Mass-Produced Handmade Ceramics
Total Page:16
File Type:pdf, Size:1020Kb
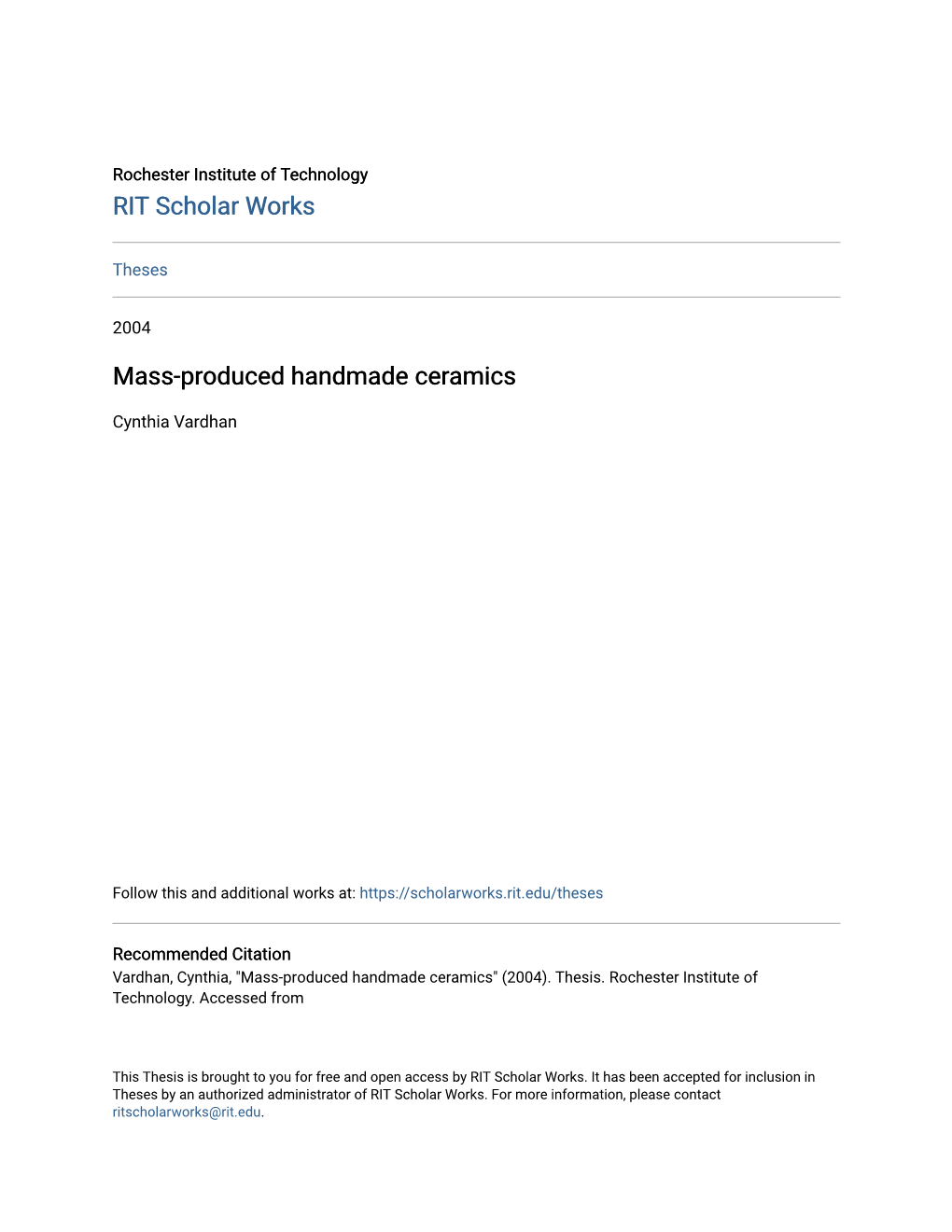
Load more
Recommended publications
-
Grand Tour of European Porcelain
Grand Tour of European Porcelain Anna Calluori Holcombe explores the major European porcelain centres Left: Gilder. Bernardaud Factory. embarked on a modern version of the 17th and 18th century Grand Limoges, France. Tour of Europe in summer of 2010 and spent two months researching Right: Designer table setting display. porcelain (primarily tableware) from historical and technical per- Bernardaud Factory. Limoges, France. Photos by Anna Calluori Holcombe. Ispectives. The tradition of Grand Tour promoted the idea of travelling for the sake of curiosity and learning by travelling through foreign lands. On a research leave with a generous Faculty Enhancement Grant A factory was started in 1863 by some investors and, at about from the University of Florida (UF), I visited factories and museums in that time, an apprentice was hired 10 major European ceramics centres. named Léonard Bernardaud. He Prior to this interest in investigating European porcelain, I spent time worked his way up to become a studying Chinese porcelains with fascination and awe. On one of my partner, then acquiring the company in 1900 and giving it his name. many trips to China and my first visit to the famous city of Jingdezhen, I In 1949, the factory introduced climbed Gaoling Mountain, where the precious kaolin that is essential to the first gas-fuelled tunnel kiln in the Chinese porcelain formula was first mined more than 1000 years ago. France operated 24 hours a day, a Soft paste porcelain, which does not have the durability and translu- standard in most modern factories today. Although they had to cut 15 cency found in hard paste porcelain was in popular use in Europe prior percent of their employees in recent to their discovery of hard paste porcelain. -
HAMK Opinnäytetyön Mallipohja
THE BULBS A conceptual artwork cast in porcelain Bachelor’s Thesis Hämeenlinna University Center Degree Program in Design Spring 2021 Anna Siukola Degree Program in Design Abstract Hämeenlinna University Center Author Anna Siukola Year 2021 Subject The Bulbs. A conceptual artwork cast in porcelain Supervisors Helena Leppänen, Mirja Niemelä The aim of this thesis is to create a porcelain artwork by using slipcasting. The work explains what slip means, what it is composed of and how it is produced; further on, it studies surface decoration applications such as glazes; and finally, it presents the created cast porcelain artwork variations. The thesis consists of a knowledge base and an implementation part. In the theoretical part, a porcelain slip, high-fire glazes, the principles of creating them, and what happens to the compounds in an electric kiln during firings, are studied. The target of this research is to build a theoretical platform supporting the making process. The practical part demonstrates the process of creating the artwork, which is a combination of cast porcelain bulbs of various shapes and sizes. The porcelain slip is created and used for casting, and the glazes are made and used for the surface decoration, the porcelain bulbs are finalized. Some bulbs are glazed partially, and some are left unglazed – to show the beauty of the contrast of a stunningly white porcelain and bright glazes. The final artwork variations are multi-colored and the parts within them – all have an original look. The artwork theme presented in this work is only one of possible variations. Depending on the number of bulbs, and the means of their attachments, they can be easily re-assembled into new artistic installations. -
