Carbon Nanotubes Versus Graphene As Flexible Transparent Electrodes
Total Page:16
File Type:pdf, Size:1020Kb
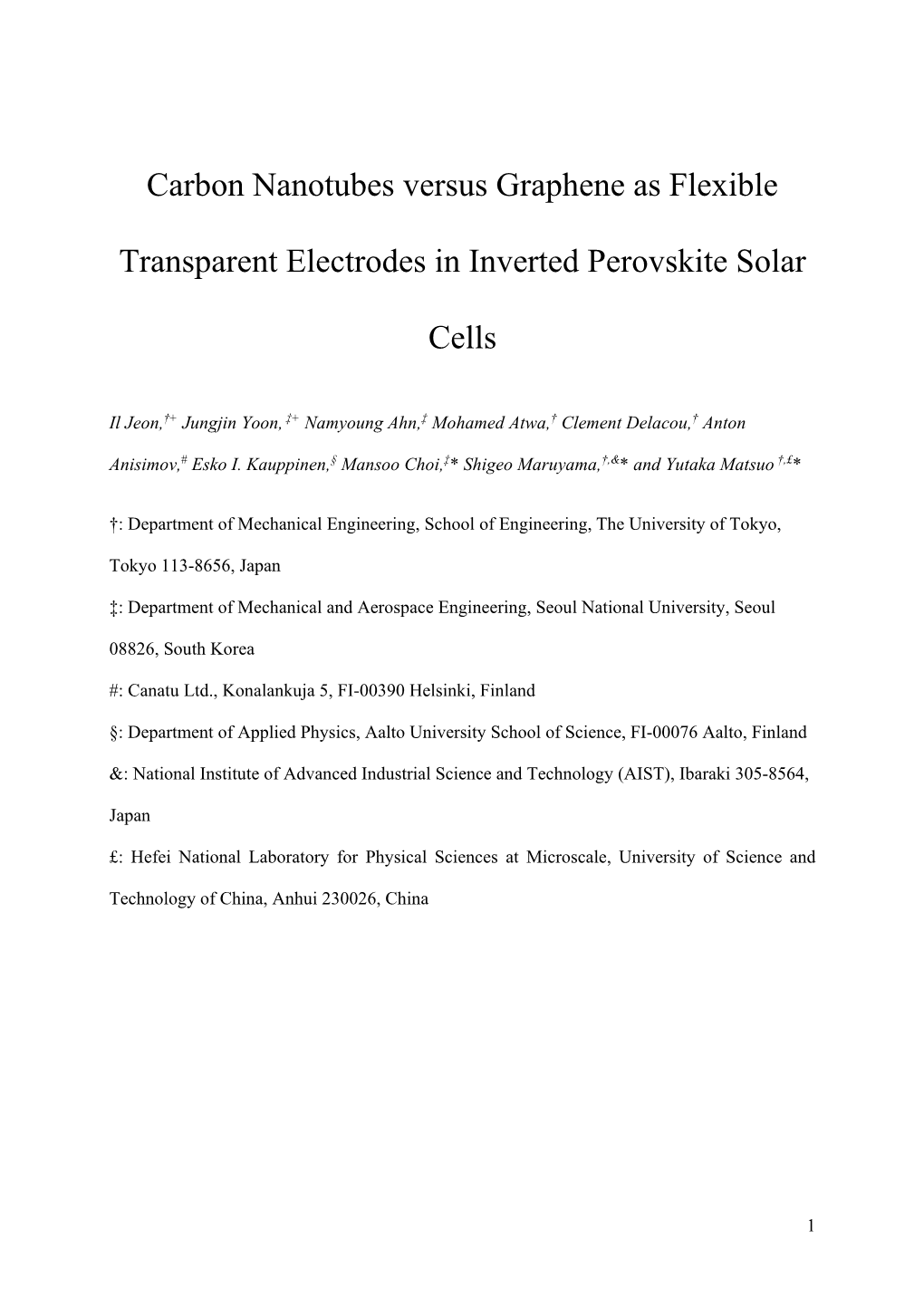
Load more
Recommended publications
-
CNT Technical Interchange Meeting
Realizing the Promise of Carbon Nanotubes National Science and Technology Council, Committee on Technology Challenges, Oppor tunities, and the Path w a y to Subcommittee on Nanoscale Science, Engineering, and Technology Commer cializa tion Technical Interchange Proceedings September 15, 2014 National Nanotechnology Coordination Office 4201 Wilson Blvd. Stafford II, Rm. 405 Arlington, VA 22230 703-292-8626 [email protected] www.nano.gov Applications Commercial Product Characterization Synthesis and Processing Modeling About the National Nanotechnology Initiative The National Nanotechnology Initiative (NNI) is a U.S. Government research and development (R&D) initiative involving 20 Federal departments, independent agencies, and independent commissions working together toward the shared and challenging vision of a future in which the ability to understand and control matter at the nanoscale leads to a revolution in technology and industry that benefits society. The combined, coordinated efforts of these agencies have accelerated discovery, development, and deployment of nanotechnology to benefit agency missions in service of the broader national interest. About the Nanoscale Science, Engineering, and Technology Subcommittee The Nanoscale Science, Engineering, and Technology (NSET) Subcommittee is the interagency body responsible for coordinating, planning, implementing, and reviewing the NNI. NSET is a subcommittee of the Committee on Technology (CoT) of the National Science and Technology Council (NSTC), which is one of the principal means by which the President coordinates science and technology policies across the Federal Government. The National Nanotechnology Coordination Office (NNCO) provides technical and administrative support to the NSET Subcommittee and supports the Subcommittee in the preparation of multiagency planning, budget, and assessment documents, including this report. -
Carbon Nanotube Research Developments in Terms of Published Papers and Patents, Synthesis and Production
View metadata, citation and similar papers at core.ac.uk brought to you by CORE provided by Elsevier - Publisher Connector Scientia Iranica F (2012) 19 (6), 2012–2022 Sharif University of Technology Scientia Iranica Transactions F: Nanotechnology www.sciencedirect.com Carbon nanotube research developments in terms of published papers and patents, synthesis and production H. Golnabi ∗ Institute of Water and Energy, Sharif University of Technology, Tehran, P.O. Box 11555-8639, Iran Received 16 April 2012; revised 12 May 2012; accepted 10 October 2012 KEYWORDS Abstract Progress of carbon nanotube (CNT) research and development in terms of published papers and Published references; patents is reported. Developments concerning CNT structures, synthesis, and major parameters, in terms Paper; of the published documents are surveyed. Publication growth of CNTs and related fields are analyzed for Patent; the period of 2000–2010. From the explored search term, ``carbon nanotubes'', the total number of papers Nanotechnology; containing the CNT concept is 52,224, and for patents is 5,746, with a patent/paper ratio of 0.11. For CNT Synthesis. research in the given period, an annual increase of 8.09% for paper and 8.68% for patents are resulted. Pub- lished papers for CNT, CVD and CCVD synthesis parameters for the period of 2000–2010 are compared. In other research, publications for CNT laser synthesis, for the period of 2000–2010, are reviewed. Publica- tions for major laser parameters in CNT synthesis for the period of 2000–2010 are described. The role of language of the published references for CNT research for the period of 2000–2010 is also investigated. -
