Machine Learning in Predictive Maintenance Towards Sustainable Smart Manufacturing in Industry 4.0
Total Page:16
File Type:pdf, Size:1020Kb
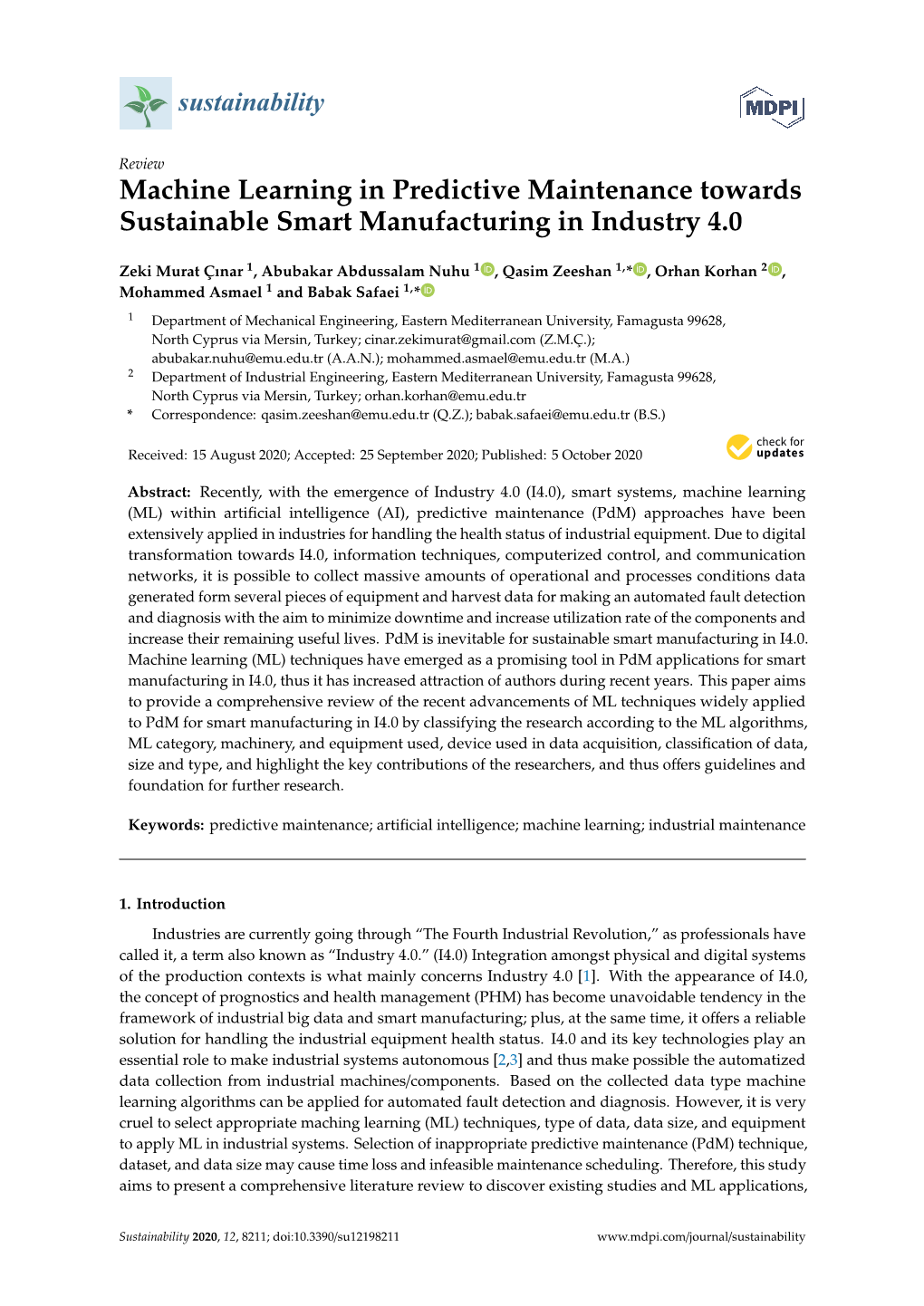
Load more
Recommended publications
-
Industrial Big Data Analytics for Quality Improvement in Complex Systems
Industrial Big Data Analytics for Quality Improvement in Complex Systems Dr. Kaibo Liu Department of Industrial and Systems Engineering University of Wisconsin-Madison 1 Lab for System Informatics and Data Analytics (SIDA) Background • A.P. 2013-now, Department of industrial and Systems Engineering, UW-Madison • Ph.D. 2013, Industrial Engineering (Minor: Machine Learning), Georgia Institute of Technology • M.S. 2011, Statistics, Georgia Institute of Technology • B.S. 2009, Industrial Engineering and Engineering Management, Hong Kong University of Science and Technology, Hong Kong 2 Lab for System Informatics and Data Analytics (SIDA) My Research & Expertise Research Interests Expertise System Informatics and data analytics: • Complex system modeling and Engineering performance assessment Multidisciplinary approach • Data fusion for online process monitoring, diagnosis and prognostics Operation Statistics/ Research/ Machine • Statistical learning, data mining, and Control Learning decision making Multi-disciplinary Research Sensor Measurement System Degradation Spatiotemporal Field and Monitoring Strategy Analysis and Prognostics Modeling and Prediction Overall, my research goal is to make sense of big data for better decision making! 3 Lab for System Informatics and Data Analytics (SIDA) Sensor Measurement and Monitoring Strategy 4 Lab for System Informatics and Data Analytics (SIDA) Objective-oriented sensor system designs in complex systems Objective Approaches • Obtain an optimal sensor allocation design at • A best allocation subsets -
Predictive Maintenance and Intelligent Sensors in Smart Factory: Review
sensors Review Predictive Maintenance and Intelligent Sensors in Smart Factory: Review Martin Pech , Jaroslav Vrchota * and Jiˇrí Bednáˇr Department of Management, Faculty of Economics, University of South Bohemia in Ceske Budejovice, Studentska 13, 370 05 Ceske Budejovice, Czech Republic; [email protected] (M.P.); [email protected] (J.B.) * Correspondence: [email protected] Abstract: With the arrival of new technologies in modern smart factories, automated predictive maintenance is also related to production robotisation. Intelligent sensors make it possible to obtain an ever-increasing amount of data, which must be analysed efficiently and effectively to support increasingly complex systems’ decision-making and management. The paper aims to review the current literature concerning predictive maintenance and intelligent sensors in smart factories. We focused on contemporary trends to provide an overview of future research challenges and classification. The paper used burst analysis, systematic review methodology, co-occurrence analysis of keywords, and cluster analysis. The results show the increasing number of papers related to key researched concepts. The importance of predictive maintenance is growing over time in relation to Industry 4.0 technologies. We proposed Smart and Intelligent Predictive Maintenance (SIPM) based on the full-text analysis of relevant papers. The paper’s main contribution is the summary and overview of current trends in intelligent sensors used for predictive maintenance in smart factories. Citation: Pech, M.; Vrchota, J.; Keywords: intelligent sensors; maintenance; smart factory; Industry 4.0 Bednáˇr,J. Predictive Maintenance and Intelligent Sensors in Smart Factory: Review. Sensors 2021, 21, 1470. https://doi.org/10.3390/ 1. Introduction s21041470 Industry sets the direction for the world economy, accounting for more than 70% of Academic Editors: Susana Vieira, the world’s total material production [1], depending on the regional economy’s develop- João Figueiredo and João Miguel da ment. -
