Analysis of Deflection of Rectangular Plates Under Different Loading Conditions
Total Page:16
File Type:pdf, Size:1020Kb
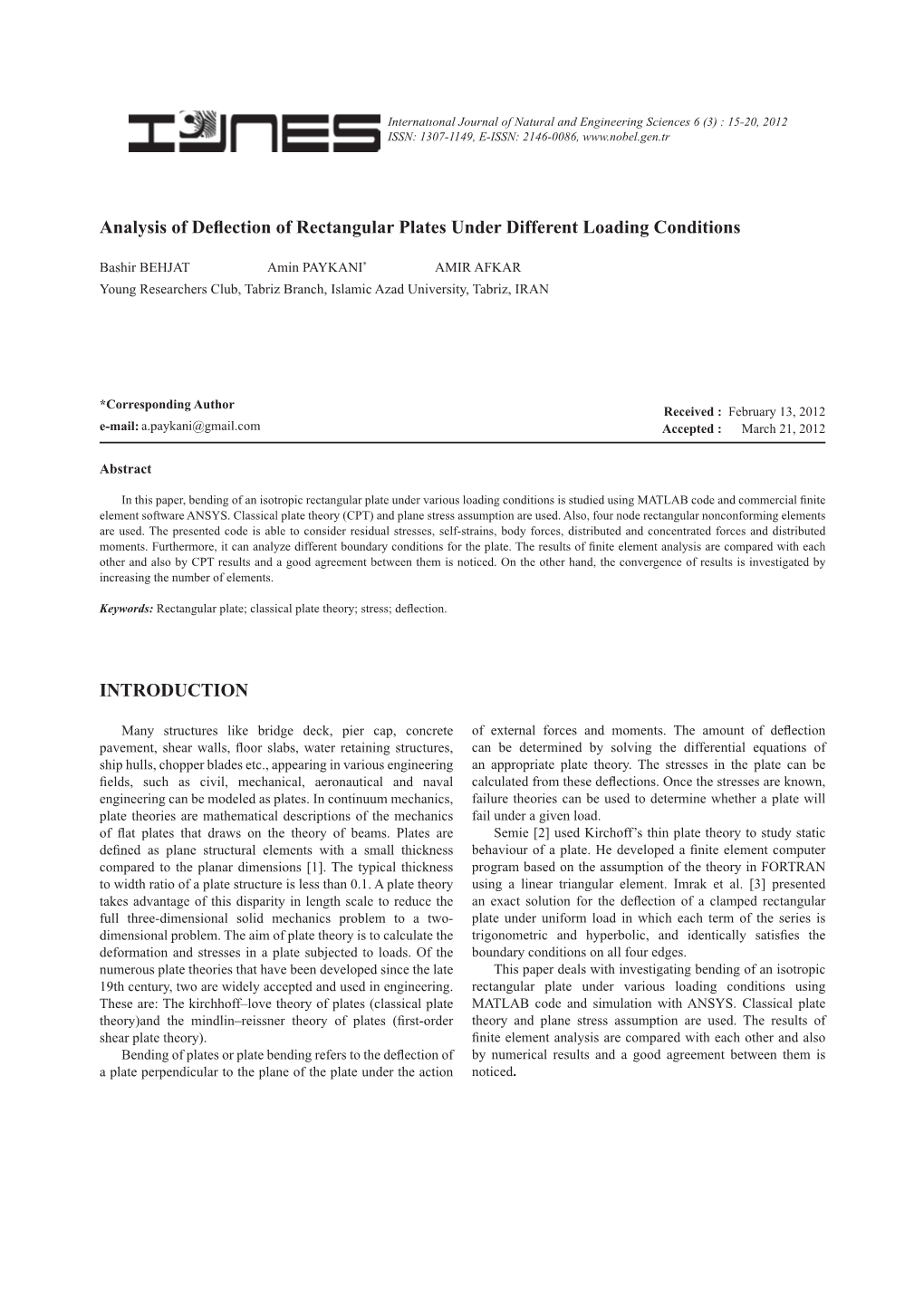
Load more
Recommended publications
-
Symplectic Elasticity Approach for Exact Bending Solutions of Rectangular Thin Plates
Copyright Warning Use of this thesis/dissertation/project is for the purpose of private study or scholarly research only. Users must comply with the Copyright Ordinance. Anyone who consults this thesis/dissertation/project is understood to recognise that its copyright rests with its author and that no part of it may be reproduced without the author’s prior written consent. SYMPLECTIC ELASTICITY APPROACH FOR EXACT BENDING SOLUTIONS OF RECTANGULAR THIN PLATES CUI SHUANG MASTER OF PHILOSOPHY CITY UNIVERSITY OF HONG KONG November 2007 CUI SHUANG RECTANGULAR TH FOR EXACT BENDING SOLUTIONS OF SYMPLECTIC ELASTICITY APPROACH IN PLATES MPhil 2007 CityU CITY UNIVERSITY OF HONG KONG 香港城市大學 SYMPLECTIC ELASTICITY APPROACH FOR EXACT BENDING SOLUTIONS OF RECTANGULAR THIN PLATES 辛彈性力學方法在矩形薄板的彎曲精確解 上的應用 Submitted to Department of Building and Construction 建築學系 in Partial Fulfillment of the Requirements for the Degree of Master of Philosophy 哲學碩士學位 by Cui Shuang 崔爽 November 2007 二零零七年十一月 i Abstract This thesis presents a bridging analysis for combining the modeling methodology of quantum mechanics/relativity with that of elasticity. Using the symplectic method that is commonly applied in quantum mechanics and relativity, a new symplectic elasticity approach is developed for deriving exact analytical solutions to some basic problems in solid mechanics and elasticity that have long been stumbling blocks in the history of elasticity. Specifically, the approach is applied to the bending problem of rectangular thin plates the exact solutions for which have been hitherto unavailable. The approach employs the Hamiltonian principle with Legendre’s transformation. Analytical bending solutions are obtained by eigenvalue analysis and the expansion of eigenfunctions. Here, bending analysis requires the solving of an eigenvalue equation, unlike the case of classical mechanics in which eigenvalue analysis is required only for vibration and buckling problems. -
On Generalized Cosserat-Type Theories of Plates and Shells: a Short Review and Bibliography Johannes Altenbach, Holm Altenbach, Victor Eremeyev
On generalized Cosserat-type theories of plates and shells: a short review and bibliography Johannes Altenbach, Holm Altenbach, Victor Eremeyev To cite this version: Johannes Altenbach, Holm Altenbach, Victor Eremeyev. On generalized Cosserat-type theories of plates and shells: a short review and bibliography. Archive of Applied Mechanics, Springer Verlag, 2010, 80 (1), pp.73-92. hal-00827365 HAL Id: hal-00827365 https://hal.archives-ouvertes.fr/hal-00827365 Submitted on 29 May 2013 HAL is a multi-disciplinary open access L’archive ouverte pluridisciplinaire HAL, est archive for the deposit and dissemination of sci- destinée au dépôt et à la diffusion de documents entific research documents, whether they are pub- scientifiques de niveau recherche, publiés ou non, lished or not. The documents may come from émanant des établissements d’enseignement et de teaching and research institutions in France or recherche français ou étrangers, des laboratoires abroad, or from public or private research centers. publics ou privés. 74 J. Altenbach et al. and rotations (and by analogy of forces and couples or force and moment stresses) is stated, see, e.g., [307]. Historically the first scientist, who obtained similar results, was L. Euler. Discussing one of Langrange’s papers he established that the foundations of Mechanics are based on two principles: the principle of momentum and the principle of moment of momentum. Both principles results in the Eulerian laws of motion [307]. In [214] is given the following comment: the independence of the principle of moment of momentum, which is a generalization of the static equilibrium of the moments, was established by Jacob Bernoulli (1686) one year before Newton’s laws (1687). -
