Development of a Cryogen-Free Compact 3 T Superconducting Magnet for an Electromagnetic Property Measurement System
Total Page:16
File Type:pdf, Size:1020Kb
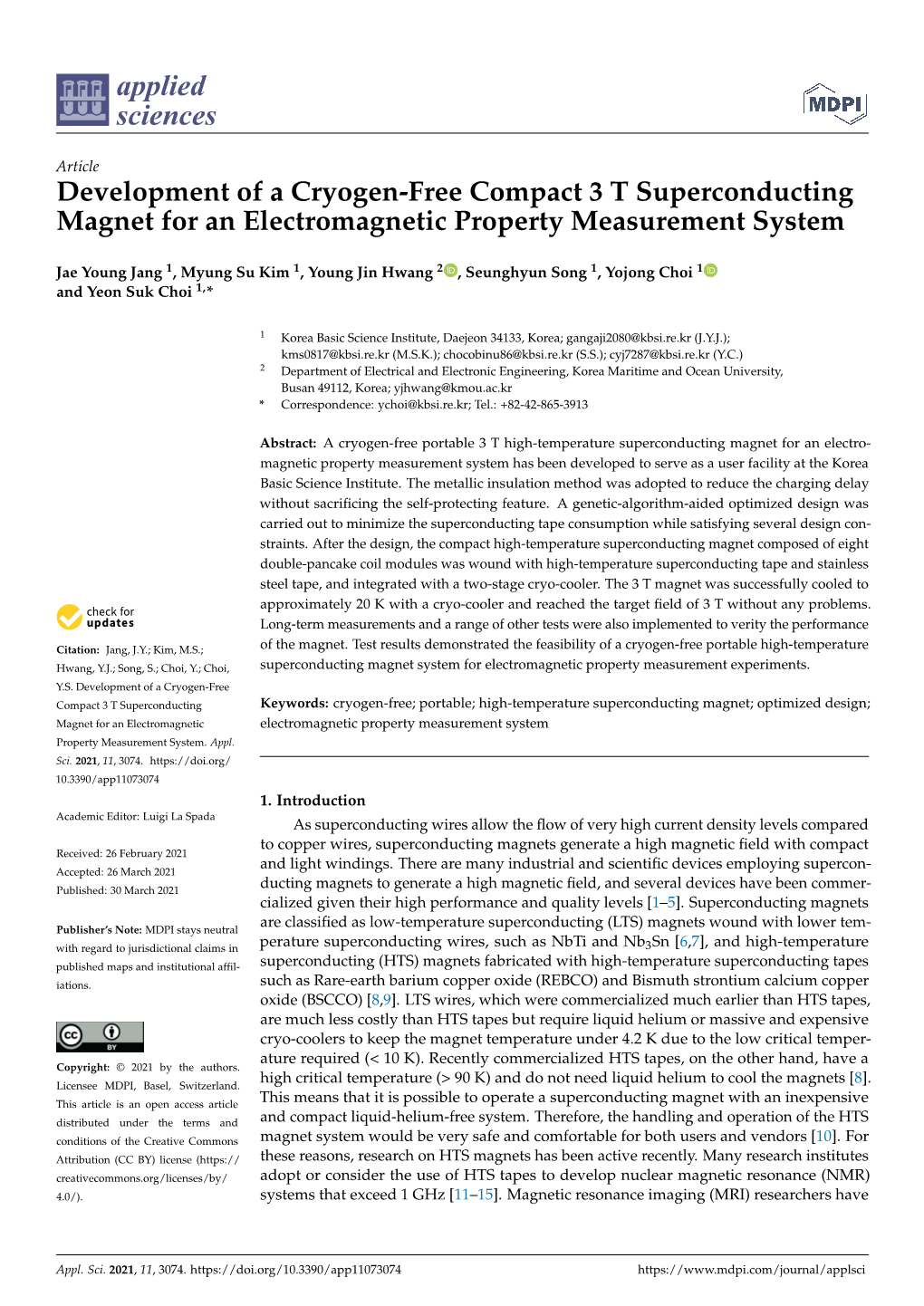
Load more
Recommended publications
-
Applications of High Temperature Superconductors
FEATURES Applications of high temperature superconductors T.M. Silver, s.x. Dou and J.x. fin Institute for Superconducting and Electronic Materials, University ofWollongong, Wollongong, NSW2522, Australia ost ofus are familiar with the basic idea ofsuperconductivi magnetic separators, these losses may account for most of the M ty, thata superconductor can carrya currentindefinitely in a energy consumed in the device. Early prototypes for motors, closed loop, without resistance and with no voltage appearing. In transmission lines and energy storage magnets were developed, a normal metal, such as copper, the free electrons act indepen but they were never widely accepted. There were important rea dently. They will move under the influence of a voltage to form a sons for this, apart from the tremendous investment in existing current, but are scattered off defects and impurities in the metal. technology. In most superconducting metals andalloys the super This scattering results in energy losses and constitutes resistance. conductivity tends to fail in self-generated magnetic fields when In a superconducting metal, such as niobium, resistance does not the current densities through them are increased to practicallev occur, because under the right conditions the electrons no longer els. A second problem was the cost and complexity of operating act as individuals, but merge into a collective entity that is too refrigeration equipment near liquid helium temperatures large to 'see' any imperfections. This collective entity, often (4 K, -269°C). Removing one watt of heat generated at 4 K described as a Bose condensate, can be described by a single demands about 1000 W ofrefrigeration power at room tempera macroscopic quantum mechanical wave function. -
Hitachi's Leading Superconducting Technologies
Hitachi’s Leading Superconducting Technologies 290 Hitachi’s Leading Superconducting Technologies Shohei Suzuki OVERVIEW: Over 30 years have passed since Hitachi began researching Ryoichi Shiobara superconductors and superconducting magnets. Its scope of activities now encompasses everything from magnetically levitated vehicles and nuclear Kazutoshi Higashiyama fusion equipment to AC generators. Three big projects that use Hitachi Fumio Suzuki superconductors are currently underway in Japan: the Yamanashi Maglev Test Line, the Large Helical Device (LHD) for nuclear fusion and the 70- MW model of superconducting power generator. Hitachi has played a vital role in these projects with its materials and application technologies. In the field of high-temperature superconducting materials, Hitachi has made a lot of progress and has set a new world record for magnetic fields. INTRODUCTION is cryogenic stability because of the extremely low HITACHI started developing superconducting temperatures, but we have almost solved this problem technology in the late 1950’s. At first, it focused on by developing fine multiple-filament superconductors superconducting magnets for magneto-hydro- and various materials for stabilization matrixes, both dynamics (MHD) power generators, but eventually of which operate at liquid helium temperature (4 K), broadened its research to applications such as as well as superconductor integration technology and magnetically levitated vehicles, nuclear fusion precise winding technology. These new developments equipment, and high energy physics. Recently have led to a number of large projects in Japan. They Hitachi’s activities have spread to the medical field are (1) the world’s largest (70 MW) model super- (magnetic-resonance-imaging technology) and other conducting generator for generating electric power, (2) fields (AC power generators and superconducting the Yamanashi Maglev Test Line train, which may magnetic energy storage). -
Design of a Superconducting DC Wind Generator
