A Topology Optimization Method for Structural Designs Reliant on Contact Phenomena
Total Page:16
File Type:pdf, Size:1020Kb
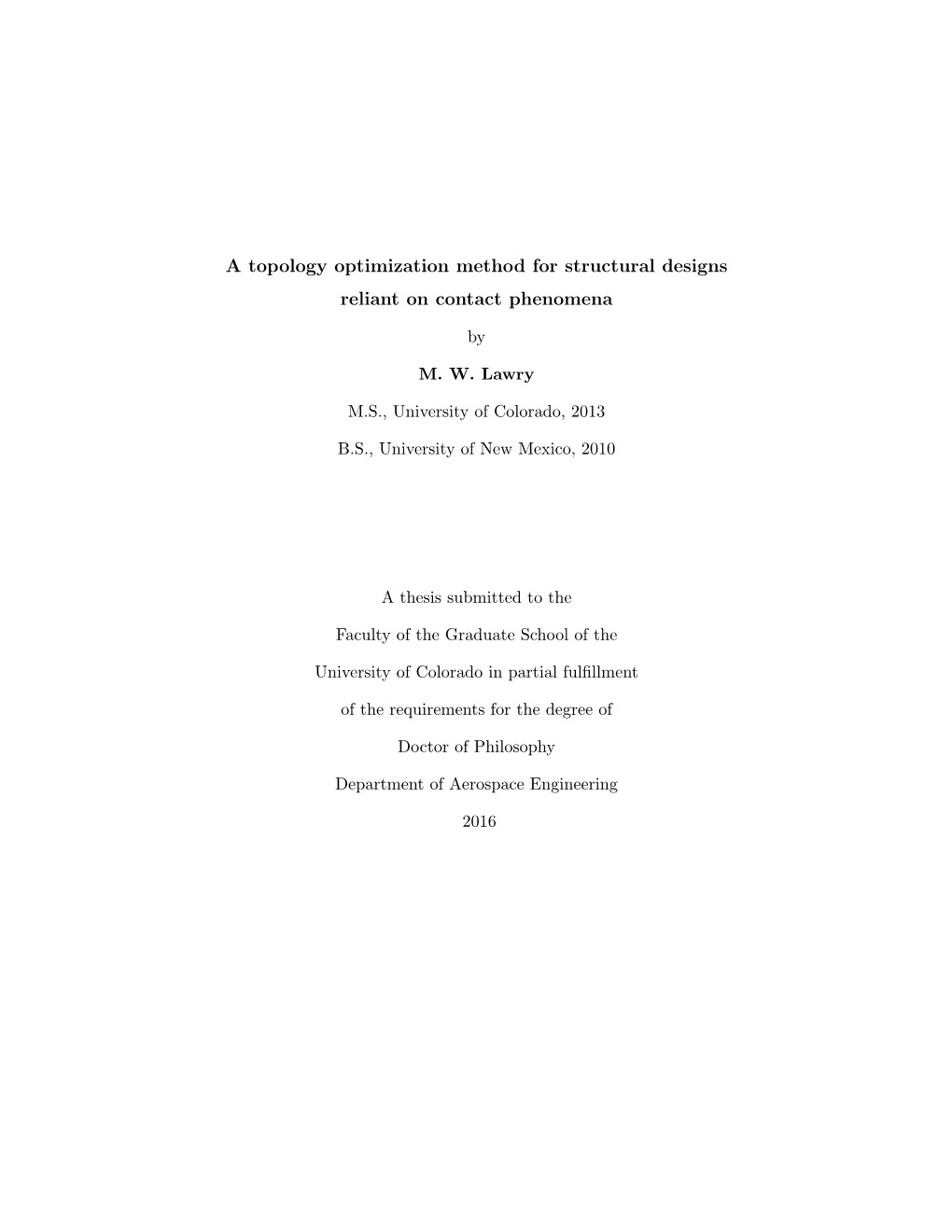
Load more
Recommended publications
-
Topology Optimization of Non-Linear, Dissipative Structures and Materials
Topology optimization of non-linear, dissipative structures and materials Ivarsson, Niklas 2020 Document Version: Publisher's PDF, also known as Version of record Link to publication Citation for published version (APA): Ivarsson, N. (2020). Topology optimization of non-linear, dissipative structures and materials. Division of solid mechanics, Lund University. Total number of authors: 1 General rights Unless other specific re-use rights are stated the following general rights apply: Copyright and moral rights for the publications made accessible in the public portal are retained by the authors and/or other copyright owners and it is a condition of accessing publications that users recognise and abide by the legal requirements associated with these rights. • Users may download and print one copy of any publication from the public portal for the purpose of private study or research. • You may not further distribute the material or use it for any profit-making activity or commercial gain • You may freely distribute the URL identifying the publication in the public portal Read more about Creative commons licenses: https://creativecommons.org/licenses/ Take down policy If you believe that this document breaches copyright please contact us providing details, and we will remove access to the work immediately and investigate your claim. LUND UNIVERSITY PO Box 117 221 00 Lund +46 46-222 00 00 TOPOLOGY OPTIMIZATION OF NON-LINEAR, DISSIPATIVE STRUCTURES AND MATERIALS niklas ivarsson Solid Doctoral Thesis Mechanics Department of Construction Sciences -
Introduction to FINITE STRAIN THEORY for CONTINUUM ELASTO
RED BOX RULES ARE FOR PROOF STAGE ONLY. DELETE BEFORE FINAL PRINTING. WILEY SERIES IN COMPUTATIONAL MECHANICS HASHIGUCHI WILEY SERIES IN COMPUTATIONAL MECHANICS YAMAKAWA Introduction to for to Introduction FINITE STRAIN THEORY for CONTINUUM ELASTO-PLASTICITY CONTINUUM ELASTO-PLASTICITY KOICHI HASHIGUCHI, Kyushu University, Japan Introduction to YUKI YAMAKAWA, Tohoku University, Japan Elasto-plastic deformation is frequently observed in machines and structures, hence its prediction is an important consideration at the design stage. Elasto-plasticity theories will FINITE STRAIN THEORY be increasingly required in the future in response to the development of new and improved industrial technologies. Although various books for elasto-plasticity have been published to date, they focus on infi nitesimal elasto-plastic deformation theory. However, modern computational THEORY STRAIN FINITE for CONTINUUM techniques employ an advanced approach to solve problems in this fi eld and much research has taken place in recent years into fi nite strain elasto-plasticity. This book describes this approach and aims to improve mechanical design techniques in mechanical, civil, structural and aeronautical engineering through the accurate analysis of fi nite elasto-plastic deformation. ELASTO-PLASTICITY Introduction to Finite Strain Theory for Continuum Elasto-Plasticity presents introductory explanations that can be easily understood by readers with only a basic knowledge of elasto-plasticity, showing physical backgrounds of concepts in detail and derivation processes -
Likely Striping in Stochastic Nematic Elastomers
