Fireproofing for Hydrocarbon Fire Exposures
Total Page:16
File Type:pdf, Size:1020Kb
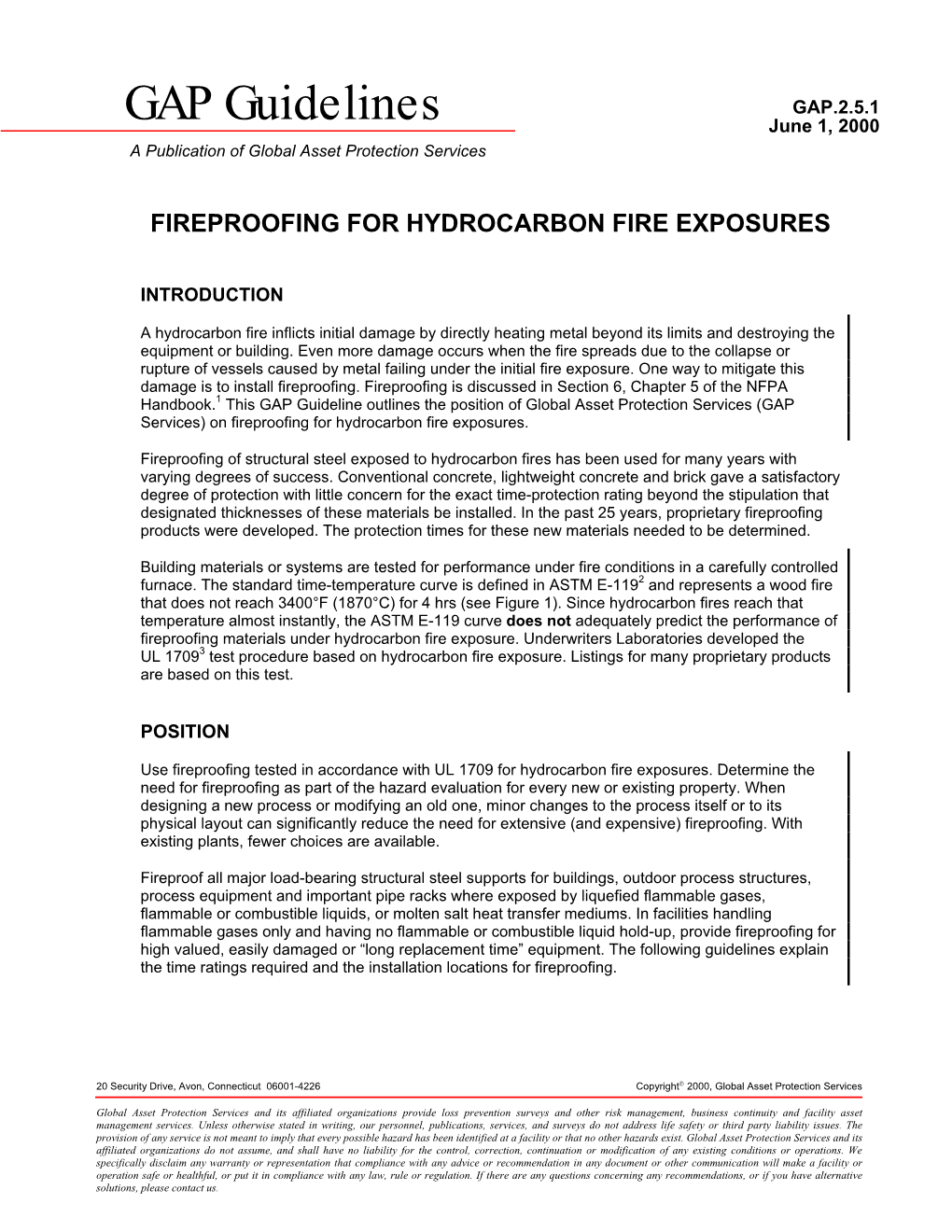
Load more
Recommended publications
-
Equipment and Caulking Installation Instructions Using Caulking Applicator Guns Photo 1A
Equipment and Caulking Installation Instructions Using Caulking Applicator Guns Photo 1a There are different types of caulking applicator guns available. The recommended procedure when using the different styles will be described in Sections A, B and C. Section D will then describe the recommended procedures to follow to install the caulk and finish the job. Section A Applying Caulk in Plastic and Cardboard Fiber Foil Wrapped Cartridges Photo 2a There are a variety of applicator caulking guns available to do firestopping. We recommend using a smooth rod style rather than the less expensive ratchet rod type. When dispensing caulk from a 29 ounce-size cartridge, we recommend using the rod tape gun with at least a 12:1 thrust ratio. The higher thrust ratio means less hand fatigue since the firestopping caulks are usually high viscous materials. It will also help when the product becomes stiffer in the colder temperatures. (12:1 ratio generates approximately 300 pound thrust) Photo 3a For manual single component cartridge applicator guns. Select the correct size manual drive frame-style cartridge gun for either the 10-ounce (300ml) or the larger 29-ounce (850 ml) plastic or cardboard fiber foil wrapped tube type. (see photo #1a) Using a utility knife cut off the end of the plastic tip/nozzle of the sealant tube to the desired opening size. The cut can be straight across (90º) or angled Photo 4a (45º). Cutting too small of an opening will restrict the flow of material and a smaller bead size than needed may result. The smaller opening will also require more triggering action (pressure) to move the material out of the tube.(see photo #2a) Using a screwdriver or other pointed utensil insert it into the plastic nozzle to puncture the membrane and allow the caulk material to flow. -
Fireproofing the Lungs Parts of the World, I Think, Should Be Watch- Ing Very Closely,” Says Wark, Particularly the Wildfire-Prone US West Coast
COPD outlook DAVID GRAY/GETTY DAVID Firefighters battle the bush fires that devastated Australia in 2019 and 2020. leads to faster lung-function decline even in people with otherwise healthy lungs. “Other Fireproofing the lungs parts of the world, I think, should be watch- ing very closely,” says Wark, particularly the wildfire-prone US west coast. People with conditions such as COPD are vulnerable “I find it rather unsettling that there are all these unknown things,” says Guy Marks, to wildfire pollution, but there is little advice on how a respiratory and environmental epidemiol- to keep safe. By Anna Nowogrodzki ogist at the University of New South Wales, Sydney. “The scale of the fire that we’ve just had is unprecedented. It represents to me a few days into the new year, an older prednisone on hand to ease her symptoms. clear turning point in our experience of the person came into John Hunter But still, she found breathing more and more consequences of climate change.” Hospital in Newcastle, Australia, difficult. wheezing and short of breath. Res- COPD is a common condition — it is the third Vulnerable lungs piratory physician Peter Wark was leading global cause of death. And people with Wark’s patient improved just by being in the Aon call at the time. He wasn’t surprised to respiratory conditions such as COPD are some air-conditioned hospital. “We really didn’t do see someone with respiratory problems — of the most vulnerable to particulate matter anything else,” he says. She was one of three or Australia was enduring an unprecedented and from air pollution and wildfires. -
Firestopping & Smoke Seals 1 General
