Spacecraft High-Voltage Paschen and Corona Design Handbook
Total Page:16
File Type:pdf, Size:1020Kb
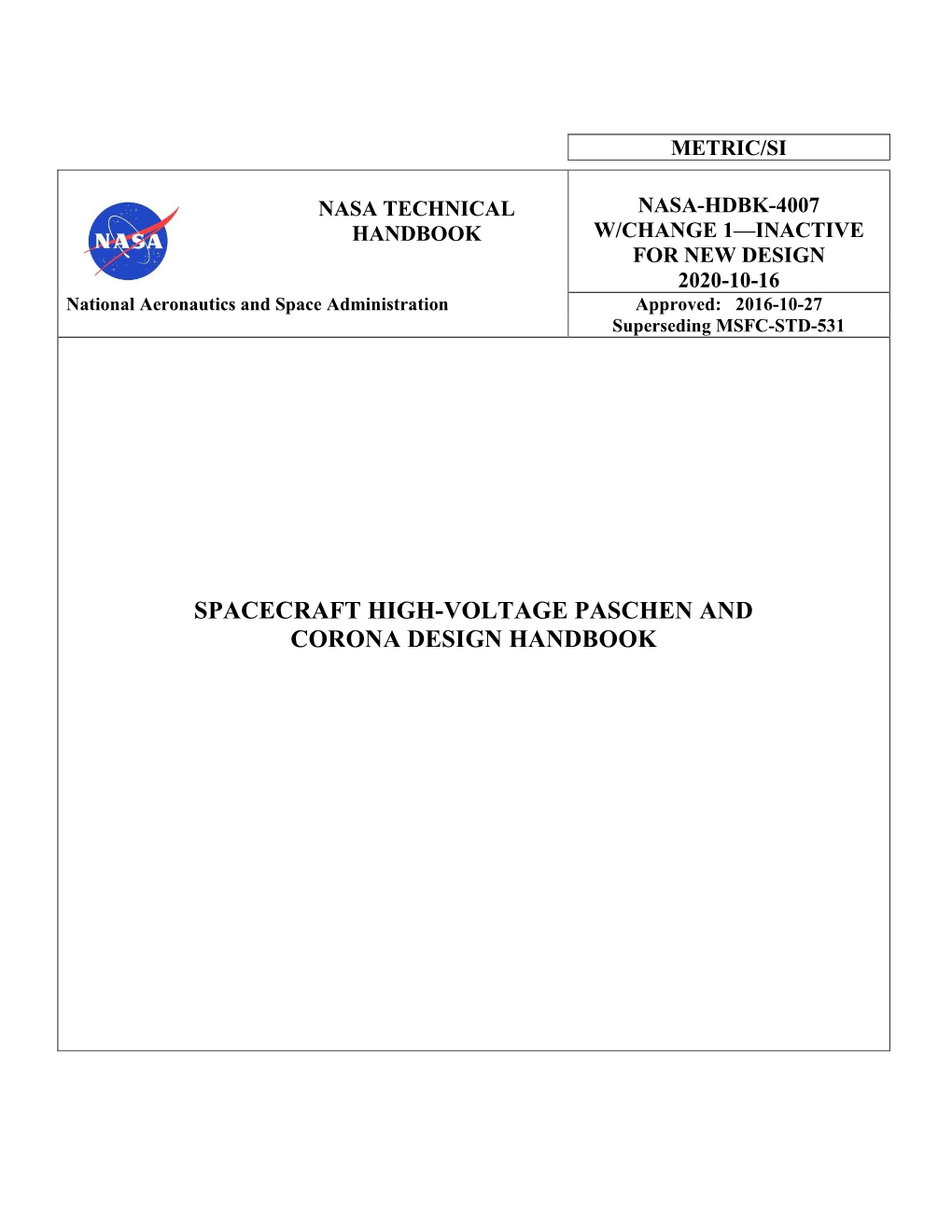
Load more
Recommended publications
-
Background Information Lichtenberg Figures
Factors That Affect Lichtenberg Figures Name Institution Date Background information Lichtenberg Figures Lichtenberg Figures are caused by electric discharges that sometimes occur on the surface of or inside insulating materials, such as wood, acrylic, or even human skin. German Physicist Georg Christoph Lichtenberg discovered them and subsequently researched them. In 1777, Lichtenberg built a large electrophorus to generate high voltage static electricity, after then discharging this high voltage he used pressed paper to record these patterns, this discovering the basic principle of xerography (What are Lichtenberg Figures? A bit of history..., 2020). These figures are of enormous interest because they exhibit fractal properties. A fractal is a never-ending pattern which repeats itself at different scales. This property is called “Self-Similarity”. Fractals are very complex; however, they are made by a straightforward repeating process. Fractals appear a lot in nature, such as in the shape of galaxies, hurricanes, and trees. One Fractal which is particularly well known is the Mandelbrot Set. What gives rise to these structures in nature? In this essay, I hypothesize what factors affect the formation of these Lichtenberg figures in insulating materials. Main Body The hypothesis I will discuss is that the following points affect the geometry Lichtenberg Figure; Distance between contact points, Duration of exposure, and Variation of material. As Lichtenberg Figures are caused by dielectric breakd changing these properties alter the electrodynamic properties of the material. By their very nature insulators do not readily allow current to flow through them, however the case of dialectic breakdown, we can see that this must be occurring. -
Lichtenberg Figures and How Are They Produced? Copyright Stoneridge Engineering, 1999-2004, Updated 8/15/04
What are Lichtenberg Figures and how are they produced? Copyright Stoneridge Engineering, 1999-2004, Updated 8/15/04 Lichtenberg Figures are patterns that are formed on the surface or inside insulating materials by high voltage electrical discharges. The first Lichtenberg Figures were actually two-dimensional patterns formed in dust on a charged plate in the laboratory of their discoverer, Georg Christoph Lichtenberg (1742-1799), a German physicist. The basic principles involved in the formation of these early figures are also fundamental to the operation of modern copy machines and laser printers. Using modern materials and powerful particle accelerators, 3-D Lichtenberg Figures can now be created inside clear plastic blocks, permanently forming beautiful “Captured Lightning ™”. Acrylic plastic (Polymethylmethacrylate - PMMA) is used as the medium for our Lichtenberg Figures because it has an excellent combination of optical, dielectric, and mechanical properties. A linear accelerator (LINAC) is used to produce large numbers of high-speed electrons - a high-energy electron beam (e-beam). Electrons in the beam are accelerated to up to 99.5% of the speed of light. These “relativistic” electrons have acquired a very large amount of kinetic energy (measured in Millions of Electron Volts or MeV). Specially selected and prepared pieces of acrylic are placed in the path of this electron beam. As the energetic electrons in the beam hit the surface of the acrylic, they don’t immediately stop. Instead, they collide with the molecules of acrylic, slowing down and coming to rest deep inside the block. Under continued irradiation, electrons rapidly accumulate inside the acrylic, forming a layer of excess negative charge called a space charge. -
