ENGINEERING Indian Journal of Engineering, Volume 9, Number 20, March 5, 2014
Total Page:16
File Type:pdf, Size:1020Kb
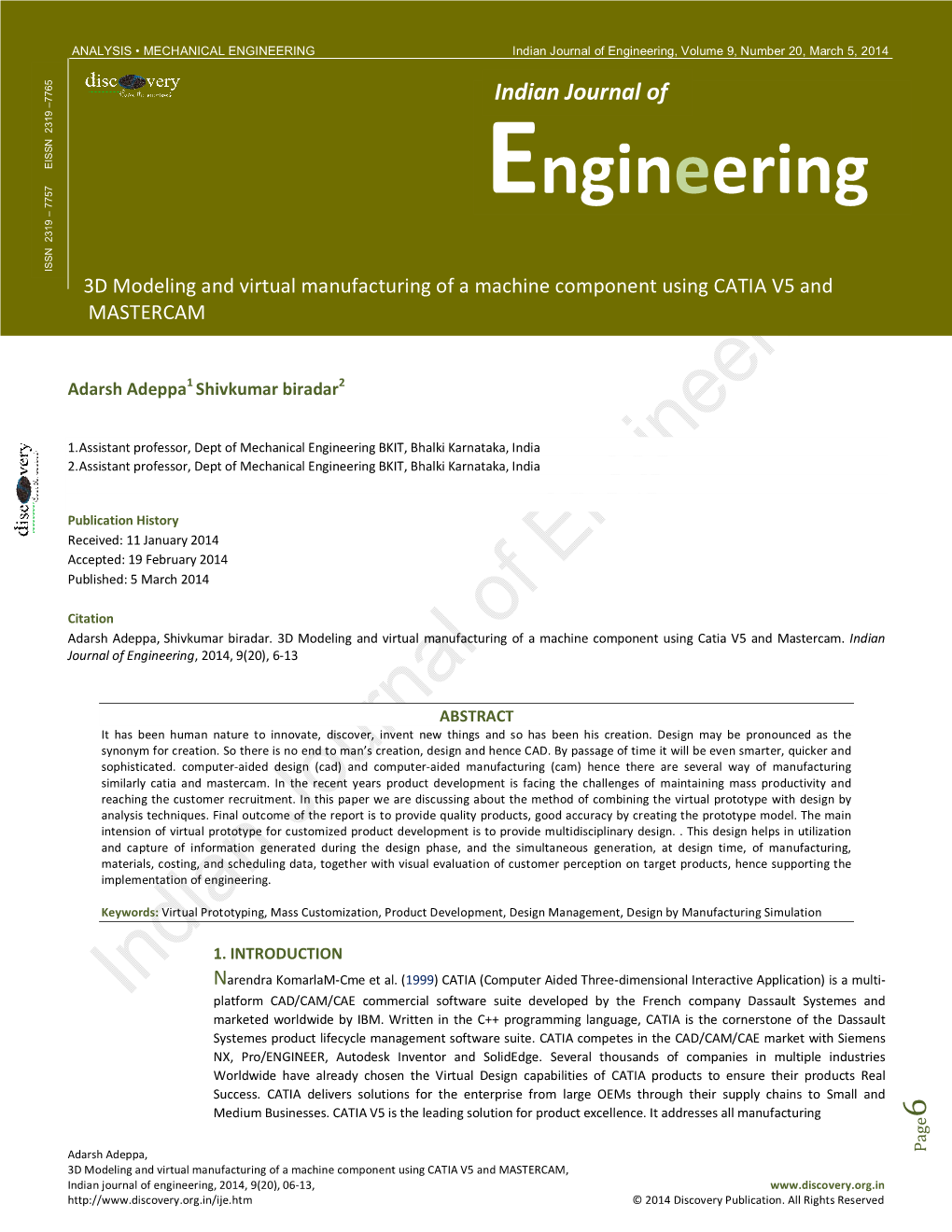
Load more
Recommended publications
-
Getting Started SURFCAM
Get Started with SURFCAM Copyright © 2010 Surfware, Inc. All rights reserved. Information is subject to change without notice. No part of this manual may be reproduced, transmitted, translated in any form or by any means, graphic, electronic, or mechanical, including photocopying, recording, taping, or by any information storage or retrieval system, without written permission from Surfware, Inc. The software described in this document may only be used or copied in accordance with the terms of the furnished license agreement and/or non-disclosure agreement. It is illegal to copy the software onto any medium except as specified in the license or non-disclosure agreement. All Surfware, Inc. software products contain integrated security programs and/or plug-in modules that are required for the software license to properly operate. It is a violation of the Surfware, Inc. copyrights and U.S. Copyright law to disable or attempt to disable or remove or otherwise operate the software without the security programs and/or modules installed. Any software not supplied by Surfware, Inc. which is intended to allow the operation of the software without the required plug-in security module and/or integrated security programs is a copyright violation. SURFCAM is a registered trademark of Surfware Inc. All brand or product names or proprietary file types mentioned in this document are trademarks or registered trademarks of their respective holders. Contact the appropriate companies for more information regarding trademarks and registration. Surfware, Inc. 100 Camino Ruiz Camarillo, California 93012 USA Phone (818) 991-1960 Fax (818) 991-1980 www.surfware.com Printed in the United States of America Contents Introduction to SURFCAM ............................................................................................1 System Requirements ................................................................................................. -
Software Tools for Cad/Cam
Software and Hardware Tools for CAD/CAM SOFTWARE TOOLS FOR CAD/CAM There is lot of companies providing software’s for CAD/CAM/CAE solutions worldwide. Each software having its own importance and specialization. Some details of the widely used software’s is as below. CATIA (CAD/CAM/CAE): CATIA (Computer Aided Three-dimensional Interactive Application) is a multi-platform CAD/CAM/CAE commercial software suite developed by the French company Dassault’s Systems. The software was created in the late 1970s and early 1980s to develop Dassault's Mirage fighter jet, and then was adopted in the aerospace, automotive, shipbuilding, and other industries. Hardware Requirements: Windows Certified Workstations: Windows XP 32-bit Windows XP 64-bit Windows vista 64-bit Windows 7 64-bit 1 Software and Hardware Tools for CAD/CAM Processor manufacturer: Intel Dual Core i3 2120, chipset Intel 6 Series C206 Processor clock speed: up to 3.30 GHz Multi proc. enabled: Yes Max number of proc: 2 Dual Core Standard/Max RAM on Motherboard: 4096 MB/16.192 MB Memory model: DDR3 ECC Graphic manufacturer: NVIDIA Graphic model: Quadro Q2000 Maximum resolution: 2560x1600 @ 60 Hz for Dual link (SLI frame rendering mode). 3840xx2400 @ 24Hz for dual dual-link (single GPU) Image planes: 32 bit Texture memory: 1 GB (DB) Z buffer depth: 24 bit Driver: 270.98 External Bus type: PCI Hard Drive Controller Manufacturer and Model: Various Pro/ENGINEER (CAD/CAM/CAE): Pro/ENGINEER is a parametric, integrated 3D CAD/CAM/CAE solution created by Parametric Technology Corporation (PTC). It was the first to market with parametric, feature- based, associative solid modeling software on the market. -
