Electrical Steel (Crgo)
Total Page:16
File Type:pdf, Size:1020Kb
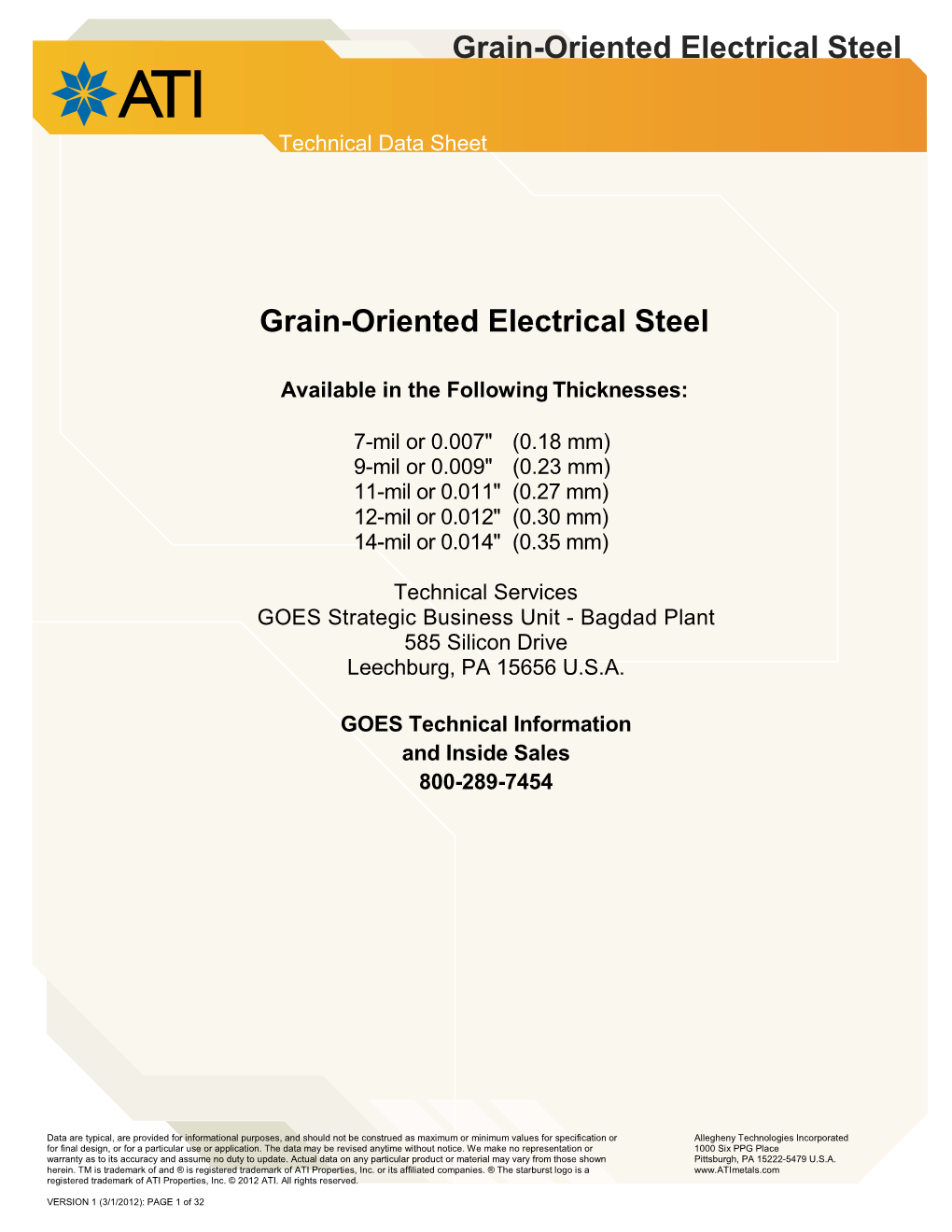
Load more
Recommended publications
-
Grain Oriented Electrical Steel Powercore®
Electrical Steel Grain oriented electrical steel powercore® Product range powercore® is the Content 06 Innovation and cooperation core material for the future 08 Energy: Our expertise 10 Grain oriented electrical steel Grain oriented electrical steel is a highly sophisticated Magnetic properties high-tech core material. It is used in transformers to 14 increase or reduce electrical voltages and currents. That is the only way that electricity can be transported over long distances with as little loss as possible. 16 Insulation types Premium powercore® electrical steel grades significantly reduce noise emissions in transformers, a distinct advan- tage in the light of growing urbanization and industrializa- tion. powercore® electrical steel is so energy-efficient that 18 Characteristics it is now possible to build considerably smaller transfor- mers with the same power output. As energy demand grows continuously, powercore® grain 20 Further processing information oriented electrical steel significantly contribute to protect- ing the environment around the world and to conserving energy resources. General note: All statements as to the properties or utilization of materials and products are for the purposes of description only. Guarantees in respect of the existence of certain properties or utilization of materials are only valid if agreed upon in writing. 06 Innovation and cooperation 07 Mindful of our responsibility at all times. Innovation & We are committed to environmental com- patibility and sustainability in everything we do. From the systematic reuse of water in our production and the use of process gases for our own heating and electrical cooperation generation needs to the resource-conserv- 3 ing utilization of all raw materials and the Developing ideas efficient recyclability of our products. -
Evolution of Power Losses in Bending Rolled Fully Finished NO Electrical Steel Treated Under Unconventional Annealing Conditions
materials Article Evolution of Power Losses in Bending Rolled Fully Finished NO Electrical Steel Treated under Unconventional Annealing Conditions Ivan Petryshynets 1,*, František Kováˇc 1,Ján Füzer 2, Ladislav Falat 1, Viktor Puchý 1 and Peter Kollár 2 1 Institute of Materials Research, Slovak Academy of Sciences, Watsonova 47, 04001 Košice, Slovakia 2 Institute of Physics, Faculty of Science, Pavol Jozef Safarik University, Park Angelinum 9, 041 54 Košice, Slovakia * Correspondence: [email protected]; Tel.: +421-55-792-2442 Received: 19 June 2019; Accepted: 5 July 2019; Published: 8 July 2019 Abstract: Currently, the non-oriented (NO) iron-silicon steels are extensively used as the core materials in various electrical devises due to excellent combination of their mechanical and soft magnetic properties. The present study introduces a fairly innovative technological approach applicable for fully finished NO electrical steel before punching the laminations. It is based on specific mechanical processing by bending and rolling in combination with subsequent annealing under dynamic heating conditions. It has been revealed that the proposed unconventional treatment clearly led to effective improvement of the steel magnetic properties thanks to its beneficial effects involving additional grain growth with appropriate crystallographic orientation and residual stress relief. The philosophy of the proposed processing was based on employing the phenomena of selective grain growth by strain-induced grain boundary migration and a steep temperature gradient through the cross-section of heat treated specimens at dynamic heating conditions. The stored deformation energy necessary for the grain growth was provided by plastic deformation induced within the studied specimens during the bending and rolling process. -
