Organic Coolants and Their Applications to Fusion Reactors
Total Page:16
File Type:pdf, Size:1020Kb
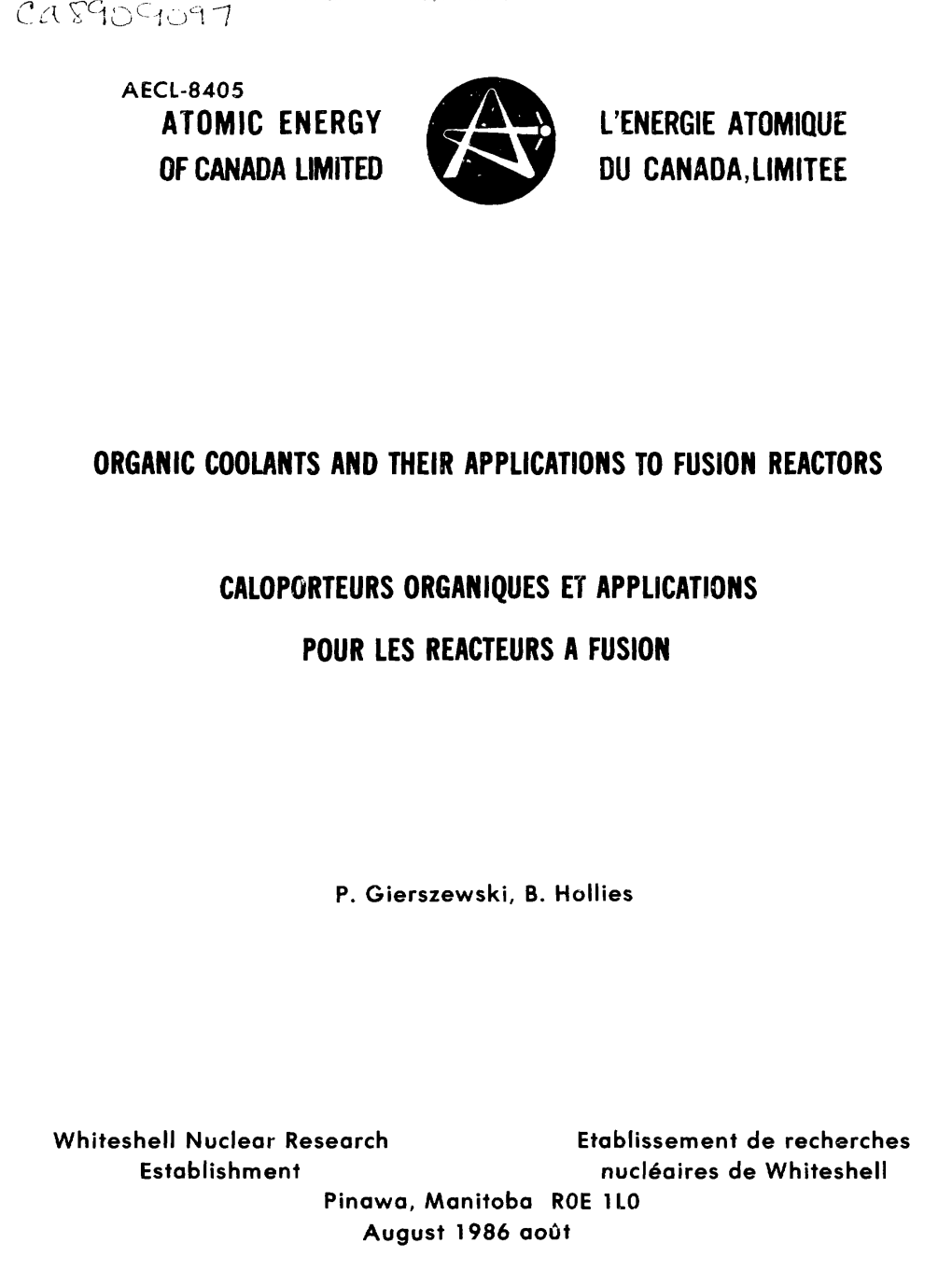
Load more
Recommended publications
-
Engineering Design of Aries-Iii*
PAPER ENGINEERING DESIGN OF ARIES-HI* O.K. Sze, Argonne National Laboratory, Argonne, IL 60439 C. Wong, General Atomics, San Diego, CA 92138 E. Cheng, TSI Research, Solana Beach, CA 92075 M.E. Sawan, I.N. Sviatoslavsky, J.P. Blanchard, L.A. El-Guebaly, H.Y. Khater, E.A. Mogahed University of Wisconsin, Madison, Wl 53706 P. Gierszewski, Canadian Fusion Fuels Tech. Prog., Mississauga, Ontario, Canada, L5J1K3 R. Hollies, Hollies Fluids Consulting, Pinawa, MB, ROE 1 L0 Canada and the ARIES Team M Z. <*• « (5 E B RECEIVE. AUG 2 6 1993 o M c -5 «3 OSTI Th« uibmitted manuscript has been authored by a contractor of the U. 5. Government under contract No. W-31-109-ENG-38- l Accordingly, the U. S. Government retains a nonexclusive, royalty-free license to publish or reproduce tha published form of this contribution, or allow others to do so, far U. 5. Government purposes. July 1993 •so * Work supported by the U.S. Department of Energy, Office of Fusion Energy, under Contract No. W-31-109-Eng-38. Paper to be presented at the Second Wisconsin Symposium on 3He and Fusion Power, University of Wisconsin, Madison, Wl, July 19-21,1993. DWTFMBUTION OF THIS DOOUMENT IS UNLIMITED ENGINEERING DESIGN OF ARIES-III* D.K. Sze, Argonne National Laboratory, Argonne, IL 60439 C. Wong, General Atomics, San Diego, CA 92138 E. Cheng, TSI Research, Solana Beach, CA 92075 M.E. Sawan, I.N. Sviatoslavsky, J.P. Blanchard, LA. El-Guebaly, H.Y. Khater, E.A. Mogahed University of Wisconsin, Madison, Wl 53706 P. -
Dr. Starr of Atomics International New Head of American Nuclear Societ Y Group Includes Members from 29 Countries Devoted to Ad- Vancement of Nuclear Scienc E
VOL. 1 NO. 2 ATOMICS INTERNATIONAL a division of North American Aviation, Inc . SEPTEMBER 1958 Dr. Starr Of Atomics International New Head Of American Nuclear Societ y Group Includes Members From 29 Countries Devoted To Ad- vancement Of Nuclear Scienc e At the annual meeting in June of the American Nuclear Society (ANS) . Dr. Chauncey Starr, general manager of Atomics International and vice president of North American Aviation, Inc., was elected president of the society to succeed Dr . Leland J . Haworth . Direc- tor of the Brookhaven National Laboratory . The American Nuclear Society was formed in 1955 to advance nuclear science and engineering . to encour- age research . establish scholarships. and to disseminate technical information . Membership of 3,000 Includes 29 Countries The organization's membership of 3 .000 includes about 140 members from 29 countries outside the United States representing many branches of science and technology . Members are associated with educa. tional , governmental, and research institutions, and with government contractors and industrial companies. First Student Award Establishe d In keeping with one of the objectives of the society, the first annual graduate student award has been estab- lished for the most outstanding graduate student work- ing in the nuclear sciences . NEW ANS OFFICERS-At the recent meeting of the URER ; Dr. Chauncey Starr, general manager of Atomics The award is the first of its kind by the society and American Nuclear Societe , new officers elected are : (felt International and vice-president of North American Avia- to right) John A . Swartnut, deputy director of Oak Ridge tion, Inc. PRESIDENT ; and Octave J. -
Organic Liquids As Reactor Codants and Moderators
