DEVELOPMENT of BATTERIES for IMPLANTABLE APPLICATIONS By
Total Page:16
File Type:pdf, Size:1020Kb
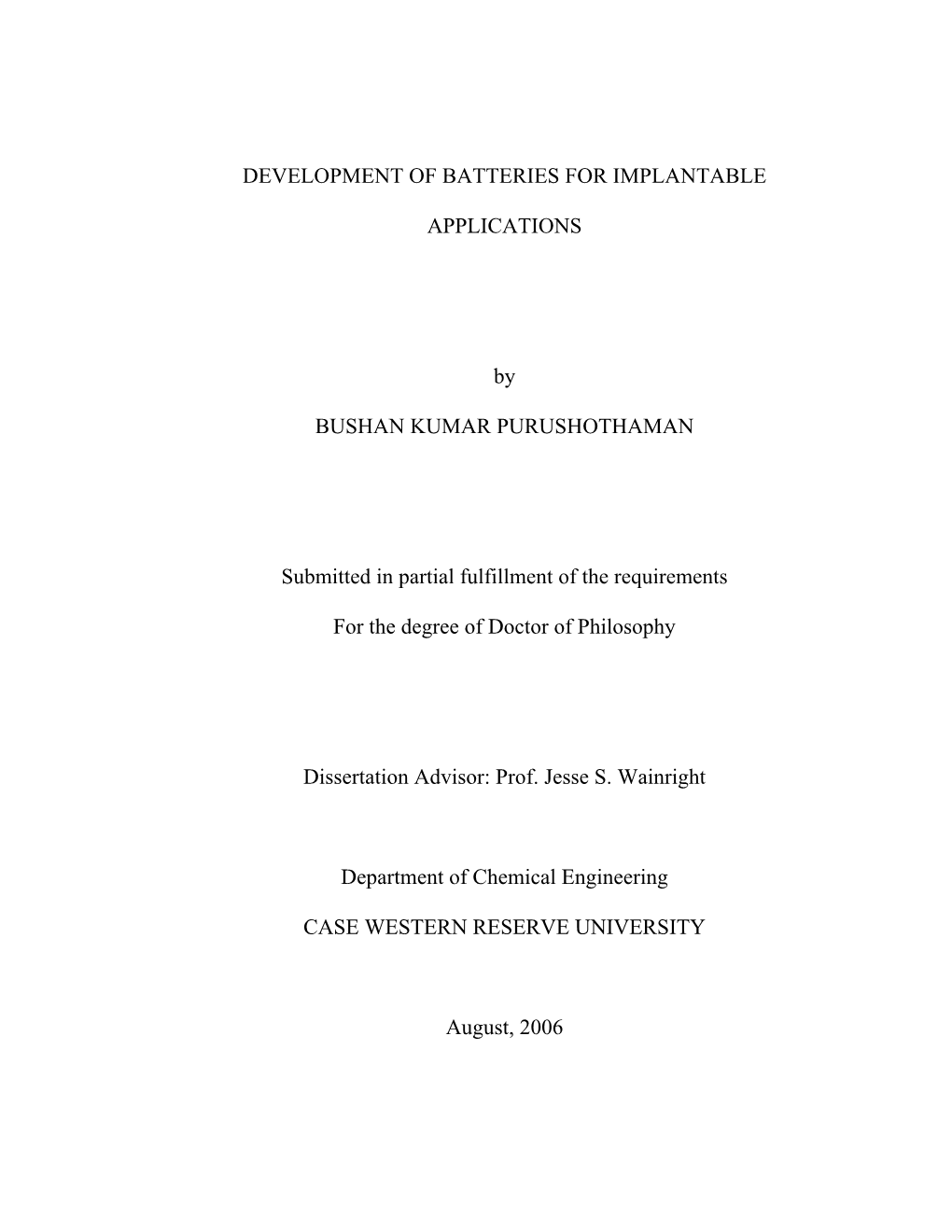
Load more
Recommended publications
-
Naming Coordination Compounds
Naming Coordination Compounds Author: Kit Mao Department of Chemistry, Washington University St. Louis, MO 63130 For information or comments on this tutorial, please contact K. Mao at [email protected]. Please click here for a pdf version of this tutorial. A coordination complex is a substance in which a metal atom or ion accepts electrons from (and thus associates with) a group of neutral molecules or anions called ligands. A complex can be an anion, a cation ion, or a neutral molecule. Coordination compounds are neutral substances (i.e. uncharged) in which at least one ion is present as a complex. You will learn more about coordination compounds in the lab lectures for experiment 5 in this course. The coordination compounds are named in the following way. (At the end of this tutorial, there are additional examples that demonstrate how coordination compounds are named.) A. When naming coordination compounds, always name the cation before the anion. This rule holds regardless of whether the complex ion is the cation or the anion. (This is just like naming an ionic compound.) B. In naming the complex ion: 1. Name the ligands first, in alphabetical order, and then name the metal atom or ion. Note: The metal atom or ion is written before the ligands in the chemical formula. 2. The names of some common ligands are listed in Table 1. · Anionic ligands end in “-o.” For anions that end in “-ide”(e.g. chloride, hydroxide), “-ate” (e.g. sulfate, nitrate), and “-ite” (e.g. nirite), change the endings as follows: -ide ® -o; e.g., chloride ® chloro and hydroxide ® hydroxo -ate ® -ato; e.g., sulfate ® sulfato and nitrate ® nitrato -ite ® -ito; e.g., nitrite ® nitrito · For neutral ligands, the common name of the molecule is used (e.g. -
Durable High Surface Area Electrodes for Rechargeable Zinc Air Batteries
Durable High Surface Area Electrodes for Rechargeable Zinc Air Batteries by Raihan Ahmed A thesis presented to the University of Waterloo in fulfillment of the thesis requirement for the degree of Master of Applied Science in Chemical Engineering Waterloo, Ontario, Canada, 2015 © Raihan Ahmed 2015 Author’s Declaration I hereby declare that I am the sole author of this thesis. This is a true copy of the thesis, including any required final revisions, as accepted by my examiners. I understand that my thesis may be made electronically available to the public. ii Abstract The fast growth in technology has led to an increase in demand for convenient storage of energy, primarily rechargeable batteries. People have shown significant interest in metal air batteries throughout history due to their high energy storage capacities, safety, and low cost. These batteries do not require the oxygen, one of their constituent fuels, to be stored inside the cell leading to high volumetric capacities. This is achievable due to the utilization of a unique gas diffusion electrode system that has a complex three phase interface regime. One of the safest and cheapest from the metal air family is the zinc air battery, zinc being one of the most abundant metals on earth. However, researchers have come across various challenges when dealing with these batteries and some of them include sluggish reaction rates, slow gas diffusion rates, and cell material degradation leading to poor power densities and charge-discharge cyclability. This work will address some of these issues via electrode and cell design optimization utilizing some of the proprietary technologies developed in the Applied Nanomaterials and Clean Energy Laboratory. -
