Design Computation Symposium December 2, 2015 | 8:00 A.M.–12:00 P.M
Total Page:16
File Type:pdf, Size:1020Kb
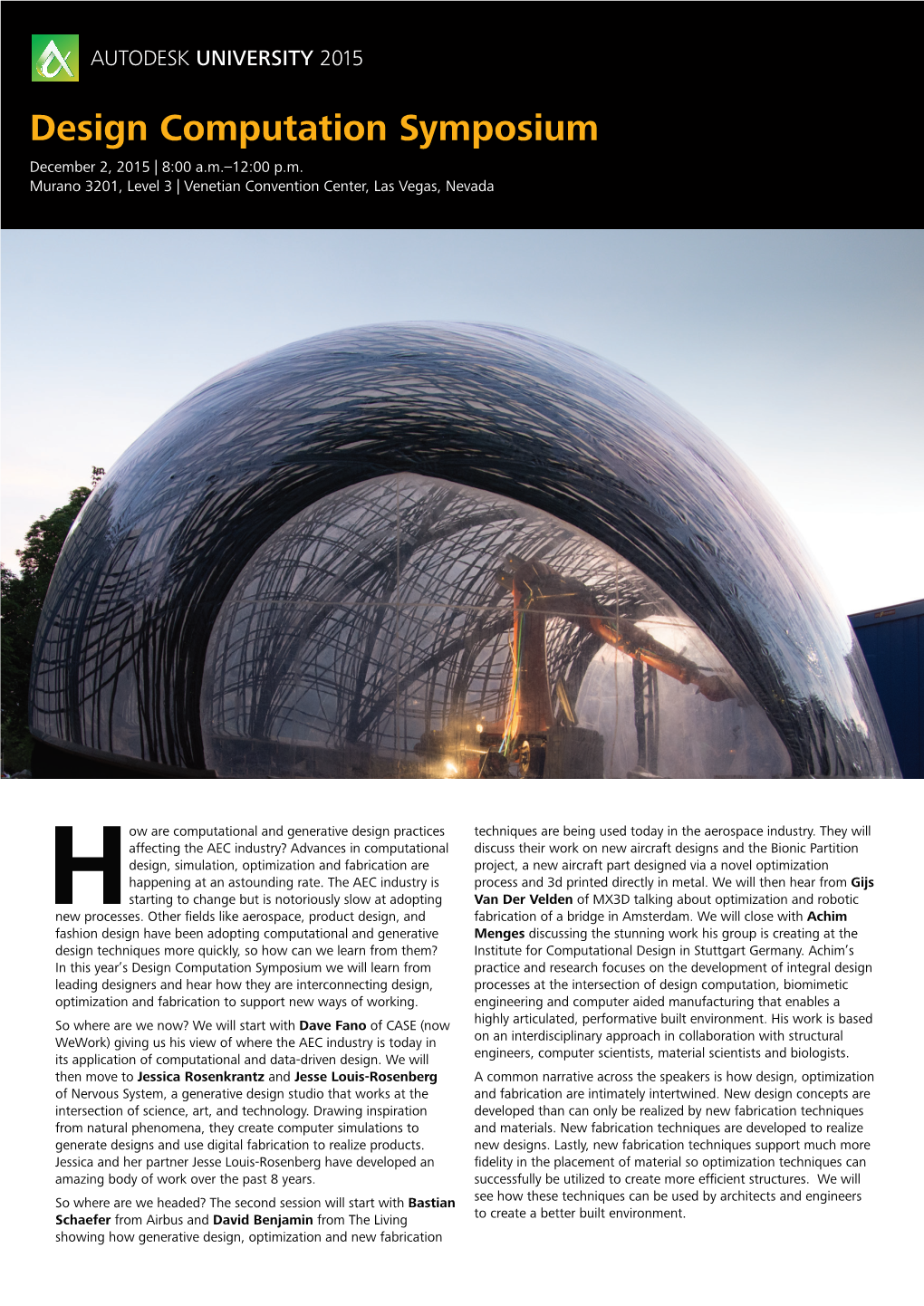
Load more
Recommended publications
-
Design Looks Ahead Our Homes Are Not Only Our Shelters
A generalized confinementis a good time to be reminded that Design looks ahead our homes are not only our shelters. As pointed by Gio Ponti Nature has always been a source of inspiration and a spur for in the first Domus editorial they are not a ‘machine à habiter’ innovation. This timeless admiration is now completed by an designed to fulfill solely our basic needs and life’s practicalities. increasing concern to harmonize our cohabitation with nature Unlike a nest or a lair, our interiors aspire to something superior and by the same token save ourselves in the long run. The expe- and to being in a way, the expression of our civilization. The rimentation on materials and techniques is not something new; cave man adorned the walls of his grottoes and since then ela- Gio Ponti used aluminium, Charles Eames and Eero Saarinen borations on our surroundings have flourished. Indeed, many polyester, etc. theories have been developed over the years as to what form the ‘art de vivre’ can take. I would like to explore some of them in However, the design discipline is undergoing drastic changes. this newsletter. Although it is difficult to identify a coherent and conceptualized movement for what is happening in the design world it seems As an art advisor I believe that my work consists in presenting that a few common threads can be put forward. They are the the most interesting intellectual and esthetic adventures, that one following: can follow to enrich its interior materially and spiritually, which I A holistic approach of the design practice in which the designer consider to be a form of art collection. -
1 W in T E R 2 0 17
WINTER 2017 1 SPRING 2016 SPRING 3 DIRECTOR’S LETTER DIRECTOR’S LETTER 5 2017 NATIONAL DESIGN AWARDS GALA 6 DESIGN AND AGENCY 9 IN MIDAIR AND OVER WATER 12 THE AXIS PROJECT: 01 02 DESIGNING FOR WELLNESS WINTER 2017 issue’s “Design Pulse” asks: What can design do to empower people with disabilities? The thought-provoking responses DEAR COOPER HEWITT broaden awareness of design’s impact on individuals with 14 DRAWING BY TOUCH different abilities. FRIENDS, On campus, a slew of initiatives are capitalizing on the A collaborative and creative process, design begins with empathy museum’s role as a dynamic hub to highlight advancements 16 DESIGN PULSE: for the user and results in systems, products, and solutions and promote design thinking for expanding access. On view in that improve lives. At Cooper Hewitt, the visitor is our user and our first-floor galleries, Access+Ability presents some of the the campus is designed to be welcoming and participatory. extraordinary research and over seventy innovative products EMPOWERMENT Everyone is encouraged to engage in the design process, and that address different physical, cognitive, and sensory these interactions transform a passive viewing experience into challenges, taking advantage of the latest developments in an immersive discovery of design. Beyond the museum’s walls, digital technologies and fabrication methods. They also reflect audiences from all over the globe explore our vast and eclectic changing attitudes that prioritize the user in the design process 18 COOPER HEWITT LAB: permanent collection and build their own online collections with our to emphasize what a person can do when given the opportunity. -