Likely striping in stochastic nematic elastomers L. Angela Mihai∗ Alain Gorielyy March 17, 2020 Abstract For monodomain nematic elastomers, we construct generalised elastic-nematic constitutive mod- els combining purely elastic and neoclassical-type strain-energy densities. Inspired by recent devel- opments in stochastic elasticity, we extend these models to stochastic-elastic-nematic forms where the model parameters are defined by spatially-independent probability density functions at a con- tinuum level. To investigate the behaviour of these systems and demonstrate the effects of the probabilistic parameters, we focus on the classical problem of shear striping in a stretched nematic elastomer for which the solution is given explicitly. We find that, unlike in the neoclassical case where the inhomogeneous deformation occurs within a universal interval that is independent of the elastic modulus, for the elastic-nematic models, the critical interval depends on the material parameters. For the stochastic extension, the bounds of this interval are probabilistic, and the homogeneous and inhomogeneous states compete in the sense that both have a a given probability to occur. We refer to the inhomogeneous pattern within this interval as `likely striping'. Key words: liquid crystal elastomers, solid mechanics, finite deformation, stochastic parameters, instabilities, probabilities. \Instead of stating the positions and velocities of all the molecules, we allow the possibility that these may vary for some reason - be it because we lack precise information, be it because we wish only some average in time or in space, be it because we are content to represent the result of averaging over many repetitions [...] We can then assign a probability to each quantity and calculate the values expected according to that probability." - C. -
Introduction to Computational Contact Mechanics a Geometrical Approach
INTRODUCTION TO COMPUTATIONAL CONTACT MECHANICS WILEY SERIES IN COMPUTATIONAL MECHANICS Series Advisors: René de Borst Perumal Nithiarasu Tayfun E. Tezduyar Genki Yagawa Tarek Zohdi Introduction to Computational Contact Konyukhov April 2015 Mechanics: A Geometrical Approach Extended Finite Element Method: Khoei December 2014 Theory and Applications Computational Fluid-Structure Bazilevs, Takizawa January 2013 Interaction: Methods and Applications and Tezduyar Introduction to Finite Strain Theory for Hashiguchi and November 2012 Continuum Elasto-Plasticity Yamakawa Nonlinear Finite Element Analysis of De Borst, Crisfield, August 2012 Solids and Structures, Second Edition Remmers and Verhoosel An Introduction to Mathematical Oden November 2011 Modeling: A Course in Mechanics Computational Mechanics of Munjiza, Knight and November 2011 Discontinua Rougier Introduction to Finite Element SzaboandBabu´ skaˇ March 2011 Analysis: Formulation, Verification and Validation INTRODUCTION TO COMPUTATIONAL CONTACT MECHANICS A GEOMETRICAL APPROACH Alexander Konyukhov Karlsruhe Institute of Technology (KIT), Germany Ridvan Izi Karlsruhe Institute of Technology (KIT), Germany This edition first published 2015 © 2015 John Wiley & Sons Ltd Registered office John Wiley & Sons Ltd, The Atrium, Southern Gate, Chichester, West Sussex, PO19 8SQ, United Kingdom For details of our global editorial offices, for customer services and for information about how to apply for permission to reuse the copyright material in this book please see our website at www.wiley.com. The right of the author to be identified as the author of this work has been asserted in accordance with the Copyright, Designs and Patents Act 1988. All rights reserved. No part of this publication may be reproduced, stored in a retrieval system, or transmitted, in any form or by any means, electronic, mechanical, photocopying, recording or otherwise, except as permitted by the UK Copyright, Designs and Patents Act 1988, without the prior permission of the publisher. -