FE-Modeling of Bolted Joints in Structures Master Thesis in Solid Mechanics Alexandra Korolija
Department of Management and Engineering Master of Science in Mechanical Engineering LIU-IEI-TEK-A—12/014446-SE FE-modeling of bolted joints in structures Master Thesis in Solid Mechanics Alexandra Korolija Linköping 2012 Supervisor: Zlatan Kapidzic Saab Aeronautics Supervisor: Sören Sjöström IEI, Linköping University Examiner: Kjell Simonsson IEI, Linköping University Division of Solid Mechanics Department of Mechanical Engineering Linköping University 581 83 Linköping, Sweden Datum Date 2012-09-04 Avdelning, Institution Division, Department Div of Solid Mechanics Dept of Mechanical Engineering SE-581 83 LINKÖPING Språk Rapporttyp Serietitel och serienummer Language Report category Title of series, Engelska / English ISRN nummer Antal sidor Examensarbete LIU-IEI-TEK-A—12/014446-SE 56 Titel FE modeling of bolted joints in structures Title Författare Alexandra Korolija Author Sammanfattning Abstract This paper presents the development of a finite element method for modeling fastener joints in aircraft structures. By using connector element in commercial software Abaqus, the finite element method can handle multi-bolt joints and secondary bending. The plates in the joints are modeled with shell elements or solid elements. First, a pre-study with linear elastic analyses is performed. The study is focused on the influence of using different connector element stiffness predicted by semi-empirical flexibility equations from the aircraft industry. The influence of using a surface coupling tool is also investigated, and proved to work well for solid models and not so well for shell models, according to a comparison with a benchmark model. Second, also in the pre-study, an elasto-plastic analysis and a damage analysis are performed. -
Applied Elasticity & Plasticity 1. Basic Equations Of
APPLIED ELASTICITY & PLASTICITY 1. BASIC EQUATIONS OF ELASTICITY Introduction, The State of Stress at a Point, The State of Strain at a Point, Basic Equations of Elasticity, Methods of Solution of Elasticity Problems, Plane Stress, Plane Strain, Spherical Co-ordinates, Computer Program for Principal Stresses and Principal Planes. 2. TWO-DIMENSIONAL PROBLEMS IN CARTESIAN CO-ORDINATES Introduction, Airy’s Stress Function – Polynomials : Bending of a cantilever loaded at the end ; Bending of a beam by uniform load, Direct method for determining Airy polynomial : Cantilever having Udl and concentrated load of the free end; Simply supported rectangular beam under a triangular load, Fourier Series, Complex Potentials, Cauchy Integral Method , Fourier Transform Method, Real Potential Methods. 3. TWO-DIMENSIONAL PROBLEMS IN POLAR CO-ORDINATES Basic equations, Biharmonic equation, Solution of Biharmonic Equation for Axial Symmetry, General Solution of Biharmonic Equation, Saint Venant’s Principle, Thick Cylinder, Rotating Disc on cylinder, Stress-concentration due to a Circular Hole in a Stressed Plate (Kirsch Problem), Saint Venant’s Principle, Bending of a Curved Bar by a Force at the End. 4. TORSION OF PRISMATIC BARS Introduction, St. Venant’s Theory, Torsion of Hollow Cross-sections, Torsion of thin- walled tubes, Torsion of Hollow Bars, Analogous Methods, Torsion of Bars of Variable Diameter. 5. BENDING OF PRISMATIC BASE Introduction, Simple Bending, Unsymmetrical Bending, Shear Centre, Solution of Bending of Bars by Harmonic Functions, Solution of Bending Problems by Soap-Film Method. 6. BENDING OF PLATES Introduction, Cylindrical Bending of Rectangular Plates, Slope and Curvatures, Lagrange Equilibrium Equation, Determination of Bending and Twisting Moments on any plane, Membrane Analogy for Bending of a Plate, Symmetrical Bending of a Circular Plate, Navier’s Solution for simply supported Rectangular Plates, Combined Bending and Stretching of Rectangular Plates. -
