Conversion Varnish Primer-White 150-0016
Total Page:16
File Type:pdf, Size:1020Kb
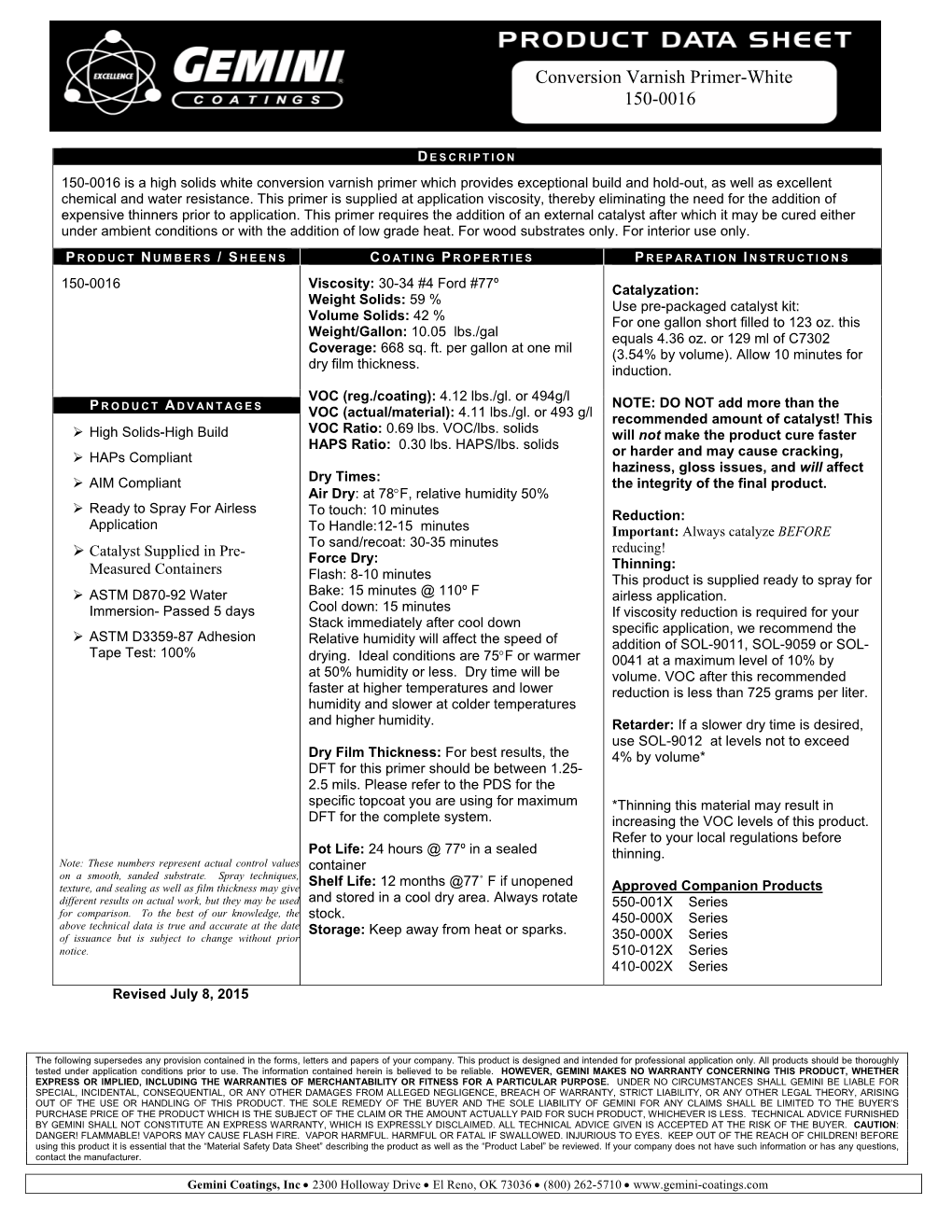
Load more
Recommended publications
-
Technical Data Sheet
Technical Data Sheet Modern Masters Inc. (800) 942-3166 9380 San Fernando Rd., Sun Valley CA 91352 Metal Effects® Copper Paint Blue or Green Patina Finish Water Base Acrylic, Low VOC System Creates a “Real” Patina Metal Finish Brush, Roll or Spray apply Products Used • Metal Effects Primer (AM203) • Blue Patina (PA902) or Green Patina (PA901) • Copper Paint (ME149) Modern Masters – Metal Effects® Copper Metallic clean and free of oil, grease, wax, and other Paint (ME149) is a water-base, modified acrylic paint contaminants, and completely dry prior to priming. with a high concentration of real copper particles. It will Surfaces previously primed require light sanding. Scuff tarnish naturally over time, if exposed to the proper sand any glossy surfaces. Stir well before and elements, but Metal Effects Green Patina (PA901) or occasionally during application. Do not thin Metal Blue Patina Aging Solutions (PA902) will speed up Effects Primer. If unsure of the substrate, test a the oxidation process and create a beautiful, authentic sample area to ensure the desired results. Apply at green or blue patina finish in minutes. Metal Effects least two coats of Metal Effects Primer to completely Copper Metallic Paint can be brush, roll, or spray seal and block the surface. Some metal surfaces, such applied. The Metal Effects Green or Blue Patina can be as bare aluminum, galvanized metal, or rusted or slag applied with a brush, sponge, spray bottle, or plastic metals, will need a specialty primer from our pump sprayer. The entire system can be applied to any recommended primer list, applied prior to the properly prepared surface, including metal, wood, application of Metal Effects Primer. -
Technical Data Rst-51
TECHNICAL DATA RST-51 ROCKSOLID® DECK START WOOD PRIMER DESCRIPTION AND USES . PRODUCT APPLICATION (cont) . RockSolid® Deck Start Wood Primer is a water-based acrylic UNCOATED NEW WOOD coating designed for application on structurally sound wood New wood surfaces need to weather at least 6 months before surfaces. application. Clean the surface using a deck brush and deck DECKS: For use on weathered, worn or previously coated wood cleaner. The surface must be clean and free of dirt, grease, decks, docks and exterior wood furniture. ROCKSOLID DECK mildew and organic growth. Loose paint or stain needs to be START WOOD PRIMER CAN ONLY BE USED UNDER A scraped or removed. Secure raised nail heads, deck screws, or SOLID TOPCOAT. Do not use under a transparent, semi- loose deck boards. Remove loose splinters and replace severely transparent or penetrating deck coating. damaged or rotting boards. PATIOS: For use on concrete patio surfaces. Not PREVIOUSLY SEALED WOOD recommended for driveways, garages or other areas with Sealed wood surfaces need to weather at least 6 months before vehicular traffic. application. Clean the surface using a deck brush and a standard RockSolid Deck Start Wood Primer is a clear primer. DO deck cleaner. The surface must be clean and free of dirt, grease, NOT TINT. mildew and organic growth. Loose paint or stain needs to be scraped and removed. RockSolid Deck Start Wood Primer can be applied using a ⅜” nap roller, a short nap stain pad or a synthetic paint SEALED DECKS MAY NOT FULLY WEATHER IN COVERED brush. AREAS. Conduct a splash test by sprinkling water on at least four or more areas, both in high traffic and non-traffic areas. -
