Supervised Learning Classification for Dross Prediction in Ductile Iron
Total Page:16
File Type:pdf, Size:1020Kb
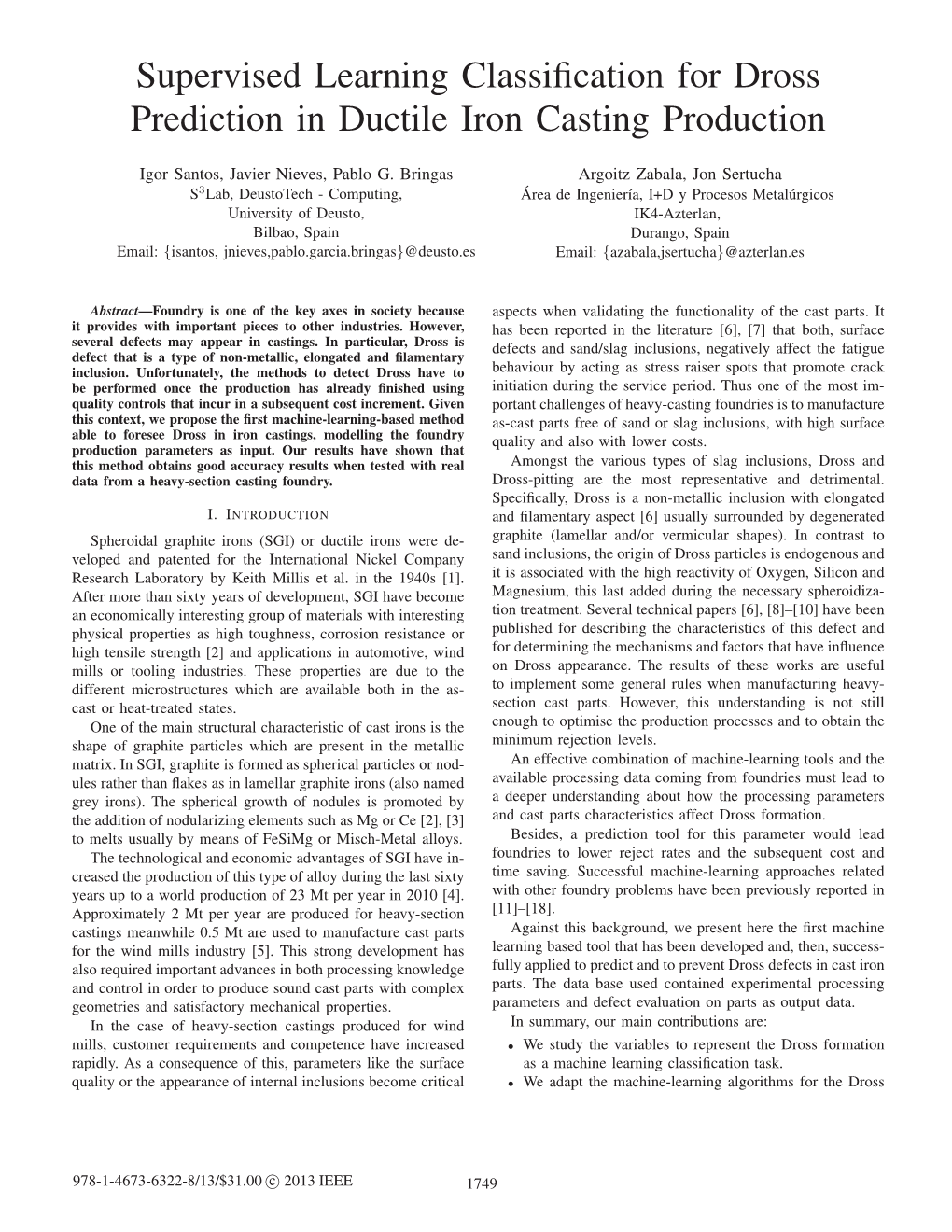
Load more
Recommended publications
-
Metals in the Bible: Silver (Part 1)
The Testimony, August 2004 329 times of restitution of all things” (Acts 3:21, AV). the last verse of his song does look forward to In contrast, the song of Moses in chapter 32 pre- the time of blessing when the Gentiles will re- dicts future rebellion and consequent punish- joice with God’s people and atonement will have ment that would occur before the final glory been provided for both land and people (v. 43). would be attained by the nation. Nevertheless, (To be continued) New feature Metals in the Bible 3. Silver (Part 1) Peter Hemingray In 1996 and 1997 The Testimony published two two-part articles under the title, “Metals in the Bible”, in which we looked at iron and copper.1 We considered the ancient technology of iron, and how this knowledge helps illuminate the Biblical references to it. In particular, we saw how the introduction of iron during the period of the conquest affected the Israelites, who had to overcome superior technology through the power of God. For copper (or brass, as the AV terms it) the ancient metalworking methods were illuminated with illustrations from Timnah in Palestine, and we argued for the symbology of copper in the Bible being primarily that of strength, and only rarely that of the strength of sin. The intention was to complete these studies on metals of the Bible by considering silver, then gold. This we have now done in two further two-part articles to be published in this and the coming months, God willing. E WILL CONTINUE the theme of il- • examine the references to refining and cruci- lustrating the Biblical passages about bles in the light of our knowledge of ancient Wmetals with descriptions of the ancient metalworking practices metalworking techniques, as we consider silver, • look at the few references to lead in the Bible, the next metal up in Nebuchadnezzar’s image often associated with silver for reasons we after the iron and brass already considered. -
DROSS in DUCTILE IRON by Hans Roedter, Sorelmetal Technical Services
98 DROSS IN DUCTILE IRON by Hans Roedter, Sorelmetal Technical Services WHAT IS “DROSS ”? magnesium with other elements. Dross also Dross is a reaction product which is formed from occurs in the form of long stringers instead of Mg treatment and during subsequent reoxidation concentrated “slag like” areas. When it occurs in of Mg rejected from the molten metal before it this string like form it acts like cracks or flake solidifies. It is therefore just another word for a graphite in the structure and so fatigue strength specific type of slag (reaction product). and impact strength of the material are lowered considerably. The reaction binds magnesium with sulphur, oxygen and silicon and forms continuously. This “dross” is light weight and so it will generally be found in the upper surfaces and under cores, but it can be entrained throughout the metal as well, especially with colder pouring tempera - tures. It is very difficult to completely avoid the reaction of magnesium with these other elements, since we need magnesium to form nodules. We are always confronted with the problem of dross in the production of Ductile Iron. WHAT IS PROMOTING “DROSS ” AND WHAT CAN BE DONE TO KEEP THE “DROSS ” OUT OF THE CASTING ? Since “dross” is always connected with magnesium, it is necessary to keep the magnesium level as low as possible. Good inoculation practice with some late inoculation in conjunction with sufficient magnesium will When looking at “dross” in the microscope you produce nice round small nodules. See will almost always find flake graphite in Suggestion Sheet 76. -
Lecture 8: Casting Technology
