Let's Re-Engine the Concorde!
Total Page:16
File Type:pdf, Size:1020Kb
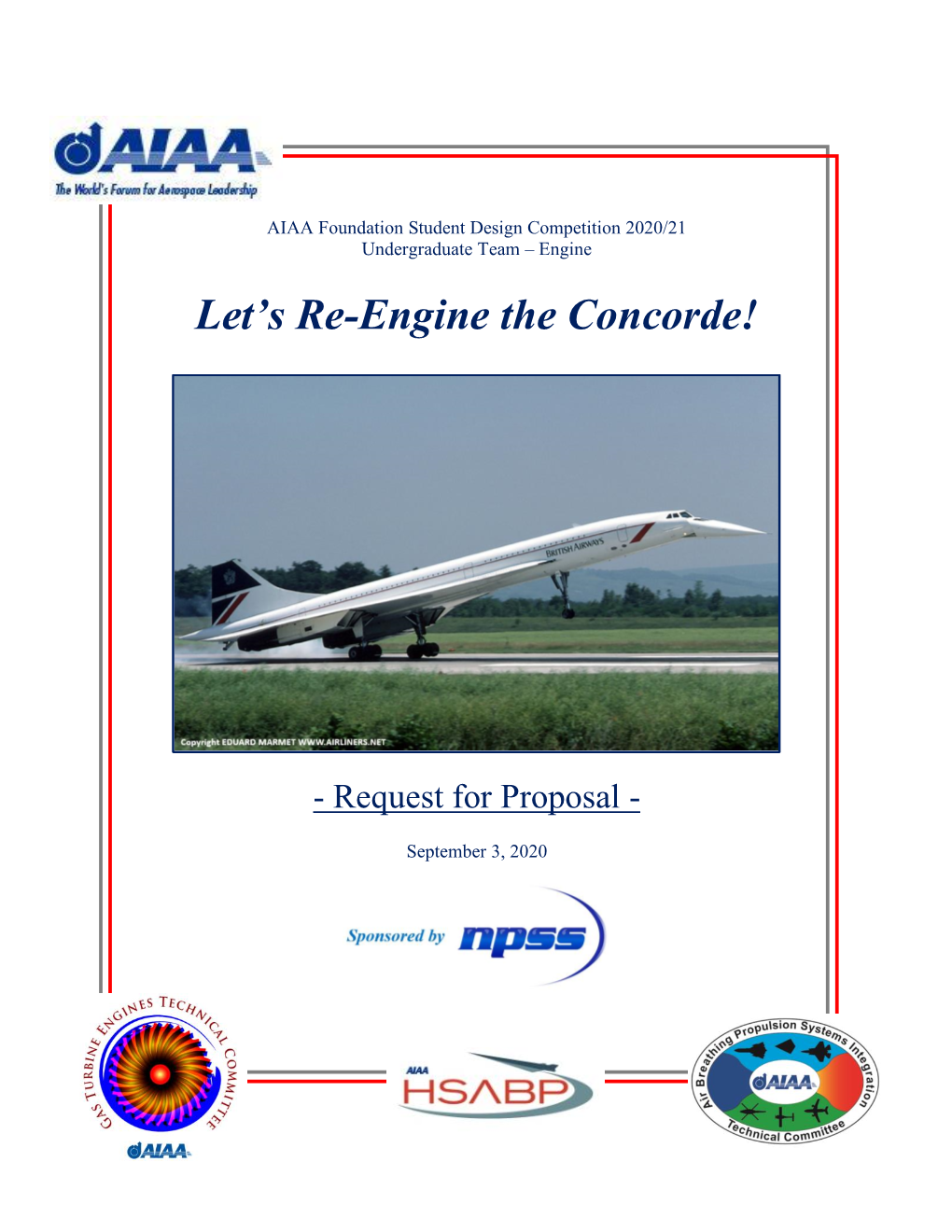
Load more
Recommended publications
-
A Nation of Aviation Pioneers
ICAO TIE-INS By Albert Pelsser Romania - A nation of aviation pioneers At the beginning of the 20th century, Romania was among the few nations in the world which brought essential contributions to aviation and flying because there were people who dedicated their life and work to fulfilling the human desire to fly and developing aviation. Among the most well-known inventors who contributed to the flight development by means of apparatuses heavier than the air, Traian Vuia, Aurel Vlaicu and Henri Coanda played a distinct role. In parallel to the above developments, schools of piloting were established and airships from other countries were purchased, with provision for specially designed workshops for the maintenance and repairing of aircraft. The first school of piloting was initiated by the Romanian lawyer Mihail Cerchez, after his return from Paris in the summer of 1909. It started its activity in the spring of 1910, on the field near Chitila, where the first aerodrome of the Romanian aviation was settled. Once the infrastructure for the construction and repair of the airships had been completed, Mihail Cerchez purchased four aircraft from France: two biplane Farman aircraft that were intended to carrying out the training flights of the future pilots, one Demoiselle aircraft and a Wright aircraft for the ground instruction. Second Lieutenants Ştefan Protopopescu and Gheorghe Negrescu were among the first six military pilots trained. Cerchez also obtained that the Farman aircraft be assembled in his workshops. Chitila’s infrastructure in 1911. Farman IV biplane. Having obtained their Pilot Licences in July 2011, Protopopescu and Negrescu, along with other pilots, participated in military maneuvers on Farmans in the fall of 1911 and carried out a series of raids to popularize aviation among youth and to maintain a high degree of readiness among pilots. -
Concorde Is a Museum Piece, but the Allure of Speed Could Spell Success
CIVIL SUPERSONIC Concorde is a museum piece, but the allure Aerion continues to be the most enduring player, of speed could spell success for one or more and the company’s AS2 design now has three of these projects. engines (originally two), the involvement of Air- bus and an agreement (loose and non-exclusive, by Nigel Moll but signed) with GE Aviation to explore the supply Fourteen years have passed since British Airways of those engines. Spike Aerospace expects to fly a and Air France retired their 13 Concordes, and for subsonic scale model of the design for the S-512 the first time in the history of human flight, air trav- Mach 1.5 business jet this summer, to explore low- elers have had to settle for flying more slowly than speed handling, followed by a manned two-thirds- they used to. But now, more so than at any time scale supersonic demonstrator “one-and-a-half to since Concorde’s thunderous Olympus afterburn- two years from now.” Boom Technology is working ing turbojets fell silent, there are multiple indi- on a 55-seat Mach 2.2 airliner that it plans also to cations of a supersonic revival, and the activity offer as a private SSBJ. NASA and Lockheed Martin appears to be more advanced in the field of busi- are encouraged by their research into reducing the ness jets than in the airliner sector. severity of sonic booms on the surface of the planet. www.ainonline.com © 2017 AIN Publications. All Rights Reserved. For Reprints go to Shaping the boom create what is called an N-wave sonic boom: if The sonic boom produced by a supersonic air- you plot the pressure distribution that you mea- craft has long shaped regulations that prohibit sure on the ground, it looks like the letter N. -
