Thermally Sprayed Coatings: Novel Surface Engineering Strategy Towards Icephobic Solutions
Total Page:16
File Type:pdf, Size:1020Kb
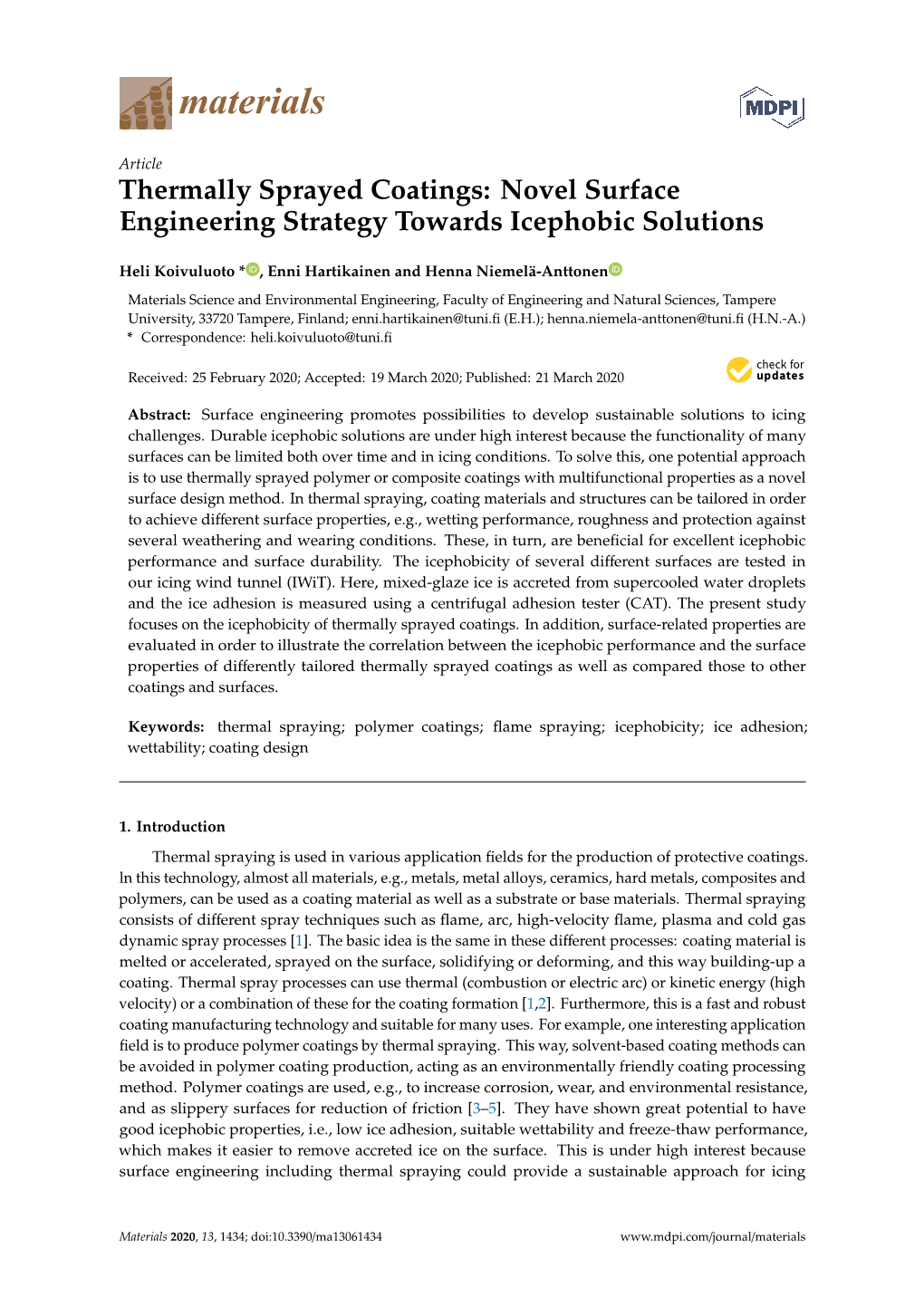
Load more
Recommended publications
-
Substrate Wettability Guided Oriented Self Assembly of Janus Particles
www.nature.com/scientificreports OPEN Substrate wettability guided oriented self assembly of Janus particles Meneka Banik1, Shaili Sett2, Chirodeep Bakli3, Arup Kumar Raychaudhuri2, Suman Chakraborty4* & Rabibrata Mukherjee1* Self-assembly of Janus particles with spatial inhomogeneous properties is of fundamental importance in diverse areas of sciences and has been extensively observed as a favorably functionalized fuidic interface or in a dilute solution. Interestingly, the unique and non-trivial role of surface wettability on oriented self-assembly of Janus particles has remained largely unexplored. Here, the exclusive role of substrate wettability in directing the orientation of amphiphilic metal-polymer Bifacial spherical Janus particles, obtained by topo-selective metal deposition on colloidal Polymestyere (PS) particles, is explored by drop casting a dilute dispersion of the Janus colloids. While all particles orient with their polymeric (hydrophobic) and metallic (hydrophilic) sides facing upwards on hydrophilic and hydrophobic substrates respectively, they exhibit random orientation on a neutral substrate. The substrate wettability guided orientation of the Janus particles is captured using molecular dynamic simulation, which highlights that the arrangement of water molecules and their local densities near the substrate guide the specifc orientation. Finally, it is shown that by spin coating it becomes possible to create a hexagonal close-packed array of the Janus colloids with specifc orientation on diferential wettability substrates. -
Porosity and Its Significance in Plasma-Sprayed Coatings
coatings Review Porosity and Its Significance in Plasma-Sprayed Coatings John Gerald Odhiambo 1,2 , WenGe Li 1,*, YuanTao Zhao 1,* and ChengLong Li 1 1 Naval Architecture and Ocean Engineering, Merchant Marine College, Shanghai Maritime University, Shanghai 201306, China 2 Marine Engineering and Maritime Operations, School of Mechanical, Manufacturing & Materials Engineering, Jomo Kenyatta University of Agriculture and Technology, P.O. Box 62000-00200 Nairobi, Kenya * Correspondence: [email protected] (W.L.); [email protected] (Y.Z.); Tel.: +86-139-1799-6912 (W.L.); +86-151-2116-7661 (Y.Z.) Received: 11 June 2019; Accepted: 16 July 2019; Published: 23 July 2019 Abstract: Porosity in plasma-sprayed coatings is vital for most engineering applications. Porosity has its merits and demerits depending on the functionality of the coating and the immediate working environment. Consequently, the formation mechanisms and development of porosity have been extensively explored to find out modes of controlling porosity in plasma-sprayed coatings. In this work, a comprehensive review of porosity on plasma-sprayed coatings is established. The formation and development of porosity on plasma-sprayed coatings are governed by set spraying parameters. Optimized set spraying parameters have been used to achieve the most favorable coatings with minimum defects. Even with the optimized set spraying parameters, defects like porosity still occur. Here, we discuss other ways that can be used to control porosity in plasma-sprayed coating with emphasis to atmospheric plasma-sprayed chromium oxide coatings. Techniques like multilayer coatings, nanostructured coatings, doping with rare earth elements, laser surface re-melting and a combination of the above methods have been suggested in adjusting porosity. -