Service Innovation and Smart Analytics for Industry 4.0 and Big Data Environment
Available online at www.sciencedirect.com ScienceDirect Procedia CIRP 16 ( 2014 ) 3 – 8 Product Services Systems and Value Creation. Proceedings of the 6th CIRP Conference on Industrial Product-Service Systems Service innovation and smart analytics for Industry 4.0 and big data environment Jay Lee*, Hung-An Kao, Shanhu Yang NSF I/UCRC Center for Intelligent Maintenance Systems (IMS), University of Cincinnati, Cincinnati, OH 45221-0072, USA * Corresponding author. Tel.: +1-513-556-3412; fax: +1-513-556-4647. E-mail address: [email protected] Abstract Today, in an Industry 4.0 factory, machines are connected as a collaborative community. Such evolution requires the utilization of advance- prediction tools, so that data can be systematically processed into information to explain uncertainties, and thereby make more “informed” decisions. Cyber-Physical System-based manufacturing and service innovations are two inevitable trends and challenges for manufacturing industries. This paper addresses the trends of manufacturing service transformation in big data environment, as well as the readiness of smart predictive informatics tools to manage big data, thereby achieving transparency and productivity. © 2014 TheElsevier Authors. B.V. Pub Thislished is an by open Elsevier access B.V. article under the CC BY-NC-ND license Selection(http://creativecommons.org/licenses/by-nc-nd/3.0/ and peer-review under responsibility of the Internationa). l Scientific Committee of “The 6th CIRP Conference on Industrial Product- ServiceSelection Systems” and peer-review in the person under of the responsibility Conference ofChair the ProfessorInternational Hoda Scientifi ElMaraghy. c Committee of “The 6th CIRP Conference on Industrial Product-Service Systems” in the person of the Conference Chair Professor Hoda ElMaraghy” Keywords: Manufacturing servitization; predictive maintenance; industrial big data 1. -
Industrial Big Data Analytics: Challenges, Methodologies, and Applications
SUBMITTED TO IEEE TRANSACTIONS ON AUTOMATION SCIENCE AND ENGINEERING 1 Industrial Big Data Analytics: Challenges, Methodologies, and Applications JunPing Wang, Member, IEEE, WenSheng Zhang, YouKang Shi, ShiHui Duan, Abstract—While manufacturers have been generating highly 5,000 data samples every 33 milliseconds, resulting in [1]. Big distributed data from various systems, devices and applications, a data analytics will be vital foundation for forecasting number of challenges in both data management and data analysis manufacturing, machine fleet, and proactive maintenance. require new approaches to support the big data era. These challenges Compared to big data in general, industrial big data has the for industrial big data analytics is real-time analysis and decision- potential to create value in different sections of manufacturing making from massive heterogeneous data sources in manufacturing business chain [2]. For example, valuable information space. This survey presents new concepts, methodologies, and applications scenarios of industrial big data analytics, which can regarding the hidden degradation or inefficiency patterns within provide dramatic improvements in velocity and veracity problem machines or manufacturing processes can lead to informed and solving. We focus on five important methodologies of industrial big effective maintenance decisions which can avoid costly failures data analytics: 1) Highly distributed industrial data ingestion: access and unplanned downtime. However, the ability to perform and integrate to highly distributed data sources from various systems, analysis on the data is constrained by the increasingly devices and applications; 2) Industrial big data repository: cope with distributed nature of industrial data sets. Highly distributed data sampling biases and heterogeneity, and store different data formats sources bring about challenges in industrial data access, and structures; 3) Large-scale industrial data management: organizes integration, and sharing. -
