Understanding Geopolymerization Process for Enhancement of Mechanical Properties of Fly Ash Based-Geopolymer Concrete Lateef Najeh Assi University of South Carolina
Total Page:16
File Type:pdf, Size:1020Kb
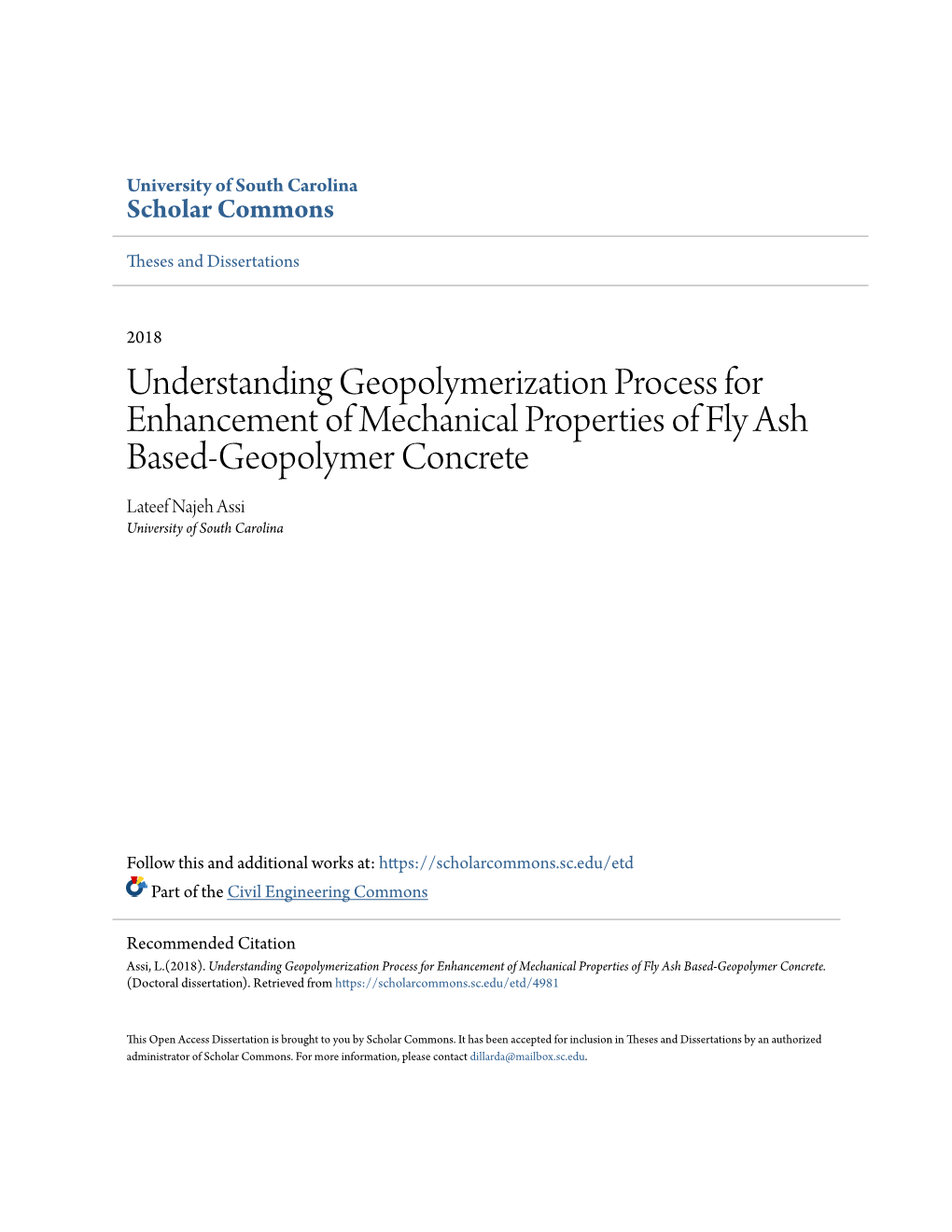
Load more
Recommended publications
-
Performance of Metakaolin Based Geopolymer Concrete at Elevated Temperature
Nigerian Journal of Technology (NIJOTECH) Vol. 39, No. 3, July 2020, pp. 732 – 737 Copyright© Faculty of Engineering, University of Nigeria, Nsukka, Print ISSN: 0331-8443, Electronic ISSN: 2467-8821 www.nijotech.com http://dx.doi.org/10.4314/njt.v39i3.11 PERFORMANCE OF METAKAOLIN BASED GEOPOLYMER CONCRETE AT ELEVATED TEMPERATURE S. Gambo1,*, K. Ibrahim2, A. Aliyu3, A. G. Ibrahim4 and H. Abdulsalam5 1, 3, 4, DEPARTMENT OF BUILDING, AHMADU BELLO UNIVERSITY, ZARIA. KADUNA STATE, NIGERIA 2, DEPARTMENT OF QUANTITY SURVEYING, UNIVERSITY OF ILORIN, ILORIN, KWARA STATE, NIGERIA 5, CENTER FOR RENEWABLE ENERGY, UMARU MUSA YAR’ADUA UNIVERSITY, KATSINA, KATSINA STATE, NIGERIA Email addresses: 1 [email protected], 2 [email protected], 3 [email protected], 4 [email protected], 5 [email protected] ABSTRACT Due to the carbon dioxide emission arising from the production of cement, alternative concrete that is environmentally friendly such as metakaolin geopolymer concrete have been developed. However, the performance of metakaolin based geopolymer concrete (MKGC) when exposed to aggressive environment particularly elevated temperature has not been investigated. Therefore, this paper assessed the performance of MKGC exposed to elevated temperatures. MKGC cube specimens of grade 25 were produced using a mix ratio of 1:1.58:3.71.After preparing the specimens, they were placed in an electric oven at a temperature of 60oC for 24 hours. Thereafter, the specimens were stored in the laboratory at ambient temperature for 28 days. The specimens were then exposed to elevated temperatures of 200, 400, 600 and 800oC. After exposure to elevated temperatures, the MKGC specimens were subjected to compressive strength, water absorption and abrasion resistance tests. -
Soil Stabilization Using Geopolymer and Biopolymer
AIJREAS VOLUME 1, ISSUE 10 (2016, OCT) (ISSN-2455-6300) ONLINE ANVESHANA’S INTERNATIONAL JOURNAL OF RESEARCH IN ENGINEERING AND APPLIED SCIENCES SOIL STABILIZATION USING GEOPOLYMER AND BIOPOLYMER P.DILIP KUMAR RAO, M.Tech(Geotech) SRINIVAS GANTA Department of Civil Engineering Associate professor, Abhinav Hitech College of Engineering Department of Civil Engineering E-mail: [email protected] Abhinav Hitech College of Engineering E-mail: [email protected] ABSTRACT permeability, durability and dust control is improved, which makes the soil suitable As stabilization of soil improves its engineering for use. There are different methods of properties, chemical and mechanical stabilization processes are in use. In the present study two stabilization, which include physical, difficult soils; expansive soil and dispersive soil are chemical and polymer methods of stabilized with geopolymer and biopolymer. stabilization. Physical methods involve Sodium based alkaline activators and fly ash as an physical processes to improve soil additive is used as geopolymer and Xanthan gum properties. This includes compaction and Guar gum are used as biopolymers. The