Aerodynamics of Winglet: a Computational Fluid Dynamics Study Using Fluent
Total Page:16
File Type:pdf, Size:1020Kb
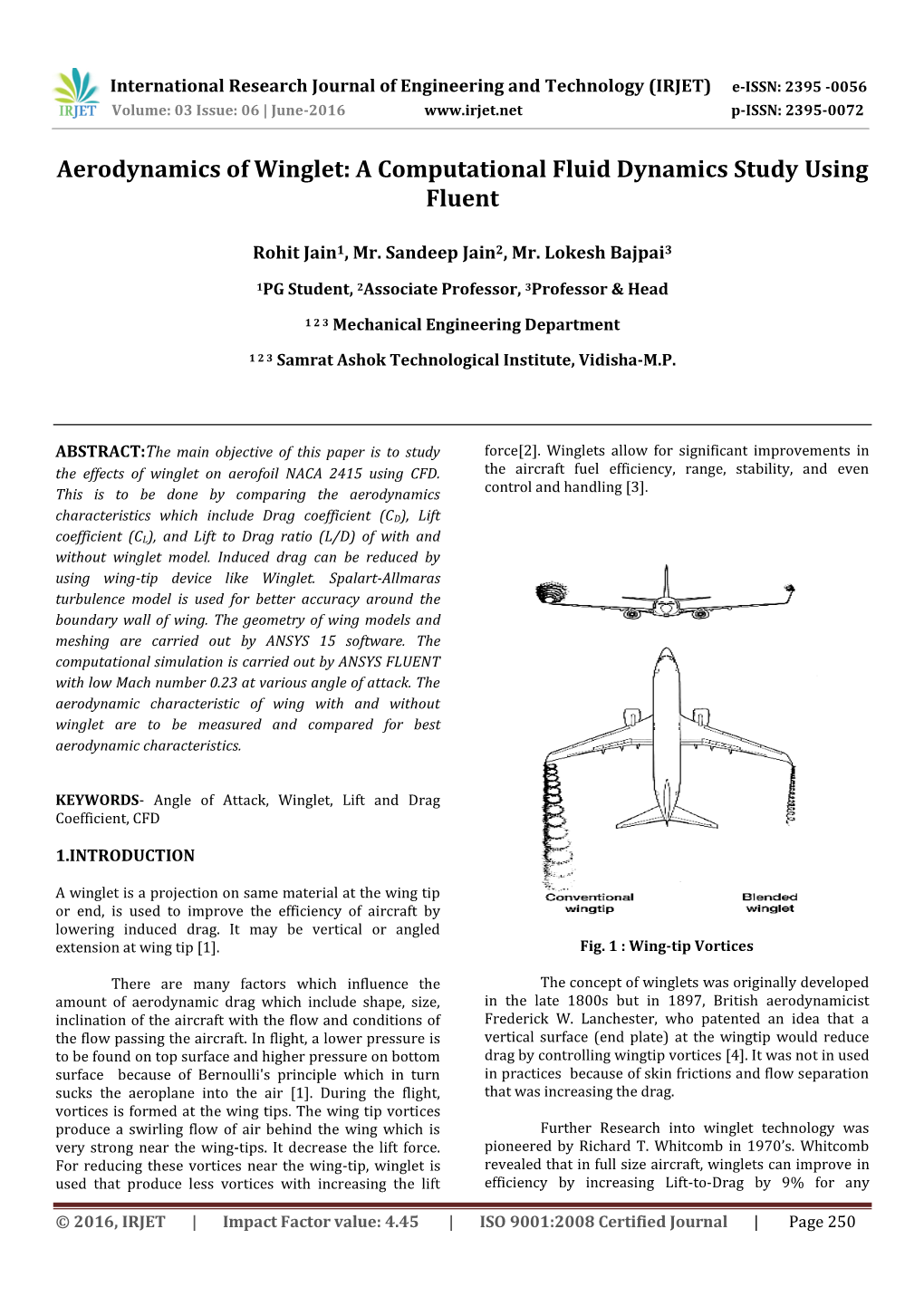
Load more
Recommended publications
-
University of Oklahoma Graduate College Design and Performance Evaluation of a Retractable Wingtip Vortex Reduction Device a Th
UNIVERSITY OF OKLAHOMA GRADUATE COLLEGE DESIGN AND PERFORMANCE EVALUATION OF A RETRACTABLE WINGTIP VORTEX REDUCTION DEVICE A THESIS SUBMITTED TO THE GRADUATE FACULTY In partial fulfillment of the requirements for the Degree of Master of Science Mechanical Engineering By Tausif Jamal Norman, OK 2019 DESIGN AND PERFORMANCE EVALUATION OF A RETRACTABLE WINGTIP VORTEX REDUCTION DEVICE A THESIS APPROVED FOR THE SCHOOL OF AEROSPACE AND MECHANICAL ENGINEERING BY THE COMMITTEE CONSISTING OF Dr. D. Keith Walters, Chair Dr. Hamidreza Shabgard Dr. Prakash Vedula ©Copyright by Tausif Jamal 2019 All Rights Reserved. ABSTRACT As an airfoil achieves lift, the pressure differential at the wingtips trigger the roll up of fluid which results in swirling wakes. This wake is characterized by the presence of strong rotating cylindrical vortices that can persist for miles. Since large aircrafts can generate strong vortices, airports require a minimum separation between two aircrafts to ensure safe take-off and landing. Recently, there have been considerable efforts to address the effects of wingtip vortices such as the categorization of expected wake turbulence for commercial aircrafts to optimize the wait times during take-off and landing. However, apart from the implementation of winglets, there has been little effort to address the issue of wingtip vortices via minimal changes to airfoil design. The primary objective of this study is to evaluate the performance of a newly proposed retractable wingtip vortex reduction device for commercial aircrafts. The proposed design consists of longitudinal slits placed in the streamwise direction near the wingtip to reduce the pressure differential between the pressure and the suction sides. -
Aviation Glossary
AVIATION GLOSSARY 100-hour inspection – A complete inspection of an aircraft operated for hire required after every 100 hours of operation. It is identical to an annual inspection but may be performed by any certified Airframe and Powerplant mechanic. Absolute altitude – The vertical distance of an aircraft above the terrain. AD - See Airworthiness Directive. ADC – See Air Data Computer. ADF - See Automatic Direction Finder. Adverse yaw - A flight condition in which the nose of an aircraft tends to turn away from the intended direction of turn. Aeronautical Information Manual (AIM) – A primary FAA publication whose purpose is to instruct airmen about operating in the National Airspace System of the U.S. A/FD – See Airport/Facility Directory. AHRS – See Attitude Heading Reference System. Ailerons – A primary flight control surface mounted on the trailing edge of an airplane wing, near the tip. AIM – See Aeronautical Information Manual. Air data computer (ADC) – The system that receives and processes pitot pressure, static pressure, and temperature to present precise information in the cockpit such as altitude, indicated airspeed, true airspeed, vertical speed, wind direction and velocity, and air temperature. Airfoil – Any surface designed to obtain a useful reaction, or lift, from air passing over it. Airmen’s Meteorological Information (AIRMET) - Issued to advise pilots of significant weather, but describes conditions with lower intensities than SIGMETs. AIRMET – See Airmen’s Meteorological Information. Airport/Facility Directory (A/FD) – An FAA publication containing information on all airports, seaplane bases and heliports open to the public as well as communications data, navigational facilities and some procedures and special notices. -
