Setting the Free Material Design Problem Through the Methods Of
Total Page:16
File Type:pdf, Size:1020Kb
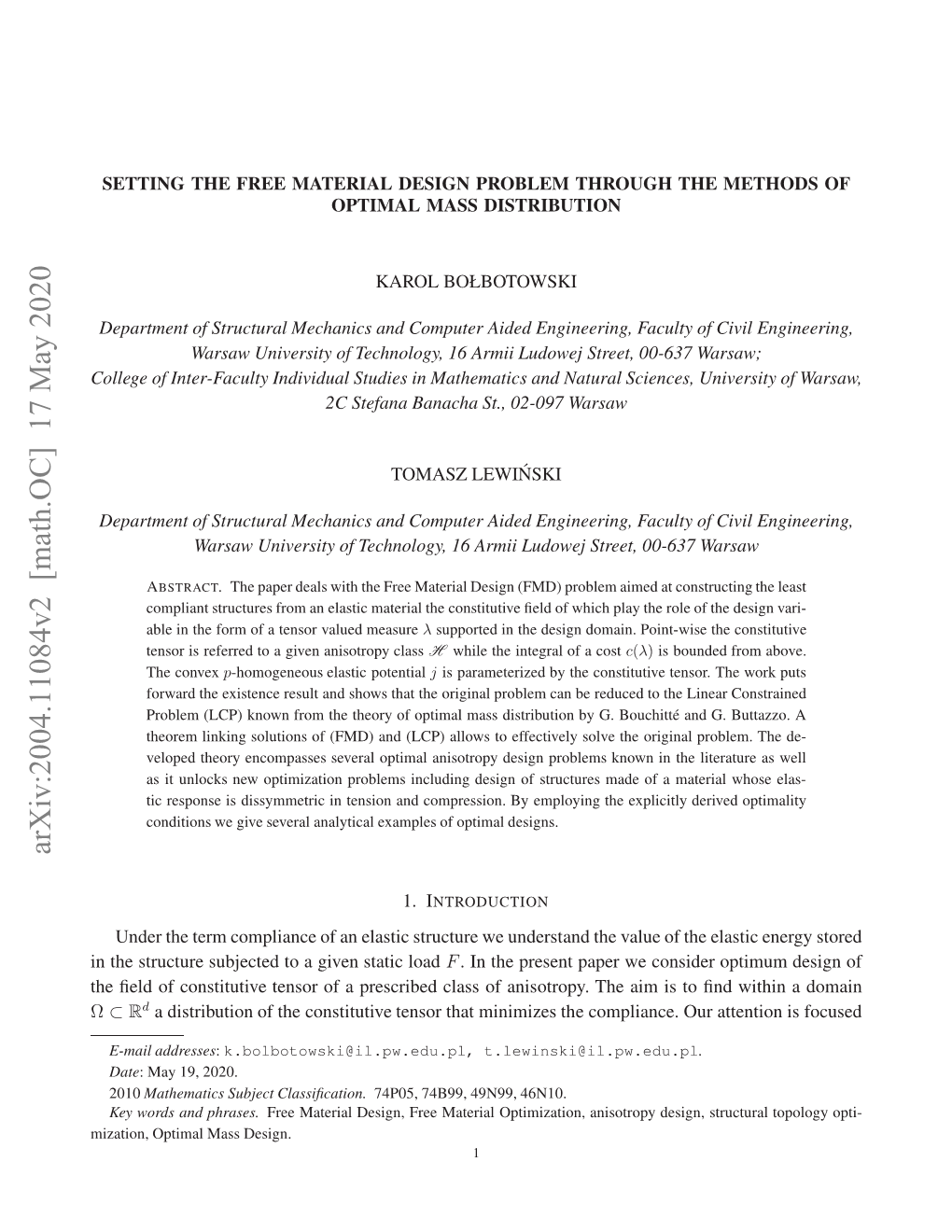
Load more
Recommended publications
-
On Bounding, Interior and Covering Functions
View metadata, citation and similar papers at core.ac.uk brought to you by CORE provided by Elsevier - Publisher Connector JOURNAL OF MATHEMATICAL ANALYSIS AND APPLICATIONS 82, 255-267 (1981) On Bounding, Interior and Covering Functions J. WARGA* Deparlmenl of Mathematics, Northeastern University, Boston, Massachusetts 02115 Submitted by Harold Kushner We prove three theorems yielding sufficient conditions for a continuous function f: X-t Y to have no isolated bounding points (i.e., points at which it is not an open mapping), to be interior a L (i.e., f(z) Ef(X)‘), and to have its image cover a segment. In the first theorem X and Y are rather general topological spaces and some applications to optimal control are discussed. In the second and third theorems X an Y are finite-dimensional and we use the concepts of ordinary and unbounded derivate containers which are a form of set-valued derivatives. The proof of the second theorem also involves the topological degree off: 1. INTRODUCTION Let X and Y be topological spaces, f: X+ Y and X E X. We shall write A’, &!,A for the interior, boundary and closure of A and shall refer to a set H as a neighborhood (nhd) of a point x or a set A if Ho contains x or A. We shall say that (a) 3 is a bounding point for f and f is bounding at X iff(2) E af(H) for some nhd H of X. If f is not bounding at X we say that f is open at X; (b) f is interior at X if f(X) E f(X)“; and (c) f is a covering of A if f(X) 2 A. -
Quasi-Barrelled Locally Convex Spaces 811
i960] quasi-barrelled locally convex spaces 811 Bibliography 1. R. E. Lane, Absolute convergence of continued fractions, Proc. Amer. Math. Soc. vol. 3 (1952) pp. 904-913. 2. R. E. Lane and H. S. Wall, Continued fractions with absolutely convergent even and odd parts, Trans. Amer. Math. Soc. vol. 67 (1949) pp. 368-380. 3. W. T. Scott and H. S. Wall, A convergence theorem for continued fractions, Trans. Amer. Math. Soc. vol. 47 (1940) pp. 155-172. 4. H. S. Wall, Analytic theory of continued fractions, New York, D. Van Nostrand Company, Inc., 1948. The University of Texas and University of Houston QUASI-BARRELLED LOCALLY CONVEX SPACES MARK MAHOWALD AND GERALD GOULD 1. Introduction and preliminary definitions. The main object of this paper is to answer some problems posed by Dieudonné in his paper Denumerability conditions in locally convex vector spaces [l]. His two main results are as follows: Proposition 1. If Eis a barrelled space on which there is a countable fundamental system of convex compact subsets, [Definition 1.2] then it is the strong dual of a Fréchet-Montel Space. Proposition 2. If E is either bornological or barrelled, and if there is a countable fundamental system of compact subsets, then E is dense in the strong dual of a Fréchet-Montel Space. Two questions raised by Dieudonné in connection with these results are: (a) If E is either bornological or barrelled then it is certainly quasi- barrelled [l, Chapter 3, §2, Example 12]. Can one substitute this weaker condition on E in Proposition 2? (b) Is there is an example of a quasi-barrelled space which is neither barrelled nor bornological? We shall show that the answer to (a) is "Yes," and that the answer to (b) is also "Yes," so that the generalization is in fact a real one. -
2-Symmetric Locally Convex Spaces