Carbon Nanotubes: Synthesis, Integration, and Properties
Acc. Chem. Res. 2002, 35, 1035-1044 Carbon Nanotubes: Synthesis, Integration, and Properties HONGJIE DAI* Department of Chemistry, Stanford University, Stanford, California 94305 Received January 23, 2002 ABSTRACT Synthesis of carbon nanotubes by chemical vapor deposition over patterned catalyst arrays leads to nanotubes grown from specific sites on surfaces. The growth directions of the nanotubes can be controlled by van der Waals self-assembly forces and applied electric fields. The patterned growth approach is feasible with discrete catalytic nanoparticles and scalable on large wafers for massive arrays of novel nanowires. Controlled synthesis of nano- tubes opens up exciting opportunities in nanoscience and nano- technology, including electrical, mechanical, and electromechanical properties and devices, chemical functionalization, surface chem- istry and photochemistry, molecular sensors, and interfacing with soft biological systems. Introduction Carbon nanotubes represent one of the best examples of novel nanostructures derived by bottom-up chemical synthesis approaches. Nanotubes have the simplest chemi- cal composition and atomic bonding configuration but exhibit perhaps the most extreme diversity and richness among nanomaterials in structures and structure-prop- erty relations.1 A single-walled nanotube (SWNT) is formed by rolling a sheet of graphene into a cylinder along an (m,n) lattice vector in the graphene plane (Figure 1). The (m,n) indices determine the diameter and chirality, which FIGURE 1. (a) Schematic honeycomb structure of a graphene sheet. Single-walled carbon nanotubes can be formed by folding the sheet are key parameters of a nanotube. Depending on the along lattice vectors. The two basis vectors a1 and a2 are shown. chirality (the chiral angle between hexagons and the tube Folding of the (8,8), (8,0), and (10,-2) vectors lead to armchair (b), axis), SWNTs can be either metals or semiconductors, with zigzag (c), and chiral (d) tubes, respectively. -
Investigation of Carbon Nanotube Grafted Graphene Oxide Hybrid Aerogel for Polystyrene Composites with Reinforced Mechanical Performance
polymers Article Investigation of Carbon Nanotube Grafted Graphene Oxide Hybrid Aerogel for Polystyrene Composites with Reinforced Mechanical Performance Yanzeng Sun †, Hui Xu †, Zetian Zhao, Lina Zhang, Lichun Ma, Guozheng Zhao, Guojun Song * and Xiaoru Li * Institute of Polymer Materials, School of Material Science and Engineering, Qingdao University, No. 308 Ningxia Road, Qingdao 266071, China; [email protected] (Y.S.); [email protected] (H.X.); [email protected] (Z.Z.); [email protected] (L.Z.); [email protected] (L.M.); [email protected] (G.Z.) * Correspondence: [email protected] (G.S.); [email protected] (X.L.) † Yanzeng Sun and Hui Xu are co-first authors. Abstract: The rational design of carbon nanomaterials-reinforced polymer matrix composites based on the excellent properties of three-dimensional porous materials still remains a significant challenge. Herein, a novel approach is developed for preparing large-scale 3D carbon nanotubes (CNTs) and graphene oxide (GO) aerogel (GO-CNTA) by direct grafting of CNTs onto GO. Following this, styrene was backfilled into the prepared aerogel and polymerized in situ to form GO–CNTA/polystyrene (PS) nanocomposites. The results of X-ray photoelectron spectroscopy (XPS) and Raman spectroscopy indicate the successful establishment of CNTs and GO-CNT and the excellent mechanical properties of the 3D frameworks using GO-CNT aerogel. The nanocomposite fabricated with around 1.0 wt% GO- CNT aerogel displayed excellent thermal conductivity of 0.127 W/m·K and its mechanical properties Citation: Sun, Y.; Xu, H.; Zhao, Z.; Zhang, L.; Ma, L.; Zhao, G.; Song, G.; were significantly enhanced compared with pristine PS, with its tensile, flexural, and compressive Li, X. -