Mass-Produced Handmade Ceramics Cynthia Vardhan
Rochester Institute of Technology RIT Scholar Works Theses Thesis/Dissertation Collections 2004 Mass-produced handmade ceramics Cynthia Vardhan Follow this and additional works at: http://scholarworks.rit.edu/theses Recommended Citation Vardhan, Cynthia, "Mass-produced handmade ceramics" (2004). Thesis. Rochester Institute of Technology. Accessed from This Thesis is brought to you for free and open access by the Thesis/Dissertation Collections at RIT Scholar Works. It has been accepted for inclusion in Theses by an authorized administrator of RIT Scholar Works. For more information, please contact [email protected]. ROCHESTER INSTITUTE OF TECHNOLOGY MASS-PRODUCED HANDMADE CERAMICS A THESIS SUBMITTED TO THE FACULTY OF THE COLLEGE OF IMAGING ARTS AND SCIENCES IN CANDIDACY FOR THE DEGREE OF MASTER OF FINE ARTS INDUSTRIAL DESIGN DEPARTMENT BY CYNTHIA VARDHAN ROCHESTER NEW YORK MAY 2004 Approvals Chief Advisor, Professor David Morgan: David Morgan Date: Associate Advisor, Professor Stan Rickel: Stan Rickel Date: Associate Advisor, Professor Julia Galloway: Julia Galloway Date: School Chairperson, Professor Patti Lachance Patti Lachance Date: I I I, Cynthia Vardhan, hereby grant permission to the Wallace Memorial Library of RIT to reproduce my thesis in whole or in part. Any reproduction will not be for commercial use or profit. Date: Cynthia Vardhan 3 '//."1 II Copyright 2003 by Cynthia Vardhan All rights reserved To Aniket Love your experiments (as you would an ugly child) Bruce Mau "An Incomplete Manifesto for Growth" CONTENTS LIST OF ILLUSTRATIONS vi Chapter 1. THESIS SUMMARY 1 Components ofThesis Necessity ofThesis Goals Limitations 2. BACKGROUND OF PRODUCTION METHODS 6 The Handrnade-to-Machine-Made Continuum Current Processes in Use Case Studies My Niche in the Spectrum 3. -
Industrial Arts Courses. It Was Include a Glossary of Ceramic Terms
DOCUMENT RESUME VT 002 002 ED 021 963 By-Hastings, James R., Ed CERAMICS, PROJECT IDEAS FORINDUSTRIAL ARTS. New York State Education Dept.,Albany. Bureau of SecondaryCurriculum Development. Pub Date 66 Note-185p. EDRS Price MF-$0.75 HC-$7.48 UNITS, Descriptors-*CERAMICS, HIGH SCHOOLS,*INDUSTRIAL ARTS, JUNIOR HIGHSCHOOLS, *RESOURCE *STUDENT PROJECTS This book of ceramic projectideas is for teacher orstudent use insecondary industrial arts courses. It wasdeveloped in a workshopby teachers. The content useful projects and unitsof instruction and togiVe direction objectives are to provide Forty-one to ceramics instructionwhich isin keeping with achanging technology. under these units: (1)Hand Forming, (2) SlabConstructing, project plans are presented Extruding, (8) (3) Free Forming, (4) PressMolding, (5) Solid Casting,(6) Slip Casting, (7) Throwing and Turning, and (9)Jiggering. Each unit givesproject plans,student activities, projectprocedures, related technicalinformation, teacher demonstrations, references. Similarly organized units cover13 tools or related- cultural information, and turning box. pieces of equipment such as...a.jiggerarm, stilts, anextrusion press, and a Information concerning the makingof glazes is also included.Supplementary materials include a glossary of ceramic terms, abibliography of books andperiodicals, and indexes to related technical