Topology Optimization for Designing Periodic Microstructures Based on finite Strain Viscoplasticity
Structural and Multidisciplinary Optimization (2020) 61:2501–2521 https://doi.org/10.1007/s00158-020-02555-x RESEARCH PAPER Topology optimization for designing periodic microstructures based on finite strain viscoplasticity Niklas Ivarsson1 · Mathias Wallin1 · Daniel A. Tortorelli2 Received: 15 September 2019 / Revised: 20 February 2020 / Accepted: 21 February 2020 / Published online: 28 May 2020 © The Author(s) 2020 Abstract This paper presents a topology optimization framework for designing periodic viscoplastic microstructures under finite deformation. To demonstrate the framework, microstructures with tailored macroscopic mechanical properties, e.g., maximum viscoplastic energy absorption and prescribed zero contraction, are designed. The simulated macroscopic properties are obtained via homogenization wherein the unit cell constitutive model is based on finite strain isotropic hardening viscoplasticity. To solve the coupled equilibrium and constitutive equations, a nested Newton method is used together with an adaptive time-stepping scheme. A well-posed topology optimization problem is formulated by restriction using filtration which is implemented via a periodic version of the Helmholtz partial differential equation filter. The optimization problem is iteratively solved with the method of moving asymptotes, where the path-dependent sensitivities are derived using the adjoint method. The applicability of the framework is demonstrated by optimizing several two-dimensional continuum composites exposed to a wide range of macroscopic strains. Keywords Topology optimization · Material design · Finite strain · Rate-dependent plasticity · Discrete adjoint sensitivity analysis 1 Introduction composite materials with enhanced properties, by optimiz- ing the material microstructure. Examples of these include Topology optimization is a powerful tool that enables engi- linear elastic materials with negative Poisson’s ratio (Sig- neers to enhance structural performance. -
LETTER Finite-Strain Analysis of Relative Compressibilities
American Mineralogist, Volume 76, pages 1765-1768, 1991 LETTER Finite-strain analysis of relative compressibilities:Application to the high-pressure wadsleyitephase as an illustration Rq,vN{oNo JuNr,oz Department of Geology and Geophysics,University of California, Berkeley,California 94720, U.S.A. Ronnnr M. HIzBN GeophysicalLaboratory and Center for High PressureResearch, Carnegie Institution of Washington, 5251 Broad BranchRoad NW, Washington,DC 20015-1305,U.S.A. Ansrnl,cr Finite-strain analysisof recentlypublished hydrostaticcompression measurements shows that the isothermal bulk modulus of B-(Mg,Fe)rSiOowadsleyite is independent of com- position [.00 > M/(Mg * Fe) > 0.75] within +2.5o/o.The averagebulk modulus over this compositionrange, Kor : l7 1.0 (+ 0.6) GPa, agreeswell with the value of 172.5(+ 1.0) GPa obtained by Brillouin scattering.This offers a significant crosscheckbetween the elastic moduli determined by independentmethods on an important mineral phaseof the Earth's mantle. fNtnonucrroN DrscussroN The application of single-crystalX-ray diffraction tech- The Taylor expansionof enthalpy in the Eulerian mea- - niques to several specimensthat are being compressed sure of finite strain,/: l(y/VJ-2/3 ll/2, resultsin the within a single,hydrostatic pressurechamber offersa pre- isothermal equation of state, or pressure-volume(P- Z) cise method for determining the relative compressibilities relation of different crystals(Hazen, I 9 8 I Hazen and Finger, I 982; ; P -- 3Korft + zf)'zs(r + af + .. .) (l) McCormick et al., 1989;Hazen et al., 1990).In this way, it is possibleto resolve the effectson the equation of state in which Ko, is the bulk modulus and a : 3(K'o, - 4)/2 of varying composition, nonstoichiometry, site disorder- (Birch, 1952, 1978).Here, subscriptszero and Zdenote ing, or other subtle factors. -
