The 5 Major Technologies
Total Page:16
File Type:pdf, Size:1020Kb
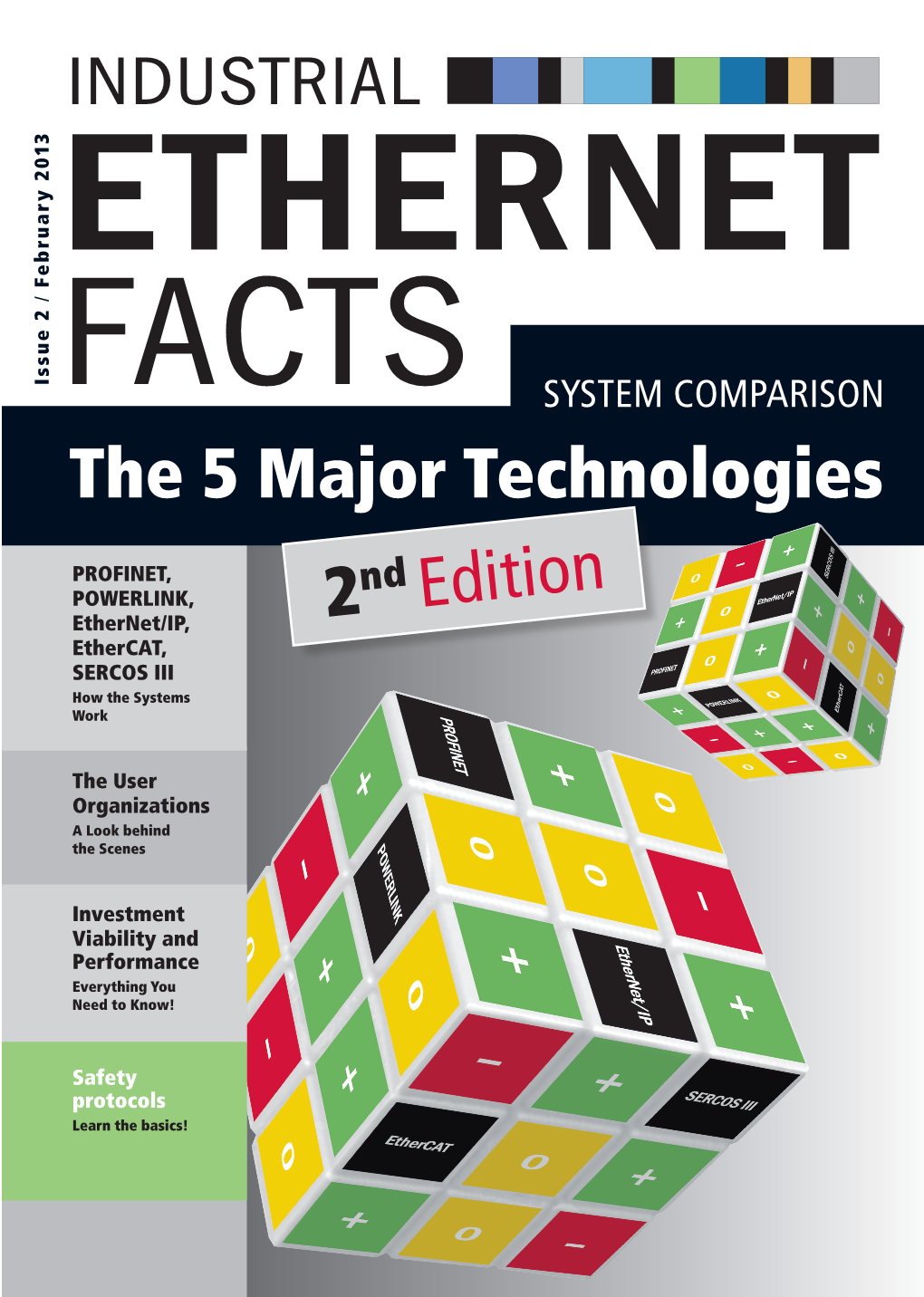
Load more
Recommended publications
-
On Ttethernet for Integrated Fault-Tolerant Spacecraft Networks
On TTEthernet for Integrated Fault-Tolerant Spacecraft Networks Andrew Loveless∗ NASA Johnson Space Center, Houston, TX, 77058 There has recently been a push for adopting integrated modular avionics (IMA) princi- ples in designing spacecraft architectures. This consolidation of multiple vehicle functions to shared computing platforms can significantly reduce spacecraft cost, weight, and de- sign complexity. Ethernet technology is attractive for inclusion in more integrated avionic systems due to its high speed, flexibility, and the availability of inexpensive commercial off-the-shelf (COTS) components. Furthermore, Ethernet can be augmented with a variety of quality of service (QoS) enhancements that enable its use for transmitting critical data. TTEthernet introduces a decentralized clock synchronization paradigm enabling the use of time-triggered Ethernet messaging appropriate for hard real-time applications. TTEther- net can also provide two forms of event-driven communication, therefore accommodating the full spectrum of traffic criticality levels required in IMA architectures. This paper explores the application of TTEthernet technology to future IMA spacecraft architectures as part of the Avionics and Software (A&S) project chartered by NASA's Advanced Ex- ploration Systems (AES) program. Nomenclature A&S = Avionics and Software Project AA2 = Ascent Abort 2 AES = Advanced Exploration Systems Program ANTARES = Advanced NASA Technology Architecture for Exploration Studies API = Application Program Interface ARM = Asteroid Redirect Mission -
Introduction to Real-Time Ethernet II
the EXTENSION JULY–AUGUST A Technical Supplement to Control Network Volume 5 Issue 4 © 2004 Contemporary Control Systems, Inc. Introduction to Real-Time Ethernet II By Paula Doyle, a doctoral researcher with the Circuits and Systems Research Centre at the University of Limerick in Ireland INTRODUCTION IEEE 1588 defines two separate types of clocks: In “Real-Time Ethernet I”, we introduced the basic ordinary and boundary. Boundary clocks (BC) are concepts of Ethernet’s capacity to deliver a real-time employed in devices such as hubs or switches—where (RT) communication system. “Real-Time Ethernet II” more than one PTP communication path (port) exists. introduces some of the RT solutions available to Ordinary clocks exist in devices having a single port— e.g., normal network devices. Each BC port can act as industry today*: PROFInet, EtherCAT and ETHERNET Powerlink. It also provides an introduction to a single a master or ordinary clock in its own segment. standard, IEEE 1588 that is growing in popularity PTP is for networks that support multicasting but amongst RT Ethernet developers to provide sub- keep multicasts within a subnet and where each local microsecond synchronization accuracy of distributed clock fulfills exacting requirements. The grandmaster clocks over Ethernet. clock (GMC) is the best clock in the system—with the best inherent stability, accuracy, resolution, etc. * EtherNet/IP is included in the full article available at defined by the standard [2]. The Best Master Clock http://www.ccontrols.com/pdf/volume5n4.pdf Algorithm (BMC), run by every live node, determines IEEE 1588 clock quality. Within each subnet, the BMC determines the master clock; in a single-subnet system the master IEEE 1588 [1] specifies “A protocol to synchronize is the GMC. -
Canopen Documentation Release 1.2.2.Dev41+Gff8b5ca
canopen Documentation Release 1.2.2.dev41+gff8b5ca Christian Sandberg Sep 13, 2021 Contents 1 Network and nodes 3 2 Object Dictionary 11 3 Network management (NMT) 17 4 Service Data Object (SDO) 19 5 Process Data Object (PDO) 27 6 Synchronization Object (SYNC) 33 7 Emergency Object (EMCY) 35 8 Time Stamp Object (TIME) 37 9 Layer Setting Services (LSS) 39 10 Integration with existing code 43 11 Device profiles 45 Index 51 i ii canopen Documentation, Release 1.2.2.dev41+gff8b5ca This package provides support for interacting with a network of CANopen nodes. Note: Most of the documentation here is directly stolen from the CANopen Wikipedia