Blinking Orbital Prosthesis
Total Page:16
File Type:pdf, Size:1020Kb
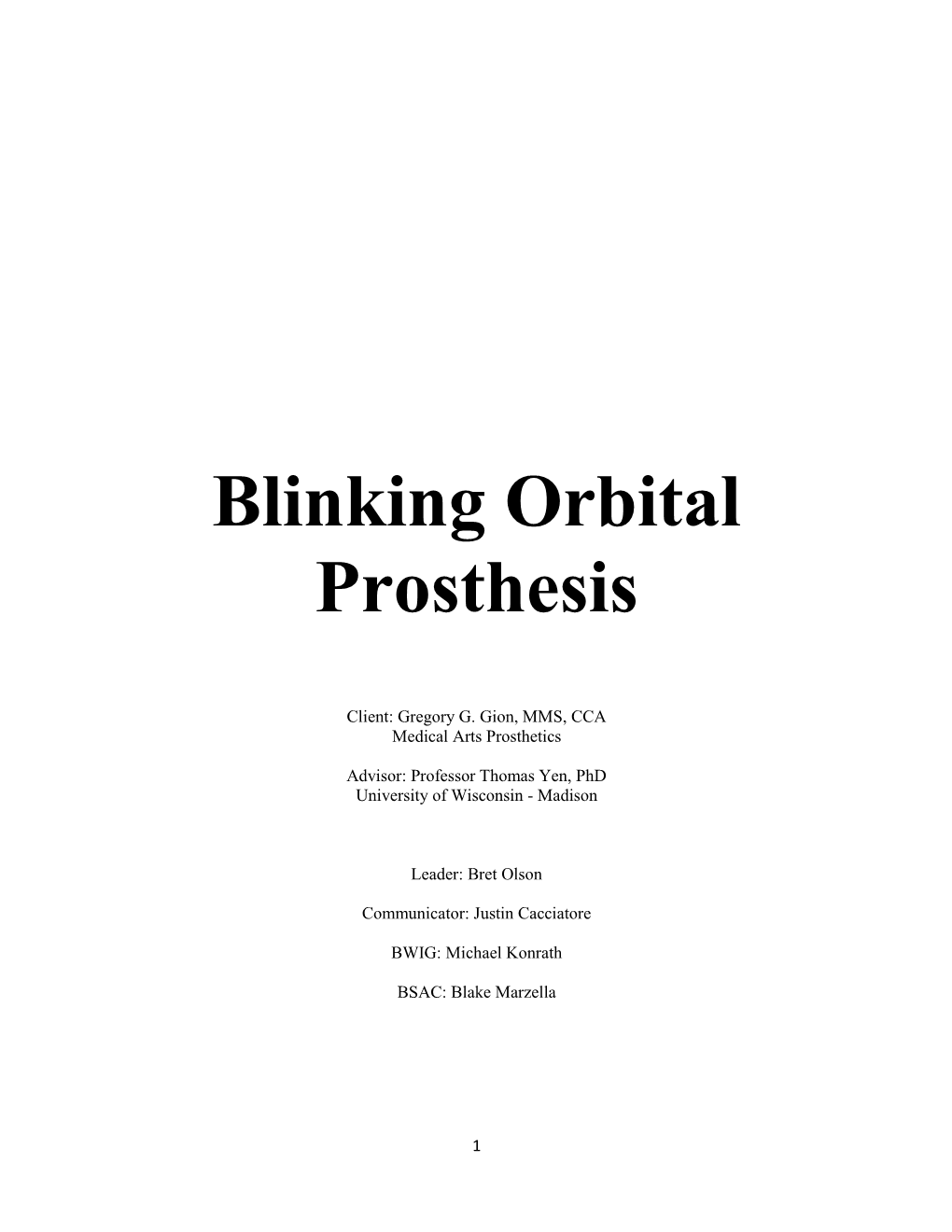
Load more
Recommended publications
-
Clinical Ocular Prosthetics
Clinical Ocular Prosthetics Keith R. Pine • Brian H. Sloan Robert J. Jacobs Clinical Ocular Prosthetics Keith R. Pine Robert J. Jacobs School of Optometry and Vision Science School of Optometry and Vision Science The University of Auckland The University of Auckland Auckland Auckland New Zealand New Zealand Brian H. Sloan New Zealand National Eye Centre The University of Auckland Auckland New Zealand ISBN 978-3-319-19056-3 ISBN 978-3-319-19057-0 (eBook) DOI 10.1007/978-3-319-19057-0 Library of Congress Control Number: 2015944089 Springer Cham Heidelberg New York Dordrecht London © Springer International Publishing Switzerland 2015 This work is subject to copyright. All rights are reserved by the Publisher, whether the whole or part of the material is concerned, specifi cally the rights of translation, reprinting, reuse of illustrations, recita- tion, broadcasting, reproduction on microfi lms or in any other physical way, and transmission or infor- mation storage and retrieval, electronic adaptation, computer software, or by similar or dissimilar methodology now known or hereafter developed. The use of general descriptive names, registered names, trademarks, service marks, etc. in this publica- tion does not imply, even in the absence of a specifi c statement, that such names are exempt from the relevant protective laws and regulations and therefore free for general use. The publisher, the authors and the editors are safe to assume that the advice and information in this book are believed to be true and accurate at the date of publication. Neither the publisher nor the authors or the editors give a warranty, express or implied, with respect to the material contained herein or for any errors or omissions that may have been made. -
Synergistic Collaboration 30TH ANNUAL EDUCATIONAL CONFERENCE Fort Worth, Texas, USA
ABSTRACTS International Anaplastology Association Synergistic Collaboration 30TH ANNUAL EDUCATIONAL CONFERENCE Fort Worth, Texas, USA International Anaplastology Association | 1 WELCOME Welcome Dear Colleagues As President of the International Anaplastology Association, I am pleased to welcome you to the 30th Annual Educational Conference that will take place in Fort Worth, Texas. The theme chosen by our Conference Planning Committee for this year will be Synergistic Collaboration, which translates the importance of collaboration among professionals from all areas of expertise involved in the rehabilitation of our patients with a common goal to improve their “Quality of Life”. Many congratulations to my dear friend and Conference Chair Suzanne Verma for her wonderful and endless dedication to organize such a fantastic CONTENTS scientific program. President‘s Welcome 02 Program Chair Welcome 03 To our keynote speakers, invited speakers and colleagues, please accept my warmest regards and be very welcome to this years “IAA Family Reunion”. Conference Sponsors 04 It has been an honor and privilege to serve as President of the IAA this year. At A Glance Schedule 06 Pre-Conference Program 10 I want to thank for the tremendous support from the IAA Board of Directors and our Executive Director Rachel Brooke, who dedicated their time and Conference Day 1 16 expertise to the development of this Conference. Conference Day 2 33 This meeting will be a great opportunity not only to expand our knowledge by Post-Conference Program 48 exchanging our experiences with the most renowned and talented speakers, Poster Presentations 52 some already known by you and some new ones. Notes 54 Our “Anaplastology Family “ is with arms wide open to receive new members and attendants from various specialties involved in the rehabilitation of people suffering from facial and somato disfigurement. -