andcultural topics. (EM) i, , U.S. DEPARTMENT OF HEALTH, EDUCATION & WELFARE OFFICE OF EDUCATION THIS DOCUMENT HAS BEEN REPRODUCED EXACTLY AS RECEIVED FROM THE PERSON OR ORGANIZATION ORIGINATING IT.POINTS OF VIEW OR OPINIONS STATED DO NOT NECESSARILY REPRESENT OFFICIAL OFFICE OF EDUCATION POSITION OR POLICY. Cetaini,a, wied feaJ FOR INDUSTRIAL ARTS , THE UNIVERSITY OF THE STATE OF NEW YORK The State Education Department Bureau of Secondary Curriculum Development Albany, 1966 THE UNIVERSITY OF THE STATE OF NEW YORK Regents of the University (with years when terms expire) EDGAR W. -
WO 2013/032520 Al 7 March 2013 (07.03.2013) P O P C T
(12) INTERNATIONAL APPLICATION PUBLISHED UNDER THE PATENT COOPERATION TREATY (PCT) (19) World Intellectual Property Organization International Bureau (10) International Publication Number (43) International Publication Date WO 2013/032520 Al 7 March 2013 (07.03.2013) P O P C T (51) International Patent Classification: (81) Designated States (unless otherwise indicated, for every F27D 1/14 (2006.01) kind of national protection available): AE, AG, AL, AM, AO, AT, AU, AZ, BA, BB, BG, BH, BN, BR, BW, BY, (21) International Application Number: BZ, CA, CH, CL, CN, CO, CR, CU, CZ, DE, DK, DM, PCT/US2012/000333 DO, DZ, EC, EE, EG, ES, FI, GB, GD, GE, GH, GM, GT, (22) International Filing Date: HN, HR, HU, ID, IL, IN, IS, JP, KE, KG, KM, KN, KP, 27 July 2012 (27.07.2012) KR, KZ, LA, LC, LK, LR, LS, LT, LU, LY, MA, MD, ME, MG, MK, MN, MW, MX, MY, MZ, NA, NG, NI, (25) Filing Language: English NO, NZ, OM, PE, PG, PH, PL, PT, QA, RO, RS, RU, RW, (26) Publication Language: English SC, SD, SE, SG, SK, SL, SM, ST, SV, SY, TH, TJ, TM, TN, TR, TT, TZ, UA, UG, US, UZ, VC, VN, ZA, ZM, (30) Priority Data: ZW. 13/222,037 31 August 201 1 (3 1.08.201 1) US (84) Designated States (unless otherwise indicated, for every (71) Applicant (for all designated States except US): SENECA kind of regional protection available): ARIPO (BW, GH, CERAMICS CORP. [US/US]; 45 Main Street, Phelps, GM, KE, LR, LS, MW, MZ, NA, RW, SD, SL, SZ, TZ, New York 14532 (US). -
I AP42 Section: 111.7 Reference: DW Richerson, 4 Title
I AP42 Section: 111.7 - Reference: 4 Title: Modern Ceramic Engineering: Properties Processing, And Use In Design, D. W. Richerson, I Marcel Dekker, Inc., New York, NY, 1982. I1 PROCESSING OF CERAMICS The relationships among atomic bonding, crystal structure, and properties for ceramics, metals, and polymers were discussed in Part I. It was shown that the theoretical strength is controlled by the strength of bonding, but that in actual ceramic components the theoretical strength is not achieved due to flaws in the fabricated material. The objectives of Part Il are to review the fabrication processes used for manufacturing ceramic compo- nents, determine where in these processes strength-limiting flaws are likely to occur, and provide the reader with approaches for detecting these flaws and worldng with the ceramic fabricator to eliminate them. Most ceramic fabrication processes begin with finely ground powder. Chapter 5 describes the criteria for selection of the starting powder, meth- ods of achieving the proper particle size distribution, and requirement8 for pretreating the powder before it can be formed into the desired wm- ponent. Chapter 6 describes the processes used to form the ceramic powders into the component shapes. Uniaxial and isostatic pressing, slip casting, emion, injection molding, tape forming, and green machining are included. The shapes resulting from the forming processes described in Chap. 6 consist essentially of powder compacts that must be densified by high- temperature processing before they will have adequate strength and other properties. The mechanisms and processes for densification are explored in Chap. 7. Some processes combine formtng and densification in a single step. -