Carbon-Based Nanomaterials/Allotropes: a Glimpse of Their Synthesis, Properties and Some Applications
materials Review Carbon-Based Nanomaterials/Allotropes: A Glimpse of Their Synthesis, Properties and Some Applications Salisu Nasir 1,2,* ID , Mohd Zobir Hussein 1,* ID , Zulkarnain Zainal 3 and Nor Azah Yusof 3 1 Materials Synthesis and Characterization Laboratory (MSCL), Institute of Advanced Technology (ITMA), Universiti Putra Malaysia, 43400 Serdang, Selangor, Malaysia 2 Department of Chemistry, Faculty of Science, Federal University Dutse, 7156 Dutse, Jigawa State, Nigeria 3 Department of Chemistry, Faculty of Science, Universiti Putra Malaysia, 43400 Serdang, Selangor, Malaysia; [email protected] (Z.Z.); [email protected] (N.A.Y.) * Correspondence: [email protected] (S.N.); [email protected] (M.Z.H.); Tel.: +60-1-2343-3858 (M.Z.H.) Received: 19 November 2017; Accepted: 3 January 2018; Published: 13 February 2018 Abstract: Carbon in its single entity and various forms has been used in technology and human life for many centuries. Since prehistoric times, carbon-based materials such as graphite, charcoal and carbon black have been used as writing and drawing materials. In the past two and a half decades or so, conjugated carbon nanomaterials, especially carbon nanotubes, fullerenes, activated carbon and graphite have been used as energy materials due to their exclusive properties. Due to their outstanding chemical, mechanical, electrical and thermal properties, carbon nanostructures have recently found application in many diverse areas; including drug delivery, electronics, composite materials, sensors, field emission devices, energy storage and conversion, etc. Following the global energy outlook, it is forecasted that the world energy demand will double by 2050. This calls for a new and efficient means to double the energy supply in order to meet the challenges that forge ahead. -
Review on Carbon Nanomaterials-Based Nano-Mass and Nano-Force Sensors by Theoretical Analysis of Vibration Behavior
sensors Review Review on Carbon Nanomaterials-Based Nano-Mass and Nano-Force Sensors by Theoretical Analysis of Vibration Behavior Jin-Xing Shi 1, Xiao-Wen Lei 2 and Toshiaki Natsuki 3,4,* 1 Department of Production Systems Engineering and Sciences, Komatsu University, Nu 1-3 Shicyomachi, Komatsu, Ishikawa 923-8511, Japan; [email protected] 2 Department of Mechanical Engineering, University of Fukui, 3-9-1 Bunkyo, Fukui 910-8507, Japan; [email protected] 3 Faculty of Textile Science and Technology, Shinshu University, 3-15-1 Tokida, Ueda-shi 386-8567, Japan 4 Institute of Carbon Science and Technology, Shinshu University, 4-17-1 Wakasato, Nagano 380-8553, Japan * Correspondence: [email protected] Abstract: Carbon nanomaterials, such as carbon nanotubes (CNTs), graphene sheets (GSs), and carbyne, are an important new class of technological materials, and have been proposed as nano- mechanical sensors because of their extremely superior mechanical, thermal, and electrical perfor- mance. The present work reviews the recent studies of carbon nanomaterials-based nano-force and nano-mass sensors using mechanical analysis of vibration behavior. The mechanism of the two kinds of frequency-based nano sensors is firstly introduced with mathematical models and expressions. Af- terward, the modeling perspective of carbon nanomaterials using continuum mechanical approaches as well as the determination of their material properties matching with their continuum models are concluded. Moreover, we summarize the representative works of CNTs/GSs/carbyne-based Citation: Shi, J.-X.; Lei, X.-W.; nano-mass and nano-force sensors and overview the technology for future challenges. -
Carbon Nanotubes in Our Everyday Lives