2-SYMMETRIC LOCALLYCONVEX SPACES D. E. EDMUNDS In [l] it is shown that barrelledness and quasi-barrelledness are merely the two extreme examples of a property, called 2-symmetry, which may be possessed by a locally convex Hausdorff topological vector space. The object of this note is to show how recent char- acterisations [2; 3] of barrelled and quasi-barrelled spaces may be subsumed under characterisations of 2-symmetric spaces, and to ex- hibit some properties of these spaces. First we need some definitions and simple results. 1. Let £ be a locally convex Hausdorff topological vector space (abbreviated to LCS in what follows), and let S be a class of bounded subsets of E whose union is E. Let E' denote the topological dual of E, and let E'z be the set E' endowed with the topological of uniform convergence on the members of 2. Definition 1. A subset of E is said to be X-bornivorous if it absorbs every member of 2. Definition 2. We say that E is "2-symmetric if any of the following equivalent conditions hold : (a) Every S-bornivorous barrel in £ is a neighbourhood of zero. (b) Every bounded subset of E'j¡ is equicontinuous. (c) The topology induced on E by the strong dual of E% is the original topology of E. The equivalence of these conditions was proved in [l]. If 2iG22 it is easy to see that Si-symmetry implies 22-symmetry ; the strongest restriction on E is obtained by taking for 2 the class s of all subsets of E consisting of a single point, and then S-symmetry is simply the property of being barrelled. -
Abdus Salam United Nations Educational, Scientific and Cultural International Organization Centre
the Miii abdus salam united nations educational, scientific and cultural international organization centre international atomic energy agency for theoretical physics ON WEIGHTED SPACES WITHOUT I A FUNDAMENTAL SEQUENCE OF BOUNDED SETS J.O. Olaleru 4 Available at: http://www. ictp.trieste.it/~pub_ off IC/2001/7 United Nations Educational Scientific and Cultural Organization and International Atomic Energy Agency THE ABDUS SALAM INTERNATIONAL CENTRE FOR THEORETICAL PHYSICS ON WEIGHTED SPACES WITHOUT A FUNDAMENTAL SEQUENCE OF BOUNDED SETS J.O. Olaleru1 Mathematics Department, University of Lagos, Yaba, Lagos and The Abdus Salam International Centre for Theoretical Physics, Trieste, Italy. Abstract The problem of countably quasibarrelledness of weighted spaces of continuous functions, of which there are no results in the general setting of weighted spaces, is takcled in this paper. This leads to the study of quasibarrelledness of weighted spaces which, unlike that of Ernst and Schnettler[4], though with a similar approach, we drop the assumption that the weighted space has a fundamental sequence of bounded sets. The study of countably quasibarrelledness of weighted spaces naturally leads to definite results on the weighted (DF)-spaces for those weighted spaces with a fundamental sequence of bounded sets. MIRAMARE - TRIESTE September 2001 'E-mail: [email protected] 1. Introduction and notations The countably barrelledness,countably quasibarrelledness, barrelledness, quasibarrelleness of the space C(X) of continuous functions on a completely regular Hausdorff space X equipped with the compact open topology(c-op), including when it is a (DF)-space and (gDF)-space, is well known (e.g.see [8] and [14]). In the more general setting of weighted spaces, Ernst and Schnettler[4] studied the (gDF) and the quasibarrelledness of weighted spaces by constructing a Nachbin family on X which is based on the assumption that the weighted space has a fundamental sequence of bounded sets. -
Fundamental Bounded Resolutions and Quasi-$(DF) $-Spaces