effectiveness of geopolymer is studied in terms of methods and drainage. Drainage is an unconfined compressive strength (UCS), efficient way to remove excessive water differential free swelling (DFS), swelling pressure from soil by means of pumps, pipes and (SP), durability and dispersion tests. The swelling canal with an aim to prevent soil from pressure got reduced by 97.14% finally with swelling due to saturation with water. addition of 40% fly ash and 15% bentonite. The dispersion test showed bentonite to be an extremely Compaction processes lead to increase in dispersive soil, whose dispersiveness is controlled water resistance capacity of soil. -
Characteristics of Metakaolin-Based Geopolymer with Cathode Ray Tube Glass
polymers Article Characteristics of Metakaolin-Based Geopolymer with Cathode Ray Tube Glass Marcin Górski 1,* , Natalia Wielgus 1, Krzysztof Loska 2, Michał Kozioł 3, Marcin Landrat 3 , Waldemar Scierski´ 3 and Krzysztof Piko ´n 3 1 Department of Structural Engineering, Faculty of Civil Engineering, The Silesian University of Technology, Akademicka 5, 44-100 Gliwice, Poland; [email protected] 2 Department of Water and Wastewater Engineering, Faculty of Energy and Environmental Engineering, The Silesian University of Technology, Akademicka 2, 44-100 Gliwice, Poland; [email protected] 3 Department of Technologies and Installations for Waste Management, Faculty of Energy and Environmental Engineering, The Silesian University of Technology, Konarskiego 18, 44-100 Gliwice, Poland; [email protected] (M.K.); [email protected] (M.L.); [email protected] (W.S.);´ [email protected] (K.P.) * Correspondence: [email protected] Abstract: Geopolymers can be treated as an environmentally friendly alternative for concrete and enables utilization of various wastes. This paper focuses on the possibility of application of discarded cathode ray tube (CRT) glass inside a metakaolin-based geopolymer in the form of an aggregate, providing an ecological method of recycling of this hazardous material. The main goal of this paper was to develop an optimal composition of a new geopolymer and to describe its behavior under varying curing conditions. A geopolymer made of different mixtures was subjected to flexural and compressive strength tests. The density, mass loss, temperature changes, and metals leaching were determined as well. The results demonstrated that neither the content of CRT glass nor the Citation: Górski, M.; Wielgus, N.; curing regime has a significant influence on the mechanical behavior. -
Strength Development and Microstructural Behavior of Soils Stabilized with Palm Oil Fuel Ash (POFA)-Based Geopolymer
applied sciences Article Strength Development and Microstructural Behavior of Soils Stabilized with Palm Oil Fuel Ash (POFA)-Based Geopolymer Isam Adnan Khasib, Nik Norsyahariati Nik Daud * and Noor Azline Mohd Nasir Civil Engineering Department, Engineering Faculty, Universiti Putra Malaysia, Serdang 43400, Selangor, Malaysia; [email protected] (I.A.K.); [email protected] (N.A.M.N.) * Correspondence: [email protected] Abstract: Using geopolymer in soil stabilization has gained much attention recently due to its efficiency in improving soil properties and being environmentally friendly at the same time. This research aims to investigate the effect of palm oil fuel ash (POFA)-based