EXPERIMENTAL STUDY of MECHANICAL POWER AMPLIFIER ¹Prof
Total Page:16
File Type:pdf, Size:1020Kb
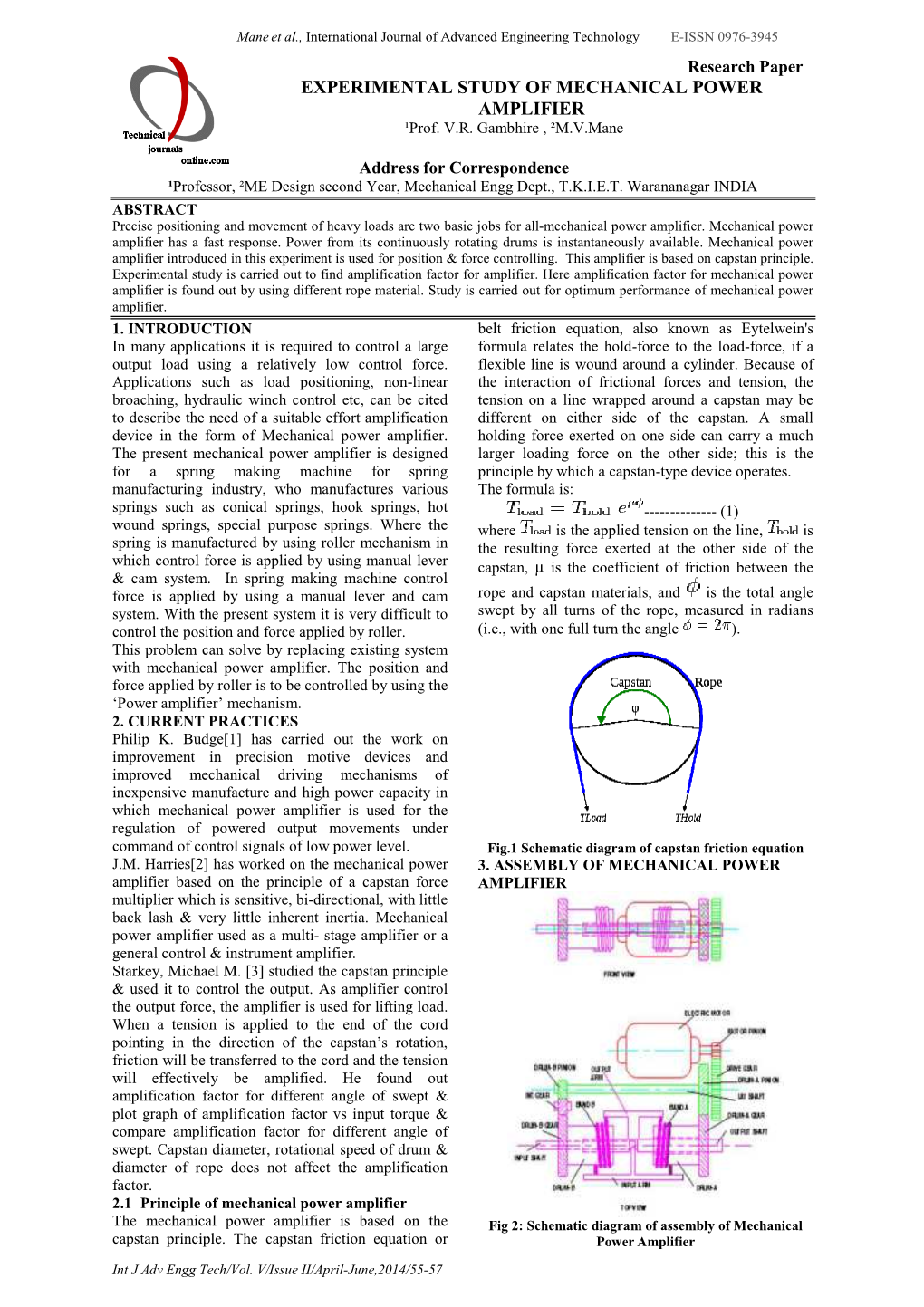
Load more
Recommended publications
-
Package Consideration in Capacitive Sensor Design
MECHANICALLY AMPLIFIED CAPACITIVE STRAIN SENSOR by JUN GUO Submitted in partial fulfillment of the requirements For the degree of Doctor of Philosophy Dissertation Adviser: Dr. Wen H. Ko Department of Electrical Engineering and Computer Science CASE WESTERN RESERVE UNIVERSITY May, 2007 CASE WESTERN RESERVE UNIVERSITY SCHOOL OF GRADUATE STUDIES We hereby approve the dissertation of ______________________________________________________ candidate for the Ph.D. degree *. (signed)_______________________________________________ (chair of the committee) ________________________________________________ ________________________________________________ ________________________________________________ ________________________________________________ ________________________________________________ (date) _______________________ *We also certify that written approval has been obtained for any proprietary material contained therein. Dedication To my parents. TABLE OF CONTENTS Mechanical Amplified Capacitive Strain Sensor Table of Contents ......................................................................................................................... 1 List of Tables ................................................................................................................................ 7 List of Figures .............................................................................................................................. 9 Acknowledgements ................................................................................................................. -
Converting Quantum Information to Mechanical Motion
Converting quantum information to mechanical motion by Adam P. Reed B.S., The Ohio State University, 2011 M.S., University of Colorado, 2015 A thesis submitted to the Faculty of the Graduate School of the University of Colorado in partial fulfillment of the requirements for the degree of Doctor of Philosophy Department of Physics 2017 This thesis entitled: Converting quantum information to mechanical motion written by Adam P. Reed has been approved for the Department of Physics Konrad Lehnert John Teufel Date The final copy of this thesis has been examined by the signatories, and we find that both the content and the form meet acceptable presentation standards of scholarly work in the above mentioned discipline. iii Reed, Adam P. (Ph.D., Physics) Converting quantum information to mechanical motion Thesis directed by Prof. Konrad Lehnert Mechanical systems that combine motion and electricity are often used to process information. They are employed as compact clocks, filters, and sensors in almost all modern electronic devices. Yet these devices are limited to processing classical information. To exploit mechanical systems in emerging quantum communication and computation technologies, such systems must process fragile quantum bits of information. In this thesis, I experimentally demonstrate the conversion of quantum bits encoded in electrical signals to the motion of a micron-scale mechanical resonator. This capability is crucial for harnessing mechanical systems as memories for quantum signals, or as converters of information between electronic quantum processors and telecommunications light. Beyond quantum information processing, this work opens up the possibility to test quantum theory in objects of an unprecedented mass scale. -
Two-Level Bulk Microfabrication of a Mechanical Broadband Vibration Amplifier E-Mail: [email protected]
