Titanium Diboride Thin Films by Low-Temperature Chemical Vapor Deposition from the Single Source Precursor Ti(BH4)3(1,2-Dimethoxyethane)
Total Page:16
File Type:pdf, Size:1020Kb
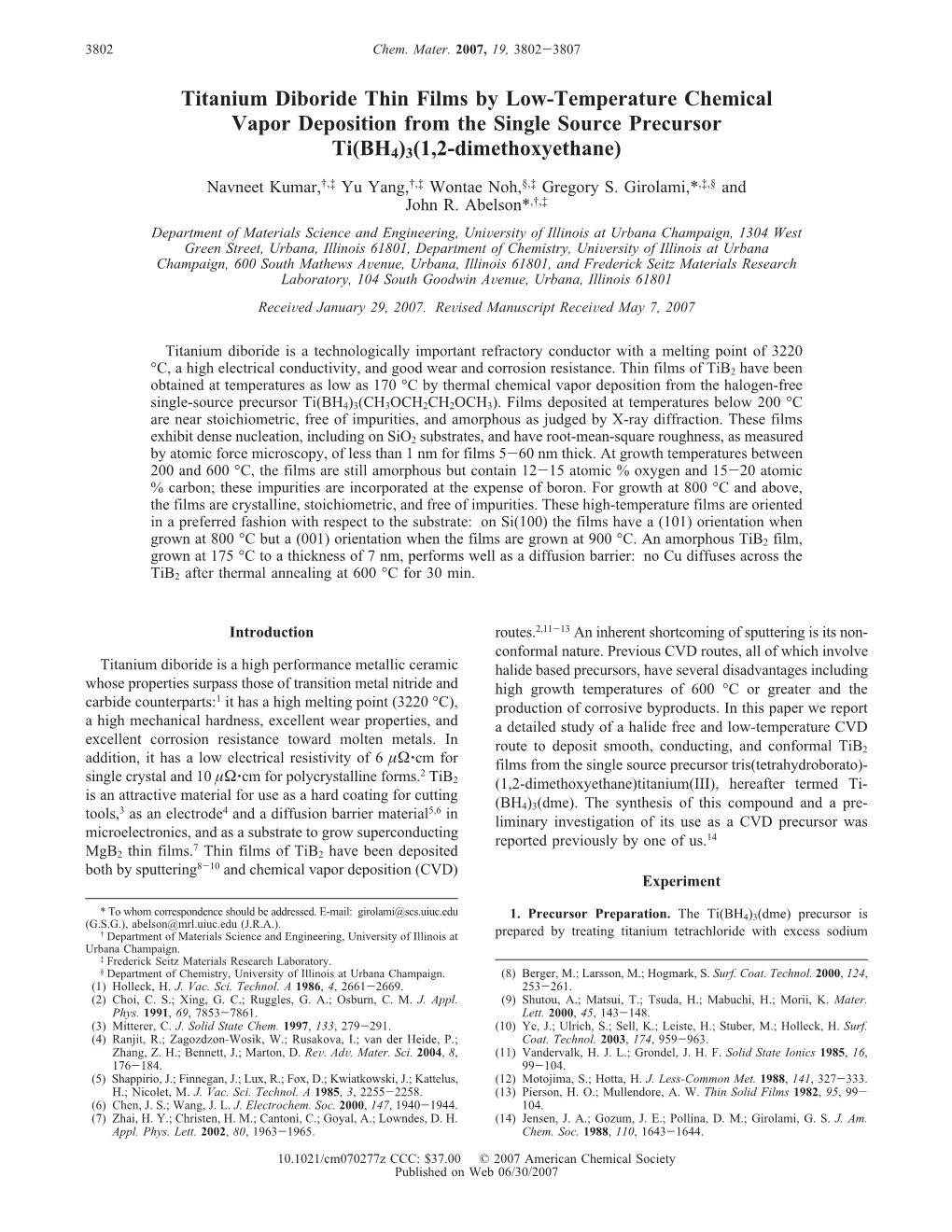
Load more
Recommended publications
-
Grain Refinement of Aluminium by Titanium Diboride Particles
EXAMENSARBETE INOM KEMIVETENSKAP, AVANCERAD NIVÅ, 30 HP STOCKHOLM, SVERIGE 2019 Grain refinement of aluminium by titanium diboride particles The importance of nucleation, growth restriction, and cooling rate SOFIA CARLSSON KTH SKOLAN FÖR INDUSTRIELL TEKNIK OCH MANAGEMENT ABSTRACT The grain refinement of aluminium by titanium diboride particles, TiB2, using Ti/B grain refiners is common practice in the aluminium industry, but exactly how this grain refinement is achieved is uncertain. Current addition of grain refiner is therefore rarely optimal and excessive addition rates of grain refiner is common. This study investigates grain refinement of aluminium by titanium diboride to create a method and/or model which can be used to aid in addition rate optimisation. The effect of different parameters on grain refinement is the focus and includes cooling rate, properties of the nucleant particles, and growth restriction. A number of experiments using different test methods was applied to investigate this. The study reveals how the parameters investigated affect grain refinement, and how these can be used to optimises grain refiner addition rate. A model aiding in dealing with the varying abilities of nominally identical grain refiners to produce grains is introduced. The conclusion emphasizes the importance of optimising addition rates of grain refiners, for mechanical as well as environmental reasons, and how this can be achieved by changing the investigated parameters. SAMMANFATTNING Kornförfining av aluminium med titandiboridpartiklar, TiB2, genom användning av Ti/B kornförfinare är standard inom aluminiumindustrin. Det är dock inte helt utrett hur denna kornförfining går till. Rådande tillsatsmängder av kornförfinare är därför sällan optimala och alltför stora tillsatsmängder av kornförfinare är vanligt förkommande. -
Fabrication of Tib2–Al1050 Composites with Improved Microstructural and Mechanical Properties by a Liquid Pressing Infiltration Process
materials Article Fabrication of TiB2–Al1050 Composites with Improved Microstructural and Mechanical Properties by a Liquid Pressing Infiltration Process Seongmin Ko 1,2, Hyeonjae Park 3, Yeong-Hwan Lee 1,2, Sangmin Shin 1,2, Ilguk Jo 3, Junghwan Kim 1, Sang-Bok Lee 1, Yangdo Kim 2,*, Sang-Kwan Lee 1,* and Seungchan Cho 1,* 1 Composites Research Division, Korea Institute of Materials Science (KIMS), Changwon 51508, Korea; [email protected] (S.K.); [email protected] (Y.-H.L.); [email protected] (S.S.); [email protected] (J.K.); [email protected] (S.-B.L.) 2 School of Materials Science and Engineering, Pusan National University, Busan 46241, Korea 3 Advanced Materials Engineering, Dong-Eui University, Busan 47340, Korea; [email protected] (H.P.); [email protected] (I.J.) * Correspondence: [email protected] (Y.K.); [email protected] (S.-K.L.); [email protected] (S.C.) Received: 9 March 2020; Accepted: 25 March 2020; Published: 30 March 2020 Abstract: This study was conducted on titanium diboride (TiB2) reinforced Al metal matrix composites (MMCs) with improved properties using a TiB2 and aluminum (Al) 1050 alloy. Al composites reinforced with fine TiB2 at volume ratios of more than 60% were successfully fabricated via the liquid pressing infiltration (LPI) process, which can be used to apply gas pressure at a high temperature. The microstructure of the TiB2–Al composite fabricated at 1000 ◦C with pressurization of 10 bar for 1 h showed that molten Al effectively infiltrated into the high volume-fraction TiB2 preform due to the improved wettability and external gas pressurization. -