Lecture 8: Casting Technology MT321: Principles of Materials Processing Lecture 8:Casting Technology 1 Design of Gating Systems Functions of a gating system: To deliver liquid metal to mould cavity within a short time. To minimise turbulent flow. To keep dross and/or inclusion particles from entering mould cavity. MT321: Principles of Materials Processing Lecture 8:Casting Technology 2 MT321: Principles of Materials Processing Lecture 8:Casting Technology 3 How to deliver liquid metal fast? By using a sufficient large cross sectional area; By using multiple runners. How to minimise turbulent flow? By using tapered sprue and runners. By bottom filling of the liquid into the mould cavity. By regulating the change of cross sectional area of the channels according to fluid dynamics principles. MT321: Principles of Materials Processing Lecture 8:Casting Technology 4 How to keep dross and inclusion particles from entering mould cavity? By using dross traps. By using filters. MT321: Principles of Materials Processing Lecture 8:Casting Technology 5 Various types of ceramic filters that may be inserted into the gating systems of metal castings MT321: Principles of Materials Processing Lecture 8:Casting Technology 6 MT321: Principles of Materials Processing Lecture 8:Casting Technology 7 Solidification Shrinkage The liquid of most metals and alloys shrinks during solidification. Solidification shrinkage (percent) of some common engineering metals and alloys MT321: Principles of Materials Processing Lecture 8:Casting Technology 8 Two considerations must be made in designing a casting mould, due to the solidification shrinkage: A riser, which is a reservoir of liquid, is needed to compensate for the shrinkage of the whole casting. -
Download European Recycling Services Brochure
ALPHA Reclamation Services Brochure Maximize Your Metal Recovery Return macdermidalpha.com August, 2020 Europe ASSEMBLY SOLUTIONS ALPHA Metal Reclamation Services Minimise Your Environmental Liability, Maximise the Value of Your Waste Materials Environmental legislation specifies the importance of proper waste management, recovery and recycling techniques to reduce pressure on resources and improve their use. Due to these requirements and considering that metal waste is recyclable, it is now essential for you to have a reliable and efficient recycler. Alpha, a brand of MacDermid Alpha Electronics Solutions, offers a safe and efficient recycling service which helps companies to meet their environmental and legislative requirements and at the same time, maximize the value of their waste stream. • Alpha’s experienced staff are dedicated to reclamation efforts and will maximize the amount of metal processed from your reclaim material. • Reclaim material sent to Alpha is carefully processed and no material that has a metal content is sent to a landfill. • Alpha provides tough, sealable and disposable metal recycling buckets and drums. • All shipments are lot traceable and certification can be provided on request. • Alpha’s Certified Recycling Partner Program enables our customers to work with local partners operating throughout Europe who are legally authorized to collect waste from electronics assembly processes. 2 ALPHA Metal Reclamation Services Recycling Waste Streams Wave Solder Dross and Hot Air Solder Level (HASL Dross) – Oxidation particles that form on the surface of molten metal (solder). This material can be skimmed off and recycled. Solder Paste – Paste that has expired its shelf life or been removed from the stencil Empty Paste Jars and Cartridges Solder Bar and Wire – Expired solder bar and wire Pot Dump and Contaminated Solder Bath – From wave and selective soldering machines. -
Foundry Industry SOQ
STATEMENT OF QUALIFICATIONS Foundry Industry SOQ TRCcompanies.com Foundry Industry SOQ About TRC The world is advancing. We’re advancing how it gets planned and engineered. TRC is a global consulting firm providing environmentally advanced and technology‐powered solutions for industry and government. From solid waste, pipelines to power plants, roadways to reservoirs, schoolyards to security solutions, clients look to TRC for breakthrough thinking backed by the innovative follow‐ through of a 50‐year industry leader. The demands and challenges in industry and government are growing every day. TRC is your partner in providing breakthrough solutions that navigate the evolving market and regulatory environment, while providing dependable, safe service to our customers. We provide end‐to‐end solutions for environmental management. Throughout the decades, the company has been a leader in setting industry standards and establishing innovative program models. TRC was the first company to conduct a major indoor air study