Journal of Micromechanics and Microengineering PAPER • OPEN ACCESS Related content - Prototyping of a highly performant and Two-level bulk microfabrication of a mechanical integrated piezoresistive force sensor for microscale applications Bilal Komati, Joël Agnus, Cédric Clévy et broadband vibration amplitude-amplifier with ten al. coupled resonators - Torsional MEMS gyroscopes with non- resonant drive Cenk Acar and Andrei M Shkel To cite this article: Michelle Müller et al 2018 J. Micromech. Microeng. 28 045009 - Wide-bandwidth piezoelectric energy harvester with polymeric structure Mehdi Rezaeisaray, Mohamed El Gowini, Dan Sameoto et al. View the article online for updates and enhancements. This content was downloaded from IP address 82.130.103.57 on 19/11/2018 at 16:31 IOP Journal of Micromechanics and Microengineering Journal of Micromechanics and Microengineering J. Micromech. Microeng. J. Micromech. Microeng. 28 (2018) 045009 (10pp) https://doi.org/10.1088/1361-6439/aaabf6 28 Two-level bulk microfabrication of a 2018 mechanical broadband vibration amplitude- © 2018 IOP Publishing Ltd amplifier with ten coupled resonators JMMIEZ Michelle Müller1 , Verena Maiwald1, Lothar Thiele2, Jan Beutel2, Cosmin Roman1 and Christofer Hierold1 045009 1 Department of Mechanical and Process Engineering, Micro and Nanosystems Group, ETH Zurich, 8092 Zurich, Switzerland Michelle Müller et al 2 Department of Information Technology and Electrical Engineering, Computer Engineering and Networks Laboratory, ETH Zurich, 8092 Zurich, Switzerland Two-level bulk microfabrication of a mechanical broadband vibration amplifier Email: [email protected] Received 14 December 2017 Printed in the UK Accepted for publication 31 January 2018 Published 19 February 2018 JMM Abstract A micromechanical broadband vibration amplitudeamplifier for low power detection of 10.1088/1361-6439/aaabf6 acoustic emission signals is presented. -
Undirectional Paramagnetic Amplifier Design Research
,/f. .ASAC ^ ...-. ,- 1-KC ~ i I ,AA.,iU,ETlL t' .i .. ; .c tic s UNDIRECTIONAL PARAMAGNETIC AMPLIFIER DESIGN M. W. P. STRANDBERG TECHNICAL REPORT 363 JUNE 26, 1959 L·A/t 1_·-l-lmr · : '' -',- I'C RESEARCH LABORATORY OF ELECTRONICS MASSACHUSETTS INSTITUTE OF TECHNOLOGY CAMBRIDGE, MASSACHUSETTS The Research Laboratory of Electronics is an interdepartmental laboratory of the Department of Electrical Engineering and the Department of Physics. The research reported in this document was made possible in part by sup- port extended the Massachusetts Institute of Technology, Research Laboratory of Electronics, jointly by the U.S. Army (Signal Corps), the U.S. Navy (Office of Naval Research), and the U.S. Air Force (Office of Scientific Re- search, Air Research and Development Command), under Signal Corps Con- tract DA36-039-sc-78108, Department of the Army Task 3-99-20-001 and Project 3-99-00-000. Unidirectional Paramagnetic Amplifier Design* M. W. P. STRANDBERGt, FELLOW, IRE Summary-The radio-frequency parameters and the quantum- amplifiers along these lines is apparent. This is difficult mechanical parameters entering into the design of paramagnetic to understand because, for example, the application of quantum-mechanical amplifiers are described and discussed. The physical and electrical limitations on such parameters as gain-band- paramagnetic amplifiers to L-band radioastronomy is width product, gain stability, and nonreciprocity are described ana- hampered by the lack of a lossless L-band circulator. lytically and with design curves. Two realizations of nonreciprocal Furthermore, other methods of obtaining unidirectional amplifiers are described and discussed. In particular, operation of a gain-for example, through the use of a circulator (non- nonreciprocal amplifier at 9 kmc is described. -