page. This documentation is a work in progress. Feedback and revisions are most welcome! CANopen is a communication protocol and device profile specification for embedded systems used in automation. In terms of the OSI model, CANopen implements the layers above and including the network layer. The CANopen standard consists of an addressing scheme, several small communication protocols and an application layer defined by a device profile. The communication protocols have support for network management, device monitoring and communication between nodes, including a simple transport layer for message segmentation/desegmentation. Easiest way to install is to use pip: $ pip install canopen Contents 1 canopen Documentation, Release 1.2.2.dev41+gff8b5ca 2 Contents CHAPTER 1 Network and nodes The canopen.Network represents a collection of nodes connected to the same CAN bus. This handles the sending and receiving of messages and dispatches messages to the nodes it knows about. Each node is represented using the canopen.RemoteNode or canopen.LocalNode class. -
PROFINET for Network Geeks
PROFINET for Network Geeks (and those who want to be) Introduction PROFINET is an open Industrial Ethernet standard. It is a communication protocol that exchanges data between automation controllers and devices. With over 25 million installed nodes (as of 2018), PROFINET is one of the most widely used Industrial Ethernet standards worldwide. But even though millions of users are familiar with PROFINET, not all users understand how it works. This white paper starts with a brief overview of Ethernet and the 7-layer ISO-OSI model. Then, it describes how PROFINET’s 3 communication channels fit in the model: TCP/IP and UDP/IP, Real-Time (RT), and Isochronous Real-Time (IRT). 1 Ethernet The transition from using 4-20 mA analog signals for I/O communication to digital fieldbuses provided the benefits of reduced wiring, access to network data, and robust diagnostics. The later transition from digital fieldbuses to Ethernet was also similarly a shift to a more modern technology. Ethernet incorporated and improved upon the benefits of fieldbuses. Ethernet is ubiquitous and PROFINET uses standard Ethernet. Ethernet gives PROFINET the ability to provide faster updates, more bandwidth, larger messages, an unlimited address space, and even more diagnostic capabilities. Also, as commercial Ethernet evolves, PROFINET can take advantage of these physical layer improvements. Figure 1 ISO-OSI Model The ISO-OSI Model Ethernet-based communications can be represented by a seven-layer model: the ISO/OSI Reference Model. The model generically describes the means and methods used to transmit data. Each layer has a specific name and function, as shown in Figure 1. -
EM133 Multifunction Meter
EM133 Multifunction Meter CANopen Communications Protocol Reference Guide BG0592 Rev. A1 Every effort has been made to ensure that the material herein is complete and accurate. However, the manufacturer is not responsible for any mistakes in printing or faulty instructions contained in this book. Notification of any errors or misprints will be received with appreciation. For further information regarding a particular installation, operation or maintenance of equipment, contact the manufacturer or your local representative or distributor. REVISION HISTORY A1 February Release 2016 AnyBus® is a registered trademark of HMS Industrial Networks AB. 2 Table of Contents 1 GENERAL........................................................................................................... 5 2 CANOPEN PROTOCOL IMPLEMENTATION .................................................... 6 2.1 CANOPEN ELECTRONIC DATA SHEET (EDS) FILE ..................................................................... 6 2.2 CANOPEN VERSION ................................................................................................................. 6 2.3 BAUD RATES ........................................................................................................................... 6 2.4 NODE ADDRESS ....................................................................................................................... 6 2.5 INPUT AND OUTPUT BUFFERS ................................................................................................... 6 2.6 EXTENDED DIAGNOSTIC -