Topology Optimization of Nonlinear Periodically Microstructured
Composite Structures 266 (2021) 113729 Contents lists available at ScienceDirect Composite Structures journal homepage: www.elsevier.com/locate/compstruct Topology optimization of nonlinear periodically microstructured materials for tailored homogenized constitutive properties ⇑ Reza Behrou a, , Maroun Abi Ghanem a, Brianna C. Macnider a, Vimarsh Verma a, Ryan Alvey a, Jinho Hong a, Ashley F. Emery b, Hyunsun Alicia Kim c, Nicholas Boechler a a Department of Mechanical and Aerospace Engineering, University of California San Diego, La Jolla, CA, USA b Department of Mechanical Engineering, University of Washington, Seattle, WA, USA c Department of Structural Engineering, University of California San Diego, La Jolla, CA, USA ARTICLE INFO ABSTRACT Keywords: A topology optimization method is presented for the design of periodic microstructured materials with pre- Topology optimization scribed homogenized nonlinear constitutive properties over finite strain ranges. Building upon an existing com- Nonlinear homogenization putational homogenization method for periodic materials undergoing finite strain, generalized sensitivity Finite strain equations are derived for the gradient‐based topology optimization of periodic unit cells that account for Materials design the nonlinear homogenized response of the unit cell. The mechanical model assumes linear elastic isotropic Periodic microstructure materials, geometric nonlinearity at finite strain, and a quasi‐static response. The optimization problem is Tailored constitutive properties solved by a nonlinear -
Ch.2. Deformation and Strain
CH.2. DEFORMATION AND STRAIN Multimedia Course on Continuum Mechanics Overview Introduction Lecture 1 Deformation Gradient Tensor Material Deformation Gradient Tensor Lecture 2 Lecture 3 Inverse (Spatial) Deformation Gradient Tensor Displacements Lecture 4 Displacement Gradient Tensors Strain Tensors Green-Lagrange or Material Strain Tensor Lecture 5 Euler-Almansi or Spatial Strain Tensor Variation of Distances Stretch Lecture 6 Unit elongation Variation of Angles Lecture 7 2 Overview (cont’d) Physical interpretation of the Strain Tensors Lecture 8 Material Strain Tensor, E Spatial Strain Tensor, e Lecture 9 Polar Decomposition Lecture 10 Volume Variation Lecture 11 Area Variation Lecture 12 Volumetric Strain Lecture 13 Infinitesimal Strain Infinitesimal Strain Theory Strain Tensors Stretch and Unit Elongation Lecture 14 Physical Interpretation of Infinitesimal Strains Engineering Strains Variation of Angles 3 Overview (cont’d) Infinitesimal Strain (cont’d) Polar Decomposition Lecture 15 Volumetric Strain Strain Rate Spatial Velocity Gradient Tensor Lecture 16 Strain Rate Tensor and Rotation Rate Tensor or Spin Tensor Physical Interpretation of the Tensors Material Derivatives Lecture 17 Other Coordinate Systems Cylindrical Coordinates Lecture 18 Spherical Coordinates 4 2.1 Introduction Ch.2. Deformation and Strain 5 Deformation Deformation: transformation of a body from a reference configuration to a current configuration. Focus on the relative movement of a given particle w.r.t. the particles in its neighbourhood (at differential level). It includes changes of size and shape. 6 2.2 Deformation Gradient Tensors Ch.2. Deformation and Strain 7 Continuous Medium in Movement Ω0: non-deformed (or reference) Ω or Ωt: deformed (or present) configuration, at reference time t0. configuration, at present time t. -
