Welding of Thermoplastic Matrix Composites
Total Page:16
File Type:pdf, Size:1020Kb
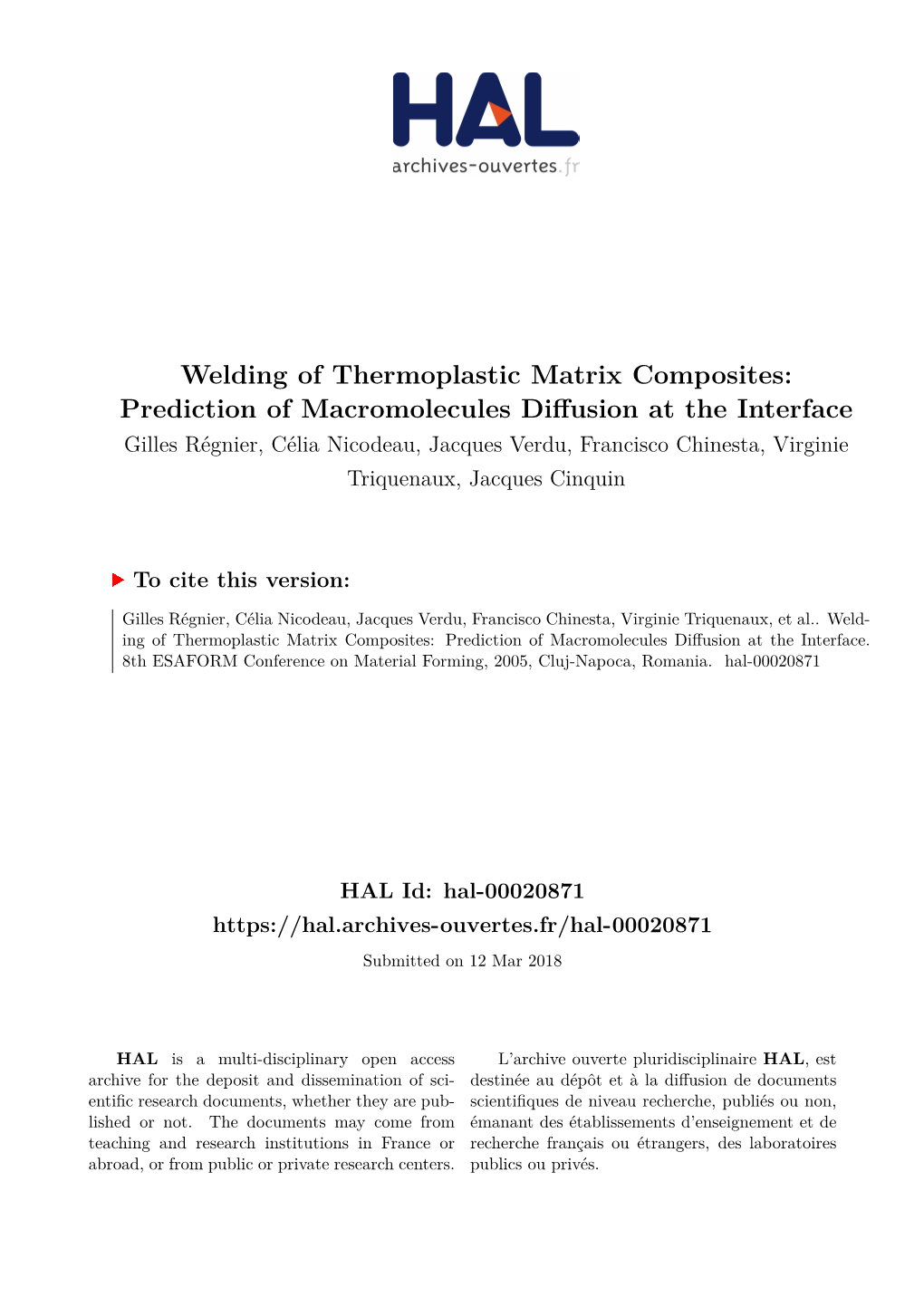
Load more
Recommended publications
-
Microrheometry of Semiflexible Actin Networks Through Enforced Single-Filament Reptation: Frictional Coupling and Heterogeneities in Entangled Networks
Microrheometry of semiflexible actin networks through enforced single-filament reptation: Frictional coupling and heterogeneities in entangled networks M. A. Dichtl† and E. Sackmann Lehrstuhl fu¨r Biophysik E22, Technische Universita¨t Mu¨ nchen, James-Franck-Strasse, D-85747 Garching, Germany Edited by Harden M. McConnell, Stanford University, Stanford, CA, and approved December 27, 2001 (received for review August 16, 2001) Magnetic tweezers are applied to study the enforced motion of filaments embedded in networks may be visualized and analyzed single actin filaments in entangled actin networks to gain insight by fluorescence microscopy (16) or by labeling with colloidal into friction-mediated entanglement in semiflexible macromolec- probes (17). In previous work, the latter possibility was used to ular networks. Magnetic beads are coupled to one chain end of test relate macroscopic viscoelastic impedance spectra to thermally filaments, which are pulled by 5 to 20 pN force pulses through driven single-filament motion. entangled solutions of nonlabeled actin, the test filaments thus The frequency-dependent viscoelastic impedance G*() ϭ acting as linear force probes of the network. The transient filament GЈ() ϩ iGЉ() exhibits three distinct frequency regimes (18): at ϭ ͞ Ͼ ͞ Ͼ Ϫ2 motion is analyzed by microfluorescence, and the deflection- high frequencies, 2 1 e [ e 10 sec; note that e versus-time curves of the beads are evaluated in terms of a is the relaxation time of the bending mode of a chain segment of ⌳ mechanical equivalent circuit to determine viscoelastic parameters, length equal to the entanglement length e (6)], the shear elastic which are then interpreted in terms of viscoelastic moduli of the modulus GЈ()Љ and the loss modulus GЉ() increase with network. -
Arxiv:1802.03702V1 [Cond-Mat.Soft] 11 Feb 2018 Relaxation Remain Controversial for Several Reasons
Disentangling Entanglements in Biopolymer Solutions Philipp Lang and Erwin Frey∗ 1Arnold Sommerfeld Center for Theoretical Physics and Center for NanoScience, Department of Physics, Ludwig-Maximilians-Universität München, Theresienstrasse 37, 80333 München, Germany Reptation theory has been highly successful in explaining the unusual material properties of entangled polymer solutions. It reduces the complex many-body dynamics to a single-polymer description where each polymer is envisaged to be confined to a tube through which it moves in a snake-like fashion. For flexible polymers, reptation theory has been amply confirmed by both experiments and simulations. In contrast, for semiflexible polymers experimental and numerical tests are either limited to the onset of reptation, or were performed for tracer polymers in a fixed, static matrix. Here we report Brownian dynamics simulations of entangled solutions of semiflexible polymers, which show that curvilinear motion along a tube (reptation) is no longer the dominant mode of dynamics. Instead, we find that polymers disentangle due to correlated constraint release which leads to equilibration of internal bending modes before polymers diffuse the full tube length. The physical mechanism underlying terminal stress relaxation is rotational diffusion mediated by disentanglement rather than curvilinear motion along a tube. Dense solutions of polymers are viscoelastic: While agarose networks seem to support Odijk’s scaling result[3] 2 they respond like a fluid to low-frequency stresses, they τr ∼ `pL . However, these experimental results do not act like a cross-linked elastic network at high frequen- settle the actual controversy, as the polymer diffuses in a cies. These intriguing material properties are attributed fixed, static matrix and not in an entangled polymer solu- to the extended structure of polymers, which makes topo- tion. -
