Straw Bale Home Basics
Total Page:16
File Type:pdf, Size:1020Kb
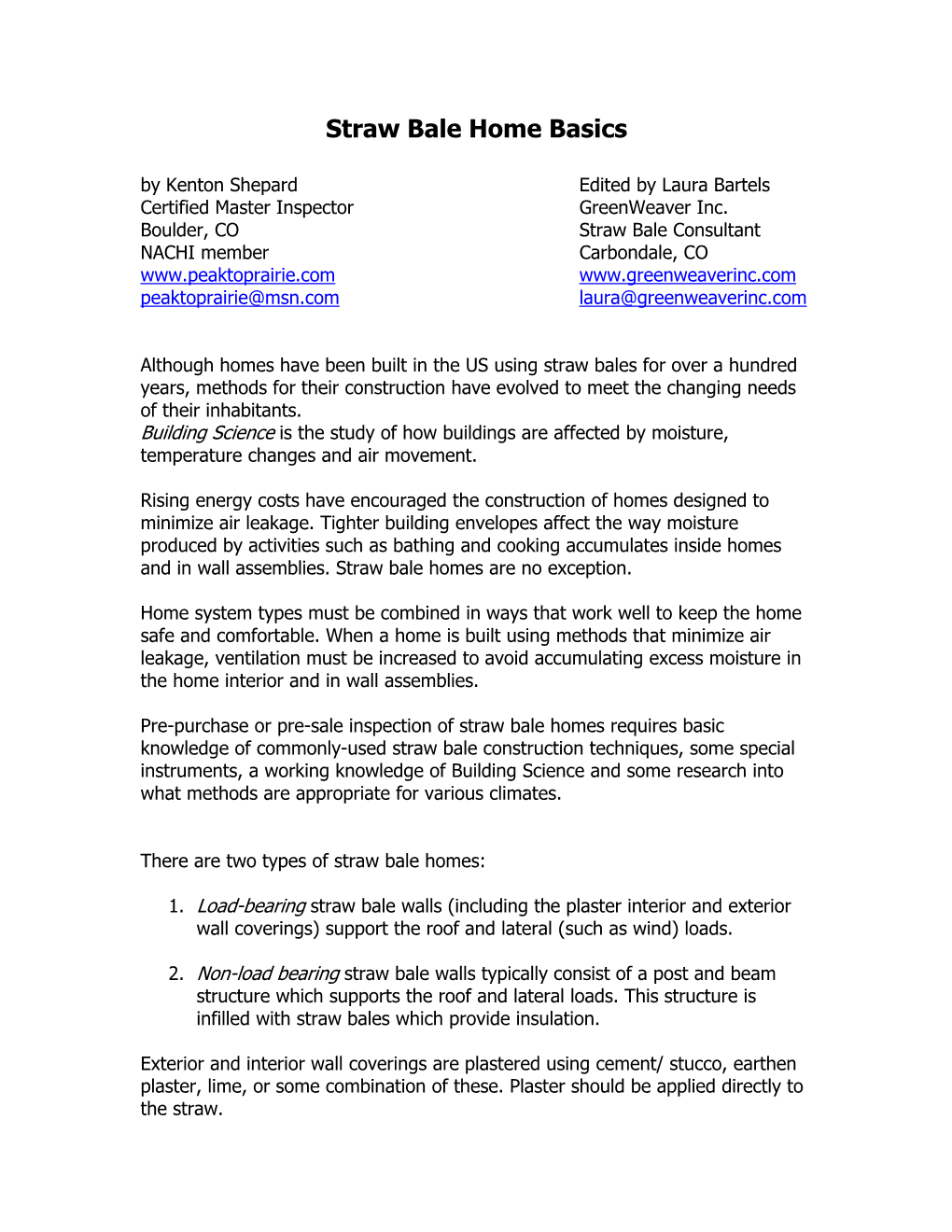
Load more
Recommended publications
-
The Stucco Technique of the Magistri Comacini: the Case Study of Santa Maria Dei Ghirli in Campione D'italia (Como, Italy)
The stucco technique of the Magistri Comacini: the case study of Santa Maria dei Ghirli in Campione d’Italia (Como, Italy) 1* 1 2 2 2 3 LAURA RAMPAZZI , BIAGIO RIZZO , CHIARA COLOMBO , CLAUDIA CONTI , MARCO REALINI , UGO BARTOLUCCI , 3 4 5 MARIA PERLA COLOMBINI , ANDREA SPIRITI , LAURA FACCHIN 1 Dipartimento di Scienze Chimiche e Ambientali, Università degli Studi dell’Insubria, via Valleggio 11, 22100 Como, Italy 2 Istituto per la Conservazione e la Valorizzazione dei Beni Culturali, Unità di Milano ‘Gino Bozza’, Area della Ricerca Milano 3 Bicocca, via Cozzi 53, 20125 Milano, Italy. 3 Dipartimento di Chimica e Chimica Industriale, Università di Pisa, Via Risorgimento 35, 56126 Pisa, Italy 4 Dipartimento di Informatica e Comunicazione, Università degli Studi dell’Insubria, Via Mazzini 5, 21100 Varese, Italy. 5 Scuola di Dottorato in Studi Umanistici, Università degli Studi di Verona, Facoltà di Lettere e Filosofia, Dipartimento di Arte, Storia e Società, via S. Francesco 22, 37129 Verona, Italy. *Corresponding author Laura Rampazzi, email address: [email protected]; phone number: +390312386475; fax number: +390312386449 Abstract This article is aimed to define the artistic technique performed by the outstanding artist Isidoro Bianchi for the Baroque stucco decorations in the church of Santa Maria dei Ghirli (Campione d’Italia, Italy). Samples of stucco were examined by means of optical microscopy, scanning electron microscopy with microprobe, X-ray powder diffraction, Fourier transform infrared spectroscopy, gas chromatography-mass spectrometry and laser ablation mass spectrometry equipped with plasma source spectrometry. On the basis of the results obtained art historians made new hypotheses on the biography of the artist and on the historical location of his birthplace. -
Greek Interior Decoration: Materials and Technology in the Art of Cosmesis and Display
CHAPTER 41 Greek Interior Decoration: Materials and Technology in the Art of Cosmesis and Display Hariclia Brecoulaki Introduction The concept of “ordering” and “adornment” is expressed in Greek culture with the word cosmesis. The interior space—be it domestic or public—adapted to architectural features and building functions is transformed into a suitable setting for the human activities that are to occur there; a setting where various movable objects and fixed decorations inter- act to order and adorn it. The interior space becomes its own closed universe, cosmos, combining a variety of materials, textures, colors, and light. To enhance a temple with monumental statues, to adorn a tomb with paintings or a house with mosaics, to display domestic paraphernalia in gynaecea (women’s quarters) or bronze armor on the walls of andrōnēs (men’s dining rooms), to furnish a king’s residence with sumptuous couches and artworks; these are acts that reflect specific social motivations and cultural behaviors, religious beliefs, political environments, and aesthetic values. We limit our focus to the fixed elements of interior decoration in ancient Greek domestic space (wall paintings and mosaics), movable artifacts (such as freestanding sculpture and furniture), and panel painting. We shall briefly touch on the interior deco- ration of Greek public spaces. While the function of architectural sculpture was decora- tive from its origin, statues and large‐scale painting in Greek public buildings assumed religious or civic roles and cannot be considered decorative in the current sense of the word (Ridgway 1971, 337). Likewise, the accumulation, with no primary planning, of countless dedications within public buildings, particularly in temples (although on view for worshipers and visitors), did not reflect a predefined concept for interior decoration. -