SPECIFICATION SECTION 07 84 00 FIRESTOPPING & SMOKE SEALS 1 GENERAL 1.1 SECTION INCLUDES 1.1.1 Comply with Division 1, General Requirements and Documents referred to therein. 1.1.2 It is the intent of this section of the specifications to establish a single, competent source to be responsible for providing all labour, materials, products, equipment and services, to supply and install the firestopping and smoke seal work for the entire project. 1.1.3 SUMMARY A. Provide firestop systems consisting of a material, or combination of materials installed to retain the integrity of fire-rated construction by maintaining an effective barrier against the spread of flame, smoke, and/or hot gases through penetrations, blank openings, construction joints, or at perimeter fire containment in or adjacent to fire-rated barriers in accordance with the requirements of the Building Code for this project. B. Firestop systems shall be used in locations including, but not limited to, the following: 1. Penetrations through fire-resistance-rated floor and roof assemblies requiring protected openings including both empty openings and openings that contain penetrations. 2. Penetrations through fire-resistance-rated wall assemblies including both empty openings and openings that contain penetrations. 3. Membrane penetrations in fire-resistance-rated wall assemblies where items penetrate one side of the barrier. 4. Joints in fire-resistance-rated assemblies to allow independent movement. 5. Perimeter Fire Barrier System between a rated floor/roof and an exterior wall assembly. 6. Joints, through penetrations and membrane penetrations in Smoke Barriers and Smoke Partitions. 1.2 RELATED SECTIONS 1.2.1 Related Sections to this Section include: 1. -
TSB-A-07(1)S:2/07:Countryside Stove & Chimney of Burnt Hills,Petition No
New York State Department of Taxation and Finance Office of Tax Policy Analysis TSB-A-07(1)S Sales Tax Technical Services Division February 8, 2007 STATE OF NEW YORK COMMISSIONER OF TAXATION AND FINANCE ADVISORY OPINION PETITION NO. S040628D On June 28, 2004, the Department of Taxation and Finance received a Petition for Advisory Opinion from Countryside Stove and Chimney of Burnt Hills, 839 Saratoga Road, Burnt Hills, New York 12027. The issues raised by Petitioner, Countryside Stove and Chimney of Burnt Hills, are: 1. Whether installations of various wood, pellet, and gas burning heating appliances qualify as capital improvements to real property for New York State and local sales and use tax purposes. 2. Whether the installation of manufactured stone veneers on an interior or exterior wall qualifies as a capital improvement to real property for New York State and local sales and use tax purposes. Petitioner submits the following facts as the basis for this Advisory Opinion. Petitioner is a retail store selling and installing gas, wood, and pellet burning stoves that are placed on the floor on noncombustible material either purchased or provided by the customer. The gas stoves can be either directly vented from the stove out the side of the building using a wall thimble and a cap on the outside of the building or vented into the customer’s existing chimney by installing a stainless steel flexible liner in the chimney with its own rain cap. The wood and pellet burning stoves are also vented straight out the back of the stove and through a wall or chimney. -
Outlet Putty Pads Specifications Section 07840 - Firestopping Part 1 - General
OUTLET PUTTY PADS SPECIFICATIONS SECTION 07840 - FIRESTOPPING PART 1 - GENERAL 1.1 RELATED DOCUMENTS A. Drawings and general provisions of the Contract, including General and Supplementary Conditions and Division 1 Specification Sections, apply to this Section. 1.2 SUMMARY A. This Section includes: Through penetration firestops and smoke-stops for all fire-rated bearing and non- bearing wall and floor assemblies, both blank (empty) and those accommodating penetrating items such as cables, conduits, pipes, ducts, etc. not covered in Division 15 and 16 Sections. Membrane penetration protection for fire-rated walls. Architectural/Construction joint firestops within walls, floors, or the intersection of floors to exterior walls, or the intersection of top of walls to ceilings. Top of wall firestopping in all fire-rated partitions. Top of wall and construction joint smoke-stopping in all smoke partitions. B. Related Sections include the following: Division 15 Sections specifying duct and pipe penetrations and firestopping for those penetrations. Division 16 Sections specifying cable and conduit penetrations and firestopping for those penetrations. 1.3 REFERENCES: A. American Society For Testing and Materials Standards (ASTM): ASTM E84: Standard Test Method For Surface Burning Characteristics of Building Materials. ASTM E814: Standard Test Method For Fire Tests of Through-Penetration Sales and support: (800) 397-8791 | www.soundproofingcompany.com | [email protected] Firestops. ASTM E1966: Test Method For Resistance of Building Joint Systems. ASTM E1399: Test Method for Cyclic Movement and Measuring Minimum and Maximum Joint Width. ASTM E119: Methods of Fire Tests of Building Construction and Materials. B. Underwriters Laboratories Inc.: UL 263: Fire Tests of Building Construction and Materials. -
