Role of Strain Crystallization in the Fatigue Resistance of Double Network Elastomers
Total Page:16
File Type:pdf, Size:1020Kb
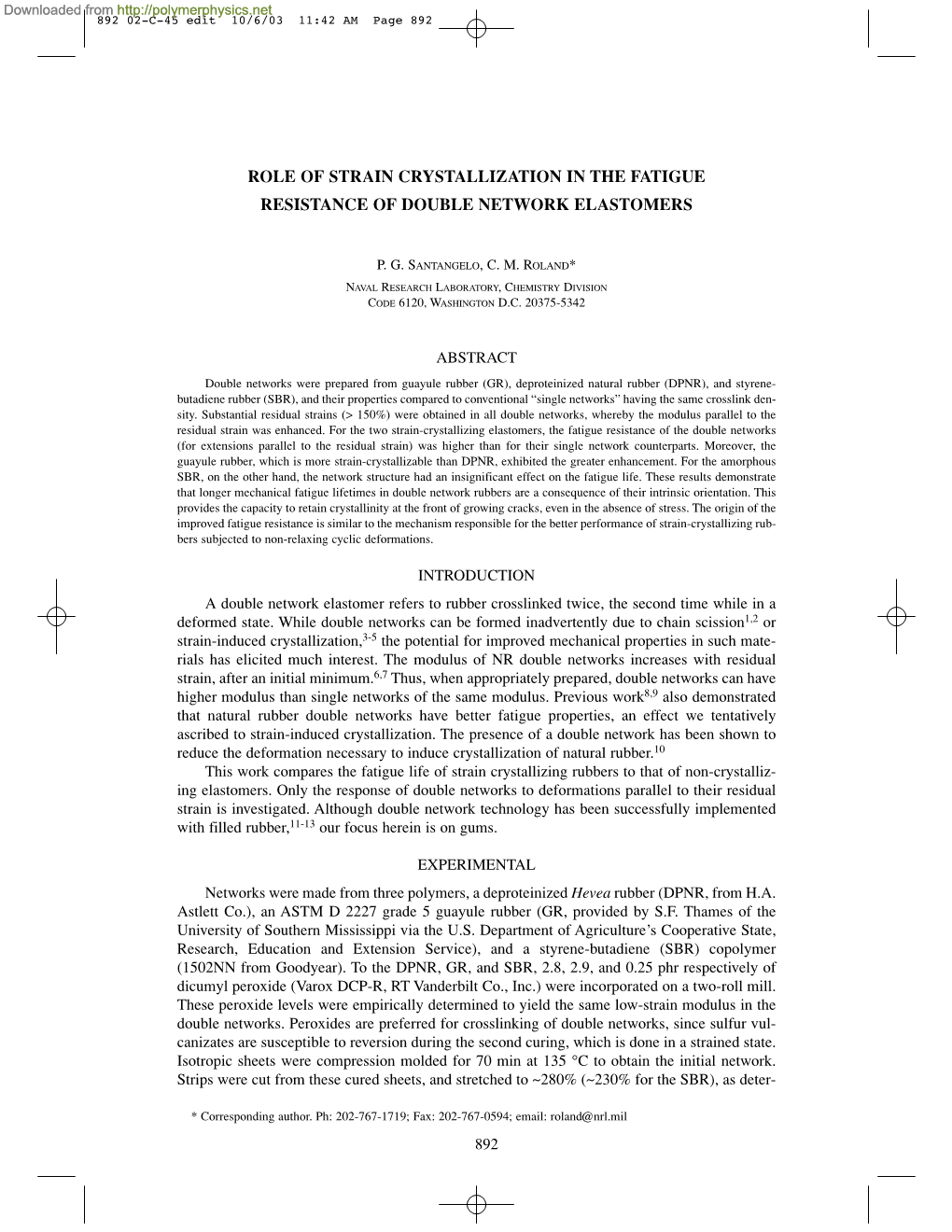
Load more
Recommended publications
-
4 -Effect of Low Temperatures: 4.1 Glass Transition: 4.2 Crystallization
4 -Effect of Low Temperatures: 4.1 Glass Transition: At very low temperatures, all elastomers undergo a rapid transition, occurring across a few degrees only, to the glassy state, becoming brittle and stiffening by factors of up to 1000. In this state, they clearly cannot display elastomeric properties. The temperature range over which this occurs differs widely for different elastomers, depending mainly on the molecular structure of the polymer. Some elastomer glass transition temperatures, Tg, representing the approximate mid-point of this range, are given in the Appendix, Table 1. There can be significant changes in mechanical properties compared to ambient temperature values at temperatures even 20 °C or more above the actual transitional temperature range to a glassy state as characterized above. Stiffness may increase along with hysteresis, creep, stress relaxation, and set. In dynamic applications, Tg increases, perhaps by many tens of degrees, if frequency is increased. Viscoelastic properties are discussed in Chapter 4. Engineering design with elastomers for dynamic purposes must allow for the associated stiffening at temperatures well above the "static" Tg. 4.2 Crystallization: Some elastomers can also crystallize. This occurs at temperatures well above Tg, but can be still below ambient. Polychloroprene (CR) and natural rubber (NR) are the principal types of crystallizing rubbers, having maximum crystallization rates at —10 and —25 °C, respectively. In fact, the extremely good strength and fatigue resistance of CR and NR derive largely from their ability to strain-crystallize locally at a crack tip, even at working temperatures. EPDM can also crystallize, depending on ethylene content (high for crystallization). -
Study of Genistein /Epoxidized Natural Rubber (Enr)
STUDY OF GENISTEIN /EPOXIDIZED NATURAL RUBBER (ENR) BLENDS AND ITS APPLICATION FOR POLY (VINYL CHLORIDE) (PVC) PLASTICIZATION A Thesis Presented to The Graduate Faculty of The University of Akron In Partial Fulfillment of the Requirements for the Degree Master of Science Kangli Tang May, 2015 STUDY OF GENISTEIN /EPOXIDIZED NATURAL RUBBER (ENR) BLENDS AND ITS APPLICATION FOR POLY (VINYL CHLORIDE) (PVC) PLASTICIZATION Kangli Tang Thesis Approved: Accepted: ______________________________ ______________________________ Advisor Department Chair Dr. Thein Kyu Dr. Sadhan C. Jana ______________________________ ______________________________ Committee Member Dean of the College Dr. Avraam Isayev Dr. Eric J. Amis ______________________________ ______________________________ Committee Member Interim Dean of the Graduate School Dr. Kevin Cavicchi Dr. Rex D. Ramsier ______________________________ Date ii ABSTRACT In this thesis, the properties of binary blends of epoxidized natural rubber(ENR) and genistein have been explored by thermal gravimetric analysis(TGA), polarized optical microscope(POM), differential scanning calorimetry(DSC), advanced polymer analyzer(APA) and dynamic mechanical analysis(DMA). Although the melt blends of ENR/genistein are partially miscible, the functional groups of the constituents can react with each other at elevated temperatures above 220 oC, resulting in cured ENR networks by genistein. The cured network showed systematic movement of the glass transition temperatures and also melting point depression at genistein rich compositions, suggestive of miscible character. The theoretical binary phase diagram was constructed in comparison with the observed melting points depression in the framework of Flory-Huggins theory of mixing and the phase field theory of crystallization. The crystal-amorphous interaction parameter was determined based on the melting point depression and heat of fusions as a function of blend compositions. -