Aerospace Engine Data
AEROSPACE ENGINE DATA Data for some concrete aerospace engines and their craft ................................................................................. 1 Data on rocket-engine types and comparison with large turbofans ................................................................... 1 Data on some large airliner engines ................................................................................................................... 2 Data on other aircraft engines and manufacturers .......................................................................................... 3 In this Appendix common to Aircraft propulsion and Space propulsion, data for thrust, weight, and specific fuel consumption, are presented for some different types of engines (Table 1), with some values of specific impulse and exit speed (Table 2), a plot of Mach number and specific impulse characteristic of different engine types (Fig. 1), and detailed characteristics of some modern turbofan engines, used in large airplanes (Table 3). DATA FOR SOME CONCRETE AEROSPACE ENGINES AND THEIR CRAFT Table 1. Thrust to weight ratio (F/W), for engines and their crafts, at take-off*, specific fuel consumption (TSFC), and initial and final mass of craft (intermediate values appear in [kN] when forces, and in tonnes [t] when masses). Engine Engine TSFC Whole craft Whole craft Whole craft mass, type thrust/weight (g/s)/kN type thrust/weight mini/mfin Trent 900 350/63=5.5 15.5 A380 4×350/5600=0.25 560/330=1.8 cruise 90/63=1.4 cruise 4×90/5000=0.1 CFM56-5A 110/23=4.8 16 -
Critical Mach Number, Transonic Area Rule
Critical Mach number - Compressibility Effects on Lift The design parameter that influences compressibility effects on lift is the Critical Mach number (Mcr). This is the free stream Mach number when sonic conditions (M = 1) is reached at some point on the airfoil surface The figure illustrates the same airfoil, at the same angle of attack at different free stream Mach numbers leading to the definition of the critical Mach number The critical Mach number can be obtained through the curve for the minimum pressure coefficient as a function of Mach number. It can be determined through the intersection of the two equations The lift coefficient correction for compressibility is The figure above illustrates that If you plan to fly at high free stream Mach number, you airfoil should be thin to (a) increase your critical Mach number as this will keep your drag rise small This will also result in lower minimum pressure: Therefore your lift coefficient will decrease Note that the minimum pressure coefficient on thick airfoil is high; this means that the velocity is also correspondingly high. Therefore the critical Mach number is reached for lower value of the free stream Mach number. Swept wing A B-52 Stratofortress showing wing with a large sweepback angle. A swept wing is a wing planform favored for high subsonic jet speeds first investigated in Germany from 1935 onwards until the end of the Second World War. Since the introduction of the MiG-15 and North American F-86 which demonstrated a decisive superiority over the slower first generation of straight-wing jet fighters during the Korean War, swept wings have become almost universal on all but the slowest jets (such as the A- 10). -
