Understanding Interdependencies Between Mechanical Velocity and Electrical Voltage in Electromagnetic Micromixers
Total Page:16
File Type:pdf, Size:1020Kb
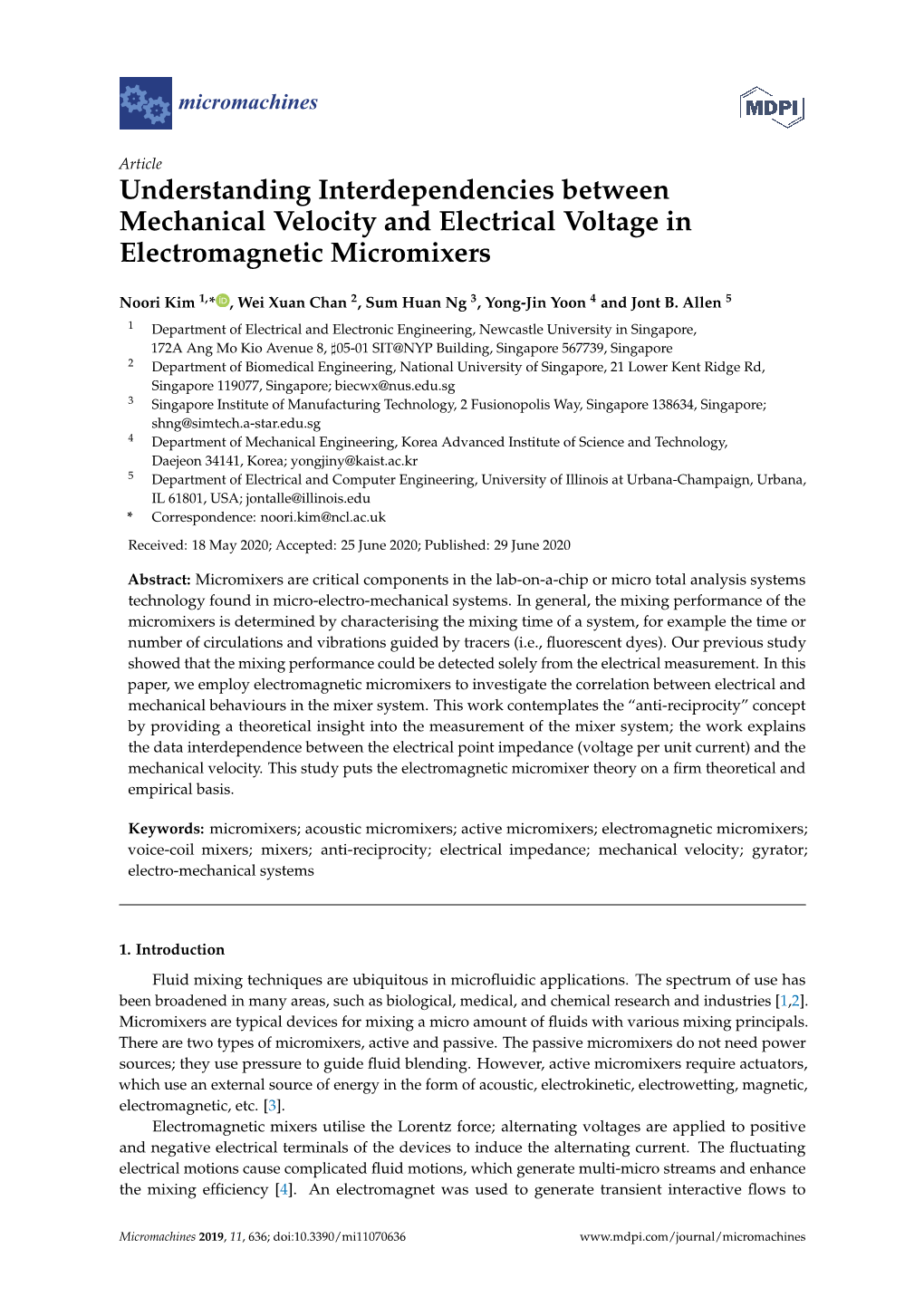
Load more
Recommended publications
-
Analysis and Measurement of Anti-Reciprocal Systems By
ANALYSIS AND MEASUREMENT OF ANTI-RECIPROCAL SYSTEMS BY NOORI KIM DISSERTATION Submitted in partial fulfillment of the requirements for the degree of Doctor of Philosophy in Electrical and Computer Engineering in the Graduate College of the University of Illinois at Urbana-Champaign, 2014 Urbana, Illinois Doctoral Committee: Associate Professor Jont B. Allen, Chair Professor Stephen Boppart Professor Steven Franke Associate Professor Michael Oelze ABSTRACT Loudspeakers, mastoid bone-drivers, hearing-aid receivers, hybrid cars, and more – these “anti-reciprocal” systems are commonly found in our daily lives. However, the depth of understanding about the systems has not been well addressed since McMillan in 1946. The goal of this study is to provide an intuitive and clear understanding of the systems, beginning from modeling one of the most popular hearing-aid receivers, a balanced armature receiver (BAR). Models for acoustic transducers are critical in many acoustic applications. This study analyzes a widely used commercial hearing-aid receiver, manufactured by Knowles Electron- ics, Inc (ED27045). Electromagnetic transducer modeling must consider two key elements: a semi-inductor and a gyrator. The semi-inductor accounts for electromagnetic eddy cur- rents, the “skin effect” of a conductor, while the gyrator accounts for the anti-reciprocity characteristic of Lenz’s law. Aside from the work of Hunt, to our knowledge no publications have included the gyrator element in their electromagnetic transducer models. The most prevalent method of transducer modeling evokes the mobility method, an ideal transformer alternative to a gyrator followed by the dual of the mechanical circuit. The mobility ap- proach greatly complicates the analysis. The present study proposes a novel, simplified, and rigorous receiver model. -
Chapter 6 Two-Port Network Model
Chapter 6 Two-Port Network Model 6.1 Introduction In this chapter a two-port network model of an actuator will be briefly described. In Chapter 5, it was shown that an automated test setup using an active system can re- create various load impedances over a limited range of frequencies. This test set-up can therefore be used to automatically reproduce any load impedance condition (related to a possible application) and apply it to a test or sample actuator. It is then possible to collect characteristic data from the test actuator such as force, velocity, current and voltage. Those characteristics can then be used to help to determine whether the tested actuator is appropriate or not for the case simulated. However versatile and easy to use this test set-up may be, because of its limitations, there is some characteristic data it will not be able to provide. For this reason and the fact that it can save a lot of measurements, having a good linear actuator model can be of great use. Developed for transduction theory [29], the linear model presented in this chapter is 77 called a Two-Port Network model. The automated test set-up remains an essential complement for this model, as it will allow the development and verification of accuracy. This chapter will focus on the two-port network model of the 1_3 tube array actuator provided by MSI (Cf: Figure 5.5). 6.2 Theory of the Two–Port Network Model As a transducer converts energy from electrical to mechanical forms, and vice- versa, it can be modelled as a Two-Port Network that relates the electrical properties at one port to the mechanical properties at the other port. -
