I Lecture Note
Total Page:16
File Type:pdf, Size:1020Kb
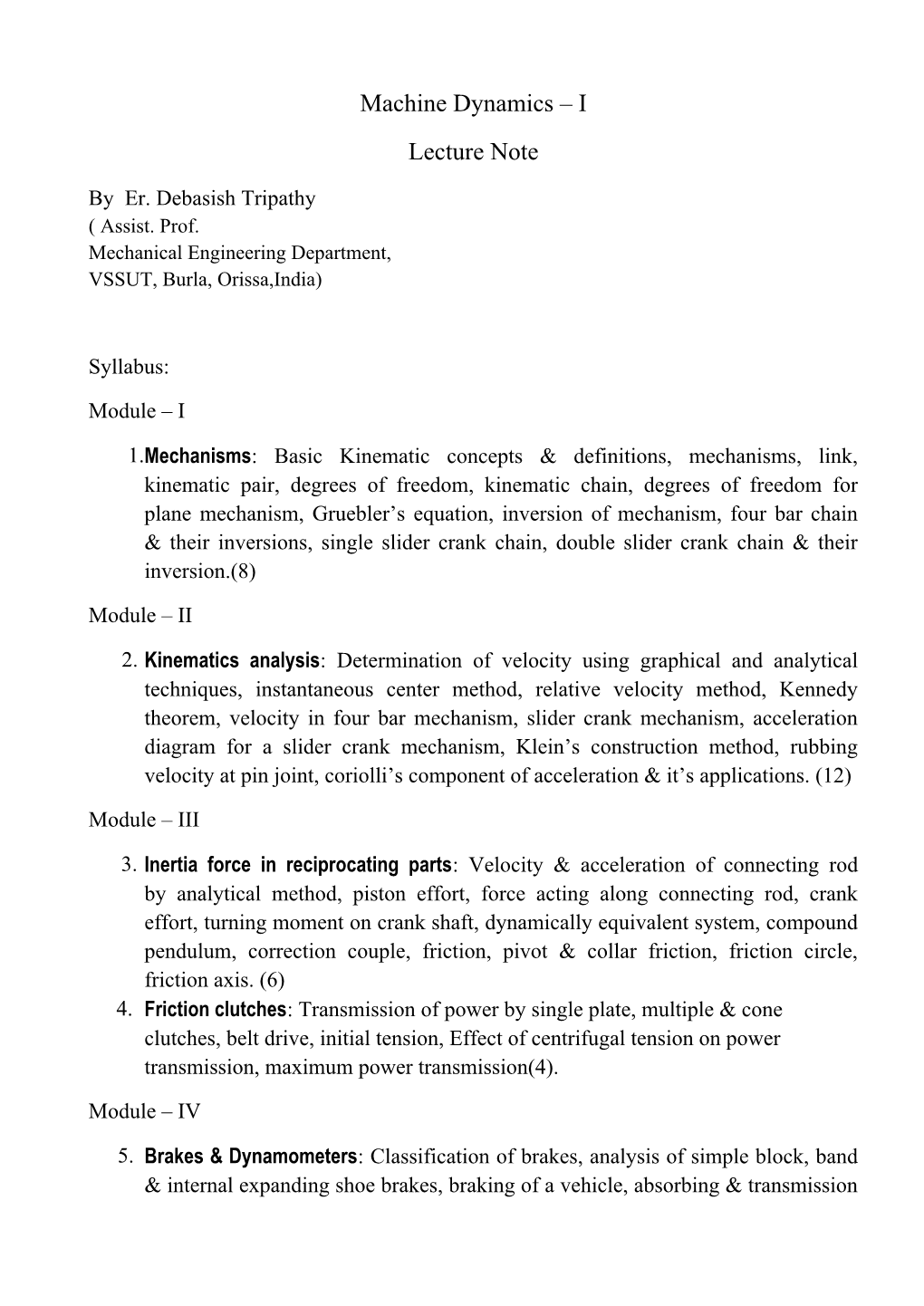
Load more
Recommended publications
-
A Collision Avoidance Method Using Assur Virtual Chains
ABCM Symposium Series in Mechatronics - Vol. 3 - pp.316-325 Copyright °c 2008 by ABCM A COLLISION AVOIDANCE METHOD USING ASSUR VIRTUAL CHAINS Henrique Simas, [email protected] Universidade do Vale do Itajaí - Centro de Ensino São José Curso de Engenharia de Computação Rodovia SC 407, km 4 - Sertão do Imaruim 88122 000 - São José, SC. Brasil Daniel Fontan Maia da Cruz, [email protected] Raul Guenther, [email protected] Daniel Martins, [email protected] Universidade Federal de Santa Catarina Departamento de Engenharia Mecânica Laboratório de Robótica Campus Universitário - Trindade 88040-900 – Florianópolis, SC. Brasil Abstract. In hydroelectric power plants, the rotor blades are eroded by the cavitation process. The erosion results in craters that are usually recovered by a manual welding process. The ROBOTURB project developed an automatized system, where a robot is used for recovery the rotor blade surfaces by welding process. The robot workspace is constrained by freeform surfaces and the collision imminency is constant. For this reason, the robot is redundant, making possible the collisions avoidance, keeping the end- effector trajectory tracking. In recent years, the collision avoidance problem has been dealt with algorithms based on artificial intelligence. This article considers a methodology for implementation a deterministic collision avoidance algorithm. The Solution of this proposal is based on the method of kinematic constraint and on the use of Assur virtual chains. The method consists in the obstacle identification and in the definition of a free collison workspace area. Thus, it is used a Assur virtual chain to detect and avoid the collision by evaluating the distance between a point at the robot and the obstacle. -
On the Configurations of Closed Kinematic Chains in Three
On the Configurations of Closed Kinematic Chains in three-dimensional Space Gerhard Zangerl Department of Mathematics, University of Innsbruck Technikestraße 13, 6020 Innsbruck, Austria E-mail: [email protected] Alexander Steinicke Department of Applied Mathematics and Information Technology, Montanuniversitaet Leoben Peter Tunner-Straße 25/I, 8700 Leoben, Austria E-mail: [email protected] Abstract A kinematic chain in three-dimensional Euclidean space consists of n links that are connected by spherical joints. Such a chain is said to be within a closed configuration when its link lengths form a closed polygonal chain in three dimensions. We investigate the space of configurations, described in terms of joint angles of its spherical joints, that satisfy the the loop closure constraint, meaning that the kinematic chain is closed. In special cases, we can find a new set of parameters that describe the diagonal lengths (the distance of the joints from the origin) of the configuration space by a simple domain, namely a cube of dimension n − 3. We expect that the new findings can be applied to various problems such as motion planning for closed kinematic chains or singularity analysis of their configuration spaces. To demonstrate the practical feasibility of the new method, we present numerical examples. 1 Introduction This study is the natural further development of [32] in which closed configurations of a two-dimensional kine- matic chain (KC) in terms of its joint angles were considered. As a generalization, we study the configuration spaces of a three-dimensional closed kinematic chain (CKC) with n links in terms of the joint angles of its spherical joints. -
Dynamic Analysis of Planar Rigid Multibody Systems Modeled Using Natural Absolute Coordinates C
