Understanding Catalysis—A Simplified Simulation of Catalytic
Total Page:16
File Type:pdf, Size:1020Kb
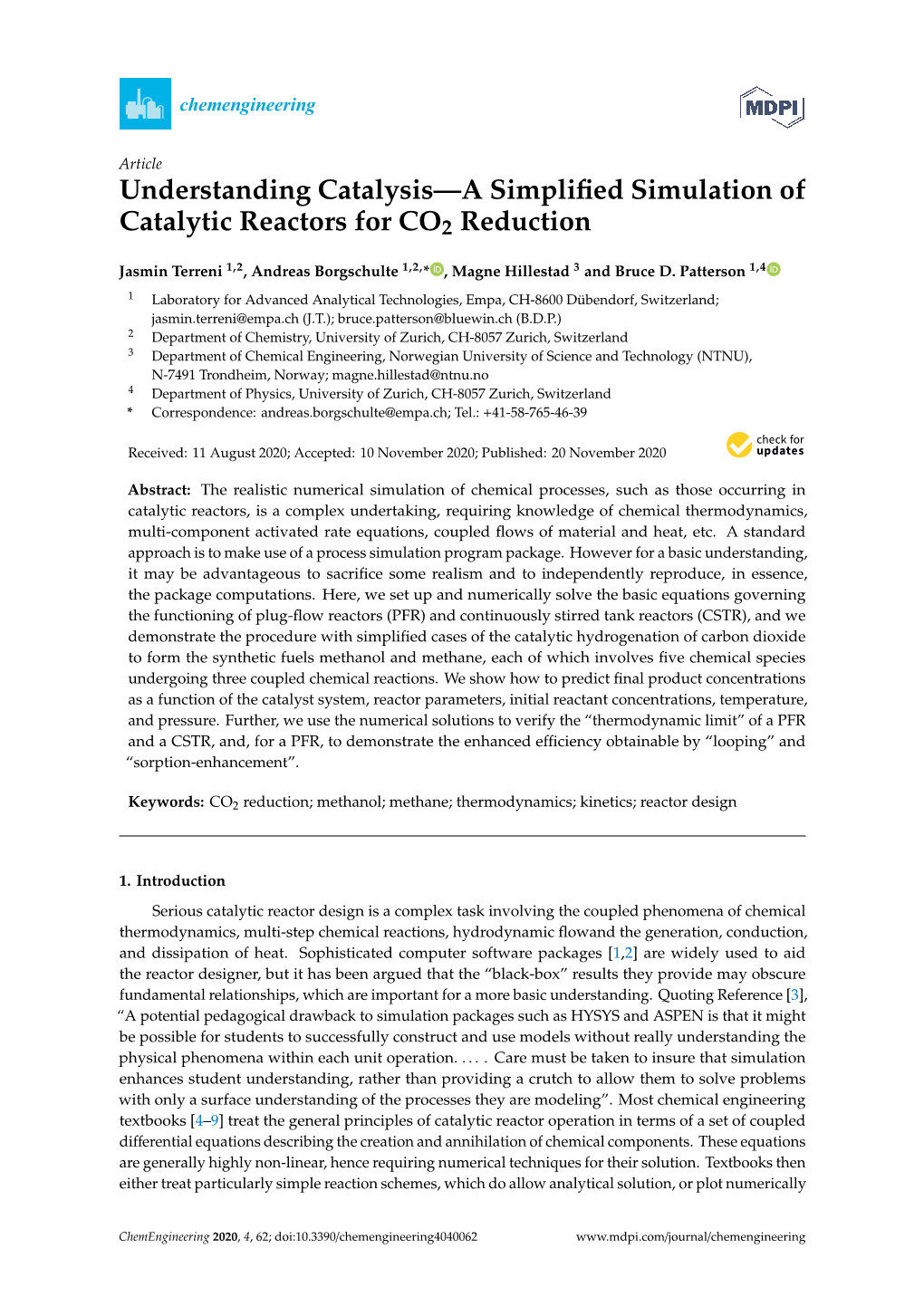
Load more
Recommended publications
-
Chemical Reactor Engineering*
CHEMICAL REACTOR ENGINEERING* JOHN B. BUTT mental topics, with more specialized applications Northwestern University in later chapters. Descriptive kinetics and data Evanston, IL 60201 interpretation are, logically, accorded first place on each list, followed by introductory material on E. E. PETERSEN reactor design and analysis. The latter is largely University of California limited to ideal reactor models; the effect of tem Berkeley, CA 94720 perature is treated somewhat differently in an organizational manner by the three authors, but HE DEVELOPMENT OF chemical reaction the level and extent of coverage is quite similar. Tengineering as an identifiable area within Concepts of selectivity as well as rate and conver chemical engineering has led to renewed interest sion are presented early in each case and main and emphasis on courses dealing with chemical tained as an important factor in kinetics and re reaction kinetics and chemical reactor design. The actor analysis throughout. Following this intro basic issues concerning instruction in these areas ductory material, each author then turns to prob are probably not much different from those in lems associated with deviations from ideal reactor volved in any other area of chemical engineering performance. Here somewhat more variation is insofar as fundamentals vs. appllcations, extent of apparent in organization and presentation but, coverage, and similar factors. There is, however, again, the net coverage and information is quite a chemical factor involved in this area that may similar. not appear quite so prominently in other endeav The point is that, in terms of information ors, and instruction at the undergraduate level which might form the core content of a typical particularly may be sensitive to the contents of current offerings in chemistry courses. -
CHEMICAL REACTION ENGINEERING* Current Status and Future Directions
[eJij9iviews and opinions CHEMICAL REACTION ENGINEERING* Current Status and Future Directions M. P. DUDUKOVIC and petrochemical industry provided a fertile ground Washington University for further development of reaction engineering con St. Louis, MO 63130 cepts. The final cornerstone of this new discipline was laid in 1957 by the First Symposium on Chemical HEMICAL REACTIONS have been used by man Reaction Engineering [3] which brought together and C kind since time immemorial to produce useful synthesized the European point of view. The Amer products such as wine, metals, etc. Nevertheless, the ican and European schools of thought were not identi unifying principles that today we call chemical reac cal, but in time they converged into the subject matter tion engineering were not developed until relatively a that we know today as chemical reaction engineering, short time ago. During the decade of the 1940's (not or CRE. The above chronology led to the establish even half a century ago!) a transition was made from ment of CRE as an accepted discipline over the span descriptive industrial chemistry to the conceptual un of a decade and a half. This does not imply that all the ification of reaction processes and reactor types. The principles important in CRE were discovered then. pioneering work in this area of industrial practice was The foundation for CRE had already been established done by Denbigh [1] in England. Then in 1947, by the early work of Frank-Kamenteski, Damkohler, Hougen and Watson [2] published the first textbook Zeldovitch, etc., but at that time they represented in the U.S. -
