Economic and Mechanical Benefits of Utilizing Automatic Balancing and Online Monitoring on Integral Engines and Compressors
Total Page:16
File Type:pdf, Size:1020Kb
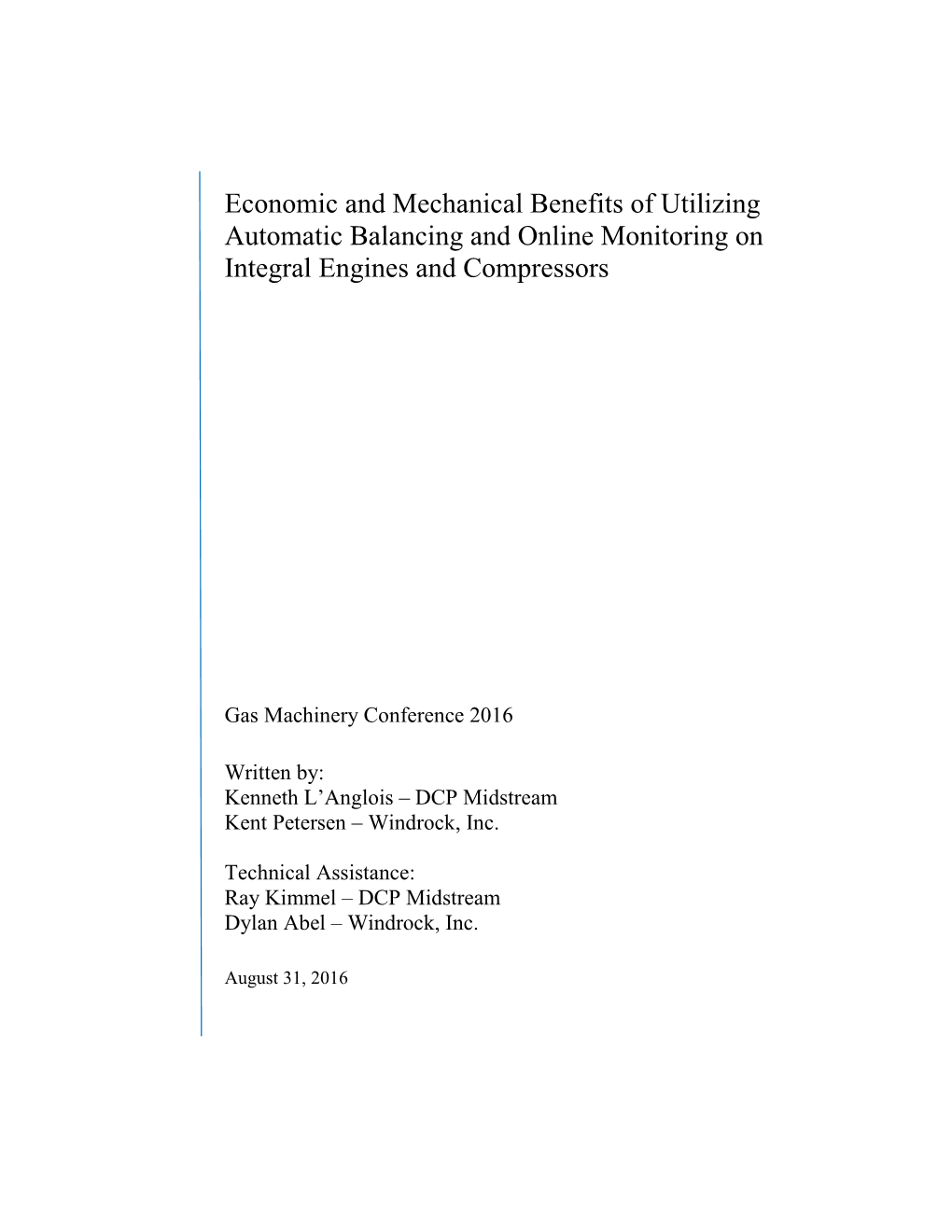
Load more
Recommended publications
-
Some Science of Balance © Tony Foale 2007
Some science of balance © Tony Foale 2007. Readers who started riding before the 1970s, will easily remember the incredible vibration that we used to have to suffer, particularly with British single and twin cylinder machines. In addition to that, we also had to endure quite severe vibration from road shocks generally because of poor suspension. However, with the advent of the Japanese multi-cylinder machines, Lanchester balance shafts and the drive towards better suspension, today we can enjoy a much greater freedom from annoying vibration. In this article, we will only consider the vibration caused by the engine. This vibration has two basic sources, the least severe of which stems from the irregular torque output of reciprocating internal combustion engines. However, the biggest problem is due to the inability to balance inertia forces due to the piston motion in certain types of engine configuration. There can be two sources of mechanical imbalance, they are; rotating and reciprocating. Rotating balance Any rotating object can produce nett rotating forces if not properly balanced. Typical items of concern to us, would be the clutch assembly, alternators, flywheels and crankshaft. These out of balance forces are due to asymmetrical mass distribution about the rotating axis of the object in question. The clutch, alternators and any external flywheels can be fully balanced. However, due to the needs of reciprocating balance, certain configurations of engine, rarely allow us to achieve perfect rotating balance of the crankshaft, single cylinder engines, for example. There are two aspects of rotating balance which need to be considered. These are usually termed static and dynamic. -
Firing Order of 4 Cylinder Engine Pdf
Firing order of 4 cylinder engine pdf Continue IT Stock Free/Polka Dot/Getty Images Building the performance of a four-cylinder engine is much more difficult than building a six- or eight-cylinder engine due to displacement. Larger engines simply transmit more air through the engine, leading to high pure horsepower and torque, thus saying: No substitute to move. However, it is still possible to get decent results with a four-cylinder engine with many techniques used in the motorsport industry. Install a blank and a full catback exhaust system to allow the engine to breathe more freely. The exhaust reserve is very restrictive on four-cylinder engines, and a lot of horsepower can easily be released simply by installing a larger diameter exhaust system. Replace the intake tube and filter with a cold air intake. The system of receiving air in the warehouse is very restrictive; It is designed to limit the amount of noise you hear under the hood. The cold air intake will re-route the intake hose to the front bumper, where colder, denser air will be directed towards the engine. Dense air ultimately means more air in the engine and more power. Install aftermarket camshafts in the engine. Stock consumption and exhaust camshafts are designed for high miles per gallon figure, not for performance, which limits power and torque. After- sales camshafts allow valves to stay open for a longer period of time, allowing more air to enter the engine to increase power. Install high compression pistons in the engine if you plan to keep a naturally aspirated engine. -
DIY Balancing
DIY balancing. I hope that the main articles on the theory behind engine balance have removed the mystic which often surrounds this subject. In fact there is no reason why anyone, with enough mechanical aptitude to assemble an engine, cannot achieve good results with some home grown balancing on certain types of engine. The only equipment necessary being a set of scales and a means of crankshaft support that allows for free low friction rotation. Traditionally, the scales were the balance beam type most often seen in chemistry lessons at school. However, modern electronic scales with digital readout have largely replaced those. Scales with a maximum capacity of 1 kg. and resolution of 1g. will do very well for most motorcycle engine balancing. Generally, one of three methods of supporting the crankshaft is used. 1. Parallel rails. 