Design of a superconducting DC wind generator zur Erlangung des akademischen Grades eines DOKTOR-INGENIEURS von der Fakultät für Elektrotechnik und Informationstechnik des Karlsruher Instituts für Technologie (KIT) genehmigte DISSERTATION von M. Eng. Yingzhen Liu geb. in: Hebei, China Tag der mündlichen Prüfung: 26. 01. 2018 Hauptreferent: Prof. Dr.-Ing. Mathias Noe Korreferent: Prof. Dr.-Ing. Martin Doppelbauer Acknowledgement This thesis was written at the Institute for Technical Physics at Karlruhe Institute of Technology and it cannot be finished without the help of my colleugues. I would like to thank my supervisor Prof. Dr.-Ing Mathias Noe, who provides me with the opportunity to pursue my PhD in Karlsruhe Institute of Technology. His continuous support, advice and insight have helped me to reach a higher research level. I highly appreciated the constructive feedback and helpful guaidance given by Prof. Noe at a regular meeting evey two to three weeks during my whole PhD period. In order to ensure the scientific quality of my work, Prof. Noe also encourages me to participate in interna- tional conferences, workshops and seminars, which benefit me a lot. My special gratitude goes to my second referee Prof. Dr.-Ing Martin Doppelbauer for his useful lessons, advice and discussions on electric machines, and the excellent and professional environment he offered to study the iron material properties. Specially, I would like to thank Prof. Doppelbauer for his scientific input and linguistic improve- ments, that helped a great deal to finish the final version of this thesis. I would like to thank my external referee Prof. Jean Lévêque for his scientific and practical comments which help me a lot to improve my thesis. -
Protection of Superconducting Magnet Circuits
Protection of superconducting magnet circuits M. Marchevsky, Lawrence Berkeley National Laboratory M. Marchevsky – USPAS 2017 Outline 1. From superconductor basics to superconducting accelerator magnets 2. Causes and mechanisms of quenching 3. Quench memory and training 4. Detection and localization of quenches 5. Passive quench protection: how to dump magnet energy 6. Active protection: quench heaters and new methods of protection (CLIQ) 7. Protection of a string of magnets. Hardware examples. 8. References and literature M. Marchevsky – USPAS 2017 Discovery of superconductivity H. K. Onnes, Commun. Phys. Lab.12, 120, (1911) M. Marchevsky – USPAS 2017 A first superconducting magnet Lead wire wound coil Using sections of wire soldered together to form a total length of 1.75 meters, a coil consisting of some 300 windings, each with a cross-section of 1/70 mm2, and insulated from one another with silk, was wound around a glass core. Whereas in a straight tin wire the threshold current was 8 A, in the case of the coil, it was just 1 A. Unfortunately, the disastrous effect of a magnetic field on superconductivity was rapidly revealed. Superconductivity disappeared when field Leiden, 1912 reached 60 mT. H. Kamerlingh Onnes, KNAWProceedings 16 II, (1914), 987. Comm. 139f. Reason: Pb is a “type-I superconductor”, where magnetic destroys superconductivity at once at Bc=803 G. Note: this magnet has reached 74% of its “operational margin” ! M. Marchevsky – USPAS 2017 First type-II superconductor magnet 0.7 T field George Yntema, Univ. of Illinois, 1954 • The first successful type-II superconductor magnet was wound with Nb wire It was also noted that “cold worked” Nb wire yielded better results than the annealed one… But why some superconductors work for magnets and some do not? And what it has to do with the conductor fabrication technique? M. -
Superconducting Magnets for Fusion
Magnets and magnetic materials Superconducting magnets for fusion The ITER's mission is to prove that magnetic confinement fusion will be a candidate source of energy by the second half of the twenty-first century. The tokamak, which is scheduled to begin operations in 2016 at the Cadarache site in the Bouches-du-Rhône, represents a key step in the development of a current-generating fusion reactor. ITER Considerable expertise acquired through its partnership with Euratom on the Tore Supra project has led the CEA to play a central role in the Overview of the magnetic design and development of the three field system equipping the ITER reactor. giant superconducting systems that will generate the intense magnetic fields vital to plasma confinement and stabilisation. he magnetic confinement fusion of thermo- magnetic field system comprises three giant super- Tnuclear plasmas requires