UCLA Electronic Theses and Dissertations
UCLA UCLA Electronic Theses and Dissertations Title Synthesis, Structure, and Properties of Refractory Hard-Metal Borides Permalink https://escholarship.org/uc/item/1hv5m731 Author Lech, Andrew Thomas Publication Date 2014 Peer reviewed|Thesis/dissertation eScholarship.org Powered by the California Digital Library University of California UNIVERSITY OF CALIFORNIA Los Angeles Synthesis, Structure, and Properties of Refractory Hard-Metal Borides A dissertation submitted in partial satisfaction of the requirements for the degree of Doctor of Philosophy in Chemistry by Andrew Thomas Lech 2014 ©Copyright by Andrew Thomas Lech 2014 ABSTRACT OF THE DISSERTATION Synthesis, Structure, and Properties of Refractory Hard-Metal Borides by Andrew Thomas Lech Doctor of Philosophy in Chemistry University of California, Los Angeles, 2014 Professor Richard B. Kaner, Chair As the limits of what can be achieved with conventional hard compounds, such as tungsten carbide, are nearing reach, super-hard materials are an area of increasing industrial interest. The refractory hard metal borides, such as ReB 2 and WB 4, offer an increasingly attractive alternative to diamond and cubic boron nitride as a next-generation tool material. In this Thesis, a thorough discussion is made of the progress achieved by our laboratory towards understanding the synthesis, structure, and properties of these extremely hard compounds. Particular emphasis is placed on structural manipulation, solid solution formation, and the unique crystallographic manifestations of what might also be called “super- hard metals”. ii The dissertation of Andrew Thomas Lech is approved. ____________________________________________ Sarah Tolbert ____________________________________________ Vijay Gupta ____________________________________________ Richard B. Kaner, Committee Chair University of California, Los Angeles 2014 iii TABLE OF CONTENTS ABSTRACT OF THE DISSERTATION ......................................................................................................................... -
Titanium Diboride Metal Matrix Hybrid Nanocomposite Afsaneh Dorri Moghdam University of Wisconsin-Milwaukee
University of Wisconsin Milwaukee UWM Digital Commons Theses and Dissertations May 2016 In-Situ Synthesis of Aluminum- Titanium Diboride Metal Matrix Hybrid Nanocomposite Afsaneh Dorri Moghdam University of Wisconsin-Milwaukee Follow this and additional works at: https://dc.uwm.edu/etd Part of the Materials Science and Engineering Commons Recommended Citation Dorri Moghdam, Afsaneh, "In-Situ Synthesis of Aluminum- Titanium Diboride Metal Matrix Hybrid Nanocomposite" (2016). Theses and Dissertations. 1137. https://dc.uwm.edu/etd/1137 This Dissertation is brought to you for free and open access by UWM Digital Commons. It has been accepted for inclusion in Theses and Dissertations by an authorized administrator of UWM Digital Commons. For more information, please contact [email protected]. IN-SITU SYNTHESIS OF ALUMINUM- TITANIUM DIBORIDE METAL MATRIX HYBRID NANOCOMPOSITE by Afsaneh Dorri Moghadam A Dissertation Submitted in Partial Fulfillment of the Requirements for the degree of Doctor of Philosophy in Engineering at The University of Wisconsin-Milwaukee May 2016 ABSTRACT IN-SITU SYNTHESIS OF ALUMINUM- TITANIUM DIBORIDE METAL MATRIX HYBRID NANOCOMPOSITE by Afsaneh Dorri Moghadam The University of Wisconsin-Milwaukee, 2016 Under the Supervision of Professor Pradeep K. Rohatgi Metal matrix nanocomposites (MMNC’s) are reported to have improved mechanical, thermal and electrical properties as compared to their respective base alloys. To date, these materials have been synthesized mainly by powder metallurgy or deformation processing. Solidification -