related to outdoor air quality standards. We also developed innovative measurements standards for fugitive emissions and ventilation standards for schools and hospitals in the 1960s; managed the monitoring program and sampled for pollutants at EPA’s Love Canal Project in the 1970s; developed the basis for many EPA air and hazardous waste regulations in the 1980s; pioneered guaranteed fixed‐price remediation in the 1990s; and earned an ENERGY STAR Partner of the Year Award for outstanding energy efficiency program services provided to the New York State Energy Research and Development Authority in the 2000s. We are proud to have developed scientific and engineering methodologies that are used in the environmental business today—helping to balance environmental challenges with economic growth. -
Analysis of Stainless Steel Waste Products Generated During Laser Cutting in Nitrogen Atmosphere
Article Analysis of Stainless Steel Waste Products Generated during Laser Cutting in Nitrogen Atmosphere Maciej Zubko 1,2,* , Jan Loskot 2 , Paweł Swiec´ 1 , Krystian Prusik 1 and Zbigniew Janikowski 3 1 Institute of Materials Engineering, University of Silesia in Katowice, 75 Pułku Piechoty 1a, 41-500 Chorzów, Poland; [email protected] (P.S.);´ [email protected] (K.P.) 2 Department of Physics, University of Hradec Králové, Rokitanského 62, 500-03 Hradec Králové, Czech Republic; [email protected] 3 “Silver” PPHU, ul. Rymera 4, 44-270 Rybnik, Poland; [email protected] * Correspondence: [email protected]; Tel.: +48-32-3497-509; Fax: +48-32-3497-594 Received: 22 October 2020; Accepted: 23 November 2020; Published: 25 November 2020 Abstract: Laser cutting technology is one of the basic approaches used for thermal processing of parts fabricated from almost all engineering materials. Various types of lasers are utilized in the industry with different attendant gases such as nitrogen or argon. When the laser beam interacts with a metal surface, the area underneath is heated to the melting point. This liquid or vaporized metal is ejected from the kerf area to the surrounding atmosphere by attendant gas and becomes undesirable waste in the form of powder. In the presented work, the X-ray diffraction, scanning electron microscopy, electron backscatter diffraction, transmission electron microscopy, and energy-dispersive X-ray spectroscopy methods were used to analyze AISI 304 stainless steel, which was cut by a semiconductor fiber laser, and the waste powder generated during the laser cutting process. The results suggest that this waste material may be reused for industrial applications such as additive manufacturing. -
ARCH 1764 Under the Microscope 250 Years of Brown's Material Past
ARCH 1764 Under the Microscope 250 Years of Brown’s Material Past Prof. Clyde Briant Office hours Wednesday 4:00-6:00 pm 220 Barus and Holley Prof. Brett Kaufman Office Hours: Tuesdays, 2:00-4:00 pm Rhode Island Hall 007 TA Susan Herringer This presentation and the images within are for educational purposes only, and are not to be distributed Metallurgical Slags Metallurgical Slags • Usually consist of SiO2 plus oxides such as CaO, Al2O3, P2O5, MnO, MgO2. • Slag is a mixture of phases. • Current technology depends on type of furnace but overall goal is to control the chemistry of the final metal through control of the chemistry of slag. • Great emphasis today on reuse of slag: added to cements, reused in additional slags, various filler materials. • https://www.youtube.com/watch?v=hBqhGHf zQFQ - https://www.youtube.com/watch?v=hBqhGHf zQFQ • http://science.howstuffworks.com/blast- furnace-videos-playlist.htm - http://science.howstuffworks.com/blast- furnace-videos-playlist.htm Archaeological Slag and Dross Slag is the byproduct of metallurgical activity resulting from the processing of metallic ores and is usually composed of a glassy mass of ore detritus that contains vitreous gangue, solid dross, and unsmelted metallic components. http://antiquity.ac.uk/projgall/ben-yosef330/images/figure6big.jpg 25 meter high slag heap from Late Roman period in Cyprus Types of slag research involves reverse engineering to study: ►much research into slag has focused on analysis of phase microstructure and chemical composition in order to deduce whether this byproduct resulted from primary smelting, secondary smelting (blooming), crucible smelting, or melting activities. -
