An Overview of Flux Pumps for HTS Coils T
Total Page:16
File Type:pdf, Size:1020Kb
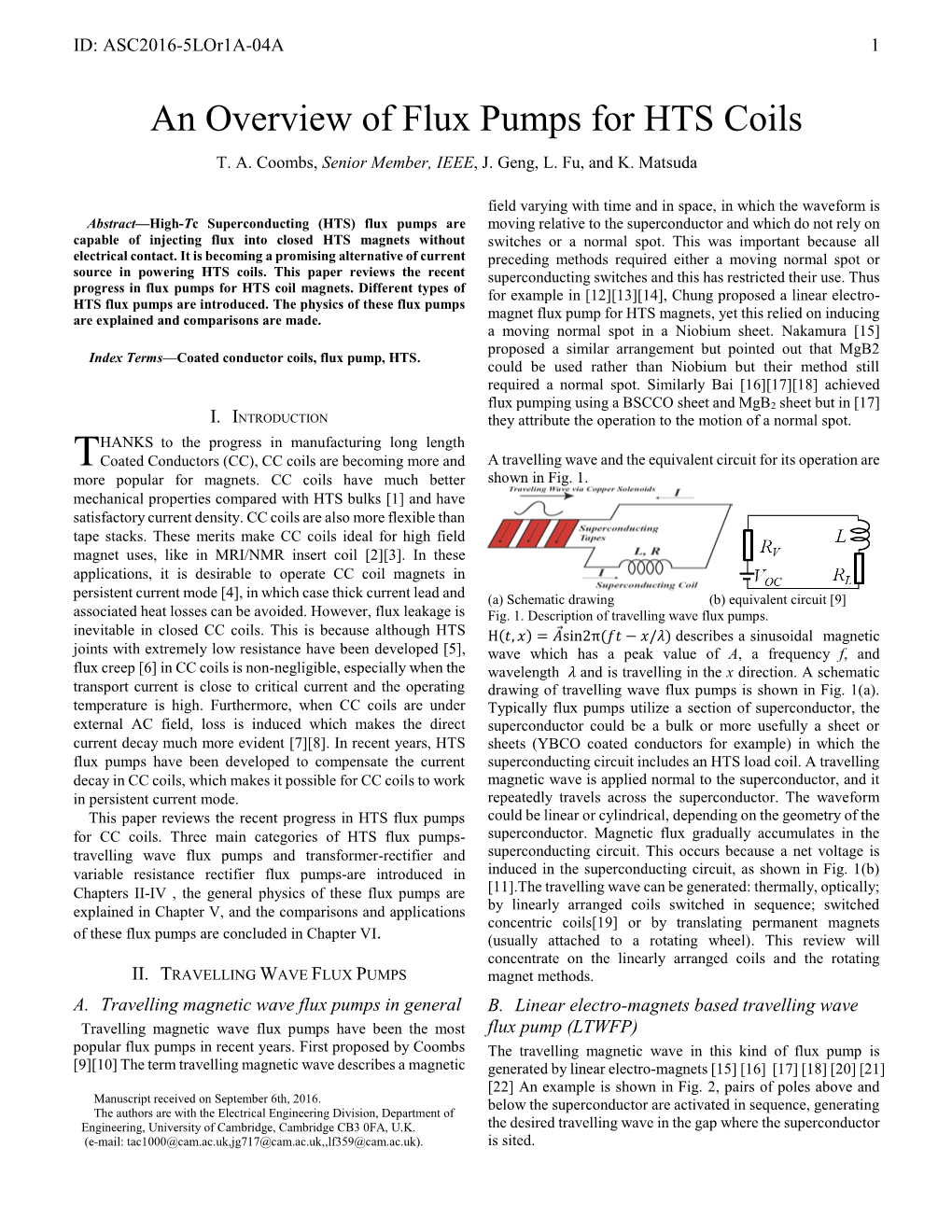
Load more
Recommended publications
-
Magnetic Flux Pumping in Superconducting Loop Containing a Josephson Ψ Junction S
Magnetic Flux Pumping in Superconducting Loop Containing a Josephson Junction S. Mironov,1 H. Meng,2, 3, 4 and A. Buzdin2, 5 1)Institute for Physics of Microstructures, Russian Academy of Sciences, GSP-105, 603950 Nizhny Novgorod, Russia 2)University Bordeaux, LOMA UMR-CNRS 5798, F-33405 Talence Cedex, France 3)School of Physics and Telecommunication Engineering, Shaanxi University of Technology, Hanzhong 723001, China 4)Shanghai Key Laboratory of High Temperature Superconductors, Shanghai University, Shanghai 200444, China 5)Sechenov First Moscow State Medical University, Moscow, 119991, Russia We demonstrate that a Josephson junction with a half-metallic weak link integrated into the superconducting loop enables the pumping of magnetic flux piercing the loop. In such junctions the ground state phase is determined by the mutual orientation of magnetic moments in two ferromagnets surrounding the half-metal. Thus, the precession of magnetic moment in one of two ferromagnets controlled, e.g., by the microwave radiation, results in the accumulation of the phase and subsequent switching between the states with different vorticities. The proposed flux pumping mechanism does not require the application of voltage or external magnetic field which enables the design of electrically decoupled memory cells in superconducting spintronics. When a superconducting loop is put in the external magnetic field the magnetic flux Φ through the loop is B~ quantized being equal to the integer number of the flux 1 quanta Φ0: Φ = nΦ0 . The interplay between the states with different vorticities n enables the implementation of multiply connected superconducting systems as flux qubits2,3, ultra-sensitive magnetic field detectors4,5, gen- erators of ac radiation6 etc. -
Design and Characterization of a LTS Flux Pump System for Possible
University of Groningen Bachelor Thesis in Physics Research performed at SRON Design and characterization of a LTS flux pump system for possible satellite application Supervisor: Author: dr. ir. G. de Lange (SRON) Laurens Even prof. dr. ir. R.A. Hoekstra (RUG) prof. dr. T. Banerjee (RUG) July 8, 2016 [email protected] student number 2315963 Abstract In this bachelor project research is performed on the design of a prototype low temperature superconducting (LTS) flux pump system. With such a system a superconducting electromagnet can be charged to high currents, while only a low current power supply and cryogenic wiring is necessary. The flux pump could find potential as an application in the SAFARI instrument for the SPICA satellite, but it can also be used for cryogenic energy storage or for offsetting a magnetic field. As a satellite application the flux pump can reduce parasitic heat load on the cold stages of the satellite. Within this thesis we continued the work on an existing flux pump design from a previous bachelor project. This design had previously shown some essential performance characteristics of a flux pump system, but the actual flux pumping was not observed. In this thesis work we investigated the possible causes of this and implemented improvements. These improvements have resulted in a working flux pump system. The main improvement (which was found in a late stage of the project) was the correction of the winding orientation of a secondary coil in the transformer. Other improvements are: (1) the optimization of the transformer cooling, such that higher critical currents in the primary transformer superconducting wire could be achieved, and (2) the increase of the self-inductance of the primary coil of the transformer by replacing the original aluminum transformer core (that will induce eddy currents) by a Vespel polyamide core. -