The Future Is Now Kitchen Exhaust Technology Advances Follow Design Innovation
OCTOBER/NOVEMBER 2007 xhaust e itchen K The Future Is Now Kitchen exhaust technology advances follow design innovation. By Joel Berkowitz Partner/Vice President, Fireproofing Corporation of America of income and is a real attraction to • Precipitator cells that produce an companies that would want to lease electrified field that ionizes grease office space and individuals seeking particles and bonds them to a filter high-rise dwellings. cell. The problem has always been the kitchen exhaust ductwork and vents. • Water wash canopies that automati- Kitchen exhaust systems, with their cally rinse grease from the interior insulated risers coming up through portions of an exhaust system every the building, occupy valuable square night. footage on every floor of the prop- erty, taking up thousands of dollars in These aren’t glimpses of the future otherwise rentable space every year. — it is technology available now. The new technology for kitchen Landlords and restaurateurs alike Left to right: Partners Glenn exhaust systems is a boon to prop- can take advantage of these systems, Catalano, author Joel Berkowitz and erty owners and managers. No lon- and build more creative kitchens Anthony Scotto. ger is there a need to place ugly in more locations than ever before. black exhaust risers up the side of the They are high-tech and cutting-edge ntil recent times, build- building. And forget relying on hot- and have the ability to revolutionize ing design and engineering dog carts outside on the sidewalk — the industry. technology placed limits on U today’s technology allows for street- Many of these technologies have where commercial kitchens could be level kitchens in multi-story build- been around for 10, 20, even 30 years located within a facility. -
Firestopping Application Guide
Firestopping Application Guide www.grabberman.com VERSION 4.0 NOTES Table of Contents Page Table of Contents Table Table of Contents .........................................................................................................................................................................................i General Certificate of Conformance ...............................................................................................................................................................iii LEEDS Information United States LEEDs .....................................................................................................................................................................v Canadian LEEDs .........................................................................................................................................................................vii Product Data Sheets GrabberGard EFC .........................................................................................................................................................................ix GrabberGard IFC ........................................................................................................................................................................ xiii GrabberGard EFS .......................................................................................................................................................................xvii Material Data Sheets GrabberGard EFC ........................................................................................................................................................................xxi -
Factory-Welded Grease Duct Systems 3