2020 Cnccookbook CAM Survey Results
2020 CNCCookbook CAM Survey Results Bob Warfield Copyright 2020 by CNCCookbook, Inc. Every year, CNCCookbook surveys readers on their CAM Software. The results provide an invaluable guide to CAM for the CNC World.. Overview very year CNCCookbook surveys readers on their CAM Software. The results are a unique and Einvaluable guide to CAM for the CNC World. This year we received over 400 responses. That’s up from our last survey, which got about 300 responses. Product Managers at a variety of CADCAM companies, large and small, tell me they find the results very valuable in their own planning. There’s really no other source of information quite like these surveys, so I wanted to get these initial results out as soon as I could. We’ve done these CAM surveys in 2010, 2012, 2014, 2015, 2016, 2017, 2018 and now 2020, so there is historical data to compare against when looking for trends. Note that the 2020 results are actually 2019, we just felt it would look funny to publish 2019 in 2020, especially given we conducted the survey at the beginning of 2020. As in the past, we divide the market into 3 segments: High-End: More expensive packages with more functionality. Tiered: Modular packages available in a range of configurations that span from the Low-End to the High-End. Low-End: These are inexpensive packages often used by Hobbyists, but as we’ll see, at least one package has come up-market to the Professional World. Let’s start by taking a look by category at market share. -
Computer-Aided Manufacturing
Computer-aided manufacturing 1 Overview See also: Printed circuit board § PCB CAM Traditionally, CAM has been considered as a Chrome-cobalt disc with crowns for dental implants, manufac- tured using WorkNC CAM numerical control (NC) programming tool, where in two-dimensional (2-D) or three-dimensional (3-D) models of components generated in CADAs with CAD model and CNC machined part other “Computer-Aided” technologies, CAM does not eliminate the need for skilled professionals such as manufacturing engineers, NC programmers, or machinists. CAM, in fact, leverages both the value of the most skilled manufacturing professionals through advanced productivity tools, while building the skills of Computer-aided manufacturing (CAM) is the use of new professionals through visualization, simulation and software to control machine tools and related ones in the optimization tools. manufacturing of workpieces.[1][2][3][4][5] This is not the only definition for CAM, but it is the most common;[1] CAM may also refer to the use of a computer to as- 2 History sist in all operations of a manufacturing plant, including planning, management, transportation and storage.[6][7] Its primary purpose is to create a faster production pro- Early commercial applications of CAM was in large com- cess and components and tooling with more precise di- panies in the automotive and aerospace industries, for ex- mensions and material consistency, which in some cases, ample Pierre Béziers work developing the CAD/CAM application UNISURF in the 1960s for car body design uses only the required amount of raw material (thus [8] minimizing waste), while simultaneously reducing en- and tooling at Renault.