2. Overlapping rollers. 3. Centres – either in a dedicated holding stand or in a lathe. Parallel rails are illustrated in fig.1. Although simple to make, their alignment is critical. They must be parallel and horizontal in both lateral and longitudinal directions to a high standard. Those shown use a circular profile but best results are obtained with the working surface hardened and ground to a blunt knife edge shape to reduce friction. Rails should only be used with crankshafts that have identical main shaft diameters on each side, otherwise the crank will want to follow a curved path and some extra friction will be introduced. Fig. 1. Using parallel rails to check balance. In this case the rails are circular in section, the inset shows an alternative cross sectional shape preferred by the author, to reduce friction. -
TECHNOLOGY STATUS ASSESSMENT (Revised)
TECHNOLOGY STATUS ASSESSMENT (Revised) Prepared by Gary D. Bourn SwRI Project No. 03.10198 DOE Contract No. DE-FC26-03NT41859 Prepared for U. S. Department of Energy National Energy Technology Laboratory 3610 Collins Ferry Road P.O. Box 880 Morgantown, WV 26507-0880 November 24, 2003 S O U T H W E S T R E S E A R C H I N S T I T U T E® SAN ANTONIO HOUSTON WASHINGTON, DC SOUTHWEST RESEARCH INSTITUTE 6220 Culebra Road San Antonio, Texas 78238 TECHNOLOGY STATUS ASSESSMENT Prepared by Gary D. Bourn SwRI Project No. 03.10198 DOE Contract No. DE-FC26-03NT41859 Prepared for U. S. Department of Energy National Energy Technology Laboratory 3610 Collins Ferry Road P.O. Box 880 Morgantown, WV 26507-0880 November 24, 2003 Approved: signature on original James J. Cole, Acting Director Design and Development Department TABLE OF CONTENTS I. Introduction ..........................................................................................................................1 II. Integral Compressor Engines ..............................................................................................1 III. Compressor Engine Controls...............................................................................................2 A. Mechanical/Pneumatic Control Systems.....................................................................2 B. Global Engine Electronic Controls...............................................................................3 C. Electronic Fuel Injection ..............................................................................................4 -
THERMAL EFFICIENCY", of the Engine
PowerPower FlowFlow andand EfficiencyEfficiency Engine Testing and Instrumentation 1 Efficiencies When the engine converts fuel into power, the process is rather inefficient and only about a quarter of the potential energy in the fuel is released as power at the flywheel. The rest is wasted as heat going down the exhaust and into the air or water. This ratio of actual to potential power is called the "THERMAL EFFICIENCY", of the engine. How much energy reaches the flywheel ( or dynamometer) compared to how much could theoretically be released is a function of three efficiencies, namely: 1. Thermal 2 Mechanical 3. Volumetric Engine Testing and Instrumentation 2 Thermal Efficiency Thermal efficiency can be quoted as either brake or indicated. Indicated efficiency is derived from measurements taken at the flywheel. The thermal efficiency is sometimes called the fuel conversion efficiency, defined as the ratio of the work produced per cycle to the amount of fuel energy supplied per cycle that can be released in the combustion process. Engine Testing and Instrumentation 3 B.S. = Brake Specific Brake Specific Fuel Consumption = mass flow rate of fuel ÷ power output bsHC = Brake Specific Hydrocarbons = mass of hydrocarbons/power output. e.g. 0.21 kg /kW hour Engine Testing and Instrumentation 4 Thermal Efficiency Wc Ps ηt = = m f QHV µ f QHV Wc − work _ per _ cycle Ps − power _ output m f − mass _ of _ fuel _ per _ cycle QHV − heating _ value _ of _ fuel µ f − fuel _ mass _ flow _ rate Specific fuel consumption µ Sfc = f Ps Therefore 1 3600 82.76 ηt = = = Sfc ⋅QHV Sfc(g / kW ⋅hr)QHV (MJ / kg) Sfc Since, QHV for petrol = 43.5 MJ/kg Therefore, the brake thermal efficiency = 82.76/ sfc The indicated thermal efficiency = 82.76 / isfc Engine Testing and Instrumentation 5 Mechanical Efficiency The mechanical efficiency compares the amount of energy imparted to the pistons as mechanical work in the expansion stroke to that which actually reaches the flywheel or dynamometer. -