Plaster, Stucco & Wallpaper
Practical Conservation Guide for Heritage Properties Plaster,Stucco & Wallpaper Introduction The conservation of plaster, stucco and wallpaper requires a highly trained professional or a knowledgeable and practiced homeowner. Although routine maintenance may seen straightforward, damage can occur to the unique materials in your heritage home as a result of inappropriate conservation efforts. This guide includes general information on plaster, stucco and wallpaper and briefly mentions guidelines for conservation to aid you in selecting the proper professional for the task at hand. In this guide: Plaster Plaster Plaster consists of a mixture of powdered lime or gypsum Decorative Plaster with water, applied to the interior surfaces of a building. Stucco The mixture was traditionally applied on walls and ceilings over a lath made of wooden bands secured to Wallpaper wall studs or ceiling joists, but has more recently been Samples and applied to heavy-duty metal mesh. The application of Documentation plaster traditionally included three coats. The first, or Maintenance and Repair base coat, was strengthened to best adhere to the lath, Safety Precautions: with binders of animal hair and aggregates of sand, for Lead-based Paints example. The second coat consisted of a similar composition and texture, but aimed at ridding the surface of irregularities. The final application often saw the addition of lime to whiten and create a smooth surface free of imperfections. Paint and wall paper would be applied directly on this top coat. Contemporary wet plaster has typically replaced lime with gypsum, a hydrated calcium sulfate or sulfate of lime that hardens more quickly. Modern-gypsum plaster does bond to the traditional plaster well, aided by lime’s softer and more porous character. -
Stucco and Clay in the Decoration of the Monumental Building of Old Nisa
AperTO - Archivio Istituzionale Open Access dell'Università di Torino Stucco and Clay in the Decoration of the Monumental Building of Old Nisa This is a pre print version of the following article: Original Citation: Availability: This version is available http://hdl.handle.net/2318/1704247 since 2020-02-19T10:43:04Z Terms of use: Open Access Anyone can freely access the full text of works made available as "Open Access". Works made available under a Creative Commons license can be used according to the terms and conditions of said license. Use of all other works requires consent of the right holder (author or publisher) if not exempted from copyright protection by the applicable law. (Article begins on next page) 07 October 2021 Stucco and clay in the decoration of the monumental buildingS of old niSa Carlo LippoLis Università degli Studi di Torino, Dipartimento di Studi Storici, Centro Ricerche Archeologiche e scavi di Torino Patrizia Davit Università degli Studi di Torino, Dipartimento di Chimica Francesca turco Università degli Studi di Torino, Dipartimento di Chimica résumé – Contrairement au décor architectural en terre cuite et à la sculpture en argile crue, la production de stucs dans l’ancienne Nisa n’a été que marginalement étudiée. Ceci est essentiellement dû à la rareté des représentations fgurées. Cependant, des fouilles récentes ont permis de découvrir quelques fagments de sculptures en stuc et en argile, en même temps que des moules doubles en mortier de gypse qui éclairent d’un nouveau jour les techniques de fabrication des sculptures. Le procédé de fabrication d’une sculpture est identique pour les deux types de matériaux puisque le modelage de la fgure se fait grâce à l’application successive de couches d’argile et de stuc (ou les deux), de plus en plus fnes et pures. -