Zinc Electrode Shape-Change in Secondary Air Batteries: a 2D Modeling Approach
Zinc Electrode Shape-Change in Secondary Air Batteries: A 2D Modeling Approach Tobias Schmitta,b,c, Tobias Arltd, Ingo Mankee, Arnulf Latza,b,c, Birger Horstmanna,b,c,∗ aGerman Aerospace Center, Pfaffenwaldring 38-40, 70569 Stuttgart, Germany bHelmholtz Institute Ulm, Helmholtzstraße 11, 89081 Ulm, Germany cUlm University, Institute of Electrochemistry, Albert-Einstein-Allee 47, 89069 Ulm, Germany dTechnical University of Berlin, Material Sciences and Technology, Hardenbergstraße 36, 10623 Berlin, Germany eHelmholtz Center for Materials and Energy, Hahn-Meitner-Platz 1, 14109 Berlin, Germany Abstract Zinc-air batteries offer large specific energy densities, while relying on abundant and non-toxic materials. In this paper, we present the first multi-dimensional simulations of zinc-air batteries. We refine our existing theory-based model of secondary zinc-air systems. The model comprises thermodynamically consistent multi-species transport in alkaline electrolytes, formation and disso- lution of metallic zinc and passivating zinc oxide, as well as multi-phase coexistence in gas diffusion electrodes. For the first time, we simulate zinc shape-change during battery cycling by modeling convection of zinc solids. We validate our model with in-situ tomography of commercial button cells. Two-dimensional volume-averaged simulations of cell voltage and zinc electrode morphology during discharge agree with these measurements. Thus, we can study how electrolyte carbonation limits shelf-life and how zinc shape-change limits cycle-life. The charging current is found to be the major contributor to cycle-life limitations. Finally, we optimize initial anode structure and charge-discharge protocols for improved performance and cycle-ability. Keywords: secondary zinc-air battery, aqueous alkaline electrolyte, simulation and validation, x-ray tomography, zinc shape-change 1. -
The Effect of Morphology on the Electrochemical Properties of Nanostructured Metal Oxide Thin Films: the Studies Based on Multi
The effect of morphology on the electrochemical properties of nanostructured metal oxide thin films : the studies based on multi-scale time-resolved fast electrogravimetric techniques Fatemeh Razzaghi To cite this version: Fatemeh Razzaghi. The effect of morphology on the electrochemical properties of nanostructured metal oxide thin films : the studies based on multi-scale time-resolved fast electrogravimetric techniques. Chemical Physics [physics.chem-ph]. Université Pierre et Marie Curie - Paris VI, 2016. English. NNT : 2016PA066346. tel-01477408 HAL Id: tel-01477408 https://tel.archives-ouvertes.fr/tel-01477408 Submitted on 27 Feb 2017 HAL is a multi-disciplinary open access L’archive ouverte pluridisciplinaire HAL, est archive for the deposit and dissemination of sci- destinée au dépôt et à la diffusion de documents entific research documents, whether they are pub- scientifiques de niveau recherche, publiés ou non, lished or not. The documents may come from émanant des établissements d’enseignement et de teaching and research institutions in France or recherche français ou étrangers, des laboratoires abroad, or from public or private research centers. publics ou privés. Thèse de doctorat Pour l’obtention du grade de Docteur De l’Université Pierre et Marie Curie École doctorale 388 - Chimie Physique et Chimie Analytique de Paris Centre The Effect of Morphology on the Electrochemical Properties of Nanostructured Metal Oxide Thin Films: The Studies based on Multi-scale Time-resolved Fast Electrogravimetric Techniques Par Fatemeh Razzaghi Directeur de thèse : Dr Hubert Perrot Présentée et soutenue publiquement le 29 septembre 2016, Devant un jury composé de : Nicole Jaffrezic DR CNRS Émérite Rapporteur Francois Tran-Van Prof. -