Electrostatic Discharges and Multifractal Analysis of Their Lichtenberg figures
J. Phys. D: Appl. Phys. 32 (1999) 219–226. Printed in the UK PII: S0022-3727(99)96851-1 Electrostatic discharges and multifractal analysis of their Lichtenberg figures T Ficker Department of Physics, Technical University, Ziˇ zkovaˇ 17, CZ-602 00 Brno, Czech Republic Received 17 August 1998, in final form 30 September 1998 Abstract. Morphological features of Lichtenberg figures created by electrostatic separation discharges on the surfaces of electret samples have been studied by means of multifractal analysis. The monofractal ramification of surface positive-channel streamers has been confirmed and found to be dependent on actual experimental conditions. For the lower level of electret saturation used, the fractal dimension D 1.4 of the surface Lichtenberg channels has been obtained. Various registration features of electret≈ and non-electret samples have been discussed and illustrated. 1. Introduction The majority of the studies dealing with Lichtenberg figures has used point-to-plane electrode systems and short Typical electrostatic discharges arise during separation of a voltage pulses in the microsecond and nanosecond regimes. charged sheet of a highly resistive material from a grounded The consequence of such special experimental arrangements object. Such electrostatic discharges are sometimes called is the characteristic form of the corresponding Lichtenberg ‘separation discharges’. Their damaging effects on some figures: a single circular star-shaped channel structure for a industrial products are well known: they degrade tracks on positive pulse (positive streamers) and a single circular spot paper and photographic materials, induce noise in electronic built up in a practically continuous manner for a negative components or cause inconvenience for the human body, pulse (negative streamers). -
Injuries and Deaths from Lightning J Clin Pathol: First Published As 10.1136/Jclinpath-2020-206492 on 12 August 2020
Review Injuries and deaths from lightning J Clin Pathol: first published as 10.1136/jclinpath-2020-206492 on 12 August 2020. Downloaded from Ryan Blumenthal Department of Forensic ABSTRACT above zero at the base of the cloud to aboutminus Medicine, University of Pretoria, This paper reviews recent academic research into 50°C at its top. Violent up and down draughts and Pretoria, Gauteng, South Africa the pathology of trauma of lightning. Lightning may severe turbulence occur in specific regions of the injure or kill in a variety of different ways. Aimed at the cloud.8 Correspondence to Professor Ryan Blumenthal, trainee, or practicing pathologist, this paper provides a According to Malan (1967), an electrically active Department of Forensic clinicopathological approach. thundercloud may be regarded as an electrostatic Medicine, University of Pretoria, generator suspended in an atmosphere of low Private Bag X323, Gezina, 0031, electrical conductivity. It is situated between two South Africa; ryan. blumenthal@ As Ponocrates grew familiar with Gargantua’s vi- up. ac. za cious manner of studying, he began to plan a differ- concentric conductors, namely, the surface of the ent course of education for the lad; but at first he let earth and the electrosphere, the latter being the Received 27 March 2020 him go on as before knowing that nature does not highly conducting layers of the atmosphere at alti- Revised 30 June 2020 9 endure abrupt changes without great violence. tudes above 50–60 km. Accepted 3 July 2020 Published Online First Rabelais, “The Old Education and the New”, Gar- There are different types of lightning discharges: 12 August 2020 gantua, Book 1. -
