Growing Plants from SEEDS on Mars for Supporting Human Exploration
Total Page:16
File Type:pdf, Size:1020Kb
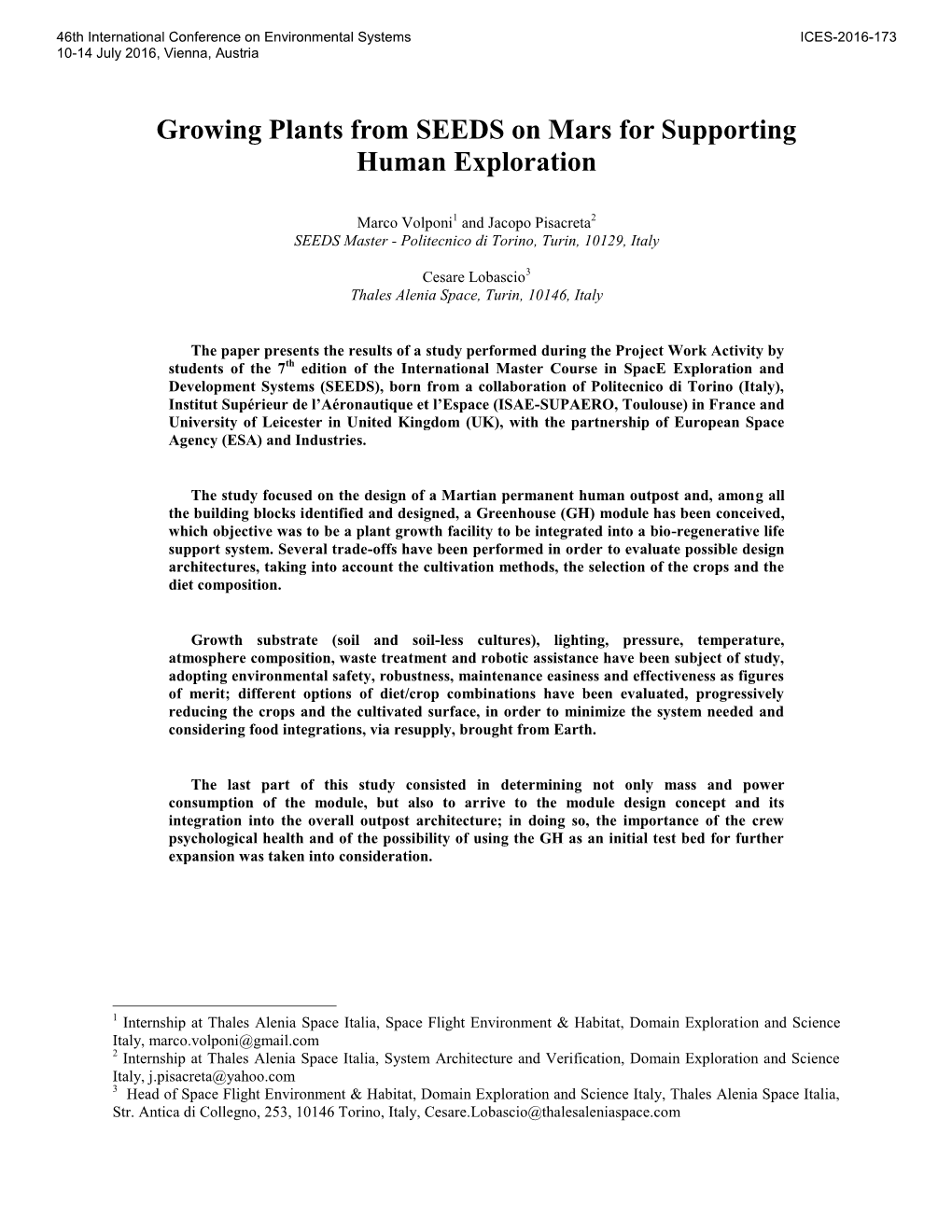
Load more
Recommended publications
-
International Space Exploration Strategy Group International Space Exploration
INTERNATIONAL SPACE EXPLORATION STRATEGY GROUP INTERNATIONAL SPACE EXPLORATION. STRATEGY GROUP ADVANCING THE EXPLORATION FRONTIER For the last forty years, human In recent years multiple reports define exploration in the coming space exploration has made have recommended international decades. significant progress through partners come together for The group will bring together the international collaboration. The strategic planning activities. interests of all human spaceflight Apollo-Soyuz Test Project and However, many national partners, rather than national Shuttle-Mir Programs marked government planning activities interests subject to changing the end of the Space Race, are severely limited in their political influences. and advanced long duration consideration of international This project provides a unique spaceflight. The International partners. Furthermore, opportunity for current and Space Station (ISS) is now in its government and industry recent graduate student second decade as a continuously planners may not have access researchers to collaborate with occupied human outpost in Low- to the latest technologies being others from around the world. Earth Orbit (LEO). While we developed at leading research Most importantly, participants expect productive utilization of institutions around the world. will have the opportunity to ISS through at least 2020, there We believe an international influence the government and is currently no internationally graduate student working group industry decision makers that recognized program for human is well-suited to generate and define future human exploration exploration beyond LEO. communicate the ideas that will strategy. 3 INTERNATIONAL SPACE EXPLORATION. STRATEGY GROUP INTERNATIONAL SPACE EXPLORATION. STRATEGY GROUP LEADERSHIP Edward Crawley is President of the Skolkovo Institute of Science and Technology (Skoltech). -
Planetary Report Report
The PLANETARYPLANETARY REPORT REPORT Volume XXIX Number 1 January/February 2009 Beyond The Moon From The Editor he Internet has transformed the way science is On the Cover: Tdone—even in the realm of “rocket science”— The United States has the opportunity to unify and inspire the and now anyone can make a real contribution, as world’s spacefaring nations to create a future brightened by long as you have the will to give your best. new goals, such as the human exploration of Mars and near- In this issue, you’ll read about a group of amateurs Earth asteroids. Inset: American astronaut Peggy A. Whitson who are helping professional researchers explore and Russian cosmonaut Yuri I. Malenchenko try out training Mars online, encouraged by Mars Exploration versions of Russian Orlan spacesuits. Background: The High Rovers Project Scientist Steve Squyres and Plane- Resolution Camera on Mars Express took this snapshot of tary Society President Jim Bell (who is also head Candor Chasma, a valley in the northern part of Valles of the rovers’ Pancam team.) Marineris, on July 6, 2006. Images: Gagarin Cosmonaut Training This new Internet-enabled fun is not the first, Center. Background: ESA nor will it be the only, way people can participate in planetary exploration. The Planetary Society has been encouraging our members to contribute Background: their minds and energy to science since 1984, A dust storm blurs the sky above a volcanic caldera in this image when the Pallas Project helped to determine the taken by the Mars Color Imager on Mars Reconnaissance Orbiter shape of a main-belt asteroid. -
A Future Mars Environment for Science and Exploration