26Th Annual IAA Conference Anaplastology: Beyond the Horizon
26th Annual IAA Conference Anaplastology: Beyond the Horizon CONFERENCE PROGRAM NH Belfort Hotel Ghent, Belgium May 30–June 2, 2012 Providing Education and Support to Anaplastology President’s Welcome Dear Colleagues, As president of the International Anaplastology Association it is my pleasure to welcome you to the 26th Annual IAA Conference in the beautiful city of Ghent, Belgium. This year’s theme Anaplastology: Beyond the Horizon is about how far we have come as an international allied-health field and what we will endeavor to attain for our future. I have witnessed the growth and maturation of the field of anaplastology; forged by the ideas, dedication, and hard work of a global village of highly skilled committed professionals who have enthusiastically supported the anaplastology association throughout the years. We are grateful to ALL who have made their mark on the field. In 1983 when osseointegrated implants became the new standard in implant technology and the personal computer was in its infancy, I was learning laboratory procedures such as electroplating hand molds to produce rotational castings of polyvinylchloride prosthetic gloves. Techniques that came out of post World War II research developed by my mentors Felix B. Weinberg and Carl Dame Clarke. From the beginning of my career I have been Table of Contents keenly aware that there are untold pioneers in the field whose shoulders we stand on and to whom we owe a great debt. 3 Chairman’s Welcome Through generations we have made great strides. Today we take for granted the reliability of craniofacial osseointegration methods established by Professor Per- 4 About IAA Ingvar Brånemark. -
About Face Newsletter Article by Suzanne Verma and Sharon Haggerty
Leading the Way for People with Facial Differences Winter 2005 Volume 21, Number 1 “The Perfect Flaw”— Anaplastology An Interview ______________ 2-3 “The Perfect Flaw” is a new, multiple-award- winning documentary about David Roche, a humorist and public speaker from Mill Valley, Meet AboutFace Calif., who was born with a venous malformation USA’s new and gets speaking engagements worldwide, president ______ 12 including a performance at the White House. His condition is a benign tumor consisting of swollen blood vessels, and he uses a lifetime of public experiences regarding his face for much of his stage North American material. The film captures Roche offstage as well Craniofacial as on – with his wife, friends and storytelling Family Conferene students – and revisits the harrowing medical and Materials_____ 5-11 social ordeals of his early years. It also lets him articulate the priceless spiritual perspective that his experiences unexpectedly gave him. The filmmaker, Mike Grundmann, is a Los David Roche Angeles Times editor who was born with a cleft lip and palate. Q: Wasn’t your face a make-or-break proposition? A: My struggle has not been a clear-cut one. I have Q (Grundmann): My to keep working at it. Baseball is called a game of NACFC 2005 strategy when growing up and failure because the best batters make an out 7 out being ridiculed at school was of 10 times. Well, I would say I’m a .400 hitter in July 17-20, 2005 pretending it didn’t bother me life, which is great, but that means I make an out Las Vegas — even after I got home from more often than not. -
