Influences of the Mixed Licl-Cacl2 Liquid Desiccant Solution On
Total Page:16
File Type:pdf, Size:1020Kb
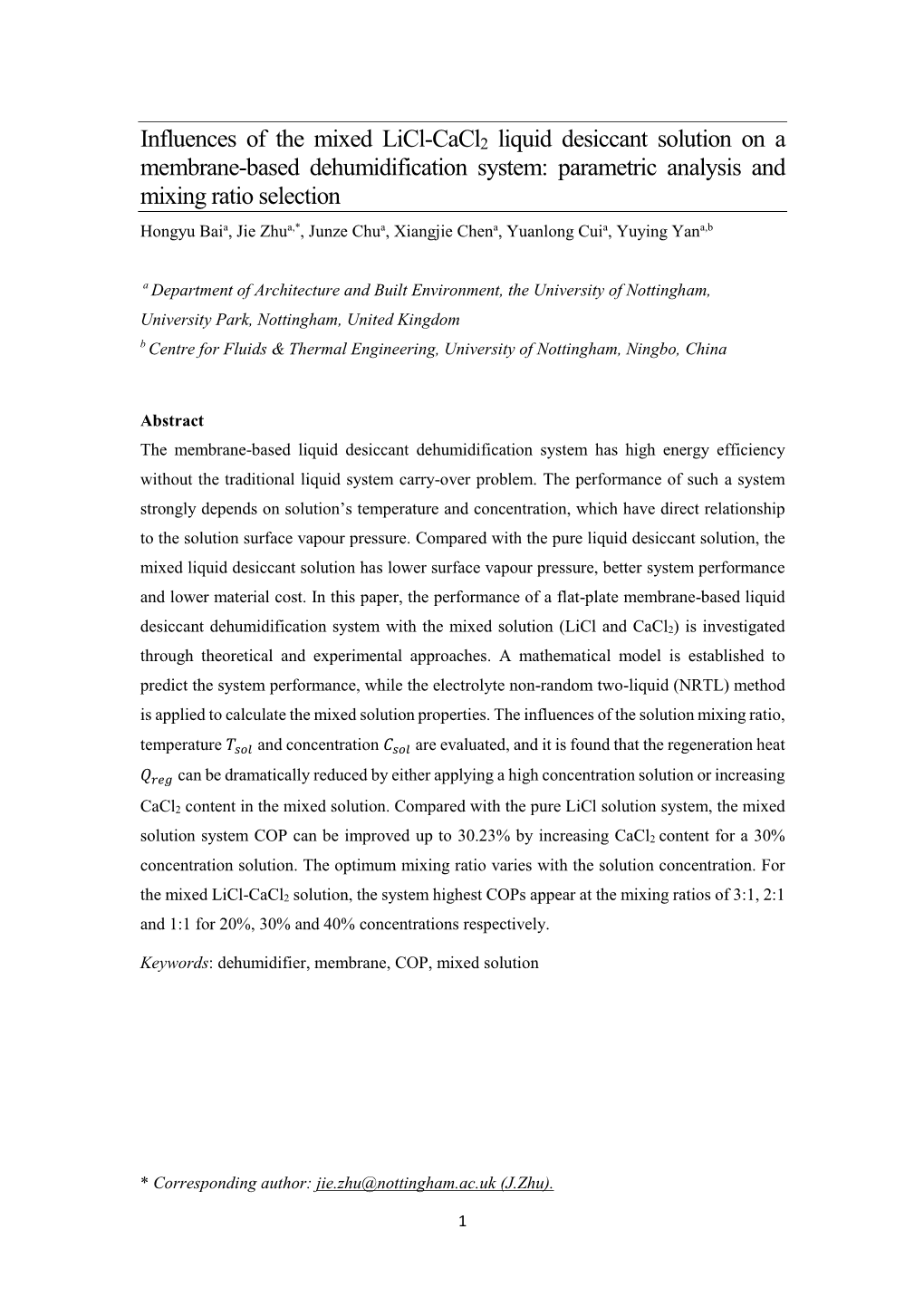
Load more
Recommended publications
-
Vapour Absorption Refrigeration Systems
Lesson 14 Vapour Absorption Refrigeration Systems Version 1 ME, IIT Kharagpur 1 The objectives of this lesson are to: 1. Introduce vapour absorption refrigeration systems (Section 14.1) 2. Explain the basic principle of a vapour absorption refrigeration system (Section 14.2) 3. Compare vapour compression refrigeration systems with continuous vapour absorption refrigeration systems (Section 14.2) 4. Obtain expression for maximum COP of ideal absorption refrigeration system (Section 14.3) 5. Discuss properties of ideal and real refrigerant-absorbent mixtures (Section 14.4) 6. Describe a single stage vapour absorption refrigeration system with solution heat exchanger (Section 14.5) 7. Discuss the desirable properties of refrigerant-absorbent pairs for vapour absorption refrigeration systems and list the commonly used working fluids (Section 14.6) At the end of the lecture, the student should be able to: 1. List salient features of vapour absorption refrigeration systems and compare them with vapour compression refrigeration systems 2. Explain the basic principle of absorption refrigeration systems and describe intermittent and continuous vapour absorption refrigeration systems 3. Find the maximum possible COP of vapour absorption refrigeration systems 4. Explain the differences between ideal and real mixtures using pressure- composition and enthalpy-composition diagrams 5. Draw the schematic of a complete, single stage vapour absorption refrigeration system and explain the function of solution heat exchanger 6. List the desirable properties of working fluids for absorption refrigeration systems and list some commonly used fluid pairs 14.1. Introduction Vapour Absorption Refrigeration Systems (VARS) belong to the class of vapour cycles similar to vapour compression refrigeration systems. However, unlike vapour compression refrigeration systems, the required input to absorption systems is in the form of heat. -
A Simple Theoretical Model of Heat and Moisture Transport in Multi-Layer Garments in Cool Ambient Air
View metadata, citation and similar papers at core.ac.uk brought to you by CORE provided by Loughborough University Institutional Repository This item was submitted to Loughborough’s Institutional Repository (https://dspace.lboro.ac.uk/) by the author and is made available under the following Creative Commons Licence conditions. For the full text of this licence, please go to: http://creativecommons.org/licenses/by-nc-nd/2.5/ A Simple Theoretical Model of Heat and Moisture Transport in Multi-layer Garments in Cool Ambient Air Eugene H. Wissler Department of Chemical Engineering The University of Texas at Austin Austin, Texas, USA George Havenith Environmental Ergonomics Research Group Department of human sciences Loughborough University Loughborough LE11 3TU, UK Tel. No.: (936) 597-9233 e-mail: [email protected] Abstract Overall resistances for heat and vapour transport in a multilayer garment depend on the properties of individual layers and the thickness of any air space between layers. Under uncomplicated, steady-state conditions, thermal and mass fluxes are uniform within the garment, and the rate of transport is simply computed as the overall temperature or water concentration difference divided by the appropriate resistance. However, that simple computation is not valid under cool ambient conditions when the vapour permeability of the garment is low, and condensation occurs within the garment. Several recent studies have measured heat and vapour transport when condensation occurs within the garment (Richards, et al., 2002, and Havenith, et al., 2008). In addition to measuring cooling rates for ensembles when the skin was either wet or dry, both studies employed a flat-plate apparatus to measure resistances of individual layers. -