Ethercat – Ultra-Fast Communication Standard
EtherCAT – ultra-fast communication standard In 2003, Beckhoff introduces its EtherCAT tech- In 2007, EtherCAT is adopted as an IEC standard, EtherCAT: nology into the market. The EtherCAT Technology underscoring how open the system is. To this Group (ETG) is formed, supported initially by day, the specification remains unchanged; it has global standard 33 founder members. The ETG goes on to stan- only been extended and compatibility has been dardize and maintain the technology. The group is retained. As a result, devices from the early years, the largest fieldbus user organization in the world, even from as far back as 2003, are still interopera- for real-time with more than 5000 members (as of 2019) cur- ble with today’s devices in the same networks. rently. In 2005, the Safety over EtherCAT protocol Another milestone is achieved in 2016 Ethernet from the is rolled out, expanding the EtherCAT specification with EtherCAT P, which introduces the ability to to enable safe transmission of safety-relevant carry power (2 x 24 V) on a standard Cat.5 cable field to the I/Os control data. The low-footprint protocol uses a alongside EtherCAT data. This paves the way for so-called Black Channel, making it completely machines without control cabinets. independent of the communication system used. The launch of EtherCAT G/G10 in 2018 in- How it works The key functional principle of EtherCAT lies in how its nodes process Ethernet frames: each node reads the data addressed to it and writes its data back to Flexible topology the frame all while the frame is An EtherCAT network can sup- moving downstream. -
Configuring PROFINET
CHAPTER9 Configuring PROFINET This chapter describes how to configure the PROFINET feature on the Cisco IE 3000 switch. • Understanding PROFINET, page 9-1 • Configuring PROFINET, page 9-4 • Displaying the PROFINET Configuration, page 9-5 • Troubleshooting PROFINET, page 9-5 Understanding PROFINET PROFINET is the PROFIBUS International (PI) open Industrial Ethernet Standard that uses TCP/IP and IT standards for automation control. PROFINET is particularly useful for industrial automation systems and process control networks, in which motion control and precision control of instrumentation and test equipment are important. It emphasizes data exchange and defines communication paths to meet speed requirements. PROFINET communication is scalable on three levels: • Normal non-real-time communication uses TCP/IP and enables bus cycle times of approximately 100 ms. • Real-time communication enables cycle times of approximately 10 ms. • Isochronous real-time communication enables cycle times of approximately 1 ms. Note The switch does not support isochronous real-time communication channels. PROFINET IO is a modular communication framework for distributed automation applications. PROFINET IO uses cyclic data transfer to exchange data, alarms, and diagnostic information with programmable controllers, input/output (I/O) devices, and other automation controllers (for example, motion controllers). PROFINET IO recognizes three classes of devices: • IO devices • IO controllers • IO supervisors Cisco IE 3000 Switch Software Configuration Guide OL-27302-02 -
Xilinx Ethernet POWERLINK Solution Sell Sheet
Xilinx Ethernet POWERLINK Xilinx Ethernet POWERLINK Solution: Synchronizing High-Performance Control Systems The Challenges to Industrial Ethernet POWERLINK is an open, software-based Real Time Communication Network Design protocol compatible with standard Ethernet hardware. Both the Controlled Nodes (slaves) and the Managing Nodes (masters) can be built on standard Ethernet • Provide high performance, cost- components for 100 Mbits/s Ethernet. effective Ethernet-based communication technology for control applications Designed For Ultimate Flexibility POWERLINK's flexibility results is standardization, ease of service and maintenance • Integrate design changes to meet and reduced implementation and operating costs. POWERLINK is ideal for future specifications synchronization of high performance motion control systems. The POWERLINK IP developed by port GmbH adheres to Ethernet POWERLINK protocol. Its four variants • Bridge between multiple