1 XXX XXX FACTORY-WELDED GREASE DUCT SYSTEMS 3 General Information Product Overview GeneralXXX Notification Grease duct is an ETL listed, single wall construction The purpose of the NFPA 96 Standard is to reduce the potential fire hazard of cooking operations, independent made from 430 stainless steel. Duct diameters range from of the type of cooking equipment used and whether used in public or private facilities. Please refer to Chapter 7 8” to 24”, with multiple lengths and accessories available. of the NFPA 96 Standard, Exhaust Duct Systems, for Grease duct is ideal for use in kitchen ventilation applica- detailed description of duct requirements and design. tions and is available as a stand-alone system or part of All dimensions are shown in American Standard (feet and inches). a fully integrated package. Grease duct is pre-engineered for optimum performance for exhaust fans and hoods. Grease duct is ETL listed to Standard UL-1978; duct does not have to be welded in the field. Table of Contents 4 5 Table of Contents Standards & Key Words* & References 01 General Information 10 Grease Duct Components UL- 1978 Test Standard for Safety Grease Ducts. -Product Overview -Factory Installed Riser -General Notification 11 -Field Installed Riser NFPA- 96 Standard for Ventilation Control and Fire Protection of Commercial Cooking Operations. 12 -Straight Duct 02 Table of Contents 13 -Adjustable Straight Duct ETL- Edison Testing Laboratory, http://www.intertek-etlsemko.com. The ETL listed Mark is the legal equivalent of the UL Listed and 14 -Table 9- Dynamic Loss Coefficient Table CSA Listed Marks throughout the United States and Canada. -
Summaries of Center for Fire Research Grants and In-House Programs - 1984
4 NAT'L INST. OF STAND & TECH NBS REFERENCE PUBLICATIONS AlllOb 0371LD NBSIR 85-3136 Summaries of Center for Fire Research Grants and In-House Prog rams - 19 8 Sonya M. Cherry, Editor U S. DEPARTMENT OF COMMERCE National Bureau of Standards National Engineering Laboratory Center for Fire Research Gaithersburg, MD 20899 April 1985 Final Report U S. DEPARTMENT OF COMMERCE -ATIONAL BUREAU OF STANDARDS 100 ,U56 85-3136 1985 NATIONAL BUREAU OF STANDARDS LIBRARY NBSIR 85-3136 SUMMARIES OF CENTER FOR FIRE RESEARCH GRANTS AND IN-HOUSE PROGRAMS - 1984 Sonya M. Cherry, Editor U S. DEPARTMENT OF COMMERCE National Bureau of Standards National Engineering Laboratory Center for Fire Research Gaithersburg, MD 20899 April 1985 Final Report U.S. DEPARTMENT OF COMMERCE, Malcolm Baldrige, Secretary NATIONAL BUREAU OF STANDARDS. Ernest Ambler. Director TABLE OF CONTENTS Page ABSTRACT 1 CENTER FOR FIRE RESEARCH PROGRAMS Ad Hoc Working Group of Mathematical Fire Modeling 2 Compartment Fire Modeling 3 Exploratory Fire Research 8 Fire Growth and Extinction 14 Fire Performance and Validation 20 Fire Safety Performance 24 Fire Toxicology 28 Furnishings Flammability 34 Smoke Hazard 37 GRANTS AND CONTRACTS American Institute of Architects A Computerized Model for the Simulation of General Fire Emergency Evacuations 40 Brown University Soot Dynamics in Flames 43 Brown University Study of Effects of Material Properties on Flaming Combustion of Charring Fuels 47 California Institute of Technology Experimental Study of Environment and Heat Transfer in a Room Fire 51 Case Western Reserve University Experimental and Analytical Study of Fire Sprinkler Scaling Laws 55 Case Western Reserve University Flame Spread and Spread Limits 58 l Page Clemson University Ternary Reactions Among Polymer Substrate- Organohalogen-Ant imony Oxides in the Condensed Phase Under Pyrolytic, Oxidative and Flaming Conditions 60 Colorado School of Mines Characterization of Aerosols from Fires 63 Factory Mutual Research Corp. -
The Hose Stream Test
