Molecular Dynamics Simulations of Surface Modification Formations On
Total Page:16
File Type:pdf, Size:1020Kb
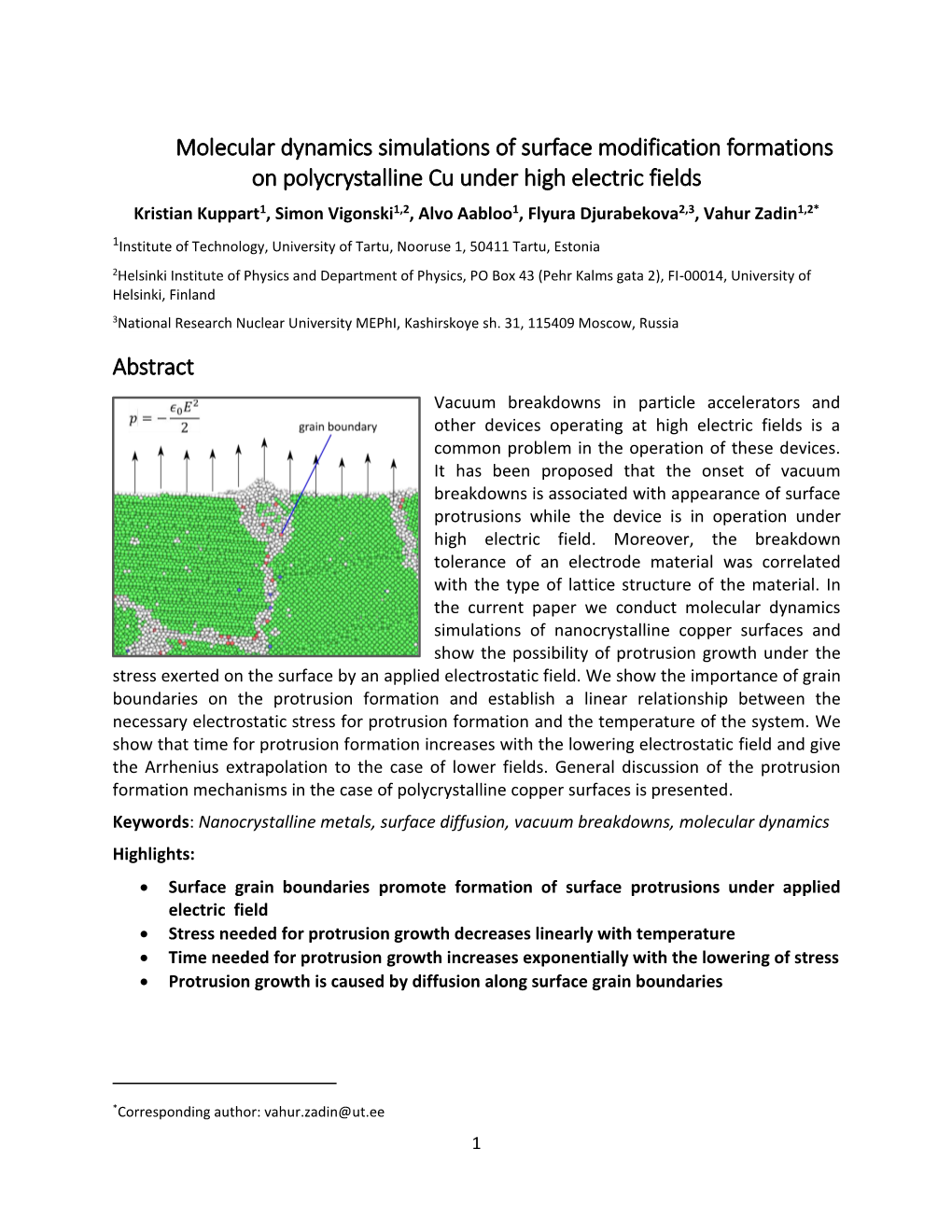
Load more
Recommended publications
-
Surface Properties of 3D Transition Metals Marko P J Punkkinen, Qing-Miao Hu, Se Kyun Kwon, Borje Johansson, János Kollár, Levente Vitos
Surface properties of 3d transition metals Marko P J Punkkinen, Qing-Miao Hu, Se Kyun Kwon, Borje Johansson, János Kollár, Levente Vitos To cite this version: Marko P J Punkkinen, Qing-Miao Hu, Se Kyun Kwon, Borje Johansson, János Kollár, et al.. Surface properties of 3d transition metals. Philosophical Magazine, Taylor & Francis, 2011, 10.1080/14786435.2011.586953. hal-00714554 HAL Id: hal-00714554 https://hal.archives-ouvertes.fr/hal-00714554 Submitted on 5 Jul 2012 HAL is a multi-disciplinary open access L’archive ouverte pluridisciplinaire HAL, est archive for the deposit and dissemination of sci- destinée au dépôt et à la diffusion de documents entific research documents, whether they are pub- scientifiques de niveau recherche, publiés ou non, lished or not. The documents may come from émanant des établissements d’enseignement et de teaching and research institutions in France or recherche français ou étrangers, des laboratoires abroad, or from public or private research centers. publics ou privés. Philosophical Magazine & Philosophical Magazine Letters For Peer Review Only Surface properties of 3d transition metals Journal: Philosophical Magazine & Philosophical Magazine Letters Manuscript ID: TPHM-11-Feb-0082.R1 Journal Selection: Philosophical Magazine Date Submitted by the 06-May-2011 Author: Complete List of Authors: Punkkinen, Marko; Royal Institute of Technology, Department of Materials Science and Engineering; University of Turku, Department of Physics and Astronomy Hu, Qing-Miao; Institute of Metal Research, Chinese Academy -
Arxiv:1304.0144V1
Thermodynamics of coherent interfaces under mechanical stresses. I. Theory T. Frolov1, ∗ and Y. Mishin1, † 1Department of Physics and Astronomy, MSN 3F3, George Mason University, Fairfax, Virginia 22030, USA Abstract We present a thermodynamic theory of plane coherent solid-solid interfaces in multicomponent systems subject to non-hydrostatic mechanical stresses. The interstitial and substitutional chemical components are treated separately using chemical potentials and diffusion potentials, respectively. All interface excess quan- tities are derived using Cahn’s (1979) generalized excess method without resorting to geometric dividing surfaces. We present expressions for the interface free energy as an excess quantity and derive a general- ized adsorption equation and an interface Gibbs-Helmholtz equation which does not contain the interface entropy. The interface stress tensor emerges naturally from the generalized adsorption equation as an ap- propriate excess over bulk stresses and is shown to be generally non-unique. Another interface property emerging from the generalized adsorption equation is the interface excess shear. This property is specific to coherent interfaces and represents the thermodynamic variable conjugate to the shear stress applied parallel to the interface. The theory reveals a number of Maxwell relations describing cross-effects between ther- mal, chemical and mechanical responses of coherent interfaces. In Part II of this work this theory will be applied to atomistic computer simulations of grain boundaries. PACS numbers: 64.10.+h, 64.70.K-, 68.35.-p, 68.35.Md Keywords: interface thermodynamics, coherent interface, interface free energy, interface stress. arXiv:1304.0144v1 [cond-mat.mtrl-sci] 30 Mar 2013 1 I. INTRODUCTION Thermodynamics properties of interfaces can have a strong impact on microstructure de- velopment in materials by controlling phase nucleation, growth, coarsening and many other processes.1,2. -
