New Horizons for Processing and Utilizing Red Mud
Total Page:16
File Type:pdf, Size:1020Kb
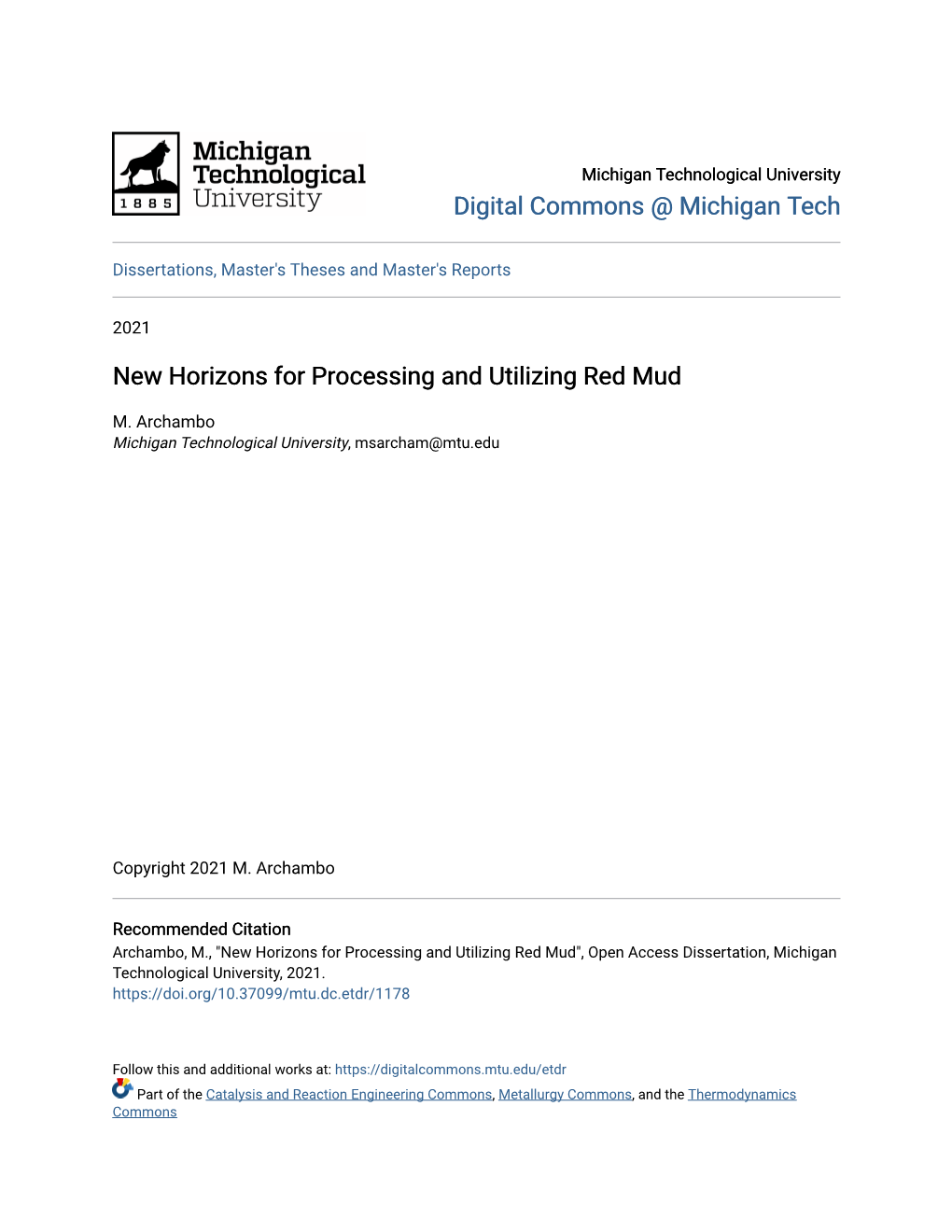
Load more
Recommended publications
-
Eparation of the Purest Aluminum Chemicals
III. MINERAL COMMODITIES A. INDIVIDUAL MINERAL COMMODITY REVIEWS ALUMINA & ALUMINUM A. Commodity Summary Aluminum, the third most abundant element in the earth's crust, is usually combined with silicon and oxygen in rock. Rock that contains high concentrations of aluminum hydroxide minerals is called bauxite. Although bauxite, with rare exceptions, is the starting material for the production of aluminum, the industry generally refers to metallurgical grade alumina extracted from bauxite by the Bayer Process, as the ore. Aluminum is obtained by electrolysis of this purified ore.1 The United States is entirely dependent on foreign sources for metallurgical grade bauxite. Bauxite imports are shipped to domestic alumina plants, which produce smelter grade alumina for the primary metal industry. These alumina refineries are in Louisiana, Texas, and the U.S. Virgin Islands.2 The United States must also import alumina to supplement this domestic production. Approximately 95 percent of the total bauxite consumed in the United States during 1994 was for the production of alumina. Primary aluminum smelters received 88 percent of the alumina supply. Fifteen companies operate 23 primary aluminum reduction plants. In 1994, Montana, Oregon, and Washington accounted for 35 percent of the production; Kentucky, North Carolina, South Carolina, and Tennessee combined to account for 20 percent; other states accounted for the remaining 45 percent. The United States is the world’s leading producer and the leading consumer of primary aluminum metal. Domestic consumption in 1994 was as follows: packaging, 30 percent; transportation, 26 percent; building, 17 percent; electrical, 9 percent; consumer durables, 8 percent; and other miscellaneous uses, 10 percent. -
Study on New Desilication Technology of High Silica Bauxite
2016 2nd International Conference on Sustainable Energy and Environmental Engineering (SEEE 2016) ISBN: 978-1-60595-408-0 Study on New Desilication Technology of High Silica Bauxite Hai-yun XIE 1, Chao DING 1, Peng-fei ZHANG 1,2 , Lu-zheng CHEN 1, and Xiong-TONG 1 1Faculty of Land Resource Engineering, Kunming University of Science and Technology, Kunming 650093, China 2State Key Laboratory of Complex Nonferrous Metal Resource Clean Utilization, Kunming 650093, China Keywords: High silicon bauxite, Desilication, Gravity separation, Froth flotation. Abstract: There are abundant diasporic bauxite resource in China. The gravity separation and flotation process are utilized for treating this kind of ore. When the ore grinding fineness is -200 mesh 80%, the qualified bauxite concentrate can be obtained, and it contains Al 2O3 71.62%, SiO 2 8.94%, and its Al 2O3 recovery rate is 75.43%, A/S is 8.02.Compared with single flotation process, it can be reduced for the dosage flotation reagent and the cost of mineral processing. Introduction China's bauxite resources are rich, the amount of resources of 1.914 billion, ranking the fifth in the world, but more than 80% are medium and low grade ore, Aluminum silicon ratio (A/S) between 4 to 7 of the bauxite accounted for 59.5%. These minerals can not meet the basic conditions for the production of alumina by Bayer process. (A/S>8) [1]. The vast majority of China's bauxite belong to high-alumina, high-silicon, fine-grained embedded diaspore-type bauxite, so the bauxite is difficult to concentrate. -