Bending Analysis of Simply Supported and Clamped Circular Plate P
SSRG International Journal of Civil Engineering (SSRG-IJCE) Volume 2 Issue 5–May 2015 Bending Analysis of Simply Supported and Clamped Circular Plate P. S. Gujar 1, K. B. Ladhane 2 1Department of Civil Engineering, Pravara Rural Engineering College, Loni,Ahmednagar-413713(University of Pune), Maharashtra, India. 2Associate Professor, Department of Civil Engineering, Pravara Rural Engineering College, Loni,Ahmednagar- 413713(University of Pune), Maharashtra, India. ABSTRACT : The aim of study is static bending appropriate plate theory. The stresses in the plate can analysis of an isotropic circular plate using be calculated from these deflections. Once the analytical method i.e. Classical Plate Theory and stresses are known, failure theories can be used to Finite Element software ANSYS. Circular plate determine whether a plate will fail under a given analysis is done in cylindrical coordinate system by load [1]. using Classical Plate Theory. The axisymmetric Vanam et al.[2] done static analysis of an bending of circular plate is considered in the present isotropic rectangular plate using finite element study. The diameter of circular plate, material analysis (FEA).The aim of study was static bending properties like modulus of elasticity (E), poissons analysis of an isotropic rectangular plate with ratio (µ) and intensity of loading is assumed at the various boundary conditions and various types of initial stage of research work. Both simply supported load applications. In this study finite element and clamped boundary conditions subjected to analysis has been carried out for an isotropic uniformly distributed load and center concentrated / rectangular plate by considering the master element point load have been considered in the present as a four noded quadrilateral element. -
The Bending and Stretching of Plates
The bending and stretching of plates The bending and stretching of plates Second edition E. H. MANSFIELD Formerly Chief Scientific Officer Royal Aircraft Establishment Farnborough The right of the University of Cambridge to print and sell all manner of books was granted by Henry VIII in IS34. The University has printed and published continuously since IS84. CAMBRIDGE UNIVERSITY PRESS CAMBRIDGE NEW YORK NEW ROCHELLE MELBOURNE SYDNEY CAMBRIDGE UNIVERSITY PRESS Cambridge, New York, Melbourne, Madrid, Cape Town, Singapore, Sao Paulo Cambridge University Press The Edinburgh Building, Cambridge CB2 2RU, UK Published in the United States of America by Cambridge University Press, New York www.cambridge.org Information on this title: www.cambridge.org/9780521333047 © Cambridge University Press 1989 This book is in copyright. Subject to statutory exception and to the provisions of relevant collective licensing agreements, no reproduction of any part may take place without the written permission of Cambridge University Press. First published 1964 by Pergamon Press Second edition first published 1989 This digitally printed first paperback version 2005 A catalogue record for this publication is available from the British Library Library of Congress Cataloguing in Publication data Mansfield, Eric Harold. 1923- The bending and stretching of plates/E.H. Mansfield. — 2nd ed. p. cm. Includes bibliographies and indexes. ISBN 0-521-33304-0 1. Elastic plates and shells. I. Title. QA935.M36 1989 88-29035 624.1'776-dc 19 CIP ISBN-13 978-0-521-33304-7 hardback ISBN-10 0-521-33304-0 hardback ISBN-13 978-0-521-01816-6 paperback ISBN-10 0-521-01816-1 paperback CONTENTS Preface page IX Principal notation X Part I. -