View metadata, citation and similar papers at core.ac.uk brought to you by CORE provided by DSpace at University of West Bohemia ARTICLE IN PRESS Applied and Computational Mechanics 12 (2018) XXX–YYY Dynamic analysis of planar rigid multibody systems modeled using Natural Absolute Coordinates C. M. Pappalardoa,∗,D.Guidaa a Department of Industrial Engineering, University of Salerno, Via Giovanni Paolo II, 132, 84084 Fisciano, Salerno, Italy Received 5 July 2017; accepted 1 February 2018 Abstract This paper deals with the dynamic simulation of rigid multibody systems described with the use of two-dimensional natural absolute coordinates. The computational methodology discussed in this investigation is referred to as planar Natural Absolute Coordinate Formulation (NACF). The kinematic representation used in the planar NACF is based on a vector of generalized coordinates that includes two translational coordinates and four rotational parameters. In particular, the set of natural absolute coordinates is employed for describing the global location and the geometric orientation relative to the general configuration of a planar rigid body. The kinematic description utilized in the planar NACF is based on the separation of variable principle. Therefore, a constant symmetric positive-definite mass matrix and a zero inertia quadratic velocity vector associated with the centrifugal and Coriolis inertia effects enter in the formulation of the equations of motion. However, since a redundant set of rotational parameters is used in the kinematic description of the planar NACF for defining the geometric orientation of a rigid body, the introduction of a set of intrinsic normalization conditions is necessary for the mathematical formulation of the algebraic constraint equations. -
Mechanical Advantage Use the Equation for Mechanical Advantage to See How Machines Multiply Force
Name Date Class WORKSHEET MATH SKILLS USED Division MATH IN SCIENCE: PHYSICAL SCIENCE 53 Decimals Mechanical Advantage Use the equation for mechanical advantage to see how machines multiply force. The mechanical advantage of a machine is the factor by which the machine multiplies force. The mechanical advantage of a machine can be used to determine how well a ma- chine works and whether it can perform a particular job. output force EQUATION: mechanical advantage (MA) ϭ ᎏᎏ input force SAMPLE PROBLEM: What is the mechanical advantage of a lever that requires an input force of 20 N and lifts an object that weighs 60 N? 60 N mechanical advantage (MA) ϭ ᎏ 20 N MA ϭ 3 Practice Your Skills! Use the equation for mechanical advantage to answer the following questions: 1. Amanda uses a wheelbarrow to lift a load of bricks. The bricks weigh 600 N, which is more than Amanda could normally carry. However, with the wheelbarrow, Amanda can lift the bricks with as little as 120 N. What is the mechanical advantage of the wheelbarrow? 2. Marshall wants to remove a tree stump from the ground. To do this, he puts one end of a long beam under the stump and puts all of his weight on the other end. His weight is just enough to lift the stump. The stump weighs 400 N. Marshall weighs 250 N. What is the mechanical advantage of the lever Marshall is using? 3. A system of pulleys allows a mechanic to lift an 1800 N engine. t and Winston. All rights reserved. -
Chapter 14 Work, Power, and Machines
0161_hsps09_GRSW_Ch14.qxd 7/27/07 3:33 PM Page 157 Name ___________________________ Class ___________________ Date _____________ Chapter 14 Work, Power, and Machines Summary 14.1 Work and Power For a force to do work on an object, some of the force must act in the same direction as the object moves. If there is no movement, no work is done. • Work is the product of force and distance. • Work is done when a force moves an object over a distance. Any part of a force that does not act in the direction of motion does no work on an object. • The joule (J) is the SI unit of work. • When a force of 1 newton moves an object 1 meter in the direction of the force, 1 joule of work is done. Doing work at a faster rate requires more power. To increase power, you can increase the amount of work done in a given time, or you can do a given amount of work in less time. • Power is the rate of doing work. • The SI unit of power is the watt (W), which is equal to one joule per second. • One horsepower (hp) is equal to about 746 watts. 14.2 Work and Machines Machines make work easier to do. They change the size of a force needed, the direction of a force, or the distance over which a force acts. •Amachine is a device that changes a force. Because of friction, the work done by a machine is always less than the work done on the machine. -