A Method for Calculating Surface Stress and Elastic Constants by Molecular Dynamics
A METHOD FOR CALCULATING SURFACE STRESS AND ELASTIC CONSTANTS BY MOLECULAR DYNAMICS Satoshi Izumi Dept. of Mechanical Engineering, Univ. of Tokyo., JAPAN Shotaro Hara Dept. of Mechanical Engineering, Univ. of Tokyo., JAPAN Tomohisa Kumagai Dept. of Mechanical Engineering, Univ. of Tokyo., JAPAN Shinsuke Sakai Dept. of Mechanical Engineering, Univ. of Tokyo., JAPAN Abstract 1 Introduction For nano-scale thin film, effects of The films used in the manufacture surface and interface, which can be ig- of semiconductors are less than 10 nm nored on a macro scale, become impor- thick. At this thickness, the effects of tant. For example, surface energy and surface and interface, which can be ig- stress are key parameters for predicting nored on a macro scale, become impor- the intrinsic stress of thin films. Sev- tant. For example, surface (interface) eral researchers have reported that the energy and stress are key parameters elastic constants of thin films are dif- for predicting the intrinsic stress of thin ferent from those of bulks. We have films, though the stress depends also on recently proposed new definitions and the microstructures and growth mode at calculation methods regarding surface atomic level[1][2]. However, it is difficult stress and elastic constants for thin films to obtain values of surface energy and by extending Martin's method, which surface stress experimentally. Therefore, is useful for obtaining the internal dis- numerical evaluation by molecular sim- placement and elastic constants within ulation has been attempted. In addi- the framework of the molecular dynam- tion, several researchers have reported ics method. We applied our method that the elastic properties (e.g. -
A Curvature-Dependent Interfacial Energy-Based Interface Stress Theory and Its Applications to Nano-Structured Materials: (I) General Theory
Journal of the Mechanics and Physics of Solids 66 (2014) 59–77 Contents lists available at ScienceDirect Journal of the Mechanics and Physics of Solids journal homepage: www.elsevier.com/locate/jmps A curvature-dependent interfacial energy-based interface stress theory and its applications to nano-structured materials: (I) General theory Xiang Gao a, Zhuping Huang a, Jianmin Qu b, Daining Fang a,n a LTCS and Department of Mechanics and Engineering Science, College of Engineering, Peking University, Beijing 100871, China b Department of Civil and Environmental Engineering, Northwestern University, Evanston, IL 60208, USA article info abstract Article history: Experimental observations have shown the size-dependent residual surface stresses on Received 24 July 2013 spherical nanoparticles and their influence on the effective modulus of heterogeneous Received in revised form nanostructures. Based on these experimental findings, this paper proposes a new interface 17 December 2013 stress theory that considers the curvature effect on the interfacial energy. To investigate Accepted 31 January 2014 this curvature-dependent interfacial energy, we use the Green elasticity theory to describe Available online 10 February 2014 the nonlinear constitutive relation of the interface at finite deformation, thus explicitly Keywords: demonstrating the curvature-dependent nature of the interface stress and bending Curvature-dependence moment. By introducing a fictitious stress-free configuration, we then propose a new Interfacial energy energy functional for heterogeneous hyperelastic solids with interfaces. For the first time, Interface constitutive relation both the Lagrangian and Eulerian descriptions of the generalized Young–Laplace equation, Generalized Young–Laplace equation Residual elastic field which describes the intrinsic flexural resistance of the interface, are derived from the newly developed energy functional. -