Moments and Reactions for Rectangular Plates
A WATER RESOURCES TECHNICAL PUBLICATION ENGINEERING MONOGRAPH NO. 27 Moments and Reactions for Rectangular Plates UNITED STATES DEPARTMENT OF THE INTERIOR BUREAU OF RECLAMATION A WATER RESOURCES TECHNICAL PUBLICATION Engineering Monograph NO. P7 Moments and Reactions for Rectangular Plates By W. T. MOODY Division of Design Denver, Colorado United States Department of the Interior BUREAU OF RECLAMATION As the Nation’s principal conservation agency, the Department of the Interior has responsibility for most of our nationally owned public lands and natural resources. This includes fostering the wisest use of our land and water resources, protecting our fish and wildlife, preserv- ing the environmental and cultural values of our national parks and historical places, and providing for the enjoyment of life through out- door recreation. The Department assesses our energy and mineral resources and works to assure that their development is in the best interests of all our people. The Department also has a major respon- sibility for American Indian reservation communities and for people who live in Island Territories under U.S. Administration. First Printing: October 1963 Revised: July 1963 Reprinted: April 1966 Reprinted: July 1970 Reprinted: June 1975 Reprinted: December 1976 Reprinted: January 1978 Reprinted: April 1980 Reprinted: March 1983 Reprinted: June 1986 Reprinted: August 1990 U.S. GOVERNMENT PRINTING OFFICE WASHINGTON : 1978 Preface THIS MONOGRAPH presents a series of tables con- As supplementary guides to the use and devel- taining computed data for use in the design of opment of the data compiled in this monograph, components of structures which can be idealized two appendixes are included. The first appendix as rectangular plates or slabs. -
A Study of Large Deflection of Beams and Plates
A STUDY OF LARGE DEFLECTION OF BEAMS AND PLATES BY VINESH V. NISHAWALA A thesis submitted to the Graduate School—New Brunswick Rutgers, The State University of New Jersey in partial fulfillment of the requirements for the degree of Master of Science Graduate Program in Mechanical and Aerospace Engineering Written under the direction of Dr. Haim Baruh and approved by New Brunswick, New Jersey January, 2011 c 2011 Vinesh V. Nishawala ALL RIGHTS RESERVED ABSTRACT OF THE THESIS A Study of Large Deflection of Beams and Plates by Vinesh V. Nishawala Thesis Director: Dr. Haim Baruh For a thin plate or beam, if the deformation is on the order of the thickness and remain elastic, linear theory may not produce accurate results as it does not predict the in plane movement of the member. Therefore, a geometrically nonlinear, large deforma- tion theory is required to account for the inconsistencies. This thesis discusses nonlinear bending and vibrations of simply-supported beams and plates. Theoretical results are compared with other well-known solutions. The effects of geometric nonlinearities are discussed. The equation of motion for plates with ‘stress-free’ and ‘immovable’ edges are derived using modal analysis in conjunction with the expansion theorem. Theo- retical results are compared with a finite element simulation for plates. ‘Immovable’ edges are studied for beams. For large bending of beams with ‘stress-free’ edges, a the- ory by Conway is presented. A brief introduction to Duffing’s equation and Gaussian curvature is presented and their relevance to nonlinear deformations are discussed. ii Nomenclature δ¯ Dirac delta function ρ¯ Density - mass per unit volume κij Curvature ij A generic basis B 2 Biharmonic operator ∇ ν Poission’s ratio Ω Excitationfrequency ωij Natural frequency φ Airy’s stress function ρ Plate: mass per unit area (=ρh ¯ ). -
