Copolymerization of Carbon Dioxide with Propylene Oxide and Chain Transfer Agents
Total Page:16
File Type:pdf, Size:1020Kb
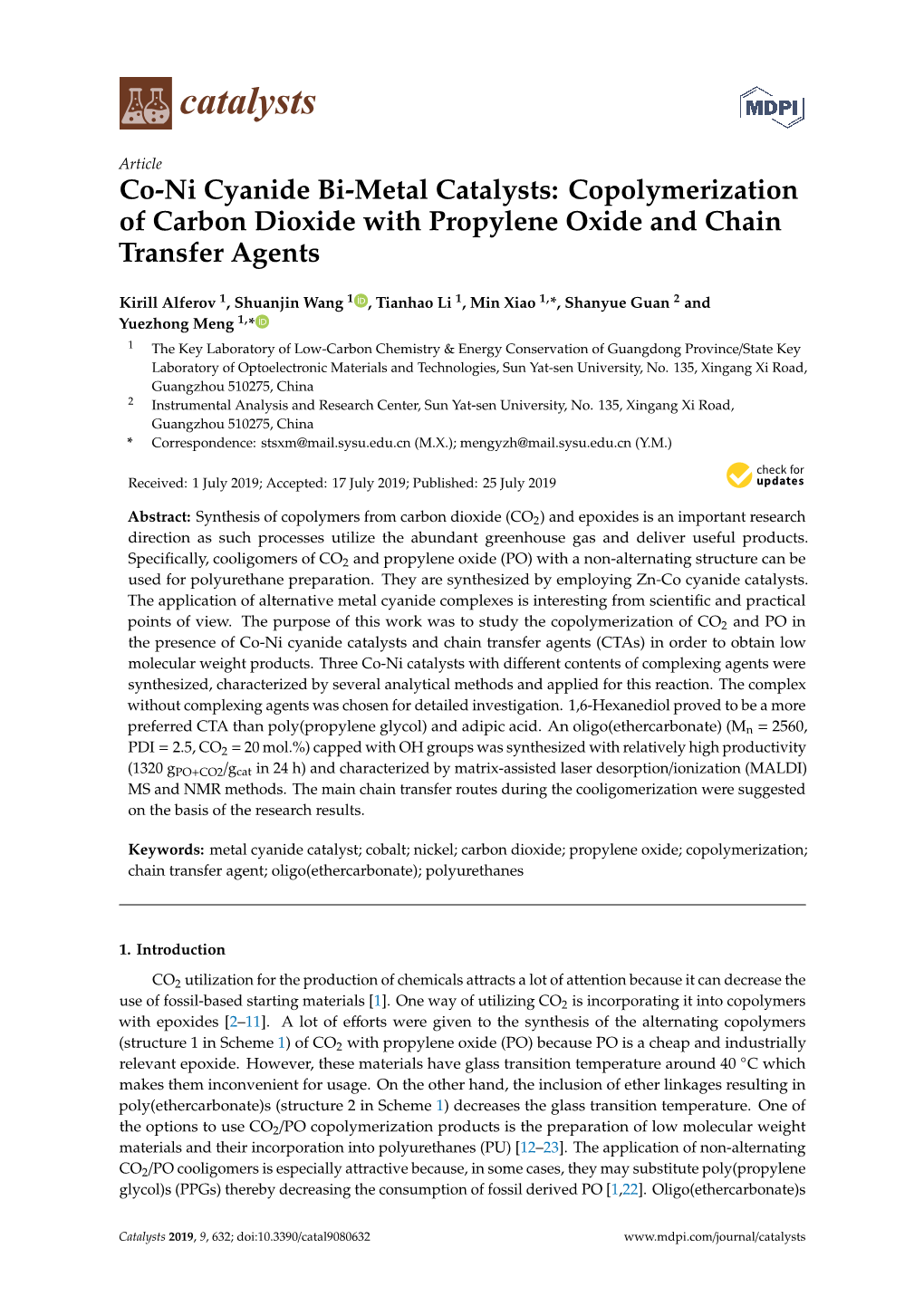
Load more
Recommended publications
-
Mechanochemical Preparation of Novel Polysaccharide-Supported Nb2o5 Catalysts
catalysts Article Mechanochemical Preparation of Novel Polysaccharide-Supported Nb2O5 Catalysts Esther Rincon 1, Araceli Garcia 1 , Antonio A. Romero 1 , Luis Serrano 2 , Rafael Luque 1,3,* and Alina M. Balu 1,* 1 Departamento de Quimica Organica, Universidad de Cordoba, Campus de Rabanales, Edificio Marie Curie (C-3), Ctra Nnal IV-A, Km. 396, E-14014 Cordoba, Spain; [email protected] (E.R.); [email protected] (A.G.); [email protected] (A.A.R.) 2 Chemical Engineering Department, Faculty of Sciences, Building Marie-Curie, Campus of Rabanales, University of Cordoba, 14014 Cordoba, Spain; [email protected] 3 Scientific Center for Molecular Design and Synthesis of Innovative Compounds for the Medical Industry, People´s Friendship University of Russia (RUDN University), 6 Miklukho-Maklaya str., 117198 Moscow, Russia * Correspondence: [email protected] (R.L.); [email protected] (A.M.B.) Received: 26 November 2018; Accepted: 17 December 2018; Published: 3 January 2019 Abstract: Polysaccharides extracted from natural sources can be used as starting material for the preparation of nanoparticle supported composites. A novel family of bio-nanocomposites was mechanochemically synthesized by using niobium oxide and enzymatically produced polysaccharides. The structural, textural and surface properties of nanomaterials, were determined by X-Ray diffraction (XRD), nitrogen adsorption-desorption (N_2 porosimetry), pulse chromatography, infrared spectroscopy (ATR-IR) and dynamic light scattering (DLS). Selective oxidation of isoeugenol to vanillin was carried out to demonstrate the catalytic activity of the Nb-polysaccharides nanocomposites. Interestingly, most of our material showed high conversion of isoeugenol (60–70%) with selectivity to vanillin over 40%. The optimum conversion and selectivity were achieved with a reaction time between 8 and 24 h. -
Mechanochemistry and Preparation O Nanocrystalline Materials
A. ALÁÈOVÁ,ALÁÈOVÁ J. et 'ICERIOVÁ, al.: MECHANOCHEMISTRY M. GOLJA AND PREPARATION O' NANOCRYSTALLINE MATERIALSISSN 0543-5846 METABK 43 (4) 305-309 (2004) UDC - UDK 541.12:669.09:549.1=111 MECHANOCHEMISTRY AND PREPARATION O NANOCRYSTALLINE MATERIALS Received - Primljeno: 2003-02-30 Accepted - Prihvaæeno: 2003-07-30 Preliminary Note - Prethodno priopæenje The possibility of application of mechanochemistry in extractive metallurgy and material science is illustrated. Surface oxidation of mechanically activated sulphides, sorption properties of CaCO after mechanical activa- 3 tion, gold leaching from mechanochemically pretreated Cu-Pb-Zn complex concentrate and pilot plant tests of mechanochemical technology (process MELT) have been selected as examples of application of mechanochem- istry in physical chemistry and extractive metallurgy. The mechanochemical reduction of Cu S with the aim to 2 prepare nanocrystalline copper can serve as an example of a novel process for preparation of advanced mate- rials in materials science. Key words: mechanochemistry, leaching, sorption, reduction, mineral Mehanokemija i priprema nanokristaliniènih materijala. U radu su prikazane mo-guænosti primjene mehanokemije na procese ekstrakcije u metalurgiji i znanosti o materijalima. Za primjer takve primjene mehanokemije u fizièkoj kemiji i metalurgiji ekstrakcije odabrani su oksidacija povrine mehanièki aktiviranih sulfida, apsorpciona svojstva CaCO nakon mehanièkog aktiviranja, izdvajanje zlata luenjem prethodno 3 mehanokemijski pripremljenog kompleksnog koncentrata -