FUNDAMENTAL BOUNDED RESOLUTIONS AND QUASI-(DF )-SPACES J. C. FERRANDO, S. GABRIYELYAN, AND J. KA¸KOL Abstract. We introduce a new class of locally convex spaces E, under the name quasi-(DF )- spaces, containing strictly the class of (DF )-spaces. A locally convex space E is called a quasi- (DF )-space if (i) E admits a fundamental bounded resolution, i.e. an NN-increasing family of bounded sets in E which swallows all bounded set in E, and (ii) E belongs to the class G (in sense of Cascales–Orihuela). The class of quasi-(DF )-spaces is closed under taking subspaces, countable direct sums and countable products. Every regular (LM)-space (particularly, every metrizable locally convex space) and its strong dual are quasi-(DF )-spaces. We prove that Cp(X) has a fundamental bounded resolution iff Cp(X) is a quasi-(DF )-space iff the strong dual of Cp(X) is a quasi-(DF )-space iff X is countable. If X is a metrizable space, then Ck(X) is a quasi-(DF )-space iff X is a Polish σ-compact space. We provide numerous concrete examples which in particular clarify differences between (DF )-spaces and quasi-(DF )-spaces. 1. Introduction An important class of locally convex spaces (lcs, for short), the class of (DF )-space, was intro- duced by Grothendieck in [20], we refer also to monographs [21] or [31] for more details. Definition 1.1. A locally convex space E is called a (DF )-space if (1) E has a fundamental sequence of bounded sets, and (2) E is ℵ0-quasibarrelled. -
Some Examples on Quasi-Barrelled Spaces Annales De L’Institut Fourier, Tome 22, No 2 (1972), P
ANNALES DE L’INSTITUT FOURIER MANUEL VALDIVIA Some examples on quasi-barrelled spaces Annales de l’institut Fourier, tome 22, no 2 (1972), p. 21-26 <http://www.numdam.org/item?id=AIF_1972__22_2_21_0> © Annales de l’institut Fourier, 1972, tous droits réservés. L’accès aux archives de la revue « Annales de l’institut Fourier » (http://annalif.ujf-grenoble.fr/) implique l’accord avec les conditions gé- nérales d’utilisation (http://www.numdam.org/conditions). Toute utilisa- tion commerciale ou impression systématique est constitutive d’une in- fraction pénale. Toute copie ou impression de ce fichier doit conte- nir la présente mention de copyright. Article numérisé dans le cadre du programme Numérisation de documents anciens mathématiques http://www.numdam.org/ Ann. Inst. Fourier, Grenoble 22, 2 (1972), 21-26. SOME EXAMPLES ON QUASI-BARRELLED SPACES Q by Manuel VALDIVIA J. Dieudonne has proved in [2] the following theorem: a) Let E be a bornological space. If F is a subspace of E, of finite codimension, then F is bornological. We have given in [6] and [7], respectively, the following results : b) Let E be a quasi-barrelled space. If ¥ is a subspace of E, of finite codimension, then F is quasi-barrelled. c) Let E be an ultrabornological space. If ¥ is a subspace of E, of infinite countable codimension, then ¥ is bornological. The results a), b) and c) lead to the question if the results a) and b) will be true in the case of being F a subspace of infinite countable codimension. In this paper we give an example of a bornological space E, which has a subspace F, of infinite countable codimension, such that F is not quasi-barrelled. -
Multi-Objective Branch-And-Bound. Application To