Simulation of HDS Tests in Trickle-Bed Reactor
Simulation of HDS Tests in Trickle-Bed Reactor V. Tukač1, A. Prokešová1, J. Hanika1, M. Zbuzek2 and R. Černý2 1Institute of Chemical Technology, Prague, Technická 5, CZ-16628 Prague, Czech Rebublic 2Research and education centre UniCRE Litvínov, CZ-43670 Litvínov, Czech Rebublic Keywords: Hydrodesulfurization Simulation, Catalyst Tests, Trickle-Bed Reactor. Abstract: The paper deals with methodology of simulation study devoted to evaluation of reliability of HDS catalyst testing procedure in pilot three phase fixed bed reactor. Hydrodynamic behaviour of test reactor was determined by residence time distribution method. Residence time and Peclet number of axial dispersion of liquid phase were obtained by nonlinear regression of experimental data. Hydrodesulfurization reaction kinetics was evaluated by analysis of concentration data measured in high pressure trickle-bed reactor and autoclave. Simulation of reaction courses were carried out both by pseudohomogeneous model of ODE in Matlab and heterogeneous reactor model of PDE solved by COMSOL Multiphysics. Final results confirm presumption of eliminating influence of hydrodynamics on reaction kinetic results by dilution of catalyst bed by inert fine particles. 1 INTRODUCTION were supplemented by kinetic measurement of reaction rate constants and activation energies of Sustainable development demands ultra-low selected sulfuric compounds. Parallel to HDS concentrations of sulfur and nitrogen compounds in reaction also hydrodenitrogenation (HDN) takes produced engine fuels – gasoline and diesel. Present place in the catalytic reactor. Hydrodynamic data sulfur content valid in EU 10 ppm represents less were evaluated by residence time distribution (RTD) than one thousands of sulfur content of original method in laboratory glass model of pilot reactor. crude oil. Deep hydrodesulfurization (HDS) of Mathematical models of the process (Ancheyta, engine fuels is dominantly carried out in catalytic 2011) were formulated both like 1D trickle-bed reactors. -
Ideal Models of Reactors - A
CHEMICAL ENGINEEERING AND CHEMICAL PROCESS TECHNOLOGY – Vol. III - Ideal Models Of Reactors - A. Burghardt IDEAL MODELS OF REACTORS A. Burghardt Institute of Chemical Engineering, Polish Academy of Sciences, Poland Keywords: Thermodynamic state, conversion degree, extent of reaction, classification of chemical reactors, mass balance, energy balance, reactor models, reactor design. Contents 1. Introduction 2. Thermodynamic State of a System 3. The Plug Flow Reactor 4. The Perfectly Mixed Tank Reactor 5. The Batch Reactor 6. The Cascade of Tank Reactors 7. Comparison of Different Types of Reactors 7.1. Size Comparison of Single Reactors 7.2. The Cascade of Tank Reactors 7.3. Multireaction systems Bibliography Biographical Sketch Summary The range of application of chemical reactors is extremely broad not only in the chemical industry but also in the petrochemical industry and in refineries. Recently these apparatuses have also been more often used in the dynamically developing field of biotechnology as well as in the processes connected with environmental protection. The main goal of the discipline named chemical reaction engineering is to elaborate quantitative fundamentals for reactor design and for a proper operation of these apparatuses in real industrial conditions. The tool applied in these investigations is modeling, whose task is to establish relationships which could quantitatively describe the course ofUNESCO the process in reactors of various – EOLSStypes and scales. These relationships constitute the mathematical model. The mathematical model is usually much simpler than the real physical object but should comprise all these features and parameters whose influence on the process is crucial. SAMPLE CHAPTERS The rational basis for developing these models is provided by the principles of conservation of mass, momentum and energy. -