Experimental Determination of Surface Stress Changes in Electro- Chemical Systems – Possibilities and Pitfalls”, Chem
Experimental methods for the determination of stress changes at electrified solidliquid interfaces Gyözö G. Láng*, Noémi Kovács, Soma Vesztergom, Mária Ujvári, Dóra Zalka, Krisztina Sze- keres Eötvös Loránd University, Institute of Chemistry, Department of Physical Chemistry H-1117 Budapest, Pázmány P. s. 1/A Abstract: In the present study some of the methods developed for the experimental determina- tion of (interfacial or film) stress changes in electrochemical systems containing solid-liquid interfaces are briefly reviewed, as well as the kind and quality of information that can be ob- tained using these methods are discussed. The “bending beam” (“bending cantilever”, “laser beam deflection”, ”wafer curvature”) method and related techniques, the piezoelectric method, the extensometer method, and the method based on the measurement of contact angle are dis- cussed in detail. Special attention has been paid to problems related to the use of optical meth- ods for position sensing. Keywords: solid-liquid interface, solid electrode, electrocapillarity, interface stress 1 Introduction The intensive parameter conjugate to surface area [1] (often called the “surface tension”, “interfacial tension”, “surface stress”, “interface stress” or “specific surface energy”) is an im- portant parameter in the thermodynamic theory of electrodes, since most electrochemical sys- tems are, in fact, capillary systems, because any interaction between the bulk solid and the remainder of the system takes place via the interface region. The thermodynamic properties of this region (i.e. the electronic conductor | ionic conductor interface, for instance the interface between a metal and an electrolyte solution) directly influence the electrochemical processes, an understanding of the thermodynamics of interfaces is of importance to all surface scientists and electrochemists. -
Equation of Motion for Viscous Fluids
1 2.25 Equation of Motion for Viscous Fluids Ain A. Sonin Department of Mechanical Engineering Massachusetts Institute of Technology Cambridge, Massachusetts 02139 2001 (8th edition) Contents 1. Surface Stress …………………………………………………………. 2 2. The Stress Tensor ……………………………………………………… 3 3. Symmetry of the Stress Tensor …………………………………………8 4. Equation of Motion in terms of the Stress Tensor ………………………11 5. Stress Tensor for Newtonian Fluids …………………………………… 13 The shear stresses and ordinary viscosity …………………………. 14 The normal stresses ……………………………………………….. 15 General form of the stress tensor; the second viscosity …………… 20 6. The Navier-Stokes Equation …………………………………………… 25 7. Boundary Conditions ………………………………………………….. 26 Appendix A: Viscous Flow Equations in Cylindrical Coordinates ………… 28 ã Ain A. Sonin 2001 2 1 Surface Stress So far we have been dealing with quantities like density and velocity, which at a given instant have specific values at every point in the fluid or other continuously distributed material. The density (rv ,t) is a scalar field in the sense that it has a scalar value at every point, while the velocity v (rv ,t) is a vector field, since it has a direction as well as a magnitude at every point. Fig. 1: A surface element at a point in a continuum. The surface stress is a more complicated type of quantity. The reason for this is that one cannot talk of the stress at a point without first defining the particular surface through v that point on which the stress acts. A small fluid surface element centered at the point r is defined by its area A (the prefix indicates an infinitesimal quantity) and by its outward v v unit normal vector n . -
