Parameter Definition Using Vibration Prediction Software Leads To
Total Page:16
File Type:pdf, Size:1020Kb
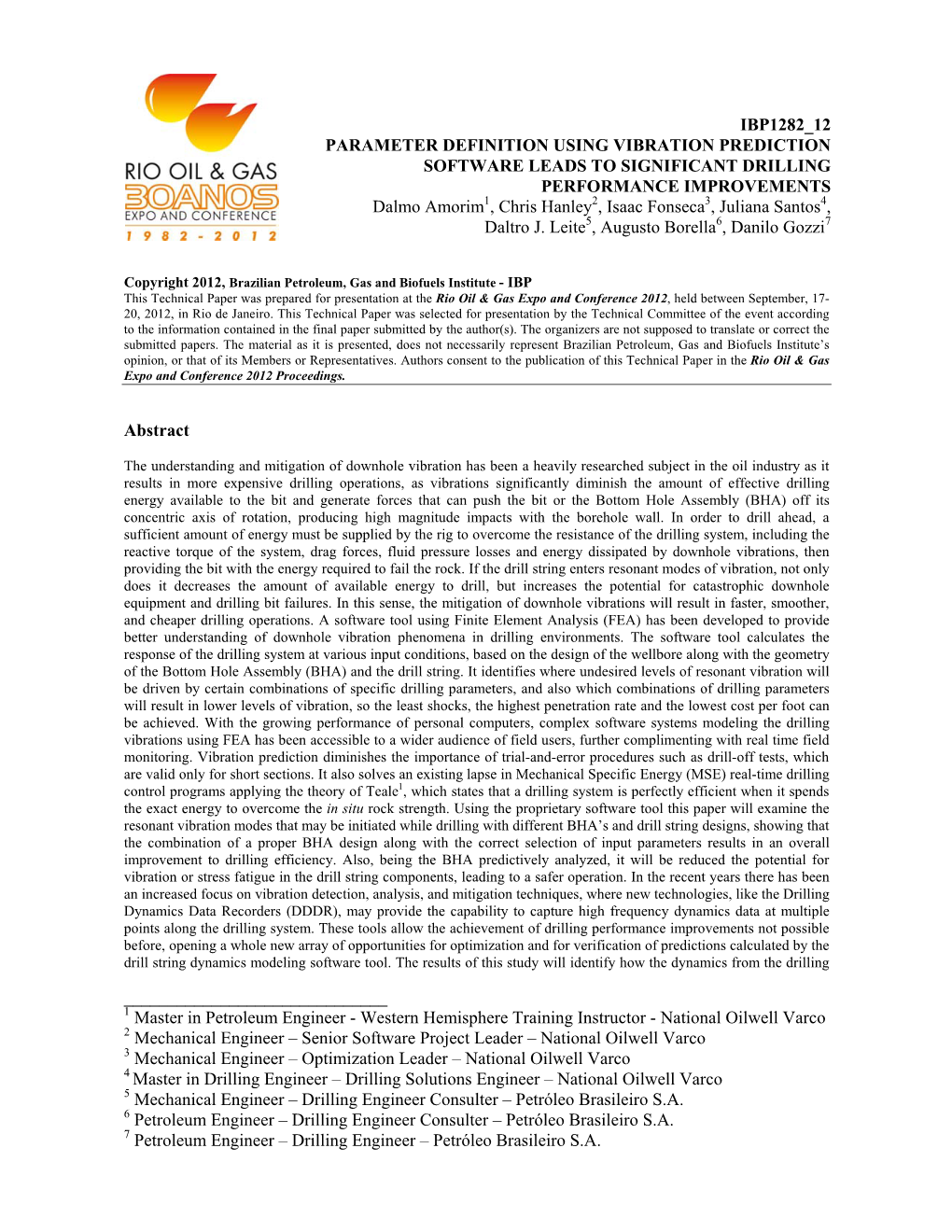
Load more
Recommended publications
-
Downhole Sensors in Drilling Operations
PROCEEDINGS, 44th Workshop on Geothermal Reservoir Engineering Stanford University, Stanford, California, February 11-13, 2019 SGP-TR-214 Downhole Sensors in Drilling Operations Nathan Pastorek, Katherine R. Young, and Alfred Eustes 15013 Denver West Blvd., Golden, CO 80401 [email protected] Keywords: MWD, LWD, Rate of Penetration, Drilling Data, Geothermal, Telemetry ABSTRACT Before downhole and surface equipment became mainstream, drillers had little way of knowing where they were or the conditions of the well. Eventually, breakthroughs in technology such as Measurement While Drilling (MWD) devices and the Electronic Drilling Recorder system allowed for more accurate and increased data collection. More modern initiatives that approach drilling as manufacturing— such as Lean Drilling, Drilling the Limit, and revitalized Drilling the Limit programs—have allowed petroleum drilling operations to become more efficient in the design and creation of a well, increasing rates of penetration by more than 50%. Unfortunately, temperature and cost limitations of these tools have prevented geothermal operations from using this state-of-the-art equipment in most wells. Today, petroleum drilling operations can collect surface measurements on key drilling data such as rotary torque, hook load (for surface weight on bit), rotary speed, block height (for rate of penetration), mud pressure, pit volume, and pump strokes (for flowrates). They also can collect downhole measurements of azimuth, inclination, temperature, pressure, revolutions per minute, downhole torque on bit, downhole weight on bit, downhole vibration, and bending moment using an MWD device (although not necessarily in real time). These data can be used to calculate and minimize mechanical specific energy, which is the energy input required to remove a unit volume of rock. -
Msc Martin Fosse Wired Drill Pipe Technology Technical And
The Author intentionally left this page blank 2| P a g e Abstract The author have designed this thesis to give the reader detailed knowledge about wired drill pipe technology (WDP technology). Focusing on providing the reader with unbiased examples and explanations have been of top priority. The optimal result being that the reader will be able to, with only little or none prior knowledge about WDP technology, fully understand the WDP technology’s economics and technical aspects. Wired drill pipe technology (WDP technology) is becoming more and more known to the oil industry. WDP provides wired communication with downhole tools, instead of conventional wireless communicating- methods like mud pulse telemetry (MPT) and electromagnetic telemetry (EMT). Up to this point, this new and sophisticated technology have been used to drill more than 120 wells worldwide. The technology have been around for some time, but have in later years gained more attention from oil companies, especially the companies regularly drilling highly challenging fields. This thesis gives a close examination of all the technical parts of the technology. Looks closer upon the transmission speed. How the telemetry works and the route between surface equipment and all the way down to the bottom hole assembly (BHA). The thesis also closely examines the economics of the technology and relate this to the cost of drilling operations offshore in the North Sea. New technology provide new possibilities, but they often tend to have a steep price tag. This thesis examines if the additional cost of wired pipe is worth the investment. It also provides calculations from two different example-wells, and the results from these calculations clearly states the cost of WDP. -