Titanium Diboride Ceramics for Solar Thermal Absorbers
Paper published on: Solar Energy Materials and Solar Cells, Volume 169 (2017) Pages 313-319 https://doi.org/10.1016/j.solmat.2017.05.038 http://www.sciencedirect.com/science/article/pii/S0927024817302556 Titanium diboride ceramics for solar thermal absorbers Elisa Sani*, Marco Meucci, Luca Mercatelli CNR-INO National Institute of Optics, Largo E. Fermi, 6, I-50125 Firenze, Italy Andrea Balbo Corrosion and Metallurgy Study Centre “Aldo Daccò”, Engineering Department, University of Ferrara, G. Saragat 4a, Ferrara 44122, Italy & ISTEC-CNR, Institute of Science and Technology for Ceramics, Via Granarolo 64, Faenza 48018, Italy; Clara Musa, Roberta Licheri, Roberto Orrù, Giacomo Cao Dipartimento di Ingegneria Meccanica, Chimica e dei Materiali, Unità di Ricerca del Consorzio Interuniversitario Nazionale per la Scienza e Tecnologia dei Materiali (INSTM), Università degli Studi di Cagliari, Piazza D’Armi, 09123 Cagliari, Italy * Corresponding author, email:[email protected] Abstract Titanium diboride (TiB2) is a low-density refractory material belonging to the family of ultra-high temperature ceramics (UHTCs). This paper reports on the production and microstructural and optical characterization of nearly fully dense TiB2, with particular interest to its potential utilization as novel thermal solar absorber. Monolithic bulk samples are produced starting from elemental reactants by a two-step method consisting of the Self-propagating High-temperature Synthesis (SHS) followed by the Spark Plasma Sintering (SPS) of the resulting powders. The surface of obtained samples has-been characterized from the microstructural and topological points of view. The hemispherical reflectance spectrum has been measured from 0.3 to 15 µm wavelength, to evaluate the potential of this material as solar absorber for future concentrating solar plants. -
Carbothermic Synthesis of Titanium Diboride: Upgrade
View metadata, citation and similar papers at core.ac.uk brought to you by CORE provided by Siberian Federal University Digital Repository Journal of Siberian Federal University. Chemistry 2 (2018 11) 156-166 ~ ~ ~ УДК 666.3-135 Carbothermic Synthesis of Titanium Diboride: Upgrade Evgeniy S. Gorlanova, Vladimir Yu. Bazhin*b and Sergey N. Fedorovb a“Expert-Al” LLC 5-7 20-th line, V.O., St. Petersburg, 199106, Russia bSt. Petersburg Mining University 2 21-th line, V.O., St. Petersburg, 199106, Russia Received 15.01.2018, received in revised form 17.01.2018, accepted 26.03.2018 The technology of carbothermic reduction of titanium and boron oxides in the TiО2-B2О3-C reaction mixture at temperatures up to 1070 °C is presented. The temperature and atmospheric regimes of low- temperature reduction of TiO2 are determined. In the Ti-B-O-C system, successive phase formation of TiО2→TinO2n-1→TiBО3→TiCxO1-x→TiB2 at 1030 ÷ 1050 °C was realized, which was recorded by X-ray phase analysis of the samples after synthesis. The conditions for the realization of low-temperature synthesis are established, which consist in observing the prescriptions and special regimes for preparing the reaction mixture, the conditions for heating and holding the samples in a controlled atmosphere. For discussion, the mechanism of oxycarboboride phases formation at each of the stages of reduction of activated titanium oxide is presented. The principal possibility of low-temperature synthesis of TiB2 in the composition of carbon-graphite products by free pitch technology in the conditions of existing kilns is shown. Keywords: sol-gel technology, anatase-rutile transformation, phase formation, low-temperature synthesis, titanium oxycarbide, titanium diboride, dynamic vacuum, controlled atmosphere. -