Flux Pumping Simulation
HTS Thin Films for Flux Pumping James Gawith Boyang Shen, Jun Ma, Chao Li, Yavuz Ozturk, Tim Coombs University of Cambridge Electrical Power and Energy Conversion Group Contents • Flux pump background • SPICE simulations • HTS thin film AC field switch • Thin film flux pump initial results • Proposed future designs James Gawith Flux Pumps – Superconducting Rectifiers • Wireless (inductive) power supply for superconducting magnets • Provides thermal, mechanical, electrical isolation of magnet • No high-current DC supply or current leads required University of Cambridge/NHMFL University of Cambridge Application: High Field Magnets Application: Compact MRI James Gawith SPICE Simulation • Standard for simulating SMPS • Verified with prototypes • Useful for design and analysis James Gawith Key Findings from Simulation • Superconducting transformer • Power density proportional to operating frequency • Superconducting switches • Operation frequency is limited by on/off switching time • Majority of power loss depends on switch off-state resistance • Maximum pump current limited by switch IC James Gawith AC Field Switch AC Field Switch Developed by Geng [2] ퟒ풂푳풇 푹풅⊥ = 푩풂,⊥ − 푩풕풉,⊥ 푰풄ퟎ (for Ba,⊥ >> Bth,⊥) • Off-state resistance only ≈ 0.2mΩ • Increase frequency and field • Better electromagnets • Use suitable superconductors [2] J. Geng et al., “HTS Persistent Current Switch Controlled by AC Magnetic Field,” IEEE Trans. Appl. Supercond., vol. 26, no. 3, pp. 1–4, Apr. 2016 James Gawith Improved AC Field Switch – Conductor Layer Resistance per meter (Ω) 40μm Copper Stabilizer 0.015 at 77 K 3.8 μm Ag layer at 77 K 0.3 50 μm Hastelloy at 77 K 7.5 Dynamic Resistance of YBCO layer at 100 mT, 1 1.5 kHz Dynamic resistance of ‘2G HTS Wire’. -
Transconductance Quantization in a Topological Josephson Tunnel Junction Circuit
Transconductance quantization in a topological Josephson tunnel junction circuit L. Peyruchat,1 J. Griesmar,1, 2 J.-D. Pillet,1, 3 and Ç. Ö. Girit1, ∗ 1 Φ0, JEIP, USR 3573 CNRS, Collège de France, PSL University, 11, place Marcelin Berthelot, 75231 Paris Cedex 05, France 2Institut Quantique et Département GEGI, Université de Sherbrooke, Sherbrooke, QC, Canada 3LSI, CEA/DRF/IRAMIS, Ecole Polytechnique, CNRS, Institut Polytechnique de Paris, F-91128 Palaiseau, France (Dated: September 8, 2020) arXiv:2009.03291v1 [cond-mat.mes-hall] 7 Sep 2020 1 Abstract Superconducting circuits incorporating Josephson tunnel junctions are widely used for funda- mental research as well as for applications in fields such as quantum information and magnetometry. The quantum coherent nature of Josephson junctions makes them especially suitable for metrology applications. Josephson junctions suffice to form two sides of the quantum metrology triangle, relating frequency to either voltage or current, but not its base, which directly links voltage to current. We propose a five Josephson tunnel junction circuit in which simultaneous pumping of 2 flux and charge results in quantized transconductance in units 4e /h = 2e/Φ0, the ratio between the Cooper pair charge and the flux quantum. The Josephson quantized Hall conductance device (JHD) is explained in terms of intertwined Cooper pair pumps driven by the AC Josephson effect. We discuss the experimental implementation as well as optimal configuration of external param- eters and possible sources of error. JHD has a rich topological structure and demonstrates that Josephson tunnel junctions are universal, capable of interrelating frequency, voltage, and current via fundamental constants. Among quantum coherent electronic components the most prominent are Josephson junc- tions and quantum Hall systems. -