Eighteenth-Century Plasterwork in Ireland and Europe
TRINITY COLLEGE DUBLIN Department of History of Art and Architecture Eighteenth-century Plasterwork in Ireland and Europe AN INTERNATIONAL CONFERENCE The conference acknowledges the financial assistance provided by the Environment Fund of the Department of the Environment, Heritage and Local Government. CONFERENCE SCHEDULE 9.30 am Registration SESSION 1 10.00 am Is stucco just the icing on the cake? Alastair Laing – Keynote Speaker 10.30 am Before stucco: decorative plasterwork in England and Ireland 1550-1650 Claire Gapper 11.00 am A baptism of fire: what the flames revealed. The plasterwork of Uppark and Prior Park Ian Constantinides 11.30 am Coffee SESSION 2 11.50 pm Stuccoes of the masters of the Lombard lakes Andrea Spiriti 12.20 pm Baroque stucco in Bohemia and Moravia Martin Krummholz 12.50 pm QUESTIONS 1.00 pm Lunch SESSION 3 2.00 pm Eighteenth-century stucco in Germany Barbara Rinn 2.30 pm Stucco and sterling: the earning power of stuccatori Christine Casey 3.00 pm Masterpieces of rococo stucco in the Netherlands Wijnand Freling 3.30 pm Coffee SESSION 4 3.50 pm Cramillion and continental rococo Joseph McDonnell 4.20 pm Peculiar plaster: recent conservation of Irish eighteenth-century modelled plaster Richard Ireland 4.50 pm Plasterers and stucco-workers of the Dublin School Conor Lucey 5.20 pm QUESTIONS and DISCUSSION CONTRIBUTORS Alastair Laing read Modern History at Corpus Christi College, Oxford. In 1968 he began a – regrettably, never completed – thesis on ‘The origins of South German Rococo stucco’ under Sir Anthony Blunt at the Courtauld Institute. The chief products of this have been Baroque & Rococo: Architecture & Decoration (1978), written with Anthony Blunt; ‘French ornamental engravings and the diffusion of the Rococo’, in Le stampe e la diffusione delle imagini e degli stili, ed. -
A Short Survey of Stucco Decoration in the Mahabat Khan Mosque, Peshawar
9 Ancient Pakistan, Vol. XIV A Short Survey of Stucco Decoration in the Mahabat Khan Mosque, Peshawar IBRAHIM SHAH AND NIDAULLAH SEHRAI Introduction The Mahabat Khan Mosque (Pl.. 1), "the chief congregational mosque of the city", is located in the Andarshahr area inside the Asamai Gate of the walled city of Peshawar. It was built by Mahabat Khan Mirza Luhrasp, son of Mahabat Khan Zamanah Beg, governor of the "Subah-e- Kabul wa Peshawar", during AD 1660 and 1670 (Shah, 1993, p.151; 1994, p. 499; 1999, p. 97). The mosque, in view of its gigantic structure and sur;nptuous embellishment, is justifiably regarded as " a real ornament of the city of Peshawar" (Dani, 1969, p. 175). The decorative work of this mosque falls into three major classes: a. Calligraphic Specimens b. Painted Decoration c. Stucco Relief Work The principal author has already published articles on the first two classes of the decoration (Shah, 1996, pp. 389-410; 1997, pp. 91-112), we, therefore, confine here to examining decoration executed in stucco. Stucco Relief Work Stucco, in this mosque, is used for three main purposes: 1. as mortar for laying bricks in courses (or as binding agent). 11. as plaster for covering naked bricks to get a smooth ground. iii. as a medium for relief work-tracery, stamped or moulded. The first two being out of context here, we, therefore, confine ourselves to the description of the third purpose, i.e., stucco relief work. The term 'stucco' is" applied to fine exterior or interior plaster work used as a three dimensional ornamentation, as a smooth plaster surface or as a wet ground for the painting of frescoes" (Encyc. -
