Thermtrac™SKIN EFFECT HEATING SYSTEMS
Total Page:16
File Type:pdf, Size:1020Kb
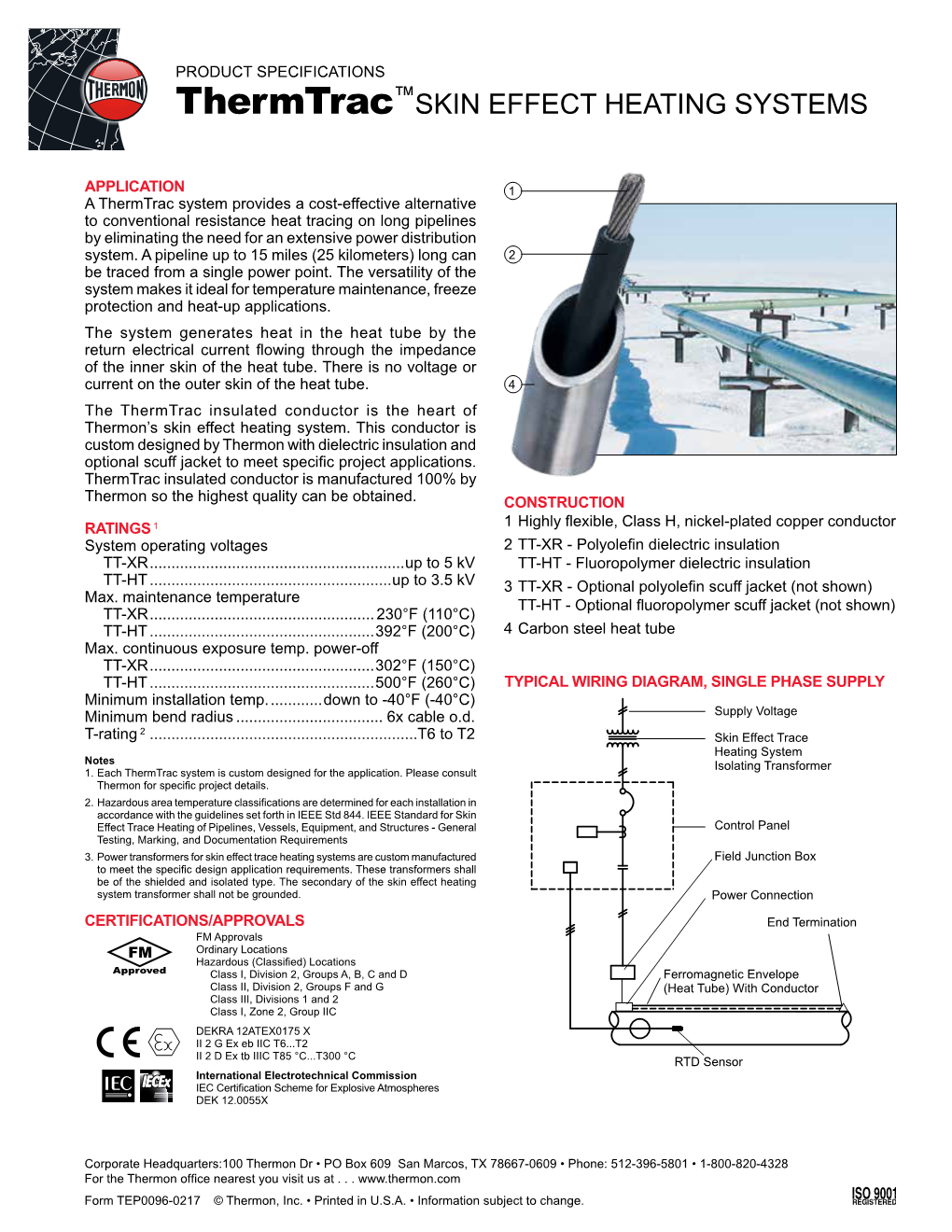
Load more
Recommended publications
-
Electromagnetic Fields and Energy
MIT OpenCourseWare http://ocw.mit.edu Haus, Hermann A., and James R. Melcher. Electromagnetic Fields and Energy. Englewood Cliffs, NJ: Prentice-Hall, 1989. ISBN: 9780132490207. Please use the following citation format: Haus, Hermann A., and James R. Melcher, Electromagnetic Fields and Energy. (Massachusetts Institute of Technology: MIT OpenCourseWare). http://ocw.mit.edu (accessed [Date]). License: Creative Commons Attribution-NonCommercial-Share Alike. Also available from Prentice-Hall: Englewood Cliffs, NJ, 1989. ISBN: 9780132490207. Note: Please use the actual date you accessed this material in your citation. For more information about citing these materials or our Terms of Use, visit: http://ocw.mit.edu/terms 10 MAGNETOQUASISTATIC RELAXATION AND DIFFUSION 10.0 INTRODUCTION In the MQS approximation, Amp`ere’s law relates the magnetic field intensity H to the current density J. � × H = J (1) Augmented by the requirement that H have no divergence, this law was the theme of Chap. 8. Two types of physical situations were considered. Either the current density was imposed, or it existed in perfect conductors. In both cases, we were able to determine H without being concerned about the details of the electric field distribution. In Chap. 9, the effects of magnetizable materials were represented by the magnetization density M, and the magnetic flux density, defined as B ≡ µo(H+M), was found to have no divergence. � · B = 0 (2) Provided that M is either given or instantaneously determined by H (as was the case throughout most of Chap. 9), and that J is either given or subsumed by the boundary conditions on perfect conductors, these two magnetoquasistatic laws determine H throughout the volume. -
Power Transmission Lines the Most Common Methods for Transfer of Electric Power Are: Overhead AC; Underground AC; Overhead DC; Underground DC Distribution Lines
ELG4125: Power Transmission Lines The most common methods for transfer of electric power are: Overhead AC; Underground AC; Overhead DC; Underground DC Distribution Lines Distribution Lines and Transformers Transmission Lines Types of Conductors Aluminum has replaced copper as the most common conductor metal for overhead transmission (Why?). In general, the types of conductors are: solid; stranded; and hollow conductors. Bundled Conductors in Transmission Lines Advantages: Reduced corona loss due to larger cross-sectional area; reduced interference with telecommunication systems; improved voltage regulation. Insulators The insulators used for overhead transmission lines are: Pin; suspension; strain; and shackle. The following figure shows a suspension type (for above 33 kV). Insulator Chain Number of separate discs are joined with each other by using metal links to form a string. The insulator string is suspended from the cross arm of the support. Composite Insulator 1. Sheds to prevent bridging by ice and snow. 2. Fibreglass reinforced resin rod. 3. Rubber weather shed. 4. Forced steel end fitting. Line Post for Holding Two Lines • (1) Clevis ball; (2) Socket for the clevis; (3) Yoke plate; (3) Suspension clamp. Support Structures Wooden poles; tubular poles; RCC poles (above 33 kV); Latticed steel towers (above 66 kV, see below) where double circuit transmission lines can be set on the same tower. Transmission Line Model • A transmission line is a distributed element in which voltage and current depend on both time and space. • A property of a distributed system is that waves can travel both in a forward and reverse direction. • The voltage at any given point is the superposition of the forward and reverse traveling waves. -
Harmonics in Transmission Lines