2019 Conference Program
The 66th Annual Meeting of the AMERICAN ACADEMY OF MAXILLOFACIAL PROSTHETICS The Changing Art and Science of Maxillofacial Prosthetics MIAMI BEACH, FLORIDA OCT 26 - 29, 2019 2019 CONFERENCE PROGRAM Tulip For Team Fox A portion of proceeds from all purchases supports The Michael J. Fox Foundation for Parkinson’s Research AVAILABLE AT MONTEGRAPPA BOUTIQUES, ONLINE AND AUTHORISED DEALERS WORLDWIDE MONTEGRAPPA.COM Welcome Colleagues to the 66th annual meeting of the American Academy of Maxillofacial Prosthetics Conference Dates: October 26-29, 2019 Eden Roc Hotel Miami Beach, Florida USA 2019 Conference Title: The Changing Art and Science of Maxillofacial Prosthetics RES SEMINARS 4425 Cass St. Suite A. San Diego, CA 92109 T: 858-272-1018 F: 858-272-7687 www.res-inc.com 1 AAMP MISSION STATEMENT We are an association of prosthodontists who are engaged in the art and science of maxillofacial prosthetics. Our mission is to accumulate and disseminate knowledge and experience; and, to promote and maintain research programs involving methods, techniques and devices used in maxillofacial prosthetics. The Academy is devoted to the study and practice of methods used to habilitate esthetics and function of patients with acquired, congenital and developmental defects of the head and neck; and of methods used to maintain the oral health of patients exposed to cancer-cidal doses of radiation or cytotoxic drugs. MEMBERSHIP INFORMATION How to Become a Member: If you are interested in becoming a member, attending our Annual Meeting is the best way to become -
Fifty Years—American Society of Ocularists—1957–2007
JOURNAL OF OPHTHALMIC PROSTHETICS FIFTY YEARS—AMERICAN SOCIETY OF OCULARISTS—1957–2007 CANADIAN FOCUS ISSUE VOLUME 20 • NUMBER 1 FALL 2015 VOL. VOL. 12 , NO. 1 JOURNAL OF OPHTHALMIC PROSTHETICS Official Journal of the VOLUME 20 • NUMBER 1 FALL 2015 American Society of ISSN 1091-2983 ISBN: 978-1-886236-63-9 Ocularists EDITORIAL iv President’s Message vi Announcements v From the Senior Editor ARTICLES 1 Tear Abnormalities Associated with Anophthalmos and Ocular Prosthetic Wear Jonathan S. Brett, B.C.O., B.A.D.O. 5 Prosthetic Fabrication in Identical Triplets with Bilateral Retinoblastoma and a Single Enucleated Globe Using a Myoconjuntival Enucleation Procedure Matthew Milne, B.C.O., B.A.D.O; Sameh E. Solima, M.D. 13 Maya’s Special Eye: Encouraging Ocularists Working with Children and their Families Robert Drennan, B.C.O., B.A.D.O. 21 Fabrication and Function of the LaFuente Pressure Mask Pauline Slorach, B.C.O., B.A.D.O.; Michael Webb, B.C.O., B.A.D.O., F.A.S.O. 29 Syndromes and Abnormalities Associated with Congenital Microphthalmia Shirley D. Weyland, B.C.O., B.A.D.O.; Femida Kherani, B.Sc., M.D. F.R.C.S.C. DEPARTMENTS: News: 37 Changing the World One Eye at a Time: Practical Considerations for Serving in the Developing World Ian McRobbie, B.C.O., B.A.D.O; James Willis, B.C.O., B.A.D.O., F.A.S.O.; Jon Koroscil, B.C.O., B.A.D.O. 55 Passing the Torch: A New Generation Takes Over the Proprietorship of an Established Practice in Ocularistry Marie-France Clermont, B.C.O., B.A.D.O. -
Surgical Versus Prosthetic Reconstruction of Microtia: the Case for Prosthetic Reconstruction Gregory G
