Troubleshooting Bearing and Lube Oil System Problems
Total Page:16
File Type:pdf, Size:1020Kb
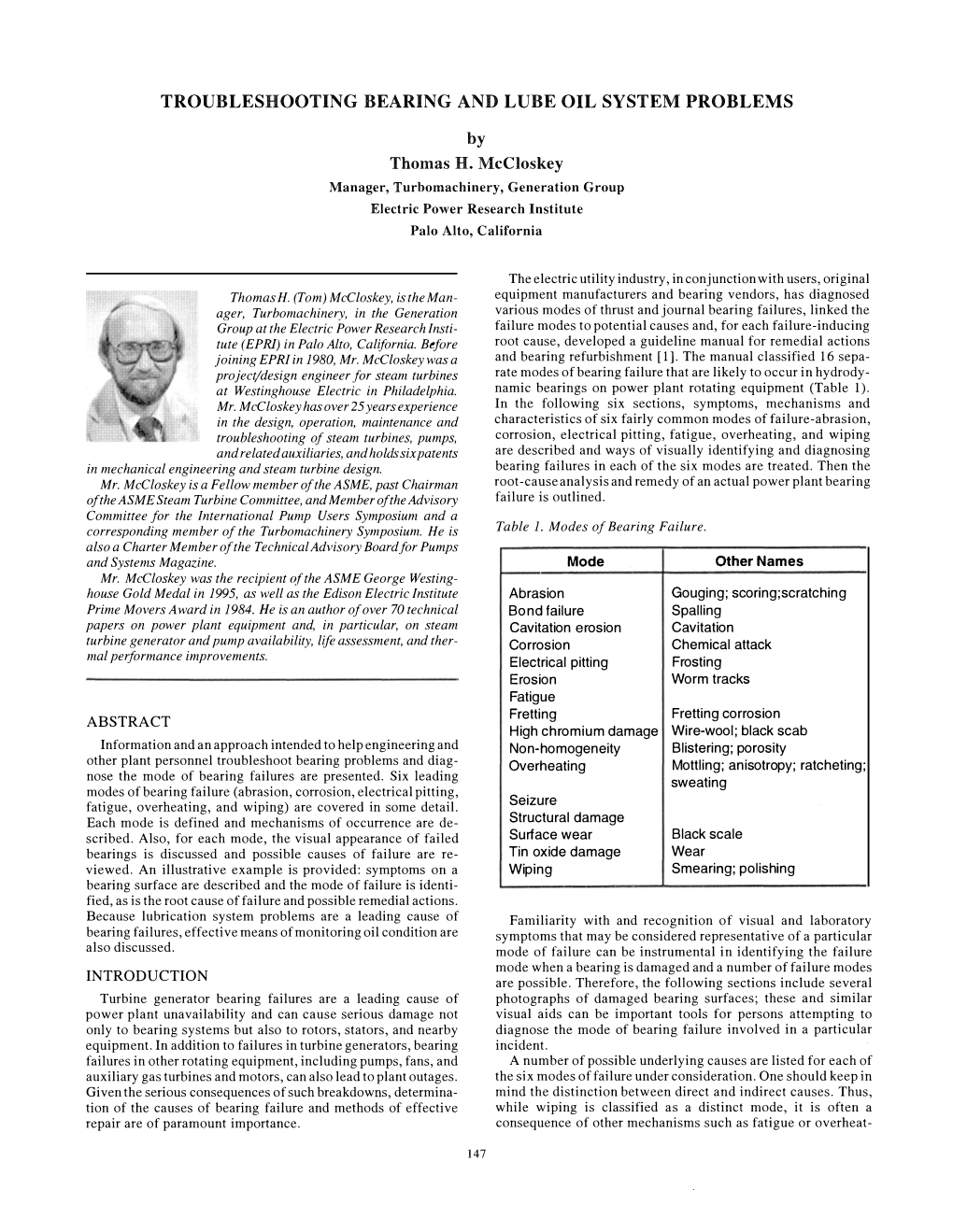
Load more
Recommended publications
-
Journal Bearings and Their Lubrication
Issue Number: 200503 Journal Bearings and Their Lubrication Robert Scott, Noria Corporation Journal or plain bearings consist of a shaft or journal which rotates freely in a supporting metal sleeve or shell. There are no rolling elements in these bearings. Their design and construction may be relatively simple, but the theory and operation of these bearings can be complex. This article concentrates on oil- and grease-lubricated full fluid film journal bearings; but first a brief discussion of pins and bushings, dry and semi-lubricated journal bearings, and tilting- pad bearings. Low-speed pins and bushings are a form of journal bearing in which the shaft or shell generally does not make a full rotation. The partial rotation at low speed, before typically reversing direction, does not allow for the formation of a full fluid film and thus metal-to-metal contact does occur within the bearing. Pins and bushings continually operate in the boundary lubrication regime. These types of bearings are typically lubricated with an extreme pressure (EP) grease to aid in supporting the load. Solid molybdenum disulfide (moly) is included in the grease to enhance the load-carrying capability of the lubricant. Many outdoor construction and mining equipment applications incorporate pins and bushings. Consequently, shock loading and water and dirt contamination are often major factors in their lubrication. Dry journal bearings consist of a shaft rotating in a dry sleeve, usually a polymer, which may be blended with solids such as molybdenum, graphite, PTFE or nylon. These bearings are limited to low-load and low-surface speed applications. -
1. Introduction the Most Popular Bearing Alloys Are Based on Tin And
ARCHIVESOFMETALLURGYANDMATERIALS Volume 56 2011 Issue 3 DOI: 10.2478/v10172-011-0089-6 B. LESZCZYŃSKA-MADEJ∗, M. MADEJ∗ THE PROPERTIES OF BABBITT BUSHES IN STEAM TURBINE SLIDING BEARINGS WŁASNOŚCI BABBITU STOSOWANEGO NA PANWIE ŁOŻYSKA ŚLIZGOWEGO W TURBINIE GAZOWEJ The analysis of the properties of babbitt bushes is presented in this article. Materials intended for examinations were charged from the TK-120 steam turbine of TG-8 turbosystem from the Power Station Stalowa Wola. The specimens were subsequently tested for Brinell hardness, microhardness, bending strength and wear resistance. The wear tests were carried out using the block-on-ring tester. The samples were also investigated by means of both light microscopy (LM) and scanning electron microscopy (SEM). Keywords: Babbitt bushes, properties, ingot, Babbitt bearing, microstructure Do najpowszechniej stosowanych stopów łożyskowych należą stopy cyny i ołowiu. Stopy te posiadają plastyczną osnowę z cząstkami nośnymi twardych faz zapewniających dużą odporność na ścieranie. Najkorzystniejsze własności wykazują stopy na osnowie cyny zawierające: 7÷13% Sb, 3÷7% Cu i do 1,2% Cd, zwane babbitami cynowymi. Łożyska nośne wykonane z babbitów cynowych pracują w turbinie w warunkach tarcia płynnego. W wyniku tarcia w łożysku powstaje ciepło, co powoduje pracę łożyska w temperaturze zazwyczaj mieszczącej się w zakresie od 45 do 60◦C. Zjawisko ścierania najintensywniej pojawia się podczas zatrzymywania lub rozruchu, kiedy łożysko pracuje w warunkach tarcia półpłynnego. W tych dwóch etapach pracy łożysk uwidacznia się wpływ materiałów, z jakich wykonano zarówno panew jak i czop. W pracy stosowano stop łożyskowego Ł83 pobrany z gąski oraz turbozespołu TG-8 turbiny parowej TK-120 z Elektrowni Stalowa Wola. -