Mural Creation Best Practices
Mural Creation Best Practices Since 2006, Heritage Preservation’s Rescue Public Murals (RPM) initiative has confronted the risks that community murals face by being located in outdoor, public spaces. Murals have been, and are an increasingly, popular public art form that adds vibrancy and vitality to the built landscape. Many communities in the United States, large and small, have mural programs or are actively commissioning murals. Unfortunately, almost every community is also aware of the negative image that a faded, flaking, or vandalized mural creates or the misfortune of an artist’s work that has been unjustly removed or destroyed. While working to ensure the protection and preservation of existing murals, RPM recognizes that many common issues that murals face could have been mitigated with careful planning and preparation. RPM has held conversations and brainstorming sessions with muralists, conservators, art historians, arts administrators, materials scientists, and engineers to document best practices for mural creation. We present these recommendations on this website. Recommendations are not meant to be prescriptive but instead to pose questions and raise issues that should be considered at each stage of creating a mural: planning, wall selection, wall and surface preparation, painting, coating, and maintenance. Each recommendation has been considered both for mural commissioning organizations/agencies and for artists to address their particular needs and concerns. Each section includes links to further reading on the topic. The recommendations on this website assume that a mural that is painted with careful planning and consideration to technique and materials and that receives regular maintenance could have a lifespan of 20-30 years. -
Adhesive Bonding of Polyolefin Edward M
White Paper Adhesives | Sealants | Tapes Adhesive Bonding of Polyolefin Edward M. Petrie | Omnexus, June 2013 Introduction Polyolefin polymers are used extensively in producing plastics and elastomers due to their excellent chemical and physical properties as well as their low price and easy processing. However, they are also one of the most difficult materials to bond with adhesives because of the wax-like nature of their surface. Advances have been made in bonding polyolefin based materials through improved surface preparation processes and the introduction of new adhesives that are capable of bonding to the polyolefin substrate without any surface pre-treatment. Adhesion promoters for polyolefins are also available that can be applied to the part prior to bonding similar to a primer. Polyolefin parts can be assembled via many methods such as adhesive bonding, heat sealing, vibration welding, etc. However, adhesive bonding provides unique benefits in assembling polyolefin parts such as the ability to seal and provide a high degree of joint strength without heating the substrate. This article will review the reasons why polyolefin substrates are so difficult to bond and the various methods that can be used to make the task easier and more reliable. Polyolefins and their Surface Characteristics Polyolefins represent a large group of polymers that are extremely inert chemically. Because of their excellent chemical resistance, polyolefins are impossible to join by solvent cementing. Polyolefins also exhibit lower heat resistance than most other thermoplastics, and as a result thermal methods of assembly such as heat welding can result in distortion and other problems. The most well-known polyolefins are polyethylene and polypropylene, but there are other specialty types such as polymethylpentene (high temperature properties) and ethylene propylene diene monomer (elastomeric properties). -