<" . • t téLb TECHNICAL REPORTS SERIES No. 70 Organic Liquids as Reactor Codants and Moderators ?J INTERNATIONAL ATOMIC ENERGY AGENCY, VIENNA, 1967 ORGANIC LIQUIDS AS REACTOR COOLANTS AND MODERATORS The following States are Members of the International Atomic Energy Agency: AFGHANISTAN GABON NICARAGUA ALBANIA GERMANY, FEDERAL NIGERIA ALGERIA REPUBLIC OF NORWAY ARGENTINA GHANA PAKISTAN AUSTRALIA GREECE PANAMA AUSTRIA GUATEMALA PARAGUAY BELGIUM HAITI PERU BOLIVIA HOLY SEE PHILIPPINES BRAZIL HONDURAS POLAND BULGARIA HUNGARY PORTUGAL BURMA ICELAND ROMANIA BYELORUSSIAN SOVIET INDIA SAUDI ARABIA SOCIALIST REPUBLIC INDONESIA SENEGAL CAMBODIA IRAN SOUTH AFRICA CAMEROON IRAQ SPAIN CANADA ISRAEL SUDAN CEYLON ITALY SWEDEN CHILE IVORY COAST SWITZERLAND CHINA JAMAICA SYRIAN ARAB REPUBLIC COLOMBIA JAPAN THAILAND CONGO, DEMOCRATIC JORDAN TUNISIA REPUBLIC OF KENYA TURKEY COSTA RICA KOREA, REPUBLIC OF UKRAINIA N SOVIET SOCIALIST CUBA KUWAIT REPUBLIC CYPRUS LEBANON UNION OF SOVIET SOCIALIST CZECHOSLOVAK SOCIALIST LIBERIA REPUBUCS REPUBLIC LIBYA UNITED ARAB REPUBLIC DENMARK LUXEMBOURG UNITED KINGDOM OF GREAT DOMINICAN REPUBLIC MADAGASCAR BRITAIN AND NORTHERN ECUADOR MALI IRELAND EL SALVADOR MEXICO UNITED STATES OF AMERICA ETHIOPIA MONACO URUGUAY FINLAND MOROCCO VENEZUELA FRANCE NETHERLANDS VIET-NAM NEW ZEALAND YUGOSLAVIA The Agency's Statute was approved on 26 October 1956 by the Conference -on the Statute of the IAEA held at United Nations Headquarters, New York; it entered into force on 29 July 1951. The Headquarters of the Agency are situated in Vienna. Its principal objective is "to accelerate and enlarge the contribution of atomic energy to peace, health and prosperity throughout the world". © IAEA, 1967 Permission to reproduce or translate the information contained in this publication may be obtained by writing to the International Atomic Energy Agency, Kârntner Ring 11, A-1010 Vienna I, Austria. -
Dr. Starr of Atomics International New Head of a Mer Ican Nuc Lear Societ Y Group Includes Members from 29 Countries Devoted to Ad- Vancement of Nuclear Scienc E
VOL. 1 NO. 2 ATOMICS INTERNATIONAL a division of North American Aviation, Inc. SEPTEMBER 195 8 Dr. Starr Of Atomics International New Head Of A mer ican Nuc lear Societ y Group Includes Members From 29 Countries Devoted To Ad- vancement Of Nuclear Scienc e At the annual meeting in June of the American Nuclear Society (ANS) . Dr . Chauncey Starr . general manager of Atomics International and vice president of North American Aviation, Inc. was elected president of the society to succeed Dr. Leland J . Haworth, Direc- tor of the Brookhaven National Laboratory . The American Nuclear Society was formed in 1955 to advance nuclear science and engineering . to encour- age research. establish scholarships, and to disseminate technical information. Membership of 3,000 Includes 29 Countries The organizations membership of 3 .000 includes about 140 members from 29 countries outside the United States representing many branches of science and technology . Members are associated with educa . tional . governmental . and research institutions, and with government contractors and industrial companies . First Student Award Established In keeping with one of the objectives of the society, the first annual graduate student award has been estab- lished for the most outstanding graduate student work- ing in the nuclear sciences. MR' ANS OFFICERS-At the recent meeting of the URER Chauncey Starr. general manager ; The. of Atomics The atcard is the first of its kind by the society and American Nuclear Societe, new officers elected are : (felt lnternatianaf and rice- president /,North American Aria- to right) John A. Straetout. deputy director of Oak Ridge tion, his .. PRESIDENT; and Octane J. -