Planetary Science Vision 2050 Workshop 2017 (LPI Contrib. No. 1989) 8250.pdf A FUTURE MARS ENVIRONMENT FOR SCIENCE AND EXPLORATION. J. L. Green1, J. Hol- lingsworth2, D. Brain3, V. Airapetian4, A. Glocer4, A. Pulkkinen4, C. Dong5 and R. Bamford6 (1NASA HQ, 2ARC, 3U of Colorado, 4GSFC, 5Princeton University, 6Rutherford Appleton Laboratory) Introduction: Today, Mars is an arid and cold world of existing simulation tools that reproduce the physics with a very thin atmosphere that has significant frozen of the processes that model today’s Martian climate. A and underground water resources. The thin atmosphere series of simulations can be used to assess how best to both prevents liquid water from residing permanently largely stop the solar wind stripping of the Martian on its surface and makes it difficult to land missions atmosphere and allow the atmosphere to come to a new since it is not thick enough to completely facilitate a equilibrium. soft landing. In its past, under the influence of a signif- Models hosted at the Coordinated Community icant greenhouse effect, Mars may have had a signifi- Modeling Center (CCMC) are used to simulate a mag- cant water ocean covering perhaps 30% of the northern netic shield, and an artificial magnetosphere, for Mars hemisphere. When Mars lost its protective magneto- by generating a magnetic dipole field at the Mars L1 sphere, three or more billion years ago, the solar wind Lagrange point within an average solar wind environ- was allowed to directly ravish its atmosphere.[1] The ment. The magnetic field will be increased until the lack of a magnetic field, its relatively small mass, and resulting magnetotail of the artificial magnetosphere its atmospheric photochemistry, all would have con- encompasses the entire planet as shown in Figure 1. -
Design of a Human Settlement on Mars Using In-Situ Resources
46th International Conference on Environmental Systems ICES-2016-151 10-14 July 2016, Vienna, Austria Design of a Human Settlement on Mars Using In-Situ Resources Marlies Arnhof1 Vienna University of Technology, Vienna, 1040, Austria Mars provides plenty of raw materials needed to establish a lasting, self-sufficient human colony on its surface. Due to the planet's vast distance from Earth, it is neither possible nor economically reasonable to provide permanent, interplanetary supply. In-situ resource utilization (ISRU) will be necessary to keep the Earth launch burden and mission costs as low as possible, and to provide – apart from propellant and life support – a variety of construction material. However, to include outposts on other planets into the scope of human spaceflight also opens up new psychological and sociological challenges. Crews will live in extreme environments under isolated and confined conditions for much longer periods of time than ever before. Therefore, the design of a Mars habitat requires most careful consideration of physiological as well as psychosocial conditions of living in space. In this design for a Martian settlement, the author proposes that – following preliminary automated exploration – a basic surface base brought from Earth would be set up. Bags of unprocessed Martian regolith would be used to provide additional shielding for the habitat. Once the viability of the base and its production facilities are secured, the settlement would be expanded, using planetary resources. Martian concrete – processed regolith with a polymeric binder – would be used as main in-situ construction material. To provide optimum living and working conditions, the base would respond to the environment and the residents' number and needs, thereby evolving and growing continuously. -
Marathon 2,500 Years Edited by Christopher Carey & Michael Edwards
MARATHON 2,500 YEARS EDITED BY CHRISTOPHER CAREY & MICHAEL EDWARDS INSTITUTE OF CLASSICAL STUDIES SCHOOL OF ADVANCED STUDY UNIVERSITY OF LONDON MARATHON – 2,500 YEARS BULLETIN OF THE INSTITUTE OF CLASSICAL STUDIES SUPPLEMENT 124 DIRECTOR & GENERAL EDITOR: JOHN NORTH DIRECTOR OF PUBLICATIONS: RICHARD SIMPSON MARATHON – 2,500 YEARS PROCEEDINGS OF THE MARATHON CONFERENCE 2010 EDITED BY CHRISTOPHER CAREY & MICHAEL EDWARDS INSTITUTE OF CLASSICAL STUDIES SCHOOL OF ADVANCED STUDY UNIVERSITY OF LONDON 2013 The cover image shows Persian warriors at Ishtar Gate, from before the fourth century BC. Pergamon Museum/Vorderasiatisches Museum, Berlin. Photo Mohammed Shamma (2003). Used under CC‐BY terms. All rights reserved. This PDF edition published in 2019 First published in print in 2013 This book is published under a Creative Commons Attribution-NonCommercial- NoDerivatives (CC-BY-NC-ND 4.0) license. More information regarding CC licenses is available at http://creativecommons.org/licenses/ Available to download free at http://www.humanities-digital-library.org ISBN: 978-1-905670-81-9 (2019 