Neutron Scattering from Polymers 3 CH07CH01-Higgins ARI 14 May 2016 9:6
CH07-FrontMatter ARI 14 May 2016 8:27 Access provided by University of Cincinnati on 02/03/17. For personal use only. Annu. Rev. Chem. Biomol. Eng. 2016.7:1-28. Downloaded from www.annualreviews.org CH07CH01-Higgins ARI 14 May 2016 9:6 ANNUAL REVIEWS Further Click here to view this article's online features: • Download figures as PPT slides • Navigate linked references • Download citations Neutron Scattering from • Explore related articles • Search keywords Polymers: Five Decades of Developing Possibilities J.S. Higgins Department of Chemical Engineering, Imperial College London, London SW7 2AZ, United Kingdom Annu. Rev. Chem. Biomol. Eng. 2016. 7:1–28 Keywords The Annual Review of Chemical and Biomolecular neutron scattering, polymer molecular dynamics, polymer blends, spinodal Engineering is online at chembioeng.annualreviews.org decomposition, polymer interfaces Access provided by University of Cincinnati on 02/03/17. For personal use only. This article’s doi: Annu. Rev. Chem. Biomol. Eng. 2016.7:1-28. Downloaded from www.annualreviews.org 10.1146/annurev-chembioeng-080615-034429 Abstract Copyright c 2016 by Annual Reviews. The first three decades of my research career closely map the development All rights reserved of neutron scattering techniques for the study of molecular behavior. At the same time, the theoretical understanding of organization and motion of polymer molecules, especially in the bulk state, was developing rapidly and providing many predictions crying out for experimental verification. Neu- tron scattering is an ideal technique for providing the necessary evidence. This autobiographical essay describes the applications by my research group and other collaborators of increasingly sophisticated neutron scattering tech- niques to observe and understand molecular behavior in polymeric materials. -
Experimental Tests of Polymer Reptation
Copyright is owned by the Author of the thesis. Permission is given for a copy to be downloaded by an individual for the purpose of research and private study only. The thesis may not be reproduced elsewhere without the permission of the Author. EXPERIMENTAL TESTS OF POLYMER REPTATION A thesis presented in partial fulfillment of the requirements for the degree of Doctor of Philosophy in Physics at Massey University Michal Komlosh 1999 ABSTRACT Pulsed Gradient Spin Echo Nuclear Magnetic Resonance (PGSE-NMR) and rheology measurements were used to test whether the dynamics of entangled polymer chains in semidilute solution follow the reptation theory. Nine molar masses from 1 to 20 million daltons at a fixed concentration of 4.96% w/v along with a range of concentrations from 4.96% to 23.58% w/v at fixed molar mass of 3 million daltons were studied using PGSE-NMR techniques. The response to mechanical deformation of fivedif ferent concentrations from 4.96% to 23.58% w/v at fixed molar mass of 3.9 million daltons was also studied. The distance and time scales accessed by PGSE-NMR were 20 to 1000 nm and 10 to 3000 ms respectively. As a result the mean square segmental motion over three reptation regimes was obtained and the reptation fm ger l print, ((r(t) -r(O))) - t1 4 , was observed. The resulting concentration and molecular weight scaling laws for the disengagement time, center of mass diffusion and the tube tube diameter, which were obtained in PGSE-NMR and rheology experiments, were found to be in good agreement with the reptation theory and its standard modifications, and a good quantitative fit to the mean square displacement was given by this theory. -