C 2016 by Ponnuraj Krishnakumar. All Rights Reserved. CHERN-SIMONS THEORY of MAGNETIZATION PLATEAUS on the KAGOME LATTICE
c 2016 by Ponnuraj Krishnakumar. All rights reserved. CHERN-SIMONS THEORY OF MAGNETIZATION PLATEAUS ON THE KAGOME LATTICE BY PONNURAJ KRISHNAKUMAR DISSERTATION Submitted in partial fulfillment of the requirements for the degree of Doctor of Philosophy in Physics in the Graduate College of the University of Illinois at Urbana-Champaign, 2016 Urbana, Illinois Doctoral Committee: Professor Mike Stone, Chair Professor Eduardo Fradkin, Director of Research Assistant Professor Gregory MacDougall Professor John Stack Abstract Frustrated spin systems on Kagome lattices have long been considered to be a promising candidate for realizing exotic spin liquid phases. Recently, there has been a lot of renewed interest in these systems with the discovery of experimental materials such as Volborthite and Herbertsmithite that have Kagome like structures. In this thesis I will focus on studying frustrated spin systems on the Kagome lattice using a spin-1/2 antiferromagnetic XXZ Heisenberg model in the presence of an external magnetic field as well as other perturbations. Such a system is expected to give rise to magnetization platueaus which can exhibit topological characteristics in certain regimes. We will first develop a flux-attachment transformation that maps the Heisenberg spins (hard-core bosons) onto a problem of fermions coupled to a Chern-Simons gauge field. This mapping relies on being able to define a consistent Chern-Simons term on the lattice. Using this newly developed mapping we analyse the phases/magnetization plateaus that arise at the mean-field level and also consider the effects of adding fluctuations to various mean-field states. Along the way, we show how to discretize an abelian Chern-Simons gauge theory on generic 2D planar lattices that satisfy certain conditions. -
A Kilo-Ampere Level HTS Flux Pump
A kilo-Ampere level HTS flux pump Jianzhao Geng1, a), Tom Painter 2), Peter Long 1), Jamie Gawith 1), Jiabin Yang 1), Jun Ma 1), Qihuan Dong1), Boyang Shen1), Chao Li 1), and T. A. Coombs 1,a) 1) Department of Engineering, University of Cambridge, Cambridge, CB3 0FA, United Kingdom 2) National High Magnetic Field Lab, Tallahassee, FL 32310, USA a) Email: [email protected], [email protected] Abstract This paper reports a newly developed high current transformer-rectifier High-Tc Superconducting (HTS) flux pump switched by dynamic resistance. A quasi-persistent current of over 1.1 kA has been achieved at 77 K using the device, which is the highest reported operating current by any HTS flux pumps to date. The size of the device is much smaller than traditional current leads and power supplies at the same current level. Parallel YBCO coated conductors are used in the transformer secondary winding as well as in the superconducting load coil to achieve high current. The output current is limited by the critical current of the load rather than the flux pump itself. Moreover, at over 1 kA current level, the device can maintain high flux injection accuracy, and the overall flux ripple is less than 0.2 mili-Weber. The work has shown the potential of using the device to operate high field HTS magnets in ultra-high quasi-persistent current mode, thus substantially reducing the inductance, size, weight, and cost of high field magnets, making them more accessible. It also indicates that the device is promising for powering HTS NMR/MRI magnets, in which the requirement for magnetic field satiability is demanding. -