Chapter 8 Glossary
Technology: Engineering Our World © 2012 Chapter 8: Machines—Glossary friction. A force that acts like a brake on moving objects. gear. A rotating wheel-like object with teeth around its rim used to transmit force to other gears with matching teeth. hydraulics. The study and technology of the characteristics of liquids at rest and in motion. inclined plane. A simple machine in the form of a sloping surface or ramp, used to move a load from one level to another. lever. A simple machine that consists of a bar and fulcrum (pivot point). Levers are used to increase force or decrease the effort needed to move a load. linkage. A system of levers used to transmit motion. lubrication. The application of a smooth or slippery substance between two objects to reduce friction. machine. A device that does some kind of work by changing or transmitting energy. mechanical advantage. In a simple machine, the ability to move a large resistance by applying a small effort. mechanism. A way of changing one kind of effort into another kind of effort. moment. The turning force acting on a lever; effort times the distance of the effort from the fulcrum. pneumatics. The study and technology of the characteristics of gases. power. The rate at which work is done or the rate at which energy is converted from one form to another or transferred from one place to another. pressure. The effort applied to a given area; effort divided by area. pulley. A simple machine in the form of a wheel with a groove around its rim to accept a rope, chain, or belt; it is used to lift heavy objects. -
To Download the PDF File
NOTE TO USERS This reproduction is the best copy available. UMJ Algebraic Screw Pairs by James D. Robinson A Dissertation submitted to the Faculty of Graduate and Postdoctoral Affairs in partial fulfilment of the requirements for the degree of Doctor of Philosophy in Mechanical Engineering Ottawa-Carleton Institute for Mechanical and Aerospace Engineering Department of Mechanical and Aerospace Engineering Carleton University Ottawa, Ontario, Canada May 2012 Copyright © 2012 - James D. Robinson Library and Archives Bibliotheque et Canada Archives Canada Published Heritage Direction du 1+1 Branch Patrimoine de I'edition 395 Wellington Street 395, rue Wellington Ottawa ON K1A0N4 Ottawa ON K1A 0N4 Canada Canada Your file Votre reference ISBN: 978-0-494-93679-5 Our file Notre reference ISBN: 978-0-494-93679-5 NOTICE: AVIS: The author has granted a non L'auteur a accorde une licence non exclusive exclusive license allowing Library and permettant a la Bibliotheque et Archives Archives Canada to reproduce, Canada de reproduire, publier, archiver, publish, archive, preserve, conserve, sauvegarder, conserver, transmettre au public communicate to the public by par telecommunication ou par I'lnternet, preter, telecommunication or on the Internet, distribuer et vendre des theses partout dans le loan, distrbute and sell theses monde, a des fins commerciales ou autres, sur worldwide, for commercial or non support microforme, papier, electronique et/ou commercial purposes, in microform, autres formats. paper, electronic and/or any other formats. The author retains copyright L'auteur conserve la propriete du droit d'auteur ownership and moral rights in this et des droits moraux qui protege cette these. Ni thesis. -
Levers and Gears: a Lot for a Little