Residual Stress and Microhardness Increasing Induced by Two-Sided Laser Shock Processing
View metadata, citation and similar papers at core.ac.uk brought to you by CORE provided by Vibroengineering PROCEDIA Residual stress and microhardness increasing induced by two-sided laser shock processing Gerontiy Sakhvadze1, Alexander Shokhin2, Omar Kikvidze3 1, 2Blagonravov Institute of Machines Science, Russian Academy of Sciences, Moscow, Russia 3Tsereteli State University, Kutaisi, Georgia 1Corresponding author E-mail: [email protected], [email protected], [email protected] (Received 26 July 2016; accepted 3 September 2016) Abstract. Two-sided laser shock processing (TSLSP) is often employed to improve the surface quality of thin section components, which can reduce excessive plastic deformation induced by one-sided laser shock processing. Residual stresses (RS) field induced in a thin Ti-6Al-4V alloy plate by TSLSP was investigated through numerical simulation. The multiple TSLSP impacts and the increasing laser shock pressure were found to have significant effects on the RS field. Microhardness distribution on the section of specimen, calculated from RS by Carlsson-Larsson model, is analyzed Keywords: two-sided laser shock processing (TSLSP), finite element method (FEM), residual stresses (RS) field, microhardness, shock wave pressure, multiple laser shocks. 1. Introduction Residual stresses (RS) are often left in the material as a result of plastic deformation after the metal components are processed. Compressive residual stresses (CRS) can improve the fatigue life of the components in practice, while tensile residual stresses (TRS) have an adverse effect on the fatigue resistance. In order to prolong the fatigue life of the components, the CRS are always introduced into its surface layer through various surface treatment techniques, such as shot peening, ultrasonic peening, cold extruding and cold rolling. -
Molecular Dynamics Simulation Studies of Surface-Stress Effects in Metallic Nanostructures" (2011)
Louisiana State University LSU Digital Commons LSU Doctoral Dissertations Graduate School 2011 Molecular dynamics simulation studies of surface- stress effects in metallic nanostructures Jijun Lao Louisiana State University and Agricultural and Mechanical College, [email protected] Follow this and additional works at: https://digitalcommons.lsu.edu/gradschool_dissertations Part of the Mechanical Engineering Commons Recommended Citation Lao, Jijun, "Molecular dynamics simulation studies of surface-stress effects in metallic nanostructures" (2011). LSU Doctoral Dissertations. 2037. https://digitalcommons.lsu.edu/gradschool_dissertations/2037 This Dissertation is brought to you for free and open access by the Graduate School at LSU Digital Commons. It has been accepted for inclusion in LSU Doctoral Dissertations by an authorized graduate school editor of LSU Digital Commons. For more information, please [email protected]. MOLECULAR DYNAMICS SIMULATION STUDIES OF SURFACE-STRESS EFFECTS IN METALLIC NANOSTRUCTURES A Dissertation Submitted to the Graduate Faculty of the Louisiana State University and Agriculture and Mechanical College in partial fulfillment of the requirements for the degree of Doctor of Philosophy in The Department of Mechanical Engineering By Jijun Lao B.S. Shanghai Jiaotong University, Shanghai, China, 2001 M.S. Shanghai Jiaotong University, Shanghai, China, 2004 May, 2011 ACKNOWLEDGEMENTS I would like to take this opportunity to express my sincere thanks to all the people who directly or indirectly have been instrumental to my success throughout study here at Louisiana State University. First and foremost I would like to express my deep gratitude to Dr. Dorel Moldovan, my major professor, for the invaluable guidance and inspiration ideas extended through my study. His constant supervision, helpful discussions, patience and insistence on learning deserve a special mention. -