Roadmap Chemical Reaction Engineering an Initiative of the Processnet Subject Division Chemical Reaction Engineering
Roadmap Chemical Reaction Engineering an initiative of the ProcessNet Subject Division Chemical Reaction Engineering 2nd edition May 2017 roadmap chemical reaction engineering Table of contents Preface 3 1 What is Chemical Reaction Engineering? 4 2 Relevance of Chemical Reaction Engineering 6 3 Experimental Reaction Engineering 8 A Laboratory Reactors 8 B High Throughput Technology 9 C Dynamic Methods 10 D Operando and in situ spectroscopic methods including spatial information 11 4 Mathematical Modeling and Simulation 14 A Challenges 14 B Workflow of Modeling and Simulation 15 C Achievements & Trends 20 5 Reactor Design and Process Development 22 A Optimization of Transport Processes in the Reactor 22 B Miniplant Technology and Experimental Scale-up 24 C Equipment Development 25 D Process Intensification 29 E Systems Engineering Approaches for Reactor Analysis, Synthesis, Operation and Control 32 6 Case studies 35 Case Study 1: The EnviNOx® Process 35 Case Study 2: Redox-Flow Batteries 36 Case Study 3: On-Board Diagnostics for Automotive Emission Control 37 Case Study 4: Simulation-based Product Design in High-Pressure Polymerization Technology 39 Case Study 5: Continuous Synthesis of Artemisinin and Artemisinin-derived Medicines 41 7 Outlook 43 Imprint 47 2 Preface This 2nd edition of the Roadmap on Chemical Reaction Engi- However, Chemical Reaction Engineering is not only driven by neering is a completely updated edition. Furthermore, it is the need for new products (market pull), but also by a rational written in English to gain more international visibility and approach to technologies (technology push). The combina- impact. Especially for the European Community of Chemical tion of digital approaches such as multiscale modeling and Reaction Engineers organized under the auspices of European simulation in combination with experimentation and space Federation of Chemical Engineering (EFCE) it can be a contri- and time-resolved in situ measurements opens up the path to bution to help to establish a Roadmap on a European level. -
Advanced Control Methodology for Biomass Combustion
Advanced Control Methodology for Biomass Combustion Stefan Bjornsson A thesis submitted in partial fulfillment of the requirements for the degree of Master of Science in Mechanical Engineering University of Washington 2014 Committee: Igor V. Novosselov, Chair Philip C. Malte John C. Kramlich Program Authorized to Offer Degree: Department of Mechanical Engineering Table of Contents List of Figures .................................................................................................................................................iii List of Tables ................................................................................................................................................... vi Chapter 1 Introduction ................................................................................................................................ 2 1.1 Motivation ............................................................................................................................................. 2 1.2 Objectives .............................................................................................................................................. 3 Chapter 2 Literature Review & Fundamental Concepts ................................................................. 5 2.1 Biomass .................................................................................................................................................. 5 2.2 Biomass Combustion ........................................................................................................................ -