The Cup, the Mug 2020
THE CUP, THE MUG 2020 About the Exhibition The fifth annual The Cup, The Mug exhibition at Main Street Arts features work by 55 artists from 24 states. A national juried exhibition of drinking vessels, this year’s The Cup, The Mug exhibition was juried by Christina Erives of Helena, MT and Masa Sasaki of Atlanta, GA. Exhibition Dates: November 7—December 4, 2020 Award Annoucement (Facebook live): Saturday, November 7 at 6 p.m. “What a pleasure to get to examine so many wonderful cups. It was exciting to see such a wonderful range of material, form, and surfaces. I was particularly drawn to the amount of character and playfulness in many of these submissions. Many left such a lingering image in mind after viewing them that proved their quality and skill to be unforgettable. I think the toughest choice in this show will be which cup to take home!” — Christina Erives “It was a great pleasure to participate in the jurying process. All of the outstanding artists that submitted cups should be commended. Along with the demonstration of technical skill, I looked for artistic expression that embodies both esthetic quality and originality. Each of the cups we reviewed had exceptional desirable characteristics and choosing a winner was challenging indeed.” — Masa Sasaki FEATURING THE WORK OF: Hadi Abbas (Orlando, FL) Camilla Ascher (Baltimore, MD) Casey Beck (St. Paul, MN) Eve Behar (Sag Harbor, NY) Collin Blackmore (Earlville, NY) Sandy Blain (Tempe, AZ) Tracy L. Burton (Chicago, IL) Brooke Cashion (Alfred, NY) Joey Chiarello (Honolulu, HI) Marissa -
MEACAP: Survey of Technical and Management-Based Mitigation
MEACAP – D7a Technical and management-based mitigation measures in agriculture – June 2005 SIXTH FRAMEWORK PROGRAMME PRIORITY 8: Policy-Oriented Research SPECIFIC TARGETED RESEARCH PROJECT n°SSPE-CT-2004-503604 Impact of Environmental Agreements on the CAP Document number: MEACAP WP3 D7a Dissemination level: public Survey of technical and management-based mitigation measures in agriculture Author: A. Weiske Author’s Organisation(s): Institute for Energy and Environment (IE) Date: June 2005 1 MEACAP – D7a Technical and management-based mitigation measures in agriculture – June 2005 TABLE OF CONTENTS Introduction............................................................................................................... 7 1 Measures related to livestock and poultry farming ....................................... 9 1.1 Animal breeding and husbandry ................................................................................. 9 1.1.1 Livestock breeding ................................................................................................ 9 1.1.2 Artificial insemination........................................................................................... 9 1.1.3 Planned selection of male/female at insemination (embryo and sperm sexing) . 10 1.1.4 Twinning ............................................................................................................. 11 1.1.5 Lifetime efficiency (calves, cattle, cows / meat, milk) ....................................... 11 1.1.6 Multi use of cows (milk, calves and meat)......................................................... -