A Study of Oxides for Solid Oxide Cells
NORTHWESTERN UNIVERSITY AStudyofOxidesforSolidOxideCells ADISSERTATION SUBMITTED TO THE GRADUATE SCHOOL IN PARTIAL FULFILLMENT OF THE REQUIREMENTS for the degree DOCTOR OF PHILOSOPHY Field of Materials Science and Engineering By Olivier Comets EVANSTON, ILLINOIS December 2013 UMI Number: 3605699 All rights reserved INFORMATION TO ALL USERS The quality of this reproduction is dependent upon the quality of the copy submitted. In the unlikely event that the author did not send a complete manuscript and there are missing pages, these will be noted. Also, if material had to be removed, a note will indicate the deletion. UMI 3605699 Published by ProQuest LLC (2013). Copyright in the Dissertation held by the Author. Microform Edition © ProQuest LLC. All rights reserved. This work is protected against unauthorized copying under Title 17, United States Code ProQuest LLC. 789 East Eisenhower Parkway P.O. Box 1346 Ann Arbor, MI 48106 - 1346 2 c Copyright by Olivier Comets 2013 All Rights Reserved 3 ABSTRACT AStudyofOxidesforSolidOxideCells Olivier Comets As the world energy consumption increases, it is a question of global health to increase energy production efficiency and to reduce CO2 emissions. In that respect, solid oxide cells are solid state devices that convert directly fuel into electricity, or vice versa. In fact, when run in fuel cell mode, such devices produce electricity with efficiency up to twice that of current natural gas power plants. However, systems equipped with them have only seen limited commercialization owing to issues of cost, durability, and performance. In this thesis, three di↵erent aspects of solid oxide cells are studied. First, the e↵ects of stress on the properties of mixed ionic electronic conducting oxides are considered. -
Simulations of Surface Stress Effects in Nanoscale Single Crystals
Simulations of surface stress effects in nanoscale single crystals V. Zadina,b,1, M. Veskea,b, S. Vigonskia,b, V. Janssonb, J. Muszinskyb, S.Parviainenb, A. Aablooa, F.Djurabekovab aIntelligent Materials and Systems Lab, Institute of Technology, University of Tartu, Nooruse 1, 50411 Tartu, Estonia bHelsinki Institute of Physics and Department of Physics, P.O.Box 43 (Pietari Kalminkatu 2), FI- 00014 University of Helsinki, Finland Abstract Onset of vacuum arcing near a metal surface is often associated with nanoscale asperities, which may dynamically appear due to different processes ongoing in the surface and subsurface layers in the presence of high electric fields. Thermally activated processes, as well as plastic deformation caused by tensile stress due to an applied electric field, are usually not accessible by atomistic simulations because of long time needed for these processes to occur. On the other hand, finite element methods, able to describe the process of plastic deformations in materials at realistic stresses, do not include surface properties. The latter are particularly important for the problems where the surface plays crucial role in the studied process, as for instance, in case of plastic deformations at a nanovoid. In the current study by means of molecular dynamics and finite element simulations we analyse the stress distribution in single crystal copper containing a nanovoid buried deep under the surface. We have developed a methodology to incorporate the surface effects into the solid mechanics framework by utilizing elastic properties of crystals, pre-calculated using molecular dynamic simulations. The method leads to computationally efficient stress calculations and can be easily implemented in commercially available finite element software, making it an attractive analysis tool. -