Evaluating the Vapour Evaporation from the Surface of Liquid Pure Organic Solvents and Their Mixtures
Food Science and Applied Biotechnology, 2020, 3(1), 77-84 Food Science and Applied Biotechnology Journal home page: www.ijfsab.com https://doi.org/10.30721/fsab2020.v3.i1 Research Article Evaluating the vapour evaporation from the surface of liquid pure organic solvents and their mixtures Stepan Akterian1✉ 1 Department of Technology of fats, essential oils, perfumery and cosmetics. Technological Faculty. University of Food Technologies - Plovdiv. Bulgaria Abstract Some perfumery and cosmetic products represent mixtures and they include large parts of solvents as ethanol, water, acetone and isopropyl alcohol. Solvents as pure hexane and ethanol-water mixtures are used in the solvent extraction of oil-bearing plant materials and herbs. The goal of this study was the emissions of volatile solvents released during above pointed productions to be evaluated. It was found that the specific evaporation rate varies from 1.2 kg/(m2.h) (for pure methoxy-propanol) to 66 kg/(m2.h) (for three-component mixture including acetone). The evaporation rate is higher for solvents with higher vapour pressure and at a higher velocity of surrounding air. The evaporation is less intensive from pure solvents than their mixtures. The time for the evaporation from a film of solvents and their mix- tures was also evaluated. It varies from 14 s (for acetone) to 9 min (for methoxy-propanol). Practical applications: The evaluation of volatile solvent emissions is a mandatory step in the design of plants for manufacturing perfumery, cosmetics, deriving essential and edible oils by means of organic solvents. Most of volatile organic solvents used are highly flammable and healthy hazardous. -
Unit 5 Psychometric 2. Explain the Properties of Phychrometry
Unit 5 Psychometric 1. What is psychometry. Atmospheric air makes up the environment in almost every type of air conditioning system. Hence a thorough understanding of the properties of atmospheric air and the ability to analyze various processes involving air is fundamental to air conditioning design. Psychrometry is the study of the properties of mixtures of air and water vapour. Atmospheric air is a mixture of many gases plus water vapour and a number of pollutants (Fig.27.1). The amount of water vapour and pollutants vary from place to place. The concentration of water vapour and pollutants decrease with altitude, and above an altitude of about 10 km, atmospheric air consists of only dry air. The pollutants have to be filtered out before processing the air. Hence, what we process is essentially a mixture of various gases that constitute air and water vapour. This mixture is known as moist air. The moist air can be thought of as a mixture of dry air and moisture. 2. Explain the Properties of Phychrometry The properties of moist air are called psychrometric properties and the subject which deals with the behaviour of moist air is known as psychrometry. Moist air is a mixture of dry air and water vapour. They form a binary mixture. A mixture of two substances requires three properties to completely define its thermodynamic state, unlike a pure substance which requires only two. One of the three properties can be the composition. Water vapour is present in the atmosphere at a very low partial pressure. At this low pressure and atmospheric temperature, the water vapour behaves as a perfect gas. -