Inverse Gas Chromatographic Examination of Polymer Composites
Open Chem., 2015; 13: 893–900 Invited Paper Open Access Adam Voelkel*, Beata Strzemiecka, Kasylda Milczewska, Zuzanna Okulus Inverse Gas Chromatographic Examination of Polymer Composites DOI: 10.1515/chem-2015-0104 received December 30, 2014; accepted April 1, 2015. of composite components and/or interactions between them, and behavior during technological processes. This paper reviews is the examination of Abstract: Inverse gas chromatographic characterization various polymer-containing systems by inverse gas of resins and resin based abrasive materials, polymer- chromatography. polymer and polymer-filler systems, as well as dental restoratives is reviewed. Keywords: surface activity, polymer-polymer interactions, 2 Discussion adhesion, dental restoratives, inverse gas chromatography 2.1 Surface energy and adhesion 1 Introduction IGC is useful for surface energy determination of solid polymers and fillers. Solid surface energy of consists of Inverse gas chromatography (IGC) was introduced in 1967 dispersive ( , from van der Waals forces) and specific by Kiselev [1], developed by Smidsrød and Guillet [2], and ( , from acid-base interactions) components: is still being improved. Its popularity is due to its simplicity D and user friendliness. Only a standard gas chromatograph = + (1) is necessary [3] although more sophisticated equipment has been advised. “Inverse” relates to the aim of the experiment. for solids can be calculated according to several It is not separation as in classical GC, but examination of methods [7]; one of the most often used is that of Schultz- the stationary phase properties. Test compounds with Lavielle [8-12]: known properties are injected onto the column containing dd the material to be examined. Retention times and peak RT××ln VN =× 2 N ×× aggsl × + C (2) profiles determine parameters describing the column filling. -
Nanoparticles Improving the Wetting Ability of Biological Liquids
dynam mo ic Torrisi and Scolaro, J Thermodyn Catal 2017, 8:1 er s h & T f C DOI: 10.4172/2157-7544.1000184 o a t l a a l Journal of y n r s i u s o J ISSN: 2157-7544 Thermodynamics & Catalysis Research Article Open Access Nanoparticles Improving the Wetting Ability of Biological Liquids Torrisi L* and Scolaro C Dottorato di Ricerca in Fisica and Dipartimento di Scienze Fisiche MIFT, Università di Messina, V.le F.S. D’Alcontres 31, 98166 S. Agata (ME), Italy Abstract The contact angle of some biological liquids was investigated on different biocompatible surfaces and nanoparticles were employed to improve their wetting ability. Biocompatible nanoparticles based on titanium, silver and gold were prepared using the technique of the pulsed laser ablation in liquids. The nanoparticles were characterized in size, shape, coalescence and concentration in solutions. Solid biocompatible substrates based on polyethylene, hydroxyapatite and titanium were employed as simulation of prosthetic surfaces. Measurements of contact angle were performed in different biological solution, including the human blood, with respect to the distilled water, without and with the use of the metallic nanoparticles at concentration of the order of 80-370 µg/ml. Keywords: Nanoparticles; Laser ablation; Contact angle; viscosity, thermal and electric conduction, vapour pressure, the PH Biocompatibility; Interfaces and other parameters [5,9]. The wetting ability of the liquid on a given surface changes introducing specific nanoparticles at the interface. This Introduction aspect is of special interest in Biology and Medicine, especially due More and more the nanotechnology is becoming important to the impact on the protein absorption and the cellular response in and promising in different fields of the science. -
