Master Thesis Energy Science
Total Page:16
File Type:pdf, Size:1020Kb
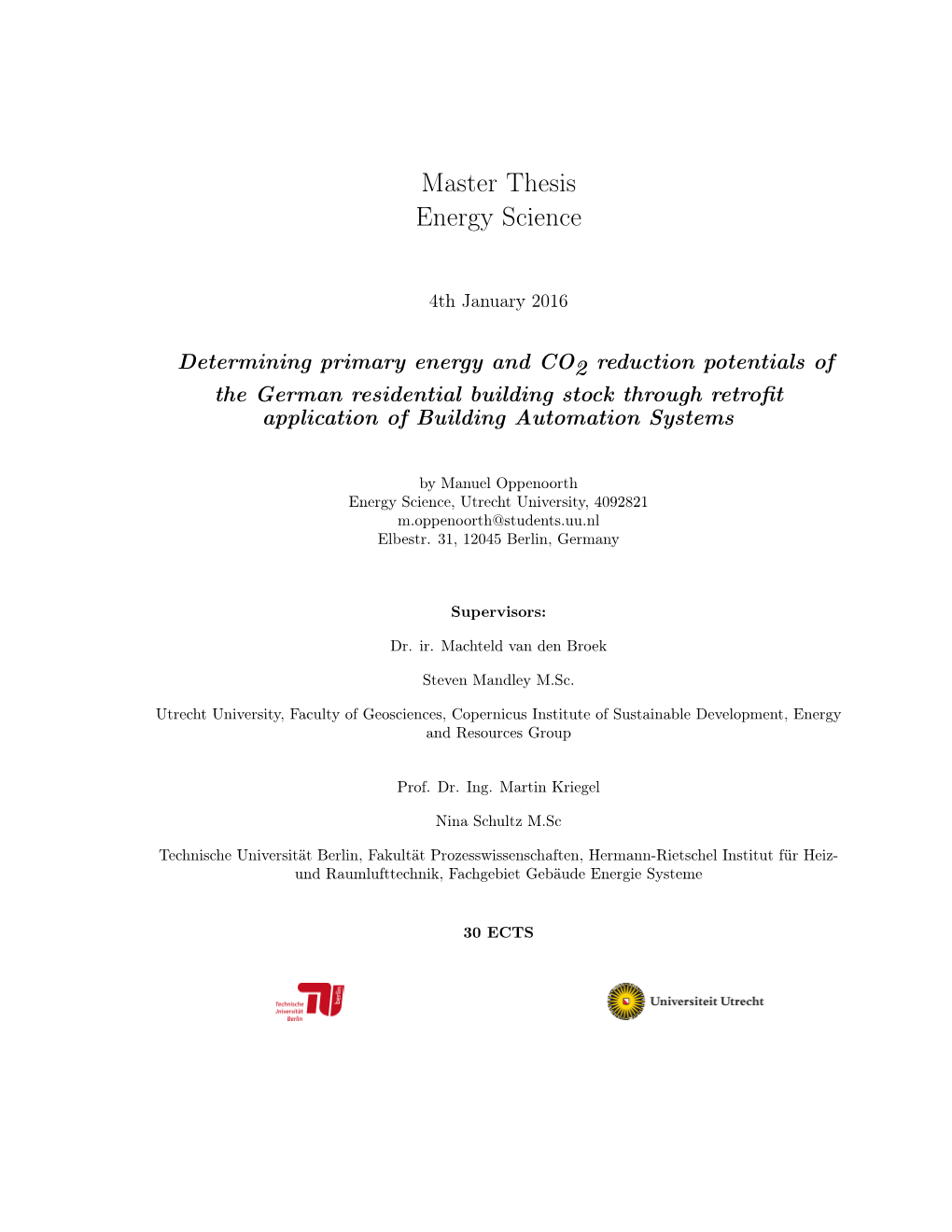
Load more
Recommended publications
-
Panther Auto Corner Left: the Band Marches on to Victory
PA NTHER PRIDE Volume 11, I ssue #2 TABLE OF CONTENTS Band's Victory in M aryville Page 1: Bands Victory in Maryville The marching band has had a fantastic Middle School Sports season! At the first competition in Carrollton they Middle School Football had a high music score but a low marching score and Page 2: Clubs and Activities flipped the scores in Cameron. On October 26th they Art Club had a competition in Maryville where they placed Elementary News second in their class 2A, only four points away from Blast Off Into the School Year first. The band had the third-highest music score over all the bands that performed. The band was very Stacking It Up excited to beat some very good bands for their last Books for First Grade marching competition of the year and are getting Character Assembly ready for concert season. Page 3: Current Events Florida Man Drumline this year had a good season. They Hong Kong Protests only had two competitions compared to the three that Creative Minds the whole band had. They played Blazed Blues and Lobster Walk for their performance. The drumline Photography Basics placed fourth in Carrollton and didn?t place in Kara Claypole, Mr.Dunker, and Ysee Chorot celebrate their "Song of the Sea" Cameron. second place trophy as they marched at Maryville for the "Bernard's Poem" Northwest Homecoming Parade. Page 4: Panther Auto Corner Left: The band marches on to victory. Ask Anonymous Entertainment Corbin's Destroy... Page 5: Joker Is a Marvel New Music Releases Page 6: New Video Game Releases Page 7: Horoscopes Page 8: November Menu Polo M iddle School Sports M iddle School Football Stats Board - By: M r. -
MASSJCL CLASSICS DAY 2020 STREET CERTAMEN a Round on a Wide Distribution of Popular Culture Written by Jinwoo Kim T1: Bearing It
MASSJCL CLASSICS DAY 2020 STREET CERTAMEN A round on a wide distribution of popular culture Written by Jinwoo Kim T1: Bearing its name from a despicable Roman deity that was uninvited to the marriage of Peleus and Thetis, what application is known for its countless servers, including a namesake “Certaminatores” server? DISCORD B1: Bearing its name from a mythological group that lived in the Caucasus Mountains, what company is owned by the current richest man in the world? AMAZON B2: Bearing its name from the first mythological woman created by Zeus, what company offers a streaming service for music and podcasts? PANDORA T2: What American name, derived from a Latin adjective meaning “small”, is shared by the 10th pick of the 2010 NBA draft associated with the nickname “Pandemic P”, an actor that played as Brian O’Conner in Fast and Furious, and another actor that is famous for playing Ant-Man? PAUL B1: Give the