Mechanochemical Transformation of Planar Polyarenes to Curved Fused-Ring Systems ✉ ✉ Teoh Yong1,2, Gábor Báti1,2, Felipe García 1 & Mihaiela C
ARTICLE https://doi.org/10.1038/s41467-021-25495-6 OPEN Mechanochemical transformation of planar polyarenes to curved fused-ring systems ✉ ✉ Teoh Yong1,2, Gábor Báti1,2, Felipe García 1 & Mihaiela C. Stuparu 1 The transformation of planar aromatic molecules into π-extended non-planar structures is a challenging task and has not been realized by mechanochemistry before. Here we report that mechanochemical forces can successfully transform a planar polyarene into a curved geo- 1234567890():,; metry by creating new C-C bonds along the rim of the molecular structure. In doing so, mechanochemistry does not require inert conditions or organic solvents and provide better yields within shorter reaction times. This is illustrated in a 20-minute synthesis of cor- annulene, a fragment of fullerene C60, in 66% yield through ball milling of planar tetra- bromomethylfluoranthene precursor under ambient conditions. Traditional solution and gas-phase synthetic pathways do not compete with the practicality and efficiency offered by the mechanochemical synthesis, which now opens up a new reaction space for inducing curvature at a molecular level. 1 Division of Chemistry and Biological Chemistry, School of Physical and Mathematical Sciences, Nanyang Technological University, Singapore, Singapore. ✉ 2These authors contributed equally: Teoh Yong, Gábor Báti. email: [email protected]; [email protected] NATURE COMMUNICATIONS | (2021) 12:5187 | https://doi.org/10.1038/s41467-021-25495-6 | www.nature.com/naturecommunications 1 ARTICLE NATURE COMMUNICATIONS | https://doi.org/10.1038/s41467-021-25495-6 he synthesis of strained aromatic molecules from strain-free Br Br precursors is a challenging task. This requires the natural T 2 trigonal planar geometry of the sp -hybridised carbon atoms to become non-planar. -
Todd Martinez David Mulvane Ehrsam and Edward Curtis Franklin Professor of Chemistry and Professor of Photon Science
Todd Martinez David Mulvane Ehrsam and Edward Curtis Franklin Professor of Chemistry and Professor of Photon Science CONTACT INFORMATION • Administrative Contact Maggie Yeung - Administrative Associate Email [email protected] Tel (650) 724-7306 Bio BIO Theoretical chemist Todd Martínez develops and applies new methods that predict and explain how atoms move in molecules. These methods are used both to design new molecules and to understand the behavior of those that already exist. His research group studies the response of molecules to light (photochemistry) and external force (mechanochemistry). Photochemistry is a critical part of human vision, single-molecule spectroscopy, harnessing solar energy (either to make fuels or electricity), and even organic synthesis. Mechanochemistry represents a novel scheme to promote unusual reactions and potentially to create self-healing materials that resist degradation. The underlying tools embody the full gamut of quantum mechanical effects governing molecules, from chemical bond breaking/formation to electron/ proton transfer and electronic excited states. Professor Martínez was born in Amityville, New York, but spent most of his childhood in Central America and the Caribbean. His chemical curiosity benefitted tremendously from the relaxed safety standards in Central American chemical supply houses, giving him unfettered access to strong acids and bases. When he also became interested in computation, limited or nonexistent computer access forced him to write and debug computer programs on paper. Today, Prof. Martínez combines these interests by working toward theoretical and computational modeling and design of molecules. Martínez received his PhD in chemistry from UCLA in 1994. After postdoctoral study at UCLA and the Hebrew University in Jerusalem, he joined the faculty at the University of Illinois in 1996. -