A Brief Review of Elasticity and Viscoelasticity for Solids 1
Advances in Applied Mathematics and Mechanics DOI: 10.4208/aamm.10-m1030 Adv. Appl. Math. Mech., Vol. 3, No. 1, pp. 1-51 February 2011 REVIEW ARTICLE A Brief Review of Elasticity and Viscoelasticity for Solids ∗ Harvey Thomas Banks 1, , Shuhua Hu 1 and Zackary R. Kenz 1 1 Center for Research in Scientific Computation and Department of Mathematics, North Carolina State University, Raleigh, NC 27695-8212, USA Received 25 May 2010; Accepted (in revised version) 31 August 2010 Available online 15 October 2010 Abstract. There are a number of interesting applications where modeling elastic and/or viscoelastic materials is fundamental, including uses in civil engineering, the food industry, land mine detection and ultrasonic imaging. Here we provide an overview of the subject for both elastic and viscoelastic materials in order to understand the behavior of these materials. We begin with a brief introduction of some basic terminology and relationships in continuum mechanics, and a review of equations of motion in a continuum in both Lagrangian and Eulerian forms. To complete the set of equations, we then proceed to present and discuss a number of specific forms for the constitutive relationships between stress and strain pro- posed in the literature for both elastic and viscoelastic materials. In addition, we discuss some applications for these constitutive equations. Finally, we give a com- putational example describing the motion of soil experiencing dynamic loading by incorporating a specific form of constitutive equation into the equation of motion. AMS subject classifications: 93A30, 74B05, 74B20, 74D05, 74D10 Key words: Mathematical modeling, Eulerian and Lagrangian formulations in continuum me- chanics, elasticity, viscoelasticity, computational simulations in soil, constitutive relationships. -
A Finite Element Method Model for Large Strains Analysis of Timber a Finite Element Method Model for Large Strains Analysis of Timber Vincenzo De Luca
Chapter 3 Provisional chapter A Finite Element Method Model for Large Strains Analysis of Timber A Finite Element Method Model for Large Strains Analysis of Timber Vincenzo De Luca AdditionalVincenzo information De Luca is available at the end of the chapter Additional information is available at the end of the chapter http://dx.doi.org/10.5772/67184 Abstract In this report a Finite Element Method (FEM) model, within the continuum mechanics of solids, for mechanical long term response of timber structures is presented. The pro- posed model can analyze three-dimensional solids, within the theory for non-linear material orthotropic elastic-viscous-plastic. It can account ductile behaviour in compres- sion and brittle behaviour in tension, under the kinematics hypothesis of large displace- ments and large strains. The work has been carried out with a general purpose FEM software code in which a specific stress-strain law for wood, by a proper subroutine, has been built in. The constitutive equations have been formulated by a multi-surface yield approach of viscoplasticity, each yield surface acts separately each other. This approach is specifically almost necessary for some problems, such as glued composite parts or steel bolt connections. Specialized solution algorithms, which adopt time-stepping and automating relaxation techniques, have been used to handle the behaviour of the load- ing path response for elastic-viscous-plastic or elastic-brittle behaviours. The model has been applied to examples to test the effectiveness of the suggested approach. The results obtained have shown the potentiality of the proposed model to effectively simulate the overall mechanical behaviour of timber. -