Simple, Compact Source for Low-Temperature Air Plasmas
University of South Carolina Scholar Commons Faculty Publications Biological Sciences, Department of 7-25-2002 Simple, Compact Source for Low-Temperature Air Plasmas D. P. Sheehan University of San Diego J. Lawson University of San Diego M. Sosa University of San Diego Richard A. Long University of South Carolina - Columbia, [email protected] Follow this and additional works at: https://scholarcommons.sc.edu/biol_facpub Part of the Biology Commons Publication Info Review of Scientific Instruments, Volume 73, Issue 8, 2002, pages 3128-3130. © Review of Scientific Instruments 2002, The American Institute of Physics. This Article is brought to you by the Biological Sciences, Department of at Scholar Commons. It has been accepted for inclusion in Faculty Publications by an authorized administrator of Scholar Commons. For more information, please contact [email protected]. REVIEW OF SCIENTIFIC INSTRUMENTS VOLUME 73, NUMBER 8 AUGUST 2002 Simple, compact source for low-temperature air plasmas D. P. Sheehan,a) J. Lawson, and M. Sosa Physics Department, University of San Diego, San Diego, California 92110 R. A. Long Scripps Institute of Oceanography, UCSD, La Jolla, California ͑Received 14 August 2001; accepted for publication 8 May 2002͒ A simple, compact source of low-temperature, spatially and temporally uniform air plasma using a Telsa induction coil driver is described. The low-power ionization discharge plasma is localized (2 cmϫ0.5 cmϫ0.1 cm) and essentially free of arc channels. A Teflon coated rolling cylindrical electrode and dielectric coated ground plate are essential to the source’s operation and allow flat test samples to be readily exposed to the plasma. -
Feasibility Study on the Use of Fast Camera and Recording in Time-Domain to Characterize ESD
MATEC Web of Conferences 247, 00028 (2018) https://doi.org/10.1051/matecconf/201824700028 FESE 2018 Feasibility study on the use of fast camera and recording in time-domain to characterize ESD Szymon Ptak1,*, Albert Smalcerz1, Piotr Ostrowski1 1Central Institute for Labour Protection – National Research Institute, 16 Czerniakowska St., 00-701 Warsaw, Poland Abstract. Fire and explosion protection in industrial conditions requires multidimensional approach. Usually the risk of hazardous zone creation is unavoidable, if the combustible material is processed. Therefore controlling of potential ignition sources is introduced. One of most popular sources of ignition is electrostatic discharge. Depending on the type of the discharge, as well as on exact discharge conditions, energy released might reach hundreds or even thousands of mJ, being able to ignite most of gaseous or dust-air hazardous mixtures. A dedicated methodology was created to record the discharge with fast camera with maximum speed of 1M fps and with the oscilloscope up to 25 GS/s. Dedicated test stand allows to obtain high voltage to create the conditions for electrostatic discharge. The aim of presented research was to analyze the course of electrostatic spark discharge in laboratory conditions and to place the outcomes in the context of explosion safety in the industrial conditions. The course of electrostatic discharge is dependent on various conditions: the polarity, distance between the electrodes, shape of electrodes, grounding conditions, etc. Understanding of the phenomenon is crucial from the point of view of explosion safety. 1 Introduction In every industrial process the safety of people, equipment and environment must be ensured. Despite the safety of the process itself, the risk of fire and/or explosion should be always taken into consideration. -