Psychrometry Psychrometric Properties Atmospheric Air Makes up the Environment in Almost Every Type of Air Conditioning System
Psychrometry Psychrometric Properties Atmospheric air makes up the environment in almost every type of air conditioning system. Hence a thorough understanding of the properties of atmospheric air and the ability to analyze various processes involving air is fundamental to air conditioning design. Psychrometry is the study of the properties of mixtures of air and water vapour. Atmospheric air is a mixture of many gases plus water vapour and a number of pollutants. The amount of water vapour and pollutants vary from place to place. The concentration of water vapour and pollutants decrease with altitude, and above an altitude of about 10 km, atmospheric air consists of only dry air. The pollutants have to be filtered out before processing the air. Hence, what we process is essentially a mixture of various gases that constitute air and water vapour. This mixture is known as moist air. Fig. Atmospheric air The molecular weight of dry air is found to be 28.966 and the gas constant R is 287.035 J/kgK. The molecular weight of water vapour is taken as 18.015 and its gas constant R is 461.52 J/kgK. 1 Specific Humidity or Humidity Ratio The humidity ratio (or specific humidity) W is the mass of water associated with each kilogram of dry air. Assuming both water vapour and dry air to be perfect gases, the humidity ratio is given by: Substituting the values of gas constants of water vapour and air Rv and Ra in the above equation; the humidity ratio is given by: Specific humidity or absolute humidity or humidity ratio (w) = If Pa and Pv denote respectively the partial pressure of dry air and that of water vapour in moist air, the specific humidity of air is given by (We know Pa = Pb – Pv) 2 Where ф is the relative humidity (in fraction). -
Chapter 6 (Pdf)
6. Fanefjord Church and Gundsømagle Church 109 6 CASE STUDIES IN HUMIDITY BUFFERING BY POROUS WALLS Humidity buffering in the real world The purpose of the experimental part of this thesis has been to give some quantitative support to the concept of using interior walls as buffers for the interior climate, particularly in museums and archives. In this chapter I describe some case histories where the principle of using porous materials as a buffer has been applied in real life. In some of these examples buffering has not been the intent of the builder. Humidity buffering by the walls of Fanefjord Church There are few buildings which are porous right through. Stables and churches are just about the only buildings which have a porous inner surface to the outer walls. They are limewashed and many of the churches are also decorated with ancient paintings. It is the challenge of preserving these paintings that has provided the opportunity to study their microclimate in some detail. The first example is Fanefjord Church on the Danish island of Møn (23). The walls are made of brick, with lime plaster inside Figure 6.1 Fanefjord Church, Møn, and outside. The ceiling is brick vaults. Denmark, from the south west. The climate inside and outside the church is Photo: Poul Klenz Larsen shown in figure 6.2. The inside RH is lower than that outside, as expected, because the church is heated. The diagram also has a line showing the expected inside RH, calculated from the water content of the outside air, operated on by the inside temperature The observed RH is higher than it should be and is remarkably stable at about 45%. -
Revisiting Kelvin Equation and Peng–Robinson Equation of State For