Chemical Reaction Engineering A. Sarath Babu
CHEMICAL REACTION ENGINEERING A. SARATH BABU 1 Course No. Ch.E – 326 CHEMICAL REACTION ENGINEERING Periods/ Week : 4 Credits: 4 Examination Teacher Assessment: Marks: 20 Sessionals: 2 Hrs Marks: 30 End Semester: 3 Hrs Marks : 50 1. KINETICS OF HOMOGENEOUS REACTIONS 2. CONVERSION AND REACTOR SIZING 3. ANALYSIS OF RATE DATA 4. ISOTHERMAL REACTOR DESIGN 5. CATALYSIS AND CATALYTIC RECTORS 6. ADIABATIC TUBULAR REACTOR DESIGN 7. NON-IDEAL REACTORS 2 TEXT BOOKS 1. Elements of Chemical Reaction Engineering - Scott Fogler H 2. Chemical Reaction Engineering - Octave Levenspiel 3. Introduction to Chemical Reaction Engineering & Kinetics, Ronald W. Missen, Charles A. Mims, Bradley A. Saville 4. Fundamentals of Chemical Reaction Engineering – Charles D. Holland, Rayford G. Anthony 5. Chemical Reactor Analysis – R. E. Hays 6. Chemical Reactor Design and operation – K. R. Westerterp, Van Swaaij and A. A. C. M. Beenackers 7. The Engineering of Chemical Reactions – Lanny D. Schmidt 8. An Introduction to Chemical Engineering Kinetics and Reactor Design – Charles G. Hill, Jr. 9. Chemical Reactor Design, Optimization and Scaleup – E. Bruce Nauman 3 10.Reaction Kinetics and Reactor Design – John B. Butt Without chemical reaction our world would be a barren planet. No life of any sort would exist. There would be no fire for warmth and cooking, no iron and steel to make even the crudest implements, no synthetic fibers for clothing, and no engines to power our vehicles. One feature that distinguishes the chemical engineer from others is the ability to analyze systems in which chemical reactions occur and to apply the results of the analysis in a manner that benefits society. -
16 Residence Time Distributions of Chemical Reactors Chapter 16
Fogler_Ch16.fm Page 1 Tuesday, March 14, 2017 6:24 PM Residence Time 16 Distributions of Chemical Reactors Nothing in life is to be feared. It is only to be understood. —Marie Curie Overview. In this chapter we learn about nonideal reactors; that is, reactors that do not follow the models we have developed for ideal CSTRs, PFRs, and PBRs. After studying this chapter the reader will be able to describe: • General Considerations. How the residence time distribution (RTD) can be used (Section 16.1). • Measurement of the RTD. How to calculate the concentration curve (i.e., the C-curve) and residence time distribution curve, (i.e., the E-curve (Section 16.2)). • Characteristics of the RTD. How to calculate and use the cumula- tive RTD function, F(t), the mean residence time, tm, and the vari- ance σ2 (Section 16.3). σ2 • The RTD in ideal reactors. How to evaluate E(t), F(t), tm, and for ideal PFRs, CSTRs, and laminar flow reactors (LFRs) so that we have a reference point as to how much our real (i.e., nonideal) reac- tor deviates form an ideal reactor (Section 16.4). • How to diagnose problems with real reactors by comparing tm, E(t), and F(t) with ideal reactors. This comparison will help to diagnose and troubleshoot by-passing and dead volume problems in real reactors (Section 16.5). 16.1 General Considerations The reactors treated in the book thus far—the perfectly mixed batch, the plug-flow tubular, the packed bed, and the perfectly mixed continuous tank reactors—have been modeled as ideal reactors. -