Operator's Ready Reference
Operator’s Ready Reference We Bring Intelligence to the Table.TM VictorThermalDynamics.com What is plasma? Plasma is a gas heated to an extremely high temperature and ionized so that it becomes electrically conductive. Plasma arc cutting uses the plasma as an electrode to transfer a electrical arc to the work piece. The heat of the arc melts the work piece and the force of the plasma and shield gases blow away the molten metal to cut the work piece. Different metals react differently to plasma cutting. Carbon steel can be oxidized, and is usually cut with a plasma containing oxygen to take advantage of the exothermic process. Higher levels of oxygen in the plasma result in higher heat and higher rates of oxidation. The result is a faster and cleaner cut. Stainless steel and aluminum are not subject to rapid oxidation and depend entirely on the plasma’s heat for the cutting process. Because plasma produces much higher heat than the oxygen-fuel cutting process, plasma can cut stainless steel and aluminum quickly and cleanly. Choosing a plasma process Thermal Dynamics systems offer a variety of plasma cutting processes for precision and general purpose cutting. Ultra-Cut systems offer precision cutting as well as conventional cut options. Auto-Cut O2 systems offer high speed oxygen cutting, precision non-ferrous and conventional cut options. Auto-Cut systems offer conventional mild steel and precision non-ferrous options. Process Used For Advantages Plasma Shield Mild Steel Precision 50-300 Amps O Air Weld Ready Cut Surface 2 and High Speed -
Remanded Smelting Wastes
REMANDED SMELTING WASTES Technical Background Document Office of Solid Waste U.S. Environmental Protection Agency December 1995 TABLE OF CONTENTS INTRODUCTION .........................................................................................................................1 1.0 BACKGROUND ...............................................................................................................1 1.1 Exclusion of Mining Wastes from RCRA Regulation ..........................................3 1.2 Development of a Narrower Interpretation of the Mining Waste Exclusion .........3 1.3 Reversion to the 1980 Interpretation of the Mining Waste Exclusion ..................4 1.4 Court Challenges to the Broad Interpretation .......................................................4 1.5 Court Challenges to the Re-Listing ......................................................................4 2.0 INDUSTRY OVERVIEW ...................................................................................................5 2.1 Description of Facilities Generating Wastes ........................................................5 2.2 Description of Industrial Processes and Waste Management .............................6 3.0 BASIS FOR THE NO-LIST DECISION ...........................................................................13 4.0 SUMMARY OF FINDINGS ..............................................................................................14 BIBLIOGRAPHY APPENDICES A. Rissmann Trip Report B. Magma and Cyprus Trip Report C. Letter from Benito Garcia, -
Ae Signals During Laser Cutting of Different Steel Sheet Thicknesses
AE SIGNALS DURING LASER CUTTING OF DIFFERENT STEEL SHEET THICKNESSES TOMAŽ KEK and JANEZ GRUM University of Ljubljana, Faculty of Mechanical Engineering, Askerceva 6, 1000 Ljubljana, Slovenia Abstract Laser cutting is an established industrial method for cutting of various steels in the produc- tion process. However, each laser cut poses a question of quality estimation during and immedi- ately after the laser cutting process. The capturing and evaluating of acoustic emission (AE) sig- nals reveals a great potential for the laser cut quality estimation. This paper presents the results of the AE bursts measurement after the laser cutting of steel sheets of various thicknesses using oxygen or nitrogen as cutting gas. The method of the laser cut quality estimation described here was applied to the austenitic stainless steel, mild steel, and structural steel. The laser cut quality, which is related to the size of the dross and the waviness of the cut surface can be