TAFA ® Wire Brochure
Wire Solutions Catalog Praxair and TAFA thermal spray wires Praxair Surface Technologies, Inc. and TAFA Incorporated offers a complete line of arc spray wires in its portfolio of thermal spray materials. Proud of our role in the emergence and growth of the arc spray process, we continue to develop and refine thermal spray wires of all types – solid or cored, soft or hard – to help you take full advantage of the exceptional value arc spray provides. Whether your application calls for a reliable bond coat, dimensional restoration or resistance to wear and corrosion, Praxair and TAFA has a wire to meet the challenge. Understanding that “not all wires are alike”– in part because we optimize wires for superior arc spray coatings – we provide materials that perform every time. And we offer the complete “system”, including six hardware options, to start you on the way to productive solutions. When you search for the right thermal spray wire, remember the company that built its reputation on arc spray technology: Praxair and TAFA. Let us work with you to continue to develop and perfect quality arc spray wires and coatings. Phone: 1-603-223-2100 Fax: 1-603-225-4342 E-mail: [email protected] Quality thermal spray wires must be made to tight compositional tolerances, have the appropriate surface finish, and be spooled properly for consistent performance. Exceptional wires for superiorsuperior coatings We recognize that high quality spray All Praxair and TAFA wires are engi- testing and analysis assure that the equipment without compatible, first-rate neered and manufactured exclusively targeted characteristics are achieved. -
DODGE® SLEEVOIL®RTL PILLOW BLOCKS Sizes 3-7/16” Through 12” These Instructions Must Be Read Thoroughly Before Installation Or Operation
DODGE® SLEEVOIL®RTL PILLOW BLOCKS Sizes 3-7/16” through 12” These instructions must be read thoroughly before installation or operation. This instruction manual was accurate at the time of printing. Please see www.dodge-pt.com for updated instruction manuals. This manual is best suited for RTL Pillow Blocks. If your SLEEVOIL housing nameplate specifies “RTL SPHERICAL HOUSING,” use manual MN3085. Dodge started manufacturing RTL SPHERICAL PILLOW BLOCKS in 2014. WARNING: All products over 25 kg (55 lbs) are noted on the PRE-ASSEMBLY INSTRUCTIONS shipping package. Proper lifting practices are required for these products. Refer to applicable contract/assembly drawings to verify that all parts are available prior to assembly. Disassemble and CAUTION: Do not scrape, rebabbitt or otherwise alter this thoroughly clean all parts of the pillow block. The installer is the product. Such action adversely affects bearing performance last person to inspect all parts for fit, damage and cleanliness. and may result in damage to or destruction of equipment. Care MUST be taken to avoid contaminating the internal surfaces of the bearing. SLEEVOIL RTL pillow blocks are designed for applications requiring a bearing with high thrust load capacities and are WARNING: Rust Preventatives and solvents can be toxic available in expansion and non-expansion types. and/or flammable. Follow directions and safety procedures recommended by their manufacturers. WARNING: Liner assembly has critical machined surfaces which are easily damaged. Use care in handling to protect these surfaces. Liner parts should be placed on a soft, CLEAN surface. For ease of installation, the housings and liners are split and match-marked. -