The Hose Stream Test What is the Hose Stream Test? The hose stream test is an integral part of many fire testing standards. ASTM E 119, ASTM E 814/UL 1479, and ASTM E 1966/UL 2079 are all standards that affect the firestopping industry. All three standards require a hose stream test. What's the history of the Hose Stream? In the late 1890's, cast & wrought iron were commonly used in construction. Unlike steel, they failed in a brittle manner when heated in a fire, creating a risk for firefighters who were in the wrong place at the wrong time. As a result, the hose stream was created to test the integrity of these support members (columns/beams). In 1918, the first edition of ASTM standard E 119--then numbered C19, Standard Test Method for Fire Tests of Building Construction and Materials-- included a hose stream test to measure a material's integrity. Because ASTM E 119 includes the hose stream test as acceptance criteria of assemblies, it is considered applicable to fire stops as well. What is the intent of the Hose Stream? The hose stream serves as an indicator for two important attributes: 1) the integrity of a fire stop or assembly during fire exposure and 2) the overall reliability of the material to perform its intended function. For firestop systems it is important to obtain an indication of performance integrity. A firestop system that loses its integrity can allow the spread of fire by creating passages for flames and hot gases to propagate from one side of a rated assembly to another. -
Assembly and User Instructions Fireplace Insert, Lotus H370 Petite
Assembly and User Instructions Fireplace Insert, Lotus H370 Petite Version 3, 04/10-2017 Introduction Congratulations on your new Lotus Fireplace Insert We hope and believe that it will give you many warm hours. But before you may truly benefit from your investment, you should read this guide thoroughly. It provides some specific advice as to how you will benefit the most from your fireplace insert – now, as well as in the years to come. This is why this guide would be worth while keeping, like all other directions for use. Lotus may look back on a long tradition, making our first productions back in 1979. Our production is now running in Langeskov, and exported to many European markets. Lotus products are made to a fine Danish tradition, serving its owners faithfully for years. So, once again congratulations on your new Lotus fireplace insert – making for a warm and cosy beginning of an all new home life for you. Fireplace Insert Assembly Before your new fireplace insert will be ready to exude warmth and a cosy atmosphere, you should read these lines thoroughly, reviewing the requirements for the assembly and the environment. Also, reference is made to all local regulations, including those referring to national and European standards, to be met in the installation of your fireplace insert. The hole size required for assembly appears from the leaflet material as well as the line drawings on the last page of these instructions. A: Holes used for fastening the insert to the base. B: Set screws for adjustment of the insert in relation to the base. -
Trafalgar Fyrewrap
® FYREWRAP Lightweight Fireproofing for Ducts The Trafalgar fire stopping range includes: Sealant | Pillows | Mortar | FR Batts FR Collars | FR Access Panels | Pipe Wraps FyreWrap Duct Wrap | FR Downlight Covers Intumescent Dampers | Fire Door Hardware Fire Rated Board and Systems | Cable Coating FYREBOX for multiple and mixed services fyrewrap.com.au V1.0419 Product FYREWRAP Lightweight Fireproofing for Ducts Overview Unifrax and Trafalgar have partnered in Australia to bring you FyreWrap® duct fireproofing systems. Simply put, this is the only way to go when it comes to providing passive fire protection for ductwork in commercial buildings. FyreWrap comes ready to use as a foil finished roll to wrap around the ductwork of all configurations. It eliminates the need for messy spray applied materials, which are known to require hours of masking to avoid resulting overspray. FyreWrap results in fast, simple, cost effective and clean fireproofing while providing pleasing aesthetics. FyreWrap is beneficial for project work and planning, as it allows for other trades to be working in close vicinity to the contractors doing the duct wrapping and with careful planning, large quantities of the duct fireproofing can be completed off-site. This is a revolution in duct fireproofing so insist on FyreWrap lightweight fireproofing for your next project. Fast | Clean | Easy fyrewrap.com.au 1800 888 714 Page 2 of 5 Product FYREWRAP Lightweight Fireproofing for Ducts Overview APPLICATION: FyreWrap is used to provide 2 and 3 hour protection for fire rated ductwork in commercial buildings where fire rating and FRL requirements are necessary. FyreWrap can be pre-wrapped around ducts before they are installed, or retrofitted over existing ductwork.