CLINICAL CONTROVERSIES IN ORAL AND MAXILLOFACIAL SURGERY: PART ONE J Oral Maxillofac Surg 64:1639-1654, 2006 Surgical Versus Prosthetic Reconstruction of Microtia: The Case for Prosthetic Reconstruction Gregory G. Gion, BA, BS, MMS, CCA* The auricular prosthesis and the autogenous recon- collaboration with university implant teams in Dallas, struction must ultimately be judged on their ability to Texas. This article suggests that the prosthetic option free the patient from the stigmatization of their con- has historically been poorly represented, even misrep- dition. Excellent esthetic results are key in providing resented for various reasons, and that more should be patients with the confidence that their correction will published in the future to give a more complete go undetected. There are other technical and psycho- picture of the prosthetic option to help with this logical issues that impact prostheses success in par- decision of treatment selection. It is hoped that the ticular, but the wide variability in esthetic quality author’s experience, not as plastic surgeon, implant available historically and around the world today surgeon, or prosthodontist, but as the silicone ear might still be unnecessarily complicating if not bias- specialist of 25 years, will add a different perspective ing the treatment selection process. The thrust of this to help guide future decisions. article is to provide current advantages and future Treatment options for children with absence or potential of prostheses, along with demonstration of other malformation of the pinna remain; no treat- esthetic results that are possible with ear prostheses. ment, autogenous reconstruction, or prosthetic re- The hope is that readers will come away more en- construction. -
Holding Hands to Improve Quality of Life
HOLDING HANDS TO IMPROVE QUALITY OF LIFE Holding Hands to Improve Quality of Life ANAPLASTOLOGY – MEDICINE – DENTISTRY International Anaplastology Association 29TH ANNUAL EDUCATIONAL CONFERENCE Rio de Janeiro, Brazil 1 HOLDING HANDS TO IMPROVE QUALITY OF LIFE Welcome Dear Colleagues, It is a pleasure to welcome you to the 29th Annual International Anaplastology Association Educational Conference. We are delighted to host a conference in Brazil and South America for the first time. I believe that this year’s theme, “Holding Hands to Improve Quality of Life,” speaks to our diverse rolls in collaborative patient care teams and our mission for quality patient care. I congratulate Dr. Marcelo Ferraz de Oliveira on a terrific program. I thank him for his many hours dedicated to developing the educational conference. It is an honor to welcome and thank our keynote speakers, our invited speakers, and colleagues. We appreciate their time their time and expertise. It was a privilege to serve as President of the IAA this year. I received tremendous support from the IAA Board of Directors and our Executive Director, Rachel Brooke. It was an honor to serve with this team of leaders. The Board’s dedication and support were invaluable, as we hosted our conference in South America for the first time. One of our goals this year was to strengthen membership value through online educational opportunities. I would particularly like to highlight the work of board member and Education Committee Chair, Colette Shrader. Her committee brought regular online educational opportunities to accomplish our goal. Already this year, we completed four online webinars, which are free to members. -
Clinical Anaplastology Guidelines