Institute of Electrical Power Systems Harmonics in Transmission Lines A master thesis by Ali Pouriman Supervisor Ao.Univ.-Prof. Dipl.-Ing. Dr.techn. Renner February 2021 I Harmonics in Transmission Lines Graz University of Technology Institute of Electrical Power Systems Inffeldgasse 18/I 8010 Graz Austria Head of Institute Robert Schürhuber Supervisor Ao.Univ.-Prof. Dipl.-Ing. Dr.techn. Renner A master thesis by Ali Pouriman February 2021 II Harmonics in Transmission Lines Statutory Declaration I declare that I have authored this thesis independently, that I have not used other than the declared sources / resources, and that I have explicitly marked all material which has been quoted either literally or by content from the used sources. Graz, 20.02.2021 Ali Pouriman III Harmonics in Transmission Lines Acknowledgements I would particularly like to thank Professor. Renner, who is my supervisor, cared and provided sources and so many support and tips. Moreover, I am grateful to the company DigSilent for letting me using this great programme module Power Quality/Harmonics for a period of time to make progress and finish my master degree accurately. A very special thanks to my parents and siblings for being patience and supportive to me all time therefore without their support and encouragement it was tough to reach my goals. At the end, my warm and best regards and many thanks to the following people Mrs. Renate Muhry and Mag. Heinz Schubert. IV Harmonics in Transmission Lines Abstract This master thesis presents the general information about harmonics and which consequences they have. After that a simplified high voltage network is used as a study case. -
Reduction of Rf Power Loss Caused by Skin Effect Y
THP43 Proceedings of LINAC 2004, Lübeck, Germany REDUCTION OF RF POWER LOSS CAUSED BY SKIN EFFECT Y. Iwashita, ICR, Kyoto Univ., Kyoto, JAPAN Abstract Skin effect on a metal foil that is thinner than a skin depth is investigated starting from general derivation of skin depth on a bulk conductor. The reduction of the Figure 1: Half of the space is filled by conductor. power loss due to the skin effect with multi-layered conductors is reported and discussed. A simple application on a dielectric cavity is presented. INTRODUCTION RF current flows on a metal surface with only very thin skin depth, which decreases with RF frequency. Thus the surface resistance increases with the frequency. Because the skin depth also decreases when the metal conductivity increases, the improvement of the conductivity does not contribute much; it is only an inverse proportion to the square root of the conductivity. Recently, it is shown Figure 2: Left: j as a function of x/$. Right: polar plot. that such a power loss can be reduced on a dielectric Markers are put in every unit. cavity with thin conductor layers on the surface, where Although it is necessary to increase the conductance for the layers are thinner than the skin depth [1]. The thin lower RF power loss, the higher conductance leads to foil case is analyzed after a review of the well-known higher current density and thus the thinner skin depth theory of the skin effect. Then an application to a reduces the improvement by the good conductance. It dielectric cavity with TM0 mode is discussed [2]. -
Skin Effect on Wire
Application Note Skin Effect on Wire This application note discusses material effect on skin depth on an electrical conductor such as wire. What is Skin Effect? Skin effect can be defined as the tendency for alternating electric current (AC) to flow mostly near the outer surface of an electrical conductor, and not through the core. The term “skin” refers to the outer surface of the conductor. “Depth” is used to describe the depth of the skin where the current is flowing. Skin depth can also be thought of as a measurement of distance over which the current falls from its original value. The decline in current density (electrical current in a given area) versus depth is known as the skin effect. The skin effect causes the effective resistance of the electrical conductor to increase as the frequency of the current increases. This occurs because most of the conductor is carrying very little of the current, and because of the oscillation of the electrical AC current to the skin of the conductor. Therefore, at high frequencies of current skin depth is small. Analyzing skin depth helps to determine the material properties of a good conductor on a solid conductive wire. The skin depth formula equation below can be utilized to determine skin depth effect on a solid conductive material: Skin effect occurs when frequencies start to increase, and as conduction starts to move from the inner cross section of the conductor toward the outer surface of the cross sectional of the conductor. Skin effect is mainly cause by circulating eddy currents. -