Dynamic Balance of a Single Cylinder Reciprocating Engine with Optical Access
DYNAMIC BALANCE OF A SINGLE CYLINDER RECIPROCATING ENGINE WITH OPTICAL ACCESS By Trevor W. Ruckle A THESIS Submitted to Michigan State University in partial fulfillment of the requirements for the degree of Mechanical Engineering – Master of Science 2014 ABSTRACT DYNAMIC BALANCE OF A SINGLE CYLINDER RECIPROCATING ENGINE WITH OPTICAL ACCESS By Trevor W. Ruckle The balance within reciprocating engines has always been a concern of engine designers. Any unbalance within an engine can result in component fatigue and failure, excessive vibration, and radiated noise (airborne and structural). When an engine is created with optical access, a Bowditch piston is placed on top a standard piston. This results in the reciprocating mass being significantly greater, and it greatly increases the reciprocating force. The components that affect the balance of the engine were identified and different design aspects within each component that affect the balance were explored. The calculations that were used to calculate static and dynamic balance of the system and how these affect the design of our engine were investigated. Practical techniques were demonstrated to validate the balance of each component after they had been fabricated. Through testing, the first and second order balance effects were analyzed and the harmonic resonances within the system were identified. The interactions between the harmonic resonances and the first and second order forces were also explored. ACKNOWLEDGEMENTS I’d like to take this opportunity to thank the many individuals who have, so graciously, helped me with this research project. I would like to thank Harold Schock for acting as my advisor and supporting me during my master’s program; Dr. -
2003-01-0410 Turbocharging the Chrysler 2.4L Engine
Downloaded from SAE International by Old Dominion Univ, Wednesday, October 19, 2016 SAE TECHNICAL PAPER SERIES 2003-01-0410 Turbocharging the Chrysler 2.4L Engine Garry W. McKissick Jr. and David M. Schmidt DaimlerChrysler Corporation Reprinted From: New SI Engine and Component Design (SP-1747) 2003 SAE World Congress Detroit, Michigan March 3-6, 2003 400 Commonwealth Drive, Warrendale, PA 15096-0001 U.S.A. Tel: (724) 776-4841 Fax: (724) 776-5760 Web: www.sae.org Downloaded from SAE International by Old Dominion Univ, Wednesday, October 19, 2016 All rights reserved. No part of this publication may be reproduced, stored in a retrieval system, or transmitted, in any form or by any means, electronic, mechanical, photocopying, recording, or otherwise, without the prior written permission of SAE. For permission and licensing requests contact: SAE Permissions 400 Commonwealth Drive Warrendale, PA 15096-0001-USA Email: [email protected] Fax: 724-772-4028 Tel: 724-772-4891 For multiple print copies contact: SAE Customer Service Tel: 877-606-7323 (inside USA and Canada) Tel: 724-776-4970 (outside USA) Fax: 724-776-1615 Email: [email protected] ISSN 0148-7191 Copyright © 2003 SAE International Positions and opinions advanced in this paper are those of the author(s) and not necessarily those of SAE. The author is solely responsible for the content of the paper. A process is available by which discussions will be printed with the paper if it is published in SAE Transactions. Persons wishing to submit papers to be considered for presentation or publication by SAE should send the manuscript or a 300 word abstract of a proposed manuscript to: Secretary, Engineering Meetings Board, SAE. -
Internal Combustion Engine