last name of this other Paul, a Celtics superstar who was infamously dragged away in a wheelchair during game 1 of the 2008 NBA finals. PIERCE B2: What last name is shared by the husband of Paul George’s ex-girlfriend Callie Rivers and the favorite basketball player of the Youtube star FlightReacts, as well as by a popular Indian dish? CURRY T3: The quotes, “I will reduce illiteracy, that is my first goal. And my second goal will be to help the poor” and “My pledge is that I’ll be pilot, and I’ll help” were said by students in what country? One student declared that “When I grow up, I will be army and save” this country, as another claimed that he desired nothing else but “to sacrifice my own life” for this country. -
Night at the Lab Students Travel to Colby for Science-Related Competition
TRICK OR TREAT Q AND A Hays High School DECA helps Professional Choreographer community by volunteering during the holds Q & A with Trick or Treat So Others Can Eat Event Chamber Singers Page 6 Page 12 THE VOL. 94 NO. 2 • HAYS HIGH SCHOOL UIDO 2300 E. 13th ST. • HAYS, KAN. 67601 G www.hayshighguidon.comOCTOBER 17, 2019 N FUTURE PREPARATION RESPONSIBLE STUDENTS Students participate in mock interviews Teachers encourage students By Nikka Vuong to be more stable financially Hays High Guidon expected emergencies and your Most jobs will require an in- By Michaela Austin Hays High Guidon long-term savings goals,” Per- terview for the employer to sonal Finance instructor Silas know who they are hiring. The Almost all people have strug- Hibbs said. interview process can consist of gled with money management According to “Foundations many different steps. at some point of their lives. in Personal Finance” by Dave In order to practice this pro- Whether it is attempting to in- Ramsey, people need to know cess and to learn their strengths crease their income or simply their “money personality.” Does and weaknesses when being in- not knowing how to manage money frustrate you? Is money terviewed, all seniors were re- their finances, money manage- everything, or is it not every- quired to do a mock interview on ment is a common issue among thing? You will need to analyze Sept. 18 or 19 for their English high school students. your money habits. classes. Some people do not know how According to Ramsey, a good “We do panel presentations much money they should be way to always make sure a per- first, where we have the volun- saving, and some do not save son is handling his or her money teers come in and talk to the any money at all, but taking a well is by following Ramsey’s students about how they should ALEXIS PFANNENSTIEL / The Guidon Personal Finance class can help Five Foundations. -
Travis Scott Is Back with Blockbuster New Single & Music Video “Highest in the Room”