Preliminary Estimates of the Quantities of Rare-Earth Elements Contained in Selected Products and in Imports of Semimanufactured Products to the United States, 2010
Preliminary Estimates of the Quantities of Rare-Earth Elements Contained in Selected Products and in Imports of Semimanufactured Products to the United States, 2010 By Donald I. Bleiwas and Joseph Gambogi Open-File Report 2013–1072 U.S. Department of the Interior U.S. Geological Survey U.S. Department of the Interior KEN SALAZAR, Secretary U.S. Geological Survey Suzette M. Kimball, Acting Director U.S. Geological Survey, Reston, Virginia: 2013 For more information on the USGS—the Federal source for science about the Earth, its natural and living resources, natural hazards, and the environment—visit http://www.usgs.gov or call 1–888–ASK–USGS For an overview of USGS information products, including maps, imagery, and publications, visit http://www.usgs.gov/pubprod To order other USGS information products, visit http://store.usgs.gov Suggested citation: Bleiwas, D.I., and Gambogi, Joseph, 2013, Preliminary estimates of the quantities of rare-earth elements contained in selected products and in imports of semimanufactured products to the United States, 2010: U.S. Geological Survey Open–File Report 2013–1072, 14 p., http://pubs.usgs.gov/of/2013/1072/. Any use of trade, firm, or product names is for descriptive purposes only and does not imply endorsement by the U.S. Government. Although this information product, for the most part, is in the public domain, it also may contain copyrighted materials as noted in the text. Permission to reproduce copyrighted items must be secured from the copyright owner. Cover. Left: Aerial photograph of Molycorp, Inc.’s Mountain Pass rare-earth oxide mining and processing facilities in Mountain Pass, California. -
Transmittal of Draft EIR for Molycorp Mountain Pass Mine Expansion, for Review and Comment
COUNTY OF SAN BERNARDINO PLANNING DEPARTMENT I,regular-! I PUBLIC WORKS GROUP -- W&- Sw1. NENNO lorth Arrowhead Avenue * San Bernardino, CA 924154182 * (909) 3874131 VALERY PILMER Director of Planning December 9, 1996No. 909) 3873223 IY RESPONSIBLE AND TRUSTEE AGENCIES INTERESTED ORGANIZATIONS AND INDIVIDUALS RE: NOTICE OF AVAILABILITY FOR THE DRAFT EIR ON THE MOLYCORP MOUNTAIN PASS MINE EXPANSION Dear Reader/Reviewer: Enclosed for your review and comment is the Draft EIR for the Molycorp Mountain Pass Mine Expansion. The purpose of the document is to identify and describe the probable environmental impacts that would result from the proposed expansion of Molycorp's existing mine and processing plant complex located at Mountain Pass, California. Mountain Pass is within the unincorporated portion San Bernardino County along Interstate 15 approximately 30 miles northeast of Baker and approximately 14 miles southwest of the Nevada stateline. The proposed quarry and waste rock areas would add 696 acres of disturbance to the existing mine site, resulting in a total disturbed area of approximately 1,044 acres. sag_> This document has been prepared to meet the State requirements of the California Environmental Quality Act. The Draft EIR has been prepared under the supervision of the County of San Bernardino Planning Department. The public comment period will end on January 27, 1997. Written comments should be addressed to: County of San Bemnardino- Planning Dgparnn 385 N. Arrowhead Avenue, Third Floor San Bernardino, CA 92415-0182 Attn: Randy Scott Sincerely, Randy Scottjlanning Manager, San Berardo County Planning Department ~-! - nLA ,;;K Scr.'Eperviscs .,* 1:,. 3 - -, I- . 1 12 4~ ..!A','V34-' TUrCCI Vi~i D;s~ri:n, BARBA~RA CPANM FURtOPAN . -
Producers Case Study the Changing
