Service Manual Nissan Cedric Model 31 Series
Total Page:16
File Type:pdf, Size:1020Kb
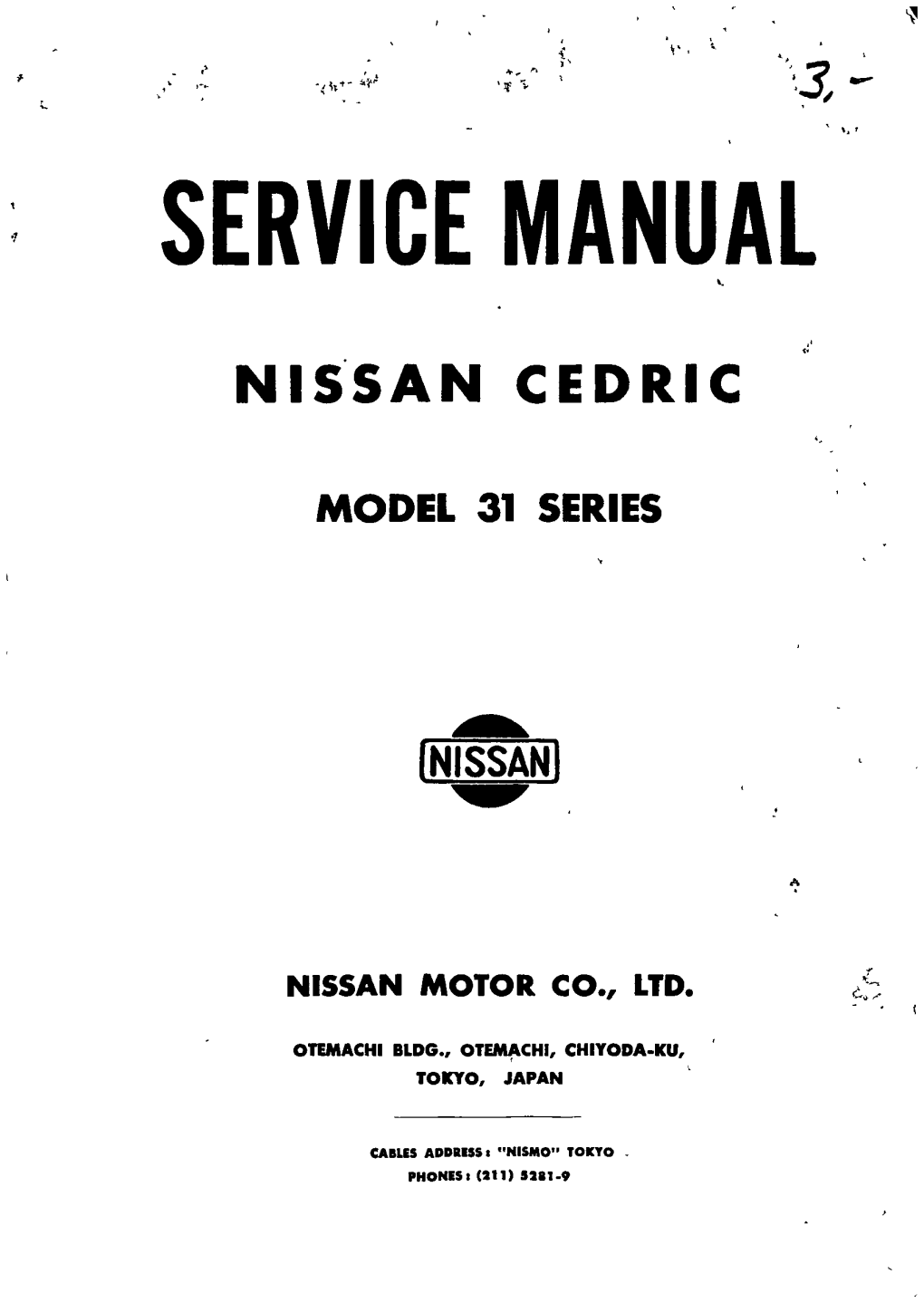
Load more
Recommended publications
-
Quattro Freni Qf13c00046
QUATTRO FRENI QF13C00046 КРЕСТОВИНА КАРДАННОГО ВАЛА 24X63 CROSS-REFERENCE: 37000BR52A, 370001DB0B, 370001DB0E, 370001DF0B, 370001DF0C, 370001DF0D, 37000BR51A, 37000JD000, 37000JD200 Характеристики: Применяемость INFINITI FX 45 Привод на все колеса 01.2003 - 12.2008 INFINITI FX 45 02.2003 - 12.2008 INFINITI FX 35 Привод на все колеса 01.2003 - 12.2008 INFINITI FX 35 02.2003 - 12.2008 INFINITI M30 Convertible 3.0 01.1990 - 12.1993 INFINITI M30 купе 3.0 01.1989 - 12.1993 INFINITI Q45 I 4.5 01.1989 - 12.1993 INFINITI Q45 II (FY33) 4.1 01.1997 - 01.2001 NISSAN 180 SX купе (S13) 2.0 Turbo 04.1991 - 03.1994 NISSAN 180 SX купе (S13) 1.8 Turbo II 04.1989 - 06.1992 NISSAN 180 SX купе (S13) 1.8 Turbo 09.1988 - 06.1992 NISSAN 200 SX (S13) 1.8 Turbo 01.1992 - 09.1994 NISSAN 200 SX (S13) 1.8 09.1988 - 03.1994 NISSAN 200 SX (S14) 2.0 i 16V 10.1993 - 12.1999 NISSAN 200 SX купе 2.0 01.1979 - 06.1981 NISSAN 240 SX 2.4 05.1994 - 08.1997 NISSAN 240 SX 2.4 04.1993 - 09.1994 NISSAN 300 ZX (Z31) 3.0 Turbo 04.1984 - 10.1990 NISSAN BLUEBIRD (910) 2.0 TD 01.1983 - 09.1983 NISSAN BLUEBIRD (910) 2.0 i 01.1982 - 12.1983 NISSAN BLUEBIRD (910) 2.0 D 01.1980 - 12.1983 NISSAN BLUEBIRD (910) 1.8 01.1980 - 12.1983 NISSAN BLUEBIRD (910) 1.6 01.1980 - 11.1983 NISSAN BLUEBIRD SYLPHY I (N16) 1.8 4x4 08.2000 - 07.2002 NISSAN BLUEBIRD Traveller (W910) 2.0 D 01.1980 - 05.1984 NISSAN BLUEBIRD Traveller (W910) 1.8 01.1980 - 05.1984 NISSAN BLUEBIRD Traveller (W910) 1.6 05.1980 - 05.1982 NISSAN BLUEBIRD седан (910) 1.9 i 01.1982 - 05.1984 NISSAN BLUEBIRD седан (910) 1.8 Turbo 01.1980 -
Die-Cast Model Fire Engines Tomica
Die-Cast Model Fire Engines Tomica Regular Series + Special Editions + Anniversary Editions + Gift Set Editions Number Description Year Scale Notes Photo Regular 3-2 Isuzu Telesquirt 1974 110 Release Nissan Cedric 2800SGL Fire Chief Regular 13-3 ? ? Car Release Regular 13-4 Nissan Cedric Ambulance ? ? Release Rescue Work Car Regular 13-7 1996 110 Variations include paint, coloring, Release lettering, and light bar shape Gift set editions Nissan Skyline GT-R R32 Regular 20-6 ? 59 Ambulance release Regular 21-4 Subaru 360 Fire Chief Car 1984 50 release Nissan Diesel Aerial Ladder Fire Truck 22-4 1987 120 Variations include paint, lettering, detailing, and light bar shape Crown Fire Chief Car 27-1 1971 65 First of three types, each using different castings 29-1 Hino Aerial Ladder Fire Truck 1972 ? 