What Are Lichtenberg Figures and How Are They Created? Copyright 2010, Bert Hickman
What are Lichtenberg Figures and how are they created? Copyright 2010, Bert Hickman Lichtenberg Figures are branching, tree-like patterns that are sometimes formed on the surface or inside insulating materials by high voltage electrical discharges. The first Lichtenberg Figures were two-dimensional patterns formed in dust on charged insulating plates by the German physicist who discovered them, Georg Christoph Lichtenberg (1742-1799). The principles involved in the formation of these early figures are also fundamental to the operation of modern copy machines and laser printers. Using modern materials and powerful particle accelerators, beautiful 3-D Lichtenberg Figures can now be created inside clear acrylic, creating lightning sculptures. We use acrylic (Polymethyl Methacrylate or PMMA) to make our Lichtenberg Figures, since it has an ideal combination of optical, electrical, and mechanical properties. We also use a linear accelerator (LINAC) to create a beam of high-speed electrons. Electrons in the beam are accelerated to as much as 99.5% of the speed of light. These “relativistic” electrons have a very large amount of kinetic energy, measured in millions of electron Volts (MeV). Polished acrylic specimens are placed in the path of the beam. As the high speed electrons hit the acrylic surface, they don’t stop immediately. Instead, they collide with acrylic molecules, rapidly slowing down, eventually coming to rest deep inside the acrylic. As we continue to irradiate the specimens, huge numbers of electrons accumulate inside, forming an invisible cloud-like layer of excess negative charge. Since acrylic is an excellent electrical insulator, the excess electrons are trapped within the charge layer. -
Bibliography
Bibliography F.H. Attix, Introduction to Radiological Physics and Radiation Dosimetry (John Wiley & Sons, New York, New York, USA, 1986) V. Balashov, Interaction of Particles and Radiation with Matter (Springer, Berlin, Heidelberg, New York, 1997) British Journal of Radiology, Suppl. 25: Central Axis Depth Dose Data for Use in Radiotherapy (British Institute of Radiology, London, UK, 1996) J.R. Cameron, J.G. Skofronick, R.M. Grant, The Physics of the Body, 2nd edn. (Medical Physics Publishing, Madison, WI, 1999) S.R. Cherry, J.A. Sorenson, M.E. Phelps, Physics in Nuclear Medicine, 3rd edn. (Saunders, Philadelphia, PA, USA, 2003) W.H. Cropper, Great Physicists: The Life and Times of Leading Physicists from Galileo to Hawking (Oxford University Press, Oxford, UK, 2001) R. Eisberg, R. Resnick, Quantum Physics of Atoms, Molecules, Solids, Nuclei and Particles (John Wiley & Sons, New York, NY, USA, 1985) R.D. Evans, TheAtomicNucleus(Krieger, Malabar, FL USA, 1955) H. Goldstein, C.P. Poole, J.L. Safco, Classical Mechanics, 3rd edn. (Addison Wesley, Boston, MA, USA, 2001) D. Greene, P.C. Williams, Linear Accelerators for Radiation Therapy, 2nd Edition (Institute of Physics Publishing, Bristol, UK, 1997) J. Hale, The Fundamentals of Radiological Science (Thomas Springfield, IL, USA, 1974) W. Heitler, The Quantum Theory of Radiation, 3rd edn. (Dover Publications, New York, 1984) W. Hendee, G.S. Ibbott, Radiation Therapy Physics (Mosby, St. Louis, MO, USA, 1996) W.R. Hendee, E.R. Ritenour, Medical Imaging Physics, 4 edn. (John Wiley & Sons, New York, NY, USA, 2002) International Commission on Radiation Units and Measurements (ICRU), Electron Beams with Energies Between 1 and 50 MeV,ICRUReport35(ICRU,Bethesda, MD, USA, 1984) International Commission on Radiation Units and Measurements (ICRU), Stopping Powers for Electrons and Positrons, ICRU Report 37 (ICRU, Bethesda, MD, USA, 1984) 646 Bibliography J.D. -