geopolymer on soft soil stabilization. The mechanical and microstructural performance of two types of clay soil treated with geopolymer produce from POFA material was the focus of this study. In this respect, a series of unconfined compression and direct shear tests were conducted to investigate the mechanical properties of soils treated with POFA-based geopolymer. Furthermore, the microstructural changes in the treated samples were analyzed using field emission electron microscopy (FESEM) and energy dispersive X-ray (EDX). In accordance with the results, it was indicated that the shear strength of both soils soared by increasing the dosage of POFA-based geopolymer. Geopolymer with 40% POFA of the dry weight of soils yielded the highest UCS value at both curing periods, 7 and 28 days. Furthermore, the microstructural analysis revealed material modifications (N-A-S-H gel formation) related to strength enhancement. These results suggest the potentiality of using a POFA-based geopolymer binder to stabilize soft soil. -
Clayey Soil Stabilization Using Geopolymer and Portland Cement Pooria Ghadir 1, Navid Ranjbar2, * Abstract This Study Compares T
Clayey soil stabilization using geopolymer and Portland cement Pooria Ghadir 1, Navid Ranjbar 2, * 1Department of Civil Engineering, Iran University of Science and Technology, Tehran, Iran 2 Advanced and Innovative Materials (AIM) Group, Department of Civil, Environmental and Geomatic Engineering, University College London, London WC1E 6BT, UK Abstract This study compares the mechanical performance of clayey soil stabilization using volcanic ash (VA) based geopolymer and ordinary Portland cement (OPC). The effects of curing conditions and time, alkali activator/clay and alkali activator molarity, and VA/clay ratio are determined. The compressive strength of the untreated clayey soil specimens could be increased from 0.2 to 4 MPa and 2 to 12 MPa at the OC and DC conditions, respectively, when the soil partially replaced by 15 wt% of the binders. It is observed that geopolymer treatment is more efficient at the dry conditions (DC) while the Portland cement is superb at the wet environments (OC). This difference is associated with the role of water and pH in the kinetics of geopolymerization and the Portland cement hydration. Moreover, increasing the molarity of alkali activator and alkali activator/clay improve the compressive strength of the geopolymer treated soil. Besides, the higher energy absorption in all geopolymer specimens shows the superior ductility of this material in comparison with OPC. Keywords: Soil stabilization; Geopolymer; Cement; Volcanic ash; Clay; Natural pozzolan. *Corresponding author. E-mail addresses: [email protected] and [email protected] Introduction Lack of consideration for building and infrastructure construction on weak or soft soils is highly risky due to their poor shear strength and high compressibility. -
Novel Geopolymers Incorporating Silicate Waste