intense magnetic fields. conducting systems: the toroidal magnetic field sys- The production of these magnetic fields in the large tem (TF), the poloidal magnetic field system (PF), and vacuum chamber (837 m3) of the ITER International the central solenoid (CS); Focus B, Superconductivity Thermonuclear Experimental Reactor, currently being and superconductors, p. 16. It could be said to repre- built at the Cadarache site in the Bouches-du-Rhône sent the backbone of the tokamak (Figure 1). is in itself a major technological challenge. The ITER's Superconductivity for fusion applications Up to the early 1980s, all magnetic confinement machines relied on resistive magnets, which were CS system generally built using silver-doped copper in order to TF system improve their mechanical properties. -
Superconducting Magnets for Accelerators Lecture
Superconductivity for accelerators - why bother? Abolish Ohm's Law • no power consumption (although do need refrigeration power) • high current density compact windings, high gradients • ampere turns are cheap, so don’t need iron (although often use it for shielding) Consequences • lower power bills • higher magnetic fields mean reduced bend radius smaller rings reduced capital cost new technical possibilities (eg muon collider) • higher quadrupole gradients higher luminosity Martin Wilson Lecture 1 slide 1 JUAS February 2013 Plan of the Lectures 1 Introduction to Superconductors 4 Quenching and Cryogenics • critical field, temperature & current • the quench process • superconductors for magnets • resistance growth, current decay, temperature rise • manufacture of superconducting wires • quench protection schemes • high temperature superconductors HTS • cryogenic fluids, refrigeration, cryostat design 2 Magnetization, Cables & AC losses 5 Practical Matters • superconductors in changing fields • filamentary superconductors and magnetization • LHC quench protection • coupling between filaments magnetization • current leads • why cables, coupling in cables • accelerator magnet manufacture • AC losses in changing fields • some superconducting accelerators 3 Magnets, ‘Training’ & Fine Filaments Tutorial 1: Fine Filaments • coil shapes for solenoids, dipoles & quadrupoles • how filament size affects magnetization • engineering current density & load lines Tutorial 2: Quenching • degradation & training minimum quench energy • current decay -
Mechanical Design and Construction of Superconducting E-Lens Solenoid Magnet System for RHIC Head-On Beam-Beam Compensation
1PoCB-08 1 Mechanical Design and Construction of Superconducting e-Lens Solenoid Magnet System for RHIC Head-on Beam-Beam Compensation M. Anerella, W. Fischer, R. Gupta, A. Jain, P. Joshi, P. Kovach, A. Marone, A. Pikin, S. Plate, J. Tuozzolo, P. Wanderer Abstract —Each 2.6-meter long superconducting e-Lens magnet assembly consists of a main solenoid coil and corrector coils mounted concentric to the axis of the solenoid. Fringe field and “anti-fringe field” solenoid coils are also mounted coaxially at each end of the main solenoid. Due to the high magnetic field of 6T large interactive forces are generated in the assembly between and within the various magnetic elements. The central field uniformity requirement of ± 0.50% and the strict field straightness requirement of ± 50 microns over 2.1 meters of length provide additional challenges. The coil construction details to meet the design requirements are presented and discussed. The e-Lens coil assemblies are installed in a pressure vessel cooled to 4.5K in a liquid helium bath. The design of the magnet adequately cools the superconducting coils and the power leads using the available cryogens supplied in the RHIC tunnel. The mechanical design of the magnet structure including thermal considerations is also presented. Index Terms —Accelerator, electron lens, solenoids, superconducting magnets. Fig. 1. Longitudinal section view of e-Lens solenoid II. MAIN SOLENOID DESIGN I. INTRODUCTION The main solenoid design is comprised of eleven “double To increase the polarized proton luminosity in RHIC, a layers” of rectangular monolithic conductor, 1.78 mm wide superconducting electron lens (e-Lens) magnet system is being and 1.14 mm tall, with a 3:1 copper to superconductor ratio. -
Superconductors: the Next Generation of Permanent Magnets