Multi-objective branch-and-bound. Application to the bi-objective spanning tree problem Francis Sourd, Olivier Spanjaard Laboratoire d’Informatique de Paris 6 (LIP6-UPMC), 4 Place Jussieu, F-75252 Paris Cedex 05, France, {[email protected]} This paper focuses on a multi-objective derivation of branch-and-bound procedures. Such a procedure aims to provide the set of Pareto optimal solutions of a multi-objective combina- torial optimization problem. Unlike previous works on this issue, the bounding is performed here via a set of points rather than a single ideal point. The main idea is that a node in the search tree can be discarded if one can define a separating hypersurface in the objective space between the set of feasible solutions in the subtree and the set of points corresponding to potential Pareto optimal solutions. Numerical experiments on the bi-objective spanning tree problem are provided that show the efficiency of the approach. Key words: multi-objective combinatorial optimization; branch-and-bound; bi-objective span- ning tree problem 1. Introduction Branch-and-bound methods (which belong to the class of implicit enumeration methods) have proved to perform well on many combinatorial optimization problems, provided good bounding functions are known. They have been designed under the assumption that the quality of a solution is evaluated by a single objective function on a totally ordered scale. However, many real world problems involve multiple, potentially conflicting, objectives. This has led practioners to investigate problems where each solution x in the set X of feasible solutions is evaluated by p objective functions f(x) = (f1(x), . -
Exploiting Regularities in Natural Acoustical Scenes for Monaural Audio Signal Estimation, Decomposition, Restoration and Modification
Exploiting regularities in natural acoustical scenes for monaural audio signal estimation, decomposition, restoration and modification 音環境に内在する規則性に基づくモノラル音響 信号の推定・分解・復元・加工に関する研究 { Exploitation de r´egularit´esdans les sc`enes acoustiques naturelles pour l'estimation, la d´ecomposition, la restauration et la modification de signaux audio monocanal Jonathan Le Roux ルルー ジョナトン THE UNIVERSITY OF TOKYO GRADUATE SCHOOL OF INFORMATION SCIENCE AND TECHNOLOGY DEPARTMENT OF INFORMATION PHYSICS AND COMPUTING 東京大学 大学院情報理工学系研究科 システム情報学専攻 Ph.D. Thesis 博士論文 submitted by Jonathan LE ROUX in partial fulfillment of the requirements for the degree of Doctor of Philosophy in Information Science and Technology Exploiting regularities in natural acoustical scenes for monaural audio signal estimation, decomposition, restoration and modification (音環境に内在する規則性に基づくモノラル音響 信号の推定・分解・復元・加工に関する研究) defended on January 29, 2009 in front of the committee composed of Shigeki SAGAYAMA University of Tokyo Thesis Supervisor Alain de CHEVEIGNE´ Ecole´ Normale Sup´erieure Co-supervisor Shigeru ANDO^ University of Tokyo Examiner Keikichi HIROSE University of Tokyo Examiner Nobutaka ONO University of Tokyo Examiner Susumu TACHI University of Tokyo Examiner UNIVERSITE´ PARIS VI { PIERRE ET MARIE CURIE ECOLE´ DOCTORALE EDITE THESE` DE DOCTORAT sp´ecialit´e INFORMATIQUE, TEL´ ECOMMUNICATIONS´ ET ELECTRONIQUE´ pr´esent´eepar Jonathan LE ROUX pour obtenir le grade de DOCTEUR de l'UNIVERSITE´ PARIS VI { PIERRE ET MARIE CURIE Exploitation de r´egularit´es dans les sc`enesacoustiques naturelles pour l'estimation, la d´ecomposition, la restauration et la modification de signaux audio monocanal (Exploiting regularities in natural acoustical scenes for monaural audio signal estimation, decomposition, restoration and modification) soutenue le 12 mars 2009 devant le jury compos´ede Alain de CHEVEIGNE´ Ecole´ Normale Sup´erieure Directeur de Th`ese Shigeki SAGAYAMA University of Tokyo Co-Directeur Dan P. -
Invariant Metrics on Convex Cones Annali Della Scuola Normale Superiore Di Pisa, Classe Di Scienze 4E Série, Tome 3, No 4 (1976), P