MINIATURE PENNING CELL ARRAY for ON-CHIP VACUUM PUMPING Scott R
MINIATURE PENNING CELL ARRAY FOR ON-CHIP VACUUM PUMPING Scott R. Green and Yogesh B. Gianchandani University of Michigan Engineering Research Center for Wireless Integrated Microsystems (WIMS), Ann Arbor, Michigan, USA ABSTRACT This paper presents a miniaturized Penning cell array for on-chip sputter-ion vacuum pumping. The effects of miniaturization on pumping performance – including cut-off magnetic flux, pumping rate, and minimum operating pressure – are examined. The pump is experimentally shown to reduce pressure by 600 mTorr (80 Pa) from a starting pressure of 18 Torr (2.4 kPa) in 30 minutes of operation. The rate of molecular removal is typically 3-15 x 1013 molecules per second. The architecture allows device operation at pressures at least as low as 70 mTorr (9.3 Pa), representing an improvement of two orders of magnitude over previously reported micro-sputter-ion pumps. INTRODUCTION Figure 1: MEMS devices requiring precise high-vacuum On-chip vacuum generation is an attractive alternative pressure levels for operation can be packaged with a and complement to vacuum sealing for microsystems that Penning cell array sputter-ion pump. require very long-term or very precise control over package work presents theoretical modeling and experimental pressure, including chip-scale atomic clocks and micro- validation of a miniature Penning cell array SIP architecture. mass spectrometers. In micro-scale packages with reduced volumes, the pressure increase due to even small outgassing DESIGN AND MODELING and leakage sources is amplified. Thus, the presence of a A single Penning cell consists of a cylindrical anode pump can add to system robustness and decreased sandwiched between two planar titanium cathodes, resulting requirements for hermetic sealing and use of low outgassing in radially-directed electric field lines at the mid-length of materials. -
Ba-Cu-O Bulk High-Temperature Superconductors
IEEE/CSC & ESAS EUROPEAN SUPERCONDUCTIVITY NEWS FORUM, No. 19, January 2012 Materials Process and Applications of Single Grain (RE)-Ba-Cu-O Bulk High-temperature Superconductors Beizhan Li, Difan Zhou, Kun Xu, Shogo Hara, Keita Tsuzuki, Motohiro Miki, Brice Felder, Zigang Deng and Mitsuru Izumi* Laboratory of Applied Physics, Department of Marine Electronics and Mechanical Engineering, Tokyo University of Marine Science and Technology (TUMSAT), 2-1-6, Etchu-jima, Koto-ku, Tokyo 135-8533, Japan *E-mail: [email protected] Abstract - This paper reviews recent advances in the melt process of (RE)-Ba-Cu-O [(RE)BCO, where RE represents a rare earth element] single grain high-temperature superconductors (HTS), bulks and its applications. The efforts on the improvement of the magnetic flux pinning with employing the top-seeded melt-growth process technique and using a seeded infiltration and growth process are discussed. Which including various chemical doping strategies and controlled pushing effect based on the peritectic reaction of (RE)BCO. The typical experiment results, such as the largest single domain bulk, the clear TEM observations and the significant critical current density, are summarized together with the magnetization techniques. Finally, we highlight the recent prominent progress of HTS bulk applications, including Maglev, flywheel, power device, magnetic drug delivery system and magnetic resonance devices. Preprint of plenary SCC paper submitted to Physica C (should be cited accordingly) Submitted to ESNF November 30, 2011; accepted Dec. 6, 2011. Reference No. CR24; Category 3. Keywords – rare earth, cuprate, high-temperature superconductor, HTS, bulk superconductor, melt growth process, flux pinning, MAGLEV, MRI, Flywheel, Motor I. -
3D Modeling of a Superconducting Dynamo-Type Flux Pump