Patented Apr. 23, 1963
3,086,932 ice Patented Apr. 23, 1963 2 and increases of the proportion of higher polyphenyls 3,086,932 PROCESS FOR PRODUtIiNG A RECOVERENG is an undesirable tendency. This is true as well for other ORGANIC NUCLEAR REACTOR COOLANT hydrocarbons, e.g., partially hydrogenated or alkylated MODERATGRS polyphenyls. Robert 0. Bolt, San Rafael, and William W. West, El The present invention is predicated on the discovery Cerrito, Cali?, assignors, by mesne assignments, to the that catalytic hydrogenolysis of ‘di?erent polyphenyls United States of America as represented by the United produces a marked reversion or conversion of higher States Atomic Energy Commission molecular weight constituents of aromatic and especially No Drawing. Filed Nov. 3%, 1959, Ser. No. 856,321 polyphenyl mixtures having undesirable characteristics 3 Claims. (Cl. Zita-493.2) 10 into lower molecular weight mixtures of more useful and The present invention relates, in general, to the pro desirable coolant-moderator types. Most unexpectedly duction and recovery of polyphenyl coolants from in hydrogenolysis, i.e., ring cleavage occurs with little ring tractable polyphenyl tars or residues and, more particu hydrogenation which might have been expected. Thus, larly, to the treatment of intractable, insoluble tarry resi highly damaged reactor coolant-moderator materials may dues obtained from coolants or moderators employed in 15 be reconditioned or various component fractions thereof nuclear reactors for conversion into useful moderator separated and treated to provide a material which is coolant products. highly satisfactory for reuse in the reactor. Varieties of aromatic hydrocarbons have been utilized Accordingly, it is an object of the present invention or have been proposed or investigated for use as coolants to provide a method for reconditioning coolant-moderator or moderators in nuclear reactors including polyphenyls, materials for use in a nuclear reactor. -
Part Ii: Technical Analysis and Systems Study
PART II: TECHNICAL ANALYSIS AND SYSTEMS STUDY 111 1. PARTITIONING 1.1 Aqueous separation techniques This section briefly describes aqueous separation techniques currently used on industrial scale and research activities in the field of new separation methods for more effective separation of minor actinides and fission products. There has been a large number of reports published until now and a selection of the important ones is listed in Annex D. 1.1.1 PUREX process The PUREX process, see Figure II.1, which is universally employed in the irradiated fuel reprocessing industry, is a wet chemical process based on the use of TBP, a solvent containing phosphorus. As shown in Table II.1 this solvent displays the property of extracting actinide cations in even oxidation states IV and VI, in the form of a neutral complex of the type M•An•2TBP (where M is the metallic cation and A an anion, generally nitrate ion), from an acidic aqueous medium. Conversely, the actinide cations with odd oxidation state are not significantly extracted, at least in the high acidity conditions prevailing during reprocessing operations. Uranium and plutonium, whose stable oxidation states in nitric medium are VI and IV, respectively, are co-extracted by TBP and thus separated from the bulk of the fission products which remain in the aqueous phase. This is the basic principle of the PUREX process. Table II.1 Extractability of actinide nitrates in 3 M nitric acid by TBP Oxidation state III IV V VI U (m) (l) m Np (m) l m Pu (l) m (l) (m) Am l (m) Cm l m: extractable by TBP, l: not extractable by TBP, ( ): unstable in the media Uranium and plutonium are recovered with an industrial yield close to 99.9% (including losses in secondary wastes). -