The Economics of the UK Aerospace Industry: a Transaction Cost Analysis
The economics of the UK aerospace industry: A transaction cost analysis of defence and civilian firms Ian Jackson PhD Department of Economics and Related Studies University of York 2004 Abstract The primaryaim of this thesisis to assessvertical integration in the UK aerospace industrywith a transactioncost approach. There is an extensivetheoretical and conceptualliterature on transactioncosts, but a relativelack of empiricalwork. This thesisapplies transaction cost economics to the UK aerospaceindustry focusing on the paradigmproblem of the make-or-buydecision and related contract design. It assesses whetherthe transactioncost approachis supported(or rejected)by evidencefrom an originalsurvey of theUK aerospaceindustry. The centralhypothesis is that UK aerospacefirms are likely to makecomponents in- housedue to higherlevels of assetspecificity, uncertainty, complexity, frequency and smallnumbers, which is reflectedin contractdesign. The thesismakes these concepts operational.The empiricalmethodology of the thesisis basedon questionnairesurvey dataand econometric tests using Ordinary Least Squares (OLS) andlogit regressions to analysethe make-or-buy decision and the choiceof contracttype. The resultsfrom this thesisfind limited evidencein supportof the transactioncost approachapplied to the UK aerospaceindustry, in spiteof a bespokedataset. The empiricaltests of verticalintegration for both make-or-buyand contracttype as the dependentvariable yield insufficientevidence to concludethat the transactioncost approachis an appropriateframework -
The Potential of Turboprops to Reduce Fuel Consumption in the Chinese Aviation System
THE POTENTIAL OF TURBOPROPS TO REDUCE FUEL CONSUMPTION IN THE CHINESE AVIATION SYSTEM Megan S. Ryerson, Xin Ge Department of City and Regional Planning Department of Electrical and Systems Engineering University of Pennsylvania [email protected] ICRAT 2014 Agenda • Introduction • Data collection • Turboprops in the current CAS network • Spatial trends for short-haul aviation • Regional jet and turboprop trade space • Turboprops in the future CAS network 2 1. Introduction – Growth of the Chinese Aviation System Number of Airports • The Chinese aviation system is in a period 300 of rapid growth • China’s civil aviation system grew at a rate 250 244 of 17.6%/year, 1980 - 2009 • Number of airports grew from 77 to 166 and annual traffic volume increasing from 3.43 million to 230 million 200 • The Civil Aviation Administration of China 166 (CAAC) maintains a target of 244 airports 150 across the country by 2020 • The CAAC plans for 80% of urban and suburban areas to be within a 100km (62 100 77 miles) of aviation service by 2020 • Plans also include strengthening hub-and- 50 spoke networks across the country to meet the dual goals of improving the competitiveness and efficiency of domestic 0 and international aviation. 1980 2009 2020 (Planned) 3 1. Introduction – Reform of the Chinese Aviation System • Consolidation Strong national hubs + insufficient regional coverage • Regional commuter airlines could fill this gap by partnering with China’s major carriers and serving the second-tier and emerging hubs (Shaw, 2009) 4 1. Introduction – Aircraft of the Short Haul Chinese Aviation System Narrow Body Jet Fuel per seat: 7.9 gal Regional Jet Fuel per seat: 19.0 gal Turboprop Fuel per seat: 4.35 gal 5 1. -