Displacement Amplifier Mechanism for Piezoelectric Actuators Design
Displacement amplifier mechanism for piezoelectric actuators design using SIMP topology optimization approach Thomas Schlinquer, Abdenbi Mohand-Ousaid and Micky Rakotondrabe, member, IEEE Abstract— Due to their inherent crystalline properties piezo- non-compact actuators. The second configuration combines electric actuators have a limited deformation. This intrinsic two piezoelectric layers. It provides a larger displacement drawback deprives to exploit the potential of these actuators than piezostack however the provided force is low. Another such as, high bandwidth and high resolution in applications that require large displacement range. To overcome this limitation, classical approach employs external mechanism to magnify classical as well as systematic approaches were proposed to the deformation of the piezoelectric actuator. Known as am- design amplification mechanisms. The classical approach leads plifying mechanism, several structures have been proposed to empirical mechanisms which are not trivial and needs much in the literature. The widespread one is the flexural lever experience and intuition. In contrast, systematic approach uses structure [4]. Flextensional mechanism such as Moonie [5] topology optimization method which permits to automatically derive optimal designs that can satisfy specified performances [6], Cymbal [7] and nested rhombus structure [3] are also and imposed constraints simultaneously, this with a reasonable investigated. However, the design of such mechanisms is not time and cost. trivial because much experience and intuition are required. This paper proposes the design of a mechanism devoted to In contrast to the above mentioned approach, systematic amplify the displacement of a piezoelectric actuators (PEA). approaches including topology optimization [8], interval [9]– Based on the SIMP topology optimization method, the approach permits to derive a design with a displacement amplification [11] and blocs methods [12] can be used. -
A New Semi-Active Piezoelectric Based Friction Damper
Page number: 1 A NEW SEMI-ACTIVE PIEZOELECTRIC BASED FRICTION DAMPER Memet Unsal, Christopher Niezrecki, Carl D. Crane III University of Florida, Department of Mechanical Engineering Gainesville, Florida, 32611, USA e-mail address of lead author: [email protected] Abstract A new way to perform vibration control on a single-degree-of-freedom system using a piezoelectric friction damper is developed. The damper consists of an actuator, which is based on a piezoelectric stack with a mechanical amplifying mechanism that provides symmetric forces within the isolator. The advantages of such an actuator are its high bandwidth, actuating response and its ability to operate in vacuum environments such as in space. The damper is constrained to move using an air bearing that produces a virtually ideal single-degree-of-freedom spring-mass system. Within this work, the actuating ability of the friction-based actuator is characterized. INTRODUCTION Vibration isolation and control has traditionally been performed using passive techniques (damping material, viscoelastic mounts, etc.). With the recent advances in computer technology, active vibration control has become realizable and researchers have investigated using active control techniques for vibration control. Including an active component in the design allows a system the flexibility to tailor its dynamic characteristics depending upon the loading. However active control systems also have Page number: 2 significant limitations that prevent their implementation in real world systems (i.e. actuator power requirements, instability ). Semi-Active Vibration Control The concept of using semi-active control for vibration suppression was originally proposed by Karnopp, et al. They suggested varying the force in a viscous damper by controlling the orifice area [1]. -