Director's Letter
DIRECTOR’S LETTER 01 02 SPRING/SUMMER 2017 how the creative awakening of American design further propelled the United States to a place of hope and economic opportunity. DEAR COOPER HEWITT Coupled with Jeweled Splendors of the Art Deco Era: The Prince and Princess Sadruddin Aga Khan Collection, visitors cannot help FRIENDS, but leave in awe of this fertile period. It’s my favorite time of year and an opportune moment to inject For today’s young people, design expands academic and some optimism into our minds. This journal brims with optimism, career horizons, boosts confidence, and promises a productive from the vibrating cover celebrating design legend Ingo Maurer future. Thanks to the generous support of Target, Cooper and his work full of dreaming and creativity to a slew of topics Hewitt’s National High School Design Competition opens the exploring the promise of design. Be sure to see Ingo's LED doors for students to engage in design thinking and tackle real- wallpaper on display in our current exhibition on the first floor, life challenges. This year, our judges include Alice Waters, chef Making | Breaking: New Arrivals, emphasizing breakthroughs in and owner of the groundbreaking restaurant Chez Panisse in new technologies and techniques and in-depth process stories. Berkeley, California, and founder of the Edible Schoolyard Project Design optimism is rooted in the discipline’s commitment (ESP), featured in this issue. A nationwide school program, ESP to collaboration, experimentation, and, most importantly, teaches children to become creative problem-solvers and fosters innovation and progress. A dynamic learning laboratory, Cooper a lifelong appreciation for food’s ability to connect and sustain Hewitt harnesses the power of its educational resources—built our communities. -
Heatwave-Vel, Amivel Sok Nemzetközi Múzeumba Nyert Bebocsátást, És Amivel Számtalan Díjat Gyűjtött Be
ARLI Magyarország Kft. – JAGA radiátor Magyar Képviselet www.JAGA.hu E-mail: [email protected] 1037 Budapest, Bécsi út 269. Telefon: (06-1) 453-3712 453-3713 Fax: (06-1) 453-3714 J A G A H E A T W A V E Az ARLI Magyarország Kft. által képviselt, 1962-ben alapított belga JAGA cég formatervezői a fűtőtestek kidolgozásakor klasszikus formaelemekből táplálkozó innovatív műalkotásaikon keresztül frissességet hoznak a dekorációs radiátorok világába, amit a gyártástechnológia tartóssággal és finom megmunkáltsággal ötvöz. A JAGA egyedi karakterisztikával rendelkező alkotásai egyedi enteriőrök remek kiegészítői, hatalmas inspirációt nyújtva a legkülönbözőbb belsőépítészeti megoldások számára. A JAGA design radiátorai olyan embereknek kínálják magukat, akik nyitottak az esztétikára, a szimbolikus