High Pressure Ratio Intercooled Turboprop Study
E AMEICA SOCIEY O MECAICA EGIEES 92-GT-405 4 E. 4 S., ew Yok, .Y. 00 h St hll nt b rpnbl fr ttnt r pnn dvnd In ppr r n d n t tn f th St r f t vn r Stn, r prntd In t pbltn. n rnt nl f th ppr pblhd n n ASME rnl. pr r vlbl fr ASME fr fftn nth ftr th tn. rntd n USA Copyright © 1992 by ASME ig essue aio Iecooe uoo Suy C. OGES Downloaded from http://asmedigitalcollection.asme.org/GT/proceedings-pdf/GT1992/78941/V002T02A028/2401669/v002t02a028-92-gt-405.pdf by guest on 23 September 2021 Sundstrand Power Systems San Diego, CA ASAC NOMENCLATURE High altitude long endurance unmanned aircraft impose KFT Altitude Thousands Feet unique contraints on candidate engine propulsion systems and HP Horsepower types. Piston, rotary and gas turbine engines have been proposed for such special applications. Of prime importance is the HIPIT High Pressure Intercooled Turbine requirement for maximum thermal efficiency (minimum specific Mn Flight Mach Number fuel consumption) with minimum waste heat rejection. Engine weight, although secondary to fuel economy, must be evaluated Mls Inducer Mach Number when comparing various engine candidates. Weight can be Specific Speed (Dimensionless) minimized by either high degrees of turbocharging with the Ns piston and rotary engines, or by the high power density Exponent capabilities of the gas turbine. pps Airflow The design characteristics and features of a conceptual high SFC Specific Fuel Consumption pressure ratio intercooled turboprop are discussed. The intended application would be for long endurance aircraft flying TIT Turbine Inlet Temperature °F at an altitude of 60,000 ft.(18,300 m). -
Some Supersonic Aerodynamics
Some Supersonic Aerodynamics W.H. Mason Configuration Aerodynamics Class Grumman Tribody Concept – from 1978 Company Calendar The Key Topics • Brief history of serious supersonic airplanes – There aren’t many! • The Challenge – L/D, CD0 trends, the sonic boom • Linear theory as a starting point: – Volumetric Drag – Drag Due to Lift • The ac shift and cg control • The Oblique Wing • Aero/Propulsion integration • Some nonlinear aero considerations • The SST development work • Brief review of computational methods • Possible future developments Are “Supersonic Fighters” Really Supersonic? • If your car’s speedometer goes to 120 mph, do you actually go that fast? • The official F-14A supersonic missions (max Mach 2.4) – CAP (Combat Air Patrol) • 150 miles subsonic cruise to station • Loiter • Accel, M = 0.7 to 1.35, then dash 25nm – 4 ½ minutes and 50nm total • Then, head home or to a tanker – DLI (Deck Launch Intercept) • Energy climb to 35K ft., M = 1.5 (4 minutes) • 6 minutes at 1.5 (out 125-130nm) • 2 minutes combat (slows down fast) After 12 minutes, must head home or to a tanker Very few real supersonic airplanes • 1956: the B-58 (L/Dmax = 4.5) – In 1962: Mach 2 for 30 minutes • 1962: the A-12 (SR-71 in ’64) (L/Dmax = 6.6) – 1st supersonic flight, May 4, 1962 – 1st flight to exceed Mach 3, July 20, 1963 • 1964: the XB-70 (L/Dmax = 7.2) – In 1966: flew Mach 3 for 33 minutes • 1968: the TU-144 – 1st flight: Dec. 31, 1968 • 1969: the Concorde (L/Dmax = 7.4) – 1st flight, March 2, 1969 • 1990: the YF-22 and YF-23 (supercruisers) – YF-22: 1st flt. -
Make America Boom Again: How to Bring Back Supersonic Transport,” Eli Dourado and Samuel Hammond Show That It Is Time to Revisit the Ban