Development of Novel Thin Membrane Electrode Assemblies (Meas) for High-Efficiency Energy Storage
University of Tennessee, Knoxville TRACE: Tennessee Research and Creative Exchange Doctoral Dissertations Graduate School 5-2018 Development of Novel Thin Membrane Electrode Assemblies (MEAs) for High-Efficiency Energy Storage Zhenye Kang University of Tennessee, [email protected] Follow this and additional works at: https://trace.tennessee.edu/utk_graddiss Recommended Citation Kang, Zhenye, "Development of Novel Thin Membrane Electrode Assemblies (MEAs) for High-Efficiency Energy Storage. " PhD diss., University of Tennessee, 2018. https://trace.tennessee.edu/utk_graddiss/4863 This Dissertation is brought to you for free and open access by the Graduate School at TRACE: Tennessee Research and Creative Exchange. It has been accepted for inclusion in Doctoral Dissertations by an authorized administrator of TRACE: Tennessee Research and Creative Exchange. For more information, please contact [email protected]. To the Graduate Council: I am submitting herewith a dissertation written by Zhenye Kang entitled "Development of Novel Thin Membrane Electrode Assemblies (MEAs) for High-Efficiency Energy Storage." I have examined the final electronic copy of this dissertation for form and content and recommend that it be accepted in partial fulfillment of the equirr ements for the degree of Doctor of Philosophy, with a major in Mechanical Engineering. Feng-Yuan Zhang, Major Professor We have read this dissertation and recommend its acceptance: Lloyd M. Davis, Matthew M. Mench, Zhili Zhang Accepted for the Council: Dixie L. Thompson Vice Provost and Dean of the Graduate School (Original signatures are on file with official studentecor r ds.) Development of Novel Thin Membrane Electrode Assemblies (MEAs) for High-Efficiency Energy Storage A Dissertation Presented for the Doctor of Philosophy Degree The University of Tennessee, Knoxville Zhenye Kang May 2018 Copyright © 2018 by Zhenye Kang. -
Thulhu Muttur
THULHUUS009793542B2 MUTTUR (12 ) United States Patent ( 10 ) Patent No. : US 9 , 793 ,542 B2 Nelson et al. ( 45 ) Date of Patent: Oct . 17 , 2017 (54 ) BETA - DELITHIATED LAYERED NICKEL (58 ) Field of Classification Search OXIDE ELECTROCHEMICALLY ACTIVE CPC .. .. HO1M 4 /244 ; HOTM 4 / 366 ; HOTM 4 /52 ; CATHODE MATERIAL AND A BATTERY HOTM 4 / 131; HOTM 4 / 32 ; HO1M 4 / 525 INCLUDING SAID MATERIAL See application file for complete search history . ( 71 ) Applicant : DURACELL U . S . OPERATIONS, ( 56 ) References Cited ??? INC ., Wilmington , DE (US ) U . S . PATENT DOCUMENTS (72 ) Inventors : Jennifer Anne Nelson , Waltham , CT 2 , 956 , 860 A 10 / 1960 Welsh et al . ( US ) ; David Lloyd Anglin , Brookfield , 3 ,437 ,435 A 4 /1969 Moore et al . CT (US ) ; Mariarosa Brundu , Budduso (Continued ) (IT ) ; Paul Albert Christian , Norton , MA (US ) FOREIGN PATENT DOCUMENTS ( 73 ) Assignee : DURACELL U . S . OPERATIONS , 1263697 12 / 1989 INC . , Wilmington , DE (US ) 0 702 421 A1 3 / 1996 (Continued ) ( * ) Notice : Subject to any disclaimer, the term of this ???????? patent is extended or adjusted under 35 OTHER PUBLICATIONS U . S . C . 154 ( b ) by 213 days. PCT International Search Report with Written Opinion in corre ( 21) Appl. No .: 14 /625 ,876 sponding Int' l appln . PCT/ US2015 /021381 dated Aug . 11 , 2015 . ( 22 ) Filed : Feb . 19 , 2015 (Continued ) Primary Examiner — Stewart Fraser (65 ) Prior Publication Data Assistant Examiner — Rachel L Zhang (74 ) Attorney , Agent, or Firm — Marshall , Gerstein & US 2015 /0280234 A1 Oct . 1 , 2015 Borun LLP Related U . S . Application Data (57 ) ABSTRACT The invention is directed towards an electrochemically (60 ) Provisional application No . 61 / 971, 667 , filed on Mar. -