29-2 Hino Aerial Ladder Fire Truck 1975 125 34-3 Honda Civic Country Emergency Car 1983 59 N/A Nissan Caravan Ambulance 36-2 1980 67 Variations include lettering, striping, and interior color Toyota Hiace Ambulance 36-3 1988 66 Variations include single beacon, light bar, and light bar shape Toyota Ambulance 40-1 1972 70 Variations include lettering and striping 47-2 Nissan Gloria Fire Chief 1973 ? Nissan Paramedic Ambulance 51-4 1993 78 Variations include paint and lettering 57-1 Toyota Hiace Ambulance 1972 68 58-3 Nissan Cedric Patrol Car 1984 65 58-4 Nissan Cedric Fire Chief ? ? Toyota JSDF Ambulance 67-2 1978 81 Variations include paint, wheels, and lettering Isuzu Pump Fire Engine 68-1 1973 87 Variations include coloring and wheels 68-2 Isuzu -
Cutite Pentru Desprins Geamurile U.A. 2 Buc. Tip Auto Nr
1 2 3.1 3.2 4 5 6 7 8 Foto 1 Foto 2 Foto 3 Foto 4 Foto 5 Foto 6 Foto 7 Foto 8 mm Nr. articol mm Nr. articol mm Nr. articol mm Nr. articol mm Nr. articol mm Nr. articol Nr. articol Nr. articol 35,0 696 573 16,0* 696 599 16 - 35 696 514 3* 14,0 696 582 10,0 696 583 14,0 696 512 0 696 511 3 696 513 2 26,0 696 512 1 16,0 696 512 2 18 - 39 696 517 0* 16,0 696 513 3 16,0 696 595 35,0 696 510 3 91,0 696 517 6 23,0 696 517 3 32 - 39 696 517 5* 35,0 696 513 0 16,0 696 510 8 35,0 696 510 4 25,0 696 512 4 42 - 60 696 518 2* 39,0 696 515 2 18,0 696 587 35,0 696 510 9 27,0 696 517 4 60 - 76 696 516 9* 45,0* 696 572 18,0 696 512 7 35,0 696 516 4 45,0 696 516 8 * cu rola de afisare * fara rola de afisare 19,5 696 511 8 35,0 696 517 2 46,0* 696 517 9 reglabila 22,0 696 511 5 54,0* 696 516 0 24,0 696 576 696 512 9 55,0 696 512 3 28,0 696 516 3 58,0* 696 597 32,0 696 511 4 80,0 696 517 1 32,0 696 519 1 85,0 696 581 32,0 696 514 7 85,0 696 512 5 36,0 696 579 110,0 696 519 4 40,0 696 511 0 696 514 4 * cu rola de afisare 40,0 696 515 6 45,0 696 515 4 52,0 696 515 3 60,0 696 510 1 60,0 696 510 7 696 514 6 60,0 696 515 7 70,0 696 515 5 95,0 696 511 1 Cutite pentru desprins geamurile U.A. -
Glazing at Tokyo Motor Show ’95
Automotive glass Glazing at Tokyo Motor Show ’95 The principle trends of Japanese auto manufacturers for colour, aerodynamic shape, safety, driver visibility and innovations designed in collaboration with glass manufacturers are the focus of this article. The author has made comparisons with European trends and points out differences which lead to competitive solutions. Giovanni Manfrè* MG CONSULT general view of the Tokyo Mo- tor Show ’95, held 25 October to 11 November, confirmed that Fig. 1 JapaneseA auto makers have shifted interest from Mitsubishi’s luxury cars to sporty utility vehicles, minivans “Gaus” on and station wagons. “Down-to-earth” models re- show in Tokyo flected the impact of the decrease in Japanese auto production, and that Japanese auto manufacturers are now following western glazing designs to in- crease market potential of new vehicles. Based on the shapes and colours seen at the show, it was ev- ident that