Novel geopolymers incorporating silicate waste Neuartige Geopolymere aus silikatischen Industrieabfällen Der Technischen Fakultät der Friedrich-Alexander-Universität Erlangen-Nürnberg zur Erlangung des Grades DOKTOR-INGENIEUR vorgelegt von Nicoletta Toniolo aus Velo d´Astico, Italy Als Dissertation genehmigt von der Technischen Fakultät der Friedrich-Alexander-Universität Erlangen-Nürnberg Tag der mündlichen Prüfung: 27.07.2018 Vorsitzende des Promotionsorgans: Prof. Dr. –Ing. Reinhard Lerch Gutachter: Prof. Dr.-Ing. habil. Aldo R. Boccaccini Prof. Enrico Bernardo Prof. Cristina Leonelli “Al mio angelo custode” I II Acknowledgements Firstly, I would like to express my sincere gratitude to Prof. Aldo Boccaccini, supervisor and head of the Institute of Biomaterials, who gave me the opportunity to do my PhD research at his Institute. I want to thank him for all the support during the past 3 years, all the suggestions he gave me and for the opportunity to take part to numerous international conferences, which were important for my knowledge and my personal experience. This research project was carried out within the framework of the poject “CoACH”, funded under the Marie Sklodowska-Curie action of the EU funding program for research and innovation “Horizon 2020”. I am grateful for the financial support it gave me. Thanks to the coordinator of the project Monica Ferraris, Milena Salvo and Cristiana Contardi, thanks for being always available, thanks for organizing meetings, training, etc. I really enjoyed everything. A super thanks to my “CoACH” fellows, I really think that it would have been impossible for me to have better project mates: thanks to Fra, for all the time together, for organizing all the meetings together, for supporting me and listening to my presentation 100 times. -
Mechanisms and Kinetics of Gel Formation in Geopolymers
Mechanisms and kinetics of gel formation in geopolymers By Catherine Anne Rees Supervisors: Professor Jannie S.J. van Deventer, Dr John Provis and Dr Grant C. Lukey A thesis submitted in total fulfilment of the requirements of the degree of Doctor of Philosophy Department of Chemical and Biomolecular Engineering The University of Melbourne March 2007 ii There is no duty we so much underestimate as the duty of being happy. Being happy we sow anonymous benefits upon the world… RoRoRobertRo bert Louis Stevenson (1850(1850----1894)1894) iii iv Abstract Geopolymer chemistry governs the formation of an X-ray amorphous aluminosilicate cement material. Binders form at ambient temperatures from a variety of different raw material sources, including industrial wastes. Early research in this field was based around investigating binder material properties; however, more recently, geopolymer formation chemistry has been intensively studied. Better understanding of the chemical processes governing geopolymer curing reactions will allow a wider variety of waste materials to be utilised and also the tailoring of binder properties for specific applications. Two different gel phases have been found previously to develop consecutively in a fly ash geopolymer system. However, an understanding of the factors which control the phase development and the process of transformation into the final binder are not well understood. This necessitates the use of a variety of analytical techniques, and has led in this thesis to the application of a novel in situ method, capable of analysing the high pH gels without destructive sample preparation. Attenuated total reflectance Fourier Transform infrared spectroscopy (ATR-FTIR) is used to analyse partially reacted geopolymers and hardened pastes both in and ex situ. -