DODGE® SLEEVOIL®RTL PILLOW BLOCKS Sizes 3-7/16” Through 12” These Instructions Must Be Read Thoroughly Before Installation Or Operation
DODGE® SLEEVOIL®RTL PILLOW BLOCKS Sizes 3-7/16” through 12” These instructions must be read thoroughly before installation or operation. This instruction manual was accurate at the time of printing. Please see www.dodge-pt.com for updated instruction manuals. This manual is best suited for RTL Pillow Blocks. If your SLEEVOIL housing nameplate specifies “RTL SPHERICAL HOUSING,” use manual MN3085. Dodge started manufacturing RTL SPHERICAL PILLOW BLOCKS in 2014. WARNING: All products over 25 kg (55 lbs) are noted on the PRE-ASSEMBLY INSTRUCTIONS shipping package. Proper lifting practices are required for these products. Refer to applicable contract/assembly drawings to verify that all parts are available prior to assembly. Disassemble and CAUTION: Do not scrape, rebabbitt or otherwise alter this thoroughly clean all parts of the pillow block. The installer is the product. Such action adversely affects bearing performance last person to inspect all parts for fit, damage and cleanliness. and may result in damage to or destruction of equipment. Care MUST be taken to avoid contaminating the internal surfaces of the bearing. SLEEVOIL RTL pillow blocks are designed for applications requiring a bearing with high thrust load capacities and are WARNING: Rust Preventatives and solvents can be toxic available in expansion and non-expansion types. and/or flammable. Follow directions and safety procedures recommended by their manufacturers. WARNING: Liner assembly has critical machined surfaces which are easily damaged. Use care in handling to protect these surfaces. Liner parts should be placed on a soft, CLEAN surface. For ease of installation, the housings and liners are split and match-marked. -
AIM's Babbitt Bearing Alloys
AIM’s Babbitt Bearing Alloys Babbitt Description Babbitt is a white metal alloy that was patented by Isaac Babbitt in 1839. Over time, the term Babbitt has been applied to other similar white metals comprised of tin, copper and antimony. Lead can sometimes be added in place of the tin. Babbitt alloys offer corrosion resistance, excellent wetting, low wear and friction resistance and are known for their hard/soft composition. While the tin and lead are soft, the copper and antimony form hard crystals throughout the structure. The wearing of the softer metal allows for better absorption of the lubricant as well as any foreign particles. Babbitt Uses Babbitt is used as a lining for bearing shells of cast iron, steel and bronze. The Babbitt lining prevents friction and wear that is common when a lubricant is not able to prevent the bearing’s moving parts from welding together. The Babbitt therefore extends the life of the bearing. ASTM B-23 Chemical Composition (%) Tin Base Alloy Number (GRADE) 1 2 3 11 Tin 90.0 - 92.0 88.0 - 90.0 83.0 - 85.0 86.0 - 89.0 Antimony 4.0 - 5.0 7.0 - 8.0 7.5 - 8.5 6.0 - 7.5 Lead 0.35 0.35 0.35 0.50 Copper 4.0 - 5.0 3.0- 4.0 7.5 - 8.5 5.0 - 6.5 Iron 0.08 0.08 0.08 0.08 Arsenic 0.10 0.10 0.10 0.10 Bismuth 0.08 0.08 0.08 0.08 Zinc 0.005 0.005 0.005 0.005 Aluminum 0.005 0.005 0.005 0.005 Cadmium 0.05 0.05 0.05 0.05 Total Named Elements, Min. -