The, Skin .Effect
366 PHILlPS TECHNICAL REVIEW VOLUME 28 The, skin .effect Ill. The skin effect ill superconductors H. B. G. Casimir and J. Ubbink In parts I and II of this article we studied the skin tron in an electric field, a new equation for the current. effect in ordinary metals possessing finite conduc- In terms of the skin effect their hypothesis might be for- tivity [1]. In this third part we shall consider the skin mulated by saying that a superconductor, even at zero effect in metals that are in the superconducting state [2]. frequency, behaves like a normal metal in the relaxa- The superconducting state is limited to temperatures tion limit. Thus, even at W = 0, they find a penetration and magnetic fields that do not exceed certain depth equal to the relaxation skin depth Ap if all elec- critical values. Between the critical field He and the trons are superconducting; if, more generally, ns is the temperature Tthere exists the empirical relation: concentration of the superconducting electrons, the "London penetration depth" is AL = V(mjf-lnse2j. Thè , HcjHco = 1- (TjTc)2, (1) fact that this is a new hypothesis, and cannot be where He» is the critical field at T = 0 and Tc the deduced by taking the limit for a -+ 00 of a normal critical temperature at H = O. conductor, is immediately apparent from fig. 1, an The most striking property of a superconductor is its W-7: diagram like fig. 11 in part Il. For 7: -+ 00 at low zero resistance to direct current; not merely extremely frequencies we do not arrive in the relaxation region B low but really zero, as is evident from the existence of or E but in the region of the anomalous skin effect D. -
RF for Mes Belomestnykh.Pptx
RF fundamentals for mechanical engineers Lecture 1: Transmission lines and S-parameters Sergey Belomestnykh BNL April 19, 2011 RF lectures for Mechanical Engineers BNL April 19 & 21, 2011 Introduction to lectures ² The goal of these lectures is to provide C-AD mechanical engineers some background in RF. ² The formulae for the most part will not be derived, but rather given with (hopefully) sufficient explanations. ² We are not in a position to cover all topics, but just a few directly related to developing accelerating structures. RF circuits, power generation, LLRF, etc. will not be covered. Most of the topics came from the original request of Steve Bellavia. ² The material is split into three lectures that will be delivered during two one-hour sessions on April 19th (3:00 pm to 4:00 pm) and April 21st (10:00 am to 11:00 am). ¨ Lecture 1 – S. Belomestnykh – April 19: Transmission lines and S-parameters. ¨ Lecture 2 – Q. Wu – April 19 & 21: Resonant cavities (pill-box, elliptical cavities, quarter-wave and half-wave resonators), figures of merits. ¨ Lecture 3 – W. Xu – April 21: Input couplers, multipacting, HOM couplers. April 19, 2011 S. Belomestnykh: Transmission lines, matching, S parameters 2 Outline ¨ What is an RF transmission line? ¨ Transmission line parameters. ¨ Reflection. ¨ Impedance transformation in transmission lines. ¨ S-parameters. ¨ Common types of transmission lines used in accelerators: Coaxial line and Rectangular waveguide. April 19, 2011 S. Belomestnykh: Transmission lines, matching, S parameters 3 What is an RF transmission line? ¨ In general, a transmission line is a medium or structure that forms a path to direct energy from one place to another. -
Dissipative (Lossy) Media