1 Superconductors: The Next Generation of Permanent Magnets T. A. Coombs, Z. Hong, Y. Yan, C. D. Rawlings fault current limiters, bearings and motors. Both fault current Abstract—Magnets made from bulk YBCO are as small and as limiters and bearings are enabling technologies and a great compact as the rare earth magnets but potentially have magnetic deal of successful research has been devoted to these areas[4- flux densities orders of magnitude greater than those of the rare 8]. With motors, though, we are seeking to supplant an earths. In this paper a simple technique is proposed for existing and mature technology. Therefore the advantages of magnetising the superconductors. This technique involves repeatedly applying a small magnetic field which gets trapped in superconductors have to be clearly defined before the superconductor and thus builds up and up. Thus a very small superconducting motors can become widely accepted. magnetic field such as one available from a rare earth magnet The principle advantages of a superconducting motor or can be used to create a very large magnetic field. This technique generator are size, weight and efficiency. Which of these is which is applied using no moving parts is implemented by the most important depends on the application. In a wind generating a travelling magnetic wave which moves across the turbine for example power to weight ratio is paramount. Any superconductor. As it travels across the superconductor it trails flux lines behind it which get caught inside the superconductor. weight in the nacelle has to be supported and considerable With each successive wave more flux lines get caught and the savings can be made if the machine is lighter especially if it field builds up and up. -
Design Considerations of the Superconducting Magnet
1 Electromagnetic, stress and thermal analysis of the Superconducting Magnet 1 1 , 2 Yong Ren *, Xiang Gao * 1 Institute of Plasma Physics, Hefei Institutes of Physical Science, Chinese Academy of Sciences, PO Box 1126, Hefei, Anhui, 230031, People's Republic of China 2University of Science and Technology of China, Hefei, Anhui 230026, People’s Republic of China *E-mail: [email protected] and [email protected] Abstract—Within the framework of the National Special but also to implement a background field superconducting Project for Magnetic Confined Nuclear Fusion Energy of China, magnet for testing the CFETR CS insert and TF insert coils. the design of a superconducting magnet project as a test facility During the first stage, the main goals of the project are of the Nb3Sn coil or NbTi coil for the Chinese Fusion Engineering composed of: 1) to obtain the maximum magnetic field of Test Reactor (CFETR) has been carried out not only to estimate the relevant conductor performance but also to implement a above 12.5 T; 2) to simulate the relevant thermal-hydraulic background magnetic field for CFETR CS insert and toroidal characteristics of the CFETR CS coil; 3) to test the sensitivity field (TF) insert coils. The superconducting magnet is composed of the current sharing temperature to electromagnetic and of two parts: the inner part with Nb3Sn cable-in-conduit thermal cyclic operation. During the second stage, the conductor (CICC) and the outer part with NbTi CICC. Both superconducting magnet was used to test the CFETR CS insert parts are connected in series and powered by a single DC power and TF insert coils as a background magnetic field supply. -
Magnetic Design of Superconducting Magnets
Published by CERN in the Proceedings of the CAS-CERN Accelerator School: Superconductivity for Accelerators, Erice, Italy, 24 April – 4 May 2013, edited by R. Bailey, CERN–2014–005 (CERN, Geneva, 2014) Magnetic Design of Superconducting Magnets E. Todesco1, CERN, Geneva, Switzerland Abstract In this paper we discuss the main principles of magnetic design for superconducting magnets (dipoles and quadrupoles) for particle accelerators. We give approximated equations that govern the relation between the field/gradient, the current density, the type of superconductor (Nb−Ti or Nb3Sn), the thickness of the coil, and the fraction of stabilizer. We also state the main principle controlling the field quality optimization, and discuss the role of iron. A few examples are given to show the application of the equations and their validity limits. Keywords: magnets for accelerators, superconducting magnets, magnet design. 