Human Landing System Human Landing System (HLS)
Total Page:16
File Type:pdf, Size:1020Kb
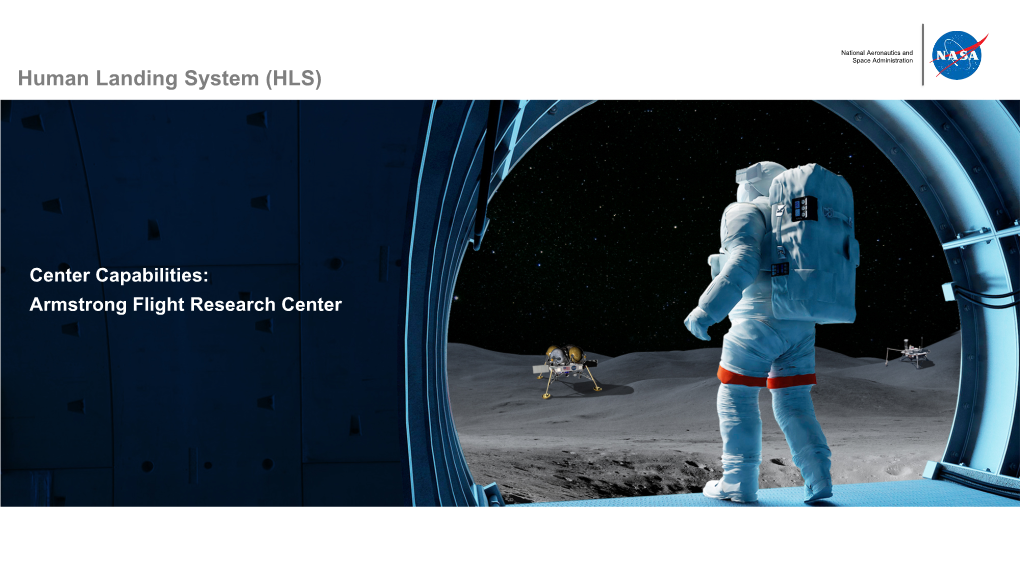
Load more
Recommended publications
-
Spacex CRS-10
March 2017 Vol. 4 No. 3 National Aeronautics and Space Administration KENNEDY SPACE CENTER’S magazine SpaceX CRS-10 SpaceX’s Falcon 9 takes off from historic Launch Pad 39A cementing Kennedy Space Center as a multi-user spaceport Earth Solar Aeronautics Mars Technology Right ISS System & NASA’S Research Now Beyond LAUNCH FROM OUR KENNEDY SPACE CENTER’S SCHEDULE CENTER DIRECTOR SPACEPORT MAGAZINE Date: Targeted for March 19 Launch Window: 10:56 p.m. to 11:26 p.m. EDT Kennedy Space Center Mission: Orbital ATK Resupply Mission to solidifies multi-user CONTENTS International Space Station (CRS-7) Description: The Atlas V launch of Orbital spaceport status ATK’s Cygnus cargo craft from Cape Canaveral Air Force Station in Florida is targeted at 4 �������������������NASA cargo headed to space station on CRS-10 mission 12:29 a.m. EST, the beginning of a 30-minute As I reflect on the successful 10th window. Commercial Resupply Services mission, http://go.nasa.gov/2jetyfU with a SpaceX Falcon 9 and Dragon carrying 8 �������������������Fifth crop harvested aboard space station Date: April 10 supplies and experiments to the International Mission: Expedition 50 Undocking and Space Station, I realized every Kennedy Landing directorate had a role to play in the success Description: NASA astronaut Shane ����������������New plant habitat will increase harvest on station 10 Kimbrough and cosmonauts Sergey Ryzhikov of the mission. We truly are a multiuser and Andrey Borisenko of the Russian space spaceport. agency Roscosmos undock their Soyuz MS-02 Obviously, the role that Spaceport 18 ����������������Final work platform installed for Space Launch System spacecraft from the International Space Integration and Services played in supporting Station’s Poisk module and land in Kazakhstan. -
Nasa Engineering & Safety Center
National Aeronautics and Space Administration NASA ENGINEERING & SAFETY CENTER 2008 TECHNICAL UPDATE www.nasa.gov 1 It gives me a lot of pleasure to recognize the 5th anniversary of the establishment of the NASA Engineering and Safety Center. It also offers, for me, a valuable reminder that it is important always to be open to new ideas and new approaches to solving problems. When the NESC was established, I was more than a bit pessimistic that it could work, that it could provide value for the Agency over and above that offered by our various center engineering directorates. I was wrong. The synergy that has been achieved by the NESC and its cross-agency approach to solving difficult technical problems has been truly impressive. It is, in my mind, a useful model for future endeavors and a great example that it is actually possible for us to “be NASA”, to rise above some of the parochial geographic concerns which have plagued NASA for five decades. These days, when someone tells me that the NESC is looking at a particular issue, I am reassured, because I know that if a solution can be found, this group will find it. – Dr. Michael D. Griffin, NASA Administrator 2 Table of Contents Stakeholder Messages ........................................................................................ 2 NESC Leadership ................................................................................................ 3 Overview: How the NESC Works .......................................................................... 4 NESC Academy: Learning from the Past ............................................................... 8 Technical Highlights Collecting Flight Force Measurements to Improve Coupled Loads Analysis ... 11 Analysis of Constellation Program Mass Properties ....................................... 11 Prediction and Reduction of Ares SRB Thrust Oscillation ............................... 12 Review of the Launch Abort System Motor Qualification Plan ....................... -
A Comparative Analysis of the Geology Tools Used During the Apollo Lunar Program and Their Suitability for Future Missions to the Om on Lindsay Kathleen Anderson