TRAVIS SCOTT IS BACK WITH BLOCKBUSTER NEW SINGLE & MUSIC VIDEO “HIGHEST IN THE ROOM” JOINS FORCES WITH POSTMATES FOR THE “TRAVIS SCOTT COLLECTION” ON-DEMAND (October 4, 2019 – Los Angeles, CA) Six-time GRAMMY® Award-nominated superstar, fashion trendsetter, and 21st century disruptor Travis Scott returns with his anxiously awaited new single “Highest In The Room” today. Get it HERE via Epic Records. This marks the modern icon’s first new music since the arrival of his double-platinum history-making 2018 #1 opus, ASTROWORLD. Once again, “Highest In The Room” sees Travis take flight. He vaults from hypnotic highly quotable verses towards an intoxicating, irresistible, and infectious refrain—“I’m the highest in the room. Hope I make it out of here”–on par with his biggest anthems. It sees him level up to new heights altogether. The blockbuster music video expands his world. It opens on Travis topping a towering skyscraper as he swallows the camera. Overseeing a sweeping skyline, the star walks the exposed metal framework of the building before battling cyborgs intercut with sexy and stirring sci-fi visuals. It’s unlike anything he’s ever dropped. Experience it now. Watch HERE. In celebration of “Highest In The Room,” Travis teamed up with Postmates to introduce the “Travis Scott Collection.” Fans may order from his personal favorite restaurants across Houston and L.A. when they’re “the hungriest in the room.” Selections include Jamba Juice, Shake Shack, and Chipotle—each boast a menu curated by the legend himself. Most importantly, “Highest In The Room” sets the stage for the impending arrival of his highly anticipated fourth full-length and the most anticipated record of the year. -
Most Requested Songs of 2020
Top 200 Most Requested Songs Based on millions of requests made through the DJ Intelligence music request system at weddings & parties in 2020 RANK ARTIST SONG 1 Whitney Houston I Wanna Dance With Somebody (Who Loves Me) 2 Mark Ronson Feat. Bruno Mars Uptown Funk 3 Cupid Cupid Shuffle 4 Journey Don't Stop Believin' 5 Neil Diamond Sweet Caroline (Good Times Never Seemed So Good) 6 Usher Feat. Ludacris & Lil' Jon Yeah 7 Walk The Moon Shut Up And Dance 8 V.I.C. Wobble 9 Earth, Wind & Fire September 10 Justin Timberlake Can't Stop The Feeling! 11 Garth Brooks Friends In Low Places 12 DJ Casper Cha Cha Slide 13 ABBA Dancing Queen 14 Bruno Mars 24k Magic 15 Outkast Hey Ya! 16 Black Eyed Peas I Gotta Feeling 17 Kenny Loggins Footloose 18 Bon Jovi Livin' On A Prayer 19 AC/DC You Shook Me All Night Long 20 Spice Girls Wannabe 21 Chris Stapleton Tennessee Whiskey 22 Backstreet Boys Everybody (Backstreet's Back) 23 Bruno Mars Marry You 24 Miley Cyrus Party In The U.S.A. 25 Van Morrison Brown Eyed Girl 26 B-52's Love Shack 27 Killers Mr. Brightside 28 Def Leppard Pour Some Sugar On Me 29 Dan + Shay Speechless 30 Flo Rida Feat. T-Pain Low 31 Sir Mix-A-Lot Baby Got Back 32 Montell Jordan This Is How We Do It 33 Isley Brothers Shout 34 Ed Sheeran Thinking Out Loud 35 Luke Combs Beautiful Crazy 36 Ed Sheeran Perfect 37 Nelly Hot In Herre 38 Marvin Gaye & Tammi Terrell Ain't No Mountain High Enough 39 Taylor Swift Shake It Off 40 'N Sync Bye Bye Bye 41 Lil Nas X Feat. -