1 Introduction The common thread of these notes is to provide some analytical guidelines with which to outline the design of a superconducting accelerator magnet. We consider this for both dipoles and quadrupoles: the aim is to understand the trade-offs between the main parameters such as the field/gradients, the free aperture, the type of superconductor, the operational temperature, and the current density. These guidelines are rarely treated in handbooks: here, we derive a set of equations that provides us with the main picture, with an error that can be as low as 5%. This initial guess can then be used as a starting point for fine tuning by means of a computer code to account for other field quality effects not discussed here, such as iron saturation, persistent currents, eddy currents, etc. -
Thermal Analysis and Simulation of the Superconducting Magnet in the Spinquest Experiment at Fermilab
Thermal Analysis and Simulation of the Superconducting Magnet in the SpinQuest Experiment at Fermilab Z. Akbar∗and D. Keller† University of Virginia November 18, 2020 Abstract The SpinQuest experiment at Fermilab aims to measure the Sivers asymmetry for theu ¯ and d¯ sea quarks in the range of 0.1 < xB < 0.5 using the Drell-Yan production of dimuon pairs. A nonzero Sivers asym- metry would provide an evidence for a nonzero orbital angular momentum of sea quarks. The proposed beam intensity is 1.5 × 1012 of 120 GeV unpo- larized proton/sec. The experiment will utilize a target system consisting 4 of a 5T superconducting magnet, NH3 and ND3 target material, a He evaporation refrigerator, a 140 GHz microwave source and a large pump- ing system. The expected average of the target polarization is 80% for the proton and 32% for the deuteron. The polarization will be measured with three NMR coils per target cell. A quench analysis and simulation of the superconducting magnet is performed to determine the maximum intensity of the proton beam be- fore the magnet transitions to a resistive state. Simulating superconduc- tor as they transition to a quench is notoriously very difficult. Here we approach the problem with the focus on producing an estimate of the maximum allowable proton beam intensity given the necessary instru- mentation materials in the beam-line. The heat exchange from metal to helium goes through different transfer and boiling regimes as a function of temperature, heat flux, and transferred energy. All material proper- ties are temperature dependent. A GEANT-4 based simulation is used to calculate the heat deposited in the magnet and the subsequent cooling processes are modeled using the COMSOL Multiphysics simulation pack- age. -
Cryogen-Free Superconducting Magnet
Cryogen-free Superconducting Magnet Ryoichi HIROSE, Dr. Seiji HAYASHI, Dr. Kazuyuki SHIBUTANI, JAPAN SUPERCONDUCTOR TECHNOLOGY, INC. Cryogen-free superconducting magnets are becoming Vacuum GM popular due to their simple operation compared with vessel cryocooler conventional liquid helium cooled magnets. JAPAN Radiation 1st stage shield SUPERCONDUCTOR TECHNOLOGY INC. has HTS current manufactured more than a hundred cryogen-free leads 2nd stage superconducting magnets based on technologies Nb Sn coil developed by the R&D division of Kobe Steel. The 3 company has the largest worldwide market share. This NbTi coil report describes the basic features of cryogen-free magnets, as well as related recent and future developments. 1. Features and structures of cryogen-free Fig. 1 Schematic view of cryogen-free superconducting magnet superconducting magnets stage of which cools the thermal shield to prevent Superconducting magnets are advantageous for use heat radiation from outside and the second stage of in applications for which conventional electromagnets which, connected to a superconducting magnet, is are not applicable, such as high magnetic fields in used to cool the magnet. Since no cryogen is used, large spaces, because they can utilize large current the cryogen-free magnets are featured by 1) ease of densities. However, their application has been limited handling, 2) free rotation of magnetic field axes, 3) to physical experiments and chemical analysis, ease of operation in clean rooms and 4) ease of because cooling by liquid helium requires