3% Silicon Steel Core Material
3% Silicon Steel Core Material (Grain-Oriented Electrical Steel) datasheet 3% (Grain-Oriented) Silicon Steel is a soft magnetic material that is best used in electrical power transformers and inductors. It has a silicon content up to 3.2 mass %, which increases the electrical resistivity and reduces eddy current losses. The magnetic properties can be enhanced during a cold rolling stage (along the length) to produce textured sheets, known as grain-oriented electrical steel. Due to its preferred crystallographic orientation, it is used primarily for non-rotating applications, i.e. transformers and inductors. Typical operating frequency of 3% Silicon Steel is 50-60 Hz (hertz). A variety of forms can be manufactured, including lamination, toroidal and C-cores, as well as glued block cores of various shapes by cutting or pressing. Date: September 2018 Revision 0.1 © U.S. Department of Energy - National Energy Technology Laboratory 3% Silicon Steel core Fig. 1: 3% silicon core Dimensions Table 1: Core dimensions Description Symbol Finished dimension (mm) Width of core A 180 Height of core B 240 Depth of core (or cast width) D 30 Thickness or build E 50 Width of core window F 80 Height of core window G 140 Minimum Gap width H Fig. 2: Illustration of core dimensions (cut surface to cut surface) Acknowledgement This technical effort was performed in support of the National Energy Technology Laboratory’s ongoing research in DOE’s The Offi ce of Electricity’s (OE) Transformer Resilience and Advanced Components (TRAC) program under the RES contract DE-FE0004000. Disclaimer This project was funded by the Department of Energy, National Energy Technology Laboratory, an agency of the United States Government, through a support contract with AECOM. -
IS 649 (1997): Methods for Testing Steel Sheets for Magnetic Circuits of Power Electrical Apparatus [MTD 4: Wrought Steel Products]
इंटरनेट मानक Disclosure to Promote the Right To Information Whereas the Parliament of India has set out to provide a practical regime of right to information for citizens to secure access to information under the control of public authorities, in order to promote transparency and accountability in the working of every public authority, and whereas the attached publication of the Bureau of Indian Standards is of particular interest to the public, particularly disadvantaged communities and those engaged in the pursuit of education and knowledge, the attached public safety standard is made available to promote the timely dissemination of this information in an accurate manner to the public. “जान का अधकार, जी का अधकार” “परा को छोड न 5 तरफ” Mazdoor Kisan Shakti Sangathan Jawaharlal Nehru “The Right to Information, The Right to Live” “Step Out From the Old to the New” IS 649 (1997): Methods for testing steel sheets for magnetic circuits of power electrical apparatus [MTD 4: Wrought Steel Products] “ान $ एक न भारत का नमण” Satyanarayan Gangaram Pitroda “Invent a New India Using Knowledge” “ान एक ऐसा खजाना > जो कभी चराया नह जा सकताह ै”ै Bhartṛhari—Nītiśatakam “Knowledge is such a treasure which cannot be stolen” IS 649 : 1997 METHODS OF TESTING STEEL SHEETS FOR MAGNETIC CIRCUITS OF POWER ELECTRICAL APPARATUS ( Secod Revision, ) ICS 77.1403); 77.IJO.W; 2O.O-K~.10 BUREAU OF INDIAN STANDARDS h4ANAK BIHAVAN, 9 BAHADUR SHAIH ZAFAR h4ARC; NEW DELHI 1 10002 l’rice Croup 1 1 Wrought Steel Products Sectional Committee MTD 4 FOREWORD This Indian Standard (Second Revision) was adopted by the Bureau of Indian Standards, after the draft finalized by the Wrought Steel Products Sectional Committee had been approved by the Metallurgical Engineering Division Council. -