Heat Exchanger/Reactors (HEX Reactors): Concepts, Technologies: State-Of-The-Art
Review Heat exchanger/reactors (HEX reactors): Concepts, technologies: State-of-the-art Z. Anxionnaz a,b, M. Cabassud a,∗, C. Gourdon a, P. Tochon b a Laboratoire de Génie Chimique, UMR 5503 CNRS/INPT/UPS, 5 rue P. Talabot, BP 1301, 31106 Toulouse Cedex 1, France b Atomic Energy Commission-GRETh, 17 avenue des Martyrs, F-38054 Grenoble Cedex 9, France abstract Process intensification is a chemical engineering field which has truly emerged in the past few years and is currently rapidly growing. It consists in looking for safer operating conditions, lower waste in terms of costs and energy and higher productivity; and a way to reach such objectives is to develop multifunctional devices such as heat exchanger/reactors for instance. This review is focused on the latter and makes a point on heat exchanger/reactors. After a brief presentation of requirements due to transposition from batch to continuous apparatuses, Keywords: heat exchangers/reactors at industrial or pilot scales and their applications are described. Process intensification Heat exchanger reactor State-of-the-art Technology Continuous reactor Contents 1. Introduction........................................................................................................................................ 2030 2. Transposition from batch to continuous heat-exchanger/reactor ................................................................................ 2030 2.1. Thermal intensification.................................................................................................................... -
Distillation with Chemical Reaction
DISTILLATION WITH CHEMICAL REACTION:. ESTERIFICATION IN A PACKED COLUMN A thesis submitted to the University of London for the degree of Doctor of Philosophy by PETER ARISTOCLES PILAVAKIS, M.Sc., D.I.C. Department of Chemical Engineering and Chemical Technology, Imperial College of Science and Technology, London. February 1974 ABSTRACT A theoretical and experimental study was conducted of the esterification of methanol and acetic acid in a packed distillation column.. The investigation was divided into two parts dealing respectively with the equilibrium data and the distillation-reaction process. The isobaric vapour-liquid equilibrium data were determined experimentally for the binary, ternary and quaternary systems for which no data were available in literature. Cathala's ebulliometer was used for this purpose. The Margules equations in combination with Marek's equations, to take into consideration the nonideality of acetic acid, were used to correlate the equilibrium data for the quaternary system. In the process investigation part experiments were carried out in a distillation reaction column and compared with theoretical predictions. The latter were obtained from mathematical description of the steady-state operation of the process and'i€ consisted of the integration of differential equations obtained from combination of the mass and heat balances of the reacting system with the kinetic equations of reaction and mass transfer under distillation conditions. The model was employed to predict the performance of the column under different operating conditions which had not been examined experiment- ally. For design purposes a calculation procedure was developed to determine the column height under different operating conditions. To my family 4 ACKNOWLEDGEMENTS I wish to express my deep gratitude to Dr. -
Masters Thesis: Control of Reactive Batch Distillation Columns Via