Real Time Torque and Drag Analysis During Directional Drilling
University of Calgary PRISM: University of Calgary's Digital Repository Graduate Studies The Vault: Electronic Theses and Dissertations 2013-03-06 Real Time Torque and Drag Analysis during Directional Drilling Fazaelizadeh, Mohammad Fazaelizadeh, M. (2013). Real Time Torque and Drag Analysis during Directional Drilling (Unpublished doctoral thesis). University of Calgary, Calgary, AB. doi:10.11575/PRISM/27551 http://hdl.handle.net/11023/564 doctoral thesis University of Calgary graduate students retain copyright ownership and moral rights for their thesis. You may use this material in any way that is permitted by the Copyright Act or through licensing that has been assigned to the document. For uses that are not allowable under copyright legislation or licensing, you are required to seek permission. Downloaded from PRISM: https://prism.ucalgary.ca UNIVERSITY OF CALGARY Real Time Torque and Drag Analysis during Directional Drilling by Mohammad Fazaelizadeh A THESIS SUBMITTED TO FACUALTY OF GRADUATE STUDIES IN PARTIAL FULFILMENT OF THE REQUIREMENTS FOR THE DEGREE OF DOCTOR OF PHILOSOPHY DEPARTMENT OF CHEMICAL AND PETROLEUM ENGINEERING CALGARY, ALBERTA March, 2013 © Mohammad Fazaelizadeh 2013 Abstract The oil industry is generally producing oil and gas using the most cost-effective solutions. Directional drilling technology plays an important role especially because the horizontal wells have increased oil production more than twofold during recent years. The wellbore friction, torque and drag, between drill string and the wellbore wall is the most critical issue which limits the drilling industry to go beyond a certain measured depth. Surface torque is defined as the moment required rotating the entire drill string and the bit on the bottom of the hole. -
Chapter 5: Drilling and Coring Requirements
CHAPTER 5: DRILLING AND CORING REQUIREMENTS Based on the scientific objectives of the IODP, there are a number of drilling and coring characteristics that were defined by the CDC as necessary or desirable for the Phase 2 riserless platform. Of primary importance is the ability to provide continuous sampling. Continuous sampling is defined as the ability to retrieve samples (core) as the hole is deepened without tripping the drill string back to the surface. This is typically accomplished using a wire line retrieval method. There are modifications and additions required to basic drilling equipment in order to achieve this goal. This is a departure from typical exploration/production drilling, but in keeping with drilling operations on the JOIDES Resolution. Additionally, due to the nature of riserless drilling and the remote operations of the program, the CDC report recommends that there be sufficient capacity for bulk mud storage and storage facilities for 1500 m of casing. Finally, the CDC report requested a combined drill string length of approximately 11,000 m and that the drill pipe have a minimum interior diameter of 4.125 inches to ensure passage of all sampling, coring, and wireline logging tools. In all the cases listed above, the RFP meets or exceeds the requirements specified in the CDC report. This section seeks to provide a vision of the drilling and coring package for the new riserless program. All of the equipment outlined below has been requested in the RFP. The eventual specifications for the drilling and coring equipment will depend on the selection of an SODV for the riserless program. -
Alternative Applications of Wired Drill Pipe in Drilling and Well Operations