Curium in Space
ROBIN JOHANSSON Curium in Space KTH Royal Institute of Technology Master Thesis 2013-05-05 Abstract New technology has shown the possibility to use a miniature satellite in conjunction with an electric driven engine to make a spiral trajectory into space from a low earth orbit. This report has done an investigation of the new technique to produce power sources replacing solar panels which cannot be used in missions out in deep space. It is in essence an alternative use of curium among the many proposals on how to handle the intermediate stored used nuclear fuel or once through nuclear fuel as some people prefer to call it. The idea of sending radioactive used nuclear fuel into outer space has been considered before. There was a proposal, for example, to load a space shuttle with radioactive material. This could have serious consequences to the nearby population in the event of a major malfunction to the shuttle. The improvement to this old idea is to use a small satellite with only a fraction of the spent fuel. With this method and other technological advances, it is possible to further reduce the risk of contamination in the event of a crash. This report has looked into the nuclear energy production of Sweden and the current production of transuranium elements (Pu, Np, Am and Cm). The report has also focused on the curium (Cm) part of the transuranium elements, which is the most difficult to recycle in a fast neutron spectra. The physical property of curium reduces many of the safety parameters in the reactor as it is easily transmutated into californium, which is a high neutron emitter. -
NUCLEAR POWER: the Second Encounter
NUCLEAR POWER: THE SECOND ENCOUNTER Ludwik dobrzyński kajetan różycki KACPER SAMUL NATIONAL CENTRE FOR NUCLEAR RESEARCH December 2015 From the Authors This brochure is a sequel to the “Nuclear power: the first encounter” brochure by L. Dobrzyński and K. Żuchowicz (NCBJ, 2012). Just like the previous one, it has been written generally for persons interested in nuclear power, in particular in development of new types of power reactors. Some elements of the Polish government programme to develop the first nuclear power plant in Poland – including nuclear safety issues – are also presented. In that context we considered useful to describe also reasons and consequences of the most important nuclear accidents that happened in history of commercial nuclear power industry. However, scope of subjects dealt with in this brochure is quite broad, for example some economic aspects of nuclear power have also been tackled. This brochure (as well as several others devoted to various ionising-radiation-related subjects) may be downloaded from NCBJ webpages, e.g. from http://ncbj.edu.pl/materialy- edukacyjne/materialy-dla-uczniow (majority of the brochures are in Polish). As usual, we have tried to make this brochure as easy to comprehend and absorb as practical, but readers are strongly advised to first read the above mentioned “Nuclear power: the first encounter” brochure. The latter will be referred to many times in this text as “previous brochure” or “the first brochure” and we hope that the context will undoubtedly indicate what is referred to. Lecture of the first brochure is especially recommended to readers not familiar with basics of nuclear power. -
Mk-18A) Target Materials