Explosive Safety with Regards to Electrostatic Discharge Francis Martinez
University of New Mexico UNM Digital Repository Electrical and Computer Engineering ETDs Engineering ETDs 7-12-2014 Explosive Safety with Regards to Electrostatic Discharge Francis Martinez Follow this and additional works at: https://digitalrepository.unm.edu/ece_etds Recommended Citation Martinez, Francis. "Explosive Safety with Regards to Electrostatic Discharge." (2014). https://digitalrepository.unm.edu/ece_etds/ 172 This Thesis is brought to you for free and open access by the Engineering ETDs at UNM Digital Repository. It has been accepted for inclusion in Electrical and Computer Engineering ETDs by an authorized administrator of UNM Digital Repository. For more information, please contact [email protected]. Francis J. Martinez Candidate Electrical and Computer Engineering Department This thesis is approved, and it is acceptable in quality and form for publication: Approved by the Thesis Committee: Dr. Christos Christodoulou , Chairperson Dr. Mark Gilmore Dr. Youssef Tawk i EXPLOSIVE SAFETY WITH REGARDS TO ELECTROSTATIC DISCHARGE by FRANCIS J. MARTINEZ B.S. ELECTRICAL ENGINEERING NEW MEXICO INSTITUTE OF MINING AND TECHNOLOGY 2001 THESIS Submitted in Partial Fulfillment of the Requirements for the Degree of Master of Science In Electrical Engineering The University of New Mexico Albuquerque, New Mexico May 2014 ii Dedication To my beautiful and amazing wife, Alicia, and our perfect daughter, Isabella Alessandra and to our unborn child who we are excited to meet and the one that we never got to meet. This was done out of love for all of you. iii Acknowledgements Approximately 6 years ago, I met Dr. Christos Christodoulou on a collaborative project we were working on. He invited me to explore getting my Master’s in EE and he told me to call him whenever I decided to do it. -
Copies in Seconds by David Owen
From Copies in Seconds by David Owen. Copyright © 2004 by David Owen. Reprinted by permission of Simon & Schuster, Inc., New York. Copies in Seconds by David Owen When Chester Carlson, working in the patent office at P. R. Mallory, needed a copy of a drawing in a patent application, his only option was to have a photographic copy made by an outside company that owned a Photostat or Rectigraph machine. “Their representative would come in, pick up the drawing, take it to their plant, make a copy, bring it back,” he recalled later. “It might be a wait of half a day or even twenty-four hours to get it back.” This was a costly nuisance, and it meant that what we now think of as a mindless clerical task was then an ongoing corporate operation involving outside vendors, billing, record keeping, and executive supervision. “So I recognized a very great need for a machine that could be right in an office,” he con- tinued, “where you could bring a document to it, push it in a slot, push a button, and get a copy out.” As Carlson began to consider how such a machine might work, he naturally thought first of photography. But he realized quickly that photog- raphy had distressingly many inherent limitations. Reducing the size of a bulky Photostat machine might be possible, but a smaller machine would still require coated papers and messy chemi- cals—the two main reasons making Photostats was expensive and inconvenient. Photography, furthermore, was already so well understood that it was unlikely to yield an important discovery to a lone inventor like Carlson. -