értékekre, kényelemre, színekre, formákra. Játszi hullámok betonból A Jaga és Joris Laarman által tervezett nagyszerű sík-dombormű egy tekintetet vonzó falon függő műalkotás. Megigéző, felfrissíti az elmét, dinamizmust, kreativitást sugároz és egyben adományoz. A visszatérő motívumok bonyolult ritmusában táncoló, elragadóan könnyed hullámok merész ellentétet formálnak a kemény betonszerkezettel. Ez az érdekes fűtőtest a legelső, amely egyesíti a képzőművészetet és a mesterségbeli tudást az ipari hatékonysággal. ARLI Magyarország Kft. – JAGA radiátor Magyar Képviselet www.JAGA.hu E-mail: [email protected] 1037 Budapest, Bécsi út 269. Telefon: (06-1) 453-3712 453-3713 Fax: (06-1) 453-3714 A tervező Joris Laarman Joris Laarman 1979-ben született Hollandiában a német határ mellett. Képzőművészeti képzések után 1998-ban kezdte meg iparművészeti tanulmányait az Eindhoveni Iparművészeti Akadémián, ahol cum laude végzett. 2003-ban szerzett hírnevet a teljes mértékben általa tervezett rokokó radiátorral, a Heatwave-vel, amivel sok nemzetközi múzeumba nyert bebocsátást, és amivel számtalan díjat gyűjtött be. -
1976, Jeroen and Twin Brother, Joep Verhoeven Born in Tegelen, NL Lives and Works with Joep Verhoeven in the Netherlands
1976, Jeroen and twin brother, Joep Verhoeven born in Tegelen, NL Lives and works with Joep Verhoeven in The Netherlands EDUCATION 2004 Art Academy, Eindhoven, NL TEACHING 2008 Art Academy, Maastricht, NL 2004 Architectural Association School of Architecture, London, UK AWARDS/NOMINATIONS 2009 Best socially oriented foreign production, Toon van Tuilprijs, NL 2008 “Light Wind”, Design Museum Award, London, UK 2007 “Light Wind” nomination, Well Tech Design Award, UK “Lucky Charms” nomination, EDIDA: Elle Decoration International Design Award, UK 2006 “Demakersvan werk alg.” Nomination, Design Prijs Rotterdam, NL “Demakersvan werk alg.” Nomination, Woonbeurspin, NL 2005 DSM Design Award, NL Best graduation work, Renee Smeetsprijs, NL 2004 “Lace Fence”, First Prize, Rene Smeetsprijs, NL “Cinderella”, First Prize, Best Graduation Project, Items-Ahrend, NL SELECTED EXHIBITIONS 2015-2016 This Is for Everyone: Design Experiments for the Common Good, Museum of Modern Art (MoMA), New York, US 2012-2014 Against the Grain: Wood in Contemporary Art, Craft, and Design, Mint Museum of Craft and Design, Charlotte, US; Museum of Arts and Design, New York, US; Museum of Art, Fort Lauderdale, US 2013 Design Icons (highlights from the permanent collection of the Die Neue Sammlung Design Museum), Audi Forum, Neckarsulm, DE 2011-2012 Standard Deviations: Types and Families in Contemporary Design 2011 New Energy in Design and Art, Museum Boijmans Van Beuningen, Rotterdam, NL The Curious Image, Blain|Southern, London, UK Thinking Big, Brooklyn Museum, New York, -
We Wish Our Readers a Happy Father's