Exploration of Novel Carbon-Hydrogen Interactions
IV.H.10 Exploration of Novel Carbon-Hydrogen Interactions dynamics with reactive force fields (ReaxFF) have been Angela D. Lueking (Primary Contact), implemented in modeling compressed hydrocarbons and Xiao Ming Liu, En Shi Xu, Thomas C. Fitzgibbons, hydrogenated C60 (mainly C60H36 and C60H18, systems also being investigated experimentally). The cage structure of C Paramita Ray, Greg Larsen, Youjian Tang, 60 and the interplay between inter-ball polymerization into sp3 Humberto R. Gutierrez, John V. Badding, 3 Vincent H. Crespi geometries and on-ball sp sites of H attachment could be beneficial for loading hydrogen into local traps. Compression The Pennsylvania State University of two initial crystal structures of C H was simulated 120 Hosler 60 36 University Park, PA 16802 by ReaxFF under a series of high pressures up to 30 GPa. Phone: (814) 862-6256 Polymerization of hydrogenated C60 is not achieved under Email: [email protected] hydrostatic compression, but under shock compression it can be induced, with hydrogen released. A simple theoretical DOE Program Officer: Bonnie Gersten model for understanding the propensity for H release during Phone: (301) 903-0002 compression of various hydrocarbon systems has been Email: [email protected] designed in which a volume is associated with each bond type (C-H, etc.). The model shows consistency with simple alkane molecules. The model needs more delicate tweaks to accommodate complex hydrocarbons such as hydrogenated Objectives C60 with the simulation support of first principle theory and ReaxFF. Hydrogen trapped in a carbon cage, captured through repulsive interactions, is a novel concept in hydrogen storage Experimentally, C60H14 has been synthesized to validate which borrows an idea from macroscale hydrogen storage the ReaxFF models. -
Chem Soc Rev
Chem Soc Rev View Article Online REVIEW ARTICLE View Journal | View Issue The historical development of mechanochemistry Cite this: Chem. Soc. Rev., 2013, Laszlo Takacs* 42, 7649 This paper reviews the history of mechanochemistry. It begins with prehistoric times, when reactions could be initiated during grinding and rubbing accidentally, and follows the main developments until recent results and current trends. There are very few records on mechanochemistry until the first systematic investigations by Spring and Lea at the end of the 19th century. For the next decades, mechanochemistry developed slowly; minerals, inorganic compounds, and polymers were the main subjects of investigation. The area became more organized in the 1960s, when several large groups were established and the first dedicated conferences were held. Mechanical alloying was invented in 1966 independently and it became a subject of intense research. Interaction between the two topics was established in the 1990s. In recent years, the mechanochemical synthesis of organic compounds was added to the main subjects and the invention of the atomic force microscope provided new ways to manipulate atoms and molecules by direct mechanical action. The theoretical explanation of mechanochemical phenomena is difficult, as the mechanism is system specific and several length and Received 28th October 2012 time scales are involved. Thiessen proposed the first theory, the magma–plasma model, in 1967, and DOI: 10.1039/c2cs35442j deeper insight is being obtained by computer modelling combined with empirical work. Practical applications have been an important motivation throughout the history of mechanochemistry. It is used www.rsc.org/csr alone or in combination with other steps in an increasing number of technologies. -