Altogether More Powerful Non-Oriented Electrical Steel
Altogether more powerful Non-oriented electrical steel www.cogent-power.com ALTOGETHER MORE POWERFUL Cogent Power provides a broad range of high quality products manufactured to customers’ most demanding requirements, and has a responsive approach to the market. Our business Cogent Power is a Tata Steel Enterprise. The These non oriented electrical steels are Cogent Power Inc., in Burlington, Ontario, is a specialist product range from Cogent Electrical principally used for motors, generators, world leader in the design and manufacture of Steels ranges from high permeability grain alternators, small transformers and a variety of transformer cores and components, including oriented steels for power transformers to fully other electromagnetic applications. Thin distributed gap cores, toroidal cores and flat- processed silicon steels for all sizes of rotating gauge materials are also available which offer stacked cores. Cogent Power Inc. also makes machines, including thin gauge materials for the superior performance required for high amorphous cores. Cogent Power Inc. has a high speed machines operating at medium to frequency applications, such as hybrid car high quality slitting operation for electrical high frequencies. motors, flywheels and harmonic filters. The full steels, used to support its own business and product range is marketed worldwide direct or also to supply a range of grades across Electrical steels are manufactured on two sites: through the Tata Steel International global North America. Surahammar Bruks, in Sweden produces non- sales offices. oriented fully processed electrical steels. These steels are iron-silicon alloys with varying silicon Orb Electrical Steels, in the UK is responsible content and have similar magnetic properties for the production and global sales of in all directions in the plane of the sheet. -
Electrical Steel Sheet for Traction Motor of Hybrid/Electrical Vehicles
NIPPON STEEL TECHNICAL REPORT No. 103 MAY 2013 Technical Report UDC 669 . 14 . 018 . 583 : 629 . 113 . 6 Electrical Steel Sheet for Traction Motor of Hybrid/Electrical Vehicles Takeaki WAKISAKA* Satoshi ARAI Yousuke KUROSAKI Abstract 15 years have passed since the first commercial hybrid electric vehicle (HEV) was sold. Meanwhile, the market has been expanding and the type of HEV/EV has been increasing, and then demands to electrical steel sheet for traction motor cores of HEV/EV has become diversified. In this paper, the demands to electrical steel sheet for traction motor cores of HEV/EV are reconfirmed, and then newly developed elec- trical steel sheet and the application techniques of electrical steel sheet are informed. traction motor needs to be not only economical but also compact in 1. Introduction size and light in weight, especially for HEVs that have a compara- Fifteen years have passed since the world’s first production tively small space for the motor (Fig. 1). model hybrid electric vehicle (HEV) was introduced to the market. In order to increase the torque of a motor, it is important to pass Since then the market for HEVs has expanded with HEV models in- a larger driving current through the motor windings and increase the creasing in number. Today, electric vehicles (EVs) and plug-in magnetic flux that interlinks with the windings. For reducing the HEVs are being manufactured on a commercial basis. Compared motor size, the electrical steel sheet used is required to have a high with the conventional gasoline engine, the electric motor has better magnetic flux density. -