Alternative applications of wired drill pipe in drilling and well operations FACULTY OF SCIENCE AND TECHNOLOGY MASTER THESIS Study program/specialization: Spring semester, 2019 Petroleum Engineering Open - Drilling & Wells Specialization Author: Bevin Babu Bevin Babu (Signature of author) Faculty supervisor: Mesfin Belayneh External Supervisor: Øystein Klokk Thesis title: Alternative applications of wired drill pipe in drilling and well operations Credits (ECTS): 30 Keywords: Wired Drill Pipe Number of pages: 128 Telemetry Systems Along String Measurements (ASM) Supplemental material/other: 1 Enhanced Measurement System (EMS) Date/year: 15-06-/2019 Well Operations - Drilling, Completions, Cementing, Perforation, Side Place: Stavanger, Norway Tracking Alternative applications of wired drill pipe in drilling and well operations ACKNOWLEDGMENT This master thesis is written the spring of 2019 as the final work of a Master of Science in Petroleum Engineering specialization in Drilling and Well technology from University of Stavanger, Norway. The scope of the thesis was initiated by Equinor ASA. The work was carried out at Equinor ASA, Stavanger and University of Stavanger, Norway. First, I would like to express my gratitude towards Equinor ASA for providing relevant information and data for aiding me in any way possible with regards to everything from workshop visits to technical information. I would like to thank my supervisor Dr. Mesfin Belayneh, Professor at Department of Energy and Petroleum, University of Stavanger for providing advice and guidance throughout the work. I would also like to express my greatest gratitude to Åsmund Gyldenskog, Leader Drilling and Well Operations, Mobile Units at Equinor ASA, Stavanger for providing me with the opportunity of writing this interesting thesis with his team. -
Research on a Measurement Method for Downhole Drill String Eccentricity Based on a Multi-Sensor Layout
sensors Article Research on a Measurement Method for Downhole Drill String Eccentricity Based on a Multi-Sensor Layout Hongqiang Li 1,2 and Ruihe Wang 1,* 1 School of Petroleum Engineering, China University of Petroleum, Qingdao 266580, China; [email protected] 2 Sinopec Shengli Drilling Technology Research Institute, Dongying 257000, China * Correspondence: [email protected]; Tel.: +86-159-5466-6188 Abstract: The drill string used in drilling is in a complex motion state downhole for several kilometers. The operating attitude and eccentricity of the downhole drill string play important roles in avoiding downhole risks and correcting the output of the imaging measurement sensor while drilling (IMWD). This paper proposes a method for measuring eccentricity while drilling using two sets of caliper sensors coupled with a fiber-optic gyroscope for continuous attitude measurement, which is used to solve the problem of the quantitative measurement of complex eccentricity that changes in real- time downhole. According to the measurement and calculation methods involved in this article, we performed simulations of the attitude of the drill string near where the IMWD tool is located in the wellbore under a variety of complex downhole conditions, such as centering, eccentricity, tilt, buckling, rotation, revolution, etc. The simulation and field test results prove that the distance between the imaging while drilling sensor and the borehole wall is greatly affected by the downhole attitude and revolution. The multi-sensor layout measurement scheme and the data processing based on the above-mentioned measurement involved can push the drill collar movement and eccentricity matrix specifically studied downhole from only qualitative estimation to real-time measurement and quantitative calculation. -