AccessScience from McGraw-Hill Education Page 1 of 15 www.accessscience.com Internal combustion engine Contributed by: Neil MacCoull, Donald L. Anglin Publication year: 2014 A prime mover that burns fuel inside the engine, in contrast to an external combustion engine, such as a steam engine, which burns fuel in a separate furnace. See also: ENGINE . Most internal combustion engines are spark-ignition gasoline-fueled piston engines. These are used in automobiles, light- and medium-duty trucks, motorcycles, motorboats, lawn and garden equipment, and light industrial and portable power applications. Diesel engines are used in automobiles, trucks, buses, tractors, earthmoving equipment, as well as marine, power-generating, and heavier industrial and stationary applications. This article describes these types of engines. For other types of internal combustion engines see GAS TURBINE ; ROCKET PROPULSION ; TURBINE PROPULSION . The aircraft piston engine is fundamentally the same as that used in automobiles but is engineered for light weight and is usually air-cooled. See also: RECIPROCATING AIRCRAFT ENGINE . Engine types Characteristics common to all commercially successful internal combustion engines include (1) the compression of air, (2) the raising of air temperature by the combustion of fuel in this air at its elevated pressure, (3) the extraction of work from the heated air by expansion to the initial pressure, and (4) exhaust. Four-stroke cyc le. William Barnett first drew attention to the theoretical advantages of combustion under compression in 1838. In 1862 Beau de Rochas published a treatise that emphasized the value of combustion under pressure and a high ratio of expansion for fuel economy; he proposed the four-stroke engine cycle as a means of accomplishing these conditions in a piston engine ( Fig. -
Design and Analysis of Ic Engine Enginevalves Using Ansys
DESIGN AND ANALYSIS OF IC ENGINE ENGINEVALVES USING ANSYS 1DUDEKULA HUSSAIN BASHA, 2B.V.AMARNATH REDDY, 3P.HUSSAIN, 4Dr.P.MALLIKARJUNA REDDY 1M.Tech Student, 2Assistant Professor, 3Associate Professor, 4Professor DEPARTMENT OF MECHANICAL ENGINEERING SVR Engineering College, Nandyal ABSTRACT valve that operates without premature failure. In order to develop an exhaust valve with high Exhaust valves with better material strength can thermal and structural strength, experimental provide significant benefits in cost reduction while investigations are often costly and time consuming, also reducing its weight. affecting manufacturing time as well as time-to- Several material studies show that Magnesium market. An alternative approach is to utilize alloy and Nimonic105A are some of the best computational methods such as Finite Element suitable materials for exhaust valves. Modifying Analysis, which provides greater insights on the exhaust valve by varying its position size and temperature distribution across the valve geometry shape and with particular thermal and structural as well as possible deformation due to structural considerations, helps in increasing the rate of heat and thermal stresses. This method significantly transfer from the seat portion of the exhaust valve, shortens the design cycle by reducing the number thereby reducing the possibility of knocking. of physical tests required. Utilizing the Utilizing finite element analysis, exhaust valve computational capability, this research aims to design can be optimized without affecting its identify possible design optimization of the exhaust thermal and structural strength. valve for material and weight reduction, without A study is carried out on exhaust valve affecting the thermal and structural strength.In this with and without air cavity using finite element project we are using single metallic and bi-metallic approach. -
Four Stroke SI Engine
Four Stroke SI Engine Stroke 1: Fuel-air mixture introduced into cylinder through intake valve Stroke 2: Fuel-air mixture compressed Stroke 3: Combustion (~constant volume) occurs and product gases expand doing work Stroke 4: Product gases pushed out of the cylinder through the exhaust valve FUEL A I Ignition R Fuel/Air Mixture Combustion Products Intake Compression Power Exhaust Stroke Stroke Stroke Stroke Spark plug for SI engine Cylinder Fuel injector for CI engine Components Valves Top Clearance Center volume (TC) Cylinder Stroke wall Bottom Center (BC) Piston TC 0o Crank shaft q 270o 90o 180o BC Four-Stroke SI Engine Exhaust gas residual IVO - intake valve opens, IVC – intake valve