VOL 9 ISSUE 24 ● NEW YORK ● JUNE 19 - JUNE 25, 2015 ● Tel: 646-247-9458 ● www.theindianpanorama.com ●PRICE 40 CENTS BJP BLEEDS: We wish our readers a Happy Father’s Day Lalitgate and now Advani Emergency Remark ‘Investors are certainly looking NEW DELHI (TIP): As if the pain of Lalitgate involving Sushma Swaraj forward to making large amount of and Vasundhara Raje Scindia was not enough , Advani chose to inject a little more of it with his investments in India’: Arun Jaitley emergency remarks. Already in the line of NEW YORK CITY (TIP): opposition's fire over the India's Finance Minister Lalit Modi issue, the ruling International Arun Jaitley sounded BJP on Thursday, June 18, Day of Yoga optimistic that foreign was further driven to a June 21, 2015 investors are going to make corner over remarks of a large amount of party senior L.K. Advani This special issue is investments in India,. The that he did not rule out dedicated to the First International Day of Yoga reason- they are highly another Emergency-like satisfied with the reform situation in the country. Sponsored by Dr. Parveen Chopra and process initiated by the As the Congress Mrs. Usha P. Chopra Modi government in the last continued its attacks on one year. the Bharatiya Janata Party "I clearly see two kinds of over the help provided to reactions. The predominant "fugitive" former IPL reaction is that there is a lot commissioner Lalit Modi of excitement and a lot of by External Affairs India's Finance Minister Arun Jaitley rang the closing bell at New York Stock Exchange, June 17. -
Experimenting the Future: the Symbiosis of Handcrafts and Digital Technologies in the Joris Laarman Lab
Experimenting the Future: the symbiosis of handcrafts and digital technologies in the Joris Laarman Lab. Name: Anouk Reijmer Student number: S1133659 Email: [email protected] Supervisor: Prof. Dr. T. R. A. de Rijk Second reader: Drs. M.A. de Ruiter Master thesis: Arts & Culture Specialization: Design and Decorative Art Studies Academic year: 2015-2016 1 LIST OF CONTENTS Introduction¼¼¼¼¼¼¼¼¼¼¼¼¼¼¼¼¼¼¼¼¼¼¼¼¼¼¼¼¼¼¼..1 1. Joris Laarman Lab¼¼¼¼¼¼¼¼¼¼¼¼¼¼¼¼¼¼¼¼¼¼¼¼¼¼¼7 1.1. Introduction¼¼¼¼¼¼¼¼¼¼¼¼¼¼¼¼¼¼¼¼¼¼¼¼¼¼¼¼.7 1.2. Ornament versus Functionality¼¼¼¼¼¼¼¼¼¼¼¼¼¼¼¼¼¼¼..11 1.2.1. Reinventing Functionality¼¼¼¼¼¼¼¼¼¼¼¼¼¼¼¼¼¼¼.11 1.2.2. Vortex¼¼¼¼¼¼¼¼¼¼¼¼¼¼¼¼¼¼¼¼¼¼¼¼¼¼¼..12 1.3. Technology versus Craft¼¼¼¼¼¼¼¼¼¼¼¼¼¼¼¼¼¼¼¼¼¼.13 1.3.1. Forest Tables¼¼¼¼¼¼¼¼¼¼¼¼¼¼¼¼¼¼¼¼¼¼¼¼.14 1.3.2. Digital Matter¼¼¼¼¼¼¼¼¼¼¼¼¼¼¼¼¼¼¼¼¼¼¼¼..15 1.3.3. Makerchairs¼¼¼¼¼¼¼¼¼¼¼¼¼¼¼¼¼¼¼¼¼¼¼¼¼16 1.4. New Methods and Materials¼¼¼¼¼¼¼¼¼¼¼¼¼¼¼¼¼¼¼¼..17 1.4.1. Bone Furniture¼¼¼¼¼¼¼¼¼¼¼¼¼¼¼¼¼¼¼¼¼¼¼...17 1.4.2. Foam China¼¼¼¼¼¼¼¼¼¼¼¼¼¼¼¼¼¼¼¼¼¼¼¼¼19 1.4.3. Microstructures¼¼¼¼¼¼¼¼¼¼¼¼¼¼¼¼¼¼¼¼¼¼¼..20 1.4.4. MX3D¼¼¼¼¼¼¼¼¼¼¼¼¼¼¼¼¼¼¼¼¼¼¼¼¼¼¼..21 2. Craft in the Digital Age¼¼¼¼¼¼¼¼¼¼¼¼¼¼¼¼¼¼¼¼¼¼¼¼¼ 23 2.1. Traditional Notion of Craft¼¼¼¼¼¼¼¼¼¼¼¼¼¼¼¼¼¼¼¼.¼.24 2.1.1. Definition¼¼¼¼¼¼¼¼¼¼¼¼¼¼¼¼¼¼¼¼¼¼¼¼¼¼.26 2.1.2. Etymology¼¼¼¼¼¼¼¼¼¼¼¼¼¼¼¼¼¼¼¼¼¼¼¼¼...27 2.2. Contemporary Notion of Craft¼¼¼¼¼¼¼¼¼¼¼¼¼¼¼¼¼¼¼¼28 2.2.1. Current Debates¼¼¼¼¼¼¼¼¼¼¼¼¼¼¼¼¼¼¼¼¼¼¼29 2.2.2. The Amateur-Craftsman¼¼¼¼¼¼¼...¼¼¼¼¼..¼¼¼¼¼¼.32 Conclusion¼¼¼.¼¼¼¼¼¼¼¼¼¼¼¼¼¼¼¼¼¼¼¼¼¼¼¼¼¼¼¼35 Appendices¼¼¼¼¼¼¼¼¼¼¼¼¼¼¼¼¼¼¼¼¼¼¼¼¼¼¼¼¼¼¼39 -
JORIS LAARMAN Present Lives and Works in the Netherlands 2004