Surface Energy and Nanoscale Mechanics
Surface Energy and Nanoscale Mechanics Kosar Mozaffari, Shengyou Yang, and Pradeep Sharma Contents 1 Introduction............................................................... 2 2 Preliminary Concepts....................................................... 4 2.1 The Need for Surface Tensors............................................ 4 2.2 Differentiation and Integration on a Surface................................. 6 3 Theoretical Framework for Surface Mechanics................................... 9 3.1 Kinematics........................................................... 9 3.2 Energy Variation and Equations of Equilibrium.............................. 10 3.3 Constitutive Equations and Elastic Stress Tensors............................ 13 3.4 Linearized Bulk and Surface Stresses and Constitutive Choice.................. 14 4 Illustrative Examples........................................................ 17 4.1 Young’s Modulus of a Nano-rod Considering Surface Effects .................. 17 4.2 Influence of Surface Effects on the Thermoelastic State of a Ball ............... 19 4.3 Effect of Residual Stress of Surfaces on Elastic State of Spherical Inclusion ...... 21 5 Perspectives on Future Research............................................... 24 References................................................................... 25 Abstract The mechanical response of nanostructures, or materials with characteristic features at the nanoscale, differs from their coarser counterparts. An important physical reason for this size-dependent phenomenology -
Measuring the Surface Stress Polar Dependence J.J.Métois, A.Saùl, P.Müller
Measuring the surface stress polar dependence J.J.Métois, A.Saùl, P.Müller Centre de Recherche sur la Matière Condensée et les Nanosciences1 Campus de Luminy, case 913, F-13288 Marseille Cedex 9, France Abstract: While measurements of the polar dependence of the surface free energy are easily available, measurements of the whole polar dependence of the surface stress of a crystal do not exist. In this paper is presented a new procedure that allows, for the first time, the experimental determination of the surface stress polar dependence of a crystal. For this purpose (1) electromigration is used to control the kinetic facetting of surface orientations that belong to the equilibrium shape of the crystal (2) for each destabilised surface, the period of facetting as well as the crystallographic angle of the appearing facets are measured by AFM. The so- obtained data lead to a set of equations whose mathematical solution, compatible with physical constraints, give access to the surface stress polar dependence of the whole crystal and thus to a better understanding of surface stress properties. Two distinct macroscopic quantities are needed to characterise the thermodynamics properties of a crystalline surface n characterised by its normal direction nˆ : the surface free energy per unit area γ n which measures the cost of creating a surface area at constant deformation and the surface stress []s n , which measures the energy cost for deforming a surface at constant number of surface atoms. While γ n is a positive scalar, the surface stress which depends upon the direction of stretching the surface, is a second rank tensor.