Songs by Title
16,341 (11-2020) (Title-Artist) Songs by Title 16,341 (11-2020) (Title-Artist) Title Artist Title Artist (I Wanna Be) Your Adams, Bryan (Medley) Little Ole Cuddy, Shawn Underwear Wine Drinker Me & (Medley) 70's Estefan, Gloria Welcome Home & 'Moment' (Part 3) Walk Right Back (Medley) Abba 2017 De Toppers, The (Medley) Maggie May Stewart, Rod (Medley) Are You Jackson, Alan & Hot Legs & Da Ya Washed In The Blood Think I'm Sexy & I'll Fly Away (Medley) Pure Love De Toppers, The (Medley) Beatles Darin, Bobby (Medley) Queen (Part De Toppers, The (Live Remix) 2) (Medley) Bohemian Queen (Medley) Rhythm Is Estefan, Gloria & Rhapsody & Killer Gonna Get You & 1- Miami Sound Queen & The March 2-3 Machine Of The Black Queen (Medley) Rick Astley De Toppers, The (Live) (Medley) Secrets Mud (Medley) Burning Survivor That You Keep & Cat Heart & Eye Of The Crept In & Tiger Feet Tiger (Down 3 (Medley) Stand By Wynette, Tammy Semitones) Your Man & D-I-V-O- (Medley) Charley English, Michael R-C-E Pride (Medley) Stars Stars On 45 (Medley) Elton John De Toppers, The Sisters (Andrews (Medley) Full Monty (Duets) Williams, Sisters) Robbie & Tom Jones (Medley) Tainted Pussycat Dolls (Medley) Generation Dalida Love + Where Did 78 (French) Our Love Go (Medley) George De Toppers, The (Medley) Teddy Bear Richard, Cliff Michael, Wham (Live) & Too Much (Medley) Give Me Benson, George (Medley) Trini Lopez De Toppers, The The Night & Never (Live) Give Up On A Good (Medley) We Love De Toppers, The Thing The 90 S (Medley) Gold & Only Spandau Ballet (Medley) Y.M.C.A. -
Bullets High Five
DUC REDAKTION Hofweg 61a · D-22085 Hamburg T 040 - 369 059 0 WEEK 03 [email protected] · www.trendcharts.de 09.01.2020 Approved for publication on Tuesday, 14.01.2020 THIS LAST WEEKS IN PEAK WEEK WEEK CHARTS ARTIST TITLE LABEL/DISTRIBUTOR POSITION 01 01 04 Tyga Ayy Macarena Last Kings/Columbia/Sony 01 02 04 10 Travis Scott Highest In The Room Epic/Sony 02 03 02 07 Tyga x YG x Santana Mamacita Last Kings/Columbia/Sony 02 04 03 10 DJ ClimeX Ft. Michael Rankiao & Öz Fuego ClimeX Entertainment 01 05 08 09 The Black Eyed Peas x J Balvin RITMO (Bad Boys For Life) BEP/Epic/Sony 05 06 12 08 Apache 207 Wieso Tust Du Dir Das An? TwoSides/Four Music/Sony 06 07 18 04 > The Cratez, Bausa & Maxwell Skifahren RBK/Gold League/Sony 07 08 05 09 Bausa & Zuna Biturbo Downbeat/WMD/Warner 04 09 07 04 Tory Lanez Ft. T-Pain Jerry Sprunger Mad Love/Interscope/UMI/Universal 06 10 21 09 Fat Joe x Cardi B x Anuel AA Yes RNG/Empire 09 11 NEW Nimo & Hava Kein Schlaf 385i/Urban/VEC/Universal 11 12 14 02 Koffee Ft. Gunna W Columbia/Sony 12 13 11 04 Fard ZAPPZARAPP Ruhrpott Elite/Urban/VEC/Universal 11 14 10 08 RIN x Bausa Keine Liebe Division/Gold League/Sony 10 15 13 06 The Game Ft. Anderson. Paak Stainless eOne/SPV 13 16 19 02 Nicky Jam Ft. Anuel AA Whine Up Sony Latin/Sony 16 17 22 07 Maluma Ft. Ricky Martin No Se Me Quita Sony Latin/Sony 17 18 NEW Ardian Bujupi Eine Nacht Columbia/Sony 18 19 NEW DaBaby BOP South Coast/Interscope/UMI/Universal 19 20 09 03 Stormzy Ft. -