Effect of Solids-To-Liquids, Na2sio3-To-Naoh and Curing Temperature on the Palm Oil Boiler Ash (Si + Ca) Geopolymerisation System
Materials 2015, 8, 2227-2242; doi:10.3390/ma8052227 OPEN ACCESS materials ISSN 1996-1944 www.mdpi.com/journal/materials Article Effect of Solids-To-Liquids, Na2SiO3-To-NaOH and Curing Temperature on the Palm Oil Boiler Ash (Si + Ca) Geopolymerisation System Zarina Yahya 1,*, Mohd Mustafa Al Bakri Abdullah 2,3,*, Kamarudin Hussin 1,2, Khairul Nizar Ismail 4, Rafiza Abd Razak 1 and Andrei Victor Sandu 5 1 Center of Excellence Geopolymer and Green Technology, School of Materials Engineering, Universiti Malaysia Perlis (UniMAP), P.O. Box 77, D/A Pejabat Pos Besar, Kangar 01000, Perlis, Malaysia; E-Mails: [email protected] (K.H.); [email protected] (R.A.R.) 2 Faculty of Engineering Technology, Uniciti Alam Campus, Universiti Malaysia Perlis, Sungai Chuchuh 02100, Padang Besar, Perlis, Malaysia 3 Faculty of Technology, Universitas Ubudiyah Indonesia, Jl. Alue Naga, Kec. Syiah Kuala Desa Tibang 23536, Banda Aceh, Indonesia 4 School of Environmental Engineering, Universiti Malaysia Perlis (UniMAP), P.O. Box 77, D/A Pejabat Pos Besar, Kangar 01000, Perlis, Malaysia; E-Mail: [email protected] 5 Faculty of Materials Science and Engineering, Gheorghe Asachi Technical University of Iasi, Blvd. D. Mangeron 41, Iasi 700050, Romania; E-Mail: [email protected] * Authors to whom correspondence should be addressed; E-Mails: [email protected] (Z.Y.); [email protected] (M.M.A.B.A.); Tel.: +6-012-5431426 (Z.Y.); +6-012-5055020 (M.M.A.B.A.); Fax: +6-04-9798178 (Z.Y. & M.M.A.B.A.). Academic Editor: Jérôme Chevalier Received: 12 February 2015 / Accepted: 17 April 2015 / Published: 28 April 2015 Abstract: This paper investigates the effect of the solids-to-liquids (S/L) and Na2SiO3/NaOH ratios on the production of palm oil boiler ash (POBA) based geopolymer. -
Formulation and Durability of Metakaolin-Based Geopolymers Raphaëlle Pouhet
Formulation and durability of metakaolin-based geopolymers Raphaëlle Pouhet To cite this version: Raphaëlle Pouhet. Formulation and durability of metakaolin-based geopolymers. Civil Engineering. Université Paul Sabatier - Toulouse III, 2015. English. NNT : 2015TOU30085. tel-01297848 HAL Id: tel-01297848 https://tel.archives-ouvertes.fr/tel-01297848 Submitted on 5 Apr 2016 HAL is a multi-disciplinary open access L’archive ouverte pluridisciplinaire HAL, est archive for the deposit and dissemination of sci- destinée au dépôt et à la diffusion de documents entific research documents, whether they are pub- scientifiques de niveau recherche, publiés ou non, lished or not. The documents may come from émanant des établissements d’enseignement et de teaching and research institutions in France or recherche français ou étrangers, des laboratoires abroad, or from public or private research centers. publics ou privés. THÈSE En vue de l'obtention du DOCTORAT DE L’UNIVERSITÉ DE TOULOUSEE Délivré par l’Université Toulouse III - Paul Sabatier Discipline ou spécialité : Génie Civil Présentée et soutenue par Raphaëlle POUHET Le 25 juin 2015 Titre : Formulation and durability of metakaolin-based geopolymers JURY M. Frizon Fabien Rapporteur M. Habert Guillaume Rapporteur Mme. Rossignol Sylvie Examinateur Mme. Escaffit Pascale Examinateur M. Cyr Martin Examinateur, directeur de thèse Ecole doctorale : Mécanique, Energétique, Génie Civil & Procédés Unité de recherche : Laboratoire Matériaux et Durabilité des Constructions de Toulouse Directeur(s) de Thèse : M. Martin Cyr Abstract Title : !"