Japanese auto makers were projecting a “touch of happiness” image. Consequently, glass manufacturers will benefit 92 Glass-Technology International 3/1996 from the new trend of auto makers for modular blind spots, anti-glare, micro camera applica- car glazing, transparent pavilions, flushing and tion, the mirror as a monitor for new display wrapping aerodynamic shapes, and colours on signals, the mirror as an extensive depth dis- Fig. 2 windows. Longer side play, water-repellent, and anti-reflective surfac- windows, es; Cooperation between auto and new mirror - transparent plastics: these are currently used in position, projector lenses and demonstrate that with ease glass manufacturers front volets of shaping, the face of any vehicle can be An analysis of the show leads to the conclusion on Toyota’s changed. -
Announcement on the 50Th Anniversary for “Tomica” to Be Celebrated in 2020
For Immediate Release February 26, 2020 [Revised version 1: Event information changed] March 19, 2020 [Revised version 2: Event information changed] March 27, 2020 [Revised version 3: Event information changed] May 15, 2020 [Revised version 4: Event information changed] July 3, 2020 [Revised version 5: Event information changed] January 15, 2020 A total of more than 670 million cars sold! Miniature cars, one of which is sold every two second! (*1) Announcement on the 50th anniversary for “Tomica” to be celebrated in 2020 ■Commemorative project: collaborative project with carmakers ■Events: Fan Appreciation Festival for Tomica 50th Anniversary ■Animation: A Tomica animation adaptation has been decided! TOMY Company, Ltd. “Tomica” die-cast miniature cars that have been sold by TOMY Company, Ltd. (Representative Director, President & COO: Kazuhiro Kojima, headquarters: Katsushika-ku, Tokyo) since 1970 mark the 50th anniversary this year 2020. The 50th anniversary’s key message is “Cool, at all times.” TOMY Company will deliver the stylishness of “Tomica” that never loses luster, together with our thanks, to everyone who has played with “Tomica.” This year, which will be the 50th anniversary, TOMY Company plans to hold user- participation events, release commemorative products, develop a media mix in line with an animation adaptation, collaborate with a variety of other industries and so on, to boost “Tomica” even further. Cool, at all times Key visual for 50th anniversary for “Tomica” “Tomica 50th anniversary celebration” [1] Commemorative -
European Commission Adopts New Car Block Exemption