Top 40 Singles Top 40 Albums Dance Monkey in the Air Six60 (3) Beerbongs & Bentleys 1 Tones and I 21 L.A.B
06 January 2020 CHART #2224 Top 40 Singles Top 40 Albums Dance Monkey In The Air Six60 (3) beerbongs & bentleys 1 Tones And I 21 L.A.B. 1 Six60 21 Post Malone Last week 3 / 22 weeks Platinum x2 / BadBatch/SonyMus... Last week - / 1 weeks LOOP/Border Last week 3 / 8 weeks Platinum / Massive/Universal Last week 33 / 88 weeks Platinum x4 / Republic/Universal Roxanne Senorita Fine Line Free Spirit 2 Arizona Zervas 22 Shawn Mendes And Camila Cabello 2 Harry Styles 22 Khalid Last week 4 / 10 weeks Platinum / ArizonaZervas/SonyM... Last week 38 / 28 weeks Platinum x2 / Island/Universal/So... Last week 1 / 3 weeks Columbia/SonyMusic Last week 32 / 39 weeks Platinum / RightHand/RCA/Sony... Glitter Good As Hell (Remix) No. 6 Collaborations Project Complete Greatest Hits 3 BENEE 23 Lizzo feat. Ariana Grande 3 Ed Sheeran 23 The Eagles Last week 8 / 6 weeks Gold / Republic/Universal Last week - / 16 weeks Platinum / NiceLife/Atlantic/Warn... Last week 5 / 25 weeks Platinum x2 / Asylum/Warner Last week 29 / 63 weeks Platinum x2 / Elektra/Warner Circles Someone You Loved WHEN WE ALL FALL ASLEEP, WH... don't smile at me 4 Post Malone 24 Lewis Capaldi 4 Billie Eilish 24 Billie Eilish Last week 9 / 18 weeks Platinum / Republic/Universal Last week 35 / 37 weeks Platinum x3 / Vertigo/Capitol/Univ... Last week 6 / 40 weeks Platinum x2 / Darkroom/Interscop... Last week 30 / 104 weeks Platinum x2 / Darkroom/Interscop... Memories Before You Go JACKBOYS Special Edition, Pt. 1 5 Maroon 5 25 Lewis Capaldi 5 JACKBOYS And Travis Scott 25 Fat Freddy's Drop Last week 10 / 15 weeks Platinum / 222/Interscope/Univer.. -
ARIA URBAN SINGLES CHART WEEK COMMENCING 11 MAY, 2020 TW LW TI HP TITLE Artist CERTIFIED COMPANY CAT NO
CHART KEY <G> GOLD 35000 UNITS <P> PLATINUM 70000 UNITS TW THIS WEEK LW LAST WEEK TI TIMES IN HP HIGH POSITION ARIA URBAN SINGLES CHART WEEK COMMENCING 11 MAY, 2020 TW LW TI HP TITLE Artist CERTIFIED COMPANY CAT NO. 1 1 23 1 BLINDING LIGHTS The Weeknd <P>2 REP/UMA 00602508575167 2 2 5 2 TOOSIE SLIDE Drake REP/UMA 0899150 3 10 7 3 SAVAGE Megan Thee Stallion WAR QM-CE3-20-00097 4 5 17 2 SAY SO Doja Cat <P> RCA/SME G010004182077K 5 4 10 3 DEATH BED Powfu <P> SME G010004262147O 6 3 2 3 THE SCOTTS The Scotts (Travis Scott & Kid Cudi) UMA/SME G010004380997L 7 6 3 6 ROCKSTAR DaBaby Feat. Roddy Ricch INR/UMA US-UM7-20-07941 8 8 9 8 BOSS B**CH Doja Cat ATL/WAR US-AT2-19-07355 9 7 2 7 RIGHTEOUS Juice WRLD INR/UMA 0712865 10 12 36 1 CIRCLES Post Malone <P>4 REP/UMA US-UM7-19-15699 11 11 12 6 BLUEBERRY FAYGO Lil Mosey INR/UMA 877692 12 9 18 2 THE BOX Roddy Ricch <P>2 ATL/WAR US-AT2-19-06978 13 13 10 10 WHATS POPPIN Jack Harlow WAR US-AT2-20-00162 14 20 7 14 ROVER S1mba Feat. DTG PLG/WAR GB-CUW-19-00128 15 15 13 9 KNOW YOUR WORTH Khalid x Disclosure <G> RCA/SME G010004214490R 16 14 91 2 SICKO MODE Travis Scott & Drake <P>7 UMA/SME G0100039765104 17 19 25 1 ROXANNE Arizona Zervas <P>3 COL/SME G010004196719S 18 17 10 8 CITY OF ANGELS 24KGOLDN <G> COL/SME G010004178581V 19 16 31 2 HIGHEST IN THE ROOM Travis Scott <P>2 EPI/SME G0100041677460 20 21 16 2 GODZILLA Eminem Feat. -
The Top Dance Songs of 2019 1
th 45 Year THE TOP DANCE SONGS OF 2019 1. HIGHER LOVE – Kygo & Whitney Houston (RCA) 124/104 51. YOU LITTLE BEAUTY – Fisher (Astralwerks/Capitol) 124 2. PIECE OF YOUR HEART – Meduza ft. Goodboys (Capitol) 124 52. GO SLOW – Gorgon City & Kaskade ft. ROMEO (Capitol) 124 3. I DON’T CARE – Ed Sheeran & Justin Bieber (Atlantic) 122/102 53. SUMMER DAYS – Martin Garrix ft. Macklemore & Patrick Stump (RCA) 126/114 4. SUCKER – Jonas Brothers (Republic) 126/138 54. ON MY WAY – Alan Walker, Sabrina Carpenter & Farruko (RCA) 120/85 5. BAD GUY – Billie Eilish (Interscope) 126/135 55. HEY LOOK MA, I MADE IT – Panic! At The Disco (Atlantic) 124/108 6. CON CALMA – Daddy Yankee & Katy Perry ft. Snow (El Cartel/Capitol) 109/94 56. FIND U AGAIN – Mark Ronson & Camila Cabello (RCA) 124/104 7. SENORITA – Shawn Mendes & Camila Cabello (Republic) 124/117 57. BREAK UP WITH YOUR GIRLFRIEND, I’M BORED – Ariana Grande (Republic) 124/85 8. 7 RINGS/THANK U NEXT – Ariana Grande (Republic) 126/70, 124/107 58. SELFISH – Dimitri Vegas & Like Mike ft. Era Istrefi (Arista) 126/96 9. DANCING WITH A STRANGER – Sam Smith & Normani (Capitol) 123/103 59. 365 – Zedd & Katy Perry (Interscope) 124/98 10. DANCE MONKEY – Tones and I (Elektra) 122/98 60. BEAUTIFUL PEOPLE – Ed Sheeran ft. Khalid (Atlantic) 120/93 11. OLD TOWN ROAD – Lil Nas X ft. Billy Ray Cyrus (Columbia) 124/70 61. QUE CALOR – Major Lazer ft. J Balvin & El Alfa (Mad Decent) 126 12. SO CLOSE – NOTD & Felix Jaehn ft. Georgia Ku & Captain Cuts (Republic) 126 62. -
Access the Best in Music. a Digital Version of Every Issue, Featuring: Cover Stories
Bulletin YOUR DAILY ENTERTAINMENT NEWS UPDATE JUNE 10, 2020 Page 1 of 27 INSIDE Recording Academy Announces • AEG Layoffs Hit 9 Rule Changes to Its Grammy as Company Looks to Reschedule Awards & Nominations Process Coachella, Global Tours to Next Year BY PAUL GREIN • iHeartMedia Extends Staff The Recording Academy announced nine key changes lar problem for rap and hip-hop artists, who tend to Furloughs Another to its awards and nominations process on Wednesday release more songs than artists in other genres. They 90 Days morning (June 10). These changes were ratified at the can hit the 30-song cap with just two mixtapes. “In • Latin American semiannual