Non-Oriented Electrical Steel Sheet and Its Application Technology for the Traction Motors of Hybrid/Electrical Vehicles
NIPPON STEEL TECHNICAL REPORT No. 122 NOVEMBER 2019 Technical Report UDC 629 . 113 . 6 : 669 . 14 . 018 : 583 Non-oriented Electrical Steel Sheet and Its Application Technology for the Traction Motors of Hybrid/Electrical Vehicles Hiroshi FUJIMURA* Ryu HIRAYAMA Kiyoshi WAJIMA Shuichi YAMAZAKI Abstract Non-oriented electrical steel (NO) is widely used as a motor core material since, economi- cally, it meets requirements for high-efficiency, high-power motors. The market for hybrid elec- trical vehicles (HEV) and electrical vehicles (EV) has been expanding and the models of HEV/ EV have been increasing; thus, performance requirements of NO for traction motor cores have diversified. In this paper, we introduce newly developed NOs and its application technology. 1. Introduction cient compared to other types of motors for other applications (refer Vehicles in the 21st century need to be environment friendly. To to Fig. 1). reduce gas emissions that contribute to global warming and improve In order to increase the torque of a motor, it is important to pass fuel efficiency, the hybrid technology to combine an engine and a larger driving current through the motor windings and increase the electric motor was developed, and, in 1997, the world-first mass- magnetic flux that interlinks with the windings. The electrical steel produced hybrid electric vehicles (HEVs) were put on the market. sheet used needs to have high magnetic flux density for a given The mass production of plug-in hybrid electric vehicles (PHEVs) magnetic field intensity, that is to say, high permeability. An effec- and electric vehicles (EVs) whose percentage of electricity use was tive way to increase the magnetic flux is to narrow the clearance be- higher began. -
Physics and Measurements of Magnetic Materials
Physics and measurements of magnetic materials S. Sgobba CERN, Geneva, Switzerland Abstract Magnetic materials, both hard and soft, are used extensively in several components of particle accelerators. Magnetically soft iron–nickel alloys are used as shields for the vacuum chambers of accelerator injection and extraction septa; Fe-based material is widely employed for cores of accelerator and experiment magnets; soft spinel ferrites are used in collimators to damp trapped modes; innovative materials such as amorphous or nanocrystalline core materials are envisaged in transformers for high- frequency polyphase resonant convertors for application to the International Linear Collider (ILC). In the field of fusion, for induction cores of the linac of heavy-ion inertial fusion energy accelerators, based on induction accelerators requiring some 107 kg of magnetic materials, nanocrystalline materials would show the best performance in terms of core losses for magnetization rates as high as 105 T/s to 107 T/s. After a review of the magnetic properties of materials and the different types of magnetic behaviour, this paper deals with metallurgical aspects of magnetism. The influence of the metallurgy and metalworking processes of materials on their microstructure and magnetic properties is studied for different categories of soft magnetic materials relevant for accelerator technology. Their metallurgy is extensively treated. Innovative materials such as iron powder core materials, amorphous and nanocrystalline materials are also studied. A section considers the measurement, both destructive and non-destructive, of magnetic properties. Finally, a section discusses magnetic lag effects. 1 Magnetic properties of materials: types of magnetic behaviour The sense of the word ‘lodestone’ (waystone) as magnetic oxide of iron (magnetite, Fe3O4) is from 1515, while the old name ‘lodestar’ for the pole star, as the star leading the way in navigation, is from 1374. -