Analysis of Microwave Networks
! a b L • ! t • h ! 9/ a 9 ! a b • í { # $ C& $'' • L C& $') # * • L 9/ a 9 + ! a b • C& $' D * $' ! # * Open ended microstrip line V + , I + S Transmission line or waveguide V − , I − Port 1 Port Substrate Ground (a) (b) 9/ a 9 - ! a b • L b • Ç • ! +* C& $' C& $' C& $ ' # +* & 9/ a 9 ! a b • C& $' ! +* $' ù* # $ ' ò* # 9/ a 9 1 ! a b • C ) • L # ) # 9/ a 9 2 ! a b • { # b 9/ a 9 3 ! a b a w • L # 4!./57 #) 8 + 8 9/ a 9 9 ! a b • C& $' ! * $' # 9/ a 9 : ! a b • b L+) . 8 5 # • Ç + V = A V + BI V 1 2 2 V 1 1 I 2 = 0 V 2 = 0 V 2 I 1 = CV 2 + DI 2 I 2 9/ a 9 ; ! a b • !./5 $' C& $' { $' { $ ' [ 9/ a 9 ! a b • { • { 9/ a 9 + ! a b • [ 9/ a 9 - ! a b • C ) • #{ • L ) 9/ a 9 ! a b • í !./5 # 9/ a 9 1 ! a b • C& { +* 9/ a 9 2 ! a b • I • L 9/ a 9 3 ! a b # $ • t # ? • 5 @ 9a ? • L • ! # ) 9/ a 9 9 ! a b • { # ) 8 -
A Review of Electric Impedance Matching Techniques for Piezoelectric Sensors, Actuators and Transducers
Review A Review of Electric Impedance Matching Techniques for Piezoelectric Sensors, Actuators and Transducers Vivek T. Rathod Department of Electrical and Computer Engineering, Michigan State University, East Lansing, MI 48824, USA; [email protected]; Tel.: +1-517-249-5207 Received: 29 December 2018; Accepted: 29 January 2019; Published: 1 February 2019 Abstract: Any electric transmission lines involving the transfer of power or electric signal requires the matching of electric parameters with the driver, source, cable, or the receiver electronics. Proceeding with the design of electric impedance matching circuit for piezoelectric sensors, actuators, and transducers require careful consideration of the frequencies of operation, transmitter or receiver impedance, power supply or driver impedance and the impedance of the receiver electronics. This paper reviews the techniques available for matching the electric impedance of piezoelectric sensors, actuators, and transducers with their accessories like amplifiers, cables, power supply, receiver electronics and power storage. The techniques related to the design of power supply, preamplifier, cable, matching circuits for electric impedance matching with sensors, actuators, and transducers have been presented. The paper begins with the common tools, models, and material properties used for the design of electric impedance matching. Common analytical and numerical methods used to develop electric impedance matching networks have been reviewed. The role and importance of electrical impedance matching on the overall performance of the transducer system have been emphasized throughout. The paper reviews the common methods and new methods reported for electrical impedance matching for specific applications. The paper concludes with special applications and future perspectives considering the recent advancements in materials and electronics. -
Electrical Impedance Tomography