The Microstructure of Nanocrystalline Tib2 Films Prepared by Chemical Vapor Deposition
materials Article The Microstructure of Nanocrystalline TiB2 Films Prepared by Chemical Vapor Deposition Xiaoxiao Huang, Shuchen Sun *, Ganfeng Tu, Shuaidan Lu, Kuanhe Li and Xiaoping Zhu School of Metallurgy, Northeastern University, No. 3-11, Wenhua Road, Heping District, Shenyang 110819, China; [email protected] (X.H.); [email protected] (G.T.); [email protected] (S.L.); [email protected] (K.L.); [email protected] (X.Z.) * Correspondence: [email protected]; Tel.: +86-024-8368-9195 Received: 7 November 2017; Accepted: 11 December 2017; Published: 13 December 2017 Abstract: Nanocrystalline titanium diboride (TiB2) ceramics films were prepared on a high purity graphite substrate via chemical vapor deposition (CVD). The substrate was synthesized by a gas ◦ mixture of TiCl4, BCl3, and H2 under 1000 C and 10 Pa. Properties and microstructures of TiB2 films were also examined. The as-deposited TiB2 films had a nano-sized grain structure and the grain size was around 60 nm, which was determined by X-ray diffraction, field emission scanning electron microscopy, and transmission electron microscopy. Further research found that a gas flow ratio of TiCl4/BCl3 had an influence on the film properties and microstructures. The analyzed results illustrated that the grain size of the TiB2 film obtained with a TiCl4/BCl3 gas flow ratio of 1, was larger than the grain size of the as-prepared TiB2 film prepared with a stoichiometric TiCl4/BCl3 gas flow ratio of 0.5. In addition, the films deposited faster at excessive TiCl4. However, under the condition of different TiCl4/BCl3 gas flow ratios, all of the as-prepared TiB2 films have a preferential orientation growth in the (100) direction. -
Titanium Diboride Reinforced Boron Carbide
UNCLASSIFIED Titanium Diboride Reinforced Boron Carbide Azmi M. Celik, Dr. Chawon Hwang, Dr. Vladislav Domnich, Dr. Atta Ullah Khan, Dr. Richard A. Haber Enterprise for Mul/-scale Research of Materials Rutgers, The State University of New Jersey How We Fit Major Results Major Results (Continued) Materials-by-Design Process Mechanism-based Approach Microstructure Evaluation & Vickers Hardness (HP) Crack Propagation Behavior (SPS) B4C TiB2 B4C crack branching intergranular transgranular 1/2 Sample Hv(1kg), GPa Std. dev. KIc, MPa.m Std. dev. Monolithic B4C 30.03 1.50 2.30 0.19 B4C + 10wt%TiB2 32.92 1.47 2.77 0.51 Spark Plasma Sintering Conditions: 1950ºC, 5 minutes, 50 MPa Grain size: ~10-20 µm TiB addition inhibits the grain growth of B C Key Goals 2 4 Key Accomplishments B4C+10wt% TiB2 • Improve mechanical properties and investigate toughening • Composites with improved toughness were produced mechanisms of boron carbide-titanium diboride composites • Hot press was utilized to fabricate large samples (up to ø6”) • Fabricate industry-scale samples via Hot Press • Grain growth in B4C was suppressed by TiB2 addition (HP) Technical Approach Transitions to ARL, within TiB2 B4C CMRG and to other CMRGs To improve its resistance to crack propagation, boron • Ballistic impact tests on hot pressed plates to investigate carbide (B4C) was reinforced with titanium diboride (TiB2). ballistic performance (ARL) Spark plasma sintering was utilized in preliminary work to • Kolsky bar expt. to examine fracture and fragmentation (JHU) investigate microstructure and crack propagation behavior. B4C Grain size: ~1-2 µm The most promising composition (B4C + 10wt%TiB2) was B4C Impact hot pressed to examine feasibility of large-scale production. -