Title Here Electricity, Magnetism And… Survival
3/1/2015 Electricity,Title Magnetism Here and… Survival Author Steve Constantinides,Venue Director of Technology Arnold Magnetic TechnologiesDate Corporation March 1, 2015 1 © Arnold Magnetic Technologies [email protected] What we do… Performance materials enabling energy efficiency Magnet Permanent High Precision Thin Production & Magnet Performance Metals Fabrication Assemblies Motors • Specialty Alloys from 0.000069” ~1.75 microns • Rare Earth • Precision • Smaller, Faster, • Sheets, Strips, & Samarium Cobalt Component Hotter motors Coils (RECOMA®) Assembly • Power dense • Milling, Annealing, • Alnico • Tooling, package Coating, Slitting • Injection molded Machining, • High RPM magnet • ARNON® Motor • Flexible Rubber Cutting, Grinding containment Lamination • Balancing • >200°C Operation Material • Sleeving • Light‐weighting Engineering | Consulting | Testing Stabilization & Calibration | Distribution 2 © Arnold Magnetic Technologies 1 3/1/2015 Agenda • Energy and Magnetism • Permanent Magnets and Motors • Applications • Soft magnetic materials • Future of magnetic materials 3 © Arnold Magnetic Technologies Energy in-Efficiency 25.8 65% is waste energy 38.2 60.6% Lost Energy 39.4% “Useful” Delivered Energy Additional losses at end use applications A quad is a unit of energy equal to 1015 (a short-scale quadrillion) BTU, or 1.055 × 1018 joules (1.055 exajoules or EJ) in SI units. 4 © Arnold Magnetic Technologies 2 3/1/2015 Renewable Energy Electricity Generation (USA) U.S. 4.8% of total production CHP= Combined Heat -
Magnetic Properties of Silicon Steel After Plastic Deformation
materials Article Magnetic Properties of Silicon Steel after Plastic Deformation Andries Daem 1,2,*, Peter Sergeant 1,2 , Luc Dupré 1,2, Somsubhro Chaudhuri 1, Vitaliy Bliznuk 1 and Leo Kestens 1 1 Department of Electromechanical, Systems and Metal Engineering, Ghent University, B-9000 Ghent, Belgium; [email protected] (P.S.); [email protected] (L.D.); [email protected] (S.C.); [email protected] (V.B.); [email protected] (L.K.) 2 Flanders Make@UGent, Core Lab EEDT, 9000 Ghent, Belgium * Correspondence: [email protected] Received: 31 August 2020; Accepted: 21 September 2020; Published: 30 September 2020 Abstract: The energy efficiency of electric machines can be improved by optimizing their manufacturing process. During the manufacturing of ferromagnetic cores, silicon steel sheets are cut and stacked. This process introduces large stresses near cutting edges. The steel near cutting edges is in a plastically deformed stress state without external mechanical load. The magnetic properties of the steel in this stress state are investigated using a custom magnetomechanical measurement setup, stress strain measurements, electrical resistance measurements, and transmission electron microscopic (TEM) measurements. Analysis of the core energy losses is done by means of the loss separation technique. The silicon steel used in this paper is non-grain oriented (NGO) steel grade M270-35A. Three differently cut sets of M270-35A are investigated, which differ in the direction they are cut with respect to the rolling direction. The effect of sample deformation was measured—both before and after mechanical load release—on the magnetization curve and total core energy losses. -