BIOMIMETIC SYNTHETIC RUBBER Better Than Natural Rubber
Better than natural rubber BISYKA BIOMIMETIC SYNTHETIC RUBBER 30 % less FRAUNHOFER abrasion EXPERTISE Elastomers Superior Life sciences roll resistance Silica fillers Scale up Can be produced in existing plants THE FRAUNHOFER-GESELLSCHAFT ABOUT THE FRAUNHOFER-GESELLSCHAFT The Fraunhofer-Gesellschaft is contract research, 70 percent of Europe’s leading organization which is through contracts with in applied research. It is made up of industry and with publicly financed 72 institutes and research facilities research projects. International collab- located throughout Germany. More oration with outstanding research than 26,600 employees generate partners and innovative companies an annual research volume of more worldwide provides direct access than 2.5 billion euros. Of this, more to major scientific and economic than 2.1 billion euros come from regions now and into the future. www.fraunhofer.de/en 2 CONTENT On behalf of the Fraunhofer-Gesellschaft, 4 Why is rubber so important for the auto- I would like to congratulate the BISYKA motive industry? Fraunhofer’s project on consortium on its excellent outcomes in the field biomimetic synthetic rubber of biomimetic synthetic rubber. “BISYKA” 6 What makes natural rubber so unique? Within the framework of MAVO, 8 Understanding Fraunhofer’s internal research program for dandelion rubber market-oriented preliminary research, Biocomponents enable innovative elastomers the Fraunhofer-Gesellschaft bundles the 12 From natural rubber expertise of various institutes into original to biomimetic preliminary research projects. synthetic rubber Synthesis of BISYKA rubber BISYKA is an excellent example of how on a pilot scale synergies can be used effectively in this way 16 Novel silica fillers for the rubber and tire industry to develop new and original solutions. -
Micromechanical Modeling of Cracking and Damage Of
Combined Numerical and Experimental Analysis of the Mechanical and Thermal Stress Distribution in a Rubber-Aluminum Roll A. Dorfmann1, O. Pabst2, R. Beha2 1. Abstract Structural components made of rubber play an important role in engineering processes. In spite of the widespread and necessary use of rubber in engineering, a general working knowledge of rubber properties and technology is rather uncommon. A typical application in ropeway engineering is the rubber-aluminum roller subjected to very high thermal and stress gradients during its service life. An attempt is made to describe chemical constitution and compounding of natural rubber as well as the mechanical properties of the elastomer. Material model characterization is summarized and hyperelastic models are reviewed. Important factors influencing energy conversion into heat are introduced and an attempt is made to analyze the thermal pressure generated during oscillating loads. It is shown that the thermal load case is important in determining the stress distribution in the roller components and must be included during the design process. 2. Introduction Structural design and analysis routines applied to ropeway engineering have developed to a mature science over the last thirty years. The use of advanced materials and state of the art quality control allowed developing rope transportation systems with a very high standard of safety. However, even with the advancement in computer technology and the development of faster numerical methods, testing of full-scale systems is still the method of choice to verify and validate new components. The continuous increase in transportation speed and applied loads requires a more accurate analysis of the rubber-aluminum roller typically used in ropeway systems. -