PDF edition) DOI: 10.14296/1019.9781905670819 ISBN: 978-1-905670-52-9 (2013 paperback edition) ©2013 Institute of Classical Studies, University of London The right of contributors to be identified as the authors of the work published here has been asserted by them in accordance with the Copyright, Designs and Patents Act 1988. Designed and typeset at the Institute of Classical Studies TABLE OF CONTENTS Introductory note 1 P. J. Rhodes The battle of Marathon and modern scholarship 3 Christopher Pelling Herodotus’ Marathon 23 Peter Krentz Marathon and the development of the exclusive hoplite phalanx 35 Andrej Petrovic The battle of Marathon in pre-Herodotean sources: on Marathon verse-inscriptions (IG I3 503/504; Seg Lvi 430) 45 V. -
An Economic Analysis of Mars Exploration and Colonization Clayton Knappenberger Depauw University
DePauw University Scholarly and Creative Work from DePauw University Student research Student Work 2015 An Economic Analysis of Mars Exploration and Colonization Clayton Knappenberger DePauw University Follow this and additional works at: http://scholarship.depauw.edu/studentresearch Part of the Economics Commons, and the The unS and the Solar System Commons Recommended Citation Knappenberger, Clayton, "An Economic Analysis of Mars Exploration and Colonization" (2015). Student research. Paper 28. This Thesis is brought to you for free and open access by the Student Work at Scholarly and Creative Work from DePauw University. It has been accepted for inclusion in Student research by an authorized administrator of Scholarly and Creative Work from DePauw University. For more information, please contact [email protected]. An Economic Analysis of Mars Exploration and Colonization Clayton Knappenberger 2015 Sponsored by: Dr. Villinski Committee: Dr. Barreto and Dr. Brown Contents I. Why colonize Mars? ............................................................................................................................ 2 II. Can We Colonize Mars? .................................................................................................................... 11 III. What would it look like? ............................................................................................................... 16 A. National Program ......................................................................................................................... -
2. Going to Mars
aMARTE A MARS ROADMAP FOR TRAVEL AND EXPLORATION Final Report International Space University Space Studies Program 2016 © International Space University. All Rights Reserved. The 2016 Space Studies Program of the International Space University (ISU) was hosted by the Technion – Israel Institute of Technology in Haifa, Israel. aMARTE has been selected as the name representing the Mars Team Project. This choice was motivated by the dual meaning the term conveys. aMARTE first stands for A Mars Roadmap for Travel and Exploration, the official label the team has adopted for the project. Alternatively, aMARTE can be interpreted from its Spanish roots "amarte," meaning "to love," or can also be viewed as "a Marte," meaning "going to Mars." This play on words represents the mission and spirit of the team, which is to put together a roadmap including various disciplines for a human mission to Mars and demonstrate a profound commitment to Mars exploration. The aMARTE title logo was developed based on sections of the astrological symbols for Earth and Mars. The blue symbol under the team's name represents Earth, and the orange arrow symbol is reminiscent of the characteristic color of Mars. The arrow also serves as an invitation to go beyond the Earth and explore our neighboring planet. Electronic copies of the Final Report and the Executive Summary can be downloaded from the ISU Library website at http://isulibrary.isunet.edu/ International Space University Strasbourg Central Campus Parc d’Innovation 1 rue Jean-Dominique Cassini 67400 Illkirch-Graffenstaden France Tel +33 (0)3 88 65 54 30 Fax +33 (0)3 88 65 54 47 e-mail: [email protected] website: www.isunet.edu I. -
Nagy Commentary on Euripides, Herakles