International Anaplastology Association Published November 2020 Clinical Anaplastology Guidelines Contents Table of Contents Introduction and History Definition of Terms Scope of Practice Clinical Anaplastology Guidelines ▪ Section 1: Patient Assessment and Treatment ▪ Section 2: Quality Assurance ▪ Section 3: Professional Performance Standards 1 Introduction and History Founded in 1980, the International Anaplastology Association (IAA), formerly the American Anaplastology Association (AAA) defines the professional image and field of anaplastology worldwide by promoting excellence within the field of facial, ocular, and somatic prosthetics to enhance the lives of patients. The IAA provides for continued education, research, and advocacy opportunities among professionals involved in restoring malformed or absent parts of the human body through custom-made prosthetics that normalize appearance and restore function. The practice of anaplastology has changed significantly during the last several decades. Increased autonomy, clinical team membership, and higher qualifications have developed the operational role and professional sphere of the clinical anaplastologist. Coincident with role development is greater accountability, increasing professional responsibility and the requirement for basic guidelines to ensure patient care and safety. The Clinical Anaplastology Guidelines (CAG) are evidence-based recommendations for the health and care of patients requiring facial and somatic prosthetics internationally. The IAA is cognizant of both the importance and the challenges of developing sound, credible and relevant guidelines for anaplastologists internationally. Taking this into consideration, these guidelines are suitable for most practitioners and their patients realizing the diversity of specific conditions and needs, and people in unique circumstances and settings. The guidelines are to give an overview of recommendations on how to perform the task of restoring and/or replacing the form and function of human anatomy with custom-made devices. -
1 Faculty Council Meeting Meeting Minutes Monday, September 17
Faculty Council Meeting Meeting Minutes Monday, September 17, 2018 4:00-5:30PM – BRB 105 4:00PM Welcome and Chair’s Comments Sudha Chakrapani 4:10PM Introduction of New FC Members Sudha Chakrapani 4:20PM Approval of Minutes from June 18, 2018 Meeting Sudha Chakrapani 4:25PM Steering Committee Activities Report Sudha Chakrapani 4:30PM New Minor Program Application, Nutrition James Swain 4:40PM Amendments Discussion from the Bylaws Committee Darin Croft 4:50PM New Department Application: Otolaryngology-Head Gene Barnett and Neck Surgery, CCLCM 5:00PM New Department Application: Dermatology, CCLCM Gene Barnett 5:10PM Discuss Chair-Election Election and the NEC Recommendation 5:20PM New Business 5:30PM Adjourn Members Present Corinne Bazella Zachary Grimmett Nimitt Patel Tracey Bonfield Beata Jastrzebska P. Ramakrishnan Robert Bonomo Hung-Ying Kao Ben Roitberg David Buchner Stathis Karathanasis Satya Sahoo Cathleen Carlin Laura Kreiner Scott Simpson Sudha Chakrapani Varun Kshettry Jochen Son-Hing Shu Chen Cynthia Kubu Phoebe Stewart Gary Clark Suet Kam Lam Charles Sturgis Brian D'Anza Maria Cecilia Lansang James Howard Swain Piet de Boer Charles Malemud Daniel Sweeney Philipp Dines Danny Manor Melissa Times Jennifer Dorth Jenifer McBride Carlos Trombetta William Dupps Vincent Monnier Anna Valujskikh Judith French Vicki Noble Richard Zigmond Pamela Davis 1 Members Absent Bryan Baskin Mahmoud Ghannoum Aparna Roy Monica Gerrek Rekhy Mody Barbara Snyder Sherine Ghafoori Clifford Packer Patricia Thomas Hilary Petersen Michael Wolfe Others Present Nicole Deming Supriya Goyal Gene Barnett Peter Harte Maureen McEnery Nicole Ward Welcome and Chair’s Comments Dr. Sudha Chakrapani, Faculty Council Chair, called the meeting to order at 4:05pm. -