Robust Omniphobic Surfaces
Robust omniphobic surfaces Anish Tutejaa,1, Wonjae Choib,1, Joseph M. Mabryc, Gareth H. McKinleyb,2, and Robert E. Cohena,2 aDepartment of Chemical Engineering, bDepartment of Mechanical Engineering, Massachusetts Institute of Technology, Cambridge, MA, 02139; and cAir Force Research Laboratory, Propulsion Directorate, Edwards Air Force Base, CA 93524 Edited by John M. Prausnitz, University of California, Berkeley, CA, and approved September 26, 2008 (received for review May 20, 2008) Superhydrophobic surfaces display water contact angles greater angle. The question that arises is, ‘‘Which of these states is naturally than 150° in conjunction with low contact angle hysteresis. Micro- realized by any given surface, and how can one design textures that scopic pockets of air trapped beneath the water droplets placed on promote the formation of a composite interface for a given liquid?’’ these surfaces lead to a composite solid-liquid-air interface in The answer is determined by considering the overall free energy of thermodynamic equilibrium. Previous experimental and theoreti- the system comprising the liquid droplet, the surrounding vapor, cal studies suggest that it may not be possible to form similar and the textured solid surface (13, 16, 18, 19). The critical value of fully-equilibrated, composite interfaces with drops of liquids, such the equilibrium contact angle (c) beyond which the composite as alkanes or alcohols, that possess significantly lower surface interface leads to a lower overall free energy, in comparison to the ؍ ␥ tension than water ( lv 72.1 mN/m). In this work we develop fully wetted interface, can be determined by equating the Wenzel surfaces possessing re-entrant texture that can support strongly and Cassie-Baxter relations. -
Inverse Gas Chromatography a Tool to Follow
Inverse gas chromatography a tool to follow physicochemical modifications of pharmaceutical solids: Crystal habit and particles size surface effects María Graciela Cares Pacheco, Rachel Calvet, G. Vaca-Medina, A. Rouilly, Fabienne Espitalier To cite this version: María Graciela Cares Pacheco, Rachel Calvet, G. Vaca-Medina, A. Rouilly, Fabienne Espitalier. In- verse gas chromatography a tool to follow physicochemical modifications of pharmaceutical solids: Crystal habit and particles size surface effects. International Journal of Pharmaceutics, Elsevier, 2015, 494 (1), pp.113-126. 10.1016/j.ijpharm.2015.07.078. hal-01611017 HAL Id: hal-01611017 https://hal.archives-ouvertes.fr/hal-01611017 Submitted on 5 Sep 2018 HAL is a multi-disciplinary open access L’archive ouverte pluridisciplinaire HAL, est archive for the deposit and dissemination of sci- destinée au dépôt et à la diffusion de documents entific research documents, whether they are pub- scientifiques de niveau recherche, publiés ou non, lished or not. The documents may come from émanant des établissements d’enseignement et de teaching and research institutions in France or recherche français ou étrangers, des laboratoires abroad, or from public or private research centers. publics ou privés. Inverse gas chromatography a tool to follow physicochemical modifications of pharmaceutical solids: Crystal habit and particles size surface effects a, a b,c b,c a M.G. Cares-Pacheco *, R. Calvet , G. Vaca-Medina , A. Rouilly , F. Espitalier a Université de Toulouse; Mines Albi, UMR CNRS 5302, Centre RAPSODEE; Campus Jarlard, F-81013 Albi cedex 09, France b Université de Toulouse; INP-ENSIACET, LCA, 310130 Toulouse, France c INRA; UMR 1010 CAI, 310130 Toulouse, France A B S T R A C T Powders are complex systems and so pharmaceutical solids are not the exception. -