ORNL/TM-2013/148 Evaluation of Disposition Options for Mark-18A (Mk-18A) Target Materials May 2013 Prepared by Sharon Robinson Charles Alexander Jeffery Allender Emory Collins Kenneth Fuller Bradley Loftin Bradley Patton Approved for public release; distribution is unlimited. DOCUMENT AVAILABILITY Reports produced after January 1, 1996, are generally available free via the U.S. Department of Energy (DOE) Information Bridge. Web site http://www.osti.gov/bridge Reports produced before January 1, 1996, may be purchased by members of the public from the following source. National Technical Information Service 5285 Port Royal Road Springfield, VA 22161 Telephone 703-605-6000 (1-800-553-6847) TDD 703-487-4639 Fax 703-605-6900 E-mail [email protected] Web site http://www.ntis.gov/support/ordernowabout.htm Reports are available to DOE employees, DOE contractors, Energy Technology Data Exchange (ETDE) representatives, and International Nuclear Information System (INIS) representatives from the following source. Office of Scientific and Technical Information P.O. Box 62 Oak Ridge, TN 37831 Telephone 865-576-8401 Fax 865-576-5728 E-mail [email protected] Web site http://www.osti.gov/contact.html This report was prepared as an account of work sponsored by an agency of the United States Government. Neither the United States Government nor any agency thereof, nor any of their employees, makes any warranty, express or implied, or assumes any legal liability or responsibility for the accuracy, completeness, or usefulness of any information, apparatus, product, or process disclosed, or represents that its use would not infringe privately owned rights. Reference herein to any specific commercial product, process, or service by trade name, trademark, manufacturer, or otherwise, does not necessarily constitute or imply its endorsement, recommendation, or favoring by the United States Government or any agency thereof. -
Tschernobyl-Katastrophe"
Gesellschaft für Anlagen- und Reaktorsicherheit (GRS) mbH The Accident and the Safety of RBMK-Reactors February 1996 GRS - 121 GRS in Eastern Europe The accident in the Chernobyl Nuclear Power Plant has shown the necessity of international cooperation in the field of reactor safety in a dramatical way. Under this impression GRS initiated first contacts to Eastern European expert organizations at the end of the 80ies. Within the framework of projects commissioned by the Federal Ministry for the Environment, Nature Con- servation and Reactor Safety, the Federal Ministry for Education, Science and Technology, the European Union and other international organizations these have developed to an intensive cooperation in the course of the years. Together with its French partner organization, the Institut de Protection et de Sûreté Nucléaire, GRS established technical offices in Moscow and Kiev and equipped these with modern telecommunication to render the cooperation with these countries more efficient. In Eastern Europe GRS concentrates on three main areas: - Cooperation in reactor safety research At the beginning of the technological-scientific cooperation with Russia and other Eastern European countries which is getting closer and closer there was an exchange of information with the Kurchatov-Institute in Moscow. Possibilities for the use of German computer codes to simulate accidents in Soviet reactors were thus created, for example, and a joint further development of such tools was initiated. The knowledge acquired during these joint projects at the same time represent the basis for safety assessments of Eastern European nuclear power plants and for the establishment of a mutual understanding of essential safety issues. -
Model Investigation of Initial Fouling Rates of Protein