INSTITUTE OF PHYSICS PUBLISHING INVERSE PROBLEMS Inverse Problems 18 (2002) R99–R136 PII: S0266-5611(02)95228-7 TOPICAL REVIEW Electrical impedance tomography Liliana Borcea Computational and Applied Mathematics, MS 134, Rice University, 6100 Main Street, Houston, TX 77005-1892, USA E-mail: [email protected] Received 16 May 2002, in final form 4 September 2002 Published 25 October 2002 Online at stacks.iop.org/IP/18/R99 Abstract We review theoretical and numerical studies of the inverse problem of electrical impedance tomographywhich seeks the electrical conductivity and permittivity inside a body, given simultaneous measurements of electrical currents and potentials at the boundary. (Some figures in this article are in colour only in the electronic version) 1. Introduction Electrical properties such as the electrical conductivity σ and the electric permittivity , determine the behaviour of materials under the influence of external electric fields. For example, conductive materials have a high electrical conductivity and both direct and alternating currents flow easily through them. Dielectric materials have a large electric permittivity and they allow passage of only alternating electric currents. Let us consider a bounded, simply connected set ⊂ Rd ,ford 2and, at frequency ω, let γ be the complex admittivity function √ γ(x,ω)= σ(x) +iω(x), where i = −1. (1.1) The electrical impedance is the inverse of γ(x) and it measures the ratio between the electric field and the electric current at location x ∈ .Electrical impedance tomography (EIT) is the inverse problem of determining the impedance in the interior of ,givensimultaneous measurements of direct or alternating electric currents and voltages at the boundary ∂. -
Impedance Matching
Impedance Matching Advanced Energy Industries, Inc. Introduction The plasma industry uses process power over a wide range of frequencies: from DC to several gigahertz. A variety of methods are used to couple the process power into the plasma load, that is, to transform the impedance of the plasma chamber to meet the requirements of the power supply. A plasma can be electrically represented as a diode, a resistor, Table of Contents and a capacitor in parallel, as shown in Figure 1. Transformers 3 Step Up or Step Down? 3 Forward Power, Reflected Power, Load Power 4 Impedance Matching Networks (Tuners) 4 Series Elements 5 Shunt Elements 5 Conversion Between Elements 5 Smith Charts 6 Using Smith Charts 11 Figure 1. Simplified electrical model of plasma ©2020 Advanced Energy Industries, Inc. IMPEDANCE MATCHING Although this is a very simple model, it represents the basic characteristics of a plasma. The diode effects arise from the fact that the electrons can move much faster than the ions (because the electrons are much lighter). The diode effects can cause a lot of harmonics (multiples of the input frequency) to be generated. These effects are dependent on the process and the chamber, and are of secondary concern when designing a matching network. Most AC generators are designed to operate into a 50 Ω load because that is the standard the industry has settled on for measuring and transferring high-frequency electrical power. The function of an impedance matching network, then, is to transform the resistive and capacitive characteristics of the plasma to 50 Ω, thus matching the load impedance to the AC generator’s impedance. -
Brief Study of Two Port Network and Its Parameters