www.nature.com/scientificreports OPEN Revisiting Kelvin equation and Peng–Robinson equation of state for accurate modeling of hydrocarbon phase behavior in nano capillaries Ilyas Al‑Kindi & Tayfun Babadagli* The thermodynamics of fuids in confned (capillary) media is diferent from the bulk conditions due to the efects of the surface tension, wettability, and pore radius as described by the classical Kelvin equation. This study provides experimental data showing the deviation of propane vapour pressures in capillary media from the bulk conditions. Comparisons were also made with the vapour pressures calculated by the Peng–Robinson equation‑of‑state (PR‑EOS). While the propane vapour pressures measured using synthetic capillary medium models (Hele–Shaw cells and microfuidic chips) were comparable with those measured at bulk conditions, the measured vapour pressures in the rock samples (sandstone, limestone, tight sandstone, and shale) were 15% (on average) less than those modelled by PR‑EOS. Abbreviations SAGD Steam assisted gravity drainage C5+ Pentane and higher carbon number hydrocarbons EOR Enhanced oil recovery SOS-FR Steam-over-solvents in fractured reservoir CSS Cyclic steam stimulation EOS Equation-of-state SRP Solvent retrieval process PVT Pressure–volume-temperature CO2 Carbon dioxide PR-EOS Peng–Robinson equation-of-state K Kelvin vL Liquid molar volume r Droplet radius γ Surface tension R Universal gas constant T Temperature P∞ Vapour pressure at fat surface Pr Vapour pressure at curved interface Tr Temperature at porous medium T∞ Temperature at bulk medium Hvap Heat of vaporization Vm Molar volume ZC Critical compressibility factor Department of Civil and Environmental Engineering, School of Mining and Petroleum Engineering, University of Alberta, 7-277 Donadeo Innovation Centre for Engineering, 9211-116th Street, Edmonton, AB T6G 1H9, Canada. -
Design and Performance Analysis of a Modified Vacuum Single Basin Solar Still
Smart Grid and Renewable Energy, 2011, 2, 388-395 doi:10.4236/sgre.2011.24044 Published Online November 2011 (http://www.SciRP.org/journal/sgre) Design and Performance Analysis of a Modified Vacuum Single Basin Solar Still Moses Koilraj Gnanadason1*, Palanisamy Senthil Kumar2, Gopal Sivaraman3, 4 Joseph Ebenezer Samuel Daniel 1Research Scholar, PRIST University, Thanjavur, India; 2Mechanical Engineering Department, KSR College of Engineering, Ti- ruchengode, India; 3Faculty of Mechanical Engineering, PAAVAI Group of Institutions, Pachel, India; 4Faculty of Mechanical Engi- neering, JACSI College of Engineering, Nazareth, India. Email: *[email protected] Received July 26th, 2011; revised September 23rd, 2011; accepted September 30th, 2011. ABSTRACT Water is essential to life. The origin and continuation of mankind is based on water. The supply of drinking water is an important problem for the developing countries. Among the non-conventional methods to desalinate brackish water or seawater, is solar distillation. The solar still is the most economical way to accomplish this objective. Tamilnadu lies in the high solar radiation band and the vast solar potential can be utilized to convert saline water to potable water. The sun’s energy heats water to the point of evaporation. When water evaporates, water vapour rises leaving the impurities like salts, heavy metals and condensate on the underside of the glass cover. Sunlight has the advantage of zero fuel cost but it requires more space and generally more equipment. Solar distillation has low yield, but safe and pure supplies of water in remote areas. In this context, the design modification of a single basin solar still has been discussed to improve the solar still performance through increasing the production rate of distilled water. -