Stability Analysis of the Rotary Drill-String
University of Tennessee, Knoxville TRACE: Tennessee Research and Creative Exchange Doctoral Dissertations Graduate School 12-2014 Stability Analysis of the Rotary Drill-String Liangming Pan University of Tennessee - Knoxville, [email protected] Follow this and additional works at: https://trace.tennessee.edu/utk_graddiss Part of the Computer-Aided Engineering and Design Commons, and the Manufacturing Commons Recommended Citation Pan, Liangming, "Stability Analysis of the Rotary Drill-String. " PhD diss., University of Tennessee, 2014. https://trace.tennessee.edu/utk_graddiss/3159 This Dissertation is brought to you for free and open access by the Graduate School at TRACE: Tennessee Research and Creative Exchange. It has been accepted for inclusion in Doctoral Dissertations by an authorized administrator of TRACE: Tennessee Research and Creative Exchange. For more information, please contact [email protected]. To the Graduate Council: I am submitting herewith a dissertation written by Liangming Pan entitled "Stability Analysis of the Rotary Drill-String." I have examined the final electronic copy of this dissertation for form and content and recommend that it be accepted in partial fulfillment of the equirr ements for the degree of Doctor of Philosophy, with a major in Mechanical Engineering. J. A. M. Boulet, Major Professor We have read this dissertation and recommend its acceptance: Hans DeSmidt, Subhadeep Chakraborty, Yulong Xing Accepted for the Council: Carolyn R. Hodges Vice Provost and Dean of the Graduate School (Original signatures are on file with official studentecor r ds.) Stability Analysis of the Rotary Drill-String A Dissertation Presented for the Doctor of Philosophy Degree The University of Tennessee, Knoxville Liangming Pan December 2014 Copyright © 2014 by Liangming Pan. -
The Horizontal Directional Drilling Process
APPENDIX J HORIZONTAL DIRECTIONAL DRILLING The Horizontal Directional Drilling Process The tools and techniques used in the horizontal directional drilling (HDD) process are an outgrowth of the oil well drilling industry. The components of a horizontal drilling rig used for pipeline construction are similar to those of an oil well drilling rig with the major exception being that a horizontal drilling rig is equipped with an inclined ramp as opposed to a vertical mast. HDD pilot hole operations are not unlike those involved in drilling a directional oil well. Drill pipe and downhole tools are generally interchangeable and drilling fluid is used throughout the operation to transport drilled spoil, reduce friction, stabilize the hole, etc. Because of these similarities, the process is generally referred to as drilling as opposed to boring. Installation of a pipeline by HDD is generally accomplished in three stages as illustrated in Figure 1. The first stage consists of directionally drilling a small diameter pilot hole along a designed directional path. The second stage involves enlarging this pilot hole to a diameter suitable for installation of the pipeline. The third stage consists of pulling the pipeline back into the enlarged hole. Pilot Hole Directional Drilling Pilot hole directional control is achieved by using a non-rotating drill string with an asymmetrical leading edge. The asymmetry of the leading edge creates a steering bias while the non-rotating aspect of the drill string allows the steering bias to be held in a specific position while drilling. If a change in direction is required, the drill string is rolled so that the direction of bias is the same as the desired change in direction. -
Resonance: the Science Behind the Art of Sonic Drilling