Gortex-Based Gas Diffusion Electrodes with Unprecedented Resistance to Flooding and Leaking Prerna Tiwari University of Wollongong, [email protected]
University of Wollongong Research Online Australian Institute for Innovative Materials - Papers Australian Institute for Innovative Materials 2018 Gortex-Based Gas Diffusion Electrodes with Unprecedented Resistance to Flooding and Leaking Prerna Tiwari University of Wollongong, [email protected] George Tsekouras University of Wollongong, [email protected] Gerhard F. Swiegers University of Wollongong, [email protected] Gordon G. Wallace University of Wollongong, [email protected] Publication Details Tiwari, P., Tsekouras, G., Swiegers, G. F. & Wallace, G. G. (2018). Gortex-Based Gas Diffusion Electrodes with Unprecedented Resistance to Flooding and Leaking. Acs Applied Materials & Interfaces, 10 (33), 28176-28186. Research Online is the open access institutional repository for the University of Wollongong. For further information contact the UOW Library: [email protected] Gortex-Based Gas Diffusion Electrodes with Unprecedented Resistance to Flooding and Leaking Abstract A significant and long-standing problem in electrochemistry has demanded the need for gas diffusion electrodes that are "flood-proof" and "leak-proof" when operated with a liquid electrolyte. The bsa ence of a solution to this problem has, effectively, made it unviable to use gas diffusion electrodes in many electrochemical manufacturing processes, especially as "gas-depolarized" counter electrodes with significantly decreased energy consumption. In this work, Gortex membranes (also known as expanded PTFE or ePTFE) have been studied as novel, leak-proof substrates for gas diffusion electrodes [PTFE = poly(tetrafluoroethylene)]. We report the fabrication, characterization, and operation of gas diffusion electrodes comprising finely pored Gortex overcoated with 10% Pt on Vulcan XC72, PTFE binder, and a fine Ni mesh as a current carrier. -
Salts in Organic Synthesis: an Overview and Their Diversified Use
Salts in Organic Synthesis: an overview and their diversified use Dirgha Raj Joshi1* and Nisha Adhikari2 1. College of Pharmacy, Yonsei University International Campus, Incheon, Republic of Korea 2. College of Pharmacy, Gachon University Medical Campus, Incheon, Republic of Korea *Correspondence: Dirgha Raj Joshi Email:[email protected], [email protected] ORCID ID: 0000-0002-0303-5677 Abstract The chemistry of salt is of great importance due to its immense potential from the daily life use to the synthetic chemistry like as workup material, as reagents, as phase transfer catalyst, as acid, as base, as catalyst, as agents for asymmetric synthesis, for some specific reaction transformation, to increase yield, decrease reaction time, ecofriendly synthesis, handling easiness and many more. This review summarizes the basic background of salts, its application, synthesis of new salts, and list of individual categories of major commercially available salts with some structure. Keywords: Organic synthesis, green chemistry, salts, catalyst, reagent, asymmetric synthesis, acid, base Introduction In chemistry, the salt is usually a solid chemical compound having related numbers of positively charged ions called cation and negatively charged ions called anions which are assembled to form a solid mass, so the whole mass is electrically neutral 2- (no net charge). These ions particle can be either organic (acetate- CH3CO ) or inorganic (chloride- Cl-, fluoride- F- etc.) and can be as a monoatomic (chloride- - 2- Cl ) or polyatomic (sulfate- SO 4)[1]. For organic synthesis, the considerations about various factors play a crucial role. With this respect, the organic and inorganic salts always remain core corner in the reagents category. -
