Algorithm for Automatic Differential Locking System of a Heavy Truck
Total Page:16
File Type:pdf, Size:1020Kb
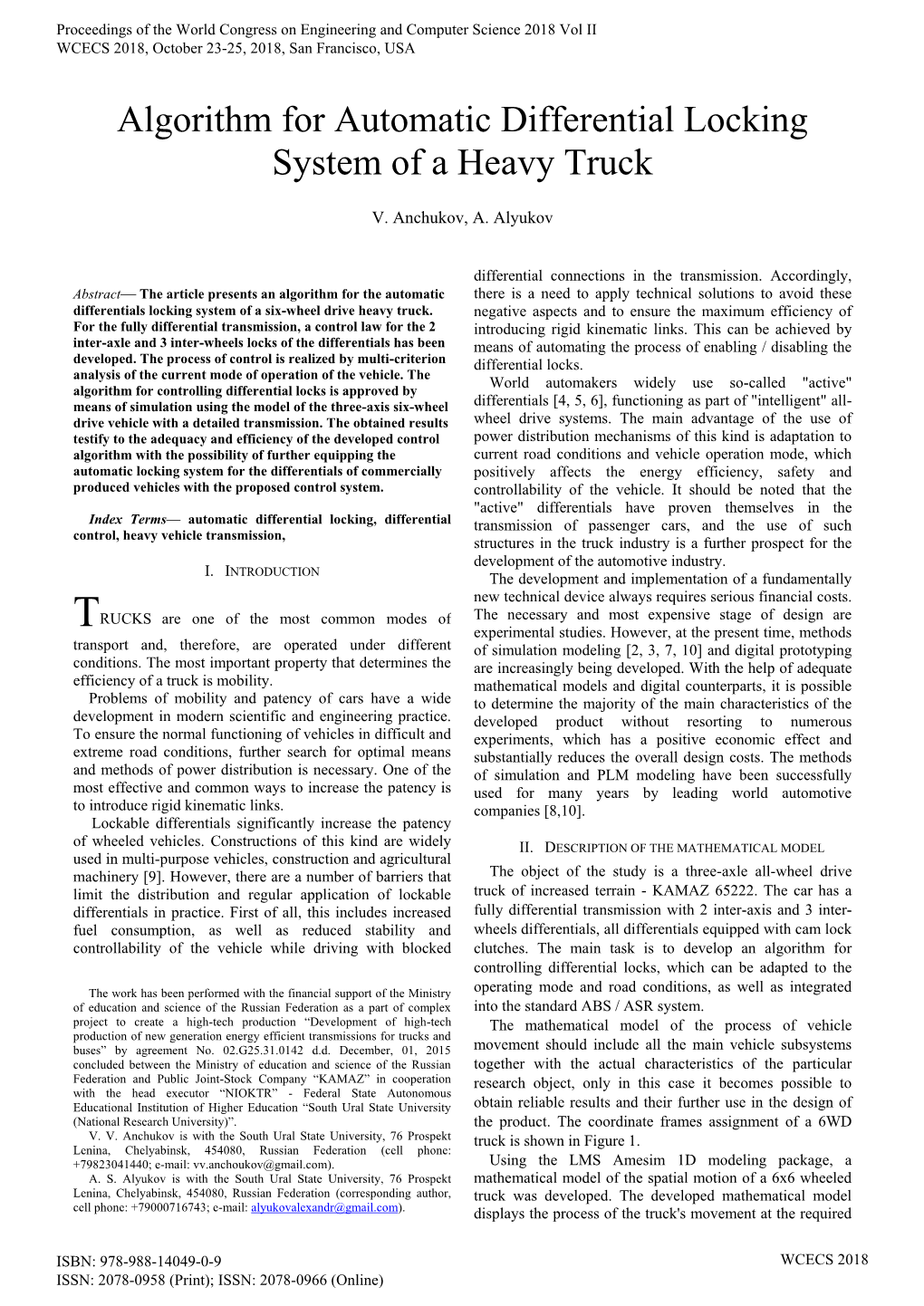
Load more
Recommended publications
-
LOCK-RIGHT™ Performance Locker Installation Manual
TM INSTALLATION MANUAL #1000703MIB LOCK-RIGHT BY POWERTRAX AUTOMATIC POSITIVE-LOCKING DIFFERENTIAL LOCK-RIGHT™ Performance Locker Installation Manual Integral Carrier Axles–C-Clip and non-C-Clip Versions Typical of Spicer, Jeep, G.M. 10-, 12-bolt, Ford 8.8-inch, Toyota L.C., etc. Introduction . .2 Differential Assembly Inspection . .19 Background Information . .3 Vehicle Final Assembly . .19 Tire Diameters . .21 Installations Covered . .6 Preliminary Steps . .6 Testing Your Installation . .21 Determination of Axle Type . .6 Driving Your Vehicle . .22 Differential Case Removal (thick ring gear) . .6 Subsequent Disassembly . .22 Disassembly of Differential Case . .8 Technical Assistance . .23 Inspection of the Parts . .9 Warranty Information . .23 Preparing Parts for Assembly . .10 The LOCK-RIGHT™ is manufactured in the U.S.A. Assembly of the Parts . .10 Powertrax by RICHMOND Differential Case Completion . .15 1208 Old Norris Road, P.O. Box 238 Case Final Assembly Into Vehicle . .18 Liberty, S.C. 29657 1 Introduction exactly what you are doing. These instructions also assume that you have the proper shop manual for reference to instruc- Welcome to the growing family of LOCK-RIGHT tions about axle shaft removal, torque values, settings, clear- owners! This manual will help you install your new ances, etc. that apply to your particular vehicle. Our manual is LOCK-RIGHT automatic 100% full-locking differential. When a general guide to operations but does not contain specific the installation is complete, your vehicle will have extreme information for each vehicle. traction! We trust that you will be pleased with its performance Remember: This instruction manual is provided for your and thank you for your confidence in our products. -
Differential Owner's Manual
Eaton Differentials Owner’s Manual NoSPIN® Revised 05/26/2020 Eaton Differentials Owner’s Manual Table of Contents Preface...................................................................... 2 History....................................................................... 2 Warranty.................................................................... 4 Detroit Locker / NoSPIN............................................ 6 Detroit Truetrac.......................................................... 10 Eaton Posi..................................................................14 Eaton ELocker............................................................ 18 Safety........................................................................ 23 Lubrication................................................................ 26 Installation................................................................. 28 Preface Eaton has been a leading manufacturer of premium quality OEM, military and aftermarket traction enhancing and performance differentials for more than 80 years. Each step in our manufacturing process, from design to final assembly and inspection, reflects the highest industry quality and engineering standards. This manual is intended to help provide safe and trouble- free operation for the life of the product. General Information Telephone: 800-328-3850 Website: eatonperformance.com Office Hours: 7:30 a.m. - 5:30 p.m. (ET) Mon. - Thu. 7:30 a.m. - 4:30 p.m. (ET) Fri. Automotive Focused History of Eaton 1900 - Viggo Torbensen develops and patents -
Eaton Axle Company, Manufacturing Conventional and Internal Gear Truck Axles 1920 - Eaton Axle Company Builds a New $1 Million Plant in Cleveland, OH