© 2014 IJIRT | Volume 1 Issue 6 | ISSN : 2349-6002 Brief study of two port network and its parameters Rishabh Verma, Satya Prakash, Sneha Nivedita Abstract- this paper proposes the study of the various ports (of a two port network. in this case) types of parameters of two port network and different respectively. type of interconnections of two port networks. This The Z-parameter matrix for the two-port network is paper explains the parameters that are Z-, Y-, T-, T’-, probably the most common. In this case the h- and g-parameters and different types of relationship between the port currents, port voltages interconnections of two port networks. We will also discuss about their applications. and the Z-parameter matrix is given by: Index Terms- two port network, parameters, interconnections. where I. INTRODUCTION A two-port network (a kind of four-terminal network or quadripole) is an electrical network (circuit) or device with two pairs of terminals to connect to external circuits. Two For the general case of an N-port network, terminals constitute a port if the currents applied to them satisfy the essential requirement known as the port condition: the electric current entering one terminal must equal the current emerging from the The input impedance of a two-port network is given other terminal on the same port. The ports constitute by: interfaces where the network connects to other networks, the points where signals are applied or outputs are taken. In a two-port network, often port 1 where ZL is the impedance of the load connected to is considered the input port and port 2 is considered port two. -
TWO MODELS of ELECTRICAL IMPEDANCE for ELECTRODES with TAP WATER and THEIR CAPABILITY to RECORD GAS VOLUME FRACTION Revista Mexicana De Ingeniería Química, Vol
Revista Mexicana de Ingeniería Química ISSN: 1665-2738 [email protected] Universidad Autónoma Metropolitana Unidad Iztapalapa México Rodríguez-Sierra, J.C.; Soria, A. TWO MODELS OF ELECTRICAL IMPEDANCE FOR ELECTRODES WITH TAP WATER AND THEIR CAPABILITY TO RECORD GAS VOLUME FRACTION Revista Mexicana de Ingeniería Química, vol. 15, núm. 2, 2016, pp. 543-551 Universidad Autónoma Metropolitana Unidad Iztapalapa Distrito Federal, México Available in: http://www.redalyc.org/articulo.oa?id=62046829020 How to cite Complete issue Scientific Information System More information about this article Network of Scientific Journals from Latin America, the Caribbean, Spain and Portugal Journal's homepage in redalyc.org Non-profit academic project, developed under the open access initiative Vol. 15, No. 2 (2016) 543-551 Revista Mexicana de Ingeniería Química CONTENIDO TWO MODELS OF ELECTRICAL IMPEDANCE FOR ELECTRODES WITH TAP WATER ANDVolumen THEIR 8, número CAPABILITY 3, 2009 / Volume TO 8, RECORD number 3, GAS2009 VOLUME FRACTION DOS MODELOS DE IMPEDANCIA ELECTRICA´ PARA ELECTRODOS CON AGUA POTABLE Y SU CAPACIDAD DE REPRESENTAR LA FRACCION´ VOLUMEN DE 213 Derivation and application of the Stefan-MaxwellGAS equations * (Desarrollo y aplicaciónJ.C. de Rodr las ecuaciones´ıguez-Sierra de Stefan-Maxwell) and A. Soria Departamento de Ingenier´ıade Procesos e Hidr´aulica.Divisi´onCBI, Universidad Aut´onomaMetropolitana-Iztapalapa. San Stephen Whitaker Rafael Atlixco No. 186 Col. Vicentina, CP 09340 Cd. de M´exico,M´exico. Received May 24, 2016; Accepted July 5, 2016 Biotecnología / Biotechnology Abstract 245 Modelado de la biodegradación en biorreactores de lodos de hidrocarburos totales del petróleo Bubble columns are devices for simultaneous two-phase or three-phase flows. -
Hamilton Equations, Commutator, and Energy Conservation †