Dependence of Adhesion Properties on Blend Ratio of Ethylene-Propylene-Diene Rubber/Standard Malaysian Rubber Blend Adhesive
Hindawi Publishing Corporation Journal of Coatings Volume 2013, Article ID 383276, 6 pages http://dx.doi.org/10.1155/2013/383276 Research Article Dependence of Adhesion Properties on Blend Ratio of Ethylene-Propylene-Diene Rubber/Standard Malaysian Rubber Blend Adhesive B. T. Poh, J. Lamaming, and G. S. Tay SchoolofIndustrialTechnology,UniversitiSainsMalaysia,11800Penang,Malaysia Correspondence should be addressed to B. T. Poh; [email protected] Received 15 May 2013; Revised 1 November 2013; Accepted 8 November 2013 Academic Editor: Fahmina Zafar Copyright © 2013 B. T. Poh et al. This is an open access article distributed under the Creative Commons Attribution License, which permits unrestricted use, distribution, and reproduction in any medium, provided the original work is properly cited. Viscosity, tack and, peel and shear strengths of ethylene-propylene-diene rubber (EPDM)/standard Malaysian rubber (SMR L) blend adhesive were studied using various blend ratios of the two rubbers, ranging from 0 to 100% EPDM. Coumarone-indene resin, toluene, and poly(ethylene terephthalate) (PET) were used as the tackifier, solvent, and coating substrate, respectively. The tackifiercontentwasfixedat40partsperhundredpartsofrubber(phr).ASHEENhandcoaterwasusedtocoattheadhesive on PET film at four coating thicknesses, that is, 30, 60, 90, and 120 m. The viscosity and adhesion properties were determined by a Brookfield viscometer and a Lloyd Adhesion Tester, respectively. Results show that the viscosity, loop tacks and peel strength of blend adhesives decrease gradually with increasing % EPDM. This observation is attributed to dilution effect and lowering in wettability and compatibility. Shear strength, however, passes through a maximum at 20–40% EPDM blend ratio, an observation which is ascribed to culmination of cohesive strength at the optimum EPDM blend ratio. -
And Epoxidized Natural Rubber (ENR) Were Much Discussed in This Thesis
STUDY OF ADHESION PROPERTIES OF NATURAL RUBBER, EPOXIDIZED NATURAL RUBBER, AND ETHYLENE-PROPYLENE DIENE TERPOLYMER-BASED ADHESIVES KWO HAN KIU UNIVERSITI SAINS MALAYSIA 2007 STUDY OF ADHESION PROPERTIES OF NATURAL RUBBER, EPOXIDIZED NATURAL RUBBER, AND ETHYLENE-PROPYLENE DIENE TERPOLYMER-BASED ADHESIVES by KWO HAN KIU Thesis submitted in fulfilment of the requirements for the Degree of Master of Science January 2007 ACKNOWLEDGEMENTS Heartiest thankful goes to Assoc. Prof. Dr. Poh Beng Teik since he agreed to become my very Supervisor for the lab work and tried to assist me in filling forms for pursuing the Degree of Master of Science. He had been providing me a lot of opportunities and flexibilities in viewing out my own ideas and most of them were supported by him. The guide that had given by him was remarkably useful and really helpful. He was never being selfish to view out his opinions for my guidance and he is definitely a sincere person. The fully spiritually support, love and care, and partially financial that had given by my family is gratefully acknowledged. The author has no reason for not to express his sincere gratitude to his parents for their encouragement between the course of this research and until the writing of this thesis. Lastly, the author shall thank Universiti Sains Malaysia (USM) for its wonderful study environment and beautiful landscape. Special thankful makes for Institute of Graduate Studies (IPS) and personnel for making this study possible through a postgraduate assistantship. The author at very last not forget to express his very last thankful to School of Industrial Technology, USM for providing him facilities and very much opportunities to work and co-operate with all staffs and lecturers. -