Development and Implementation of a Deflection Amplification Mechanism for Capacitive Accelerometers
University of Southampton Research Repository ePrints Soton Copyright © and Moral Rights for this thesis are retained by the author and/or other copyright owners. A copy can be downloaded for personal non-commercial research or study, without prior permission or charge. This thesis cannot be reproduced or quoted extensively from without first obtaining permission in writing from the copyright holder/s. The content must not be changed in any way or sold commercially in any format or medium without the formal permission of the copyright holders. When referring to this work, full bibliographic details including the author, title, awarding institution and date of the thesis must be given e.g. AUTHOR (year of submission) "Full thesis title", University of Southampton, name of the University School or Department, PhD Thesis, pagination http://eprints.soton.ac.uk UNIVERSITY OF SOUTHAMPTON FACULTY OF PHYSICAL AND APPLIED SCIENCES Electronics and Computer Science Development and Implementation of a Deflection Amplification Mechanism for Capacitive Accelerometers by Ioannis Zeimpekis A Thesis for the degree of Doctor of Philosophy January 2012 UNIVERSITY OF SOUTHAMPTON ABSTRACT FACULTY OF PHYSICAL AND APPLIED SCIENCES ELECTRONICS AND COMPUTER SCIENCE Doctor of Philosophy Ioannis Zeimpekis Micro-Electro-Mechanical-Systems (MEMS) and especially physical sensors are part of a flourishing market ranging from consumer electronics to space applications. They have seen a great evolution throughout the last decades, and there is still considerable research effort for further improving their performance. This is reflected by the plethora of commercial applications using them but also by the demand from industry for better specifications. This demand together with the needs of novel applications fuels the research for better physical sensors. -
WO 2015/121710 Al 20 August 2015 (20.08.2015) P O P C T
(12) INTERNATIONAL APPLICATION PUBLISHED UNDER THE PATENT COOPERATION TREATY (PCT) (19) World Intellectual Property Organization International Bureau (10) International Publication Number (43) International Publication Date WO 2015/121710 Al 20 August 2015 (20.08.2015) P O P C T (51) International Patent Classification: KZ, LA, LC, LK, LR, LS, LT, LU, LY, MA, MD, ME, F16H 25/24 (2006.01) MG, MK, MN, MW, MX, MY, MZ, NA, NG, NI, NO, NZ, OM, PA, PE, PG, PH, PL, PT, QA, RO, RS, RU, RW, SA, (21) International Application Number: SC, SD, SE, SG, SK, SL, SM, ST, SV, SY, TH, TJ, TM, PCT/IB2014/059035 TN, TR, TT, TZ, UA, UG, US, UZ, VC, VN, ZA, ZM, (22) International Filing Date: ZW. 17 February 2014 (17.02.2014) (84) Designated States (unless otherwise indicated, for every (25) Filing Language: English kind of regional protection available): ARIPO (BW, GH, GM, KE, LR, LS, MW, MZ, NA, RW, SD, SL, SZ, TZ, (26) Publication Language: English UG, ZM, ZW), Eurasian (AM, AZ, BY, KG, KZ, RU, TJ, (72) Inventor; and TM), European (AL, AT, BE, BG, CH, CY, CZ, DE, DK, (71) Applicant : MUKHAMEDJANOV, Shukhrat [UZ/UZ]; EE, ES, FI, FR, GB, GR, HR, HU, IE, IS, IT, LT, LU, LV, 11, Ozodlik Street, Keles, 111101 (UZ). MC, MK, MT, NL, NO, PL, PT, RO, RS, SE, SI, SK, SM, TR), OAPI (BF, BJ, CF, CG, CI, CM, GA, GN, GQ, GW, (81) Designated States (unless otherwise indicated, for every KM, ML, MR, NE, SN, TD, TG). kind of national protection available): AE, AG, AL, AM, AO, AT, AU, AZ, BA, BB, BG, BH, BN, BR, BW, BY, Published: BZ, CA, CH, CL, CN, CO, CR, CU, CZ, DE, DK, DM, — with international search report (Art. -