Marguerite Wildenhain: Bauhaus to Pond Farm January 20 – April 15, 2007
MUSEUM & SCHOOLS PROGRAM EDUCATOR GUIDE Kindergarten-Grade 12 Marguerite Wildenhain: Bauhaus to Pond Farm January 20 – April 15, 2007 Museum & Schools program sponsored in part by: Daphne Smith Community Foundation of Sonoma County and FOR MORE INFORMATION ABOUT THE EXHIBITION OR EDUCATION PROGRAMS PLEASE CONTACT: Maureen Cecil, Education & Visitor Services Coordinator: 707-579-1500 x 8 or [email protected] Hours: Open Wednesday through Sunday 11:00 a.m. to 5:00 p.m. Admission: $5 General Admission $2 Students, Seniors, Disabled Free for children 12 & under Free for Museum members The Museum offers free tours to school groups. Please call for more information. SONOMA COUNTY MUSEUM 425 Seventh Street, Santa Rosa CA 95401 T. 707-579-1500 F. 707-579-4849 www.sonomacountymuseum.org INTRODUCTION Marguerite Wildenhain (1896-1985) was a Bauhaus trained Master Potter. Born in Lyon, France her family moved first to Germany then to England and later at the “onset of WWI” back to Germany. There Wildenhain first encountered the Bauhaus – a school of art and design that strove to bring the elevated title of artist back to its origin in craft – holding to the idea that a good artist was also a good craftsperson and vice versa. Most modern and contemporary design can be traced back to the Bauhaus, which exalted sleekness and functionality along with the ability to mass produce objects. Edith Heath was a potter and gifted form giver who started Heath Ceramics in 1946 where it continues today in its original factory in Sausalito, California. She is considered an influential mid-century American potter whose pottery is one of the few remaining. -
Bisque Or Biscuit: the First Firing a Pot Undergoes to Prepare It for Glazing
Glossary of Ceramic Terms: Introduction to Ceramic Terms and Definitions Bisque or Biscuit: The first firing a pot undergoes to prepare it for glazing. In industry this is done at a higher temperature than the subsequent glaze firing, the reverse is usually true of the studio potter. Burnishing: A technique where the Leather hard clay is polished with a hard instrument to force the smallest clay particles to the surface creating a soft sheen. This surface remains after the pot is fired so long as the firing temperature is kept below 1100oC. Clay: AL2O3 2SiO2 2H2O. The decomposition of Granite through the process of Kaolinization creates clay (see Kaolinization). Clay is a mineral with a plate (platelet) like structure; it is these plates, (about 0.5 microns across) when lubricated with water, slide against each other to form the plastic mass we know as clay (see Water). 'Primary ' clays are those found close to the area of Kaolinization and hence the purest (Kaolin or China Clays). Secondary clays are those moved by water away form the site of Kaolinization and get progressively more plastic and less pure (Ball Clays, Fire clays, Earthenwares). Clay Body: A clay designed for a special purpose. It is created by blending different clays of by adding to clays other materials, such as feldspar and flint in order to produce a desired workability, maturing temperature, or finished result. A clay body is the result of mans technology. Cobalt: One of the strongest coloring oxides used by the potter. Cobalt creates a dark dense royal blue in most cases. -