Mechanical Behavior of Rubber at High Strain Rates
Downloaded from http://polymerphysics.net MECHANICAL BEHAVIOR OF RUBBER AT HIGH STRAIN RATES C. M. ROLAND* CHEMISTRY DIVISION, CODE 6120 NAVA L RESEARCH LABORATORY WASHINGTON, DC 20375-5342 ABSTRACT Methods to obtain the mechanical response of rubber at high rates of strain are reviewed. These techniques include the extrapolation of low strain, low strain rate data, the limitations of which are discussed, extrapolations to elevated hydrostatic pressure, and direct determinations using split Hopkinson bar and drop weight testers, as well as miscella- neous methods. Some applications involving rubber at strain rates sufficient to induce a transition to the glassy state are described. CONTENTS I. Introduction . .429 II. Extrapolation of Low Strain Rate Measurements . .431 A. Time-Temperature Superpositioning . .431 B. Temperature-Volume Superpositioning . .435 C. Temperature-Pressure Superpositioning . .438 III. Direct Measurement at High Rates and Large Strains . .441 A. Wave Propagation . .441 B. Servohydraulic Test Instruments . .443 C. Split Hopkinson Bar (SHB) . .443 D. Drop Weight and Pendulum Testers . .446 E. Expanding Ring Technique . .451 F. Catapult Apparatus . .452 IV. Strain-Induced Glass Transition . .452 A. Wet Skid Resistance of Tires . .453 B. Sound Transmission and Damping . .453 C. Impact Protection . .454 V. Summary . .455 VI. Acknowledgements . .456 VII. References . .456 I. INTRODUCTION This review discusses the mechanical behavior of rubber at high strain rates, a topic that taken to the extreme is a contradiction in terms. Rubber refers to any amorphous, flexible chain high-polymer having a sub-ambient glass transition temperature, Tg. Since effectively Tg is defined as the temperature at which the material response (i.e., the local segmental dynamics) becomes significantly slower than the experimental time scale (i.e., Deborah number >> 1), the glass transition is rate-dependent. -
Co-Processable Multi-Layer Laminates for Forming High Strength, Haze-Free, Transparent Articles and Methods of Producing Same
^ ^ ^ ^ I ^ ^ ^ ^ ^ ^ II ^ ^ ^ II ^ II ^ ^ ^ ^ ^ ^ ^ ^ ^ I ^ European Patent Office Office europeen des brevets EP 0 928 683 A2 EUROPEAN PATENT APPLICATION (43) Date of publication: (51) |nt Cl.e: B32B 27/18, B32B 27/08, 14.07.1999 Bulletin 1999/28 B65D 65/40 (21) Application number: 99300034.8 (22) Date of filing: 05.01.1999 (84) Designated Contracting States: • Wolf, Arno E. AT BE CH CY DE DK ES Fl FR GB GR IE IT LI LU Martinsville, New Jersey 08836 (US) MC NL PT SE • Penoyer, John A. Designated Extension States: Greenville, South Carolina 29615 (US) AL LT LV MK RO SI • Roth, Douglas D. Taylors, South Carolina 29615 (US) (30) Priority: 06.01.1998 US 3220 (74) Representative: (71) Applicant: HNA Holdings, Inc. De Minvielle-Devaux, Ian Benedict Peter Warren, New Jersey 07959 (US) CARPMAELS & RANSFORD 43, Bloomsbury Square (72) Inventors: London WC1 A 2RA (GB) • Kimmel, Robert M. Simpsonville, South Carolina 29681 (US) (54) Co-processable multi-layer laminates for forming high strength, haze-free, transparent articles and methods of producing same (57) Co-processable multi-layer laminates having a stantial haze in the low Tg layer upon heating. In most high Tg layer and at least one low Tg layer with layers applications, the total amount of crystallization rate in- having properties of high strength, lo- or no-haze, and hibitor also does not substantially inhibit strain-induced transparency after processing into various multi-layer crystallization of the at least one low Tg layer when the forms are useful for packaging and container applica- laminate is stretched during processing. -