The Future Green Power
The Future Green Power DE NORA E-TEK® ELECTRODE TECHNOLOGY FOR ENERGY SOLUTIONS ELECTROCHEMISTRY AT YOUR SERVICETM SPECIALTIES & NEW APPLICATIONS E-TEK® technology is a trusted platform worldwide known as the main component in Proton Exchange Membrane (PEM) fuel cells, the future green energy. From vehicles De Nora pioneered and patented to shuttle, E-TEK® technology designing, developing and supplying Gas Diffusion from energy Electrodes (GDE), layer and catalyst. storage to power generation in remote areas PEM Fuel cells, the core of Power to Power, Stationary power, transport and application in space, contain De Nora E-TEK® Gas Diffusion Electrode technology from the early nineties. De Nora Gas Diffusion Electrode business involves other applications as recovering energy from hydrogen produced as a by-product in chlor-alkali plants, industrial electrolytic processes, gas sensors, metal/air batteries, research and development activities. MORE POWER from RENEWABLE ENERGY Globally recognized as one of the major company in electrochemical technologies, De Nora developed the first prototypes of Gas Diffusion Electrodes to be used in electrochemical separations for hydrogen purification as well as supported catalysts. De Nora, after the acquisition of E-TEK® Inc., boosted the performances of E-TEK® products, strengthened their brand awareness and spured new industrial applications in the Chlor-Alkali electrolysis releasing a brand new family of GDE for the production of chlorine from hydrochloric acid as depolarized cathode. Matching the most complex requirements De Nora is today the only manufacturer of Gas Diffusion Electrodes assuring high product standards and the highest production capabilities of carbon coat and catalyst. High volume and wide size electrodes with an highly automated industrial production line. -
INVESTIGATION on the STRUCTURAL and OPTICAL PROPERTIES of Nio NANOFLAKES
D. Abubakar, N. Mahmoud, Sh. Mahmud doi: 10.15407/ujpe62.11.0970 D. ABUBAKAR,1 N. MAHMOUD,2 SH. MAHMUD3 1 Physics Department, Bauchi State University Gadau (65, Itas/Gadau – Bauchi Nigeria; e-mail: [email protected]) 2 Nano-Optoelectronics Research Laboratory (NOR) – School of Physics Universiti Sains Malaysia (11800 Gelugor Pulau Pinang – Malaysia) 3 Nano-Optoelectronics Research Laboratory (NOR) – School of Physics, Universiti Sains Malaysia (11800 Gelugor Pulau Pinang – Malaysia) INVESTIGATION ON THE STRUCTURAL AND OPTICAL PROPERTIES OF NiO NANOFLAKES. PACS 68.55.-a, 78.20.-e, 81.15.Lm CHEMICAL BATH DEPOSITION OF Ni(OH)2 THIN FILMS Porous nickel oxide (NiO) nanoflakes are grown by the chemical bath deposition. The thin films are produced on an ITO/glass substrate and annealed at a variable temperature ina furnace. The structural and optical properties and the surface morphology of the thin films are studied and analyzed. FESEM results display the presence of nanoflakes with the structure of NiO/Ni(OH)2 in thin films that appear to increase in size with the annealing temperature. The sample grown at 300 ∘C is observed to have the highest surface area dimension. The EDX result reveals that the atomic ratio and weight of the treated sample has a non-stoichiometric value, which results in the p-type behavior of the NiO thin film. The result obtained by AFM indicates the highest roughness value (47.9 nm) for a sample grown at 300 ∘C. The analysis on XRD shows that the NiO nanoflakes possess a cubic structure with the orientation peaks of (111), (200), and (220). -