ANNALI DELLA SCUOLA NORMALE SUPERIORE DI PISA Classe di Scienze EDOARDO VESENTINI Invariant metrics on convex cones Annali della Scuola Normale Superiore di Pisa, Classe di Scienze 4e série, tome 3, no 4 (1976), p. 671-696 <http://www.numdam.org/item?id=ASNSP_1976_4_3_4_671_0> © Scuola Normale Superiore, Pisa, 1976, tous droits réservés. L’accès aux archives de la revue « Annali della Scuola Normale Superiore di Pisa, Classe di Scienze » (http://www.sns.it/it/edizioni/riviste/annaliscienze/) implique l’accord avec les conditions générales d’utilisation (http://www.numdam.org/conditions). Toute utilisa- tion commerciale ou impression systématique est constitutive d’une infraction pénale. Toute copie ou impression de ce fichier doit contenir la présente mention de copyright. Article numérisé dans le cadre du programme Numérisation de documents anciens mathématiques http://www.numdam.org/ Invariant Metrics on Convex Cones (*). EDOARDO VESENTINI (**) dedicated to Jean Leray Let 3t be a locally convex real vector space and let S~ be an open convex cone in JI containing no non-trivial affine subspace of Jt. In the case in which has finite dimension, an affine-invariant riemannian metric has been introduced in S~ by E. B. Vinberg [16], following closely a similar construction developed earlier by M. Koecher ([11]; cf. also [14]) for the domains of positivity. The invariance of this metric under the action of the group of affine automorphisms of SZ, coupled with a classical lemma of van Dantzig and van der Waerden, implies that acts properly on S~. Furthermore, if S~ is affine-homogeneous, this invariant riemannian metric on S~ is necessarily complete [10, p. -
Structured Near-Optimal Channel- Adapted Quantum Error Correction
Structured near-optimal channel- adapted quantum error correction The MIT Faculty has made this article openly available. Please share how this access benefits you. Your story matters. Citation Fletcher, Andrew, Peter Shor, and Moe Win. “Structured near- optimal channel-adapted quantum error correction.” Physical Review A 77.1 012320 (2008) [16 pages]. © 2008 The American Physical Society. As Published http://dx.doi.org/10.1103/PhysRevA.77.012320 Publisher American Physical Society Version Final published version Citable link http://hdl.handle.net/1721.1/67444 Terms of Use Article is made available in accordance with the publisher's policy and may be subject to US copyright law. Please refer to the publisher's site for terms of use. PHYSICAL REVIEW A 77, 012320 ͑2008͒ Structured near-optimal channel-adapted quantum error correction Andrew S. Fletcher,1,2,* Peter W. Shor,3,† and Moe Z. Win1,‡ 1Laboratory for Information and Decision Systems, Massachusetts Institute of Technology, 77 Massachusetts Avenue, Cambridge, Massuchesetts 02139, USA 2MIT Lincoln Laboratory, 244 Wood Sreet, Lexington, Massachusetts 02420, USA 3Department of Mathematics, Massachusetts Institute of Technology, 77 Massachusetts Avenue, Cambridge, Massachusetts 02139, USA ͑Received 28 August 2007; published 17 January 2008͒ We present a class of numerical algorithms which adapt a quantum error correction scheme to a channel model. Given an encoding and a channel model, it was previously shown that the quantum operation that maximizes the average entanglement fidelity may be calculated by a semidefinite program ͑SDP͒, which is a convex optimization. While optimal, this recovery operation is computationally difficult for long codes. Fur- thermore, the optimal recovery operation has no structure beyond the completely positive trace-preserving constraint. -