Babbitting Manual
BABBITTING MANUAL The Most Economical Bearing is the Long-Lasting, Trouble-Free Bearing. INDEX EQUIPMENT REQUIRED FOR RE-BABBITTING. PAGE 3 VARIOUS GRADES OF BABBIT METALS. .PAGE 3 PREPARING THE SHELL. PAGE 4 PREPARING THE MANDREL. PAGE 4 FLUXING AND TINNING . PAGE 5 POURING TEMPERATURE OF BABBITT. .PAGE 5 LUBRICATION. .PAGE 6 RECOMMENDED CHAMFERS AND OIL RETAINER GROVES. PAGE 7 THE IMPROVED BEARING . PAGE 8 Page 2 EQUIPMENT REQUIRED FOR RE-BABBITTING BEARINGS Re-Babbitting of bearings is easy. However, care must be exercised to follow instructions in detail. The usual equipment required is as follows: Melting Pots Plunger Cup Ladle Skimmer Thermometer or Automatic Temperature Controls Jigs Mandrels Blow Torch Acetylene Torch Good grade of damming material. Grooving and Trimming Tools, such as Chisels, Files and Scrapers Tempil Sticks VARIOUS GRADES OF BABBITT METALS The correct grade of (lead-base), or (tin-base), must first be selected. Which grade to use is determined by the work the bearing must do. Listed below are the five Babbitt metals that are most popular and more generally used in industry. C.H.--(Copper Hardened). The finest lead-base Babbitt metal for heave-duty service. It is especially good for overcoming the effects of friction hear that is generated by heavy running loads. #5 C.H--(Copper Hardened). A heat resistant lead-base Babbitt for shafts that run hot. It is hard, dense, close- grained . tough. G.P.—(General Purpose). A lead-base Babbitt metal that runs cool, is long wearing and resists scoring. It adapts itself to misaligned shafts, withstands bear and abrasion. -
White Metal Bearing Alloys (Known Commercially As “Babbitt Metal”)1
Designation: B 23 – 00 (Reapproved 2005) Standard Specification for White Metal Bearing Alloys (Known Commercially as “Babbitt Metal”)1 This standard is issued under the fixed designation B 23; the number immediately following the designation indicates the year of original adoption or, in the case of revision, the year of last revision. A number in parentheses indicates the year of last reapproval. A superscript epsilon (e) indicates an editorial change since the last revision or reapproval. This standard has been approved for use by agencies of the Department of Defense. 1. Scope 3.1.3 Quantity, 1.1 This specification covers eight typical white metal 3.1.4 Alloy number, bearing alloys, in bar or ingot form, known commercially as 3.1.5 Inspection required (Section 9), “babbitt metal.” The alloys are specified, covering the range 3.1.6 Certification required (Section 10), commercially used, and are designated by the alloy numbers 3.1.7 Marking required (Section 11), and shown in Table 1. 3.1.8 ASTM designation and year of issue. 1.2 The values stated in inch-pound units are to be regarded 4. Materials and Manufacture as standard. The values given in parentheses are mathematical conversions to SI units that are provided for information only 4.1 The bars or ingots shall be made in accordance with and are not considered standard. such practice as to obtain the chemical composition, weight, 1.3 This standard does not purport to address all of the and dimensions as prescribed in this specification. safety concerns, if any, associated with its use. -
Some Properties of White Metal Bearing Alloys at Elevated Temperatures