OCCASION This Publication Has Been Made Available to the Public on The
OCCASION This publication has been made available to the public on the occasion of the 50th anniversary of the United Nations Industrial Development Organisation. DISCLAIMER This document has been produced without formal United Nations editing. The designations employed and the presentation of the material in this document do not imply the expression of any opinion whatsoever on the part of the Secretariat of the United Nations Industrial Development Organization (UNIDO) concerning the legal status of any country, territory, city or area or of its authorities, or concerning the delimitation of its frontiers or boundaries, or its economic system or degree of development. Designations such as “developed”, “industrialized” and “developing” are intended for statistical convenience and do not necessarily express a judgment about the stage reached by a particular country or area in the development process. Mention of firm names or commercial products does not constitute an endorsement by UNIDO. FAIR USE POLICY Any part of this publication may be quoted and referenced for educational and research purposes without additional permission from UNIDO. However, those who make use of quoting and referencing this publication are requested to follow the Fair Use Policy of giving due credit to UNIDO. CONTACT Please contact [email protected] for further information concerning UNIDO publications. For more information about UNIDO, please visit us at www.unido.org UNITED NATIONS INDUSTRIAL DEVELOPMENT ORGANIZATION Vienna International Centre, P.O. Box 300, 1400 Vienna, Austria Tel: (+43-1) 26026-0 · www.unido.org · [email protected] 1.0 22 iii; 2 0 111111.1 11111~~ 25 4 111111. 1:1111. -
Mass Production Techniques for the Studio Potter
Rochester Institute of Technology RIT Scholar Works Theses 6-1-1976 Mass Production Techniques for the Studio Potter James Halvorson Follow this and additional works at: https://scholarworks.rit.edu/theses Recommended Citation Halvorson, James, "Mass Production Techniques for the Studio Potter" (1976). Thesis. Rochester Institute of Technology. Accessed from This Thesis is brought to you for free and open access by RIT Scholar Works. It has been accepted for inclusion in Theses by an authorized administrator of RIT Scholar Works. For more information, please contact [email protected]. MASS PRODUCTION TECHNIQUES FOR THE STUDIO POTTER BY JAMES M. SQUIERS HALVORSON THESIS FOR THE MASTER OF FINE ARTS DEGREE SCHOOL FOR AMERICAN CRAFTSMEN COLLEGE OF FINE AND APPLIED ARTS ROCHESTER INSTITUTE OF TECHNOLOGY ROCHESTER, NEW YORK JUNE 1976 THESIS ADVISORS ROBERT D. SCHMITZ JUDITH SALOMON JANET R. KELLNER Dr. R. H. Johnston, Dean r^ROPOSAL The aim of this thesis will be to explore mass-production techniques available for the studio potter. These will be a blending of industrial techniques of slip-casting and jiggering with wheel-thrown work. The potter's wheel will be used as a basis for experimenting with these processes. Fabrication of master molds and working molds, development of clay bodies suited for this type of fabrication and manipulation of the molded forms will be the main emphasis of this work. ACIAS Thanks to my Friends, Fellow Students, Faculty and Administration of School for American Craftsmen. Muchos gracias to Suzanne and Fred, the Midnight Rambler. ~Wq I was first introduced to slip casting during brainwashing sessions in my beginning ceramics class.