Traditional Architectural Renders on Earthen Surfaces
University of Pennsylvania ScholarlyCommons Theses (Historic Preservation) Graduate Program in Historic Preservation 1991 Traditional Architectural Renders on Earthen Surfaces Maria Isabel G. Beas University of Pennsylvania Follow this and additional works at: https://repository.upenn.edu/hp_theses Part of the Historic Preservation and Conservation Commons Beas, Maria Isabel G., "Traditional Architectural Renders on Earthen Surfaces" (1991). Theses (Historic Preservation). 395. https://repository.upenn.edu/hp_theses/395 Copyright note: Penn School of Design permits distribution and display of this student work by University of Pennsylvania Libraries. Suggested Citation: Beas, Maria Isabel G. (1991). Traditional Architectural Renders on Earthen Surfaces. (Masters Thesis). University of Pennsylvania, Philadelphia, PA. This paper is posted at ScholarlyCommons. https://repository.upenn.edu/hp_theses/395 For more information, please contact [email protected]. Traditional Architectural Renders on Earthen Surfaces Disciplines Historic Preservation and Conservation Comments Copyright note: Penn School of Design permits distribution and display of this student work by University of Pennsylvania Libraries. Suggested Citation: Beas, Maria Isabel G. (1991). Traditional Architectural Renders on Earthen Surfaces. (Masters Thesis). University of Pennsylvania, Philadelphia, PA. This thesis or dissertation is available at ScholarlyCommons: https://repository.upenn.edu/hp_theses/395 'T,' i'&Sim mi> 'm m. i =ir,!t-i^-!vs i )'» \ •.'.i:'-ii-2\c-. fell ;;!•!' UNIVERSITVy PENNSYLVANIA. UBKARIES TRADITIONAL ARCHITECTURAL RENDERS ON EARTHEN SURFACES Maria Isabel G. Beas A THESIS in The Graduate Program in Historic Presen/ation Presented to the faculties of the University of Pennsylvania in Partial Fulfillment of the Requirements for the Degree of MASTER OF SCIENCE 1991 Frank G.lMatero, Associate Professor 'reservation, Advisor X Samuel Y. -
A Common-Sense Way to Apply Stucco to Concrete Block
Make it Stick: By Russ Flynn Concrete block makes a super base for Portland cement-based plaster (stucco). The two materials are made from the same basic ingredients and they are extremely compatible. Prop- erly done, it’s a great combination. The Block The concrete block should have an open or coarse texture. This enables the stucco to interlock with the sur- face of the block, providing a me- chanical key bond (Fig. 1). Figure 2 Figure 3 In some parts of the country, stan- tion. Spray the blockwith water. If the water beads up as if on wax paper, you can forget suction bond Your remain- ing options are the use of a bonding agent or metal reinforcement. If the water is absorbed into the block, a suction bond is possible. However, there is one other consid- eration, the absorption rate of the block. A block with a high absorption rate is capable of rapidly taking too Figure 4 Figure 1 much water from the stucco mix. This The Wall dard concrete block has a smooth “dry out” could prevent the hydra- A block wall that is ready for the texture. This block does not provide tion of the cement and destroy the application of stucco is one that is much of a mechanical bond for the conditions necessary for establishing properly cured and carrying the ma- stucco, but it may still be considered a good suction bond. It could also jority of its intended load. The mortar an excellent base if a suction bond can cause additional shrinkage and crack- joints of the wall are not struck; they be developed. -