The Journal of Facial and Somato Prosthetics
The Journal of Facial and Somato Prosthetics Volume 10 Number 2 Wimer 2004 Published by ABI Professional Publications ISSN 1082- 1821 ISBN 1-886236-49-6 The j ournal ofFacial and Somato Prostetics is listed in EMBASE, the Excerpta Medica electronic data base. INDEX ISSUE Volumes 1 to 10 EDITORIAL m Publisher's Note INDEX ISSUE 65 Table of Contents, Volume 1 through Volume 10 73 Alphabetical List of Articles, Volume 1 through Volume 10 79 Author and Coauthor Index, Volume 1 through Volume 10 91 Key Word Index, Volume 1 through Volume 10 The Journal ofFacial and Somato Prosthetics (ISSN 1082-1821) is published by AB! Professional Publications, P.O. Box 149, St. Petersburg, Florida 33731. Copyright 2006 by ABl Professional Publications. All ri ghts reserved, which includes the right ro reproduce this journal or any portion there of in any form whatsoever, except as provided. The Journal ofFacial and Somato Prosthetics has been created ro provide current and timely infor mation for the professional in the fields of facial prosthetics, prosthetic materials, artificial limb prosthetics, ocular prosthetics, surgical preparation for prosthetics, prosthetic education, and computer applications in prosthetics. Rights, Reprints, and Back Issue Sales Please contact ABI Professional Publications, P.O . Box 149, St. Petersburg, Florida 33731 Phone (727) 556-0950 email: [email protected] Liability Disclaimer While every effort is made to insure accuracy and correctness of articles, publication of an arti cle is not an endorsement of the research, techniques, or results reported in the articles. The statements and opinions in the articl es of this journal are solely those of the authors and are not necessarily those of AB! Professional Publications, any sponsoring orgaJlizations, or the edirors, staffs, and associates of the Journal. -
Clinical Anaplastology Trainee/Assistant Position
Clinical Anaplastology Trainee/Assistant Position Document created by Juan Garcia, MA, CCA, Director of the Johns Hopkins University Anaplastology/Facial Prosthetics Clinic Position Description General Purpose of Work: A Clinical Anaplastologist is a health care professional that provides custom-designed, fabricated and fitted extra-oral aesthetic prostheses or other medical devices that are non-weight bearing, as specified in the Board for Certification in Clinical Anaplastology (BCCA) Scope of Practice. These devices usually include facial, ocular, and somatic prostheses. Provision of care is based on a physician’s referral and clinical assessment to support, modify, replace, protect or restore an anatomical structure. Primary Duties and Responsibilities: The role of the Trainee is to support the clinical activities of the Director of the Anaplastology Clinic in making facial and body prostheses for patients by training in all aspects of this service including: assessment, treatment planning, implementation, device delivery, patient education, follow up care, and ethical and professional standards. Trainee will be responsible for setting their own hours of work, with a minimum expectation of 32 hour work week. Projects will be given on a per case basis and may involve some independent work. All work done directly with patients will be supervised. The Trainee will be given an opportunity to interact with other professionals involved in the care of patients and provision of services (e.g. maxillofacial prosthodontists, facial plastic