Unit 4 Psychrometry
UNIT 4 PSYCHROMETRY Structure 4.0 Objectives 4.1 Introduction 4.2 . Wet Basis and Dry Basis Moisture. Content and Driage 4.2.1 Grain Moisture Content 4.2.2 Determination of Driage 4.3 Properties of Atmospheric Air 4.3.1 Dry-Bulb Temperature 4.3.2 Wet-Bulb Temperature 4.3.3 Absolute Humidity 4.3.4 Relative Humidity 4.3.5 Percentage Humidity 4.3.6 Specific Volume 4.3.7 Dew Point Temperature 4.3.8 Enthalpy 4.3.9 Vapour Pressure of Water Vapour in Air 4.4 Psychrometric Chart 4.5 Some Applications of Psychrometric Chart 4.5.1 Determination of State Condition 4.5.2 Cooling and Heating 4.5.3 Drying 4.5.4 Mixing of air masses 4.6 Equilibrium Moisture Content, Water Activio/ 4.6.1 Equilibrium Moisture Content 4.6.2 Determination of Equilibrium Moisture Content 4.6.3 Water Activity 4.7 Water Evaporation Principles 4.8 Let Us Sum Up 4.9 Key Words 4.10 Some Useful References 4.11 Answers to Check Your Progress 4.0 OBJECTIVES After reading this unit, you should be able to: • differentiate between wet basis and dry basis moisture content; • define the important thermodynamic properties of humid air; • understand psychrometric chart an its use; 25 Parboiling and Drying • know the importance of equilibrium moisture content and water activity; and Principles • understand the water evoparation theory. 4.1 INTRODUCTION In the field of grain drying, atmospheric air is used as a heat transfer medium. Normal atmospheric air is a mixture of dry air and water vapour, atmospheric air never being completly dry. -
Laboratory and Modelling Study Evaluating Thermal Remediation of Tetrachloroethene and Multi- Component Napl Impacted Soil
LABORATORY AND MODELLING STUDY EVALUATING THERMAL REMEDIATION OF TETRACHLOROETHENE AND MULTI- COMPONENT NAPL IMPACTED SOIL by Chen Zhao A thesis submitted to the Department of Civil Engineering In conformity with the requirements for Master of Applied Science Queen’s University Kingston, Ontario, Canada (September 2013) Copyright © Chen Zhao, 2013 Abstract Dense non-aqueous phase liquids (DNAPLs) such as chlorinated solvents, coal tar and creosote are some of the most problematic groundwater and soil contaminants in industrialized countries throughout the world. In Situ Thermal Treatment (ISTT) is a candidate remediation technology for this class of contaminants. However, the relationships between gas production, gas flow, and contaminant mass removal during ISTT are not fully understood. A laboratory study was conducted to assess the degree of mass removal, as well as the gas generation rate and the composition of the gas phase as a function of different heating times and initial DNAPL saturations. Experiments consisted of a soil, water, and DNAPL mixture packed in a 1 L jar that was heated in an oven. Gas produced during each experiment, which consisted of steam and volatile organic compounds (VOCs), was collected and condensed to quantify the gas generation rate. The temperature of the contaminated soil was measured continuously using a thermocouple embedded in the source zone, and was used to identify periods of heating, co-boiling and boiling. Samples were collected from the aqueous and DNAPL phase of the condensate, as well as from the source soil, at different heating times, and analyzed by gas chromatography/mass spectrometry. In addition to laboratory experiments, a mathematical model was developed to predict the co-boiling temperature and transient composition of the gas phase during heating of a uniform source. -
Investigation of Solar Assisted Heat Pump System Integrated with High-Rise Residential Buildings