JORIS LAARMAN Present Lives and works in the Netherlands 2004 Established Joris Laarman Studio and Lab, Amsterdam, The Netherlands 2003 Graduated cum laude from Eindhoven Design Academy, Eindhoven, The Netherlands 1979 Born, Borculo, The Netherlands Select Solo Exhibitions 2020-21 Design and the Wondrous, curated by Marie-Ange Brayer, Centre Pompidou x West Bund, Shanghai, China 2018 Joris Laarman Lab: Gradients, Kukje Gallery, Seoul, South Korea 2015-18 Joris Laarman Lab, traveling exhibition: High Museum of Art, Atlanta, GA; The Museum of Fine Arts, Houston, TX; Cooper Hewitt Smithsonian Design Museum, New York, NY; Groninger Museum, Groningen, The Netherlands; Autostadt, Wolfsburg, Germany 2014 Joris Laarman Lab: Bits and Crafts, Friedman Benda, New York, New York 2011-12 Joris Laarman, Kukje Gallery, Seoul, South Korea 2010 Joris Laarman, Friedman Benda, New York, NY 2009 Inventory, Joris Laarman Studio, Amsterdam, Netherlands 2008 Joris Laarman: Stranger than Fiction, CAB Centro de Arte, Caja Burgos, Spain 2005 Limited Joris Laarman, DSM Corporate Headquarters, Heerlen, The Netherlands 2004 Joris Laarman, Design Museum Tank, London, England Joris Laarman, DSM Art Collection, Heerlen, Netherlands Select Group Exhibitions 2019 Future and the Arts: AI, Robotics, Cities, Life – How Humanity Will Live Tomorrow, Mori Art Musuem, Tokyo, Japan Designs for Different Futures, Philadelphia Museum of Art, Philadelphia, PA La Fabrique du Vivant, Centre Pompidou, Paris, France An Accelerated Culture, Friedman Benda, New York, NY 2018 Design et Merveilleux, Musée d'art moderne, Saint-Priest-en- Jarez, France When Attitude Become Chairs, Pizzuti Colletion, Columbus, OH 2017-18 Mind the Digital, Design Society, Shenzhen, China NGV Triennial, The National Gallery of Victoria, Melbourne, Australia 2017 Channeling Nature by Design, Philadelphia Museum of Art, Philadelphia, PA Gwangju Design Biennale, Gwangju, Korea Mutations-Créations/ Imprimer le monde, Centre Pompidou, Paris, France 3D. -
High Museum of Art to Present First Museum Survey for Experimental Dutch Designer Joris Laarman
FOR IMMEDIATE RELEASE HIGH MUSEUM OF ART TO PRESENT FIRST MUSEUM SURVEY FOR EXPERIMENTAL DUTCH DESIGNER JORIS LAARMAN Spring 2018 exhibition will feature groundbreaking designs from the High’s collection, which represents the second largest public repository of Laarman’s work in the world ATLANTA, Sept. 6, 2017 – From furniture generated by algorithms to a “living” lampshade made of genetically modified cells, the work of pioneering Dutch designer Joris Laarman (born 1979) redefines the boundaries between art, science and technology. The High Museum of Art will offer an in-depth look at his innovative oeuvre as the exclusive Southeast venue for “Joris Laarman Lab: Design in the Digital Age.” The exhibition, on view Feb. 18 through May 13, 2018, will feature numerous designs from the High’s collection, which boasts the largest public holdings of the Dutch artist’s work outside of his home country. Organized by the Groninger Museum, the Netherlands, “Joris Laarman Lab” is the first museum survey to comprehensively explore Laarman’s creative prowess and curiosity through a range of works dating from 2004 to the present that blend emerging technologies with skilled craftsmanship. Furniture designs, applied