Carbon Nanotubes in Our Everyday Lives Tanya David,* [email protected] Tasha Zephirin,** [email protected] Mohammad Mayy,* [email protected] Dr. Taina Matos,* [email protected] Dr. Monica Cox,** [email protected] Dr. Suely Black* [email protected] * Norfolk State University Center for Materials Research Norfolk, VA 23504 ** Purdue University Department of Engineering Education West Lafayette, IN 47907 Copyright Edmonds Community College 2013 This material may be used and reproduced for non-commercial educational purposes only. This module provided by MatEd, the National Resource Center for Materials Technology Education, www.materialseducation.org, Abstract: The objective of this activity is to create an awareness of carbon nanotubes (CNT) and how their use in future applications within the field of nanotechnology can benefit our society. This newly developed activity incorporates aspects of educational frameworks such as “How People Learn” (Bransford, Brown, & Cocking, 1999)) and “Backwards Design” (Wiggins & McTighe, 2005). This workshop was developed with high school and potentially advanced middle school students as the intended audience. The workshop facilitators provide a guided discussion via PowerPoint presentation on the relevance of nanotechnology in our everyday lives, as well as CNT potential applications, which are derived from CNT structures. An understanding of a carbon atom structure will be obtained through the use of hands-on models that introduce concepts such as bonding and molecular geometry. The discussion will continue with an explanation of how different types of molecular structures and arrangements (shapes) can form molecules and compounds to develop various products such as carbon sheets. -
ROBOTIC ARTIFICIAL MUSCLES University of Technology and Education, Cheonan 330-708, South Korea (E- Mail: [email protected])
1 Robotic Artificial Muscles: Current Progress and Future Perspectives Jun Zhang, Jun Sheng, Ciaran´ T. O’Neill, Conor J. Walsh, Robert J. Wood, Jee-Hwan Ryu, Jaydev P. Desai, and Michael C. Yip Abstract—Robotic artificial muscles are a subset of artificial details about the selection, design, and usage considerations muscles that are capable of producing biologically inspired mo- of various prominent robotic artificial muscles for generating tions useful for robot systems - i.e., large power-to-weight ratios, biomimetic motions. Past survey papers have either covered inherent compliance, and large range of motions. These actuators, ranging from shape memory alloys to dielectric elastomers, are the broad topic of general artificial muscles [1] or focused increasingly popular for biomimetic robots as they may operate on a few particular aspects of a specific robotic artificial without using complex linkage designs or other cumbersome muscle. For example, [2], [3] focused on the working mech- mechanisms. Recent achievements in fabrication, modeling, and anisms of artificial muscles, [17], [18] focused on aerospace control methods have significantly contributed to their potential applications and soft robots composed of SMA actuators, and utilization in a wide range of applications. However, no survey paper has gone into depth regarding considerations pertaining [4] focused on wearable robotic orthoses applications using to their selection, design, and usage in generating biomimetic robotic artificial muscles. [19], [20] reviewed the models of motions. This paper will discuss important characteristics and SMA and McKibben actuators, [18] discussed the designs and considerations in the selection, design, and implementation of applications of SMA actuators, [21] reviewed the technology, various prominent and unique robotic artificial muscles for applications, and challenges of dielectric elastomer actuators biomimetic robots, and provide perspectives on next-generation muscle-powered robots. -