quantum reports Article Hamilton Equations, Commutator, and Energy Conservation † Weng Cho Chew 1,* , Aiyin Y. Liu 2 , Carlos Salazar-Lazaro 3 , Dong-Yeop Na 1 and Wei E. I. Sha 4 1 College of Engineering, Purdue University, West Lafayette, IN 47907, USA; [email protected] 2 College of Engineering, University of Illinois at Urbana-Champaign, Urbana, IL 61820, USA; [email protected] 3 Physics Department, University of Illinois at Urbana-Champaign, Urbana, IL 61820, USA; [email protected] 4 College of Information Science and Electronic Engineering, Zhejiang University, Hangzhou 310058, China; [email protected] * Correspondence: [email protected] † Based on the talk presented at the 40th Progress In Electromagnetics Research Symposium (PIERS, Toyama, Japan, 1–4 August 2018). Received: 12 September 2019; Accepted: 3 December 2019; Published: 9 December 2019 Abstract: We show that the classical Hamilton equations of motion can be derived from the energy conservation condition. A similar argument is shown to carry to the quantum formulation of Hamiltonian dynamics. Hence, showing a striking similarity between the quantum formulation and the classical formulation. Furthermore, it is shown that the fundamental commutator can be derived from the Heisenberg equations of motion and the quantum Hamilton equations of motion. Also, that the Heisenberg equations of motion can be derived from the Schrödinger equation for the quantum state, which is the fundamental postulate. These results are shown to have important bearing for deriving the quantum Maxwell’s equations. Keywords: quantum mechanics; commutator relations; Heisenberg picture 1. Introduction In quantum theory, a classical observable, which is modeled by a real scalar variable, is replaced by a quantum operator, which is analogous to an infinite-dimensional matrix operator. -
The Conjugate Variable Method in Hamilton-Lie Perturbation Theory −Applications to Plasma Physics−
Plasma and Fusion Research: Regular Articles Volume 3, 057 (2008) The Conjugate Variable Method in Hamilton-Lie Perturbation Theory −Applications to Plasma Physics− Shinji TOKUDA Japan Atomic Energy Agency, Naka, Ibaraki, 311-0193 Japan (Received 21 February 2008 / Accepted 29 July 2008) The conjugate variable method, an essential ingredient in the path-integral formalism of classical statistical dynamics, is used to apply the Hamilton-Lie perturbation theory to a system of ordinary differential equations that does not have the Hamiltonian dynamic structure. The method endows the system with this structure by doubling the unknown variables; hence, the canonical Hamilton-Lie perturbation theory becomes applicable to the system. The method is applied to two classical problems of plasma physics to demonstrate its effectiveness and study its properties: a non-linear oscillator that can explode and the guiding center motion of a charged particle in a magnetic field. c 2008 The Japan Society of Plasma Science and Nuclear Fusion Research Keywords: one-form, Hamilton-Lie perturbation method, conjugate variable, non-linear oscillator, guiding cen- ter motion, plasma physics DOI: 10.1585/pfr.3.057 1. Introduction Since the Hamilton-Lie perturbation method is a pow- We begin by considering the following two non-linear erful analytical tool that enables us to investigate the prob- oscillators lem deeply, it would be a significant contribution to the de- velopment of approximation methods in physics if it were dx dy = y, = −x − x3, (1) made applicable for equations such as Eq. (2), which do dt dt not have the Hamiltonian structure. This seems impossi- and ble since the Hamilton-Lie perturbation method assumes the Hamiltonian structure of the equations. -