www.nature.com/scientificreports OPEN 3D modeling of a superconducting dynamo‑type fux pump Asef Ghabeli1, Enric Pardo1* & Milan Kapolka1,2 High temperature superconducting (HTS) dynamos are promising devices that can inject large DC currents into the winding of superconducting machines or magnets in a contactless way. Thanks to this, troublesome brushes in HTS machines or bulky currents leads with high thermal losses will be no longer required. The working mechanism of HTS dynamo has been controversial during the recent years and several explanations and models have been proposed to elucidate its performance. In this paper, we present the frst three‑dimensional (3D) model of an HTS fux pump, which has good agreement with experiments. This model can be benefcial to clarify the mechanism of the dynamo and pinpoint its unnoticed characteristics. Employing this model, we delved into the screening current and electric feld distribution across the tape surface in several crucial time steps. This is important, since the overcritical screening current has been shown to be the reason for fux pumping. In addition, we analyzed the impact of both components of electric feld and screening current on voltage generation, which was not possible in previous 2D models. We also explored the necessary distance of voltage taps at diferent airgaps for precise measurement of the voltage across the tape in the dynamo. Since 1960s, when the frst generation of superconducting fux pumps have been designed and operated, the fux pump technology has undergone a remarkable developement1–5. Within around 60 years, various mechanically or electrically driven superconducting fux pumps have been operated using low-temperature superconductor (LTS) materials in their previous generation and high-temperature superconductor (HTS) materials in their last generation. -
Origin of DC Voltage in Type II Superconducting Flux Pumps: Field, Field Rate of Change, and Current Density Dependence of Resistivity J
Origin of DC voltage in type II superconducting flux pumps: field, field rate of change, and current density dependence of resistivity J. Geng,1 K. Matsuda,1,2 L. Fu,1 J-F Fagnard,3 H. Zhang,1 X. Zhang,1 B. Shen,1 Q. Dong,1 M. Baghdadi,1 and T. A. Coombs1 1 Department of Engineering, University of Cambridge, Cambridge, CB3 0FA, United Kingdom 2 Magnifye Ltd., Cambridge, CB5 8DD United Kingdom 3. Montefiore Institute, Liège University, B-4000 Liège, Belgium Email: [email protected] Superconducting flux pumps are the kind of devices which can generate direct current into superconducting circuit using external magnetic field. The key point is how to induce a DC voltage across the superconducting load by AC fields. Giaever [1] pointed out flux motion in superconductors will induce a DC voltage, and demonstrated a rectifier model which depended on breaking superconductivity. Klundert et al. [2, 3] in their review(s) described various configurations for flux pumps all of which relied on inducing the normal state in at least part of the superconductor. In this letter, following their work, we reveal that a variation in the resistivity of type II superconductors is sufficient to induce a DC voltage in flux pumps and it is not necessary to break superconductivity. This variation in resistivity is due to the fact that flux flow is influenced by current density, field intensity, and field rate of change. We propose a general circuit analogy for travelling wave flux pumps, and provide a mathematical analysis to explain the DC voltage. -
Transconductance Quantization in a Topological Josephson Tunnel Junction Circuit