projects and experiments from every phase of his career are presented alongside related videos, sketches and renderings that illustrate the Joris Laarman Lab’s creative and production processes. Founded in 2004, the Lab is a multidisciplinary hub of scientists, engineers, programmers and craftspeople who explore the possibilities of design through research, experimentation and groundbreaking technology. “Laarman and his Lab are design pioneers and idea detonators. Laarman’s intellectual, thoughtful and collaborative approach to design propels him to explore new means and methods for creating, resulting in a remarkably innovative and beautiful body of work,” said Sarah Schleuning, High Museum of Art curator of decorative arts and design. -
Joris Laarman Solo Exhibition Joris Laarman Lab: Gradients
Joris Laarman Solo Exhibition Joris Laarman Lab: Gradients Press Conference: May 10 (Thurs.), 2018, 1:30PM at Kukje Gallery K2 Exhibition Dates: May 10 – June 17, 2018 Venue: Kukje Gallery K2 Kukje Gallery is pleased to announce Joris Laarman Lab: Gradients, a solo exhibition of work by Joris Laarman on view from May 10 to June 17, 2018, in the gallery's K2 space. Laarman’s second exhibition at Kukje Gallery following his debut in 2011, Joris Laarman Lab: Gradients presents new and recent works spanning four years of cutting-edge experimentation in the designer’s Amsterdam-based Joris Laarman Lab (hereafter “the Lab”). The installation will allow audiences to encounter a broad range of his work, framing both his skills in design and engineering as well as his visionary aesthetic. The artworks will be presented alongside related videos, sketches, and renderings that illustrate the Lab’s commitment to experimentation and innovative creative processes. Gradients is comprised of works from all of the Lab’s recent series, including Microstructures, Dragon, Maker, and Gradient Screen. The Microstructures series is based on gradient patterning and explores the pioneering use of 3D printing technology at the scale of furniture. Each work is made up of cells that vary in form, size or function. For the Dragon Benches and Gradient Screen, the Lab developed a revolutionary large scale metal printing tool, the MX3D metal printer, enabling the Lab to create unprecedented sculptural works by drawing complex curved lines and surfaces in mid-air that were previously not feasible. Various versions of Dragon Benches are now in museum collections around the world, and serve as proof of concept for much larger architectural and infrastructural projects like the Lab’s first 3D printed stainless steel bridge—to be completed later this year. -
Fruitoftheforest2.Pdf