Producers Case Study The Changing Geography of Rare Earth Element Production Introduction The locations where rare earth elements are produced changed repeatedly throughout the 1900s and early 2000s. This variation suggests that production is not determined primarily by the geographic location of rare earth ores. Instead, the location of mines and separation plants is driven by a combination of market prices, government policies, and the actions of producers and manufacturers. As a result where and how rare earth elements are produced could change in the future. Initial Rare Earth Metal Production Although a mineral containing rare earth elements was identified in Sweden in 1788, it took more than 100 years for the first significant industrial product to be made using the rare earths. In the 1890s chemist Carl Auer von Welsbach developed a mantle made of a mixture of 99% thorium and 1% cerium for use with gas streetlights. More than five billion mantles were sold worldwide through the 1930s. Welsbach also developed mischmetal, a mixture of rare earth elements cerium, lanthanum, neodymium, and praseodymium. When alloyed with iron, mischmetal produced a metal that sparked when struck. It was widely used in pocket cigarette lighters as well as automobile ignition switches. The Welsbach Company mined rare earth deposits located in coastal sands in Brazil, India, and North Carolina. India’s coastal sands are also rich in the radioactive element thorium, which is not a rare earth element. India banned the export of these sands in 1948 to preserve its thorium supply for a potential nuclear energy program. At that time the price of rare earth metals spiked until newly established mining locations briefly made South Africa the world’s leading exporter of rare earth ores in the 1950s. -
Digital Dystopia: Player Control and Strategic Innovation in the Sims Online
Chapter 12 DIGITAL DYSTOPIA: PLAYER CONTROL AND STRATEGIC INNOVATION IN THE SIMS ONLINE Francis F. Steen, Mari Siˆan Davies, Brendesha Tynes, and Patricia M. Greenfield 1. Introduction Around New Year 2004, a quiet year after the official launch, The Sims Online hit the global headlines. Disappointingly, the topic was not a celebration of how this “new virtual frontier,” this “daring collective social experiment,” had succeeded in bringing “our divided nation” together, as Time magazine had blithely prophesied [1]. Instead, the media reported that the online game had turned into a Biblical den of iniquity, a Sin City, a virtual Gomorrah—and that the whistleblower who bore witness to this had his account terminated [2–5]. Rivaling mafia organizations were practicing extortion and intimidation, pimps running brothels where underage girls provided sex for money, and con artists scamming newbies out of their start capital. Maxis, the company that designed and operated the game, maintained a relaxed laissez-fair policy of light and somewhat haphazard intervention. The first mafias and in-game brothels had been established already in the early days of beta-testing; they continued to operate unchecked. Pretend crime paid well and recruitment was good, leading to a rapidly mutating series of inventive scams targeting the inexperienced and the unwary. It wasn’t meant to be like this. Gordon Walton, one of the chief designers, had spoken in glowing terms of the game’s potential to provide opportunities for better relations between people. While “all of our mass media positions us to believe our neighbors are psychopaths, cheating husbands, and just bad people,” The Sims Online would short circuit our distrustful negative stereotypes [6]. -
Critical Materials and US Import Reliance