MAKE AMERICA BOOM AGAIN How to Bring Back Supersonic Transport _____________________ In 1973, the Federal Aviation Administration (FAA) banned civil supersonic flight over the United States, stymieing the development of a supersonic aviation industry. In “Make America Boom Again: How to Bring Back Supersonic Transport,” Eli Dourado and Samuel Hammond show that it is time to revisit the ban. Better technology—including better materials, engines, and simulation capabilities—mean it is now possible to produce a supersonic jet that is more economical and less noisy than those of the 1970s. It is time to rescind the ban in favor of a more modest and sensible noise standard. BACKGROUND Past studies addressing the ban on supersonic flight have had little effect. However, this paper takes a comprehensive view of the topic, covering the history of supersonic flight, the case for supersonic travel, the problems raised by supersonic flight, and regulatory alternatives to the ban. Dourado and Hammond synthesize the best arguments for rescinding the ban on supersonic flights over land and establish that the ban has had a real impact on the development of supersonic transport. KEY FINDINGS The FAA Should Replace the Ban on Overland Supersonic Flight with a Noise Standard The sonic boom generated by the Concorde and other early supersonic aircraft was very loud, and as a result the FAA banned flights in the United States from going faster than the speed of sound (Mach 1). This ban should be rescinded and replaced with a noise standard. A noise limit of 85–90 A-weighted decibels would be similar to noise standards for lawnmowers, blenders, and motorcy- cles, and would therefore be a reasonable standard during daytime hours. -
The Historical Fuel Efficiency Characteristics of Regional Aircraft from Technological, Operational, and Cost Perspectives
The Historical Fuel Efficiency Characteristics of Regional Aircraft from Technological, Operational, and Cost Perspectives Raffi Babikian, Stephen P. Lukachko and Ian A. Waitz* Department of Aeronautics and Astronautics Massachusetts Institute of Technology 77 Massachusetts Ave., Cambridge, MA 02139 ABSTRACT To develop approaches that effectively reduce aircraft emissions, it is necessary to understand the mechanisms that have enabled historical improvements in aircraft efficiency. This paper focuses on the impact of regional aircraft on the U.S. aviation system and examines the technological, operational and cost characteristics of turboprop and regional jet aircraft. Regional aircraft are 40% to 60% less fuel efficient than their larger narrow- and wide-body counterparts, while regional jets are 10% to 60% less fuel efficient than turboprops. Fuel efficiency differences can be explained largely by differences in aircraft operations, not technology. Direct operating costs per revenue passenger kilometer are 2.5 to 6 times higher for regional aircraft because they operate at lower load factors and perform fewer miles over which to spread fixed costs. Further, despite incurring higher fuel costs, regional jets are shown to have operating costs similar to turboprops when flown over comparable stage lengths. Keywords: Regional aircraft, environment, regional jet, turboprop 1. INTRODUCTION The rapid growth of worldwide air travel has prompted concern about the influence of aviation activities on the environment. Demand for air travel has grown at an average rate of 9.0% per year since 1960 and at approximately 4.5% per year over the last decade (IPCC, 1999; FAA, 2000a). Barring any serious economic downturn or significant policy changes, various * Contact author: 617-253-0218 (phone), 617-258-6093 (fax), [email protected] (email) 1 organizations have estimated future worldwide growth will average 5% annually through at least 2015 (IPCC, 1999; Boeing, 2000; Airbus, 2000). -