Thermal Spraying of Polymer-Ceramic Composite Coatings with Multiple Size
Thermal Spraying of Polymer-Ceramic Composite Coatings with Multiple Size Scales of Reinforcements A Thesis Submitted to the Faculty of Drexel University by Varun Gupta in partial fulfillment of the requirements for the degree of Master of Science in Materials Engineering April, 2006 i © Copyright 2006 Varun Gupta. All Rights Reserved. ii DEDICATION To my parents iii ACKNOWLEDGEMENTS I would like to express my gratitude to my primary advisor, Dr. Richard Knight, for his guidance, constant support and advice in many aspects of my graduate studies and research work but especially for the invaluable insights into thermal spray technology and a great influence on my professional development. I would like to thank my co-advisor, Dr. Richard Cairncross, for his always constant motivation, understanding, trust and support given throughout the course of my graduate studies. I deeply appreciate the friendship, assistance and practical help of Mr. Dustin Doss and Mr. Milan Ivosevic in working with me on this project, especially for the hands-on introduction to thermal spraying. I would also like to extend my thanks to Ms. Dee Breger for all her help during the SEM analysis and to Mr. Kishore Kumar Tenneti for assistance with the TGA analysis during the course of this project. I would like to give my special thanks to Mr. Ranjan Dash, Ms. Maria Pia Rossi, Mr. Davide Mattia, Mr. Brandon McWilliams and Mr. Stephen Niezgoda for their constant motivation and help. I also wish to thank all my friends, colleagues, faculty and staff members in the Department of Materials Science and Engineering who gave me the opportunity to learn from their advice and who have made my stay here at Drexel unforgettable. -
Thermal Spraying Technology and Applications
Thermal Spraying Technology and Applications Course No: T04-002 Credit: 4 PDH A. Bhatia Continuing Education and Development, Inc. 22 Stonewall Court Woodcliff Lake, NJ 07677 P: (877) 322-5800 [email protected] EM 1110-2-3401 29 Jan 99 1 EM 1110-2-3401 29 Jan 99 2 EM 1110-2-3401 29 Jan 99 DEPARTMENT OF THE ARMY EM 1110-2-3401 U.S. Army Corps of Engineers Washington, DC 20314-1000 Engineering and Design THERMAL SPRAYING: NEW CONSTRUCTION AND MAINTENANCE Table of Contents Subject Paragraph Page Chapter 1 Introduction Purpose 1-1 1-1 Applicability 1-2 1-1 References 1-3 1-1 Distribution Statement 1-4 1-1 Abbreviations and Acronyms 1-5 1-1 Neutral Language Use and Terms 1-6 1-1 Scope 1-7 1-1 Chapter 2 Thermal Spray Fundamentals Introduction 2-1 2-1 General Description of Thermal Spraying 2-2 2-1 Characteristics of Thermal Spray Coatings 2-3 2-1 Types of Thermal Spray Coatings 2-4 2-2 Thermal Spray Processes 2-5 2-3 Thermal Spray Uses 2-6 2-7 Chapter 3 Thermal Spray Materials Introduction 3-1 3-1 Specifications 3-2 3-1 Procurement 3-3 3-1 Classification 3-4 3-1 Acceptance 3-5 3-2 Certification 3-6 3-2 Sizes 3-7 3-2 Packaging 3-8 3-3 Identification and Marking 3-9 3-3 Manufacture 3-10 3-3 Testing 3-11 3-3 3 EM 1110-2-3401 29 Jan 99 Subject Paragraph Page Chapter 4 Thermal Spray Coating Cost and Service Life Introduction 4-1 4-1 Cost 4-2 4-1 Service Life 4-3 4-2 Chapter 5 Thermal Spray Coating Selection Introduction 5-1 5-1 Service Environments 5-2 5-1 Other Considerations in Coating Selection 5-3 5-4 Thermal Spray Selection for Ferrous -