PHYSICAL REVIEW RESEARCH 3, 013289 (2021) Transconductance quantization in a topological Josephson tunnel junction circuit L. Peyruchat,1 J. Griesmar ,1,* J.-D. Pillet ,1,2 and Ç. Ö. Girit 1,† 1 Flux Quantum Lab (0), JEIP, USR 3573 CNRS, Collège de France, PSL University, 11, place Marcelin Berthelot, 75231 Paris Cedex 05, France 2LSI, CEA/DRF/IRAMIS, Ecole Polytechnique, CNRS, Institut Polytechnique de Paris, F-91128 Palaiseau, France (Received 25 September 2020; revised 1 February 2021; accepted 2 February 2021; published 29 March 2021) Superconducting circuits incorporating Josephson tunnel junctions are widely used for fundamental research as well as for applications in fields such as quantum information and magnetometry. The quantum coherent nature of Josephson junctions makes them especially suitable for metrology applications. Josephson junctions suffice to form two sides of the quantum metrology triangle, relating frequency to either voltage or current, but not its base, which directly links voltage to current. We propose a five Josephson tunnel junction circuit in which 2 simultaneous pumping of flux and charge results in quantized transconductance in units 4e /h = 2e/0,the ratio between the Cooper pair charge and the flux quantum. The Josephson quantized Hall conductance device (JHD) is explained in terms of intertwined Cooper pair pumps driven by the AC Josephson effect. We describe an experimental implementation of the device and discuss the optimal configuration of external parameters and possible sources of error. The JHD has a rich topological structure and demonstrates that Josephson tunnel junctions are universal, capable of interrelating frequency, voltage, and current via fundamental constants. DOI: 10.1103/PhysRevResearch.3.013289 I. -
PERFORMANCE ANALYSIS of LOW TEMPERATURE SUPERCONDUCTING FLUX PUMP Researched at SRON Groningen, the Netherlands
Bachelors Thesis in Applied Physics PERFORMANCE ANALYSIS OF LOW TEMPERATURE SUPERCONDUCTING FLUX PUMP Researched at SRON Groningen, the Netherlands July, 2017 James Robert Lyon, S2709821 [email protected] / (+31)619671537 Faculty of Science and Engineering University of Groningen Supervised by dr. ir. G. de Lange (SRON) prof. dr. ir. C.H. van der Wal (RUG) prof. dr. T. Banerjee (RUG) 1 [This page intentionally left blank] 2 Abstract A flux pump system uses a small alternating current to build up a large current inside a superconducting load coil. An experimental prototype has been built for the purpose of analysing its performance, including its stability, reliability and limiting, for possible satellite application at SRON. The flux pump circuit is a developing project previously worked upon by two other Bachelor students. The operation of the full wave transformer rectifier flux pump is described and analysed. The experimental set-up was rebuilt, measurement methods were developed and sensors were calibrated. The optimal primary wave for this device was experimentally determined to have a frequency of 0.1667 Hz and amplitude of 250 mA from which an exponential increase was observed and a maximum output of approximately 7 A was achieved. However, it proved to be an unreliable system as repeated experiments provided inconsistent results due to suspected short circuiting of inductors. Moreover, the power and efficiency of the system is analysed and is in good agreement with theoretical predications. The flux pump has a maximum efficiency of 80% at a normalised current of 0.2. 3 Contents Abstract ................................................................................................................................................................................. 3 Acknowledgments ...............................................................................................................................................................