THE MR. BILL STORY (Ornithopter Development, 1968-1991) Jeremy M
THE MR. BILL STORY (Ornithopter Development, 1968-1991) Jeremy M. Harris Getting Started I first met Jim DeLaurier in January of 1973 when a friend, Charlie Holt, introduced us at Battelle Institute in Columbus, Ohio where the three of us were research engineers. Charlie knew that I was interested in flapping-wing flight and had built a wind tunnel in my basement. I barely remember anything of that meeting, except that Jim was tall, friendly and allowed as how he'd like to see the tunnel sometime. A week or two later he came over in the evening and we began what we came later to call the 500-year conversation. It was immediately apparent that we shared an interest in many subjects, strange aircraft and photography being the most obvious ones. Jim listened politely to my spiel about flapping-wing experiments and cast an expert eye on the tunnel and its 15-inch square test section. He didn't say so, but I imagine he was already thinking of ways to improve it. Neither of us had the slightest idea that we were going to be friends and partners for 17 years while struggling with the most difficult challenge of our careers, a challenge that would, ironically, be met almost completely outside our normal working hours. The wind tunnel as Jim first saw it Natural flight as an engineering problem had entered my consciousness in 1968, when I was daydreaming about interesting applications for a kind of mechanical amplifier I was analyzing for my Master's thesis at Ohio State. -
Design and Development of Mechanical Power Amplifier
IJRET: International Journal of Research in Engineering and Technology eISSN: 2319-1163 | pISSN: 2321-7308 DESIGN AND DEVELOPMENT OF MECHANICAL POWER AMPLIFIER V.R.Gambhire1, M.V.Mane2 1Professor of Mechanical Engg department, TKIET Warnanagar, Maharashtra, India 2P.G student of Mechanical Design Engg, Department of Mechanical Engg, TKIET Warnanagar, Maharashtra, India Abstract Precise positioning and movement of heavy loads are two basic jobs for all-mechanical power amplifier. A capstan is simply a cylinder with a flexible body such as a string or cable wrapped around it. Capstans are generally used to assist in the lifting or pulling of heavy objects. By controlling the input tension on the cord, a capstan can dynamically amplify the input. It is hypothesized that a single capstan with multiple cords wrapped about it can act as numerous mechanical amplifiers. Present invention offers a new type of power amplifier which is structurally much simpler than previous amplifier. By using capstan friction principle mechanical power amplifier is designed for position and force controlling application. --------------------------------------------------------------------***---------------------------------------------------------------------- 1. INTRODUCTION Mechanical power amplifier is based on capstan principle. The capstan in conventional terms is used simply whenever a user must lift or pull something which is out of their means to accomplish under their own abilities. Rope is wrapped about a drum which is rotated by electric motor. As force is applied in the direction of rotation, friction is developed between the rope and the drum. The generated friction will then act in the same direction of pull, Fig 1 Diagram of capstan friction equation effectively amplifying the users force. -