Dissipative (Lossy) Media In a lossy medium ( > 0), a wave will lose energy by heating up that medium, and the fields will decrease exponentially in the direction of propagation. Returning to the wave equation, and including the conductivity term, we get: 2222Ej E E E0 ±z E0e will continue to be a solution, and will be a complex number phase shift and attenuation D H JJjDJjEEjEjjE t 22j jj e j Complex Wavenumber & Penetration Depth The imaginary part of accounts for phase shift as the wave propagates, and the real part accounts for attenuation. Consider an x-polarized wave propagating in the z direction: zzjzjz E(z)x Ee00 Ee Ee 0 e z Etze0 cos Skin Depth (s): the distance at which E is reduced to 37% of its incident value. This is also called penetration depth. Ex 1 d p 1 0.37EEeEe00 0 s E0 0.37E 0 z 1 Exact & Approximate Formulas Exact 1 1 2 2 2 jjjj 111 2 Good Conductor j f Good Dielectric (low-loss dielectric) 2 1 = 1 28 2 31 1 j 82 Loss Tangent Loss Tangent is often used to determine how lossy a medium is at a particular frequency. It is the ratio of the conduction current to the displacement current. E Loss Tangent E Example: what is the skin depth and loss tangent in bottom round steak at microwave oven frequencies (2.45 GHz)? =1 S/m & r=40 1 2 2 1 1 1 1 28.8 Nepers / m so s m 0.034 m 1.3" 2 28.8 1 loss tangent = 0.184 2 2.45 10912 40 8.85 10 2 Loss Tangent Examples Loss Tangent at Freq. -
Influence of Corona and Skin Effect on the Nigerian 330Kv Interconnected Power System
IJRRAS 12 (2) ● August 2012 www.arpapress.com/Volumes/Vol12Issue2/IJRRAS_12_2_21.pdf INFLUENCE OF CORONA AND SKIN EFFECT ON THE NIGERIAN 330KV INTERCONNECTED POWER SYSTEM M.C. Anumaka Department of Electrical Electronic Engineering, Faculty of Engineering, Imo State University, Owerri, Imo State, Nigeria Email: [email protected] ABSTRACT The geographical location of Nigeria has made the country prone to natural and environmental hazards, which drastically affect the transmission network in the country. The Northern part of the country is hilly and mountainous, while the Southern part has equatorial climate with high humidity and rainfall. The consequence is ionization of air surrounding the conductor and the generation of skin effect. This paper reviews the adverse actions of corona loss and skin effect on the Nigerian 330KV transmission lines and proffers dependable solution to these problems. Keywords: Technical loss, Corona loss, Skin effect, Bundled conductors. 1. INTRODUCTION The Nigerian power system is largely affected by climatic condition. The Southern part starts with mangrove forests which is interspersed by a network of rivers and creeks. It transits to tropical rain forest further inland and progresses into savannah region in the North. The climate in the Southern area is equatorial with high humidity and rain fall [1]. Large proportion of the transmission network located in the Southern region of the country experience fog and humidity weather. The Northern areas are semi-equatorial with low humidity and rainfall. The air in the North is not perfect insulator and contains electrons and ions as a result of various effects like ultra violet rays of the sun, cosmic rays, radio activity of the soil, etc [2]. -
Electron Energy Distributions and Anomalous Skin Depth Effects in High-Plasma-Density Inductively Coupled Discharges
PHYSICAL REVIEW E 66, 066411 ͑2002͒ Electron energy distributions and anomalous skin depth effects in high-plasma-density inductively coupled discharges Alex V. Vasenkov* and Mark J. Kushner† Department of Electrical and Computer Engineering, University of Illinois, 1406 West Green Street, Urbana, Illinois 61801 ͑Received 19 July 2002; published 19 December 2002͒ Electron transport in low pressure ͑Ͻ10s mTorr͒, moderate frequency ͑Ͻ10s MHz͒ inductively coupled plasmas ͑ICPs͒ displays a variety of nonequilibrium characteristics due to their operation in a regime where the mean free paths of electrons are significant fractions of the cell dimensions and the skin depth is anomalous. Proper analysis of transport for these conditions requires a kinetic approach to resolve the dynamics of the electron energy distribution ͑EED͒ and its non-Maxwellian character. To facilitate such an investigation, a method was developed for modeling electron-electron collisions in a Monte Carlo simulation and the method was incorporated into a two-dimensional plasma equipment model. Electron temperatures, electron densities, and EEDs obtained using the model were compared with measurements for ICPs sustained in argon. It was found that EEDs were significantly depleted at low energies in regimes dominated by noncollisional heating, typically within the classical electromagnetic skin depth. Regions of positive and negative power deposition were observed for conditions where the absorption of the electric field was both monotonic and nonmonotonic. DOI: 10.1103/PhysRevE.66.066411 PACS number͑s͒: 52.27.Ϫh, 52.80.Pi, 52.20.Fs, 52.50.Qt I. INTRODUCTION are resolved on a particle-mesh basis. This approach is also computationally robust while introducing some approxima- The trend towards using high plasma density tion in the dynamics of the e-e collisions. -