University of North Dakota UND Scholarly Commons Theses and Dissertations Theses, Dissertations, and Senior Projects January 2016 A Comparative Analysis Of The Geology Tools Used During The Apollo Lunar Program And Their Suitability For Future Missions To The oM on Lindsay Kathleen Anderson Follow this and additional works at: https://commons.und.edu/theses Recommended Citation Anderson, Lindsay Kathleen, "A Comparative Analysis Of The Geology Tools Used During The Apollo Lunar Program And Their Suitability For Future Missions To The oonM " (2016). Theses and Dissertations. 1860. https://commons.und.edu/theses/1860 This Thesis is brought to you for free and open access by the Theses, Dissertations, and Senior Projects at UND Scholarly Commons. It has been accepted for inclusion in Theses and Dissertations by an authorized administrator of UND Scholarly Commons. For more information, please contact [email protected]. A COMPARATIVE ANALYSIS OF THE GEOLOGY TOOLS USED DURING THE APOLLO LUNAR PROGRAM AND THEIR SUITABILITY FOR FUTURE MISSIONS TO THE MOON by Lindsay Kathleen Anderson Bachelor of Science, University of North Dakota, 2009 A Thesis Submitted to the Graduate Faculty of the University of North Dakota in partial fulfillment of the requirements for the degree of Master of Science Grand Forks, North Dakota May 2016 Copyright 2016 Lindsay Anderson ii iii PERMISSION Title A Comparative Analysis of the Geology Tools Used During the Apollo Lunar Program and Their Suitability for Future Missions to the Moon Department Space Studies Degree Master of Science In presenting this thesis in partial fulfillment of the requirements for a graduate degree from the University of North Dakota, I agree that the library of this University shall make it freely available for inspection. -
THE MAX LAUNCH ABORT SYSTEM – CONCEPT, FLIGHT TEST, and EVOLUTION Michael G
THE MAX LAUNCH ABORT SYSTEM – CONCEPT, FLIGHT TEST, AND EVOLUTION Michael G. Gilbert(1), PhD (1) Principal Engineer, NASA Engineering and Safety Center 11 Langley Blvd., MS 116,Hampton VA 23681 USA Email:[email protected] Abstract escape system Maxime Faget [1]. The effort was intended to provide The NASA Engineering and Safety Center programmatic risk-reduction for the (NESC) is an independent engineering Constellation Program (CxP) Orion Crew analysis and test organization providing Exploration Vehicle (CEV) project. support across the range of NASA programs. In 2007 NASA was developing The CEV project baseline Launch Abort the launch escape system for the Orion System (LAS) development is an evolution spacecraft that was evolved from the of the Apollo towered-rocket design, Fig. traditional tower-configuration escape 2. Unlike the Apollo LAS, the CEV LAS systems used for the historic Mercury and incorporated an attitude control motor to Apollo spacecraft. The NESC was tasked, ensure stable flight following the escape as a programmatic risk-reduction effort to motor burn. At the time the MLAS project develop and flight test an alternative to the was initiated, the CEV LAS was Orion baseline escape system concept. experiencing development delays related This project became known as the Max to the LAS attitude control motor. Launch Abort System (MLAS), named in Therefore, the MLAS project was to honor of Maxime Faget, the developer of consider escape system concepts that the original Mercury escape system. Over would not require active attitude control or the course of approximately two years the stabilization following escape motor NESC performed conceptual and tradeoff burnout. -
Testing Strategies and Methodologies for the Max Launch Abort System Dawn M
Testing Strategies and Methodologies for the Max Launch Abort System Dawn M. Schaible Daniel E. Yuchnovicz NASA Engineering and Safety Center Hampton, Virginia ABSTRACT The National Aeronautics and Space Administration (NASA) Engineering and Safety Center (NESC) was tasked to develop an alternate, tower-less launch abort system (LAS) as risk mitigation for the Orion Project. The successful pad abort flight demonstration test in July 2009 of the “Max” launch abort system (MLAS) provided data critical to the design of future LASs, while demonstrating the Agency’s ability to rapidly design, build and fly full-scale hardware at minimal cost in a “virtual” work environment. Limited funding and an aggressive schedule presented a challenge for testing of the complex MLAS system. The successful pad abort flight demonstration test was attributed to the project’s systems engineering and integration process, which included: a concise definition of, and an adherence to, flight test objectives; a solid operational concept; well defined performance requirements, and a test program tailored to reducing the highest flight test risks. The testing ranged from wind tunnel validation of computational fluid dynamic simulations to component ground tests of the highest risk subsystems. This paper provides an overview of the testing/risk management approach and methodologies used to understand and reduce the areas of highest risk — resulting in a successful flight demonstration test. KEY WORDS: Testing, risk management, flight test, launch abort systems MLAS PROJECT OVERVIEW NASA’s next generation crewed spacecraft, named Orion, is a part of the overall Constellation Program. The baseline Orion design includes a launch abort system (LAS) with tower, derived from the Apollo design. -