Contact Angle Vs Dyne
A practical means to measure surface treatment levels of PE Film using PGX+, a new portable contact angle instrument. Contact angle measurements The PGX + uses a liquid droplet (e.g. water) applied to the surface of the substrate in order to determine properties specific to the surface layer of the material. This is commonly referred to as a contact angle measurement using “the sessile drop method”. The contact angle is measured as the inward angle between the base and the tangent at the point of contact between the liquid and the surface. This value corresponds to the surface energy level in the equilibrium system formed between the liquid and the solid on the condition the surface is smooth, non-porous, non-sorptive, and homogeneous. Furthermore the liquid must not react chemically with the substrate. The relationship between a static contact angle and the surface energy forces was defined by Young [1] from the interfacial tensions: γSV = γSL + γLV cos θ; γ LV where γSV = solid-vapour interaction γSL =solid-liquid interaction γLV = liquid-vapour interaction θ ”Wetting” is obtained if contact angle is ≤ 90° γ SV γ SL Static contact angles A static contact angle occurs where the water droplet reaches an A “flying saucer”? “equilibrium” condition and the dimensions of the liquid droplet would not change over time. This situation will normally occur for a non- θ < 9 absorbent substrate (e.g. liquid container board, release papers). This 0° condition would also occur when a water droplet is applied to a copy paper because of its “hydrophobicity” (water repellence). -
Application Notes Metallographic Preparation of Thermal Spray Coatings
Metallographic preparation of thermal spray coatings Application Notes Thermal spraying was invented in the early 1900s using zinc for „metallizing” substrates for corrosion protection. The development of the plasma spray gun in the late 50s and 60s made it commercially viable to use high temperature materials such as ceramics and refractory metals for coating materials. In addition to fl ame and plasma spraying, today thermal spray methods include high velocity and detona- tion spraying using a multitude of different spray materials for the most diverse and demanding applications. Thermal spray coatings are applied to a substrate to give a specifi c surface quali- ty, which it originally does not have. Thus Metallography of thermal spray coatings the bulk strength of a part is given by the can have several purposes: substrate, and the coating adds superior - To defi ne, monitor and control spraying surface qualities such as corrosion, wear conditions for quality control or heat resistance. - For failure analysis Therefore thermal spray coatings are wide- - For developing new products. ly used in the aerospace and power gene- ration industry for new and refurbished The procedure normally involves coating sections and parts for jet engines and a test coupon to defi ne and optimize the gas turbines, compressors and pumps. process for the part to be sprayed. Sec- The properties of some coatings can only tions of this test coupon are then metal- be fabricated by thermal spraying, using lographically prepared and examined to mainly metals, ceramics, carbides and assess coating thickness, size and distribu- composites as well as mixtures of various tion of porosity, oxides and cracks, adhe- materials. -
(12) United States Patent (10) Patent No.: US 6,852,433 B2 Maeda (45) Date of Patent: Feb