Acryshield Exterior Wood Primer
AcryShield Kelly-Moore Paints Exterior Wood Primer PRODUCT DESCRIPTION AcryShield Wood Primer is a premium quality acrylic primer designed to promote adhesion, resist tannin bleed, and seal porous wood. Excellent for use on siding, shingles, fascia, or other bare wood surfaces. FEATURES & SPECIFICATIONS PERFORMANCE FEATURES AVAILABLE PRODUCTS • Seals New Wood FINISHES: 255 Primer • Excellent Adhesion 100 White 0 – 2 oz/gal • Resists Tannin Bleed BASES & COLORANT: • Promotes Uniform Finish SIZES: Gallon & Five Gallon SUBSTRATES PRODUCT SPECIFICATIONS Wood RESIN TYPE: 100% Acrylic Composite VOC (ASTM D6886): < 100 g/L SOLIDS BY VOLUME: 38 ± 2% WEIGHT PER GAL: 10.6 ± .25 lbs. SUBSTRATES & SYSTEM RECOMMENDATIONS PREP: All surfaces must be cured, firm and dry. Use a suitable cleaner to remove all dirt, oil or other contamination. Sand glossy surfaces and remove dust. (See WARNING!) PRIME: 1 Coat – AcryShield Wood Primer Brush: Synthetic Bristle Temperature: 35°F - 100°F Dry Time: 2 Hours Touch / 4 Hours Recoat 3/8”-3/4” Synthetic Cover Roll: Spray: 2000-2500 PSI / .015”-.021” Tip Clean-up: Water Thinning: Not Required / <10% Water, If Necessary 4-6 Mils Wet / 1.5-2.3 Mils Dry Thickness: Coverage: 250-400 sq/ft Per Gallon PAINT: 2 Coats – Preferred Kelly-Moore Finish For significant color change or to block tannins, allow primer to dry 24 hours before topcoating. A second coat of primer may be required for heavy tannins. A specialty primer may be required in some situations such as porous substrates, chalky surfaces, corrosion protection, dense or glossy surfaces, or to block stains. See a Kelly-Moore representative for additional recommendations. -
Automotive Primer Surfacer
TECHNICAL DATA ATO-27 AUTOMOTIVE PRIMER SURFACER .DESCRIPTION AND USES . ..PRODUCT APPLICATION (cont.) . Rust-Oleum® Primer Surfacer is designed to improve adhesion WARNING: If you scrape, sand, or remove old paint, you may of the final topcoat and enhance the finish color. When brush or release lead dust. LEAD IS TOXIC. EXPOSURE TO LEAD spray applied, this high build, rust resistant, sandable primer will DUST CAN CAUSE SERIOUS ILLNESS, SUCH AS BRAIN hide sanding scratches and fill uneven surfaces. This product DAMAGE, ESPECIALLY IN CHILDREN. PREGNANT WOMEN must first be combined with an equal 1:1 part of Rust-Oleum SHOULD ALSO AVOID EXPOSURE. Wear a NIOSH-approved 248877 Specialty Reducer before spray application. This all respirator to control lead exposure. Clean up carefully with a purpose primer is suitable for use on metal, fiberglass, and wood. HEPA vacuum and a wet mop. Before you start, find out how to Do not use of surfaces that will come into direct contact with heat protect yourself and your family by contacting the National Lead or temperatures exceeding 350°F. Information Hotline at 1-800-424-LEAD or log on to www.eps.gov/lead. .PRODUCTS . APPLICATION SKU Description 249332 Light Gray (1-Gallon) Mix thoroughly to ensure any settled pigment is re-dispersed. 260073 Light Gray (1-Quart) Combine equal parts by volume of 1- part of Rust-Oleum Primer Surfacer with 1-part of Rust-Oleum Specialty Reducer. If using a ..PRODUCT APPLICATION . conventional spray gun, the air pressure should be adjusted to 30-40 pounds. Apply 2-3 medium coats and allow each coat to READ ALL INSTRUCTIONS CAREFULLY BEFORE dry to touch before applying the next coats. -