MODEL INVESTIGATION OF INITIAL FOULING RATES OF PROTEIN SOLUTIONS IN HEAT TRANSFER EQUIPMENT by Ian C. Rose B.E. (1993) University of Auckland, N.Z. A THESIS SUBMITTED IN PARTIAL FULFILLMENT OF THE REQUIREMENTS FOR THE DEGREE OF DOCTOR OF PHILOSOPHY in THE FACULTY OF GRADUATE STUDIES Department of Chemical and Bio-Resource Engineering We accept this thesis as conforming to the required standard THE UNIVERSITY OF BRITISH COLUMBIA April, 1999. ©Ian Rose, 1999. In presenting this thesis in partial fulfilment of the requirements for an advanced degree at the University of British Columbia, I agree that the Library shall make it freely available for reference and study. 1 further agree that permission for extensive copying of this thesis for scholarly purposes may be granted by the head of my department or by his or her representatives. It is understood that copying or publication of this thesis for financial gain shall not be allowed without my written permission. Department of CK^ICAI <?vj 7j(e- R^a^r^ -C^^e.*^^ The University of British Columbia Vancouver, Canada Date / Apr-'i \ tftl DE-6 (2/88) ii Abstract As protein solutions are heated, denaturation and aggregation processes give rise to deposition on the heated surface. The present study undertakes the problem of understanding how process variables such as fluid velocity and temperature affect the initial fouling rate. Previous studies of chemical reaction fouling for other systems have demonstrated contrasting behaviour of the initial fouling rate with respect to fluid velocity: some investigations report an increase, others a decrease, and still others both an increase followed by a decrease of initial fouling rate with increasing fluid velocity. -
NAIRA) Operations
Department of the Army Pamphlet 50–5 Nuclear and Chemical Weapons and Materiel Nuclear Accident or Incident Response and Assistance (NAIRA) Operations Headquarters Department of the Army Washington, DC 20 March 2002 UNCLASSIFIED SUMMARY of CHANGE DA PAM 50–5 Nuclear Accident or Incident Response and Assistance (NAIRA) Operations This pamphlet-- o Supersedes Training Circular (TC) 3-15, Nuclear Accident and Incident Response and Assistance (NAIRA), 27 December 1988. Eliminates the responsibilities of Army commanders to respond to accidents involving Army nuclear weapons or Army nuclear weapon delivery systems. The Army no longer possesses these assets. o Highlights general guidance for responding to radiological emergencies involving both nuclear weapons and nuclear reactor facilities. This chapter is general in nature and directs the reader to previously published and approved procedures (chap 2). o Clarifies response requirements for accidents occurring at one of the Army’s nuclear reactors. Because of the absence of explosive material in a reactor, and the physical construction of a nuclear reactor facility, there exists an inherent ability to restrict the spread of contamination should an accident occur. The actions taken to prevent contamination and damage to personnel and property are significantly different from the actions taken in an accident involving a nuclear weapon (chap 3). o Summarizes the objectives of each element responding to a nuclear accident. Although many of the actions required to successfully recover from a nuclear accident or incident will have inputs from several responders, specified elements (chap 4) will be responsible and will monitor each objective. Headquarters *Department of the Army Department of the Army Pamphlet 50–5 Washington, DC 20 March 2002 Nuclear and Chemical Weapons and Materiel Nuclear Accident or Incident Response and Assistance (NAIRA) Operations Army Regulation 50–5 for nuclear acci- a r e c o n s i s t e n t w i t h c o n t r o l l i n g l a w a n d dent or incident response and assistance r e g u l a t i o n .