199Th Technical Meeting Program
th 199 Technical Meeting Program *Schedule is subject to change. Tuesday, April 27th 9:00 a.m. KEYNOTE ADDRESS: Development of Sustainable Natural Rubber Ecosystem Toward Creation of New Industry; Seiichi Kawahara, Department of Materials Science and Technology, Nagaoka University of Technology An overview of the natural rubber ecosystem and its potential to contribute to the establishment of a sustainable society is addressed in this lecture. Preparation of protein-free natural rubber based on the nanomatrix structure of the rubber, construction of purification plant for natural rubber latex, production of a dryer for protein-free natural rubber latex and preparation of various polymers from the protein- free natural rubber are introduced as components of eco-friendly natural rubber chemistry. Failure of Rubber Materials Co-chairs: Bill Stahl, Rainbow Master Mixing and Lewis Tunnicliffe, Birla Carbon 10:30 a.m. General Considerations in Failure Analysis of Rubber and Plastics - Jason T. Poulton, Akron Rubber Development Laboratory Rubber and plastic articles can show a variety of failure modes. With an approach firmly grounded in the scientific method, the latest installment of this ongoing series of presentations will highlight the variety of analytical methods that can be employed in root cause failure analysis. Real world examples will be discussed with a focus on the problem solving approach to find the root cause of various failures. 11:00 a.m. Wear Mechanisms of Rubber Tyre Materials under Low Severity: a Model Study - Paul Sotta, Centre National de la Recherche Scientifique There is potential opportunity of enormous cost saving in developing a laboratory test which would be representative of the abrasion wear of tyres in real usage conditions. -
Effect of Testing Rate on Adhesion Properties of Acrylonitrile-Butadiene Rubber/Standard Malaysian Rubber Blend-Based Pressure-Sensitive Adhesive
Hindawi Publishing Corporation Journal of Coatings Volume 2013, Article ID 519416, 6 pages http://dx.doi.org/10.1155/2013/519416 Research Article Effect of Testing Rate on Adhesion Properties of Acrylonitrile-Butadiene Rubber/Standard Malaysian Rubber Blend-Based Pressure-Sensitive Adhesive B. T. Poh and Junidah Lamaming School of Industrial Technology, Universiti Sains Malaysia, Minden, 11800 Penang, Malaysia Correspondence should be addressed to B. T. Poh; [email protected] Received 23 May 2013; Revised 6 September 2013; Accepted 18 September 2013 Academic Editor: Fahmina Zafar Copyright © 2013 B. T. Poh and J. Lamaming. This is an open access article distributed under the Creative Commons Attribution License, which permits unrestricted use, distribution, and reproduction in any medium, provided the original work is properly cited. The dependence of loop tack, peel strength, and shear strength of NBR/SMR L blend-based pressure-sensitive adhesives on therate of testing was investigated using coumarone-indene resin and toluene as the tackifier and solvent, respectively. A 40% NBR content in the NBR/SMR L blend was used throughout the experiment. The adhesion properties were measured by a Lloyd Adhesion Tester operating at different rates of testing. The result indicates that loop tack, peels strength, and shear strength increase with the rateof testing due to the viscoelastic response of the adhesive. At low testing rate, the failure mode is cohesive in nature whereas adhesion failure mode occurs at higher testing rates. Adhesion properties also increase with the increase in adhesive coating thickness, an observation which is attributed to the wettability of the adhesive and viscoelastic behavior of the rubber blend. -
Viscoelastic Behavior of Rubbery Materials
Viscoelastic Behavior of Rubbery Materials C.M. Roland Polymer Physics Section Naval Research Laboratory Washington, DC ISBN 978–0–19–957157–4 1 3 5 7 9 10 8 6 4 2 Contents 1 Introduction 1.1 Viscoelasticity and high elasticity in polymers 1.2 Modes of motion 1.3 Fluctuations and linear response theory References 2 Cooperative local dynamics – the glass‐transition zone 2.1 Non‐exponential and non‐Arrhenius behavior 2.2 Temperature and density effects on τα 2.3 Dispersion of relaxation times and dynamic heterogeneity 2.4 Johari‐Goldstein secondary relaxation 2.5 Decoupling phenomena 2.6 Applications References 3 Chain dynamics 3.1 Unentangled polymers 3.2 Entangled polymers 3.3 Practical aspects of diffusion References 4 Networks 4.1 Phenomenological elasticity models 4.2 Chain models 4.3 Constraint models 4.4 Role of molecular motions in the elastic response 4.5 Alternative network structures References 5 Constitutive modeling, non‐linear behavior, and the stress‐optic law 5.1 Linearity and the superposition principle 5.2 Internal stress and optical birefringence 5.3 Reversing strain histories 5.4 Empirical rules for non‐linear flow 5.5 Payne effect References 6 Reduced variables and characteristic relaxation times 6.1 Time‐temperature superpositioning 6.2 Thermorheological complexity 6.3 Density scaling of the dynamics 6.4 Characteristic relaxation times References 7 Blends 7.1 Dynamic properties of miscible polymer blends 7.2 Relaxation models for miscible blends 7.3 Phase‐separated blends References 8 Liquid‐crystalline materials 8.1 -
Fatigue Life Prediction and Modeling of Elastomeric Components
A Dissertation Entitled Fatigue Life Prediction and Modeling of Elastomeric Components by Touhid Zarrin-Ghalami Submitted to the Graduate Faculty as partial fulfillment of the requirements for the Doctor of Philosophy Degree in Engineering Dr. Ali Fatemi, Committee Chair Dr. Efstratios Nikolaidis, Committee Member Dr. Mehdi Pourazady, Committee Member Dr. Vijay Goel, Committee Member Dr. Yong Gan, Committee Member Dr. Patricia R. Komuniecki, Dean College of Graduate Studies The University of Toledo May 2013 i Copyright 2013, Touhid Zarrin-Ghalami This document is copyrighted material. Under copyright law, no parts of this document may be reproduced without the expressed permission of the author. ii An Abstract of Fatigue Life Prediction and Modeling of Elastomeric Components by Touhid Zarrin-Ghalami Submitted to the Graduate Faculty as partial fulfillment of the requirements for the Doctor of Philosophy Degree in Engineering The University of Toledo May 2013 This study investigates constitutive behavior, material properties and fatigue damage under constant and variable amplitude uniaxial and multiaxial loading conditions, with the goal of developing CAE analytical techniques for durability and life prediction of elastomeric components. Such techniques involve various topics including material monotonic and cyclic deformation behaviors, proper knowledge of stress/strain histories, fatigue damage quantification parameters, efficient event identification methods, and damage accumulation rules. Elastomeric components are widely used in many applications, including automobiles due to their good damping and energy absorption characteristics. The type of loading normally encountered by these components in service is variable amplitude cyclic loading. Therefore, fatigue failure is a major consideration in their design and availability of an effective technique to predict fatigue life under complex loading is very valuable to the design procedure.