Development of a Procedure for Experimental Measurement of Shear Energy Intensity in Tire Contact Patch
DEVELOPMENT OF A PROCEDURE FOR EXPERIMENTAL MEASUREMENT OF SHEAR ENERGY INTENSITY IN TIRE CONTACT PATCH by Piyush Mohan Gulve A thesis submitted to the faculty of The University of North Carolina at Charlotte in partial fulfillment of the requirements for the degree of Master of Science in Mechanical Engineering Charlotte 2017 Approved by: ______________________________ Dr. Peter Tkacik ______________________________ Dr. Russel Keanini ______________________________ Dr. Saiful Bari © 2017 Piyush Mohan Gulve ALL RIGHTS RESERVED ii ABSTRACT PIYUSH GULVE. Development of A Procedure For Experimental Measurement Of Shear Energy Intensity In Tire Contact Patch. Under the direction of Dr. PETER TKACIK. Energy dissipated in the contact patch of a rolling tire is related to material abrasion and tire wear. In this study, we calculate the shear energy intensity as the product of the sliding distance and the shear stresses as measured in the tread block sliding deformations and normal load distribution at contact patch for a collection of low profile tires. The objective of the study is to develop a procedure to find pressure distribution in contact patch, tread displacement during rolling and shear energy intensity on low profile tire footprint. Studying shear energy intensity in contact patch of rolling tire will help in better understanding of tire wear. Shear energy is product of shear stresses and displacement. A new experimental optical method based on Total Internal Reflection was developed to get displacements in a contact patch of a tire. Another new experimental optical method based on Frustrated Total Internal Reflection was developed to get normal stresses in a contact patch of a tire. -
Level Set Shape and Topology Optimization of Finite Strain
Level set shape and topology optimization of finite strain bilateral contact problems Matthew Lawry, and Kurt Maute Department of Aerospace Engineering, University of Colorado Boulder, Boulder, CO 80309-0429, USA September 04, 2016 Abstract This paper presents a method for the optimization of multi-component structures comprised of two and three materials considering large motion sliding contact and separation along interfaces. The structural geometry is defined by an explicit level set method, which allows for both shape and topology changes. The mechanical model assumes finite strains, a nonlinear elastic material behavior, and a quasi-static response. Identification of overlapping surface position is handled by a coupled parametric representation of contact surfaces. A stabilized Lagrange method and an active set strategy are used to model frictionless contact and separation. The mechanical model is discretized by the extended finite element method which maintains a clear definition of geometry. Face-oriented ghost penalization and dynamic relaxation are implemented to improve the stability of the physical response prediction. A nonlinear programming scheme is used to solve the optimization problem, which is regularized by introducing a perimeter penalty into the objective function. Sensitivities are determined by the adjoint method. The main characteristics of the proposed method are studied by numerical examples in two dimensions. The numerical results demonstrate improved design performance when compared to models optimized with a small strain assumption. Additionally, examples with load path dependent objectives display non-intuitive designs. 1 Introduction Sliding contact phenomena between deformable structures play a crucial role in the functionality of many mechanical systems in commercial and industrial applications.