And One-Dimensional Titanium Oxide-Based Nano-Photocatalysts Dimitrios Giannakoudakis, Gregory Chatel, Juan Carlos Colmenares
Mechanochemical Forces as a Synthetic Tool for Zero- and One-Dimensional Titanium Oxide-Based Nano-photocatalysts Dimitrios Giannakoudakis, Gregory Chatel, Juan Carlos Colmenares To cite this version: Dimitrios Giannakoudakis, Gregory Chatel, Juan Carlos Colmenares. Mechanochemical Forces as a Synthetic Tool for Zero- and One-Dimensional Titanium Oxide-Based Nano-photocatalysts. Topics in current chemistry, Springer, 2020, 378 (1), 10.1007/s41061-019-0262-3. hal-02378286 HAL Id: hal-02378286 https://hal.archives-ouvertes.fr/hal-02378286 Submitted on 25 Nov 2019 HAL is a multi-disciplinary open access L’archive ouverte pluridisciplinaire HAL, est archive for the deposit and dissemination of sci- destinée au dépôt et à la diffusion de documents entific research documents, whether they are pub- scientifiques de niveau recherche, publiés ou non, lished or not. The documents may come from émanant des établissements d’enseignement et de teaching and research institutions in France or recherche français ou étrangers, des laboratoires abroad, or from public or private research centers. publics ou privés. Topics in Current Chemistry (2020) 378:2 https://doi.org/10.1007/s41061-019-0262-3 REVIEW Mechanochemical Forces as a Synthetic Tool for Zero‑ and One‑Dimensional Titanium Oxide‑Based Nano‑photocatalysts Dimitrios A. Giannakoudakis1 · Gregory Chatel2 · Juan Carlos Colmenares1 Received: 30 July 2019 / Accepted: 22 October 2019 © The Author(s) 2019 Abstract A new feld where the utilization of mechanochemistry can create new opportunities is materials chemistry, and, more interestingly, the synthesis of novel nanomateri- als. Ball-milling procedures and ultrasonic techniques can be regarded as the most important mechanochemical synthetic tools, since they can act as attractive alterna- tives to the conventional methods. -
New Lipidyl-Cyclodextrins Obtained by Ring Opening of Methyl Oleate Epoxide Using Ball Milling
biomolecules Article New Lipidyl-Cyclodextrins Obtained by Ring Opening of Methyl Oleate Epoxide Using Ball Milling Estefania Oliva 1, David Mathiron 2 ,Sébastien Rigaud 2, Eric Monflier 3 , Emmanuel Sevin 4, Hervé Bricout 3,Sébastien Tilloy 3 , Fabien Gosselet 4 , Laurence Fenart 4, Véronique Bonnet 1 , Serge Pilard 2 and Florence Djedaini-Pilard 1,* 1 LG2A UMR CNRS 7378, Université de Picardie Jules Verne, 80039 Amiens CEDEX, France; [email protected] (E.O.); [email protected] (V.B.) 2 Plateforme Analytique, Université de Picardie Jules Verne, 80039 Amiens CEDEX, France; [email protected] (D.M.); [email protected] (S.R.); [email protected] (S.P.) 3 Univ. Artois, CNRS, Centrale Lille, Univ. Lille, UMR 8181–UCCS–Unité de Catalyse et Chimie du Solide, F-62300 Lens, France; eric.monfl[email protected] (E.M.); [email protected] (H.B.); [email protected] (S.T.) 4 LBHE EA 2465, Université d’Artois, 62307 Lens CEDEX, France; [email protected] (E.S.); [email protected] (F.G.); [email protected] (L.F.) * Correspondence: fl[email protected]; Tel.: +33-322-827-562 Received: 22 January 2020; Accepted: 15 February 2020; Published: 20 February 2020 Abstract: Bearing grafts based on fatty esters derivatives, lipidyl-cyclodextrins (L-CDs) are compounds able to form water-soluble nano-objects. In this context, bicatenary biobased lipidic-cyclodextrins of low DS were easily synthesized from a fatty ester epoxide by means of alternative methods (ball-milling conditions, use of enzymes). -