Deep Learning in Industrial Internet of Things: Potentials, Challenges, And
1 Deep Learning in Industrial Internet of Things: Potentials, Challenges, and Emerging Applications Ruhul Amin Khalil Student Member, IEEE, Nasir Saeed Senior Member, IEEE, Yasaman Moradi Fard, Tareq Y. Al-Naffouri, Senior Member, IEEE, Mohamed-Slim Alouini, Fellow, IEEE Abstract—The recent advancements in the Internet of Things digital transformation in many industries is accelerating [12]– (IoT) are giving rise to the proliferation of interconnected [18]. With strong alliances between leading IIoT stakeholders devices, enabling various smart applications. These enormous and proven IIoT applications, inspire companies worldwide number of IoT devices generates a large capacity of data that further require intelligent data analysis and processing methods, to invest in the IIoT market, which is expected to grow up to such as Deep Learning (DL). Notably, the DL algorithms, $123.89 billion by 2021 (see Fig. 1). Throughout the literature, when applied in the Industrial Internet of Things (IIoT), can various terms are used to describe IoT for the industry, such enable various applications such as smart assembling, smart IIoT, smart manufacturing, and Industry 4.0 [19]–[22]. The manufacturing, efficient networking, and accident detection-and- step towards this smart production technology or IIoT is way prevention. Therefore, motivated by these numerous applications; in this paper, we present the key potentials of DL in IIoT. different from past technologies; therefore, it is also called First, we review various DL techniques, including convolutional the Industrial Revolution. The newly IIoT technology will neural networks, auto-encoders, and recurrent neural networks explicitly change the overall working conditions and day to and there use in different industries. -
Big Data Semantics in Industry 4.0
Big Data Semantics in Industry 4.0 Marek Obitko1() and Václav Jirkovský1,2 1 Rockwell Automation Research and Development Center, Pekařská 695/10a, Prague, Czech Republic {mobitko,vjirkovsky}@ra.rockwell.com 2 Czech Technical University in Prague, Zikova 4, Prague, Czech Republic Abstract. The Industry 4.0 is a vision that includes connecting more intensively physical systems with their virtual counterparts in computers. This computeri- zation of manufacturing will bring many advantages, including allowing data gathering, integration and analysis in the scale not seen earlier. In this paper we describe our Semantic Big Data Historian that is intended to handle large vo- lumes of heterogeneous data gathered from distributed data sources. We de- scribe the approach and implementation with a special focus on using Semantic Web technologies for integrating the data. Keywords: Industry 4.0 · Cyber-Physical Systems · Big Data · Semantics · Internet of Things · Industrial automation · Heterogeneity 1 Introduction One of the issues that the automation industry has to handle more and more is the amount of data that needs to be processed and analyzed for rapid decision making for improved productivity. The need for smart analytics tools is emphasized by so called “Industry 4.0”, which is a transformation towards the fourth industrial revolution. It is an effort led by Germany with the vision to connect physical systems, such as manu- facturing plants, with virtual models in computers, which will allow and provide au- tomation in the scale not seen earlier. This movement can be in short described as the “computerization of manufacturing.” In this paper we discuss our contribution that we call Semantic Big Data Historian which is intended to handle large volumes of heterogeneous data gathered from dis- tributed data sources, such as sensors. -