A Collection of Vintage Rust and Crackle Effects
A collection of vintage rust and crackle effects Find our products and videos at: owatrol-spirit.com Corresponding Smooth surfaces: Cardboard, On sensitive Application surface untreated surface Aluminium, Galvanised Plaster, Plaster- surfaces: Wood, (Steel, Cast Iron, etc. Metal, Plastic, Glass, Cera- board, Paper, Plastic. Copper or Bronze). mics, Stainless Steel, etc. Brick, etc. 1 Durieu has successfully fought Prepare Clean and dust off Clean and dust off rust since 1956 with its unique benchmark product, Owatrol Oil®. Innovative technology with exceptional penetrating and protective qualities for both rusted and non-rusted metal. 2 RUST Create effect Because the control of metal decorative corrosion and the effects of ageing effects on materials form the basis of its culture, Durieu is innovating and COPPER launching an original and creative effect product range allowing you to create and easily produce “aged effects”: rust, oxidation, crackling, etc. Presenting the Owatrol® Spirit range! BRONZE effect At the heart of the range, Rust Spirit : a natural rust creator that will revolutionise your creative spirit. Now wood, plastic, cardboard and glass can rust! 3 Metal as well of course, but in just Protect a few minutes... Corresponding Smooth surfaces: Cardboard, On sensitive Application surface untreated surface Aluminium, Galvanised Plaster, Plaster- surfaces: Wood, (Steel, Cast Iron, etc. Metal, Plastic, Glass, Cera- board, Paper, Plastic. Copper or Bronze). mics, Stainless Steel, etc. Brick, etc. Primer Blocking Primer Absolute -
Metal Primer 6455/044
Metal Primer 6455/044 TECHNICAL BULLETIN 712 1/14 Forms excellent adhesive bond to most bare metals. For use above and below the waterline. Recommended for all underwater metals and running gear. 6455/044 Metal Primer is a two component, self-etching wash primer for use only on bare metals including steel, stainless steel, cast iron, copper, bronze, galvanized steel, lead, and aluminum. It forms an excellent adhesive bond to metal hulls, keels, centerboards, and other underwater running gear, and can be used above or below the waterline. Metal Primer can be over coated with epoxy primer, tie-coat primer, topside enamels, or antifouling paint. APPLICATION INFORMATION Shake or stir 6455 Metal Primer thoroughly before using. Make sure any pigment settled to the bottom of the can during storage has been properly remixed into suspension. Add the complete pouch of 044 Metal Primer Activator to the 6455 Metal Primer very slowly with constant stirring. If smaller amounts of primer are going to be mixed, add 1 volume of Activator to 4 volumes of the Metal Primer. Do not mix more material than can be used in 8 hours. The mixture of Primer and Activator will still be fluid after 8 hours but should not be used since the quality of adhesion to metals will be reduced. Metal Primer may be applied by brush, roller, conventional or airless spray. For brush application no thinning is necessary. For roller application thin 10 to 15% with denatured alcohol. Add 20 to 25% denatured alcohol for spray application. Apply one thin wet semi- transparent coat to metal surfaces only. -