Japan Automobile Manufacturers Newsfrom Association, Inc. European Edition VOLUME 12 N° 6 JULY/AUGUST 2002 JAMA Update European Commission adopts new JAMA Update European Commission adopts Car Block Exemption new Car Block Exemption Topic Japanese Automobile Manufacturers continue to reduce CO2 emissions in 2001 Newsbrief JAMA Reception Topic II he European Commission adopted on 17 July its plans to reform the Block Exemption for motor vehicles, due to expire 2002 International Car Tat the end of September 2002. The Japanese car industry is Recycling Workshop pleased that the Block Exemption Regulation has been renewed, since the principle of selective distribution is critical to ensure high quality service to consumers. Japanese car manufacturers will operate Essay within the new framework to ensure that the competitive market that already exists within the European Union will continue to work What’s in a name? in the consumers’ interests. JAMA pleased that the Block Exemption Regulation has been renewed In general, JAMA views the new regulation as a well-balanced doc- NEWS FROM JAMA ument, which clearly reflects the broad consultations that the Commission carried out with all major stakeholders in the last cou- BY E-MAIL ple of years. For further information: [email protected] JAMA appreciates that the Commission has agreed that the car industry must be able to require all sales outlets to maintain the prevailing qualitative standards in each geographic area. JAMA members believe that the adherence to ever-higher qualitative standards is essential to Motor vehicles statistics for building brand image, and have consistently called for provisions in Japan are available at: the new regime to ensure that this essential factor of competition is www.jama.or.jp/e_press/index.html protected for the future. -
About This Report
2016 SOCIAL RESPONSIBILITY REPORT OF NISSAN’S SUBSIDIARIES IN CHINA 01 About This Report Period Covered Reference Standards From January 1 to December 31, 2015. In order to improve data This Report is prepared based on the GRI G4 Sustainability Reporting Guidelines comparability, part of contents is beyond this period. and by referring to Chinese standards and international standards. Organizational Scope Reliability Assurance This Report covers Nissan (China) Investment Co., Ltd. (hereinafter referred Nissan’s subsidiaries in China ensure that the materials related to this Report are to as “NCIC”), Nissan’s wholly-owned subsidiary in China; Dongfeng Motor authentic and reliable and that no false record, major omission or misleading Co., Ltd. (hereinafter referred to as “DFL”), Nissan’s joint venture in China, and statement is contained herein. Dongfeng Nissan Passenger Vehicle Company (hereinafter referred to as “DFL-PV”), DFL’s subsidiary in charge of the passenger vehicle business; Availability Zhengzhou Nissan Automobile Co., Ltd. (hereinafter referred to as “ZNA”), This Report is available for download on the official website of NCIC. also a joint venture of Nissan; and Dongfeng Infiniti