Physical Properties of Various Conductive Diborides and Their Binaries Austin Harold Shaw Iowa State University
Iowa State University Capstones, Theses and Graduate Theses and Dissertations Dissertations 2015 Physical properties of various conductive diborides and their binaries Austin Harold Shaw Iowa State University Follow this and additional works at: https://lib.dr.iastate.edu/etd Part of the Materials Science and Engineering Commons, and the Mechanics of Materials Commons Recommended Citation Shaw, Austin Harold, "Physical properties of various conductive diborides and their binaries" (2015). Graduate Theses and Dissertations. 14496. https://lib.dr.iastate.edu/etd/14496 This Dissertation is brought to you for free and open access by the Iowa State University Capstones, Theses and Dissertations at Iowa State University Digital Repository. It has been accepted for inclusion in Graduate Theses and Dissertations by an authorized administrator of Iowa State University Digital Repository. For more information, please contact [email protected]. Physical properties of various conductive metal diborides and their binaries by Austin Harold Shaw A dissertation submitted to the graduate faculty in partial fulfillment of the requirements for the degree of DOCTOR OF PHILOSOPHY Major: Materials Science and Engineering Program of Study Committee: Alan Russell, Major Professor Iver Anderson Ashraf Bastawros Scott Beckman Terrence Meyer Iowa State University Ames, Iowa 2015 Copyright © Austin Harold Shaw, 2015. All rights reserved. ii TABLE OF CONTENTS ABSTRACT iii CHAPTER 1: INTRODUCTION 1 CHAPTER 2: EXPERIMENTAL PROCEDURE 17 CHAPTER 3: RESULTS AND DISCUSSION 22 CHAPTER 4: CONCLUSION 57 CHAPTER 5: FUTURE WORK 60 APPENDIX 1: XRD ANALYSES 61 APPENDIX 2: TERNARY PHASE DIAGRAMS 75 APPENDIX 3: LOOP ABRASION DATA 81 APPENDIX 4: COUNTER-FACE PROFILOMETRY DATA 109 REFERENCES 117 iii ABSTRACT Hard, wear-resistant materials have potential utility as both coatings and bulk components in wear-prone applications. -
Material Properties of Titanium Diboride
Volume 105, Number 5, Se ptember–October 2000 Journal of Research of the National Institute of Standards and Technology [J. Res. Natl. Inst. Stand. Technol. 105, 709-720 (2000)] Material Properties of Titanium Diboride Volume 105 Number 5 September–October 2000 Ronald G. Munro The physical, mechanical, and thermal Key words: evaluated data; material properties of polycrystalline TiB2 are properties; mechanical properties; physical National Institute of Standards and examined with an emphasis on the signifi- properties; thermal properties; titanium Technology, cant dependence of the properties on the diboride Gaithersburg, MD 20899-8520 density and grain size of the material . specimens. Using trend analysis, prop- [email protected] erty relations, and interpolation methods, a coherent set of trend values for the prop- Accepted: July 21, 2000 erties of polycrystalline TiB2 is determined for a mass fraction of TiB2 у 98 %, a density of (4.5Ϯ0.1) g/cm3, and a mean grain size of (9Ϯ1) m. Available online: http://www.nist.gov/jres 1. Introduction Titanium diboride (TiB2) is well known as a ceramic paper addresses the latter issue by examining the material with relatively high strength and durability as physical, mechanical, and thermal properties of TiB2 as characterized by the relatively high values of its melting a function of density and grain size. point, hardness, strength to density ratio, and wear This work extends the approach to data evaluation resistance [1]. Current use of this material, however, begun in previous studies on alumina [2] and silicon appears to be limited to specialized applications in such carbide [3]. The latter studies had a significant areas as impact resistant armor, cutting tools, crucibles, advantage over the present one, namely that the process- and wear resistant coatings. -
