective is to determine whether continuous track design actually is the better wheel design with several merits to overcome the several challenges of the Mountain stage. This paper will combine STEM (Science, Technology, Engineering and Mathematics) in demonstrating the advantages of using the Continuous Track Design. -
Designing a Robotic Platform for Investigating Swarm Robotics
Running head: INVESTIGATING SWARM ROBOTICS 1 Designing a Robotic Platform for Investigating Swarm Robotics Jonathan Gray A Senior Thesis submitted in partial fulfillment of the requirements for graduation in the Honors Program Liberty University Spring 2019 INVESTIGATING SWARM ROBOTICS 2 Acceptance of Senior Honors Thesis This Senior Honors Thesis is accepted in partial fulfillment of the requirements for graduation from the Honors Program of Liberty University. ______________________________ Kyung Bae, Ph.D. Thesis Chair ______________________________ Feng Wang, Ph.D. Committee Member ______________________________ Daniel Majcherek, Ph.D. Committee Member ______________________________ David Schweitzer, Ph.D. Assistant Honors Director ______________________________ Date INVESTIGATING SWARM ROBOTICS 3 Abstract This paper documents the design and subsequent construction of a low-cost, flexible robotic platform for swarm robotics research, and the selection of appropriate swarm algorithms for the implementation of a swarm focused predominantly on target location. The design described herein is intended to allow for the construction of robots large enough to meaningfully interact with their environment while maintaining a low per- robot cost of materials and a low assembly time. The design process is separated into three stages: mechanical design, electrical design, and software design. All major design components are described in detail under the appropriate design section. The BOM for a single robot is also included, along with relevant testing information. INVESTIGATING SWARM ROBOTICS 4 Designing a Robotic Platform for Investigating Swarm Robotics Introduction Introduction to Swarm Intelligence Swarm intelligence is decentralized intelligence – a collective intelligence that arises in a group of similar organisms. Unlike a standard hierarchical control structure, a swarm has no ranks or concepts of authority. -
A Framework for Modeling and Simulation of Tracked Vehicles of High Mobility
2010 NDIA GROUND VEHICLE SYSTEMS ENGINEERING AND TECHNOLOGY SYMPOSIUM MODELING & SIMULATION , TESTING AND VALIDATION (MSTV) MINI -SYMPOSIUM AUGUST 17-19 DEARBORN , MICHIGAN A Framework for Modeling and Simulation of Tracked Vehicles of High Mobility Peilin Song, PhD Pete Melick James Horchner Mobility, Power and Energy Branch AMSAA, APG, MD ABSTRACT This paper presents a modeling and simulation framework for tracked vehicles for ride comfort and load prediction analysis. The development began with the identification of the key issues such as formulations, integration schemes and contact (with friction) modeling on which the comparative studies are conducted. Based on the results of the investigations, the framework and process for the modeling and simulation of tracked vehicles are established and appropriate algorithms for contact and friction are developed. To facilitate the modeling and simulation process, a Python-based modeling environment was developed for process automation, design optimization and design of experiment. The developed framework has been successfully applied to the dynamic load predication of a M1A1 based Joint Assault Bridge (JAB). The parameter optimization enabled with the Python-based process automation tool helps improve the design and modification of vehicles for significantly improved fatigue life of suspension component. INTRODUCTION a virtual test tool for performance prediction and evaluation. A tracked-vehicle is a vehicle that runs on the continuous track instead of wheels. The track Multi-body simulation programs have been used mechanisms in the vehicle rotate the looped tracks in the simulation of tracked vehicles and a certain to provide an endless patch of contact surfaces level of success has been achieved. -
Tracing the Agricultural to the Industrial Revolution
TRACING THE AGRICULTURAL TO THE INDUSTRIAL REVOLUTION. THE URBAN GAME UPON CONCLUSION, YOU WILL HAVE THE FOLLOWING on your town map: 125 houses 20 Tenements 50 factories 10 wealthy homes 5 schools (2 private) 5 jails 9 cemeteries 10 pubs 10 stores 4 hospitals 1 city hall 2 Theaters 1 museum 2 Railroad stations 1 Canal 5 bridges 2 railroads Roads as appropriate 1 3x3 Green Area (common) LET’S GET STARTED! 5 MINUTES With your Black Pencil…. Do the following things on your paper now! 1.Draw a river across your paper connecting east to west; the river should be about 1/2 inch wide. 2.Draw a simple wooden bridge crossing the river. 3.Draw 2 roads one running north to south and crossing the river at the bridge and one running from east to west. Neither road need be a straight line. 4.Draw 10 houses; 1 church; 1 cemetery; 1 store; 1 pub; 1 coalmine; and at least 50 trees!!) ROUND ONE! (blue) It is now 1745. England’s geography is unique in that no section of the country is more than 90 miles from the sea and there are many navigable rivers that crisscross the countryside. An enterprising young Build a canal parallel to the capitalist (you) decides to invest money river. in the construction of a canal. This is not a public venture but rather a private one. With your profits, build a The profits from your canal are nice home anywhere on astonishing! For example, one canal built the map. in 1745; the Oxford Canal yielded a 300% annual return for its investors for a period of more than 30 years. -