Physics Levers and Gears: A lot for a little A surprising number of the tools and machines we rely on every day – from door handles and cricket bats to clocks and bikes – can be explained in terms of a few simple ideas. The same principles allowed ancient civilizations to build enormous pyramids and the mysterious astronomical device known as the Antikythera Mechanism. In this lesson you will investigate the following: • How do simple machines allow us to achieve a lot with little effort? • What is mechanical advantage and how does it apply to levers, wheels and gears? • How do gear systems work? So gear up for a look at how some of our most useful machines work. This is a print version of an interactive online lesson. To sign up for the real thing or for curriculum details about the lesson go to www.cosmosforschools.com Introduction: Levers and Gears A reconstruction of the Antikythera Mechanism. In 1900 a team of divers discovered a 2000-year-old shipwreck near the Greek island of Antikythera. Inside the wreck they found an incredible range of treasures including beautiful bronze statues and glass bowls. They also found a plain-looking lump of bronze no bigger than a shoebox. Closer examination revealed that the object had gear wheels embedded in it – as though it was some kind of ancient clock. It soon became known as the Antikythera Mechanism but its internal structure and purpose remained mysterious for decades. Later investigations using X-rays uncovered thirty interlocking gears and inscriptions of the ancient Greek words for “sphere” and “cosmos”. -
Simple Machines Work 5.1 What Is Work?
5 Table of Contents 5 Unit 1: Energy and Motion Chapter 5: Work and Machines 5.1: Work 5.2: Using Machines 5.3: Simple Machines Work 5.1 What is work? • To many people, the word work means something they do to earn money. • The word work also means exerting a force with your muscles. Work 5.1 What is work? • Someone might say they have done work when they push as hard as they can against a wall that doesn't move. • However, in science the word work is used in a different way. Work 5.1 Work Makes Something Move • Remember that a force is a push or a pull. In order for work to be done, a force must make something move. • Work is the transfer of energy that occurs when a force makes an object move. • If you push against the desk and nothing moves, then you haven't done any work. Work 5.1 Doing work • There are two conditions that have to be satisfied for work to be done on an object. • One is that the applied force must make the object move, and the other is that the movement must be in the same direction as the applied force. Work 5.1 Doing work • For example, when you lift a stack of books, your arms apply a force upward and the books move upward. Because the force and distance are in the same direction, your arms have done work on the books. Work 5.1 Force and Direction of Motion • When you carry books while walking, you might think that your arms are doing work. -
Design for Additive Manufacturing of Kinematic Pairs
DESIGN FOR ADDITIVE MANUFACTURING OF KINEMATIC PAIRS Shrey Pareek*, Vaibhav Sharma*, and Rahul Rai* *Design Analytics Research and Technology (DART) Lab, Department of Mechanical and Aerospace Engineering, University at Buffalo-SUNY, Buffalo-NY, 14260 Abstract While additive manufacturing processes are better suited for fabrication of parts with complex geometries, they face serious challenges whilst fabricating parts that require relative motion with respect to each other. The primary challenge in additive manufacturing of mechanisms is preventing the mating parts from bonding with each other during the fabrication process. In this paper the authors investigate design and additive fabrication of kinematic pairs that can move relative to each other. The paper outlines fabrication of kinematic pairs based on optimal clearance value for three basic lower order kinematic pairs, viz. revolute pair, prismatic pair, and cylindrical pair. Using empirical testing functional relationships between extractive force and clearance, and between moment and clearance have been developed. These functional relationships can be used by users to fabricate kinematic pairs using FDM based 3D printing processes. The efficacy of the proposed approach is demonstrated on 3D printed kinematic pairs and experimental validation studies. Introduction Additive manufacturing holds the unquestioned advantage over conventional manufacturing techniques when it comes to fabrication of parts with complex geometries. However, additive manufacturing (Fused Deposition Modeling in particular) encounters serious challenges whilst fabricating parts that require relative motion with respect to each other. Generally such models require that each part be produced separately and then assembled together. However, due to inherent inaccuracies of 3D printing these assemblies seldom function correctly. For instance, inaccurate circularity of a 3D printed shaft may prevent its smooth movement inside the hub. -
