1.4 Natural Gas Combustion
Total Page:16
File Type:pdf, Size:1020Kb
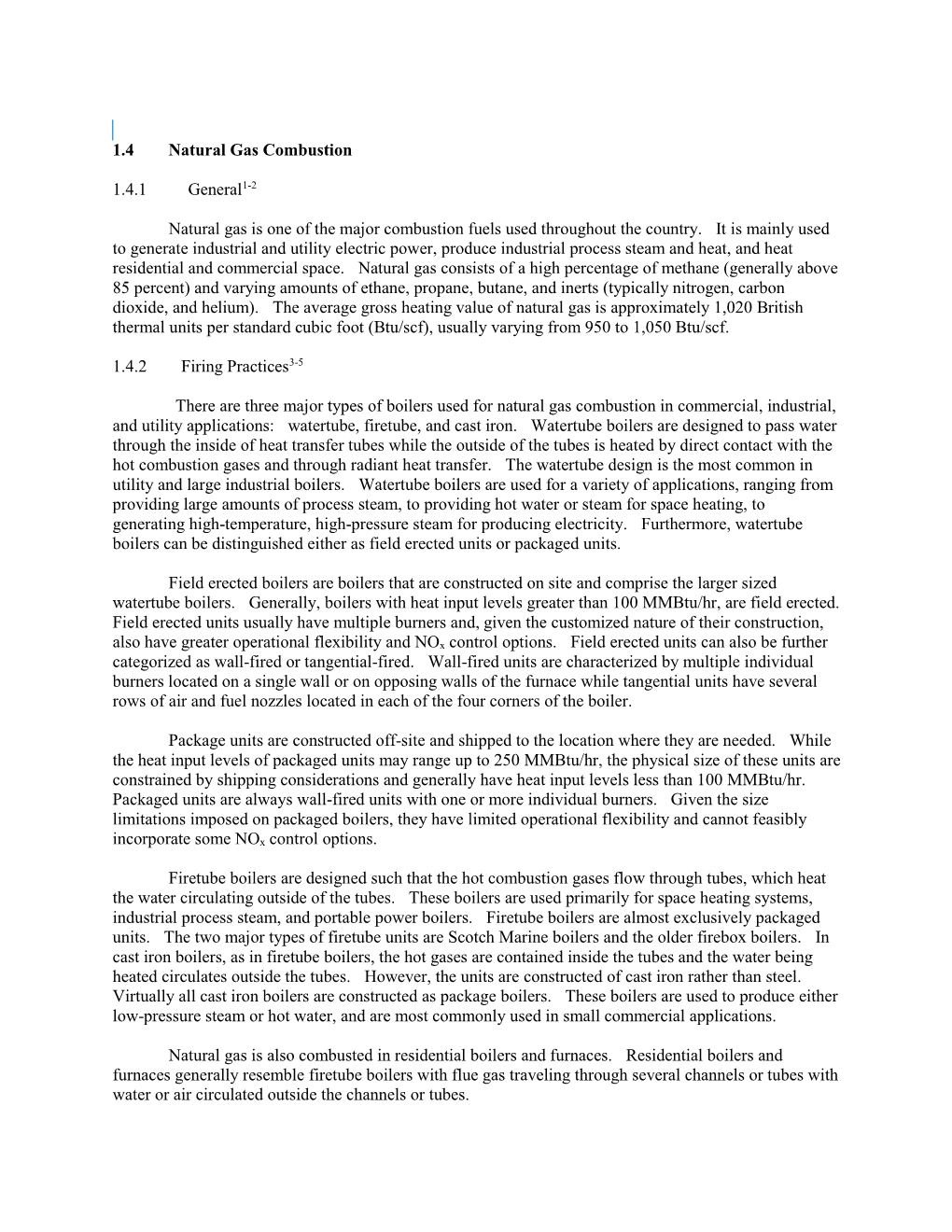
Load more
Recommended publications
-
U.S. Energy in the 21St Century: a Primer
U.S. Energy in the 21st Century: A Primer March 16, 2021 Congressional Research Service https://crsreports.congress.gov R46723 SUMMARY R46723 U.S. Energy in the 21st Century: A Primer March 16, 2021 Since the start of the 21st century, the U.S. energy system has changed tremendously. Technological advances in energy production have driven changes in energy consumption, and Melissa N. Diaz, the United States has moved from being a net importer of most forms of energy to a declining Coordinator importer—and a net exporter in 2019. The United States remains the second largest producer and Analyst in Energy Policy consumer of energy in the world, behind China. Overall energy consumption in the United States has held relatively steady since 2000, while the mix of energy sources has changed. Between 2000 and 2019, consumption of natural gas and renewable energy increased, while oil and nuclear power were relatively flat and coal decreased. In the same period, production of oil, natural gas, and renewables increased, while nuclear power was relatively flat and coal decreased. Overall energy production increased by 42% over the same period. Increases in the production of oil and natural gas are due in part to technological improvements in hydraulic fracturing and horizontal drilling that have facilitated access to resources in unconventional formations (e.g., shale). U.S. oil production (including natural gas liquids and crude oil) and natural gas production hit record highs in 2019. The United States is the largest producer of natural gas, a net exporter, and the largest consumer. Oil, natural gas, and other liquid fuels depend on a network of over three million miles of pipeline infrastructure. -
Heat Generation Technology Landscaping Study, Scotland's
Heat Generation Technology Landscaping Study, Scotland’s Energy Efficiency Programme (SEEP) BRE August 2017 Summary This landscaping study has reviewed the status and suitability of a number of near-term heat generation technologies that are not already significantly established in the market-place. The study has been conducted to inform Scottish Government on the status and the technologies so that they can make informed decisions on the potential suitability of the technologies for inclusion within Scotland’s Energy Efficiency Programme (SEEP). Some key findings which have emerged from the research include: • High temperature, hybrid and gas driven heat pumps all have the potential to increase the uptake of low carbon heating solutions in the UK in the short to medium term. • High temperature heat pumps are particularly suited for off-gas grid retrofit projects, whereas hybrids and gas driven products are suited to on-gas grid properties. They may all be used with no or limited upgrades to existing heating systems, and each offers some advantages (but also some disadvantages) compared with standard electric heat pumps. • District heating may continue to have a significant role to play – albeit more on 3rd and 4th generation systems than the large high temperature systems typical in other parts of Europe in the 1950s and 60s – due to lower heating requirements of modern retrofitted buildings. • Longer term, the development of low carbon heating fuel markets may also present significant opportunity e.g. biogas, and possibly hydrogen. -