Eaton Differentials Owner’s Manual NoSPIN® Revised 04/20/2020 Eaton Differentials Install Manual Table of Contents Preface...................................................................... 2 History....................................................................... 2 Warranty.................................................................... 4 Detroit Locker / NoSPIN............................................ 6 Detroit Truetrac.......................................................... 10 Eaton Posi..................................................................14 Eaton ELocker............................................................ 18 Safety........................................................................ 23 Lubrication................................................................ 26 Installation................................................................. 28 Preface Eaton has been a leading manufacturer of premium quality OEM, military and aftermarket traction enhancing and performance differentials for more than 80 years. Each step in our manufacturing process, from design to final assembly and inspection, reflects the highest industry quality and engineering standards. This manual is intended to help provide safe and trouble- free operation for the life of the product. General Information Telephone: 800-328-3850 Website: eatonperformance.com Office Hours: 7:30 a.m. - 5:30 p.m. (ET) Mon. - Thu. 7:30 a.m. - 4:30 p.m. (ET) Fri. Automotive Focused History of Eaton 1900 - Viggo Torbensen develops and patents -
Sidecar Torsion Bar Suspension
Ural (Урал) - Dnepr (Днепр) Russian Motorcycle Part XIV: Plunger, Swing-Arm and Torsion Bar Evolution ( Ernie Franke [email protected] 09 / 2017 Swing-Arms and Torsion Bars for Heavy Russian Motorcycles with Sidecars • Heavy Russian Motorcycle Rear-Wheel Swing-Arm Suspension –Historical Evolution of Rear-Wheel Suspension Trans-Literated Terms –Rear-Wheel Plunger Suspension • Cornet: Splined Hub • Journal: Shaft –Rear-Wheel Swing-Arm Suspension • Stroller, Pram: Sidecar • Rocker Arm: Between Sidecar Wheel Axle and Torsion Bar • One-Wheel Drive (1WD) • Swing-Arm – Rear-Drive Swing-Arm • Torsion Bar (Rod) • Sway Bar: Mounting Rod • Two-Wheel Drive (2WD) • Suspension Lever: Swing-Arm – Rear-Drive Swing-Arm • Swing Fork: Swing-Arm –Not Covered: Front-Wheel Suspension Torsion Bar • Sidecar Frames and Suspension Systems –Historical Evolution of Sidecar Suspension –Sidecar Rubber Bumper and Leaf-Spring Suspension –Sidecar Torsion Bar Suspension –Sidecar Swing-Arm Suspension • Recent Advances in Ural Suspension Systems –2006: Nylock Nuts Used to Secure Final Drive to Swing-Arm –2007: Bottom-Out Travel Limiter on Sidecar Swing-Arm –2008: Ball Bearings Replace Silent-Block Bushings in Both Front and Rear Swing-Arms Heavy Russian motorcycle suspension started with the plunger (coiled spring) rear-wheel suspension on the M-72. This was replaced with the swing-arm (pendulum) and dual hydraulic shock absorbers on the K-750. Similarly the sidecar suspension was upgraded from the spring-leaf 2 to rubber isolators and a swing-arm approach in the -
Dana 44™ Front Crate Axles
Are You a Jeep® Wrangler® JK Off-Road Enthusiast Looking for the Ultimate Axle Upgrade? DANA 44™ FRONT CRATE AXLES Quick, Easy, and Affordable Direct Bolt-In Solution – and 100% Genuine Dana®. Engineered for all Jeep® Wrangler® JKs, 2007 to current, this Ultimate Dana 44™ front axle is built to meet Typical applications include (but are not limited to): the demands of serious off-road enthusiasts. Get a direct bolt-in solution that features a number of upgrades for added off-road durability, and enjoy added strength wherever you go. For more information on this quick, easy, and affordable upgrade, contact your Spicer sales representative, or visit us on the web at www.CrateAxle.com/Ultimate-44. Off-Road Vehicles Fork Lifts Pickup Trucks Pushback Tugs Rock Crawler Buggy Small Mining Shovels Dana Aftermarket Group PO Box 1000 Maumee, Ohio 43537 Know what you’re getting. Get what you know. Genuine Dana 44™ axles are synonymous with high-quality and performance in Warehouse Distributors: 1.800.621.8084 OE Dealers: 1.877.777.5360 4-wheel drive, street, strip and off-highway applications. Drive with confidence, knowing you’re riding on the most trusted name in axles. www.CrateAxle.com 44SPECDIMFRONT-12016 Printed in U.S.A. Copyright Dana Limited, 2016. www.CrateAxle.com All rights reserved. Dana Limited. The Dana 44™ Front Crate Axle. The Dana brand has long been synonymous with proven quality and performance. Now with the innovative Crate Axle program, you can get the exact axle you need right out of the box. The optimal solution for customization. -