Designing High Frequency Planar Transformers
Helping to Power Your Next Great Idea DESIGNING HIGH FREQUENCY PLANAR TRANSFORMERS Abstract The demand for high efficiency, higher density power supplies, creates new challenges for designers of high frequency (HF) planar transformers. In order for the power system to achieve the desired efficiency, the transformer losses have to be calculated precisely. This paper will describe a step by step procedure for designing HF planar transformers and give an overview of the two predominant causes of conductor loss (Skin and Proximity effects) in multi-layer PCB transformer designs. Introduction In the majority of conventional transformer designs, calculating the total power loss was limited to core and copper losses (I^2 * Rdc). In today's HF, multilayer planar design, two effects, Skin and Proximity, increase the resistance of a winding above the DC resistance value. In an effort to understand these loss effects, and provide a meaningful and comprehensive way to calculate them, Pulse has devoted significant engineering resources to understanding and documenting these phenomena. As a result, Pulse is in a strong position to support Electrical Engineers who incorporate planar transformers into their designs. The following article is intended to help design engineers understand the dominant loss factors and how planar products are the best choice to achieve efficiency gains in future generation power supply circuits. Calculating DC copper losses without Skin and Proximity analysis can cause a significant error in winding loss calculation. This forces the designer to calculate the AC resistance of a winding to arrive at an estimate of power loss. This AC resistance is measured by multiplying the DC resistance of the winding by a correction factor called "Fr(m,x)" . -
Transmission Line Parameters
13 Transmission Line Parameters 13.1 Equivalent Circuit ........................................................... 13-1 13.2 Resistance ......................................................................... 13-2 Frequency Effect . Temperature Effect . Spiraling and Bundle Conductor Effect 13.3 Current-Carrying Capacity (Ampacity) ........................ 13-5 13.4 Inductance and Inductive Reactance............................. 13-6 Inductance of a Solid, Round, Infinitely Long Conductor . Internal Inductance Due to Internal Magnetic Flux . External Inductance . Inductance of a Two-Wire Single-Phase Line . Inductance of a Three-Phase Line . Inductance of Transposed Three-Phase Transmission Lines 13.5 Capacitance and Capacitive Reactance........................ 13-14 Capacitance of a Single-Solid Conductor . Capacitance of a Single-Phase Line with Two Wires . Capacitance of a Three-Phase Line . Capacitance of Stranded Bundle Manuel Reta-Herna´ndez Conductors . Capacitance Due to Earth’s Surface Universidad Auto´ noma de Zacatecas 13.6 Characteristics of Overhead Conductors .................... 13-28 The power transmission line is one of the major components of an electric power system. Its major function is to transport electric energy, with minimal losses, from the power sources to the load centers, usually separated by long distances. The design of a transmission line depends on four electrical parameters: 1. Series resistance 2. Series inductance 3. Shunt capacitance 4. Shunt conductance The series resistance relies basically on the physical composition of the conductor at a given temperature. The series inductance and shunt capacitance are produced by the presence of magnetic and electric fields around the conductors, and depend on their geometrical arrangement. The shunt conductance is due to leakage currents flowing across insulators and air. As leakage current is considerably small compared to nominal current, it is usually neglected, and therefore, shunt conductance is normally not considered for the transmission line modeling.