The Role of Big Data Analytics in Industrial Internet of Things
Future Generation Computer Systems 99 (2019) 247–259 Contents lists available at ScienceDirect Future Generation Computer Systems journal homepage: www.elsevier.com/locate/fgcs The role of big data analytics in industrial Internet of Things ∗ Muhammad Habib ur Rehman a, , Ibrar Yaqoob b, Khaled Salah c, Muhammad Imran d, Prem Prakash Jayaraman e, Charith Perera f a National University of Computer and Emerging Sciences, Lahore, Pakistan b Department of Computer Science and Engineering, Kyung Hee University, Yongin-si 17104, South Korea c Department of Electrical and Computer Engineering, Khalifa University, United Arab Emirates d College of Computer and Information Sciences, King Saud University, Riyadh, Saudi Arabia e Department of CS & SE, Swinburne University of Technology, VIC 3122, Australia f School of Computer Science and Informatics, Cardiff University, United Kingdom h i g h l i g h t s • We investigate the state-of-the-art research studies conducted on IIoT in terms of BDA. • We build a case of BDA for IIoT systems, and classify the literature by devising a taxonomy. • We present frameworks and case studies where BDA processes were used in IIoT systems. • We present several research opportunities, challenges, and future technologies. article info a b s t r a c t Article history: Big data production in industrial Internet of Things (IIoT) is evident due to the massive deployment Received 2 June 2018 of sensors and Internet of Things (IoT) devices. However, big data processing is challenging due Received in revised form 11 February 2019 to limited computational, networking and storage resources at IoT device-end. -
Big Data Analytics for Predictive Maintenance Strategies C.K.M
This is the Pre-Published Version. Big Data Analytics for Predictive Maintenance Strategies C.K.M. LEE The Hong Kong Polytechnic University, China Yi CAO The Hong Kong Polytechnic University, China K.K.H. NG The Hong Kong Polytechnic University, China ABSTRACT Maintenance aims to reduce and eliminate the number of failures occurred during production as any breakdown of machine or equipment may lead to disruption for the supply chain. Maintenance policy is set to provide the guidance for selecting the most cost-effective maintenance approach and system to achieve operational safety. For example, predictive maintenance is most recommended for crucial components whose failure will cause severe function loss and safety risk. Recent utilization of big data and related techniques in predictive maintenance greatly improves the transparency for system health condition and boosts the speed and accuracy in the maintenance decision making. In this chapter, a Maintenance Policies Management framework under Big Data Platform is designed and the process of maintenance decision support system is simulated for a sensor-monitored semiconductor manufacturing plant. Artificial Intelligence is applied to classify the likely failure patterns and estimate the machine condition for the faulty component. Keywords: MAINTENANCE POLICIES MANAGEMENT, MAINTENANCE DECISION SUPPORT SYSTEM, FUZZY LOGIC, ARTIFICIAL NEURAL NETWORK, DIAGONSIS AND PROGNOSIS, HEALTH CONDITION ASSESSMENT, MACHINE FAILURE PREDICTION, SENSOR-BASED PREDICTION INTRODUCTION Maintenance can be defined as all actions which are necessary to retain or restore a system and a unit to a state, which is necessary to fulfill its intended function. The main objective of maintenance is to preserve the capability and the functionality of the system while controlling the cost induced by maintenance activities and the potential production loss. -