RESONANCE: THE SCIENCE BEHIND THE ART OF SONIC DRILLING by Peter Andrew Lucon A dissertation submitted in partial fulfillment of the requirements for the degree of Doctor of Philosophy in Engineering MONTANA STATE UNIVERSITY Bozeman, Montana April 2013 ©COPYRIGHT by Peter Andrew Lucon 2013 All Rights Reserved ii APPROVAL of a dissertation submitted by Peter Andrew Lucon This dissertation has been read by each member of the dissertation committee and has been found to be satisfactory regarding content, English usage, format, citation, bibliographic style, and consistency and is ready for submission to The Graduate School. Dr. David Miller (Co-Chair) Dr. Douglas Cairns (Co-Chair) Approved for the Department of Mechanical and Industrial Engineering Dr. Christopher H.M. Jenkins Approved for The Graduate School Dr. Ronald W. Larsen iii STATEMENT OF PERMISSION TO USE In presenting this dissertation in partial fulfillment of the requirements for a doctoral degree at Montana State University, I agree that the Library shall make it available to borrowers under rules of the Library. I further agree that copying of this dissertation is allowable only for scholarly purposes, consistent with “fair use” as prescribed in the U.S. Copyright Law. Requests for extensive copying or reproduction of this dissertation should be referred to ProQuest Information and Learning, 300 North Zeeb Road, Ann Arbor, Michigan 48106, to whom I have granted “the right to reproduce and distribute my dissertation in and from microform along with the non-exclusive right to reproduce and distribute my abstract in any format in whole or in part.” Peter Andrew Lucon April 2013 iv ACKNOWLEDGEMENTS I would like to thank some of the many people who from the beginning of this work have been instrumental in its final success. -
Vibration Technologies for Friction Reduction to Overcome Weight Transfer Challenge in Horizontal Wells Using a Multiscale Friction Model
lubricants Article Vibration Technologies for Friction Reduction to Overcome Weight Transfer Challenge in Horizontal Wells Using a Multiscale Friction Model Xing-Ming Wang * and Xing-Miao Yao * School of Resources and Environment, University of Electronic Science and Technology of China, Chengdu 611731, China * Correspondence: [email protected] (X.-M.W.); [email protected] (X.-M.Y.) Received: 27 March 2018; Accepted: 17 May 2018; Published: 29 May 2018 Abstract: Drag reduction technologies mainly include the mechanical method and the chemical method. Mechanical drag reduction technologies are widespread in the drilling field due to their environmental friendliness and ease of use. Vibration technologies are among some of the most-used mechanical drag reduction technologies. However, various types of vibration tools have the negative effect of obstructing the promotion and application of mechanical drag reduction technologies. This paper widely investigated the types and applications of vibration tools. A drilling agitator system and slider drilling technology were included. The structure and mechanism of the vibration tool were studied. A multiscale friction model was proposed based on the Dahl model according to the drilling environment. The model was verified using experimental data. The multiscale friction model was used to analyze the drag reduction mechanism and the effect of different kinds of vibration technologies. Simulations demonstrated that vibration technologies can effectively reduce the axial friction of the drill string. Longitudinal vibration can reduce the axial friction such that the dependence of the reduced coefficient of friction on the reduced velocity does not change significantly after the reduced oscillation amplitude exceeds the critical value of one. -