ouieiiu uf Hfanriardfl. JUN 3 1921 DEPARTMENT OF COMMERCE Technologic Papers OF THE Bureau of Standards S. W. STRATTON DIRECTOR No. 188 SOME PROPERTIES OF WHITE METAL BEARING ALLOYS AT ELEVATED TEMPERATURES BY JOHN R. FREEMAN, Jr., Associate Physicist R. W. WOODWARD, Physicist Bureau of Standards APRIL 5 , 1921 PRICE, 5 CENTS Sold only by the Superintendent of Documents, Government Printing Office Washington, D. C. WASHINGTON GOVERNMENT PRINTING OFFICE 1921 .. SOME PROPERTIES OF WHITE METAL BEARING ALLOYS AT ELEVATED TEMPERATURES By John R. Freeman, Jr., and R. W. Woodward ABSTRACT An apparatus is described for determining the yield point and ultimate strength of white metal bearing alloys at temperatures up to ioo° C. A new design of heating apparatus is described for determining the Brinell hardness of metals at temperatures up to ioo° C. The results of compression tests and Brinell hardness tests at temperatures up to ioo° C are given for five typical white metal bearing alloys, including three tin-base alloys, one lead-base alloy, and one intermediate alloy, which show that the tin-base alloys maintain their properties better at elevated temperatures than the lead- containing alloys. Results of tests are given which indicate that up to 5 per cent of lead in a high-grade babbitt does not affect the yield point or ultimate strength at 25 or 75° C. The yield point of tin-base alloys is not affected by heating for six weeks at about 100° C, but the yield point is lowered in the lead-base alloy by heating for two weeks at about 100° C. -
Dodge® Sleevoil® Rxt Pillow Blocks
DODGE® SLEEVOIL® RXT PILLOW BLOCKS INSTRUCTION MANUAL (ASSEMBLY INSTRUCTIONS) WARNING: Because of the possible danger to person(s) or property from accidents which may result from the improper use of products, it is important that correct procedures be followed: Products must be used in accordance with the engineering information specified in the catalog. Proper installation, maintenance and operation procedures must be observed. The instructions in the instruction manuals must be followed. Inspections should be made as necessary to assure safe operation under prevailing conditions. Proper guards and other suitable safety devices or procedures as may be desirable or as may be specified in safety codes should be provided, and are neither provided by Baldor Electric Company nor are the responsibility of Baldor Electric Company. This unit and its associated equipment must be installed, adjusted and maintained by qualified personnel who are familiar with the construction and operation of all equipment in the system and the potential hazards involved. When risk to persons or property may be involved, a failsafe device must be an integral part of the driven equipment beyond the speed reducer output shaft. 1 The housing and its CAUTION associated parts are DO NOT SCRAPE, REBABBITT OR OTHERWISE in one package; the ALTER THIS PRODUCT. SUCH ACTION ADVERSELY liner and its parts in AFFECTS BEARING PERFORMANCE AND MAY another. RESULT IN DAMAGE TO OR DESTRUCTION OF EQUIPMENT. DANGER ONLY QUALIFIED PERSONNEL FAMILIAR WITH THE CONSTRUCTION AND OPERATION OF THIS EQUIPMENT AND THE HAZARDS INVOLVED SHOULD INSTALL, ADJUST, OPERATE, AND/OR SERVICE IT. READ AND UNDERSTAND Seals, heat exchangers and THIS MANUAL IN ITS ENTIRETY BEFORE PROCEEDING. -
Conservation of Tin in Bearing Metals, Bronzes, and Solders