An Analytics Environment Architecture for Industrial Cyber-Physical Systems Big Data Solutions
sensors Article An Analytics Environment Architecture for Industrial Cyber-Physical Systems Big Data Solutions Eduardo A. Hinojosa-Palafox 1 , Oscar M. Rodríguez-Elías 1,* , José A. Hoyo-Montaño 1 , Jesús H. Pacheco-Ramírez 2 and José M. Nieto-Jalil 3 1 División de Estudios de Posgrado e Investigación, Tecnológico Nacional de México/I. T. de Hermosillo, Hermosillo, Sonora 83170, Mexico; [email protected] (E.A.H.-P.); [email protected] (J.A.H.-M.) 2 Departamento de Ingeniería Industrial, Universidad de Sonora, Hermosillo, Sonora 83000, Mexico; [email protected] 3 Escuela de Ingeniería y Ciencias, ITESM Sonora, Hermosillo, Sonora 83000, Mexico; [email protected] * Correspondence: [email protected] Abstract: The architecture design of industrial data analytics system addresses industrial process challenges and the design phase of the industrial Big Data management drivers that consider the novel paradigm in integrating Big Data technologies into industrial cyber-physical systems (iCPS). The goal of this paper is to support the design of analytics Big Data solutions for iCPS for the modeling of data elements, predictive analysis, inference of the key performance indicators, and real-time analytics, through the proposal of an architecture that will support the integration from IIoT Citation: Hinojosa-Palafox, E.A.; environment, communications, and the cloud in the iCPS. An attribute driven design (ADD) approach Rodríguez-Elías, O.M.; has been adopted for architectural design gathering requirements from smart production planning, Hoyo-Montaño, J.A.; manufacturing process monitoring, and active preventive maintenance, repair, and overhaul (MRO) Pacheco-Ramírez, J.H.; scenarios. Data management drivers presented consider new Big Data modeling analytics techniques Nieto-Jalil, J.M. -
Framework of an Iot-Based Industrial Data Management for Smart Manufacturing
Journal of Sensor and Actuator Networks Article Framework of an IoT-based Industrial Data Management for Smart Manufacturing Muhammad Saqlain 1 , Minghao Piao 2 , Youngbok Shim 3 and Jong Yun Lee 1,* 1 Department of Computer Science, Chungbuk National University, Cheongju, Chungbuk 28644, Korea; [email protected] 2 Department of Smart Factory Management, Chungbuk National University, Cheongju, Chungbuk 28644, Korea; [email protected] 3 Department of Digital Information Convergence, Chungbuk National University, Cheongju, Chungbuk 28644, Korea; [email protected] * Correspondence: [email protected]; Tel.: +82(0)-43-261-2789 Received: 25 March 2019; Accepted: 26 April 2019; Published: 28 April 2019 Abstract: The Internet of Things (IoT) is the global network of interrelated physical devices such as sensors, actuators, smart applications, objects, computing devices, mechanical machines, and people that are becoming an essential part of the internet. In an industrial environment, these devices are the source of data which provide abundant information in manufacturing processes. Nevertheless, the massive, heterogeneous, and time-sensitive nature of the data brings substantial challenges to the real-time collection, processing, and decision making. Therefore, this paper presents a framework of an IoT-based Industrial Data Management System (IDMS) which can manage the huge industrial data, support online monitoring, and control smart manufacturing. The framework contains five basic layers such as physical, network, middleware, database, and application layers to provide a service-oriented architecture for the end users. Experimental results from a smart factory case study demonstrate that the framework can manage the regular data and urgent events generated from various factory devices in the distributed industrial environment through state-of-the-art communication protocols. -