Informal Commentary on Euripides, Herakles by Gregory Nagy 97 The idea of returning from Hades implies a return from death 109f The mourning swan... Cf. the theme of the swansong. Cf. 692ff. 113 “The phantom of a dream”: cf. skias onar in Pindar Pythian 8. 131f “their father’s spirit flashing from their eyes”: beautiful rendition! 145f Herakles’ hoped-for return from Hades is equated with a return from death, with resurrection; see 297, where this theme becomes even more overt; also 427ff. 150 Herakles as the aristos man: not that he is regularly described in this drama as the best of all humans, not only of the “Greeks” (also at 183, 209). See also the note on 1306. 160 The description of the bow as “a coward’s weapon” is relevant to the Odysseus theme in the Odyssey 203 sôzein to sôma ‘save the body’... This expression seems traditional: if so, it may support the argument of some linguists that sôma ‘body’ is derived from sôzô ‘save’. By metonymy, the process of saving may extend to the organism that is destined to be saved. 270 The use of kleos in the wording of the chorus seems to refer to the name of Herakles; similarly in the wording of Megara at 288 and 290. Compare the notes on 1334 and 1369. 297 See at 145f above. Cf. the theme of Herakles’ wrestling with Thanatos in Euripides Alcestis. 342ff Note the god-hero antagonism as expressed by Amphitryon. His claim that he was superior to Zeus in aretê brings out the meaning of ‘striving’ in aretê (as a nomen actionis derived from arnumai; cf. -
Resource Utilization and Site Selection for a Self-Sufficient Martian Outpost
NASA/TM-98-206538 Resource Utilization and Site Selection for a Self-Sufficient Martian Outpost G. James, Ph.D. G. Chamitoff, Ph.D. D. Barker, M.S., M.A. April 1998 The NASA STI Program Office... in Profile Since its founding, NASA has been dedicated to CONTRACTOR REPORT. Scientific and the advancement of aeronautics and space technical findings by NASA-sponsored science. The NASA Scientific and Technical contractors and grantees. Information (STI) Program Office plays a key part in helping NASA maintain this important CONFERENCE PUBLICATION. Collected role. papers from scientific and technical confer- ences, symposia, seminars, or other meetings The NASA STI Program Office is operated by sponsored or cosponsored by NASA. Langley Research Center, the lead center for NASA's scientific and technical information. SPECIAL PUBLICATION. Scientific, The NASA STI Program Office provides access technical, or historical information from to the NASA STI Database, the largest NASA programs, projects, and mission, often collection of aeronautical and space science STI concerned with subjects having substantial in the word. The Program Office is also public interest. NASA's institutional mechanism for disseminating the results of its research and • TECHNICAL TRANSLATION. development activities. These results are English-language translations of foreign scientific published by NASA in the NASA STI Report and technical material pertinent to NASA's Series, which includes the following report mission. types: Specialized services that complement the STI TECHNICAL PUBLICATION. Reports of Program Office's diverse offerings include completed research or a major significant creating custom thesauri, building customized phase of research that present the results of databases, organizing and publishing research NASA programs and include extensive results.., even providing videos. -
Hesiod Theogony.Pdf
Hesiod (8th or 7th c. BC, composed in Greek) The Homeric epics, the Iliad and the Odyssey, are probably slightly earlier than Hesiod’s two surviving poems, the Works and Days and the Theogony. Yet in many ways Hesiod is the more important author for the study of Greek mythology. While Homer treats cer- tain aspects of the saga of the Trojan War, he makes no attempt at treating myth more generally. He often includes short digressions and tantalizes us with hints of a broader tra- dition, but much of this remains obscure. Hesiod, by contrast, sought in his Theogony to give a connected account of the creation of the universe. For the study of myth he is im- portant precisely because his is the oldest surviving attempt to treat systematically the mythical tradition from the first gods down to the great heroes. Also unlike the legendary Homer, Hesiod is for us an historical figure and a real per- sonality. His Works and Days contains a great deal of autobiographical information, in- cluding his birthplace (Ascra in Boiotia), where his father had come from (Cyme in Asia Minor), and the name of his brother (Perses), with whom he had a dispute that was the inspiration for composing the Works and Days. His exact date cannot be determined with precision, but there is general agreement that he lived in the 8th century or perhaps the early 7th century BC. His life, therefore, was approximately contemporaneous with the beginning of alphabetic writing in the Greek world. Although we do not know whether Hesiod himself employed this new invention in composing his poems, we can be certain that it was soon used to record and pass them on. -