Developmental Trajectories in Electrical Steel Technology Using Patent Information
sustainability Article Developmental Trajectories in Electrical Steel Technology Using Patent Information Donghyun You and Hyunseok Park * Department of Information System, Hanyang University, Seoul 04763, Korea; [email protected] * Correspondence: [email protected]; Tel.: +82-2-2220-2396 Received: 20 July 2018; Accepted: 31 July 2018; Published: 2 August 2018 Abstract: Recently there has been growing demand for low-electricity consuming transformers and electric vehicles due to global trend of reducing use of fossil fuels and the role of electrical steel became important. Tracing and analyzing research trend and development of electrical steel will give insight for development of R&D direction and strategies. We used patent citation network and GBFP (Genetic Backward-Forward Path analysis) to identify technological trajectories of electrical steel domain and patent contents with other papers to qualitatively analyze research trend of the domain. As a result, we found that some sub-domains of electrical steel domain had close technological relationship to each other in their developmental paths and suggested further R&D direction in the electrical steel technology. Keywords: electrical steel; classification overlap method; patent citation network; GBFP-based main-path analysis 1. Introduction Electrical steel is soft-magnetic material that has a great magnetic property which is mainly used as material for core of electric devices and machines. Recently there has been growing demand for low-electricity consuming transformers and electric vehicles (EV) due to global trend of reducing use of fossil fuels, and the role of electrical steel became important because it contributes to the improvement in the efficiency of the electric motor of EV [1] and reduction of losses, temperature, energy and costs of transformers [2]. -
Electrical Steel for Motors of Electric and Hybrid Vehicles*
KAWASAKI STEEL TECHNICAL REPORT No. 48 March 2003 Electrical Steel for Motors of Electric and Hybrid Vehicles* Synopsis: Kawasaki Steel has found that there exists suitable electrical steel sheets as core materials depending on motor types such as induction, brushless DC, and reluc- tance motors, through the evaluation of core materials conducted by using several motor test machines. RP and RMA series of high flux density are suitable to induction motors. RMHE series of excellent punchability, low iron Atsuhito Honda Kunihiro Senda Kenichi Sadahiro loss and high density are suitable to brushless DC Dr. Eng., Senior Researcher, Senior Researcher, Senior Researcher, Electrical Steel Lab., Electrical Steel Lab., motors. B coating of self-adhesive type organic coating Electrical Steel Lab., Technical Res. Labs. Technical Res. Labs. was found to be effective to reduce the iron loss and the Technical Res. Labs. noise of motors. 1 Introduction Reluctance Brushless Since the second half of 20th century, the effective motor DC motor IPRM use of energy and environmental protection have been SynRM Low cost considered as the most important issues in the world. IPM SRM SPM The state of California has been especially advanced in dealing with these issues; for example it requires partial Recyclability High efficiency zero emission vehicles (PZEV) to account for at least Motor efficiency luduction 10% of all sales from 2003 onwards. This regulation by motor California has spurred the development of PZEV such Low High as an electric and hybrid vehicles which offer less Low High energy consumption and less pollution. Motor price Motors used for driving or other purposes in an auto- Fig.