#$%&'()"* '*+ +%#',)&)(- ". $/('0'"&)*1,'2/+ 3/"4"&-$/#2 Abstract : 56/ $')* ",7/8()9/2 ". (6)2 (6/2)2 :/#/ (" '22/22 (6/ ."#$%&'()"* '*+ +%#',)&)(- ". $/('0'"&)*1 ,'2/+ 3/"4"&-$/#2 '2 ' ,)*+/# ."# 8)9)& /*3)*//#)*3 $'(/#)'&2; </"4"&-$/#2 '#/ '&0'&) 1'8()9'(/+ $'(/#)'&2= (6/- '#/ )*8#/'2)*3&- 2(%+)/+ ,- (6/ )*(/#*'()"*'& 8"$$%*)(- '2 (6/- #/4#/2/*( '* '&(/#*'()9/ (" (#'+)()"*'& >"#(&'*+ 8/$/*(; 56/ .)#2( 4'#( ". -
Molecular Dynamics Simulation of Calcium-Silicate-Hydrate for Nano-Engineered Cement Composites—A Review
nanomaterials Review Molecular Dynamics Simulation of Calcium-Silicate-Hydrate for Nano-Engineered Cement Composites—A Review Byoung Hooi Cho 1 , Wonseok Chung 2,* and Boo Hyun Nam 1,* 1 Department of Civil, Environmental and Construction Engineering, University of Central Florida, 12800 Pegasus Drive, Suite 211, Orlando, FL 32816, USA; [email protected] 2 Department of Civil Engineering, Kyung Hee University, 1732 Deogyeong-daero, Giheung-gu, Yongin-si 17104, Korea * Correspondence: [email protected] (W.C.); [email protected] (B.H.N.) Received: 17 September 2020; Accepted: 20 October 2020; Published: 29 October 2020 Abstract: With the continuous research efforts, sophisticated predictive molecular dynamics (MD) models for C-S-H have been developed, and the application of MD simulation has been expanded from fundamental understanding of C-S-H to nano-engineered cement composites. This paper comprehensively reviewed the current state of MD simulation on calcium-silicate-hydrate (C-S-H) and its diverse applications to nano-engineered cement composites, including carbon-based nanomaterials (i.e., carbon nanotube, graphene, graphene oxide), reinforced cement, cement–polymer nanocomposites (with an application on 3D printing concrete), and chemical additives for improving environmental resistance. In conclusion, the MD method could not only compute but also visualize the nanoscale behaviors of cement hydrates and other ingredients in the cement matrix; thus, fundamental properties of C-S-H structure and its interaction with nanoparticles can be well understood. As a result, the MD enabled us to identify and evaluate the performance of new advanced nano-engineered cement composites. Keywords: molecular dynamics; calcium-silicate-hydrate; nano-engineered cement materials; carbon-based nanomaterials; cement–polymer nanocomposites 1. -
Stabilization of Soil Using Geopolymer: a Review
International Research Journal of Engineering and Technology (IRJET) e-ISSN: 2395-0056 Volume: 07 Issue: 10 | Oct 2020 www.irjet.net p-ISSN: 2395-0072 Stabilization of Soil using Geopolymer: A Review Keerthy R Karthikeyan1, Elba Helen George2 1PG student, Civil Engineering Department, Toc H Institute of Science and Technology, Kerala, India 2Asst. Professor, Civil Engineering Department, Toc H Institute of Science and Technology, Kerala, India ---------------------------------------------------------------------***---------------------------------------------------------------------- Abstract - In order to confront the problems associated used in embankments, canal, roadway, dams, waste landfills with