4 WELCOME 6 STAFF AND CONTRIBUTORS 9 NEW YORK by meghan dellacrosse SIMONE FORTI: VOICE IN MOVEMENT / VOICING MOVEMENTS 15 MILAN by marco tagliafIerro EMOTIONAL INTELLIGENCE 21 TOKYO by ayaki aron hortz MONJAYAKI 28 DASHBOARD by alessandro gori INTO THE WIRES. WIREFRAME AND HIDDEN-LINE 34 RADICAL POINT OF VIEW by guido molinari AN INTERVIEW WITH LAPO BINAZZI, CO-FOUNDER OF UFO 43 EVERYTHING IS ILLUMINATED by daniela lotta INSPIRED BY NATURE AND ITS “ MYSTERIOUS BEAUTY” 48 WILLIAMSBURG’S LATENT DYNAMISM by giordano pozzi 54 THE HOUSE OF EQUISETUM by lorenzo rebediani ARTIFICIAL PARADISE 62 FLASHBACK: 1981 67 STATE OF MIND: FAWN KRIEGER 72 STATE OF MIND: RESIGN 76 MATERIAL CULTURE by anne shlisler-hughes ON THE FASHION DESIGNER KAL RIEMAN 85 REPUBLISHING: NEW OBSERVATIONS N. 8 88 DESIGN FOR SOCIAL CHANGE ACROSS NYC by hala a.malak 94 PLEASE DO NOT TOUCH by matteo pini ABOUT BONES 99 SNAPSHOT n.2 by jacopo grassi 2 international modern and contemporary art fair We thought we’d hit upon a definitive layout with issue 1 of Fruit of the Forest, but we were wrong! We’ve been mixing things up again, and most WE importantly, we’ve been letting ourselves be bowled over by cities, events and encounters—designers, artists, and new writers—a whole host of ideas and L unexpected perspectives. This is a very special issue. It has taken us a long CO time to put it together; we’ve seen the winter solstice come and go, and we’ve come and gone across the Atlantic a couple of times, but we’ve ME ended up with a wonderful mix of the two places that contribute to our principal genetic make-up: Italy and the United States. -
A Future Without Waste?
A FUTURE WITHOUT WaSTE? Zero Waste in Theory and Practice Edited by Christof Mauch Transformations in Environment and Society 2016 / 3 RCC Perspectives: Transformations in Environment and Society is an open-access publication that exists to record and reflect the activities of the Rachel Carson Center for Environment and Society. The journal provides a forum for examining the interrelationship between environmental and social changes and is designed to inspire new perspectives on humanity and the wider world. RCC Perspectives aims to bridge the gap between scholarly and non-scholarly audiences and encourage international dialogue. All issues of RCC Perspectives are available online. To view past issues, please visit www.environmentandsociety.org/perspectives. A Future without Waste? Zero Waste in Theory and Practice Edited by CHRISTOF MAUCH RCC Perspectives Transformations in Environment and Society 2016 / 3 A Future without Waste? 3 Contents 5 Introduction: The Call for Zero Waste Christof Mauch Visions 15 An Impossible Ideal: The Use and Misuse of Zero Waste Tian Song 27 Learning to Celebrate Our Human Footprint Michael Braungart 33 Why Wait for the Future? There Could be a Present without Waste Herbert Köpnick Lessons 39 Waste Utopias: Lessons from Socialist Europe for the Twenty-First Century Zsuzsa Gille 45 Upcycling in History: Is the Past a Prologue to a Zero-Waste Future? Carl Zimring Transitions 55 Ways Out of the Waste Dilemma: Transforming Communities in the Global South Jutta Gutberlet 69 The Zero Garbage Affair in Bogotá Stefania Gallini Roundtable 81 Working for Zero Waste in Germany: A Discussion across Disciplines Eveline Dürr, Martin Faulstich, Christof Mauch, Heike Rieke, Markus Vogt A Future without Waste? 5 Christof Mauch Introduction: The Call for Zero Waste I The call for zero waste is a recent phenomenon—a reaction to an enormous rise in waste that set in about a hundred years ago and accelerated after World War II.