On Weighted Spaces Without a Fundamental Sequence of Bounded Sets
IJMMS 30:8 (2002) 449–457 PII. S0161171202011857 http://ijmms.hindawi.com © Hindawi Publishing Corp. ON WEIGHTED SPACES WITHOUT A FUNDAMENTAL SEQUENCE OF BOUNDED SETS J. O. OLALERU Received 5 February 2001 and in revised form 21 September 2001 The problem of countably quasi-barrelledness of weighted spaces of continuous functions, of which there are no results in the general setting of weighted spaces, is tackled in this paper. This leads to the study of quasi-barrelledness of weighted spaces in which, unlike that of Ernst and Schnettler (1986), though with a similar approach, we drop the assump- tion that the weighted space has a fundamental sequence of bounded sets. The study of countably quasi-barrelledness of weighted spaces naturally leads to definite results on the weighted (DF)-spaces for those weighted spaces with a fundamental sequence of bounded sets. 2000 Mathematics Subject Classification: 46A08, 46E30. 1. Introduction and notations. The countably barrelledness, countably quasi-bar- relledness, barrelledness, and quasi-barrelleness of the space C(X) of continuous functions on a completely regular Hausdorff space X equipped with the compact open topology (c-op), including when it is a (DF)-space and (gDF)-space, is well known (cf. [7, 13]). In the more general setting of weighted spaces, Ernst and Schnettler [3] studied the (gDF) and the quasi-barrelledness of weighted spaces by constructing a Nachbin family on X which is based on the assumption that the weighted space has a fun- damental sequence of bounded sets. A weighted space need not have a fundamental system of bounded sets. There are classical examples of such spaces, for example, let X be a noncompact locally compact and σ -compact space, and let C(X) be the space of all continuous real-valued functions on X equipped with the compact-open topology. -
SEMICONVEX SPACES by S
SEMICONVEX SPACES by S. O. IYAHEN (Received 24 June, 1967) 1. Introduction. Many of the techniques and notions used to study various important theorems in locally convex spaces are not effective for general linear topological spaces. In [4], a study is made of notions in general linear topological spaces which can be used to replace barrelled, bornological, and quasi-barrelled spaces. The present paper contains a parallel study in the context of semiconvex spaces. In section 2, we look briefly and generally at semiconvex spaces, and answer a question of S. Simons [11, p. 180]. We then define the notion of an jc-inductive limit of semiconvex spaces —a concept which plays much the same part in the theory of semiconvex spaces as an inductive limit does for locally convex spaces. In section 3, we study hyperbarrelled, hyperbornological and quasi-hyperbarrelled spaces. These respectively replace barrelled, bornological and quasi-barrelled spaces when semiconvex spaces are being considered. The K-hyperbarrelled and N-quasi-hyperbarrelled spaces introduced in section 4 are slight generalizations of what replace countably barrelled and countably quasi-barrelled spaces in a similar situation. Throughout, we shall use the terminology and notation of [4]. The author wishes to thank Professor A. P. Robertson for his help and encouragement. He is grateful to the Government of the Republic of Nigeria for financial support. 2. Semiconvex spaces. Let E be a linear space. If A is a non-negative real number, a subset A of E is called ^.-convex if A + A £ XA. A subset B of E is called a semiconvex subset if it is /i-convex for some n ^ 0.