Motor Co., Ltd. Website: http://www.nissan.com.cn/csr/china/china/psd.php (hereinafter referred to as DFI), a wholly-owned subsidiary of DFL. In this Report, “Nissan’s subsidiaries in China” refer to the companies above in general, and “Nissan” refers to Nissan Motor Corporation. Click here to visit the website to download this Report Reporting Cycle Download As an annual report, this Report is the third social responsibility report released by Nissan Motor Corporation in China. -
Project Figaro Part One Back to the Future
OUR CARS PROJECT FIGARO PROJECT FIGARO PART ONE BACK TO THE FUTURE Simon Goldsworthy waits nearly 30 years to get a car that was first shown under a banner that claimed it was ‘Back to the Future.’ And no it is not a Delorean, but the quite remarkable Figaro from a most unlikely manufacturer – Nissan. t is odd how some marques turn out drive or to look at, not to mention having However, before I get onto the main model after model that is taken to heart a body that rusted with the best of them. event, perhaps I should fill in a little of the Iby enthusiasts and rapidly gains cult and They were essentially cars that you bought background to Nissan and Datsun because classic status, whereas others rarely seem with your head rather than your heart. we don’t cover the marques too often, and to crack the emotive nut. I have to say that Like any sweeping statement, that any readers under the age of 30 may be for many years Nissan fell into the latter description may seem appealing enough on wondering what the Datsun name has to category, but that has little to do with the surface but it really does not bear up to do with them and their Nissan Juke. The the quality of their products and plenty close scrutiny. I’ve already mentioned the thing is that Nissan can trace its automotive to do with the market in which they have 240Z and Skylines, but the company also manufacturing roots to a car that was traditionally operated. -
Nissan L Engine - Wikipedia, the Free Encyclopedia Стр
Nissan L engine - Wikipedia, the free encyclopedia Стр. 1 Nissan L engine From Wikipedia, the free encyclopedia The Nissan L series of automobile engines ranged from 1.3 L to 2.8 L in both straight-4 and straight-6 configurations and were produced from 1967 through 1986. This was the engine of the Datsun 240Z sports car as well as the Datsun 510 and the first Nissan Maxima. These engines are known for their reliability, durability, and parts interchangeability. It is a 2-valve per cylinder SOHC non-crossflow engine, with an iron block and an aluminium head. The four cylinder L series engines were replaced with the Z series and later the CA series, while the six cylinder L series engines were replaced with the VG series and RB series. The design is often