Nickel-Cadmium Battery
NICKEL-CADMIUM BATTERY ELECTROCHEMICAL ENERGY STORAGE 1. Technical description A. Physical principles C. Key performance data A Ni-Cd Battery System is an energy storage system based on electrochemical charge/discharge reactions that occur between a positive electrode (cathode) Power range Some kW - some that contains nickel oxyde-hydroxide as the active material and a negative electrode (anode) that is composed of metallic cadmium. Energy range < some 10 M Wh The electrodes are separated by a permeable membrane which allows for Discharge time Some mn – some h electron and ionic flow between them and are immersed in an electrolyte that is made up of aqueous potassium hydroxide and that undergoes no significant changes during operation. Cycle life 1 000-5 000 cycles During discharge, the nickel oxide-hydroxide combines with water and produces Life duration 10 – 20 years nickel hydroxide and a hydroxide ion. Cadmium hydroxide is produced at the negative electrode. To charge the battery the process can be reversed. Reaction time Some ms Illustration: Charging principle of Ni-Cd Efficiency 60-70 % Energy (power) density 30-70 Wh/kg Positive Negative CAPEX: energy 400 - 700 € / kWh NiO2 H2-x Cd x CAPEX: power 500 – 1 500 € / kW Electrolyte D. Design variants (non exhausitive) KOH The following design variants are available: Different electrode thickness according to the power/energy ratio Different cell size from 2 Ah up to 200 Ah Different cell shapes: cylindrical (small cells) or prismatic (large cells), - Different battery systems according -
Simplified Gas Diffusion Electrode Method for Proton Exchange Membrane Water Electrolysis with a Ultralow Pt Loading
Int. J. Electrochem. Sci., 15 (2020) 2191 – 2204, doi: 10.20964/2020.03.14 International Journal of ELECTROCHEMICAL SCIENCE www.electrochemsci.org Short Communication Simplified Gas Diffusion Electrode Method for Proton Exchange Membrane Water Electrolysis with a ultralow Pt loading Xiaofeng Xie, Shusheng Chen, Yuanquan Zhou, Xiaohong Hu* Hubei Key Lab of Electrochemical Power Source, College of Chemistry and Molecular Sciences, Wuhan University. Wuhan Hubei, 430072, China *E-mail: [email protected] Received: 14 October 2019 / Accepted: 11 December 2019 / Published: 10 February 2020 Proton electrolyte membrane water electrolysis is a promising choice of hydrogen energy while limited by the high cost. Low Pt loading and large-scale application are practical for economic consideration. Here we replace the typical hydrophobic agent polytetrafluoroethylene (PTFE) with commercial fluorinated carbon (CFx) to fabricate hydrogen evolution reaction electrodes with a simplified gas diffusion electrode method. The Pt loading can be reduced as low as 0.03 mg cm-2 without performance loss, and the electrode fabrication method is easy for mass production. Cyclic voltammetry shows CFx electrode has a high Pt Electrochemical surface area (ECSA) as much as 321 m2 g-1, and larger than that of PTFE electrode, the Pt utilization increases 12%. Besides, scanning electron microscopy and pore analysis indicate the excellent performance of CFx electrode is related to the more reasonable three- phase boundaries, especially for the improved proton transfer. In addition, the performance differs with the ratio of CFx and content of CFx. We believe the application of CFx in proton exchange membrane water electrolysis has great economic potential due to the ultralow Pt consumption and easy electrode fabrication process.