2016 IEEE International Conference on Robotics and Automation (ICRA 2016)
2016 IEEE International Conference on Robotics and Automation (ICRA 2016) Stockholm, Sweden 16-21 May 2016 Pages 1-853 IEEE Catalog Number: CFP16RAA-POD ISBN: 978-1-4673-8027-0 1/6 Copyright © 2016 by the Institute of Electrical and Electronics Engineers, Inc All Rights Reserved Copyright and Reprint Permissions: Abstracting is permitted with credit to the source. Libraries are permitted to photocopy beyond the limit of U.S. copyright law for private use of patrons those articles in this volume that carry a code at the bottom of the first page, provided the per-copy fee indicated in the code is paid through Copyright Clearance Center, 222 Rosewood Drive, Danvers, MA 01923. For other copying, reprint or republication permission, write to IEEE Copyrights Manager, IEEE Service Center, 445 Hoes Lane, Piscataway, NJ 08854. All rights reserved. ***This publication is a representation of what appears in the IEEE Digital Libraries. Some format issues inherent in the e-media version may also appear in this print version. IEEE Catalog Number: CFP16RAA-POD ISBN (Print-On-Demand): 978-1-4673-8027-0 ISBN (Online): 978-1-4673-8026-3 ISSN: 1060-0272 Additional Copies of This Publication Are Available From: Curran Associates, Inc 57 Morehouse Lane Red Hook, NY 12571 USA Phone: (845) 758-0400 Fax: (845) 758-2633 E-mail: [email protected] Web: www.proceedings.com TABLE OF CONTENTS EXACT ROBOT NAVIGATION USING POWER DIAGRAMS ...............................................................................................................1 Omur Arslan ; Daniel E. Koditschek GAUSSIAN PROCESS MOTION PLANNING .............................................................................................................................................9 Mustafa Mukadam ; Xinyan Yan ; Byron Boots TOPOLOGICAL TRAJECTORY CLUSTERING WITH RELATIVE PERSISTENT HOMOLOGY ..............................................16 Florian T. -
Design and Manufacture of a Tick Collecting Robot Jeremy Manus Union College - Schenectady, NY
Union College Union | Digital Works Honors Theses Student Work 6-2017 Design and Manufacture Of A Tick Collecting Robot Jeremy Manus Union College - Schenectady, NY Follow this and additional works at: https://digitalworks.union.edu/theses Part of the Mechanical Engineering Commons Recommended Citation Manus, Jeremy, "Design and Manufacture Of A Tick Collecting Robot" (2017). Honors Theses. 57. https://digitalworks.union.edu/theses/57 This Open Access is brought to you for free and open access by the Student Work at Union | Digital Works. It has been accepted for inclusion in Honors Theses by an authorized administrator of Union | Digital Works. For more information, please contact [email protected]. 1 Design and Manufacture Of A Tick Collecting Robot Submitted in partial fulfillment of the requirements for Honors in the Department of Mechanical Engineering ****************************************************************************** Jeremy Manus MER 497 / 498 Union College Advisor: Professor William Keat, PhD 2 ABSTRACT MANUS, JEREMY Design and Manufacture of a Tick Collecting Robot. Department of Mechanical Engineering, June 2017 ADVISOR: Professor William Keat, PhD The overall goal of this research project is to fully design, manufacture, and test a robot for tick collection. The robot will be designed to collect ticks in regions with thickly branched vegetation specifically including shrubs, trees, and leaf liter. The robot will be useful to biologists who collect ticks for research or disease control purposes because it will reach areas that are inaccessible to human-powered collection methods, and thus provide them with a more accurate estimate of the tick density in a given region. Obtaining a more precise tick density is crucial because it provides more detailed information about certain regions and the likelihood of encountering a tick species that transmits a harmful disease. -
Badger Robotic Mining.Indd
Badger Robotic Mining Team 2015-2016 Technical Report¹ Tashi Atruktsang, David Zeugner, James Cho College of Engineering University of Wisconsin-Madison Abstract This report entails the frst-year Badger Robotic Mining Team’s involvement in NASA’s annual Robotic Mining Competition and design choices in constructing our Badger Lunar Excavating Robot (BLER). The team was split into three groups: mechanical, electrical, and software sub teams. The mechanical team explored several mining methods for BLER and settled on a scraper design. All three sub teams worked together to create a functioning robot that successfully met competition qualifcations. Members learned valuable engineering skills such as machining on heavy equipment, computer-aided design, electrical system design, and code. The team will return for NASA’s subsequent mining competition in May 2017 learning from their experiences from the 2016/2017 academic year. Background The Badger Robotic Mining Team competed for its frst year in NASA’s annual Robotic Mining Competition. The team is comprised of members from the student organizations, Badger Ballistics and Wisconsin Robotics. The team built a miner named the Badger Lunar Excavating Robot, or BLER. The primary objective of the competition is to construct a robot that can mine large amounts of lunar soil simulant and deposit it into a bin quickly. The majority of points are awarded for autonomy, optimizing load and capacity, lowering robot power consumption and bandwidth usage. The inspiration behind the competition stems from the abundance of Helium-3 found in the moon’s ground level, which is an effcient fuel for nuclear fusion experiments but is only found in trace quantities on Earth.