closes EVO – exhaust valve opens, EVC – exhaust valve opens Xb – burned gas mole fraction Two Stroke SI Engine Exhaust port Fuel-air-oil mixture compressed Check valve Expansion Exhaust Intake (“Scavenging”) Crank shaft Fuel-air-oil mixture Compression Ignition Two-Stroke Scavenging Cross Loop Uniflow Two-Stroke SI Engine EPO – exhaust port open EPC – exhaust port closed IPO – intake port open IPC – intake port closed scavenging Exhaust area Intake area Cylinder Arrangement Single-cylinder engine gives one power stroke per crank revolution (2 stroke) or two revolutions (4 stroke). The torque pulses are widely spaced, and engine vibration and smoothness are significant problems. Used in small engine applications where engine size is more important Multi-cylinder engines spread out the displacement volume amongst multiple smaller cylinders. Increased frequency of power strokes produces smoother torque characteristics. Engine balance (inertia forces associated with accelerating and decelerating piston) better than single cylinder. -
Technical Bulletin 26 Nov 2018
12/6/2018 JTB00667NAS1 - Whine Noise From Engine Balance Shafts | TOPIx JTB00667NAS1 TECHNICAL BULLETIN 26 NOV 2018 © Jaguar Land Rover North America, LLC NOTE: The information in Technical Bulletins is intended for use by trained, professional Technicians with the knowledge, tools, and equipment required to do the job properly and safely. It informs these Technicians of conditions that may occur on some vehicles, or provides information that could assist in proper vehicle service. The procedures should not be performed by 'do-it-yourselfers'. If you are not a Retailer, do not assume that a condition described affects your vehicle. Contact an authorized Jaguar service facility to determine whether this bulletin applies to a specific vehicle. INFORMATION SECTION: 303-01 SUBJECT/CONCERN: Whine Noise From Engine Balance Shafts AFFECTED VEHICLE RANGE: MODEL: MODEL YEAR: VIN: APPLICABILITY: F-PACE (X761) 2017 Onwards 045080 Onwards INGENIUM I4 2.0L Diesel XE (X760) 2017 923882-978627 INGENIUM I4 2.0L Diesel XE (X760) 2017 Onwards P10168 Onwards INGENIUM I4 2.0L Diesel XF (X260) 2017 Onwards Y11889 Onwards INGENIUM I4 2.0L Diesel https://topix.landrover.jlrext.com/topix/content/document/view?id=943461 1/10 12/6/2018 JTB00667NAS1 - Whine Noise From Engine Balance Shafts | TOPIx MARKETS: NORTH AMERICA CONDITION SUMMARY: SITUATION: A whine noise from the engine may be evident. CAUSE: This may be caused by excessive wear on engine dynamic balance shafts. ACTION: Should a customer express this concern, refer to the appropriate Diagnostic Procedure, -
Chapter 6 General Considerations General Considerations Con't
Chapter 6 Engine Design General Considerations The first step in designing a new engine is to choose the desired rated power output and rated speed. The load factor must be considered in choosing the speed. Load Factor = Average Power Output Maximum Power Output General Considerations con’t Engines in tractors, heavy-duty trucks, and other working vehicles have a much higher load factor than automotive engines. An automotive engine typically uses only a small fraction of its maximum available power while cruising at typical speeds on a highway, but may need to accelerate the engine to very high speed and use maximum power for brief periods. 1 General Considerations For example, an automobile engine might produce its maximum power for a brief period while accelerating to 5000 rev/min when the car is passing another vehicle on a two-lane road, but might have a normal load factor of 0.3 while cruising at 2000 rev/min. Conversely, a tractor engine might run at 2000 rev/min with a load factor close to one for long periods of time while pulling an implement in a field. General Considerations con’t After the rated speed and power output are chosen, calculate the engine displacement that would be required to produce the power output at an acceptable pbme level. Experience with other engines has shown the pbme levels of 700 to 900 kPa are reasonable. General Considerations con’t After the engine displacement is chosen, the designer must decide on the number of engine cylinders needed to achieve the required displacement with reasonable piston size.