Inside Wallops National Aeronautics and Space Administration Goddard Space Flight Center Wallops Flight Facility, Wallops Island, Va
Inside Wallops National Aeronautics and Space Administration Goddard Space Flight Center Wallops Flight Facility, Wallops Island, Va. Volume XX-08 Number 10 March 24, 2008 Max Launch Abort System Development Early last year, the Wallops Flight Facility enough and with enough distance Representatives from the Sounding embarked on a challenging effort to downrange to permit the CM to execute a Rockets Program Office and NASA support NASA Engineering and Safety nominal landing. Sounding Rocket Operations Contract, Center (NESC) with the development of (NSROC), have provided technical a composite crew module for the In addition to a wealth of solid rocket motor support associated with the solid rocket Exploration Orion spacecraft. knowledge and experience at Wallops, the motor systems. NSROC will play a major NESC found an engineering staff well- role in vehicle hardware and mechanical The NESC will design, develop, and test suited to rapid-response system GSE fabrication. an alternate concept launch abort system development. Personnel from many (LAS) for the Orion crew module (CM) Wallops organizations have joined the Team members from the Facilities as a risk mitigation for the Orion Project’s MLAS team. LAS development. Management Branch are responsible for procurement and construction of a custom Having an effective means for the crew The Wallops’ Guidance, Navigation & launch pad shelter and for infrastructure to escape in an emergency during launch Control and Mission Systems Engineering improvements related to transportation of is critical in establishing launch system Branch, have supported design and flight the MLAS demonstrator from the Wallops reliability and crew safety for the dynamics analysis. -
2020 NASA Technology Taxonomy the Page Intentionally Left Blank
National Aeronautics and Space Administration 2020 NASA Technology Taxonomy The page intentionally left blank. i CONTENTS Letter from the Chief Technologist . iii Introduction . v TX01: Propulsion Systems . 1 TX02: Flight Computing and Avionics . 15 TX03: Aerospace Power and Energy Storage . 27 TX04: Robotic Systems . 35 TX05: Communications, Navigation, and Orbital Debris Tracking and Characterization Systems . 51 TX06: Human Health, Life Support, and Habitation Systems . 65 TX07: Exploration Destination Systems . 83 TX08: Sensors and Instruments . 95 TX09: Entry, Descent, and Landing . 105 TX10: Autonomous Systems . 115 TX11: Software, Modeling, Simulation, and Information Processing . 127 TX12: Materials, Structures, Mechanical Systems, and Manufacturing . 145 TX13: Ground, Test, and Surface Systems . 157 TX14: Thermal Management Systems . 173 TX15: Flight Vehicle Systems . 185 TX16: Air Traffic Management and Range Tracking Systems . 195 TX17: Guidance, Navigation, and Control . 201 Acronyms . 222 Acknowledgements . 225 ii Letter from the Chief Technologist “And as we renew our commitment to lead in space, let’s go with confidence and let’s go with faith. Faith in the vision and the goal that’s articulated today: that we can achieve it; that Americans can achieve anything that we put our minds to. Faith in the extraordinary ingenuity and capability of the men and women of NASA and America’s space enterprise, and their ability to meet those challenges if given the resources and the support to do it. And especially faith in the courage of the men and women who are now, and those who will join, the storied ranks of American astronauts—that next generation of restless pioneers that will carry American leadership into space. -
Changing the Shape of Launch Abort Systems