clay for construction, some adequate ground etc. Clay soils feel very sticky and rolls like plasticine when improvement technique is essential. The alkaline solutions wet. They can hold more total water than most other soil such as sodium hydroxide and sodium silicate along with class types and, although only about half of this is available to F fly ash, Ground Granulated Blast Furnace Slag (GGBS)and plants, crops seldom suffer from drought. Ground-granulated metakaolin as additives are used to improve the properties of blast-furnace slag (GGBS or GGBFS) is obtained by quenching clay. Flyash greatly modifies the strength properties of soft molten iron slag, (a by-product of iron and steel-making) soils and it contain silica and aluminium materials from a blast furnace in water or steam, to obtain a glassy, (pozzolans) as well as a certain amount of lime, which granular product that is then dried and ground into a fine chemically binds to soft soil and forms cement compounds. powder. Ground-granulated blast furnace slag is strongly Metakaolin is a highly reactive pozzolana formed by the cemented and high in CSH (calcium silicate hydrate), which calcinations of kaolinite (China clay). -
Manufacture of Full-Scale Geopolymer Cement Concrete Components: a Case Study to Highlight Opportunities and Challenges
Manufacture of full-scale geopolymer cement concrete components: A case study to highlight opportunities and challenges Brett Tempest, Clarke Snell, Thomas Gentry, Maria Trejo, and Keith Isherwood nnovators throughout the construction industry are making great strides toward increased environmen- Ital sustainability by updating processes, improving designs, and selecting greener materials. These aspects of modernization are both a response to demand from build- ing owners and operators and a necessary means to remain competitive by achieving higher-performing buildings and infrastructure. Concrete producers have systematically improved the performance of their product by finding and exploiting benefits that are unique to concrete construction. These significant advances have included durable finishes, superior insulative properties in multiwythe wall compo- nents, economy with formwork, and rapid constructibility. The next frontier for the industry includes addressing the greenhouse-gas emissions associated with portland cement and further integrating the benefits of concrete materials into building functions and operations. ■ Geopolymer cement is an alternative binder that is capable of forming concrete with competent mechanical performance and This paper describes the design and construction of a attractive environmental benefits. concrete house that was designed to accommodate a small family living in an urban environment. It is grid ■ This paper presents a case study of the manufacture of full- neutral with regard to energy production, meaning that it scale geopolymer cement concrete components. generates as much energy as it uses on an annual basis. The house was a 2013 entry into the U.S. Department of ■ This paper discusses mechanical characteristics of geopolymer Energy’s Solar Decathlon.1 This biennial event engages cement concrete, quality of form finishes, strategies for curing, 20 teams from universities around the world to design, and challenges to full-scale production.