2015 GMC Canyon
2016 GMC CANYON New for 2016: • 2.8L Duramax turbo-diesel engine • Rear-sliding window now standard on SLT and included in SLE Convenience Package AWARD-WINNING GMC CANYON THRIVES AMONG 2016 MIDSIZE TRUCKS GMC Canyon, the segment’s only premium midsize truck, raises the bar for everything from horsepower and efficiency to refinement – and its attributes are drawing accolades. In 2015, Canyon won Cars.com Midsize Pickup Challenge for its segment-leading capabilities and efficiency, including the latest in safety features, cargo-hauling and trailering versatility. Cars.com also applauded the Canyon SLT, the segment’s only premium vehicle, for its performance with a full load, as well as its design and high- end materials. Autoweek also honored Canyon as the “Best of the Best Truck for 2015,” while Wards Auto World recognized the Canyon as one of Ward’s 10 Best Interiors for 2015, based on criteria such as design harmony, ergonomics, materials, driver information, safety and comfort. New for 2016, Canyon offers a 2.8L Duramax turbo-diesel engine that takes its segment-leading capability and efficiency to new heights, including a maximum trailering rating of 7,700 pounds (3,493 kg). The standard engine remains a 2.5L four-cylinder that’s rated at up to 27 mpg on the highway, while an available 3.6L V-6 tops competitors’ V-6 offerings with up to 1,590 pounds (721 kg) of payload and up to 7,000 pounds (3,175 kg) maximum trailering. Canyon lineup Canyon is offered in base, SLE and SLT models, in 2WD and 4WD, and with an aggressively styled All-Terrain package offered on SLE models. -
Electric Vehicle Drivetrain Final Design Review
Electric Vehicle Drivetrain Final Design Review June 2, 2017 Sponsor: Zachary Sharpell, CEO of Sharpell Technologies [email protected] (760) 213-0900 Team: E-Drive Jimmy King [email protected] Kevin Moore [email protected] Charissa Seid [email protected] Statement of Disclaimer Since this project is a result of a class assignment, it has been graded and accepted as fulfillment of the course requirements. Acceptance does not imply technical accuracy or reliability. Any use of information in this report is done at the risk of the user. These risks may include catastrophic failure of the device or infringement of patent or copyright laws. California Polytechnic State University at San Luis Obispo and its staff cannot be held liable for any use or misuse of the project. Table of Contents Executive Summary ...................................................................................................................1 1.0 Introduction ..........................................................................................................................2 1.1 Original Problem Statement ...........................................................................................2 2.0 Background ..........................................................................................................................2 2.1 Drivetrain Layout ...........................................................................................................2 2.2 Gear Types .....................................................................................................................4 -
2019 CHEVROLET COLORADO ZR2 FAST FACT Colorado ZR2
2019 CHEVROLET COLORADO ZR2 FAST FACT Colorado ZR2 combines the nimbleness and maneuverability of a midsize pickup with the most off-road technology of any vehicle in its class.10 STARTING MSRP $43,495 (incl. DFC)1 EPA VEHICLE CLASS Midsize truck NEW FOR 2019 • Chevrolet Infotainment 32 systems with 7-inch or 8-inch-diagonal color touchscreens; 8-inch system with navigation3 is available • Two USB data ports4, including SD card reader and auxiliary input jack, located on front console • Two USB charging ports4, located on the rear of the center console • Six-way power-adjustable driver’s seat • Heated steering wheel • Standard Rear Vision Camera5 upgraded to HD view • Exterior colors: Crush, Shadow Gray Metallic and Pacific Blue Metallic VEHICLE HIGHLIGHTS • Colorado ZR2 delivers exceptional performance in a variety of scenarios, from technical rock crawling and tight two-track trails to high-speed desert running and daily driving • Offered with standard 3.6L V-6 and available 2.8L turbo-diesel • Front and rear track widths widened 3.5 inches over a standard Colorado • Suspension lifted 2 inches higher than a standard Colorado • Class-exclusive front and rear electronic locking differentials • Segment-first off-road application of Multimatic Dynamic Suspensions Spool Valve (DSSVTM) damper technology • Exclusive cast iron control arms for exceptional strength • Functional rock sliders offer better performance over rocks and obstacles, and the front and rear bumpers have been modified for better off-road clearance. • The front bumper has tapered ends to increase tire clearance when approaching obstacles. The bumper also integrates a thick, aluminum skid plate protecting the radiator and engine oil pan. -
Automation and Synchronization of Traction Assistance Devices to Improve Traction and Steerability of a Construction Truck
DEGREE PROJECT IN VEHICLE ENGINEERING, SECOND CYCLE, 30 CREDITS STOCKHOLM, SWEDEN 2017 Automation and synchronization of traction assistance devices to improve traction and steerability of a construction truck MEET DABHI KARTHIK RAMANAN VAIDYANATHAN KTH ROYAL INSTITUTE OF TECHNOLOGY SCHOOL OF ENGINEERING SCIENCES Abstract Automotive development has always been need-based and the product of today is an evolution over several decades and a diversified technology application to deliver better products to the end users. Steady increase in the deployment of on-board electronics and software is character- ized by the demand and stringent regulations. Today, almost every function on-board a modern vehicle is either monitored or controlled electronically. One such specific demand for AB Volvo arose out of construction trucks in the US market. Users seldom have/had a view of the operational boundaries of the drivetrain components, resulting in inappropriate use causing damage, poor traction and steering performance. Also, AB Volvo's stand-alone traction assistance functions were not sufficiently capable to handle the vehicle use conditions. Hence, the goal was set to automate and synchronize the traction assistance devices and software functions to improve the traction and steerability under a variety of road conditions. The first steps in this thesis involved understanding the drivetrain components from design and operational boundary perspective. The function descriptions of the various traction software functions were reviewed and a development/integration plan drafted. A literature survey was carried out seeking potential improvement in traction from differential locking and also its effects on steerability. A benchmarking exercise was carried out to identify competitor and supplier technologies available for the traction device automation task. -
3 Installing the Air Locker
DANA 70/80, 35 SPLINE, RD172 LOW SPEED AIR OPERATED LOCKING DIFFERENTIAL INSTALLATION GUIDE No liability is assumed for damages resulting in the use of the information contained herein. ARB Air Locker Air Operated Locking Differentials and Air Locker are trademarks of ARB Corporation Limited. Other product names used herein are for identification purposes only and may be trademarks of their respective owners. ARB 4x4 ACCESSORIES Corporate Head Office 42-44 Garden St Tel: +61 (3) 9761 6622 Kilsyth, Victoria Fax: +61 (3) 9761 6807 AUSTRALIA 3137 Australian enquiries [email protected] North and South American enquiries [email protected] Other international enquiries [email protected] www.arb.com.au Table of Contents: 1 Introduction 3 1.1 Pre-Installation Preparation 3 1.2 