5Th-Generation Thermox WDG Flue Gas Combustion Analyzer
CONTROL EXCLUSIVE 5th-Generation Thermox WDG Flue Gas Combustion Analyzer “For more than 40 years, we have been a leader in combustion gas analysis,” says Mike Fuller, divison VP of sales and marketing and business development for Ametek Process Instruments, “and we believe the WDG-V is the combustion analyzer of the future.” WDG analyzers are based on a zirconium oxide cell that provides a reliable and cost-effective solution for measuring excess oxygen in flue gas as well as CO and methane levels. This information allows operators to obtain the highest fuel effi- ciency, while lowering emissions for NOx, CO and CO2. The zir- conium oxide cell responds to the difference between the concen- tration of oxygen in the flue gas versus an air reference. To assure complete combustion, the flue gas should contain several percent oxygen. The optimum excess oxygen concentration is dependent on the fuel type (natural gas, hydrocarbon liquids and coal). The WDG-V mounts directly to the process flange, and is heated to maintain all sample-wetted components above the acid dewpoint. Its air-operated aspirator draws a sample into the ana- lyzer and returns it to the process. A portion of the sample rises into the convection loop past the combustibles and oxygen cells, Ametek’s WDG-V flue gas combustion analyzer meets SIL-2 and then back into the process. standards for safety instrumented systems. This design gives a very fast response and is perfect for process heat- ers. It features a reduced-drift, hot-wire catalytic detector that is resis- analyzer with analog/HART, discrete and Modbus RS-485 bi-direc- tant to sulfur dioxide (SO ) degradation, and the instrument is suitable 2 tional communications, or supplied in a typical “sensor/controller” for process streams up to 3200 ºF (1760 ºC). -
VISCOSITY of a GAS -Dr S P Singh Department of Chemistry, a N College, Patna
Lecture Note on VISCOSITY OF A GAS -Dr S P Singh Department of Chemistry, A N College, Patna A sketchy summary of the main points Viscosity of gases, relation between mean free path and coefficient of viscosity, temperature and pressure dependence of viscosity, calculation of collision diameter from the coefficient of viscosity Viscosity is the property of a fluid which implies resistance to flow. Viscosity arises from jump of molecules from one layer to another in case of a gas. There is a transfer of momentum of molecules from faster layer to slower layer or vice-versa. Let us consider a gas having laminar flow over a horizontal surface OX with a velocity smaller than the thermal velocity of the molecule. The velocity of the gaseous layer in contact with the surface is zero which goes on increasing upon increasing the distance from OX towards OY (the direction perpendicular to OX) at a uniform rate . Suppose a layer ‘B’ of the gas is at a certain distance from the fixed surface OX having velocity ‘v’. Two layers ‘A’ and ‘C’ above and below are taken into consideration at a distance ‘l’ (mean free path of the gaseous molecules) so that the molecules moving vertically up and down can’t collide while moving between the two layers. Thus, the velocity of a gas in the layer ‘A’ ---------- (i) = + Likely, the velocity of the gas in the layer ‘C’ ---------- (ii) The gaseous molecules are moving in all directions due= to −thermal velocity; therefore, it may be supposed that of the gaseous molecules are moving along the three Cartesian coordinates each. -