Interactions Between Parallel Carbon Nanotube Quantum Dots Key Technologies
Interactions between parallel carbon nanotube quantum dots quantum parallel carbon nanotube between Interactions Karin Goß Karin Schlüsseltechnologien Technologies Key Interactions between parallel carbon nanotube quantum dots Karin Goß Schlüsseltechnologien / Key Technologies Band / Volume 30 Mitglied der Helmholtz-GemeinschaftMitglied ISBN 978-3-89336-740-5 30 Schriften des Forschungszentrums Jülich Reihe Schlüsseltechnologien / Key Technologies Band / Volume 30 Forschungszentrum Jülich GmbH Peter Grünberg Institut (PGI) Elektronische Eigenschaften (PGI-6) Interactions between parallel carbon nanotube quantum dots Karin Goß Schriften des Forschungszentrums Jülich Reihe Schlüsseltechnologien / Key Technologies Band / Volume 30 ISSN 1866-1807 ISBN 978-3-89336-740-5 Bibliographic information published by the Deutsche Nationalbibliothek. The Deutsche Nationalbibliothek lists this publication in the Deutsche Nationalbibliografie; detailed bibliographic data are available in the Internet at http://dnb.d-nb.de. Publisher and Forschungszentrum Jülich GmbH Distributor: Zentralbibliothek 52425 Jülich Phone +49 (0) 24 61 61-53 68 · Fax +49 (0) 24 61 61-61 03 e-mail: [email protected] Internet: http://www.fz-juelich.de/zb Cover Design: Grafische Medien, Forschungszentrum Jülich GmbH Printer: Grafische Medien, Forschungszentrum Jülich GmbH Copyright: Forschungszentrum Jülich 2011 Schriften des Forschungszentrums Jülich Reihe Schlüsseltechnologien / Key Technologies Band / Volume 30 D 464 (Diss., Duisburg, Univ., 2011) ISSN 1866-1807 ISBN 978-3-89336-740-5 The complete volume is freely available on the Internet on the Jülicher Open Access Server (JUWEL) at http://www.fz-juelich.de/zb/juwel Neither this book nor any part of it may be reproduced or transmitted in any form or by any means, electronic or mechanical, including photocopying, microfilming, and recording, or by any information storage and retrieval system, without permission in writing from the publisher. -
Benzene-Derived Diamondoid Carbon Nanothreads J
3,0 Tube Polymer 1 Crespi et.al. H Phys Rev Le* Hoffman et.al. JACS 87 (2001) 133, 9023 (2011) C Benzene-Derived Diamondoid Carbon Nanothreads J. V. Badding, T. Fitzgibbons, V. Crespi, E. Xu, N. Alem Pennsylvania State University G. Cody Carnegie Institution of Washington S. K. Davidowski Arizona State University R. Hoffmann, B. Chen Funding: EFRee DOE Energy Cornell University Frontier Research Center M. Guthrie European Spallation Source Carbon Nanomaterial Dimensionality and Hybridization 0-d 1-d 2-d sp2 C60 nanotubes Graphene sp3 ? diamondoids Graphane sp3 Carbon Nanotube Theory Predictions 3,0 Tube Polymer I Hydrogen First evidence that very small sp3 sp3 tube predicted to form during a carbon nanotubes are high pressure reaction of benzene thermodynamically stable. Stojkovic, D. et.al. PRL 87, (2001) Wen, X-D. et.al. JACS 133, 9023 (2011) Benzene Rapid Decompression: Amorphous Product Liquid Benzene Yellow/white solid Diamond 25 GPa anvil cell Diamond gasket aer Anvil cell decompression Decompression rate ≈12-20 GPa/hr Broad spectral features Powder X-Ray Diffraction UV Raman Spectrum 257 nm excitaon Slow Decompression in Larger Volumes SNAP/ORNL Paris- Edinburgh cell allows for large sample volumes 43 cm (mg to tens of mg scale). Decompression rate ≈ 2-7 GPa/hr PCD WC Steel C13 Solid State NMR Reveals sp3 Bonding sp2 sp3 ~80 % sp3/ tetrahedral bonding 20% 80% TEM of Slowly Decompressed Benzene: Nanothreads! 10 nm After Sonication Fitzgibbons et.al., Benzene-derived carbon nanothreads. Nat. Mater. 14, 43-47 (2015) Crystalline order -
Van Der Waals Composite of Carbon Nanotube Coated by Fullerenes