Bending Analysis of Thick Isotropic Plates by Using 5Th Order Shear Deformation Theory
Journal of Applied and Computational Mechanics, Vol. 2, No. 2, (2016), 80-95 Bending Analysis of Thick Isotropic Plates by Using 5th Order Shear Deformation Theory Yuwaraj M. Ghugal, Param D. Gajbhiye Department of Applied Mechanics, Government Engineering College, Karad, Satara-415124, M.S., India Received September 25 2016; revised October 26 2016; accepted for publication October 27 2016. Corresponding author: Yuwaraj M. Ghugal, [email protected] Abstract A 5th order shear deformation theory considering transverse shear deformation effect as well as transverse normal strain deformation effect is presented for static flexure analysis of simply supported isotropic plate. The assumed displacement field accounts for non-linear variation of in-plane displacements as well as transverse displacement through the plate thickness. The condition of zero transverse shear stresses on the upper and lower surface of plate is satisfied. Hence the present formulation does not require the shear correction factor generally associated with the first order shear deformable theory. Governing equations and boundary conditions of the theory are obtained using the principle of virtual work. Closed- form analytical solutions for simply supported square isotropic thick plates subjected to single sinusoidal distributed loads are obtained. Numerical results for static flexure analysis include the effects of side to thickness ratio and plate aspect ratio for simply supported isotropic plates. Numerical results are obtained using MATLAB programming. The results of present theory are in close agreement with those of higher order shear deformation theories and exact 3D elasticity solutions. Keywords: Thick isotropic plate, 5th order shear deformation theory, static flexure, transverse shear stress, transverse normal stress, Navier solution. -
On the Linear Theory of Micropolar Plates Holm Altenbach, Victor Eremeyev
On the linear theory of micropolar plates Holm Altenbach, Victor Eremeyev To cite this version: Holm Altenbach, Victor Eremeyev. On the linear theory of micropolar plates. Journal of Applied Mathematics and Mechanics / Zeitschrift für Angewandte Mathematik und Mechanik, Wiley-VCH Verlag, 2009, 89 (4), pp.242-256. hal-00824928 HAL Id: hal-00824928 https://hal.archives-ouvertes.fr/hal-00824928 Submitted on 22 May 2013 HAL is a multi-disciplinary open access L’archive ouverte pluridisciplinaire HAL, est archive for the deposit and dissemination of sci- destinée au dépôt et à la diffusion de documents entific research documents, whether they are pub- scientifiques de niveau recherche, publiés ou non, lished or not. The documents may come from émanant des établissements d’enseignement et de teaching and research institutions in France or recherche français ou étrangers, des laboratoires abroad, or from public or private research centers. publics ou privés. ZAMM · Z. Angew. Math. Mech. 89, No. 4 (2009) / www.zamm-journal.org 243 theory is based on eight unknowns: the averaged displacements, the averaged macrorotations of the cross-sections, and the averaged microrotations. This means that one has to introduce eight boundary conditions. The static boundary conditions in Eringen’s plate cannot be presented as forces and moments at the boundaries like in the Kirchhoff type theories [70]. From the point of view of the direct approach Eringen’s micropolar plate is a deformable surface with eight degrees of freedom. The theories of plates and shells and the theories based on the reduction of the three-dimensional equations of the micropolar continuum are presented in various publications. -