3 _ DEPARTMENT OF COMMERCE BUREAU OF STANDARDS S. W. STRATTON, Director TECHNOLOGIC PAPERS OF THE BUREAU OF STANDARDS NO. 109 Issued March 15, 1919, CONSERVATION OF TIN IN BEARING METALS, BRONZES, AND SOLDERS By G. K. Burgess, Physicist, and R. W. Woodward, Assistant Physicist CONTENTS Page I . Introduction i 1 1 . Bearing metals i [II. Standard grades of Babbitt metal 4 I V. Structural bronzes 5 V. Solders 7 VI. Cadmium as tin substitute 8 I. INTRODUCTION From a metallurgical standpoint there are several ways in which a reduction of the tin consumed in commercial nonferrous and white-metal alloys can be effected: First, a reduction of the tin content of the alloy; "second, substitution of part or all of the tin content' by some ether metal; and third, a substitution of a different type of alloy', which in some cases also involves a change in mecn&nical d'esrgn. "The Bureau of Standards has been studying these methods of conservation for tin alloys, particularly in regard to babbitts and'bearmsf metals, bronzes, and solders. Much of the inforniation^ seemed by the Bureau was obtained from answers to questionnaires sent to manufacturers and users of these materials, such that, in general, any suggestions or recom- mendations made can be considered as being practical and as having already been thoroughly tried. II. BEARING METALS There is no question but that the tin content of nearly all bearing metals can be reduced to some extent, and in some cases actually eliminated, without prejudice to the service rendered. 66Gjo°— 19 : 2 Technologic Papers of the Bureau of Standards So the problem is to determine what needs are the most exacting or when a breakdown would cause the greatest damage and confine the use of high tin babbitts to these uses only. -
Survey of Damage Investigation of Babbitted Industrial Bearings
Lubricants 2015, 3, 91-112; doi:10.3390/lubricants3020091 OPEN ACCESS lubricants ISSN 2075-4442 www.mdpi.com/journal/lubricants Article Survey of Damage Investigation of Babbitted Industrial Bearings Lyle A. Branagan Pioneer Motor Bearing Company, 129 Battleground Road, Kings Mountain, NC 28086, USA; E-Mail: [email protected]; Tel.: +1-704-937-7000 (ext. 118); Fax: +1-704-937-9429 Academic Editors: Romeo P. Glovnea and Michel Fillon Received: 28 October 2014 / Accepted: 9 March 2015 / Published: 1 April 2015 Abstract: This survey collects the efforts to understand the sources and consequences of damage to babbitted industrial bearings, which operate by means of a hydrodynamic, or hydrostatic, film. Major individual damage types are discussed in the context of major damage categories. Keywords: whitemetal; babbitt; journal; thrust; damage 1. Introduction Hydrodynamic bearings support a rotating shaft with its associated loads, by means of a pressure field developed within a lubricant which separates the solid surfaces. Generation of the separating pressure requires the presence of a converging film thickness and lubricant viscosity. With sufficient pressure over a bearing area, complete support of the loads is achieved avoiding contact between the rotating and stationary components. In theory, this hydrodynamic film prevents wear and degradation of the rotating and stationary components. For industrial equipment, the rotating shaft is more valuable than the supporting bearings. Therefore, the bearing inner diameter is lined with a sacrificial material to absorb damage and to protect the journal surface (for radial bearings) or thrust collar (for thrust bearings) from damage. To serve as a sacrificial material, this lining should be softer than the journal surface and accept contact from hard contaminants in the lubricant.