interface are designed for ultimate flexibility on Xilinx FPGAs. protocols and support various protocol technologies with a common hardware Integrates with All Standard Ethernet Protocols design POWERLINK can be implemented using any standard Ethernet hardware. While supporting all topologies, it offers complete operational conformance between systems that adhere to Ethernet communication systems. The Xilinx Ethernet POWERLINK Solution Performance Now and in the Long-Term POWERLINK meets the highest requirements of hard Real Time performance • Provide hardware necessary to achieve and determinism. POWERLINK is poised to support transmission rates 10x higher best Real Time behavior, short delays (1000 Mbits/s) than today with Gigabit Ethernet ported to FPGAs. and fast response times POWERLINKsafety and Security • Implement multiple design variants in POWERLINKsafety is an open real time safety protocol developed by Ethernet the FPGA POWERLINK Standardization Group (EPSG). -
Field Networking Solutions
Field Networking Solutions Courtesy of Steven Engineering, Inc. ! 230 Ryan Way, South San Francisco, CA 94080-6370 ! Main Office: (650) 588-9200 ! Outside Local Area: (800) 258-9200 ! www.stevenengineering.com TYPES OF FIELDBUS NETWORKS* Field Networking 101 Features and Benefits of Fieldbus Networks The combination of intelligent field devices, digital bus networks, and various open communications protocols Fieldbus networks provide an array of features and benefits that make them an excellent choice is producing extraordinary results at process plants in nearly all process control environments. around the world. Compared to conventional technology, fieldbus networks deliver the following benefits: Just as our ability to retrieve, share, and analyze data Reduced field wiring costs has increased tremendously by use of the Internet and - Two wires from the control room to many devices PC network technology in our homes and at our desk- Reduced commissioning costs tops, so has our ability to control and manage our - Less time and personnel needed to perform process plants improved. Digital connectivity in process I/O wiring checkouts - No time spent calibrating intermediate signals manufacturing plants provides an infrastructure for the (such as 4-20mA signals) - Digital values are delivered directly from field flow of real-time data from the process level, making it devices, increasing accuracy available throughout our enterprise networks. This data Reduced engineering/operating costs is being used at all levels of the enterprise to provide - Much smaller space required for panels, I/O racks, and connectivity boxes increased process monitoring and control, inventory and - Fewer I/O cards and termination panels for materials planning, advanced diagnostics, maintenance control system equipment - Lower power consumption by control system planning, and asset management. -
Communication Solutions for Rockwell Automation ® Users
WHERE AUTOMATION CONNECTS Communication Solutions for Rockwell Automation® Users ASIA PACIFIC | AFRICA | EUROPE | MIDDLE EAST | LATIN AMERICA | NORTH AMERICA Table of Contents Ethernet and Serial Gateway Solutions 2 Automotive and Inertial Navigation Gateways 2 Serial & Ethernet Modbus® Solutions 3 Scalable Modbus® & Modbus® TCP Solutions for CompactLogix™ 3 Secure Remote Connectivity 4 In-Chassis Flow Computer Solutions 6 HART Solutions 6 Power and Energy Solutions 7 DNP3 Solutions 7 Modernization Solutions 8 PROFIBUS Solutions 10 Enterprise Connectivity 11 Leverage the IIoT 11 Automated Material Handling 12 802.11n (abgn) Fast Industrial Hotspots 13 Radiating Cable 2.4 and 5 GHz Band 14 802.11n (abgn) Fast Watertight Industrial Hotspots 14 Wireless Support from Trusted Experts 15 Wireless Comparison Product Selection Chart 16 In-Chassis Product Selection Chart 17 Stand-Alone Gateways Product Selection Chart 18 Rockwell_2020_EN Ethernet and Serial Gateway Solutions ProSoft Technology’s stand-alone, DIN-rail mounted industrial gateways provide a means to read or write data from devices on dissimilar protocols. All gateways come with our ProSoft Discovery Service feature. With PDS, you don’t have to change your PC to the default subnet of the module, saving you time during setup. Building Automation solutions – including QuickServer gateways – bring key operational data directly to your Rockwell Automation controller. Use these solutions to boost energy efficiency, use the resource most productively, and decrease your usage and costs. • Gateways with two Ethernet ports allow you to isolate networks, passing only the data you want between devices • EtherNet/IP gateways support multiple I/O connections for fast real-time data • Remote configuration and diagnostics via Ethernet • SD Card slot for disaster recovery of configuration data • Up to four Serial ports PROFIBUS DP & many other protocols are also available. -