successfully forecast based on the captured AE signals. Keywords: Burst acoustic emission, laser cutting, PZT sensor, dross, unalloyed steel, austenitic stainless steel Introduction The price of the equipment and operation costs are considerable when it comes to laser sys- tems, but the higher cost is well justified by exceedingly faster treatment processes as well as good dimensional accuracy and repeatability. Laser cutting quality depends mainly on the selec- tion of the process parameters that were established with trial and error method. Changes in the beam quality, gas flow and surface of materials can lead to reduced laser cut quality. In order to eliminate these weaknesses, the monitoring and adequate adjustments of the treatment need to be ensured. -
Aluminum Foundry Products
ASM Handbook, Volume 2: Properties and Selection: Nonferrous Alloys and Special-Purpose Materials Copyright © 1990 ASM International® ASM Handbook Committee, p 123-151 All rights reserved. DOI: 10.1361/asmhba0001061 www.asminternational.org Aluminum Foundry Products Revised by A. Kearney, Avery Kearney & Company Elwin L. Rooy, Aluminum Company of America ALUMINUM CASTING ALLOYS are wrought alloys. Aluminum casting alloys cast aluminum alloys are grouped according the most versatile of all common foundry must contain, in addition to strengthening to composition limits registered with the alloys and generally have the highest cast- elements, sufficient amounts of eutectic- Aluminum Association (see Table 3 in the ability ratings. As casting materials, alumi- forming elements (usually silicon) in order article "Alloy and Temper Designation Sys- num alloys have the following favorable to have adequate fluidity to feed the shrink- tems for Aluminum and Aluminum Al- characteristics: age that occurs in all but the simplest cast- loys"). Comprehensive listings are also • Good fluidity for filling thin sections ings. maintained by general procurement specifi- The phase behavior of aluminum-silicon • Low melting point relative to those re- cations issued through government agencies compositions (Fig. 1) provides a simple quired for many other metals (federal, military, and so on) and by techni- • Rapid heat transfer from the molten alu- eutectic-forming system, which makes pos- cal societies such as the American Society sible the commercial viability of most high- minum to the mold, providing shorter for Testing and Materials and the Society of casting cycles volume aluminum casting. Silicon contents, Automotive Engineers (see Table 1 for ex- • Hydrogen is the only gas with apprecia- ranging from about 4% to the eutectic level amples). -
Pollution Prevention Progress for 23 Washington Electroplating Facilities: an Industry Sector Report
Pollution Prevention Progress for 23 Washington Electroplating Facilities: An Industry Sector Report Publication No. 96-426 August 1996 printed on recycled paper For a copy of this document, please contact: Department of Ecology Publications P.O. Box 47600 Olympia, WA 98504-7600 Please include your street address for UPS delivery If you have questions or would like more information about this report, please contact the Electroplating Sector Team member nearest you: Doug Jayne Spokane (509) 456-6171 Michael Johnson Olympia (360) 407-6338 Elliott Zimmermann Bellevue (206) 649-7072 Miles Kuntz Olympia (360) 407-6748 The Department of Ecology is an equal opportunity agency and does not discriminate on the basis of race, creed, color, disability, age, religion, national origin, sex, marital status, disabled veteran’s status, Vietnam Era veteran’s status or sexual orientation. If you have special accommodation needs or require this document in alternative format, please contact the Hazardous Waste and Toxics Reduction Program at (360) 407-6700 (Voice) or (360) 407-6006 (TDD). Ecology’s telecommunications device for the deaf (TDD) numbers in the regional offices are: Central Region (509) 454-7673 Northwest Region (206) 649-4259 Eastern Region (509) 458-2055 Southwest Region (360) 407-6306 Pollution Prevention Progress for 23 Washington Electroplating Facilities: An Industry Sector Report Prepared by: Washington State Department of Ecology Hazardous Waste and Toxics Reduction Program Publication No. 96-426 August 1996 Printed on Recycled Paper