Tool-Kit Recommendations 4 2 Removing the Existing Differential 5 2.1 Vehicle Support 5 2.2 Differential Fluid Drain 5 2.3 Disconnecting the Axles 6 2.4 Marking the Bearing Caps 6 2.5 Checking the Current Backlash Amount 7 2.6 Removing the Differential Center 8 3 Installing the Air Locker 10 3.1 Insuring Adequate Oil Drainage 10 3.2 Approximate Backlash Shimming 11 3.3 Mounting the Ring Gear 15 3.4 Drilling and Tapping the Bulkhead Port 16 3.5 Assembling the Seal Housing 17 3.6 Pre-Load Shimming 18 3.7 Reinstalling the Bearing Caps 19 3.8 Checking the Backlash 20 3.9 Setting Up the Bulkhead Fitting 21 3.10 Bench Testing the Air Locker 23 4 Installing the Air System 24 4.1 Mounting the Solenoid 24 4.2 Running & Securing the Air Line 26 4.3 Connection to the Bulkhead Fitting -
Vw Type 2 Mini Locker
VW TYPE 2 MINI LOCKER Updated 1/14/12 5255-INST HOW THE MINI LOCKER FUNCTIONS MINI LOCKER FEATURES The Type 2 Mini Locker consists of two bi-directional over-running The Mini Locker’s design is simple and rugged, with no Belleville dog clutches. Each one has a driving member (the driver) and a driv- washers, clutch packs or cone clutches to break or wear out. It uses en member (the existing sidegear). Both clutches are rotated by the stainless steel springs for excellent resistance to high temperatures differential cross shafts to form a fully locking combination when and fatigue. The drivers and couplers are made from high-carbon engine torque is applied (see Figure 1). steel and are heat-treated for toughness and durability. Because it is “all gears”, it does not require special limited-slip differential The Mini Locker provides differential action when cornering by additives in the gear oil. allowing the rear wheels to rotate at different speeds. Because the outside wheel is “ground driven” faster than the inside wheel, the VEHICLE OPERATION dog clutch disengages, allowing the outside wheel to rotate freely; The Mini Locker is recommended for off-highway use only. A vehi- power continues to be applied to the slower (inside) wheel. In low cle equipped with a Mini Locker will have much more traction than traction situations, the Mini Locker will always deliver power to the before. We suggest that you get used to its new capabilities slowly. wheel with the most grip, with up to 100% of the engine’s torque Take it to an off-road area in which several types of terrain are pres- available to either wheel. -
LOCK-RIGHT Performace Locker Vehicle Owner’S Manual Table of Contents Introduction
LOCK-RIGHT Performace Locker Vehicle Owner’s Manual Table of Contents Introduction................................................................................2 Lubrication..................................................................................13 Important Information................................................................2 Temperature and Moisture........................................................14 The LOCK-RIGHT™ Troubleshooting..........................................................................14 Function........................................................................2 Servicing.....................................................................................15 Operation......................................................................3 Important Warranty Information...............................................15 Features........................................................................3 Limited Warranty........................................................................16 Exploded View...............................................................4 Front Axle Disconnect Operation..................................5 Vehicle Performance...................................................................6 Vehicle Operation........................................................................7 Driving Precautions....................................................................10 Driving Information Summarized...............................................12 WWW.RICHMONDGEAR.COM