Professor Sir Sam Edwards 1.2.1928 – 7.7.2015 FRS 1966, Kt 1975
Professor Sir Sam Edwards 1.2.1928 – 7.7.2015 FRS 1966, Kt 1975 By Mark Warner, FRS Sam Edwards was one of the leading physicists of the second half of the 20th Century. He was Cavendish Professor in the University of Cambridge, a Vice President of the Royal Society, a member of the Academy des Sciences and of the US National Academy, and a senior figure in the University and his College. He played a major role in public life, most notably as chairman of the Science Research Council, responsible for research funding in the UK. He was chairman of the British Association, chief government scientist to the Department of Energy, and Chairman of the Defence Scientific Advisory Council. He was equally in demand to lead or to help set up bodies abroad, particularly for the Max Planck Institute for Polymers in Mainz, Germany. Remarkably, Sam made some of his most celebrated scientific discoveries, for instance the theory of spin glasses and the rheology of high polymer melts, while serving as the full-time head of the SRC. Conversely, his scientific insights informed his leadership in advising the Government. His later science was in highly applicable areas; he was an active advisor to Unilever, Dow, Lucas, and many other companies that rely on research. Wales, Cambridge and the USA ‘I was born in Swansea on 1st February 1928. I was an only child but there was a large extended working class family. Soon after my birth, my father who had found a permanent job reading electric meters, bought a house in the suburb of Manselton where I was brought up. -
The Longitudinal Superdiffusive Motion of Block Copolymer in A
polymers Article The Longitudinal Superdiffusive Motion of Block Copolymer in a Tight Nanopore Waldemar Nowicki Faculty of Chemistry, Adam Mickiewicz University in Pozna´n,ul. Uniwersytetu Pozna´nskiego8, 61-614 Pozna´n, Poland; [email protected] Received: 7 November 2020; Accepted: 3 December 2020; Published: 8 December 2020 Abstract: The structure and dynamic properties of polymer chains in a confined environment were studied by means of the Monte Carlo method. The studied chains were represented by coarse-grained models and embedded into a simple 3D cubic lattice. The chains stood for two-block linear copolymers of different energy of bead–bead interactions. Their behavior was studied in a nanotube formed by four impenetrable surfaces. The long-time unidirectional motion of the chain in the tight nanopore was found to be correlated with the orientation of both parts of the copolymer along the length of the nanopore. A possible mechanism of the anomalous diffusion was proposed on the basis of thermodynamics of the system, more precisely on the free energy barrier of the swapping of positions of both parts of the chain and the impulse of temporary forces induced by variation of the chain conformation. The mean bead and the mass center autocorrelation functions were examined. While the former function behaves classically, the latter indicates the period of time of superdiffusive motion similar to the ballistic motion with the autocorrelation function scaling with the exponent t5/3. A distribution of periods of time of chain diffusion between swapping events was found and discussed. The influence of the nanotube width and the chain length on the polymer diffusivity was studied.