INVESTIGATION OF SOLAR ASSISTED HEAT PUMP SYSTEM INTEGRATED WITH HIGH-RISE RESIDENTIAL BUILDINGS YU FU, BEng, MSc Thesis submitted to the University of Nottingham for the degree of Doctor of Philosophy SEPTEMBER 2014 Abstract ABSTRACT The wide uses of solar energy technology (solar thermal collector, photovoltaic and heat pump systems) have been known for centuries. These technologies are intended to supply domestic hot water and electricity. However, these technologies still face some barriers along with fast development. In this regards, the hybrid energy system combines two or more alternative technologies to help to increase the total efficiency of the system. Solar assisted heat pump systems (SAHP) and photovoltaic/thermal collector heat pump systems (PV/T-HP) are hybrid systems that convert solar radiation to thermal energy and electricity, respectively. Furthermore, they absorb heat first, and then release heat in the condenser for domestic heating and cooling. The research initially investigates the thermal performance of novel solar collector panels. The experimental results indicate an average daily efficiency ranging from 0.75 to 0.96 with an average of 0.83. Compared with other types of solar collectors, the average daily efficiency of novel solar thermal collectors is the highest. The research work further focuses on the integrated system which combines solar collector and air source heat pump (ASHP). The individual components, configurations and layout of the system are illustrated. Theoretical analysis is conducted to investigate thermodynamic cycle and heat transfer contained in the hybrid system. Laboratory tests are used to gauge the thermal performance of the novel SAHP. A comparison is made between the modelling and testing results, and the reasons for error formation are analysed. -
Simulating Air Absorption in a Hydraulic Air Compressor (HAC)
Simulating air absorption in a hydraulic air compressor (HAC) by Stephen M. Young A thesis submitted in partial fulfillment of the requirements for the degree of Master of Applied Science (MASc) in Natural Resources Engineering The Faculty of Graduate Studies Laurentian University Sudbury, Ontario, Canada ©Stephen Young, 2017 THESIS DEFENCE COMMITTEE/COMITÉ DE SOUTENANCE DE THÈSE Laurentian Université/Université Laurentienne Faculty of Graduate Studies/Faculté des études supérieures Title of Thesis Titre de la thèse Simulating air absorption in a hydraulic air compressor (HAC) Name of Candidate Nom du candidat Young, Stephen Degree Diplôme Master of Applied Science Department/Program Date of Defence Département/Programme MASc. Natural Resources Engineering Date de la soutenance March 3, 2017 APPROVED/APPROUVÉ Thesis Examiners/Examinateurs de thèse: Dr. Dean Millar (Supervisor/Directeur(trice) de thèse) Dr. Kim Trapani (Committee member/Membre du comité) Dr. Ramesh Subramanian (Committee member/Membre du comité) Approved for the Faculty of Graduate Studies Approuvé pour la Faculté des études supérieures Dr. David Lesbarrères Monsieur David Lesbarrères Dr. Graeme Norval Dean, Faculty of Graduate Studies (External Examiner/Examinateur externe) Doyen, Faculté des études supérieures Dr. Wilson Pascheto (External Examiner/Examinateur externe) ACCESSIBILITY CLAUSE AND PERMISSION TO USE I, Stephen Young, hereby grant to Laurentian University and/or its agents the non-exclusive license to archive and make accessible my thesis, dissertation, or project report in whole or in part in all forms of media, now or for the duration of my copyright ownership. I retain all other ownership rights to the copyright of the thesis, dissertation or project report. I also reserve the right to use in future works (such as articles or books) all or part of this thesis, dissertation, or project report.