Mechanics of Contact Between Bi-Material Elastic Solids Perturbed by a flexible Interface† Downloaded from A
IMA Journal of Applied Mathematics Advance Access published February 20, 2014 IMA Journal of Applied Mathematics (2014) Page 1 of 14 doi:10.1093/imamat/hxu001 Mechanics of contact between bi-material elastic solids perturbed by a flexible interface† Downloaded from A. P. S. Selvadurai Department of Civil Engineering and Applied Mechanics, McGill University, 817 Sherbrooke Street West, Montreal, QC., Canada H3A 0C3 [email protected] http://imamat.oxfordjournals.org/ [Received on 21 November 2013; revised on 6 January 2014; accepted on 10 January 2014] This paper generalizes the classical result of R.D. Mindlin for the axisymmetric problem related to the action of a concentrated force at the interior of an isotropic elastic half-space to include a bi-material region that is perturbed by an interface exhibiting flexural behaviour. The flexural behaviour of the inter- face is described by a Germain–Poisson–Kirchhoff thin plate theory. A Hankel integral transform tech- nique is used to obtain an explicit result for the deflection of the flexural interface. The reduction of the solution to conventional results associated with both half-space problems and infinite space problems is indicated. Formal results are also presented for the case where the flexural behaviour of the plate is modelled by the plate theory proposed by E. Reissner. at PontifÃcia Universidade Católica do Rio de Janeiro on February 21, 2014 Keywords: Mindlin’s problem; Kelvin’s problem; bi-material Infinite space; integral transforms; embed- ded plate; thin plate theory; flexural deflections of a stiffened interface. 1. Introduction The problem of an isotropic elastic solid that is internally loaded by a concentrated force was first examined by Kelvin (1848). -
Introduction to the Theory of Plates
Introduction to the Theory of Plates http://www.stanford.edu/~chasst/Course%20Notes/PlatesBook... Introduction to the Theory of Plates Charles R. Steele and Chad D. Balch Division of Mechanics and Computation Department of Mecanical Engineering Stanford University Stretching and Bending of Plates - Fundamentals Introduction A plate is a structural element which is thin and flat. By “thin,” it is meant that the plate’s transverse dimension, or thickness, is small compared to the length and width dimensions. A mathematical expression of this idea is: where t represents the plate’s thickness, and L represents a representative length or width dimension. (See Fig. See Plate and associated (x, y, z) coordinate system...) More exactly, L represents the minimum wave length of deformation, which can be much smaller than the plate minimum lateral dimension for problems of localized loading, dynamics and stability. Plates might be classified as very thin if Łt > 100, moderately thin if 20 < Łt < 100, thick if 3 < Łt < 20, and very thick if Łt < 3. The “classical” theory of plates is applicable to very thin and moderately thin plates, while “higher order theories” for thick plates are useful. For the very thick plates, however, it becomes more difficult and less useful to view the structural element as a plate - a description based on the three-dimensional theory of elasticity is required. 1 of 41 4/2/09 2:20 PM Introduction to the Theory of Plates http://www.stanford.edu/~chasst/Course%20Notes/PlatesBook... FIGURE 1.1. Plate and associated (x, y, z) coordinate system. In this chapter, we derive the basic equations which describe the behavior of plates taking advantage of the plate’s thin, planar character.