Ethercat the New Standard for Measurement Applications Central Backbone for Distributed Systems
C5.2 EtherCAT The new standard for measurement applications Central backbone for distributed systems Dr. Kessel, Jens-Achim ADDITIVE Soft- und Hardware für Technik und Wissenschaft GmbH Max-Planck-Str. 22b, 61381 Friedrichsdorf Abstract In the past years EtherCAT has become a world wide accepted new standard in automation and control. In November 2003 the EtherCAT Technology Group (ETG) was founded and it has grown up to about 900 members from 45 countries in January, 2009. EtherCAT was designed and developed as an open high performance Ethernet-based fieldbus system. The development goal of EtherCAT was to apply Ethernet technology to automation applications which require short data update times (also called cycle times) with low communication jitter (for synchronization purposes) and low hardware costs. Once the new standard was introduced for automation and control, it became interesting, too, to use Eth- erCAT also for distributed systems in measurement applications. This paper takes a focus on the special properties of EtherCAT with respect to the usability in measure- ment applications. It shows the capabilities of EtherCAT as a powerful backbone, replacing classical net- works based on CAN or ProfiBUS. In particular aspects of synchronisation and real-time-processing in combination with the compact data packaging are interesting for measurement applications with a big number of distributed analog channels. E.g. in applications where torque and speed of rotating parts are picked up just to measure, to detect or even to prevent oscillations, it is very important to synchronize the sampling of data at the distributed converter modules. Only this allows then to calculate exact phase in- formation from the measured signals and evaluate and prepare the data according to the requirements of an application on top. -
FSU Technical Manual
PROGRAMMABLE CONTROLLER FPS/FP2 Fieldbus Slave Units Technical Manual BEFORE BEGINNING Liability and Copyright for the Hardware This manual and everything described in it are copyrighted. You may not copy this manual, in whole or part, without written consent of Panasonic Electric Works Europe AG (PEWEU). PEWEU pursues a policy of continuous improvement of the design and performance of its products. Therefore we reserve the right to change the manual/product without notice. In no event will PEWEU be liable for direct, special, incidental, or consequential damage resulting from any defect in the product or its documentation, even if advised of the possibility of such damages. We invite your comments on this manual. Please e-mail us at: [email protected]. Please direct support matters and technical questions to your local Panasonic representative. LIMITED WARRANTY If physical defects caused by distribution are found, PEWEU will replace/repair the product free of charge. Exceptions include: When physical defects are due to different usage/treatment of the product other than described in the manual. When physical defects are due to defective equipment other than the distributed product. When physical defects are due to modifications/repairs by someone other than PEWEU. When physical defects are due to natural disasters. Important symbols One or more of the following symbols may be used in this documentation: DANGER! The warning triangle indicates especially important safety instructions. If they are not adhered to, the results could be fatal or critical injury. Indicates that you should proceed with caution. Failure to do so may result in injury or significant damage to instruments or their contents, e.g.