incorrectly attributed to Mercedes-Benz. In 1966 Prince Motor Company merged with Nissan. At the time of the merger, Prince was licensed to produce copies of the four and six-cylinder engines. Prince Motor Company later refined the design such that it no longer needed licensing. The engine still resembles a Mercedes in many ways, particularly the valve train. Contents 1 Straight-4 1.1 L13 1.2 L14 1.3 L16 1.4 L16S 1.5 L16T 1.6 L16P 1.7 L18 1.8 L18S 1.9 L18T 1.10 L18P 1.11 L20B 1.12 L22 1.13 LZ (competition) 1.14 LD20/LD20T 2 Straight-6 2.1 L20/L20A 2.2 L20ET 2.3 L20P 2.4 L23 2.5 L24 2.6 L24E 2.7 L26 2.8 L28 2.9 L28E 2.10 L28ET 2.11 LD28 2.12 L2.9 ~ 3.2 3 See also 4 References 5 External links Straight-4 L13 The L13 appeared in 1967, but was not available in the United States. -
For Rubber and Clips
Illustrated Guide for Rubber and Clips 2014 Contents Screen Seal Windscreen or Glazing Seals—Group 1 6 Windscreen or Glazing Seals—Group 2 7 Windscreen or Glazing Seals—Group 3 8 Windscreen or Glazing Seals—Group 4 9 Locking Strips Locking Filler Strips—Plastic/Chrome 10 Locking Filler Strips—Rubber 10 Locking Strips—Tool 10 Centre Bar Seals 11 Mylar Joining/Corner Peices 11 T Sections 11 Bailey Channel—Flock Coated Rubber 12 Bailey Channel—Flock Coated Rubber (continued) 13 Bailey Channel—Double Rubber 13 Felt—Channel Lining 13 Rubber Extrusions Rubber Extrusions—Suite Vintage Screen Seals 14 Pinchweld Pinchweld—PVC Black 15 Pinchwel—PVC Coloured 15 Pinchweld—EDPM Rubber Finish 15 Pinchweld and Seal Pinchweld and Seal—PVC Finish 16 Pinchweld and Seal—EDPM 16 Pinchweld—With Flap 16 Pinchweld and Seal—Boot Seal 17 Boot Seals—Ready to Install 18 Self Adhesive Bulb Seal 18 Quarter Vent Seals Quarter Vent Seals 19 Quarter Vent Seals—Radius Bend 19 Rubber Extrusions Rubber Extrusions —Quarter Vent Upright Seals 20 Quarter Vent Seals—Moulded—Front 20 Rubber Extrusions—General Purpose 21 P Section 24 Tank Strap 25 U Channel 25 UnCured—Mounting Rubber 26 Sponge Extrusion Sponge Extrusions—Roof Rail 27 Sponge Extrusions—Door Seal on Body 27 Sponge Extrusions—Door Seal on Door 28 Sponge Extrusions—Boot Seal on Body 29 Sponge Extrusions—Boot Seal on Lid 29 Sponge Extrusions—General Purpose 30 Sponge Extrusions—General Purpose—Square/Rectangle 31 Sponge Extrusions—General Purpose—Round 31 Weather Strips Weatherstrips/Doorbelts—Rubber (Flexible)–length -
3D Cars Models Catalogue (On September 30, 2021)