Industrial Big Data Analytics: Challenges, Methodologies, and Applications Junping Wang, Member, IEEE, Wensheng Zhang, Youkang Shi, Shihui Duan, Jin Liu
SUBMITTED TO IEEE TRANSACTIONS ON AUTOMATION SCIENCE AND ENGINEERING 1 Industrial Big Data Analytics: Challenges, Methodologies, and Applications JunPing Wang, Member, IEEE, WenSheng Zhang, YouKang Shi, ShiHui Duan, Jin Liu Abstract—While manufacturers have been generating highly maintenance decisions which can avoid costly failures and distributed data from various systems, devices and applications, a unplanned downtime. However, the ability to perform analysis number of challenges in both data management and data analysis on the data is constrained by the increasingly distributed nature require new approaches to support the big data era. These of industrial data sets. Highly distributed data sources bring challenges for industrial big data analytics is real-time analysis about challenges in industrial data access, integration, and shar- and decision-making from massive heterogeneous data sources in ing. Furthermore, massive data produced by different sources manufacturing space. This survey presents new concepts, method- ologies, and applications scenarios of industrial big data analytics, are often defined using different representation methods and which can provide dramatic improvements in velocity and verac- structural specifications. Bringing those data together becomes ity problem solving. We focus on five important methodologies of a challenge because the data are not properly prepared for data industrial big data analytics: 1) Highly distributed industrial data integration and management, and the technical infrastructures ingestion: access and integrate to highly distributed data sources lack the appropriate information infrastructure services to from from various systems, devices and applications; 2) Industrial support big data analytics if it remains distributed. big data repository: cope with sampling biases and heterogeneity, Recently, industrial big data analytics has attracted extensive and store different data formats and structures; 3) Large-scale research interests from both academia and industry. -
2015 IEEE International Conference on Big Data
2015 IEEE International Conference on Big Data October 29-November 1, 2015 • Santa Clara, CA, USA 1 Sponsored by 2 2015 IEEE International Conference on Big Data IEEE Big Data 2015 Program Schedule ......................................................................................... 4 Keynote Lectures ............................................................................................................................ 9 Conference Paper Presentations .................................................................................................... 11 Industry and Government Paper Presentations ............................................................................. 18 Panel: Key Challenges for Future Big-Data to Knowledge (BD2K) Technologies .................... 20 Big Data Start-up Showcase ......................................................................................................... 22 Workshops .................................................................................................................................... 23 Specials Sessions .......................................................................................................................... 33 Tutorials ........................................................................................................................................ 41 Posters ........................................................................................................................................... 45 Conference WiFi Instruction........................................................................................................