In Situ Formation of Tib2 in Fe-B System with Titanium Addition and Its Influence on Phase Composition, Sintering Process and Me
materials Article In Situ Formation of TiB2 in Fe-B System with Titanium Addition and Its Influence on Phase Composition, Sintering Process and Mechanical Properties Mateusz Skało ´n 1,2, Marek Hebda 2 , Benedikt Schrode 3 , Roland Resel 3 , Jan Kazior 2 and Christof Sommitsch 1,* 1 IMAT Institute of Materials Science, Joining and Forming, Graz University of Technology, Kopernikusgasse 24/1, 8010 Graz, Austria; [email protected] 2 Institute of Materials Engineering, Cracow University of Technology, 24 Warszawska ave, 31-155 Cracow, Poland; [email protected] (M.H.); [email protected] (J.K.) 3 Institute of Solid State Physics, Graz University of Technology, Petersgasse 16/II, 8010 Graz, Austria; [email protected] (B.S.); [email protected] (R.R.) * Correspondence: [email protected]; Tel.: +43-316-873-7180 Received: 20 July 2019; Accepted: 11 December 2019; Published: 13 December 2019 Abstract: Interaction of iron and boron at elevated temperatures results in the formation of an E (Fe + Fe2B) eutectic phase that plays a great role in enhancing mass transport phenomena during thermal annealing and therefore in the densification of sintered compacts. When cooled down, this phase solidifies as interconnected hard and brittle material consisting of a continuous network of Fe2B borides formed at the grain boundaries. To increase ductile behaviour, a change in precipitates’ stoichiometry was investigated by partially replacing iron borides by titanium borides. The powder of elemental titanium was introduced to blend of iron and boron powders in order to induce TiB2 in situ formation. Titanium addition influence on microstructure, phase composition, density and mechanical properties was investigated. -
Influence of Titanium Diboride Particle Size on Structure and Mechanical
metals Article Influence of Titanium Diboride Particle Size on Structure and Mechanical Properties of an Al-Mg Alloy Anton P. Khrustalyov 1,* , Alexander A. Kozulin 1, Ilya A. Zhukov 1, Marina G. Khmeleva 1 , Alexander B. Vorozhtsov 1, Dmitry Eskin 1,2, Suwaree Chankitmunkong 2,3, Vladimir V. Platov 1 and Sergey V. Vasilyev 4 1 Faculty of Physics and Engineering, National Research Tomsk State University, 634050 Tomsk, Russia; [email protected] (A.A.K.); [email protected] (I.A.Z.); [email protected] (M.G.K.); [email protected] (A.B.V.); [email protected] (V.V.P.); [email protected] (D.E.) 2 Brunel Centre for Advanced Solidification Technology, Brunel University London, Uxbridge, Middlesex UB8 3PH, UK; [email protected] 3 Department of Production Engineering, King Mongkut’s University of Technology Thonburi, Bangkok 10140, Thailand 4 Joint-Stock Company “Scientific-production concern” Mechanical engineering, 125212 Moscow, Russia; [email protected] * Correspondence: tofi[email protected]; Tel.: +79-52-155-5568 Received: 7 August 2019; Accepted: 20 September 2019; Published: 23 September 2019 Abstract: In the present study, aluminum alloys of the Al-Mg system with titanium diboride particles of different size distribution were obtained. The introduction of particles in the alloy was carried out using master alloys obtained through self-propagating high-temperature synthesis (SHS) process. The master alloys consisted of the intermetallic matrix Al-Ti with distributed TiB2 particles. The master alloys with TiB2 particles of different size distribution were introduced in the melt with simultaneous ultrasonic treatment, which allowed the grain refining of the aluminum alloy during subsequent solidification.