1 Bucky-Corn: Van der Waals Composite of Carbon Nanotube Coated by Fullerenes Leonid A. Chernozatonskii,a*Anastasiya A. Artyukh,a Victor A. Demin,a Eugene A. Katzb,c* a. Emanuel Institute of Biochemical Physics, RA S, Moscow,119334 Russia b. Dept. of Solar Energy and Environmental Physics, The Jacob Blaustein Institutes for Desert Research (BIDR), Ben-Gurion University of the Negev, SedeBoker Campus 84990, Israel c. Ilse Katz Institute for Nanoscale Science & Technology, Ben Gurion University of the Negev, BeerSheva 84105, Israel Corresponding author, e-mail address: [email protected], [email protected] 2 ABSTRACT: Can C60 layer cover a surface of single-wall carbon nanotube (SWCNT) forming an exohedral pure-carbon hybrid with only VdW interactions? The paper addresses this question and demonstrates that the fullerene shell layer in such a bucky-corn structure can be stable. Theoretical study of structure, stability and electronic properties of the following bucky-corn hybrids is reported: C60 and C70 molecules on an individual SWCNT, C60 dimers on an individual SWCNT as well C60 molecules on SWNT bundles. The geometry and total energies of the bucky-corns were calculated by the molecular dynamics method while the density functional theory method was used to simulate the electronic band structures. TOC GRAPHICS KEYWORDS.Carbon hybrid nanostructure, nanotubes, fullerenes,fullerene dimers, molecular dynamics, density functional theory. 3 1. Introduction Organic photovoltaics (OPV) has been suggested as an alternative to conventional photovoltaics due to their light weight, mechanical flexibility, and processability of large-area, low-cost devices. In particular, intense research is directed towards the development of OPV with a bulk heterojunction (BHJ) where donor-type conjugated polymers (hole conducting) and acceptor-type (electron conducting) fullerenes or fullerene derivatives.1-3 Upon illumination, light is absorbed by the conjugated polymer resulting in the formation of a neutral and stable excited state on the polymer chain. -
Hybrid Structures and Strain-Tunable Electronic Properties of Carbon Nanothreads
Hybrid Structures and Strain-Tunable Electronic Properties of Carbon Nanothreads Weikang Wu,y Bo Tai,y Shan Guan,∗,z,y Shengyuan A. Yang,∗,y and Gang Zhang∗,{ yResearch Laboratory for Quantum Materials, Singapore University of Technology and Design, Singapore 487372, Singapore zBeijing Key Laboratory of Nanophotonics and Ultrafine Optoelectronic Systems, School of Physics, Beijing Institute of Technology, Beijing 100081, China. {Institute of High Performance Computing, Agency for Science, Technology and Research, 1 Fusionopolis Way, Singapore 138632, Singapore. E-mail: [email protected]; [email protected]; [email protected] arXiv:1803.04694v1 [cond-mat.mtrl-sci] 13 Mar 2018 1 Abstract The newly synthesized ultrathin carbon nanothreads have drawn great attention from the carbon community. Here, based on first-principles calculations, we investigate the electronic properties of carbon nanothreads under the influence of two important factors: the Stone-Wales (SW) type defect and the lattice strain. The SW defect is intrinsic to the polymer-I structure of the nanothreads and is a building block for the general hybrid structures. We find that the bandgap of the nanothreads can be tuned by the concentration of SW defects in a wide range of 3:92 ∼ 4:82 eV, interpolating between the bandgaps of sp3-(3,0) structure and the polymer-I structure. Under strain, the bandgaps of all the structures, including the hybrid ones, show a nonmonotonic variation: the bandgap first increases with strain, then drops at large strain above 10%. The gap size can be effectively tuned by strain in a wide range (> 0:5 eV). Interestingly, for sp3-(3,0) structure, a switch of band ordering occurs under strain at the valence band maximum, and for the polymer-I structure, an indirect-to-direct-bandgap transition occurs at about 8% strain.