An Analysis of Heracles As a Tragic Hero in the Trachiniae and the Heracles
The Suffering Heracles: An Analysis of Heracles as a Tragic Hero in The Trachiniae and the Heracles by Daniel Rom Thesis presented for the Master’s Degree in Ancient Cultures in the Faculty of Arts and Social Sciences, at Stellenbosch University Supervisor: Prof. Annemaré Kotzé March 2016 Stellenbosch University https://scholar.sun.ac.za Declaration By submitting this thesis electronically, I declare that the entirety of the work contained therein is my own, original work, that I am the sole author thereof (save to the extent explicitly otherwise stated), that reproduction and publication thereof by Stellenbosch University will not infringe any third party rights and that I have not previously in its entirety or in part submitted it for obtaining any qualification. March 2016 Copyright © 2016 Stellenbosch University All rights reserved Stellenbosch University https://scholar.sun.ac.za Abstract This thesis is an examination of the portrayals of the Ancient Greek mythological hero Heracles in two fifth century BCE tragic plays: The Trachiniae by Sophocles, and the Heracles by Euripides. Based on existing research that was examined, this thesis echoes the claim made by several sources that there is a conceptual link between both these plays in terms of how they treat Heracles as a character on stage. Fundamentally, this claim is that these two plays portray Heracles as a suffering, tragic figure in a way that other theatre portrayals of him up until the fifth century BCE had failed to do in such a notable manner. This thesis links this claim with a another point raised in modern scholarship: specifically, that Heracles‟ character and development as a mythical hero in the Ancient Greek world had given him a distinct position as a demi-god, and this in turn affected how he was approached as a character on stage. -
18Th EANA Conference European Astrobiology Network Association
18th EANA Conference European Astrobiology Network Association Abstract book 24-28 September 2018 Freie Universität Berlin, Germany Sponsors: Detectability of biosignatures in martian sedimentary systems A. H. Stevens1, A. McDonald2, and C. S. Cockell1 (1) UK Centre for Astrobiology, University of Edinburgh, UK ([email protected]) (2) Bioimaging Facility, School of Engineering, University of Edinburgh, UK Presentation: Tuesday 12:45-13:00 Session: Traces of life, biosignatures, life detection Abstract: Some of the most promising potential sampling sites for astrobiology are the numerous sedimentary areas on Mars such as those explored by MSL. As sedimentary systems have a high relative likelihood to have been habitable in the past and are known on Earth to preserve biosignatures well, the remains of martian sedimentary systems are an attractive target for exploration, for example by sample return caching rovers [1]. To learn how best to look for evidence of life in these environments, we must carefully understand their context. While recent measurements have raised the upper limit for organic carbon measured in martian sediments [2], our exploration to date shows no evidence for a terrestrial-like biosphere on Mars. We used an analogue of a martian mudstone (Y-Mars[3]) to investigate how best to look for biosignatures in martian sedimentary environments. The mudstone was inoculated with a relevant microbial community and cultured over several months under martian conditions to select for the most Mars-relevant microbes. We sequenced the microbial community over a number of transfers to try and understand what types microbes might be expected to exist in these environments and assess whether they might leave behind any specific biosignatures.