Zinsser® Ceiling Paint Paint & Primer In
TECHNICAL DATA ZNR-19 ZINSSER® CEILING PAINT PAINT & PRIMER IN ONE DESCRIPTION AND USES PRODUCT APPLICATION (cont.) Zinsser ® Ceiling Paint – Paint & Primer in One is a high Wear a NIOSH-Approved respirator to control lead performance, low VOC, acrylic paint specifically designed for exposure. Clean up carefully with a HEPA vacuum and a ceilings. Ceiling Paint – Paint & Primer in One has excellent wet mop. Before you start, find out how to protect yourself stain blocking resistance and seals water and other and your family by contacting the National Lead Information household stains in one coat. Ceiling Paint & Prime in One Hotline at 1-800-424-LEAD or log on to www.epa.gov/lead. goes on pink and dries to a bright white finish which is APPLICATION mildew resistant. Apply only when air, material, and surface temperatures are Ceiling Paint – Paint & Primer in One can be used on new or between 50-90°F (10-32ºC) and the relative humidity is previously painted or primed wood, drywall, painted metal below 85%. Thoroughly mix to ensure any settled pigment and plaster, textured and popcorn style ceilings in kitchens, is re-dispersed before using. Apply at package bathrooms, basements, closets and other living areas. Bare consistency. Do not thin for one coat coverage. In most metal, new or knock-downed texture should be primed and cases only one coat is necessary. If excessive absorption sealed with Bulls-Eye 1-2-3 Primer. If unsure about the occurs over very porous substrates, a second coat may be integrity of the surface, test adhesion by placing a 2” piece of necessary. -
Specialty Plastic Primer Quart
TECHNICAL DATA SPC-35 SPECIALTY PLASTIC PRIMER QUART .DESCRIPTION AND USES . .PRODUCT APPLICATION (cont.) . Rust-Oleum® Specialty Plastic Primer prepares plastic for APPLICATION painting with any of the Rust-Oleum brush and spray paints ® ® ® Thoroughly mix material to ensure any settled pigment is including Stops Rust , American Accents and Painters Touch . re-dispersed. Do not thin. Apply one complete coat of Renew plastic furniture, planters and more. Plastic Primer bonds primer using a high quality brush, roller or spray gun. tightly to plastic and provides for excellent top coat adhesion and durability. Plastic Primer is suitable for use on polypropylene, Top Coat Application – A topcoat may be applied to the polystyrene, resin, fiberglass and vinyl plastics such as chairs, primed surface when fully dry, usually in 24 hours at tables and planters. Some plastics made of polyethylene 70°F(21°C) and 50% relative humidity. Allow more time at ® such as Little Tikes children’s products are manufactured cooler temperatures and higher humidity. in such a way that may hinder maximum paint adhesion. Test paint in an inconspicuous area first. Enamel Top Coat – It is recommended that a top coat be applied to the primer. Use any Rust-Oleum spray paint or .PRODUCTS . oil-based brush enamel. SKU Container Size Latex Top Coat – If a latex top coat is used, it is important 213517T 1-Quart to sand the primed surface using 400-grit sandpaper with light, even stokes. Light sanding will increase the adhesion ..PAINTING APPLICATION . of latex paint on primed plastic surfaces. Remove excess PAINTING CONDITIONS sanding dust with a tack cloth. -
PRIMER PAINT GENERAL INFORMATION Verco Decking, Inc.’S Primer Gray Steel Deck Is Produced from Steel Coils That Have Been Thoroughly Cleaned, Painted and Dried