Gramophone, Film, Typewriter
EDITORS Timothy Lenoir and Hans Ulrich Gumbrecht GRAMOPHONE, FILM, TYPEWRITER FRIEDRICH A. KITTLER Translated, with an Introduction, by GEOFFREY WINT HROP-YOUNG AND MICHAEL WUTZ STANFORD UNIVERSITY PRESS STANFORD, CALIFORNIA The publication of this work was assisted by a subsidy from Inter Nationes, Bonn Gramophone, Film, Typewriter was originally published in German in I986 as Grammophon Film Typewriter, © I986 Brinkmann & Bose, Berlin Stanford University Press Stanford, California © I999 by the Board of Trustees of the Leland Stanford Junior University Printed in the United States of America erp data appear at the end of the book TRANSLATORS' ACKNOWLEDGMENTS A translation by Dorothea von Mucke of Kittler's Introduction was first published in October 41 (1987): 101-18. The decision to produce our own version does not imply any criticism of the October translation (which was of great help to us) but merely reflects our decision to bring the Introduction in line with the bulk of the book to produce a stylisti cally coherent text. All translations of the primary texts interpolated by Kittler are our own, with the exception of the following: Rilke, "Primal Sound," has been reprinted from Rainer Maria Rilke, Selected Works, vol. I, Prose, trans. G. Craig Houston (New York: New Directions, 1961), 51-56. © 1961 by New Directions Publishing Corporation; used with permis sion. The translation of Heidegger's lecture on the typewriter originally appeared in Martin Heidegger, Parmenides, trans. Andre Schuwer and Richard Rojcewicz (Bloomington: Indiana Univ. Press, 1992), 80-81, 85-8 6. We would like to acknowledge the help we have received from June K. -
Mechanical Domain Parametric Amplification
Proceedings of the ASME 2007 International Design Engineering Technical Conferences & Computers and Information in Engineering Conference IDETC/CIE 2007 September 4-7, 2007, Las Vegas, Nevada, USA DETC2007-35426 MECHANICAL DOMAIN PARAMETRIC AMPLIFICATION Jeffrey F. Rhoads∗ Nicholas J. Miller Department of Mechanical Engineering Department of Mechanical Engineering Michigan State University Michigan State University East Lansing, Michigan 48824 East Lansing, Michigan 48824 Email: [email protected] Email: [email protected] Steven W. Shaw Brian F. Feeny Department of Mechanical Engineering Department of Mechanical Engineering Michigan State University Michigan State University East Lansing, Michigan 48824 East Lansing, Michigan 48824 Email: [email protected] Email: [email protected] ABSTRACT plications of parametric amplification in macroscale mechanical Though utilized for more than fifty years in a variety of systems. power and communication systems, parametric amplification, the process of amplifying a harmonic signal with a parametric pump, has received very little attention in the mechanical engi- INTRODUCTION neering community. In fact, only within the past fifteen to twenty years has the technique been implemented in micromechanical Parametric amplification, the process of amplifying an ex- systems as a means of amplifying the output of resonant micro- ternal, harmonic signal with a parametric pump, is a well es- transducers. While the vast potential of parametric amplifica- tablished concept in the field of electrical engineering, where tion has been demonstrated, to date, in a number of micro- and it has been employed for more than fifty years in applications nano-mechanical systems (as well as a number electrical sys- ranging from power and communication systems to Josephson tems), few, if any, macroscale mechanical amplifiers have been junctions [1, 2].