ELEC-E5650 Electroacoustics
ELEC-E5650ELECElectroacoustics-E5650 ElectroacousticsLecture 1: Overview, Electroacoustics introduction & Circuit Elements pt1 Lecture 2: SteadyRaimundo -GonzalezState Analysis / Dynamic Analogies Department of Signal Processing and Acoustics Aalto University School of Electrical Engineering Raimundo2 2GonzalezFebruary 2018 Department of Signal Processing and Acoustics Aalto University School of Electrical Engineering March 7, 2019 ELEC-E5650 Electroacoustics, Lecture 1 Raimundo Gonzalez 1 Aalto, Signal Processing & Acoustics ELEC-E5650 ElectroacousticsLecture 1: Overview, Electroacoustics introduction & Circuit Elements pt1 LectureRaimundo Gonzalez 2: Department of Signal Processing and Acoustics Aalto University School of Electrical Engineering 22 February 2018 I. Steady State Analysis ELEC-E5650 Electroacoustics, Lecture 1 Raimundo Gonzalez 2 Aalto, Signal Processing & Acoustics Steady state sinusoidal response When designing Electroacoustics systems we are usually more interestedELEC in the-E5650 steady state behavior of the system. This will ElectroacousticsLecture 1: Overview, Electroacoustics introduction & Circuit Elements pt1 lead into Raimundomostly Gonzalez working in the frequency domain. Department of Signal Processing and Acoustics Aalto University School of Electrical Engineering 22 February 2018 ELEC-E5650 Electroacoustics, Lecture 1 Raimundo Gonzalez Aalto, Signal Processing & Acoustics 3 Phasors to represent sinusoidal signals ELEC-E5650 ElectroacousticsLecture 1: Overview, Electroacoustics introduction & Circuit Elements -
A Method for Choosing an Initial Time Eigenstate in Classical and Quantum Systems
Entropy 2013, 15, 2415-2430; doi:10.3390/e15062415 OPEN ACCESS entropy ISSN 1099-4300 www.mdpi.com/journal/entropy Article A Method for Choosing an Initial Time Eigenstate in Classical and Quantum Systems Gabino Torres-Vega * and Monica´ Noem´ı Jimenez-Garc´ ´ıa Physics Department, Cinvestav, Apdo. postal 14-740, Mexico,´ DF 07300 , Mexico; E-Mail:njimenez@fis.cinvestav.mx * Author to whom correspondence should be addressed; E-Mail: gabino@fis.cinvestav.mx; Tel./Fax: +52-555-747-3833. Received: 23 April 2013; in revised form: 29 May 2013 / Accepted: 3 June 2013 / Published: 17 June 2013 Abstract: A subject of interest in classical and quantum mechanics is the development of the appropriate treatment of the time variable. In this paper we introduce a method of choosing the initial time eigensurface and how this method can be used to generate time-energy coordinates and, consequently, time-energy representations for classical and quantum systems. Keywords: energy-time coordinates; energy-time eigenfunctions; time in classical systems; time in quantum systems; commutators in classical systems; commutators Classification: PACS 03.65.Ta; 03.65.Xp; 03.65.Nk 1. Introduction The possible existence of a time operator in Quantum Mechanics has long been a subject of interest. This subject has been studied from different points of view and has led to several developments in quantum theory. At the end of this paper there is a short, incomplete, list of papers on this subject. However, we can also study the time variable in classical systems to begin to understand how to address time in quantum systems.