featured knowledge Changing the Shape of Launch Abort Systems n December 2014, NASA’s Orion Starting in December 2006, IMulti-Purpose Crew Vehicle they performed aerodynamic, (MPCV) Program successfully structural and controls analyses, conducted Experimental Flight as well as a number of wind tunnel Test-1 (EFT-1), the first orbital flight experiments, to obtain the data test of the Orion spacecraft. Close required to validate the concept. observers may have noted that the “We found that adding a fairing spacecraft had an updated shape improved the aerodynamic shape from the concepts included on the significantly,” said Schuster. “It previous Ares I-X and Orion Pad reduced drag during ascent, as well Abort 1 flight tests. In reality, the as weight by providing a separate Orion crew module (CM) shape has load path around the crew module.” not changed substantially since In addition to better quantifying these flights, but the Orion Launch the aerodynamic, performance, Abort System (LAS) has changed. and structural improvements, Reducing structural loads a major new focus investigated using the ALAS MBPC to reduce In September 2006, during a peer aeroacoustic loads on the Orion review of the NESC Composite CM. “Current predictions of Orion Crew Module (CCM) Assessment, acoustic loads far exceeded what an Alternate Launch Abort System was assumed in the design of the (ALAS) was conceived to reduce Orion subsystems,” said Scotti. structural loads carried by the “And the project hoped that the CCM during a flight abort. To ALAS approach would help solve further investigate the feasibility that problem and eliminate the of the ALAS concept, Dr. -
Toward a History of the Space Shuttle an Annotated Bibliography
Toward a History of the Space Shuttle An Annotated Bibliography Part 2, 1992–2011 Monographs in Aerospace History, Number 49 TOWARD A HISTORY OF THE SPACE SHUTTLE AN ANNOTATED BIBLIOGRAPHY, PART 2 (1992–2011) Compiled by Malinda K. Goodrich Alice R. Buchalter Patrick M. Miller of the Federal Research Division, Library of Congress NASA History Program Office Office of Communications NASA Headquarters Washington, DC Monographs in Aerospace History Number 49 August 2012 NASA SP-2012-4549 Library of Congress – Federal Research Division Space Shuttle Annotated Bibliography PREFACE This annotated bibliography is a continuation of Toward a History of the Space Shuttle: An Annotated Bibliography, compiled by Roger D. Launius and Aaron K. Gillette, and published by NASA as Monographs in Aerospace History, Number 1 in December 1992 (available online at http://history.nasa.gov/Shuttlebib/contents.html). The Launius/Gillette volume contains those works published between the early days of the United States’ manned spaceflight program in the 1970s through 1991. The articles included in the first volume were judged to be most essential for researchers writing on the Space Shuttle’s history. The current (second) volume is intended as a follow-on to the first volume. It includes key articles, books, hearings, and U.S. government publications published on the Shuttle between 1992 and the end of the Shuttle program in 2011. The material is arranged according to theme, including: general works, precursors to the Shuttle, the decision to build the Space Shuttle, its design and development, operations, and management of the Space Shuttle program. Other topics covered include: the Challenger and Columbia accidents, as well as the use of the Space Shuttle in building and servicing the Hubble Space Telescope and the International Space Station; science on the Space Shuttle; commercial and military uses of the Space Shuttle; and the Space Shuttle’s role in international relations, including its use in connection with the Soviet Mir space station. -
Launch Abort System Evolution
featured knowledge Launch Abort System Evolution critical component of crewed spacecraft, the launch Aabort system (LAS), allows for rescue of the crew in the event of a catastrophic malfunction while the spacecraft is sitting on the launch pad or on its way into orbit. For a successful rescue, however, the LAS must perform several critical maneuvers in rapid-fire succession. First, the launch abort motors must be powerful enough to fly the fairing and crew module (CM) to a safe distance away from the launch vehicle. Next, it must reorient and fly in a carefully controlled heat shield-forward attitude. Finally, it must release the CM, enabling the CM’s parachute landing system to deploy for a safe return of the crew. LAS begins with Project Mercury Since the time of Project Mercury and the Apollo Program, the LAS has maintained its traditional tower configuration. But as spacecraft design has evolved, so has the need for a new LAS. The Orion Multi-Purpose Propulsively stabilized MLAS concept. Crew Vehicle launched on December 4, 2014, featured a new Alternative Launch Abort System (ALAS) shape and structure that enhanced the aerodynamic and aeroacoustic performance of the spacecraft. But while the NESC was spearheading efforts on the ALAS design, it was also developing the Max Launch Abort System (MLAS), a follow-on to the ALAS design that incorporated the ALAS shape while fundamentally changing the LAS from a tower to a towerless design. Named in honor of Maxime Faget, developer of the original Mercury launch escape system, MLAS was a 2-year effort Left: Successful launch abort test of the passively stabilized that culminated in a full-scale flight demonstration. -
2013 Spaceport News Summary
2013 Spaceport News Summary The 2013 Spaceport News used the above banner for the year. Introduction The first issue of the Spaceport News was December 13, 1962. The 1963, 1964 and 1965 Spaceport News were issued weekly. The Spaceport News was issued every two weeks, starting July 7, 1966, until the last issue on February 24, 2014. Spaceport Magazine, a monthly issue, superseded the Spaceport News in April 2014, until the final issue, Jan./Feb. 2020. The two 1962 Spaceport News issues and the issues from 1996 until the final Spaceport Magazine issue, are available for viewing at this website. The Spaceport News issues from 1963 through 1995 are currently not available online. In this Summary, black font is original Spaceport News text, blue font is something I added or someone else/some other source provided, and purple font is a hot link. All links were working at the time I completed this Spaceport News Summary. The Spaceport News writer is acknowledged, if noted in the Spaceport News article. From The January 11, 2013, Spaceport News On page 2, “Kennedy's future bright with full plate for 2013”. Part of the feature, by Bob Cabana, states: “During the past year, Kennedy Space Center made great strides in transitioning from a historically government-only launch facility to an affordable, sustainable, multiuser spaceport for both government and commercial customers… We have a great future ahead, including a full plate for 2013… Coming up later this month is the launch of a TDRS satellite scheduled to lift off from Cape Canaveral Air Force Station… Page 1 We also are moving ahead with plans for NASA's Commercial Crew Program. -
BBN Brevard Business News
Brevard Business BBN News Vol. 36 No. 6 February 5, 2018 $1.00 A Weekly Space Coast Business Magazine with Publishing Roots in America since 1839 Space Congress to open Feb. 27 at Radisson; themed ‘Next Great Steps’ By Ken Datzman COCOA BEACH — In 2015, the Canaveral Council of Technical Societies began the rebuilding of its once high– flying Space Congress event, whose roots go back more than five decades, first in Volusia County for a short time, then locally where it enjoyed a long run. The programs of yesteryear attracted the space industry’s leading thinkers in a weeklong convention setting where cutting–edge information was freely exchanged among participating companies and organiza- tions. Space–related experts came to Brevard County from around the nation and abroad to discuss the state of their industry. The event typically drew more than 1,000 aerospace and industry professionals. It filled hotel rooms in the area and uplifted the economy, before CCTS, a nonprofit educational corporation founded in 1965, announced the closing of Space Congress about a decade ago, although it did host a one–day program in 2012. “During its peak years, Space Congress filled the hotels along A1A,” said Martin “Marty” McLellan, the chairman for the 45th Space Congress, which is set to kick off on Tuesday, Feb 27, at the Radisson Resort at the Port in Cape Canaveral and run through Thursday, March 1. “This was a big event that had a lot of visibility within the space community. We’re working to make it great again. This year, we have an outstanding group of speakers who will be addressing everything from the new multi–user spaceport at Kennedy Space Center to space tourism to NASA exploration to space legislation, all under the theme of ‘The Next Great Steps.’ We’re excited about the 45th Space Congress.” BBN photo — Adrienne B.