Mechanical Activation of Solids in Extractive Metallurgy
MECHANICAL ACTIVATION OF SOLIDS IN EXTRACTIVE METALLURGY SANJAY KUMAR*, T. C. ALEX AND RAKESH KUMAR *E mail: [email protected] INTRODUCTION Mechanochemistry is the branch of chemistry that has primarily evolved in the twentieth century. It deals with the field of reactions caused by mechanical energy, often referred to as Mechanical or Mechanochemical Activation [1-3]. The process of activation depends on the breakage process and the rate at which energy is supplied to the system [1-3]. In contrast to coarse grinding, where the objective is size reduction, mechanical activation is concerned with structural changes that are brought about by application of mechanical energy. Fine grinding is an intermediate case between coarse grinding and mechanical activation [1-3]. Mechanical activation has been attempted in a variety of disciplines, such as extractive metallurgy, waste utilisation, mechanical alloying, advanced ceramics, catalysis, coal gasification, paints and dyes, fertilizers, drugs and pharmaceuticals, organometallic synthesis, and many others. The changes occurring in solids during the course of mechanical activation are listed below: (a) Milling of the particles to a very small size (b) Generation of large new surfaces. (c) Formation of dislocations and point defects in the crystalline structure. (d) Phase transformations in polymorphic materials. (e) Chemical reactions: decomposition, ionic exchange, oxidation-reduction, complex and adduct formation, etc. As mentioned earlier, mechanochemistry, as a discipline, has evolved in 20th Century and its definition and scope has expanded with time. We have summarized the historical evolution of mechanochemistry in Table 1. Table-1 : Evolution of Mechanochemistry 1919 Study of chemical transformations induced by gravitational and kinetic energy, as well as by energies connected with change in volume, surface andshape of material (Wilhelm Ostwald in Handbuch der allgemeinen Chimie) 1943 Study of correlations between chemical bonding and mechanical strength (G.R. -
Introductory Lecture: Mechanochemistry, a Versatile Synthesis Strategy for New Materials
Faraday Discussions Cite this: Faraday Discuss.,2014,170,9 View Article Online PAPER View Journal | View Issue Introductory Lecture: Mechanochemistry, a versatile synthesis strategy for new materials William Jones* and Mark D. Eddleston Received 28th August 2014, Accepted 2nd September 2014 DOI: 10.1039/c4fd00162a Mechanochemistry deals with reactions induced by the input of mechanical energy – for example by impacts within a vibratory ball mill. The technique has a long history with significant contributions from Ostwald, Carey Lea and, notably, Faraday. Mechanochemistry Creative Commons Attribution 3.0 Unported Licence. has subsequently seen application in a variety of areas of materials science including mechanical alloying in metallurgy, the synthesis of complex organic molecules and, more recently, the discovery and development of new solid forms of active pharmaceutical ingredients. This paper overviews the broad areas of application of mechanochemistry, some key features which make it a particularly attractive approach to materials synthesis and some mechanistic aspects highlighted within the literature. A significant part, however, will focus on recent applications in the area of pharmaceuticals and its important role in exploring the rich variety of solid forms available for small, drug-like, molecules. This article is licensed under a 1. Introduction Open Access Article. Published on 02 September 2014. Downloaded 05/08/2015 14:51:19. Mechanochemistry is a long-established method for the synthesis of solids and molecules. Its chemical -