2. Afterburners
2. AFTERBURNERS 2.1 Introduction The simple gas turbine cycle can be designed to have good performance characteristics at a particular operating or design point. However, a particu lar engine does not have the capability of producing a good performance for large ranges of thrust, an inflexibility that can lead to problems when the flight program for a particular vehicle is considered. For example, many airplanes require a larger thrust during takeoff and acceleration than they do at a cruise condition. Thus, if the engine is sized for takeoff and has its design point at this condition, the engine will be too large at cruise. The vehicle performance will be penalized at cruise for the poor off-design point operation of the engine components and for the larger weight of the engine. Similar problems arise when supersonic cruise vehicles are considered. The afterburning gas turbine cycle was an early attempt to avoid some of these problems. Afterburners or augmentation devices were first added to aircraft gas turbine engines to increase their thrust during takeoff or brief periods of acceleration and supersonic flight. The devices make use of the fact that, in a gas turbine engine, the maximum gas temperature at the turbine inlet is limited by structural considerations to values less than half the adiabatic flame temperature at the stoichiometric fuel-air ratio. As a result, the gas leaving the turbine contains most of its original concentration of oxygen. This oxygen can be burned with additional fuel in a secondary combustion chamber located downstream of the turbine where temperature constraints are relaxed. -
A Statistical Analysis of Commercial Aviation Accidents 1958-2019
Airbus A Statistical Analysis of Commercial Aviation Accidents 1958-2019 Contents Scope and definitions 02 1.0 2020 & beyond 05 Accidents in 2019 07 2020 & beyond 08 Forecast increase in number of aircraft 2019-2038 09 2.0 Commercial aviation accidents since the advent of the jet age 10 Evolution of the number of flights & accidents 12 Evolution of the yearly accident rate 13 Impact of technology on aviation safety 14 Technology has improved aviation safety 16 Evolution of accident rates by aircraft generation 17 3.0 Commercial aviation accidents over the last 20 years 18 Evolution of the yearly accident rate 20 Ten year moving average of accident rate 21 Accidents by flight phase 22 Distribution of accidents by accident category 24 Evolution of the main accident categories 25 Controlled Flight Into Terrain (CFIT) accident rates 26 Loss Of Control In-flight (LOC-I) accident rates 27 Runway Excursion (RE) accident rates 28 List of tables & graphs 29 A Statistical Analysis of Commercial Aviation Accidents 1958 / 2019 02 Scope and definitions This publication provides Airbus’ a flight in a commercial aircraft annual analysis of aviation accidents, is a low risk activity. with commentary on the year 2019, Since the goal of any review of aviation as well as a review of the history of accidents is to help the industry Commercial Aviation’s safety record. further enhance safety, an analysis This analysis clearly demonstrates of forecasted aviation macro-trends that our industry has achieved huge is also provided. These highlight key improvements in safety over the factors influencing the industry’s last decades.