Drilling Methods
DRILLING METHODS This continuing education unit reviews drilling methods common to drillers, with an emphasis on water well drilling methods. For completeness mention is made of methods or tools used in the oil & gas industry. Often methods or tools first employed in the oil or gas drilling industry eventually find their way into the water well drilling field. As well mention is made of drilling methods employed in the geotechnical or environmental drilling sector. However the coverage of the methods and tool of the geotechnical or environmental sector is not exhaustive. Many drillers adopt their chosen method of both hole- making and hole clearing and become experts over time. Long and successful careers are had by working within the method of drilling/hole clearing chosen. These drillers identify themselves by their chosen methods: “cable tool driller” “mud rotary driller,” “environmental/geotechnical driller.” Large companies look for these specialists when seeking new employees. Other drillers, by choice, or happenstance are exposed to several methods of making hole and hole clearing. These drillers become comfortable using different approaches depending upon hole size, engineering specifications, equipment availability and geology. The material below reviews the range of hole making and hole clearing approaches in common use in the drilling industry. Hole making methods Making hole includes breaking rock in consolidated formations and stirring sediments in unconsolidated formations. While hole making is most commonly carried out by mechanical means, other means may also be employed such as high frequency vibration and hydraulic pressure. MECHANICAL HOLE MAKING METHODS CABLE TOOL Cable tool had its beginnings 4000 years ago in China. -
Petroleum Extension-The University of Texas at Austin Petroleum Extension-The University of Texas at Austin Contents
Petroleum Extension-The University of Texas at Austin Petroleum Extension-The University of Texas at Austin Contents The Roughneck Training Handbook First Edition by Ron Baker Petroleum Extension-The University of® Texas at Austin 2017 i THE ROUGHNECK TRAINING HANDBOOK Library of Congress Cataloging-in-Publication Data Names: Baker, Ron, 1940- Title: The roughneck training handbook / by Ron Baker. Description: First edition. | Austin, Texas : Petroleum Extension (PETEX), The University of Texas at Austin, 2017. | "Catalog No. 2.02010." | Includes index. Identifiers: LCCN 2017036251| ISBN 9780886982744 (alk. paper) | ISBN 088698274X (alk. paper) Subjects: LCSH: Oil well drilling—Study and teaching— Handbooks, manuals, etc. | Petroleum workers—Training of— Handbooks, manuals, etc. Classification: LCC TN871.2 .B31633 2017 | DDC 622/.3381— dc23 LC record available at https://lccn.loc.gov/2017036251 Disclaimer Although all reasonable care has been taken in preparing this publication, the authors, the Petroleum Extension Service (PETEX®) of The University of Texas at Austin, and any other individuals and their affiliated groups involved in preparing this content, assume no responsibility for the consequences of its use. Each recipient should ensure he or she is properly trained and informed about the unique policies and practices regarding application of the information contained herein. Any recommendations, descriptions, and methods in this book are presented solely for educational purposes. ©2017 by The University of Texas at Austin All rights reserved First Edition published 2017 Printed in the United States of America This book or parts thereof may not be reproduced in any form without permission of Petroleum Extension (PETEX), The University of Texas at Austin.