USOO6852433B2 (12) United States Patent (10) Patent No.: US 6,852,433 B2 Maeda (45) Date of Patent: Feb. 8, 2005 (54) RARE-EARTH OXIDE THERMAL SPRAY 5.993,970 A 11/1999 Oscarsson et al. COATED ARTICLES AND POWDERS FOR 6,080.232 A * 6/2000 Sperlich et al.............. 106/436 THERMAL SPRAYING 6,582,814 B2 * 6/2003 Swiler et al. ............... 428/328 2002/0177001 A1 11/2002 Harada et al. (75) Inventor: Takao Maeda, Takefu (JP) FOREIGN PATENT DOCUMENTS (73) Assignee: Shin-Etsu Chemical Co., Ltd., Tokyo (JP) JP 2001-164354 A 6/2001 (*) Notice: Subject to any disclaimer, the term of this OTHER PUBLICATIONS patent is extended or adjusted under 35 U.S.C. 154(b) by 0 days. U.S. Appl. No. 10/101,612, filed Mar. 21, 2002, Takai et al. (21) Appl. No.: 10/618,679 U.S. Appl. No. 10/173,030, filed Jun. 18, 2002, Takai et al. (22) Filed: Jul. 15, 2003 U.S. Appl. No. 10/173,031, filed Jun. 18, 2002, Takai et al. (65) Prior Publication Data * cited by examiner US 2004/0013911A1 Jan. 22, 2004 (30) Foreign Application Priority Data Primary Examiner Jennifer McNeil (74) Attorney, Agent, or Firm-Birch, Stewart, Kolasch & Jul. 19, 2002 (JP) ....................................... 2002-211400 Birch, LLP (51) Int. Cl. ............................ B32B 15/04; B32B 9/04 (57) ABSTRACT (52) U.S. Cl. ....................... 428/697; 428/701; 428/702; 428/699; 428/469; 428/698 A rare-earth oxide thermal spray coated article comprising a (58) Field of Search ................................. 428/469, 701, Substrate and a coating layer formed by thermally spraying 428/702, 699, 698, 697: 106/474, 403, a rare-earth oxide thermal spraying powder onto a Surface of 479, 436 the Substrate, Said coating layer being of a gray or black color having, in the L*a*b* color space, an L* value of up (56) References Cited to 50, an a value of -3.0 to +3.0, and a b value of -3.0 to +3.0. -
Detonation Thermal Spraying Process of Metal
Technology Lappeenranta/Imatra Degree Programme in Mechanical Engineering and Production Technology Specialisation Andrey Vinogradov Detonation thermal spraying process of metal- ceramic coating of the inner body of a regulating valve for maintenance of turbine condensate level in a deaerator for a nuclear power plant Bachelor’s Thesis 2015 1 Abstract Andrey Vinogradov Detonation thermal spraying process of metal-ceramic coating of the inner body of a regulating valve for maintenance of turbine condensate level in a deaerator for a nuclear power plant, 41 pages, 3 appendices Saimaa University of Applied Sciences Technology Lappeenranta Degree Programme in Mechanical Engineering and Production Technology Bachelor’s Thesis 2015 Instructors: Lecturer Jukka Nisonen, Saimaa University of Applied Sciences Managing Director Zelenin Y.V., main process engineer Shvedov N.G., process engineer Karpenko D., Center of Scientific-Technical Service "Prometey" The objective of the research was to examine a process of metal-ceramic deto- nation spraying, technology and realization of the procedure and its features for the given component. The work was commissioned by main process engineer Shvedov N. G. This study was carried out at the Center of Scientific-Technical Service "Prometey". The information was gathered from internal documentation of the enterprise, manuals, literature and by interviewing process engineers. As a result of this thesis the detonation coating process was investigated for a particular unit – the regulating valve. All the stages and requirements were pre- sented. The results can be applied to any detonation coating case or surface treatment matter where complex approach is necessary. Keywords: coating, valve, deposition, spraying, mixture, powder, assembly, component, aluminum oxide, spraying gun, surface, nozzle, plunger, process.