VERCO DECKING, INCORPORATED PRIMER COAT STEEL ROOF AND FLOOR DECK COATINGS SYSTEM GRAY - PRIMER PAINT GENERAL INFORMATION Verco Decking, Inc.’s Primer Gray Steel Deck is produced from steel coils that have been thoroughly cleaned, painted and dried. This involves a three (3) step process of: pressure cleaning; paint application by roller coat and oven drying. This Thermoplastic Acrylic coating is formulated to meet post forming deck specifications that are ideal for commercial or industrial roof and floor deck applications. FEATURES ♦ Weldable as defined by the American Welding Society ♦ Excellent Impact resistance and ductility ♦ Excellent humidity resistance ♦ Non toxic ♦ Excellent block resistance ♦ Verco steel decks (bare steel) with 0.3 mils gray primer paint are approved for use with appropriate spray-applied fireproofing per IAPMO ER-0217 and ANSI/UL 263. Galvanized decks with primer painted underside are not approved for use in fire-rated systems. ♦ Excellent adhesion properties TECHNICAL DATA Product: Gray Primer Generic Type: Acrylic Latex Pigment Type: Titanium Dioxide Hazardous Materials: None Chrome or Lead: None FIELD APPLIED COATINGS SURFACE PREPARATION: Ensure surface is clean, dry and free from contaminants such as; oil, grease, dirt or mud. Cleaning with water and mild detergent is a common practice. The paint applicator should follow the paint supplier’s recommended application procedure, especially with regard to temperature, humidity, and surface moisture. CHOOSE A SUITABLE FIELD COAT: Verco primer has been formulated to be compatible with various air dry coatings of good quality. Suitable coating bases may be: Alkyd, Epoxy Polyamide, Epoxy Esters and Acrylic latex. Solvent borne products based on weak solvents such as mineral spirits should be compatible. -
All Surface • All Purpose Oil-Base Primer-Sealer Stain Killer All
AA PrimerPrimer forfor Other ZINSSER Problem Solvers... EveryEvery Job...Job... Bulls Eye 1-2-3 ® - All Surface, All Purpose Water-Base Primer Recommended B-I-N Stain • Great hide Cover AllCoat 1-2-3 Applications B-I-N • Great adhesion without sanding INTERIOR SURFACES • Superior stain blocking Drywall EEEE • Mould & mildew resistant film Plaster (1) GEGE • Great for high pH surfaces Limewash/Lime Plaster NRENRE • Great under or over any paint New Wood Trim/Doors EGEE • Fast 1 hour recoat time Plywood GGEE * Available in Bulls Eye ® 1-2-3 DEEP TINT formula to Brick NRENRNR improve coverage of deep colour topcoats Concrete (1) GEGG ® Galvanised New (3)/Old NRENRG B-I-N The Ultimate Performance Aluminium/Stainless Steel GEGG Shellac-Base Primer-Sealer Plastisol® EEEE • The ultimate stain killer – blocks stains from Fibreglass/GRP NRENRNR water, smoke, fire damage and more Glossy Paints/Glass EEEE • The ultimate new wood sealer- seals knots & sap streaks Varnish/Woodstain ENRNRNR • Blocks odours permanently and completely COVCOVER-ER-STAINSTAIN Clear Finishes EGGG • Sticks to glass, metal, tile and other glossy Wood Panelling/Laminates EGGG surfaces without sanding Ceramic Tile GEGG • Lightning fast dry – recoat in 45 minutes Formica® EGGG • Great under or over any topcoat Wallcovering (non porous) EEEE * Available in handy 390ml aerosol Powder Coatings EEEE AllAll SurSurfacfacee •• AllAll PurpPurposeose Acoustic Tiles NREEE EXTERIOR SURFACES COVER STAIN® Cedar & Redwood *GE* OilOil-Base-Base PrPrimerimer-S-Sealealerer SStaintain KKilleriller