STRIKE Notes
STRIKE notes The Superior Vividness of Lightning in America This is not a photograph of lightning striking the Empire National Lightning Protection 1. In this marble sculpture of Benjamin Franklin by Hiram State Building. On July 7, 1931, bolts of lightning from an 12. Collected lightning rod sales materials and ephemera. Powers (1862), the figure is supported by a tree trunk imaginary cloud were hurled at a miniature model of the Photos: that has been visibly struck by lightning. New York City skyline. Engineers experimented with • Men examining aluminum cap of Washington 2. Franklin seized the lightning from heaven and the scepter 5,000,000 volt artificial lightning, concluding that the Monument, and Aluminum cap of Washington from tyrants. Anne-Robert-Jacques Turgot, 1778 Empire State Building would act as a lightning rod for Monument with lightning rods IV, Theodor The lightning rod was invented by Founding Father, the surrounding area. This is a photograph of the Horydczak, ca. 1920-1950 (Library of Congress Benjamin Franklin. He regularly advocated for its use in laboratory tests being conducted. No damage was done Prints and Photographs Division) his Poor Richard’s Almanac. to the model. (AP Photo) • Photograph of First M.E. Church: Scene shortly after 3. America became a leader in early electrical innovation, a severe hail and snow storm on May 5, 1906. The some attributed this to the unique quality of the air; I Sing the Body Electric steeple, 176 ft. high, was struck by lightning and a American atmosphere was thought to be more electric. 8. The thin red jellies within you or within me, the bones and little later much of the burning portion fell into the Highlighted pages from A View of the Soil and Climate of the marrow in the bones. -
Analysis of Streamer Propagation in Atmospheric Air Manfred Heiszler Iowa State University
Iowa State University Capstones, Theses and Retrospective Theses and Dissertations Dissertations 1971 Analysis of streamer propagation in atmospheric air Manfred Heiszler Iowa State University Follow this and additional works at: https://lib.dr.iastate.edu/rtd Part of the Electrical and Electronics Commons Recommended Citation Heiszler, Manfred, "Analysis of streamer propagation in atmospheric air " (1971). Retrospective Theses and Dissertations. 4459. https://lib.dr.iastate.edu/rtd/4459 This Dissertation is brought to you for free and open access by the Iowa State University Capstones, Theses and Dissertations at Iowa State University Digital Repository. It has been accepted for inclusion in Retrospective Theses and Dissertations by an authorized administrator of Iowa State University Digital Repository. For more information, please contact [email protected]. 72-5207 HEISZLER, Manfred, 1941- ANALYSIS OF STREAMER PROPAGATION IN ATMOSPHERIC AIR. Iowa State University, Ph.D., 1971 Engineering, electrical t University Microfilms. A XERDK Company, Ann Arbor, Michigan THIS DISSERTATION HAS BEEN MICROFILMED EXACTLY AS RECEIVED Analysis of streamer propagation in atmospheric air by Manfred Heiszler A Dissertation Submitted to the Graduate Faculty in Partial Fulfillment of The Requirements for the Degree of DOCTOR OF PHILOSOPHY Major Subject: Electrical Engineering Approved: Signature was redacted for privacy. In Charge of Major Work Signature was redacted for privacy. For the Major Department Signature was redacted for privacy. For the Graduate College Iowa State University Of Science and Technology Ames, lawa 1971 ii TABLE OF CCOTENTS Page I. INTRODUCTION 1 II. REVIEW OF LITERATURE 4 A. The General Streamer Model 4 B. The Critical Avalanche 6 C. The Burst Pulse and Streamer Onset 9 D.