Testimony Critical Materials and U.S. Import Reliance Recent Developments and Recommended Actions Richard Silberglitt CT-485 Testimony presented before House Natural Resources Committee, Subcommittee on Energy and Mineral Resources on December 12, 2017. For more information on this publication, visit www.rand.org/pubs/testimonies/CT485.html Testimonies RAND testimonies record testimony presented or submitted by RAND associates to federal, state, or local legislative committees; government-appointed commissions and panels; and private review and oversight bodies. Published by the RAND Corporation, Santa Monica, Calif. © Copyright 2017 RAND Corporation is a registered trademark. Limited Print and Electronic Distribution Rights This document and trademark(s) contained herein are protected by law. This representation of RAND intellectual property is provided for noncommercial use only. Unauthorized posting of this publication online is prohibited. Permission is given to duplicate this document for personal use only, as long as it is unaltered and complete. Permission is required from RAND to reproduce, or reuse in another form, any of its research documents for commercial use. For information on reprint and linking permissions, please visit www.rand.org/pubs/permissions.html. www.rand.org Critical Materials and U.S. Import Reliance: Recent Developments and Recommended Actions Testimony of Richard Silberglitt1 The RAND Corporation2 Before the Committee on Natural Resources Subcommittee on Energy and Mineral Resources United States House of Representatives December 12, 2017 hank you Chairman Gosar, Ranking Member Lowenthal, and distinguished members of the Subcommittee for inviting me to testify today. My testimony is based on the results of a 2013 study conducted by the RAND Corporation at the request of the National T 3 Intelligence Council, taking into account relevant developments and data since the publication of that report. -
Bojin-Diss-Library Copy
Exploring the Notion of ‘Grinding’ in Massively Multiplayer Online Role Playing Gamer Discourse: The Case of Guild Wars by Nis Bojin M.A. (Communication & Culture), York University, 2005 B.A. (Psychology/Classical Studies Double Major), York University, 2000 Dissertation Submitted In Partial Fulfillment of the Requirements for the Degree of Doctor of Philosophy In the School of Interactive Arts and Technology Faculty of Communication, Art and Technology © Nis Bojin 2013 SIMON FRASER UNIVERSITY Summer 2013 Approval Name: Nis Bojin Degree: Doctor of Philosophy Title of Thesis: Exploring the Notion of ‘Grinding’ in Massively Multiplayer Online Role Player Gamer Discourse Examining Committee: Chair: Halil Erhan Assistant Professor (SFU-SIAT) John Bowes Senior Supervisor Professor, Program Director (SFU- SIAT) Suzanne de Castell Co-Supervisor Professor (University of Ontario Institute of Technology) Jim Bizzocchi Supervisor Associate Professor (SFU-SIAT) Carman Neustaedter Internal Examiner Assistant Professor (SFU-SIAT) Sean Gouglas External Examiner Associate Professor, Department of Anthropology (University of Alberta) Date Defended/Approved: May 29, 2013 ii Partial Copyright License iii Ethics Statement The author, whose name appears on the title page of this work, has obtained, for the research described in this work, either: a. human research ethics approval from the Simon Fraser University Office of Research Ethics, or b. advance approval of the animal care protocol from the University Animal Care Committee of Simon Fraser University; or has conducted the research c. as a co-investigator, collaborator or research assistant in a research project approved in advance, or d. as a member of a course approved in advance for minimal risk human research, by the Office of Research Ethics. -