General Approach to Mechanochemistry and Its Relation to Tribochemistry
Chapter 11 General Approach to Mechanochemistry and Its Relation to Tribochemistry Czesław Kajdas Additional information is available at the end of the chapter http://dx.doi.org/10.5772/50507 1. Introduction 1.1. Compact information on the considered disciplines Mechanochemistry and tribochemistry disciplines are of particular importance for fundamental research and tribology engineering practice. They relate to specific coupling of physical and chemical phenomena leading to initiation of heterogeneous chemical reactions due to mechanical action. Chemical reactions in solids initiated by mechanical action had been considered for a long period of time [1]. From the viewpoint of terms, mechanochemistry and tribochemistry may be compared with terms: physical chemistry and chemical physics. In the latter term physics is first and chemistry second. In tribochemistry, friction (tribos) is the first. Since mechanics includes friction, tribochemistry should be included in mechanochemistry. Reviews on mechanochemistry [2,3] show Matthew Carey Lea as the first systematic researcher on the chemical effects of mechanical action. Mechanochemical reactions are clearly distinct from those of thermochemical ones. To initiate thermochemical reactions an adequate heat amount has to be supplied to overcome the activation energy. Mechanical interaction of a solid-solid enables chemical reactions to be initiated by lower activation energy than regular thermochemical reactions. Even a very high calculated ‘flash temperature’ is short-lived, thus, it rather cannot initiate chemical reactions by heat. Reference [4] demonstrates that high local temperatures generated by friction at the contacts between rubbing surfaces can evolve thermionic activity, likely to be short lived and random. These localized, dynamic regions of intense thermionic emission can act as catalytic sites for chemical activity. -
Dana D. Dlott William H. and Janet G. Lycan Emeritus Professor of Chemistry
Curriculum Vitae Dana D. Dlott William H. and Janet G. Lycan Emeritus Professor of Chemistry Affiliation: School of Chemical Sciences and Fredrick Seitz Materials Research Laboratory Address: Box 01-6 CLSL, 600 S. Mathews Ave., Urbana, IL 61801 Phone: (217)-333-3574 Fax: (217)-244-3186 Email: [email protected] homepage: http://dlottgroup.scs.uiuc.edu/group/ Personal Information Date of Birth: September 12, 1952 Place of Birth: Los Angeles, California Marital Status: Married (Maria), one child Education Undergraduate: Columbia University, 1970-1974, A.B (Chemistry), 1974 Graduate: Stanford University, 1974-1979, Ph.D. (Chemistry), 1979, Thesis Title: "Picosecond Dynamics of Energy Transfer in Pure and Mixed Organic Crystals". Thesis supervised by Prof. Michael D. Fayer. Professional Experience: 1973-74 Teaching assistant and Research assistant, Columbia University, 1974-79 Teaching assistant and Research assistant, Stanford University 1979-86 Assistant Professor of Chemistry, University of Illinois at Urbana-Champaign 1986 Associate Professor of Chemistry, University of Illinois at Urbana-Champaign 1987 Member of the Graduate College 1993 Professor of Chemistry, University of Illinois at Urbana-Champaign 1999 Associate, Center for Advanced Study 2008 Research Professor, Fredrick Seitz Materials Research Laboratory 2009 William H. and Janet G. Lycan Professor of Chemistry 2011 Professor, Materials Research Laboratory 2017 Research Professor of Chemistry 2017 William H. and Janet G. Lycan Professor of Chemistry Emeritus Professional Societies: