Kinetics of Hydrogen Generation from Oxidation of Hydrogenated Silicon Nanocrystals in Aqueous Solutions
Total Page:16
File Type:pdf, Size:1020Kb
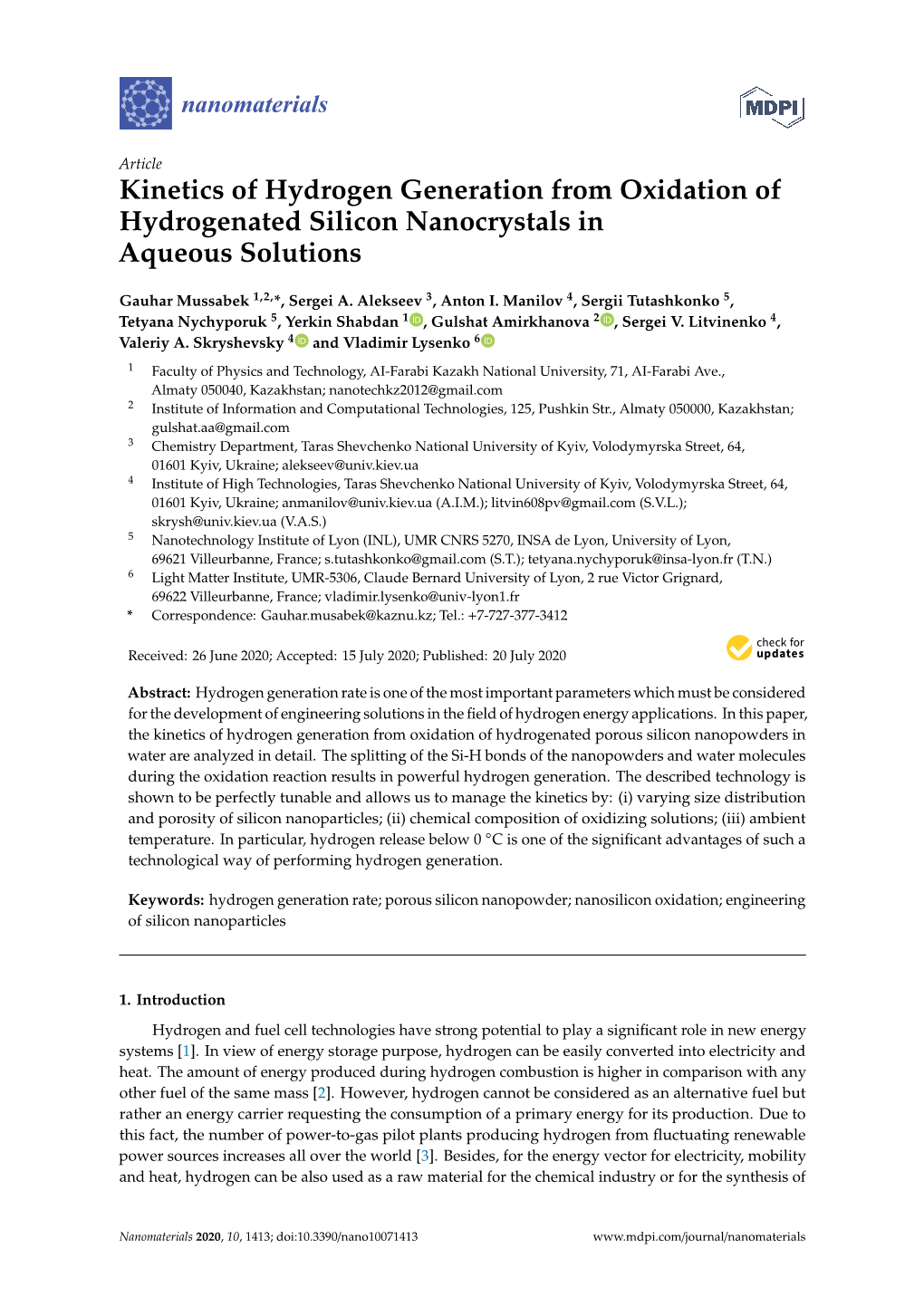
Load more
Recommended publications
-
Invited Lecture: SILICON NITRIDE NANOCOMPOSITES: FABRICATION, LUMINESCENT PROPERTIES and BIO-IMAGING APPLICATIONS V
CONTENTS OF THE IX INTERNATIONAL CONFERENCE "ELECTRONICS AND APPLIED PHYSICS" Invited Lecture: SILICON NITRIDE NANOCOMPOSITES: FABRICATION, LUMINESCENT PROPERTIES AND BIO-IMAGING APPLICATIONS V. Lysenko Nanotechnology Institute of Lyon (INL), UMR-5270, INSA/UCBL, 7, av. J. Capelle, 8 Bat. B. Pascal, 69621 Villeurbanne, France, e-mail: [email protected] 1. Laser Physics and Optoelectronics 1 SUB-NANOSECOND PULSES FROM Q-SWITCHED LASER 11 A.I. Ivanisik National Taras Shevchenko University of Kyiv, Department of Radiophysics Glushkova 4g, Kyiv 03022, e-mail: [email protected] 2 INTEGRATED PHOTONICS BASED ON THE MULTI-FUNCTIONAL 13 IMAGING SOI SENSOR I.S. Lytvyn TANE, 11 Lvivska st., 46004 Ternopil, [email protected] 3 QUASICHARACTERISTIC RADIATION SPECTRA AT PLANAR CHANNELING OF 15 RELATIVISTIC ELECTRONS IN METAL HEXABORIDE CRYSTALS M. V. Maksyuta, S. V. Yefimenko, V. I. Vysotskii Taras Shevchenko National University of Kyiv, 64/13, Volodymyrska Str., City of Kyiv, Ukraine, 01601, Radio Physics Faculty, E-mail: [email protected] 4 ON A SIMILARITY BETWEEN ELEMENTARY PARTICLES AND BLACK HOLES 17 FRОM THE POINT OF VIEW OF TWO CRYSTAL-LIKE PHYSICAL VACUA N. V. Maksyuta Taras Shevchenko National University of Kyiv, 64/13, Volodymyrska Str., City of Kyiv, Ukraine, 01601, Radio Physics Faculty, E-mail: [email protected] 5 OPTICAL IMAGING OF ULTRASONIC PULSES USING FORBIDDEN ACOUSTO- 19 OPTIC INTERACTION Polishko O., Smirnov E., Yurchenko A. Department of Radiophysics, Taras Shevchenko National University of Kyiv, 64 Volodymyrska str., Kyiv, 01601, Ukraine, E-mail: [email protected]. 6 PORTABLE FLUOROMETER FOR FLUORESCENCE ANALYSIS OF 21 AGRONOMIC PLANTS Posudin Yu.I., Godlevska O.O., Zaloilo I.A., Kozhem’yako Ya.V. -
Control of Pore Characteristics of Porous Silicon
South Dakota State University Open PRAIRIE: Open Public Research Access Institutional Repository and Information Exchange Theses and Dissertations 2017 Control of Pore Characteristics of Porous Silicon Using Non-toxic Electrochemical Etching for Photovoltaics and Supercapacitor Applications Utpal Saha South Dakota State University Follow this and additional works at: http://openprairie.sdstate.edu/etd Part of the Materials Science and Engineering Commons, and the Power and Energy Commons Recommended Citation Saha, Utpal, "Control of Pore Characteristics of Porous Silicon Using Non-toxic Electrochemical Etching for Photovoltaics and Supercapacitor Applications" (2017). Theses and Dissertations. 1676. http://openprairie.sdstate.edu/etd/1676 This Thesis - Open Access is brought to you for free and open access by Open PRAIRIE: Open Public Research Access Institutional Repository and Information Exchange. It has been accepted for inclusion in Theses and Dissertations by an authorized administrator of Open PRAIRIE: Open Public Research Access Institutional Repository and Information Exchange. For more information, please contact [email protected]. CONTROL OF PORE CHARACTERISTICS OF POROUS SILICON USING NON- TOXIC ELECTROCHEMICAL ETCHING FOR PHOTOVOLTAICS AND SUPERCAPACITOR APPLICATIONS BY UTPAL SAHA A thesis submitted in partial fulfillment of the requirements for the Master of Science Major in Electrical Engineering South Dakota State University 2017 iii ACKNOWLEDGEMENTS I would like to express my sincere gratitude to my advisor Dr. Qiquan Qiao for giving me an opportunity to work in his group and serve as my thesis adviser at the Department of Electrical Engineering, Center for Advanced Photovoltaics, South Dakota State University. His continuous motivation, support, and criticism during research work until the completion of my thesis was tremendous and above all he had extreme faith on me. -
A Bioactive Metallurgical Grade Porous Silicon- Polytetrafluoroethylene Sheet for Guided Bone Regeneration Applications
A Bioactive Metallurgical Grade Porous Silicon- Polytetrafluoroethylene Sheet for Guided Bone Regeneration Applications E.G. Chadwick 1,2 O.M Clarkin 3 R. Raghavendra 4 and D.A. Tanner 1,2* 1Materials & Surface Science Institute, 2Department of Design & Manufacturing Technology, University of Limerick, Ireland, 3School of Mechanical and Manufacturing Engineering, Dublin City University, Ireland, 4South Eastern Applied Materials Research Centre, Waterford Institute of Technology *E-mail: [email protected], Tel: 00-353-(0)61-234130; Fax: 00-353-(0)61-202913 Keywords: Porous Silicon (PS); Metallurgical Grade Silicon (MGSi); Nanoporous Silicon; Nanosponge; Porous Structure; Scanning Electron Microscopy (SEM), Energy Dispersive X- ray Spectroscopy (EDX); Hydroxyapatite (HA); Abstract: The properties of porous silicon make it a promising material for a host of applications including drug delivery, molecular and cell-based biosensing, and tissue engineering. Porous Silicon has previously shown its potential for the controlled release of pharmacological agents and in assisting bone healing. Hydroxyapatite, the principle constituent of bone, allows osteointegration in vivo, due to its chemical and physical similarities to bone . Synthetic hydroxyapatite is currently applied as a surface coating to medical devices and prosthetics, encouraging bone in-growth at their surface & improving osseointegration. This paper examines the potential for the use of an economically produced porous silicon particulate-polytetrafluoroethylene sheet for use as a guided bone regeneration device in periodontal and orthopaedic applications. The particulate sheet is comprised of a series of microparticles in a polytetrafluoroethylene matrix and is shown to produce a stable hydroxyapatite on its surface under simulated physiological conditions. The microstructure of the material is examined both before and after simulated body fluid experiments for a period of 1, 7, 14 and 30 days using Scanning Electron Microscopy. -
ANNEX XB ENHANCED DRAFT of the MANAGEMENT PLAN Mission Report Joint World Heritage Centre/ICOMOS Reactive Monitoring Mission To
ADDITIONAL MATERIALS RECEIVED DURING THE RMM ANNEX X ANNEX XB ENHANCED DRAFT OF THE MANAGEMENT PLAN CHAPTER 2 Mission Report Joint World Heritage Centre/ICOMOS Reactive Monitoring Mission to the World Heritage property Kyiv: Saint-Sophia Cathedral and Related Monastic Buildings, Kyiv-Pechersk Lavra Kyiv, Ukraine 10 – 14 February 2020 ІІ General description 2.1. Location Area. The World Heritage Property “Kyiv: Saint Sophia Cathedral and Related Monastic Buildings, Kyiv-Pechersk Lavra” is located in the central historical part of Kyiv, on the high right bank of the Dnieper River and upper sections of the plateau of Starokyivsky and Pechersky Hills. The area between the Property’s components composes the historical centre of the city with predominantly residential quarters, public buildings and parks. The distance between two ensembles is about 3.5 km. Location of the Property Geographical coordinates of the Property’s location: St. Sophia and related monastic buildings - North latitude B = 500 27 '10''.28; East longitude L = 300 30 '51''. 58. Kyiv-Pechersk Lavra - North latitude B = 500 26 '02''.17; East longitude L = 300 33 '30''. 15 The Component “St. Sophia Cathedral and Related Monastic Buildings” is located on the highest area of the historic city center (the center of the Upper Town), at the intersection of its main structure-forming axes, which in the past connected Golden, Sofiivski, Lyadski and Lvivski Gate and at present they are fixed by Volodymyrska, Velyka Zhytomyrska and Sofiivska Streets. The ensemble is located along the main axis of Volodymyrska Street with access to Sofiivska Square, on which Volodymyrskyi Passage - the main compositional axis of the Upper Town is oriented. -
Photonic Crystal Sensors Based on Porous Silicon
Sensors 2013, 13, 4694-4713; doi:10.3390/s130404694 OPEN ACCESS sensors ISSN 1424-8220 www.mdpi.com/journal/sensors Review Photonic Crystal Sensors Based on Porous Silicon Claudia Pacholski Department of New Materials and Biosystems, Max Planck Institute for Intelligent Systems, Heisenbergstr. 3, Stuttgart 70569, Germany; E-Mail: [email protected]; Tel.: +49-711-689-3620; Fax: +491-711-689-3612 Received: 8 February 2013; in revised form: 26 March 2013 / Accepted: 3 April 2013 / Published: 9 April 2013 Abstract: Porous silicon has been established as an excellent sensing platform for the optical detection of hazardous chemicals and biomolecular interactions such as DNA hybridization, antigen/antibody binding, and enzymatic reactions. Its porous nature provides a high surface area within a small volume, which can be easily controlled by changing the pore sizes. As the porosity and consequently the refractive index of an etched porous silicon layer depends on the electrochemial etching conditions photonic crystals composed of multilayered porous silicon films with well-resolved and narrow optical reflectivity features can easily be obtained. The prominent optical response of the photonic crystal decreases the detection limit and therefore increases the sensitivity of porous silicon sensors in comparison to sensors utilizing Fabry-Pérot based optical transduction. Development of porous silicon photonic crystal sensors which allow for the detection of analytes by the naked eye using a simple color change or the fabrication of stacked porous silicon photonic crystals showing two distinct optical features which can be utilized for the discrimination of analytes emphasize its high application potential. Keywords: photonic crystal; porous silicon; sensor 1. -
List of Persons Who Are Planning to Export Maize from Ukraine to the People’S Republic of China No
List of Persons Who are Planning to Export Maize from Ukraine to the People’s Republic of China No. Full Name Short Name Address 1. PJSC «RISE» 03115, Ukraine, PUBLIC JOINT STOCK Kyiv, COMPANY «RISE» Peremohy Avenue, 121 В 2. PRIVATE JOINT STOCK PJSC «RISE-MAKSYMKO» 37240, COMPANY «RISE- Ukraine, MAKSYMKO» Poltava region, Lokhvitskiy district, Chervonozavodske, Matrosova street, 10 3. Public joint stock company “State PJSC“SFGCU” 01033, food and grain corporation of Ukraine, Ukraine” Kyiv, 1 Saksahanskoho street 4. LIMITED LIABILITY “GRANUM INVEST” LLC 01133, COMPANY “GRANUM Ukraine, INVEST” Kyiv, 34 Lesya Ukrainka street, office 416 5. LIMITED LIABILITY «LDC UKRAINE» LLC 04073, COMPANY “LOUIS DREYFUS Ukraine, COMPANY UKRAINE» Kyiv, 12 Kurenivsky Lane, corpus A, office 601 6. LIMITED LIABILITY “COFCO AGRI RESOURCES 01133, COMPANY “COFCO AGRI UKRAINE LLC ” Ukraine, RESOURCES UKRAINE” Kyiv, 32-B Eugene Konovalets street, office 1019 7. PRIVATE JOINT STOCK PrJSC“ Tetiivske KhPP” 09800, COMPANY “Tetiivske Ukraine, khlibopryimalne pidpryemstvo” Kyiv region, Tetiiv, 27 Kyivska street 8. AGRICULTURAL LIMITED «PROMIN» ALLC 16531, LIABILITY COMPANY Ukraine, «PROMIN» Chernigiv region, Bakhmatskiy district, Krasne village 1, Mischenka street 9. LIMITED LIABILITY «IMPEROVO FOODS» LLC 76018, COMPANY Ivano-Frankivsk, «IMPEROVO FOODS» 29 Promyslova srteet 10. AGRICULTURAL LIMITED «KALINA» ALLC 37332, LIABILITY COMPANY Ukraine, «KALINA» Poltavska region, Gadyatskiy district, Knishivka village 11. LIMITED LIABILITY “EUROPE-TRANS LTD” LLC 76018, COMPANY “EUROPE-TRANS Ukraine, LTD” Ivano-Frankivsk, 2 Promyslova street, office 20 12. AGRICULTURAL LIMITED «Named after Dukhova» ALLC 37362, LIABILITY COMPANY Ukraine, 2 «Named after Dukhova» Poltavska region, Gadyatskiy district, Veprik village 13. LIMITED LIABILITY “Vtormetexport” LTD 04050, COMPANY “Vtormetexport” Ukraine, Kyiv, 17, Glybochytska street, letter 1 A, building №2, office 101 14. -
8A1901d9d64f5f13975845866a0
RESEARCH ARTICLE Investigation of surface topography and stiffness on adhesion and neurites extension of PC12 cells on crosslinked silica aerogel substrates Kyle J. Lynch1, Omar Skalli2, Firouzeh Sabri1* 1 Dept. of Physics and Materials Science, University of Memphis, Memphis, Tennessee, United States of America, 2 Dept. of Biological Sciences, University of Memphis, Memphis, Tennessee, United States of America a1111111111 a1111111111 * [email protected] a1111111111 a1111111111 a1111111111 Abstract Fundamental understanding and characterization of neural response to substrate topog- raphy is essential in the development of next generation biomaterials for nerve repair. Aerogels are a new class of materials with great potential as a biomaterial. In this work, OPEN ACCESS we examine the extension of neurites by PC12 cells plated on matrigel-coated and colla- Citation: Lynch KJ, Skalli O, Sabri F (2017) gen-coated mesoporous aerogel surfaces. We have successfully established the method- Investigation of surface topography and stiffness on adhesion and neurites extension of PC12 cells ology for adhesion and growth of PC12 cells on polyurea crosslinked silica aerogels. on crosslinked silica aerogel substrates. PLoS ONE Additionally, we have quantified neurite behaviors and compared their response on aero- 12(10): e0185978. https://doi.org/10.1371/journal. gel substrates with their behavior on tissue culture (TC) plastic, and polydimethylsiloxane pone.0185978 (PDMS). We found that, on average, PC12 cells extend longer neurites on crosslinked sil- Editor: Nic D. Leipzig, The University of Akron, ica aerogels than on tissue culture plastic, and, that the average number of neurites per UNITED STATES cluster is lower on aerogels than on tissue culture plastic. -
Nanostructure of Porous Si and Anodic Sio2 Surface Passivation for Improved Efficiency Porous Si Solar Cells
nanomaterials Article Nanostructure of Porous Si and Anodic SiO2 Surface Passivation for Improved Efficiency Porous Si Solar Cells Panus Sundarapura 1 , Xiao-Mei Zhang 1,2,*, Ryoji Yogai 3, Kazuki Murakami 3, Alain Fave 4 and Manabu Ihara 1,3,* 1 Department of Chemical Science and Engineering, Tokyo Institute of Technology, 2-12-1 Ookayama, Meguro, Tokyo 152-8552, Japan; [email protected] 2 Department of Mechanical Engineering, Tokyo Institute of Technology, 2-12-1 Ookayama, Meguro, Tokyo 152-8552, Japan 3 Department of Chemistry, Tokyo Institute of Technology, 2-12-1 Ookayama, Meguro, Tokyo 152-8552, Japan; [email protected] (R.Y.); [email protected] (K.M.) 4 Univ Lyon, INSA Lyon, ECL, CNRS, UCBL, CPE Lyon, INL, UMR5270, 69621 Villeurbanne, France; [email protected] * Correspondence: [email protected] (X.-M.Z.); [email protected] (M.I.) Abstract: The photovoltaic effect in the anodic formation of silicon dioxide (SiO2) on porous silicon (PS) surfaces was investigated toward developing a potential passivation technique to achieve high efficiency nanostructured Si solar cells. The PS layers were prepared by electrochemical anodization in hydrofluoric acid (HF) containing electrolyte. An anodic SiO2 layer was formed on the PS surface via a bottom-up anodization mechanism in HCl/H2O solution at room temperature. The thickness of the oxide layer for surface passivation was precisely controlled by adjusting the anodizing current density and the passivation time, for optimal oxidation on the PS layer while maintaining its original Citation: Sundarapura, P.; Zhang, nanostructure. HRTEM characterization of the microstructure of the PS layer confirms an atomic X.-M.; Yogai, R.; Murakami, K.; Fave, lattice matching at the PS/Si interface. -
MEMS Applications of Porous Silicon
MEMS Applications of Porous Silicon Wolfgang Benecke and Alexandra Splinter Institute for Microsensors, -actuators and -systems (IMSAS) University of Bremen y Dept. 1 Physics/Electrical Engineering Kufsteiner Str. y D-28359 Bremen GERMANY Phone : +49 421 218 4698/4725 Telefax : +49 421 218 4774 email : [email protected] ABSTRACT Porous silicon fabricated by partial electrochemical dissolution of bulk silicon, shows outstanding material properties. The nanostructure of the remaining Si-skeleton is used for specific optical devices, such as emitters and filters. The high internal surface of the material opens new opportunities for different types of microsensors and -actuators and microsystem concepts. The porous layers can be used as sacrificial layers due to the high reactivity of the material which leads to a new class of micromachined MEMS devices. A brief overview on the historic evolution of the material is given. The base technologies for the fabrication of porous silicon layers are described. An overview on specific applications is given to demonstrate the potential of the material and the technology behind. Keywords : Porous silicon, MEMS INTRODUCTION AND HISTORY OF POROUS SILICON Porous silicon (PSi) has been subject of intensive investigations over the last decade. The potential of the material for MEMS applications has been underestimated for a long time and it should be considered that the discovery of PSi by UHLIR [1] goes back to 1956 at Bell Labs, USA. At this time the investigations on silicon had just started and UHLIR worked on the polishing of silicon- and germanium-wafers. The wafers were electrochemically polished using an electrolyte of hydrofluoric acid. -
Light Emitting Structures Porous Silicon-Silicon Substrate ;
UAO100955 PACS 73.20.Dx, 85.42.+m LIGHT EMITTING STRUCTURES POROUS SILICON-SILICON SUBSTRATE ; L.S.Monastyrskii, I.B.Olenych, M.KPanasjuk, V.P.Savchyn, O. V.Galchynskii (Physical Department, Iv. Franko Lviv State University, 50 Dragomanov Str.,290005, Lviv, Ukraine) The research of spectroscopic properties of porous silicon has been done. Complex of photoluminescence , electroluminescence , cathodoluminescence , thermostimulated depolarisation current analyth methods have been apply ed to study of geterostructures and free layers of porous silicon. Lightemitting processes had tendency to decrease. The character of decay for all kinds of luminescence were different. Introduction technological conditions on optical constants of por-Si and porosity p of the material. The For the first time Canham [1] in Appl. Phys. porosity was calculated on the base of n and k Letters (1990) reported about exotic visible using Lorentz-Lorenc equation [2]. Error of room-temperature photoluminescence of porous calculations was about 10%. silicon. So it become the possibylyty to create The Thermo Stimulated Depolarisation light-emitting dicodes (LED) and lasers on the Current (TSDC) investigation was made by same substrate of Si. Porous silicon may be a formed thermoelectret state in the sample PS new material for intergrated micro- and with area 1 cm2 in vacuum cryostat. Polarisation optoelectronics. was carried out in the electric field of the capacitor cell at the temperature betwien 450 Experimental methods and 480 K. The electric field was about 1-2* 104 V/m. After switcing off the polarising electric Layers of porous silicon (PS) were obtained field the TSD current has been measured with by electrochemical etching of n,p-types linear heating [3]. -
Porous Silicon for Drug Delivery Applications and Theranostics
ACCEPTED VERSION Tushar Kumeria, Steven J. P. McInnes, Shaheer Maher and Abel Santos Porous silicon for drug delivery applications and theranostics: recent advances, critical review and perspectives Expert Opinion on Drug Delivery, 2017; 14(12):1407-1422 © 2017 Informa UK Limited, trading as Taylor & Francis Group This is an Accepted Manuscript of an article published by Taylor & Francis in Expert Opinion on Drug Delivery, on 17 Apr 2017 available online: http://dx.doi.org/10.1080/17425247.2017.1317245 PERMISSIONS http://authorservices.taylorandfrancis.com/sharing-your-work/ Accepted Manuscript (AM) As a Taylor & Francis author, you can post your Accepted Manuscript (AM) on your personal website at any point after publication of your article (this includes posting to Facebook, Google groups, and LinkedIn, and linking from Twitter). To encourage citation of your work we recommend that you insert a link from your posted AM to the published article on Taylor & Francis Online with the following text: “This is an Accepted Manuscript of an article published by Taylor & Francis in [JOURNAL TITLE] on [date of publication], available online: http://www.tandfonline.com/[Article DOI].” For example: “This is an Accepted Manuscript of an article published by Taylor & Francis Group in Africa Review on 17/04/2014, available online: http://www.tandfonline.com/10.1080/12345678.1234.123456. N.B. Using a real DOI will form a link to the Version of Record on Taylor & Francis Online. The AM is defined by the National Information Standards Organization as: “The version of a journal article that has been accepted for publication in a journal.” This means the version that has been through peer review and been accepted by a journal editor. -
Kyiv, Ukraine: the City of Domes and Demons from the Collapse Of
Roman Adrian Roman Cybriwsky Kyiv, Ukraine is a pioneering case study of urban change from socialism to the hard edge of a market economy after the Soviet collapse. It looks in detail at the changing social geography of the city, and on critical problems such as corruption, social inequality, sex tourism, and destruction of historical ambience by greedy developers. The book is based on fieldwork and an insider’s knowledge of the city, and is engagingly written. Roman Adrian Cybriwsky is Professor of Geography and Urban Studies at Temple University in Philadelphia, USA, and former Ukraine Kyiv, Fulbright Scholar at the National University of Kyiv Mohyla Academy. He divides his time between Philadelphia, Kyiv, and Tokyo, about which he has also written books. “Roman Cybriwsky knows this city and its people, speaks their language, feels their frustrations with its opportunist and corrupt post-Soviet public figures Roman Adrian Cybriwsky who have bankrupted this land morally and economically. He has produced a rich urban ethnography stoked by embers of authorial rage.” — John Charles Western, Professor of Geography, Syracuse University, USA “Kyiv, Ukraine is an interdisciplinary tour de force: a scholarly book that is Kyiv, Ukraine also an anthropological and sociological study of Kyivites, a guide to Kyiv and its society, politics, and culture, and a journalistic investigation of the city’s darkest secrets. At this time of crisis in Ukraine, the book is indispensable.” — Alexander Motyl, Professor of Political Science, Rutgers University, USA The City of Domes and Demons “Filled with personal observations by a highly trained and intelligent urbanist, Kyiv, Ukraine is a beautiful and powerful work that reveals from the Collapse of Socialism profound truths about a city we all need to know better.” — Blair A.