Control of Reactive Batch Distillation Columns via Extents Transformation Carlos Samuel Méndez Blanco Master of Science Thesis Delft Center for Systems and Control Control of Reactive Batch Distillation Columns via Extents Transformation Master of Science Thesis For the degree of Master of Science in Systems and Control at Delft University of Technology Carlos Samuel Méndez Blanco June 13, 2017 Faculty of Mechanical, Maritime and Materials Engineering (3mE) · Delft University of Technology The work in this literature survey was done jointly with the Eindhoven University of Tech- nology Control Systems Department. Their cooperation is hereby gratefully acknowledged. Copyright c Delft Center for Systems and Control (DCSC) All rights reserved. Table of Contents Acknowledgements vii 1 Introduction 1 2 Reactive and Distillation Processes 5 2-1 DistillationandReactiveProcesses . ......... 5 2-2 ReactiveDistillationProcess . ....... 7 3 Extents Transformation for Reaction Systems 17 3-1 ExtentsofReaction ............................... 17 3-2 Variant and Invariant Spaces of Chemical Processes . ............ 20 3-2-1 InclusionofEnergyBalance. 24 3-2-2 SensitivityAnalysis . 27 3-3 Limitations of the extent transformation approach . ............. 29 3-3-1 Spanofthechemicalspeciesspace . .... 30 ⊺ 3-3-2 Rank deficiency of [N Win n0] ...................... 31 3-4 Linear Parameter-Varying (LPV) state space model . ........... 32 3-4-1 First Approach: Model with Disturbance . ...... 33 3-4-2 Second Approach: Change of variable Z .................. 35 3-5 ControlbasedontheLPVmodels . 38 3-5-1 Case 1: Control based on model with external disturbance ........ 38 3-5-2 Case 2: Control with change of variable Z ................. 42 4 Extension of the Extent Transformations to Multiphase Reaction Systems 49 4-1 Continuous Gas-LiquidReaction Systems. -
Chemical Reactor Modeling Hugo A
Chemical Reactor Modeling Hugo A. Jakobsen Chemical Reactor Modeling Multiphase Reactive Flows Second Edition 123 Hugo A. Jakobsen Department of Chemical Engineering Norwegian University of Science and Technology Trondheim Norway ISBN 978-3-319-05091-1 ISBN 978-3-319-05092-8 (eBook) DOI 10.1007/978-3-319-05092-8 Springer Cham Heidelberg New York Dordrecht London Library of Congress Control Number: 2014933274 Ó Springer International Publishing Switzerland 2014 This work is subject to copyright. All rights are reserved by the Publisher, whether the whole or part of the material is concerned, specifically the rights of translation, reprinting, reuse of illustrations, recitation, broadcasting, reproduction on microfilms or in any other physical way, and transmission or information storage and retrieval, electronic adaptation, computer software, or by similar or dissimilar methodology now known or hereafter developed. Exempted from this legal reservation are brief excerpts in connection with reviews or scholarly analysis or material supplied specifically for the purpose of being entered and executed on a computer system, for exclusive use by the purchaser of the work. Duplication of this publication or parts thereof is permitted only under the provisions of the Copyright Law of the Publisher’s location, in its current version, and permission for use must always be obtained from Springer. Permissions for use may be obtained through RightsLink at the Copyright Clearance Center. Violations are liable to prosecution under the respective Copyright Law. The use of general descriptive names, registered names, trademarks, service marks, etc. in this publication does not imply, even in the absence of a specific statement, that such names are exempt from the relevant protective laws and regulations and therefore free for general use.