3D cars models catalogue (on September 30, 2021) Abarth 001 Abarth 205a Vignale berlinetta 1950 AC Shelby Cobra 001 AC Shelby Cobra 427 1965 002 AC Shelby Cobra 289 roadster 1966 003 Shelby Cobra Daytona 1964 004 AC 3000ME 1979 Acura 001 Acura TL 2012 001 ATS GT 2021 002 Acura MDX 2011 003 Acura ZDX 2012 004 Acura NSX 2012 005 Acura RDX 2013 006 Acura RL 2012 007 Acura NSX convertible 2012 008 Acura ILX 2013 009 Acura RLX 2013 010 Acura MDX Concept 2014 011 Acura RSX Type-S 2005 012 Acura TLX Concept 2015 013 Acura Integra 1990 014 Acura MDX 2003 015 Acura Vigor 1991 016 Acura TLX 2014 017 Acura ILX (DE) 2016 018 Acura TL 2007 019 Acura Integra coupe 1991 020 Acura NSX 2016 021 Acura Precision 2016 022 Acura CDX 2016 023 Acura NSX EV 2016 024 Acura TLX A-Spec 2017 025 Acura MDX Sport Hybrid 2017 026 Acura RLX Sport Hybrid SH-AWD 2017 027 Acura MDX Sport Hybrid with HQ interior 2017 028 Acura RLX Sport Hybrid SH-AWD with HQ interior 2017 029 Acura RDX Prototype 2018 030 Acura ILX A-spec 2019 031 Acura MDX 2014 032 Acura MDX RU-spec 2014 033 Acura RDX RU-spec 2014 034 Acura Type-S 2019 035 Acura NSX 1990 036 Acura RDX A-spec 2019 037 Acura ARX-05 DPi 2018 038 Acura RDX 2006 039 Acura MDX A-Spec 2018 040 Acura TLX Type S 2020 041 Acura TLX A-Spec 2020 042 Acura MDX A-Spec US-spec 2021 AD Tramontana 001 AD Tramontana C 2007 Adler 001 Adler Trumpf Junior Sport Roadster 1935 AEC 001 AEC Routemaster RM 1954 002 AEC Routemaster RMC 1954 Aermacchi 001 Aermacchi Chimera 1957 Aeromobil 001 Aeromobil 3.0 2014 Agrale 001 Agrale 10000 Chassis Truck -
Quattro Freni Qf00000096
QUATTRO FRENI QF00000096 ТРИПОИД 27X34 CROSS-REFERENCE: 3972010V10 Характеристики: Применяемость INFINITI EX 37 09.2010 - INFINITI EX 37 10.2008 - INFINITI EX 35 10.2008 - INFINITI EX 25 04.2010 - INFINITI FX 45 Привод на все колеса 01.2003 - 12.2008 INFINITI FX 45 02.2003 - 12.2008 INFINITI FX 35 Привод на все колеса 01.2003 - 12.2008 INFINITI FX 35 AWD 01.2012 - INFINITI FX 35 02.2003 - 12.2008 INFINITI G седан 37 X 10.2008 - INFINITI M (Y51) 37 X 09.2010 - INFINITI M30 Convertible 3.0 01.1990 - 12.1993 INFINITI M30 купе 3.0 01.1989 - 12.1993 INFINITI M35 3.5 X 01.2005 - INFINITI M37 3.7 Allrad 01.2010 - INFINITI Q70 (Y51) 3.7 AWD 10.2013 - INFINITI QX4 3.3 01.1997 - NISSAN 180 SX купе (S13) 2.0 Turbo 04.1991 - 03.1994 NISSAN 180 SX купе (S13) 1.8 Turbo 09.1988 - 06.1992 NISSAN 180 SX купе (S13) 1.8 09.1988 - 06.1992 NISSAN 200 SX (S13) 1.8 09.1988 - 03.1994 NISSAN 200 SX (S14) 2.0 Turbo 04.1994 - 09.1999 NISSAN 200 SX (S14) 2.0 i 16V Turbo 10.1993 - 12.1999 NISSAN 200 SX (S14) 2.0 i 16V 10.1993 - 12.1999 NISSAN 240 SX 2.4 04.1993 - 09.1994 NISSAN 240 SX 2.4 05.1994 - 08.1997 NISSAN AVENIR (W11) 2.0 Turbo 4x4 08.1998 - 12.2005 NISSAN AVENIR (W11) 2.0 4x4 11.1997 - 12.2005 NISSAN BLUEBIRD (U13, U14) 2000 SSS Turbo 2.0 AWD (HNU13) 09.1991 - 01.1996 NISSAN BLUEBIRD SYLPHY I (N16) 1.8 4x4 08.2000 - 07.2002 NISSAN CEDRIC (Y32) 3.0 06.1991 - 10.1997 NISSAN CEDRIC (Y32) 2.8 TD 06.1991 - 10.1995 NISSAN CEDRIC (Y32) 2.0 06.1991 - 02.1996 NISSAN CEDRIC X (Y34) 3.0 05.1999 - 08.2001 NISSAN CEDRIC X (Y34) 2.5 Turbo 4WD 05.1999 - 08.2004 NISSAN CEDRIC