Natural Finishes Overview
Page 1 Natural Finishes Overview Natural plasters and finishes are a great alternative to the conventional finishing products that are available on the market. The ones that are just riddled with toxic chemicals! Most people don’t even realize the negative effects that these products have on their health. Indoor air pollution and toxic off gassing is a whole subject unto itself. But by using natural plasters and paints, you avoid the added toxicity of cement stucco, drywall, chemical paints, and the destructive industry that produces them all. Natural plasters and finishes can be applied to cob walls or even to drywall board! The majority of natural plasters and finishes are made from a combination of these simple ingredients: Clay, sand, straw, lime, kaolin clay, wheat paste, pigments, and water. Copyright 2015 - This Cob House LLC - All Rights Reserved Page 2 Plastering your cob home is like putting the icing on the cake. Once you have built your walls, built your roof, and installed the windows and doors then you can begin to plaster your building. The plaster will protect your walls from rain on the outside, and it will protect your cob walls from any crumbling off on the inside. A good foundation and a good roof overhang (a good hat and boots, as they say) will protect your cob home from most weather and rain. Some people decide not to plaster the exterior walls of their cob homes and they are fine in many cases, but you will still get deterioration. It is recommended to plaster your walls to protect them from driving rain and frost. -
Guidelines for Masonry and Stucco
CITY OF NEW ORLEANS Historic District Landmarks Commission Guidelines for Masonry and Stucco Masonry and Stucco Section Index Exterior masonry includes stone, brick and stucco. The HDLC reviews all modifications to exterior masonry and Historically, a building’s exterior masonry surface serves stucco. This section includes: both visual and functional purposes. Visually it is an • Types of Masonry and Stucco in New Orleans – Page important design feature that establishes the rhythm and 07-2 scale of a building. Historic exterior masonry: • Components of Masonry Walls and Piers – Page 07-3 • Acts as an important design feature, helping to define a building’s architectural style • Bricks, Concrete Masonry Units and Stone – Page 07-3 • Establishes a building’s scale, mass and proportion • Mortar – Page 07-4 • Adds pattern and casts shadows on wall surfaces • Stucco – Page 07-5 Functionally, historic exterior masonry typically acts as the • Typical Masonry and Stucco Problems – Page 07-6 principal load bearing system for the building, as well as its • Repointing Historic Masonry – Page 07-9 “skin”, shedding water and typically deflects sunlight and • Patching Stucco– Page 07-9 wind. Historic exterior masonry: • Masonry Cleaning – Page 07-10 • Acts as a principal element in the structural system • Masonry Coating and Painting – Page 07-11 • Establishes a weather-tight enclosure, providing protection from rain, wind and sun • Masonry and Stucco Guide and Review – Page 07-12 All applicants must obtain a Certificate of Appropriateness Using These Guidelines (CofA) as well as all necessary permits prior to proceeding The first step in using these Guidelines is to understand with any work. -