Trustees Meeting in May. They take effect [some] genres, specifically hip-hop and rap, their Delivery App Rappi immediately and will be in place for the upcoming mode of development is record and release. We felt it Launches Livestream 63nd annual Grammy Awards. Billboard discussed the was unfairly punishing artists who are prolifically re- Offer With Manuel changes with Harvey Mason, Jr., Chair & Interim leasing material early in their careers. We do not want Medrano President/CEO of the Recording Academy. to exclude any artist based on a rule that was specifi- • Virtual Concert 1. In best new artist, the Academy dropped the cally affecting one genre more than the other.” Startup Wave Raises rule that an artist may have released no more than Mason remembers times that artists were excluded $30M From Backers 30 tracks prior to the start of the current eligibil- because of this rule. “I know that there have been Including Scooter ity year: The Academy had sought to quantify its times we’ve had to go back and do the math and look Braun, Twitch’s Kevin Lin definition of best new artist, but found that it’s almost at the number of releases and you’re calculating ‘does impossible to come up with numbers that are fair in this count?’ and ‘does that count?’…[This change] • Gotye, INXS, Tina every situation. -
Billboard Hot 100 Singles
Disc Jockey News Top 100 US Singles January 23, 2020 Page 1 TW LW Title Artist Peak Weeks TW LW Title Artist Peak Weeks 1 1 The Box Roddy Ricch 1 6 26 24 Adore You Harry Styles 24 6 2 new Life Is Good Highest Debut Future and Drake 2 1 27 35 High Fashion Roddy Ricch and Mustard 27 3 3 3 Circles Post Malone 1 20 28 23 Panini Lil Nas X 5 30 4 4 Memories Maroon 5 2 17 29 new You Should Be Sad Halsey 29 1 5 10 Lose You To Love Me Selena Gomez 1 13 30 new Rare Selena Gomez 30 1 6 6 Someone You Loved Lewis Capaldi 1 36 31 21 Hot Young Thug and Gunna 11 22 7 5 10000 Hours Dan featuring Shay and Justin Bieber 4 15 32 39 Blinding Lights The Weeknd 11 7 8 7 Dance Monkey Tones and I 7 15 33 20 Truth Hurts Lizzo 1 37 9 9 Roxanne Arizona Zervas 4 11 34 25 Only Human Jonas Brothers 18 30 10 2 Yummy Justin Bieber 2 2 35 28 Bandit Juice WRLD and Youngboy Never 10 15 11 8 Good As Hell Lizzo 3 21 36 27 One Man Band Old Dominion 20 21 12 12 Bop Dababy 11 16 37 31 Even Though I’m Leaving Luke Combs 11 20 13 11 Ballin’ Mustard and Roddy Ricch 11 26 38 32 I Don’t Care Ed Sheeran and Justin Bieber 2 33 14 14 Don’t Start Now Dua Lipa 14 11 39 41 Suicidal Ynw Melly 39 8 15 13 Highest In The Room Travis Scott 1 15 40 33 Bad Guy Billie Eilish 1 42 16 new Sum 2 Prove Lil Baby 16 1 41 38 Falling Trevor Daniel 31 9 17 new Good News Mac Miller 17 1 42 34 Sucker Jonas Brothers 1 41 18 17 Heartless The Weeknd 1 8 43 30 Futsal Shuffle 2020 Lil Uzi Vert 5 5 19 15 No Guidance Chris Brown and Drake 5 32 44 44 My Oh My Camila Cabello and Dababy 44 6 20 16 Trampoline Shaed