Aircraft Winglet Design
DEGREE PROJECT IN VEHICLE ENGINEERING, SECOND CYCLE, 15 CREDITS STOCKHOLM, SWEDEN 2020 Aircraft Winglet Design Increasing the aerodynamic efficiency of a wing HANLIN GONGZHANG ERIC AXTELIUS KTH ROYAL INSTITUTE OF TECHNOLOGY SCHOOL OF ENGINEERING SCIENCES 1 Abstract Aerodynamic drag can be decreased with respect to a wing’s geometry, and wingtip devices, so called winglets, play a vital role in wing design. The focus has been laid on studying the lift and drag forces generated by merging various winglet designs with a constrained aircraft wing. By using computational fluid dynamic (CFD) simulations alongside wind tunnel testing of scaled down 3D-printed models, one can evaluate such forces and determine each respective winglet’s contribution to the total lift and drag forces of the wing. At last, the efficiency of the wing was furtherly determined by evaluating its lift-to-drag ratios with the obtained lift and drag forces. The result from this study showed that the overall efficiency of the wing varied depending on the winglet design, with some designs noticeable more efficient than others according to the CFD-simulations. The shark fin-alike winglet was overall the most efficient design, followed shortly by the famous blended design found in many mid-sized airliners. The worst performing designs were surprisingly the fenced and spiroid designs, which had efficiencies on par with the wing without winglet. 2 Content Abstract 2 Introduction 4 Background 4 1.2 Purpose and structure of the thesis 4 1.3 Literature review 4 Method 9 2.1 Modelling -
Advanced RANS Modeling of Wingtip Vortex Flows
Center for Turbulence Research 73 Proceedings of the Summer Program 2006 Advanced RANS modeling of wingtip vortex flows By A. Revell , G. Iaccarino AND X. Wu y The numerical calculation of the trailing vortex shed from the wingtip of an aircraft has attracted significant attention in recent years. An accurate prediction of the flow over the wing is required to provide the correct initial conditions for the trailing vortex, while careful modeling is also necessary in order to account for the turbulence in the vortex core. As such, recent works have concluded that in order to achieve results of satisfac- tory accuracy, the use of complex turbulence modeling closures and numerical grids of considerable size is an absolute necessity. In Craft et al. (2006) it was proposed that a Reynolds stress-transport model (RSM) should be used, while Duraisamy & Iaccarino (2005) obtained optimal results with a version of the v2 f which was specifically sen- sitised to streamline curvature. The authors report grid requiremen− ts upward of 7 106 grid points, highlighting the substantial numerical cost involved with predicting this×flow. The computations here are reported for the flow over a NACA0012 half-wing with rounded wingtip at an incidence angle of 10◦, as measured by Chow et al. (1997). The primary aim is to assess the performance of a new turbulence modeling scheme which accounts for the stress-strain misalignment effects in a turbulent flow. This three-equation model bridges the gap between popular two equation eddy-viscosity models (EVM) and the seven equations of a RSM. Relative to a RSM, this new approach inherits the stability advantages of an eddy-viscosity scheme, together with a lower computational expense, and it has already been validated for a range of unsteady mean flows (Revell 2006). -
Influence of Aircraft Vortices on Spray Cloud
Journal of the American Mosquito Control Association, 12(2):372_379, 1996 Copyright O 1996 by the American Mosquito Control Association, Inc. INFLUENCE OF AIRCRAFT VORTICESON SPRAY CLOUD BEHAVIOR R. E. MICKLE Atmospheric Environment Service, 4905 Dufferin Street, Downsview, Ontario M3H5T4, Canada ABSTRACT. For small droplet spraying, the spray cloud is initially entrained into the wingtip vortices so that the ultimate fate of the spray is conffolled by the motion of these vortices. In close to 10O aerial sprays, the emitted spray cloud has been mapped using a scanning laser system that displays diffusion and transport of the spray cloud. Results detailing the concentrations within the spray cloud in space and time are given for sprays in parallel and crosswinds. Wind direction is seen to potentially alter the vortex motion and hence the fate of the spray cloud. In crosswind spraying, the vortex behavior associated with the 2 wings is found to differ, which leads to enhanced deposition from the upwind wing and enhanced drift from the downwind wins. INTRODUCTION EXPERIMENTAL METHODS The application of larvicides and adulticides The ARAL (AES Rapid Acquisition Lidar) by aircraft has been an effective mechanism for has been used in 2 experiments to map close to mosquito control. Howevet the benefits of 100 different spray scenarios in a variety of me- spraying are accompanied by the difficulty in teorological conditions (stable and unstable) en- targeting small droplets and by the potential en- compassing light to high winds at cross and par- vironmental impact of applying any chemical allel angles to the flight line. Aircraft used in into the environment in quantities that may be these studies have included a Cessna 188, TBM toxic to nontarget species. -
Wingtip Vortices and Free Shear Layer Interaction in The
WINGTIP VORTICES AND FREE SHEAR LAYER INTERACTION IN THE VICINITY OF MAXIMUM LIFT TO DRAG RATIO LIFT CONDITION Dissertation Submitted to The School of Engineering of the UNIVERSITY OF DAYTON In Partial Fulfillment of the Requirements for The Degree of Doctor of Philosophy in Engineering By Muhammad Omar Memon, M.S. UNIVERSITY OF DAYTON Dayton, Ohio May, 2017 WINGTIP VORTICES AND FREE SHEAR LAYER INTERACTION IN THE VICINITY OF MAXIMUM LIFT TO DRAG RATIO LIFT CONDITION Name: Memon, Muhammad Omar APPROVED BY: _______________________ _______________________ Aaron Altman Markus Rumpfkeil Advisory Committee Chairman Committee Member Professor; Director, Graduate Aerospace Program Associate Professor Mechanical and Aerospace Engineering Mechanical and Aerospace Engineering _______________________ _______________________ Jose Camberos Wiebke S. Diestelkamp Committee Member Committee Member Adjunct Professor Professor & Chair Mechanical and Aerospace Engineering Department of Mathematics _______________________ _______________________ Robert J. Wilkens, PhD., P.E. Eddy M. Rojas, PhD., M.A., P.E. Associate Dean for Research and Innovation Dean, School of Engineering Professor School of Engineering ii © Copyright by Muhammad Omar Memon All rights reserved 2017 iii ABSTRACT WINGTIP VORTICES AND FREE SHEAR LAYER INTERACTION IN THE VICINITY OF MAXIMUM LIFT TO DRAG RATIO LIFT CONDITION Name: Memon, Muhammad Omar University of Dayton Advisor: Dr. Aaron Altman Cost-effective air-travel is something everyone wishes for when it comes to booking flights. The continued and projected increase in commercial air travel advocates for energy efficient airplanes, reduced carbon footprint, and a strong need to accommodate more airplanes into airports. All of these needs are directly affected by the magnitudes of drag these aircraft experience and the nature of their wingtip vortex. -
Trailing Vortex Attenuation Devices
Calhoun: The NPS Institutional Archive Theses and Dissertations Thesis Collection 1985 Trailing vortex attenuation devices. Heffernan, Kenneth G. http://hdl.handle.net/10945/21590 DUDLEY KNOX LIBRARY NAVAL POSTGRADUATE SCHOOL MONTEREY, CALIFORNIA 93^43 NAVAL POSTGRADUATE SCHOOL Monterey, California THESIS TRAILING VORTEX ATTENUATION DEVICES by Kenneth G. Heffernan June 1985 Thesis Advisor: T. Sarpkaya Approved for public release; distribution is unlimited, T223063 Unclassified SECURITY CLASSIFICATION OF THIS PAGE (Whan Data Entered) REPORT READ INSTRUCTIONS DOCUMENTATION PAGE BEFORE COMPLETING FORM 1. REPORT NUMBER 2. GOVT ACCESSION NO. 3. RECIPIENT'S CATALOG NUMBER 4. TITLE (and Subtitle) 5. TYPE OF REPORT A PERIOD COVERED Dual Master's Thesis; Trailing Vortex Attenuation Devices June 1985 S. PERFORMING ORG. REPORT NUMBER 7. AUTHORC»> 8. CONTRACT OR GRANT NUMBERC*.) Kenneth G. Heffernan 9. PERFORMING ORGANIZATION NAME AND AODRESS 10. PROGRAM ELEMENT. PROJECT, TASK AREA & WORK UNIT NUMBERS Naval Postgraduate School Monterey, California 93943 I. CONTROLLING OFFICE NAME AND ADDRESS 12. REPORT DATE June 1985 Naval Postgraduate Schodl 13. NUMBER OF PAGES Monterey, California 93943 109 U. MONITORING AGENCY NAME 4 ADDRESSf/f different from Controlling OHicm) 15. SECURITY CLASS, (ol (his report) Unclassified 15a. DECLASSIFICATION/ DOWNGRADING SCHEDULE 16. DISTRIBUTION ST ATEMEN T (of this Report) Approved for public release; distribution is unlimited. 17. DISTRIBUTION STATEMENT (ol the abstract entered In Block 20, If different from Report) 18. SUPPLEMENTARY NOTES 19. KEY WORDS (Continue on reverse aide It necessary and Identify by block number) Trailing Vortices 20. ABSTRACT fConl/nu» on reverse side It necessary and Identity by block number) Trailing vortices generated by large aircraft pose a serious hazard to other planes. -
WINGTIP VORTICES and AIRPLANE LIFT Flying an Airplane Disturbs the Air
AIAA AEROSPACE M ICRO-LESSON Easily digestible Aerospace Principles revealed for K-12 Students and Educators. These lessons will be sent on a bi-weekly basis and allow grade-level focused learning. - AIAA STEM K-12 Committee. WINGTIP VORTICES AND AIRPLANE LIFT Flying an airplane disturbs the air. The larger the airplane, the larger the disturbance. In this lesson, we discuss the disturbance and what people do about it. Next Generation Science Standards (NGSS): Discipline: Physical Science. Crosscutting Concept: Energy and matter: Flows, cycles, and conservation. Science & Engineering Practice: Developing and using models. GRADES K-2 NGSS: Matter and Its Interactions: Plan and conduct an investigation to describe and classify different kinds of materials by their observable properties. NGSS: Motion and Stability: Forces and Interactions: Plan and conduct an investigation to compare the effects of different strengths or different directions of pushes and pulls on the motion of an object. Up in the sky! It’s a bird! No, it’s a plane! No, it’s a vortex? You have seen birds and know that birds fly. You’ve probably also seen planes, either at airports or flying high in the sky. Maybe you’ve even flown on one yourself. But what about a vortex? Do you know what a tornado is? Have you ever seen one on television? If you’ve seen a picture of a tornado, then you’ve seen an example of a large and powerful vortex. Vortices can be small too, like the little “dust devils” that you might see twirling leaves across a playground, or extremely large, like a hurricane. -
Commercial Aircraft Performance Improvement Using Winglets
Nikola N. Gavrilović Commercial Aircraft Performance Graduate Research Assistant Improvement Using Winglets University of Belgrade Faculty of Mechanical Engineering Aerodynamic drag force breakdown of a typical transport aircraft shows Boško P. Rašuo that lift-induced drag can amount to as much as 40% of total drag at Full Professor cruise conditions and 80-90% of the total drag in take-off configuration. University of Belgrade Faculty of Mechanical Engineering One way of reducing lift-induced drag is by using wing-tip devices. By applying several types of winglets, which are already used on commercial George S. Dulikravich airplanes, we study their influence on aircraft performance. Numerical Full Professor investigation of five configurations of winglets is described and Florida International University preliminary indications of their aerodynamic performance are provided. Department of Mechanical and Materials Engineering, Miami, Florida, USA Moreover, using advanced multi-objective design optimization software an optimal one-parameter winglet configuration was detrmined that Vladimir Parezanović simultaneously minimizes drag and maximizes lift. Researcher Institute PPRIME, CNRS UPR3346 Poitiers, France Keywords: Winglet, Bionics, Computational fluid dynamics, Drag reduction, Lift-induced drag, Optimization 1. INTRODUCTION of soaring birds and their use of tip feathers to control flight, continued on the quest to reduce induced drag The main motivation for using wingtip devices is and improve aircraft performance and further develop reduction of lift-induced drag force. Environmental the concept of winglets in the late 1970s [4]. This issues and rising operational costs have forced industry research provided a fundamental knowledge and design to improve efficiency of commercial air transport and approach required for extremely attractive option to this has led to some innovative developments for improve aerodynamic efficiency of civilian aircraft, reducing lift-induced drag. -
Tangled Quantum Vortices
Tangled quantum vortices Carlo F. Barenghi (http://research.ncl.ac.uk/quantum-fluids/) Carlo F. Barenghi Tangled quantum vortices Warning: vortices will interact ! Wingtip vortices move down (Helmholtz Theorem: Vortex lines move with the fluid) Carlo F. Barenghi Tangled quantum vortices Summary Part 1: quantum vortices • Absolute zero • Quantum fluids, Bose-Einstein condensation • Quantum vortices • Vortex reconnections, friction • Gross-Pitaevskii eq, Vortex Filament models • Vortex ring, Kelvin waves, vortex knots Part 2: quantum turbulence Carlo F. Barenghi Tangled quantum vortices Absolute zero: XVII-XVIII centuries Daniel Bernoulli Guillaume Amontons (1663-1705) (1700-1782) • Amontons measured pressure changes induced by temperature changes. He argued that pressure cannot become negative, so there is a minimum temperature (estimated at -240 C) corresponding to no motion. • Daniel Bernoulli's kinetic theory. Carlo F. Barenghi Tangled quantum vortices Absolute zero: XVIII-XIX century • Side track: Heat is a fluid called caloric Antoine Lavoisier (1743-1794) • Back on track: Thermodynamics Lord Kelvin (1824-1907) Carlo F. Barenghi Tangled quantum vortices Absolute zero: XX century 1908 Liquid helium (K. Onnes) 1911 Superconductivity (K. Onnes) 1924 Bose-Einstein condensation (BEC) (Bose & and Einstein) 1937 Superfluid 4He (Kapitza, Allen & Misener) 1938 Link between BEC and superfludity (F. London) 1940s Two-fluid model (Landau, Tisza) 1950s Vortex lines (Onsager, Feynman, Hall & Vinen) 1970s Superfluid 3He (Lee, Osheroff, & Richardson) 1995 -
The Design and Experimental Optimization of a Wingtip Vortex Turbine for General Aviation Use
Theses - Daytona Beach Dissertations and Theses 4-1997 The Design and Experimental Optimization of a Wingtip Vortex Turbine for General Aviation Use Andrew Roberts Embry-Riddle Aeronautical University - Daytona Beach Follow this and additional works at: https://commons.erau.edu/db-theses Part of the Aerospace Engineering Commons, and the Aviation Commons Scholarly Commons Citation Roberts, Andrew, "The Design and Experimental Optimization of a Wingtip Vortex Turbine for General Aviation Use" (1997). Theses - Daytona Beach. 234. https://commons.erau.edu/db-theses/234 This thesis is brought to you for free and open access by Embry-Riddle Aeronautical University – Daytona Beach at ERAU Scholarly Commons. It has been accepted for inclusion in the Theses - Daytona Beach collection by an authorized administrator of ERAU Scholarly Commons. For more information, please contact [email protected]. THE DESIGN AND EXPERIMENTAL OPTIMIZATION OF A WINGTIP VORTEX TURBINE FOR GENERAL AVIATION USE by Andrew Roberts A Thesis Submitted to the Office of Graduate Programs in Partial Fulfillment of the Requirements for the Degree of Master of Science in Aerospace Engineering Embry-Riddle Aeronautical University Daytona Beach, Florida April 1997 UMI Number: EP31827 INFORMATION TO USERS The quality of this reproduction is dependent upon the quality of the copy submitted. Broken or indistinct print, colored or poor quality illustrations and photographs, print bleed-through, substandard margins, and improper alignment can adversely affect reproduction. In the unlikely event that the author did not send a complete manuscript and there are missing pages, these will be noted. Also, if unauthorized copyright material had to be removed, a note will indicate the deletion. -
Analysis on Reducing the Induced Drag Using the Winglet at the Wingtip
International Journal of Engineering Research & Technology (IJERT) ISSN: 2278-0181 Vol. 2 Issue 12, December - 2013 Analysis on Reducing the Induced Drag Using the Winglet at the Wingtip Alekhya Bojja Parthasarathy Garre Assistant Professor, Associate Professor, Aeronautical Engg Dept, Mechanical Engg Dept, MLR Institute of Technology, MLR Institute of Technology, Affiliated to JNTUH, Hyderabad. Affiliated to JNTUH, Hyderabad. Abstract Fig1: Vortices occurring at the wingtips The winglet reduces the induced drag at the wing tips and increases the lift to drag ratio. Wingtip devices are Wingtip devices are used to improve the efficiency of usually intended to improve the efficiency of fixed-wing fixed-wing aircraft [1]. Winglets can also improve aircraft. The winglet also reduces the fuel usage and aircraft handling characteristics. The wingtip devices increases the single engine performance. This paper increase the lift generated at the wingtip, and reduce the deals with Analysis of reducing the induced drag using lift-induced drag caused by wingtip vortices, improving winglet at the wingtip. We have considered the Boeing lift-to-drag ratio. Winglets improve efficiency by 767 wing and attached the winglet to analyze the diffusing the shed wingtip vortex, which in turn performance. Winglets are mounted on the wing tips as reduces the drag due to lift and improves the wing’s lift the vertical extensions. The comparisons were done to over drag ratio [2]. Winglets increase the effective see the performance of winglet at different angles IJERTofIJERT aspect ratio of a wing without adding greatly to the attack. Wing and winglet are designed in Catia V5 then structural stress and hence necessary weight of its analyzed in Ansys CFX workbench and Fluent to structure.