Stucco Over Concrete Or Masonry Walls 600-609
NWCB Technical Document 01/05 EXTERIOR SYSTEMS Stucco Over Concrete or Masonry Walls 600-609 The NWCB believes it is best to install a cement plaster over CMU or concrete walls without a traditional secondary Weather-Resistive Barrier (WRB) common on framed walls. Stucco can be applied to a concrete or masonry surface with or without a reinforcing metal base (lath). The bond and/or thickness of the cement plaster will determine the need for a lath. However, the WRB (building paper and house wraps) prevents the bond between the plaster (stuc- co) and the concrete. This coupled with the fact that attaching a lath and WRB to concrete usually result in tears or holes in the barrier and ultimately has proven not to provide the desired additional moisture protection. In fact, the addition of the WRB has led to some specific problems. With CMU walls it is difficult to attach the fasteners into the grout joint when they are covered with the WRB. In freeze-thaw conditions, moisture can get behind the WRB and freeze. The expansion of the freezing water can push the plaster off the concrete or CMU wall. This method of stucco over concrete and/or masonry without a secondary WRB has been used successfully for many years in the United States and has a longer record of success in Europe. Since this is not designed as a drain- age system, there is no need for a “weep screed” at the base of the wall. If a second layer moisture defense is desired, there are trowel, spray and roller applied secondary coatings that will work. -
Assembling the Baroque
CRESC Working Paper Series Working Paper No. 109 Assembling the Baroque John Law CRESC, Open University December 2011 Centre for Research on Socio-Cultural Change (CRESC) Faculty of Social Sciences, The Open University, Walton Hall, Milton Keynes, MK7 6AA, UK Tel: +44 (0)1908 654458 Fax: +44 (0)1908 654488 Email: [email protected] or [email protected] This paper may be downloaded from http://www.cresc.ac.uk/publications/assembling-the-baroque 1 Introduction2 The baroque is a foreign country. They do things differently there. But how do they sense them? What do they experience? And what might we learn from how they understood the world? How we might use the skills and the sensibilities of the baroque or the questions that it poses to help to work empirically in the contemporary social science and humanities. These are the questions I tackle in this piece. The baroque is contested and controversial. We will need to wrestle with the fact that there are many baroques. We will also need to recognise that for many in the contemporary world it is also unappealing. But the issue is not to recommend ‘the baroque’. The argument needs to be much more limited. It is that if whatever passes for ‘the baroque’ understood the world differently, then we may have something to learn if we look at what it did. Perhaps that distant place asked questions 1 This picture comes from Wikimedia Commons at http://upload.wikimedia.org/wikipedia/commons/4/4c/Ecstasy St Theresa SM della Vittoria.jpg 2 I am grateful to the participants at the workshop on ‘The Baroque as Empirical Sensibility’ June 11th-13th 2011 at the Manchester Museum in the University of Manchester who brought the topic of the baroque in the contemporary humanities and social science to life.