Viscosity of Gases References
VISCOSITY OF GASES Marcia L. Huber and Allan H. Harvey The following table gives the viscosity of some common gases generally less than 2% . Uncertainties for the viscosities of gases in as a function of temperature . Unless otherwise noted, the viscosity this table are generally less than 3%; uncertainty information on values refer to a pressure of 100 kPa (1 bar) . The notation P = 0 specific fluids can be found in the references . Viscosity is given in indicates that the low-pressure limiting value is given . The dif- units of μPa s; note that 1 μPa s = 10–5 poise . Substances are listed ference between the viscosity at 100 kPa and the limiting value is in the modified Hill order (see Introduction) . Viscosity in μPa s 100 K 200 K 300 K 400 K 500 K 600 K Ref. Air 7 .1 13 .3 18 .5 23 .1 27 .1 30 .8 1 Ar Argon (P = 0) 8 .1 15 .9 22 .7 28 .6 33 .9 38 .8 2, 3*, 4* BF3 Boron trifluoride 12 .3 17 .1 21 .7 26 .1 30 .2 5 ClH Hydrogen chloride 14 .6 19 .7 24 .3 5 F6S Sulfur hexafluoride (P = 0) 15 .3 19 .7 23 .8 27 .6 6 H2 Normal hydrogen (P = 0) 4 .1 6 .8 8 .9 10 .9 12 .8 14 .5 3*, 7 D2 Deuterium (P = 0) 5 .9 9 .6 12 .6 15 .4 17 .9 20 .3 8 H2O Water (P = 0) 9 .8 13 .4 17 .3 21 .4 9 D2O Deuterium oxide (P = 0) 10 .2 13 .7 17 .8 22 .0 10 H2S Hydrogen sulfide 12 .5 16 .9 21 .2 25 .4 11 H3N Ammonia 10 .2 14 .0 17 .9 21 .7 12 He Helium (P = 0) 9 .6 15 .1 19 .9 24 .3 28 .3 32 .2 13 Kr Krypton (P = 0) 17 .4 25 .5 32 .9 39 .6 45 .8 14 NO Nitric oxide 13 .8 19 .2 23 .8 28 .0 31 .9 5 N2 Nitrogen 7 .0 12 .9 17 .9 22 .2 26 .1 29 .6 1, 15* N2O Nitrous -
Humidity in Gas-Fired Kilns Proportion of Excess Combustion
HUMIDITY OF COMBUSTION PRODUCTS FROM WOOD AND GASEOUS FUELS George Bramhall Western Forest Products Laboratory Vancouver, British Columbia The capital and operating costs of steam kilns and the boilers necessary for their operation are so high-in Canada that they are not economically feasible for small operations drying softwoods. About thirty years ago, direct fired or hot-air kilns were intro- duced. In such kilns natural gas, propane, butane or oil is burned and the combustion products conducted directly into the drying chamber. This design eliminates the high capital and operating costs of the steam boiler, and permits the small operator to dry lumber economically. However, such kilns are not as versatile as steam kilns. While they permit good temperature control, their humidity control is limited: they can only reduce excess humidity by venting, they cannot increase it and therefore cannot relieve drying stresses at the end of drying. For this reason, they are usually limited to the drying of structural lumber. Due to the decreasing supplies and increasing costs of fossil fuels, there is growing interest in burning wood residues to pro- vide the heat for drying. Although wood residue was often the fuel for steam boilers, the capital and operating costs of boilers are no more acceptable now to the smaller operator than they were a few years ago. The present trend is rather to burn wood cleanly and conduct the combustion products into the kiln in the same man- ner as is done with gaseous fossil fuels. This is now being done successfully with at least one type of burner, and others are in the pilot stage. -
Air Separation, Flue Gas Compression and Purification Units for Oxy-Coal Combustion Systems
View metadata, citation and similar papers at core.ac.uk brought to you by CORE provided by Elsevier - Publisher Connector Energy Energy Procedia 4 (2011) 966–971 www.elsevier.com/locate/procediaProcedia Energy Procedia 00 (2010) 000–000 www.elsevier.com/locate/XXX GHGT-10 Air Separation, flue gas compression and purification units for oxy-coal combustion systems Jean-Pierre Traniera, Richard Dubettierb, Arthur Dardeb, Nicolas Perrinc aAir Liquide SA-Centre de Recherche Claude Delorme,Chemin de la porte des Loges, Les Loges en Josas, Jouy en Josas F-78354, France bAir Liquide Engineering, 57 Ave. Carnot BP 313,Champigny-sur-Marne F-94503, France cAir Liquide SA, 57 Ave. Carnot BP 313, Champigny-sur-Marne F-94503, France Elsevier use only: Received date here; revised date here; accepted date here Abstract Air Liquide (AL) has been actively involved in the development of oxy-coal technologies for CO2 capture from power plants for almost 10 years. Large systems for oxygen production and flue gas purification are required for this technology. Air Liquide has been a leader in building large Air Separation Units (ASUs) and more developments have been performed to customize the air separation process for coal-fired power plants. Air Liquide is also actively involved in developing processes for purification of flue gas from oxy-coal combustion systems for enhanced oil recovery applications as well as sequestration in saline aquifers. Through optimization of the overall oxy-coal combustion system, it has been possible to identify key advantages of this solution: minimal efficiency loss associated with CO2 capture (less than 6 pts penalty on HHV efficiency compared to no capture), near zero emission, energy storage, high CO2 purity and high CO2 recovery capability. -
Reactions of Benzene & Its Derivatives
Organic Lecture Series ReactionsReactions ofof BenzeneBenzene && ItsIts DerivativesDerivatives Chapter 22 1 Organic Lecture Series Reactions of Benzene The most characteristic reaction of aromatic compounds is substitution at a ring carbon: Halogenation: FeCl3 H + Cl2 Cl + HCl Chlorobenzene Nitration: H2 SO4 HNO+ HNO3 2 + H2 O Nitrobenzene 2 Organic Lecture Series Reactions of Benzene Sulfonation: H 2 SO4 HSO+ SO3 3 H Benzenesulfonic acid Alkylation: AlX3 H + RX R + HX An alkylbenzene Acylation: O O AlX H + RCX 3 CR + HX An acylbenzene 3 Organic Lecture Series Carbon-Carbon Bond Formations: R RCl AlCl3 Arenes Alkylbenzenes 4 Organic Lecture Series Electrophilic Aromatic Substitution • Electrophilic aromatic substitution: a reaction in which a hydrogen atom of an aromatic ring is replaced by an electrophile H E + + + E + H • In this section: – several common types of electrophiles – how each is generated – the mechanism by which each replaces hydrogen 5 Organic Lecture Series EAS: General Mechanism • A general mechanism slow, rate + determining H Step 1: H + E+ E El e ctro - Resonance-stabilized phile cation intermediate + H fast Step 2: E + H+ E • Key question: What is the electrophile and how is it generated? 6 Organic Lecture Series + + 7 Organic Lecture Series Chlorination Step 1: formation of a chloronium ion Cl Cl + + - - Cl Cl+ Fe Cl Cl Cl Fe Cl Cl Fe Cl4 Cl Cl Chlorine Ferric chloride A molecular complex An ion pair (a Lewis (a Lewis with a positive charge containing a base) acid) on ch lorine ch loronium ion Step 2: attack of -
Summary of Gas Cylinder and Permeation Tube Standard Reference Materials Issued by the National Bureau of Standards
A111D3 TTbS?? o z C/J NBS SPECIAL PUBLICATION 260-108 o ^EAU U.S. DEPARTMENT OF COMMERCE/National Bureau of Standards Standard Reference Materials: Summary of Gas Cylinder and Permeation Tube Standard Reference Materials Issued by the National Bureau of Standards QC 100 U57 R. Mavrodineanu and T. E. Gills 260-108 1987 m he National Bureau of Standards' was established by an act of Congress on March 3, 1901. The Bureau's overall goal i s t0 strengthen and advance the nation's science and technology and facilitate their effective application for public benefit. To this end, the Bureau conducts research to assure international competitiveness and leadership of U.S. industry, science arid technology. NBS work involves development and transfer of measurements, standards and related science and technology, in support of continually improving U.S. productivity, product quality and reliability, innovation and underlying science and engineering. The Bureau's technical work is performed by the National Measurement Laboratory, the National Engineering Laboratory, the Institute for Computer Sciences and Technology, and the Institute for Materials Science and Engineering. The National Measurement Laboratory Provides the national system of physical and chemical measurement; • Basic Standards 2 coordinates the system with measurement systems of other nations and • Radiation Research furnishes essential services leading to accurate and uniform physical and • Chemical Physics chemical measurement throughout the Nation's scientific community, • Analytical Chemistry industry, and commerce; provides advisory and research services to other Government agencies; conducts physical and chemical research; develops, produces, and distributes Standard Reference Materials; provides calibration services; and manages the National Standard Reference Data System. -
Natural Gas and Propane
Construction Concerns: Natural Gas and Propane Article by Gregory Havel September 28, 2015 For the purposes of this article, I will discuss the use of natural gas and propane [liquefied propane (LP)] gas in buildings under construction, in buildings undergoing renovation, and in the temporary structures that are found on construction job sites including scaffold enclosures. In permanent structures, natural gas is carried by pipe from the utility company meter to the location of the heating appliances. Natural gas from utility companies is lighter than air and is odorized. In temporary structures and in buildings under construction or renovation, the gas may be carried from the utility company meter by pipe or a hose rated for natural gas at the pressure to be used to the location of the heating appliances. These pipes and hoses must be properly supported and must be protected from damage including from foot and wheeled traffic. The hoses, pipes, and connections must be checked regularly for leaks. For permanent and temporary structures, LP gas is usually stored in horizontal tanks outside the structure (photo 1) at a distance from the structure. September 28, 2015 (1) In Photo 1, note the frost on the bottom third of the tank that indicates the approximate amount of LP that is left in the tank. LP gas for fuel is heavier than air and is odorized. It is carried from the tank to the heating appliances by pipe or hose rated for LP gas at the pressure to be used. As it is for natural gas, these pipes and hoses must be properly supported and protected from damage including from foot and wheeled traffic. -
BENZENE AS a LARVICIDE for SCREW WORMS1 the Larval Stage
BENZENE AS A LARVICIDE FOR SCREW WORMS1 By D. C. PARMAN Assistant Entomologist, Investigations of Insects Affecting the Health of Animals, Bureau of Entomology, United States Department of Agriculture INTRODUCTION The larval stage of CocMiomyia macellaria Fab., generally known amonff stock raisers in the Southwest as the screw worm, causes con- siderable loss to the livestock industry, estimated as high as $5,000,000 in some years. It has been apparent that the larvicides used to kill the worms are either toxic to the animal or at least in most cases detrimental to the healing of the wounds. This toxicity was at first attributed to the screw worm, but as many cases were ob- served where the animal was practically consumed by the larvae and still lived until the loss of olood or injury to some vital organ brought de^th, it was surmised that the treatments with larvicides were the cause of many deaths. During the summer of 1916 syste- matic work was begun to find a more efficient larvicide than the phenols and chloroform which were generally used. At first an attempt was made to add something to these larvicides to counteract the toxic properties. As this was not successful it was deemed best to look for a chemical that might be used with more satis- factory results. Several chemical groups were studied for possible larvicides. EXPERIMENTAL PROCEDURE All available chemicals with possible larvicidal value were selected for laboratory tests to determine whether they would kill the larvae of the screw-worm fly. The first tests were made by pouring the chemical on a number of larvae in a tube, or dusting on just enough to cover the larvae. -
Specific Latent Heat
SPECIFIC LATENT HEAT The specific latent heat of a substance tells us how much energy is required to change 1 kg from a solid to a liquid (specific latent heat of fusion) or from a liquid to a gas (specific latent heat of vaporisation). �����푦 (��) 퐸 ����������푐 ������� ℎ���� �� ������� �� = (��⁄��) = 푓 � ����� (��) �����푦 = ����������푐 ������� ℎ���� �� 퐸 = ��푓 × � ������� × ����� ����� 퐸 � = �� 푦 푓 ����� = ����������푐 ������� ℎ���� �� ������� WORKED EXAMPLE QUESTION 398 J of energy is needed to turn 500 g of liquid nitrogen into at gas at-196°C. Calculate the specific latent heat of vaporisation of nitrogen. ANSWER Step 1: Write down what you know, and E = 99500 J what you want to know. m = 500 g = 0.5 kg L = ? v Step 2: Use the triangle to decide how to 퐸 ��푣 = find the answer - the specific latent heat � of vaporisation. 99500 퐽 퐿 = 0.5 �� = 199 000 ��⁄�� Step 3: Use the figures given to work out 푣 the answer. The specific latent heat of vaporisation of nitrogen in 199 000 J/kg (199 kJ/kg) Questions 1. Calculate the specific latent heat of fusion if: a. 28 000 J is supplied to turn 2 kg of solid oxygen into a liquid at -219°C 14 000 J/kg or 14 kJ/kg b. 183 600 J is supplied to turn 3.4 kg of solid sulphur into a liquid at 115°C 54 000 J/kg or 54 kJ/kg c. 6600 J is supplied to turn 600g of solid mercury into a liquid at -39°C 11 000 J/kg or 11 kJ/kg d.