FOILING the ALUMINUM INDUSTRY: a TOOLKIT for COMMUNITIES, ACTIVISTS, CONSUMERS, and WORKERS by International Rivers Network FOILING the ALUMINUM INDUSTRY
FOILING THE ALUMINUM INDUSTRY: A TOOLKIT FOR COMMUNITIES, ACTIVISTS, CONSUMERS, AND WORKERS by International Rivers Network FOILING THE ALUMINUM INDUSTRY: A TOOLKIT FOR COMMUNITIES, ACTIVISTS, CONSUMERS, AND WORKERS By Glenn Switkes Published by International Rivers Network, August 2005 Copyright © 2005 International Rivers Network 1847 Berkeley Way Berkeley, CA 94703 USA IRN gratefully acknowledges the support of The Overbrook Foundation, whose funding made this toolkit possible. Design by: Design Action Collective Graphic chart: Soft Horizons & Chartbot Foiling the Aluminum Industry Table of Contents INTRODUCTION ............................................................................................................1 THE ALUMINUM INDUSTRY TODAY AND TOMORROW ................................................................3 FIRST STEP : ..............................................................................................................5 Stripping forests for bauxite ................................................................................5 Stripping the Amazon ..........................................................................................6 Bauxite mining brings violence against indigenous people ......................................8 SECOND STEP : ............................................................................................................9 Alumina refining—white powder and red mud ........................................................9 Jamaicans demand to know whether their water supplies -
Games and Culture
Games and Culture http://gac.sagepub.com/ Building an MMO With Mass Appeal : A Look at Gameplay in World of Warcraft Nicolas Ducheneaut, Nick Yee, Eric Nickell and Robert J. Moore Games and Culture 2006 1: 281 DOI: 10.1177/1555412006292613 The online version of this article can be found at: http://gac.sagepub.com/content/1/4/281 Published by: http://www.sagepublications.com Additional services and information for Games and Culture can be found at: Email Alerts: http://gac.sagepub.com/cgi/alerts Subscriptions: http://gac.sagepub.com/subscriptions Reprints: http://www.sagepub.com/journalsReprints.nav Permissions: http://www.sagepub.com/journalsPermissions.nav Citations: http://gac.sagepub.com/content/1/4/281.refs.html >> Version of Record - Sep 12, 2006 What is This? Downloaded from gac.sagepub.com at UNIV OF FLORIDA Smathers Libraries on March 29, 2013 Games and Culture Volume 1 Number 4 October 2006 281-317 © 2006 Sage Publications Building an MMO 10.1177/1555412006292613 http://gac.sagepub.com hosted at With Mass Appeal http://online.sagepub.com A Look at Gameplay in World of Warcraft Nicolas Ducheneaut Nick Yee Eric Nickell Robert J. Moore Palo Alto Research Center World of Warcraft (WoW) is one of the most popular massively multiplayer games (MMOs) to date, with more than 6 million subscribers worldwide. This article uses data collected over 8 months with automated “bots” to explore how WoW functions as a game. The focus is on metrics reflecting a player’s gaming experience: how long they play, the classes and races they prefer, and so on. -
Proposal for a Content Analysis of Equity Versus Efficiency In