Department of Mechanical Engineering ME 8492 – Kinematics of Machinery Unit I – Introduction to Mechanism - MCQ Bank 1
ChettinadTech Dept. of MECH Department of Mechanical Engineering ME 8492 – Kinematics of Machinery Unit I – Introduction to Mechanism - MCQ Bank 1. In a reciprocating steam engine, which of the following forms a kinematic link ? (a) cylinder and piston (b) piston rod and connecting rod (c) crank shaft and flywheel (d) flywheel and engine frame Answer: (c) 2. The motion of a piston in the cylinder of a steam engine is an example of (a) completely constrained motion (b) incompletely constrained motion (c) successfully constrained motion (d) none of these Answer: (a) 3. The motion transmitted between the teeth of gears in mesh is (a) sliding (b) rolling (c) may be rolling or sliding depending upon the shape of teeth (d) partly sliding and partly rolling Answer: (d) 4. The cam and follower without a spring forms a (a) lower pair (b) higher pair (c) self closed pair (d) force closed pair Answer: (c) 5. A ball and a socket joint forms a (a) turning pair (b) rolling pair (c) sliding pair (d) spherical pair Answer: (d) 6. The lead screw of a lathe with nut forms a (a) sliding pair (b) rolling pair (c) screw pair (d) turning pair ME 8692 – Finite Element Analysis Page 1 ChettinadTech Dept. of MECH Answer: (c) 7. When the elements of the pair are kept in contact by the action of external forces, the pair is said to be a (a) lower pair (b) higher pair (c) self closed pair (d) force closed pair Answer: (d) 8. Which of the following is a turning pair ? (a) Piston and cylinder of a reciprocating steam engine (b) Shaft with collars at both ends fitted in a circular hole (c) Lead screw of a lathe with nut (d) Ball and socket joint Answer: (b) 9. -
TEE Final Report
Project Number: AHH – 1171 Pseudo‐Fluid Control Extension System A Major Qualifying Project Submitted to the Faculty of the WORCESTER POLYTECHNIC INSTITUTE in partial fulfillment of the requirements for the Degree of Bachelor of Science In Mechanical Engineering by John Dunbar ______________________________ Christopher Farren ______________________________ Mari Freitas ______________________________ Date: April 26, 2012 Approved: Keywords ______________________________ Professor Allen H. Hoffman, Major Advisor 1. Transducer 2. TEE 3. Pseudo‐fluid ______________________________ Professor Holly K. Ault, Co‐Advisor Abstract An interventional cardiologist (IC) performs procedures using a transesophageal echocardiogram transducer (TEE). The TEE is positioned by an echo cardiologist who is present for the entirety of the procedures. The purpose of this project was to redesign the user interface of the TEE in order to minimize the role of the echo cardiologist and give more control to the IC. This was accomplished by creating an extension of the TEE control system that can remotely control the TEE from a distance of five feet. Preliminary designs were created using cable and fluid hydraulic systems; however, both types of systems were problematic. A pseudo‐fluid system consisting of tubes filled with steel balls was developed to capture the positive aspects of the cable and fluid systems. The user interface of the new system consisted of two rotatable knobs that actuate rack and pinion gear sets, which push the pseudo‐ fluid balls through tubes. At the distal ends of the tubes, the balls move the racks of rack and pinion gear sets that in turn rotate shafts in the current TEE. The resulting user interface has similar ergonomic and mechanical properties as the original TEE.