DISSERTATION HUMAN-TECHNOLOGY RELATIONALITY AND SELF-NETWORK ORGANIZATION: PLAYERS AND AVATARS IN WORLD OF WARCRAFT Submitted by Jaime Banks Department of Journalism and Technical Communication In partial fulfillment of the requirements For the Degree of Doctor of Philosophy Colorado State University Fort Collins, Colorado Fall 2013 Doctoral Committee: Advisor: Rosa Mikeal Martey Donna Rouner Joseph Champ Eric Aoki James Folkestad Copyright by Jaime Banks 2013 All Rights Reserved ABSTRACT HUMAN-TECHNOLOGY RELATIONALITY AND SELF-NETWORK ORGANIZATION: PLAYERS AND AVATARS IN WORLD OF WARCRAFT Massively multiplayer online roleplaying games, or MMOs, present an increasingly popular digital media experience whereby identity emerges as players contribute materially to play but contributions are governed by affordances and constraints of the game. Unique to this medium is the player’s ability to create and control a digital body – an avatar – to represent the Self in the immersive gameworld. Although notions of identity and the Self in digital games have been examined through a number of approaches, it is still unclear how the way one sees the avatar in the uncanny situation of having two bodies – one digital, one physical – contributes to a sense of Self in and around these games. Further, it is unclear how non-human objects contribute to human senses of Self. In that vein, this study examines two research questions: How do players have relationships with their avatars in a digital game? And how does the Self emerge in relation to those relationships? Toward understanding how nonhumans play a role in the emergence of the Self, this study approaches these questions from an actor-network perspective, examining how human, nonhuman, material, and semiotic objects exist in complex webs of relations and how those relations give rise to particular senses of Self in relation to particular gameplay situations. -
Massive Multi-Player Online Games and the Developing Political Economy of Cyberspace
Fast Capitalism ISSN 1930-014X Volume 4 • Issue 1 • 2008 doi:10.32855/fcapital.200801.010 Massive Multi-player Online Games and the Developing Political Economy of Cyberspace Mike Kent This article explores economics, production and wealth in massive multi-player online games. It examines how the unique text of each of these virtual worlds is the product of collaboration between the designers of the worlds and the players who participate in them. It then turns its focus to how this collaborative construction creates tension when the ownership of virtual property is contested, as these seemingly contained virtual economies interface with the global economy. While these debates occur at the core of this virtual economy, at the periphery cheap labor from less-developed economies in the analogue world are being employed to ‘play’ these games in order to ‘mine’ virtual goods for resale to players from more wealthy countries. The efforts of the owners of these games, to curtail this extra-world trading, may have inadvertently driven the further development of this industry towards larger organizations rather than small traders, further cementing this new division of labor. Background In the late 1980s, multi-user dungeons (MUDs) such as LambdaMOO were text-based environments. These computer-mediated online spaces drew considerable academic interest.[1] The more recent online interactive worlds are considerably more complex, thanks to advances in computing power and bandwidth. Encompassing larger and more detailed worlds, they also enclose a much larger population of players. The first game in the new category of Massively Multi-player Online Role-playing Games (known initially by the acronym MMORPG and more recently as MMOG) was Ultima Online http://www.uo.com, which was launched over a decade ago in September 1997.